SAE J1100V004-机动车辆尺寸
SAEJ1100-2005机动车辆尺寸

SAEJ1100-2005机动车辆尺寸VEHICLERECSAE Technical Standards Board Rules provide that: “This report is published by SAE to advance the state of technical and engineering sciences. The use of this report is entirely voluntary, and its applicability and suitability for any particular use, including any patent infringement arising therefrom, is the sole responsibility of the user.”SAE reviews each technical report at least every five years at which time it may be reaffirmed, revised, or cancelled. SAE invites your written comments and suggestions. Copyright ? 2005 SAE InternationalAll rights reserved. No part of this publication may be reproduced, stored in a retrieval system or transmitted, in any form or by any means, electronic, mechanical, photocopying, recording, or otherwise, without the prior written permission of SAE.2. References 2.1Applicable PublicationsThe following publications form a part of this specification to the extent specified herein. Unless otherwise indicated, the latest version of SAE publications shall apply. 2.1.1SAE P UBLICATIONSAvailable from SAE, 400 Commonwealth Drive, Warrendale, PA, 15096-0001.SAE J182—Motor Vehicle Fiducial Marks S AE J287—Driver Hand Control Reach S AE J826—Devices for Use in Defining and Measuring Vehicle Seating Accommodation S AE J941—MotorVehicle Driver’s Eye Range S AE J1052—Motor Vehicle Driver and Passenger Head Position S AE J1516—Accommodation T ool Reference Point S AE J1517—Driver Selected Seat Position SAE J2732—Automotive Seat Dimensions (Pending) SAE J4002—H-Point Machine (HPM-I I ) Specifications and Procedure for H-Point Determination—Auditing Vehicle Seats SAE J4003—H-Point Machine (HPM-I ) Procedure for H-Point Determination—Benchmarking VehicleSeatsSAE J4004—Positioning the H-Point Design Tool—Seating Reference Point and Seat Track Length 2.1.2ISO P UBLICATIONAvailable from ANSI, 25 West 43rd Street, New York, NY 10036-8002. I SO 3832—Passenger cars—Luggage compartments—Method of measuring reference volume 2.2 Related PublicationsThe following publications are provided for information purposes only and are not a required part of this specification.2.2.1ISO P UBLICATIONSAvailable from ANSI, 25 West 43rd Street, New York, NY 10036-8002.ISO 1176—Road vehicles—Masses—Vocabulary and codes I SO 3833—Road vehicles—Types—T erms and definitions I SO 4131—Road vehicles—Dimensional codes for passenger cars3.2Vehicle Loads3.2.1C URB L OAD,C URB W EIGHTThe weight of the base vehicle (standard equipment only), with all fluids filled to maximum (fuel, oil, transmission, coolant,etc.). For heavy trucks, the curb weight does not include engine fuel.3.2.2G ROSS V EHICLE W EIGHT R ATINGThe value specified by the vehicle manufacturer as the maximum loaded weight of a single vehicle.3.3Coordinate DimensionAll points of interest are described as coordinates dimensioned from the intersection of the zero planes in the three-dimensional reference system. X, Y, Z coordinates are dimensioned to their respective planes. (See Figure 1. See also SAE J182.)3.4Vehicle Fiducial MarksSee SAE J182.3.5General Vehicle Reference Points and Definitions3.5.1C ARGO F LOORThe surface for supporting cargo. If ribs are present, the cargo floor is at the top of the ribs. If the floor is covered, it is the undepressed floor covering surface.3.5.2C ENTERLINE OF O CCUPANT (C/LO)The lateral (Y) centerline of an occupant in a given designated seating position.3.5.3C OWL P OINTThe highest point on the cowl or hood at the vehicle centerline (See Figure 2.)3.5.4D AYLIGHT O PENING (DLO)A line on the exterior glazing surface that defines the minimum unobstructed opening through any glass aperture. Opaque coatings, reveals, and garnish moldings are considered obstructions. Opaque coatings, reveals, and garnish moldings adjoining the interior glazing surface are projected normal andoutward to the exterior surface. Interior components not adjoining the glass are projected horizontally to the interior glazing surface, then normal and outward to the exterior surface. Exterior components are projected horizontally to the exterior surface.3.5.5D ECK P OINTThe highest point on the deck lid panel at the vehicle centerline. (See Figure 2.)3.5.6D EPRESSED F LOOR C OVERINGThe surface of the floor covering at a designated point in the vehicle, with a load applied to the covering as specified by the manufacturer.3.5.7D ESIGNATED S EATING P OSITIONAny location intended by the manufacturer to provide seating for a driver or adult passenger while the vehicle is in motion, excluding temporary seating such as folding jump seats. Examples of designated seating positions include driver, 1st row (front seat) outboard passenger, 1st row center passenger, 2nd row outboard passenger, etc.NOTE—I n this document measurements are taken to one designated seating position in each row of seats. See Table 5.3.5.8E YELLIPSESee SAE J941.3.5.9F RONT OF D ASHA vertical tangent to the foremost predominant surface of the dash panel at the centerline of the driver, disregarding flanges and small localized formations. The dash panel is usually the vertical extension of the toe panel.3.5.10H EAD P OSITION C ONTOURSee SAE J1052. Dimensions specified in this practice aremeasured from sections cut through the appropriate 95th percentile head contour. After the head contour is constructed and oriented, sections are cut normal to grid in side view and rear view through the head centroid. The side view section is used for L38, L39, H46, and H47. The rear view section is used for W27, W35 and H35.3.5.11N ORMAL T OP OF F RAME-T RUCKThe longest normal surface of the top flange of the truck frame within the wheel base.3.5.12U NDEPRESSED F LOOR C OVERINGThe surface of the floor covering at a designated point in the vehicle, without any load applied to the covering.3.5.13L ONG-C OUPLED S EATINGSuccessive row seating (2nd row, 3rd row or greater) where the distance between successive SgRP X-coordinates is large enough to permit an H-point device to be installed with an ankle angle greater than 130 degrees.3.5.14S HORT-C OUPLED S EATINGSuccessive row seating (2nd row, 3rd row or greater) where the shoe or leg of an H-point device interferes with the preceding seat trim or structure when the preceding seat is in its design (SgRP) position. (See Figure 3B)NOTE—At least one of the following dimensions – leg room (L51), leg clearance (L58), or knee clearance (L48) –will be affected by this condition.3.5.15B ELT L INEA line that constitutes the lower edge of the Daylight Opening (DLO), as defined in 3.5.4. In situations where it is necessary to define the belt line in an area where there is no glass aperture, such as along pillars or in the obstructed regionbetween rear cargo doors, the belt line is defined by a straight line that connects the lower edges of the two adjacent openings. If the lower edges of the adjacent openings are not collinear then connect the endpoints of the two lower edges, not considering any points on a fillet radius. (See Figure 4)3.5.16M AXIMUM H OLD-O PEN P OSITIONThe maximum position of a vehicle closure that can be maintained without any applied force, or without the removal of any component or restraining device.3.6H-Point Devices – Reference Points and DefinitionsH-point devices are used to establish key reference points and dimensions in the vehicle’s interior. The most critical reference point established is the H-point. There are three types of devices that can be used to define the location of an H-point; the original H-Point Machine (HPM) and 2d H-point template as defined in J826, the new H-Point Machine (HPM-I I) as defined in J4002, and the H-Point Design Tool (HPD) as defined in J4004. The HPM and HPM-II are physical devices used in physical properties for the purpose of auditing and benchmarking. The HPD is a CAD tool used during design for establishing the occupant package.Terms and reference points related to the shoe are listed in section 3.7.This document is supplemental to the procedures addressed in SAE J826, J4002, J4003, and J4004. It is a reference for key terms and definitions. However, it does not provide sufficient information for someone to properly position and use an H-point device.3.6.1B ACK L INEA line in side view on the back pan of the H-point deviceupward from the H-point that is used to define back angle. On the HPM-II, this line connects the H-point to the sliding thorax pivot. On the HPM, this line is parallel to the flat portion of the back pan contour. The angle of this line from vertical defines back angle. (See Figure 5.)3.6.2C USHION L INEA line in side view on the cushion pan of H-point device forward from the H-point that is used to define cushion angle. On the HPM, this line connects to the K-point (knee pivot center). (See Figure 5 and SAE J826.)3.6.3D-P OINTA point on the bottom surface of the HPM-II cushion pan, at the lateral centerline, 25.5 mm (15 degrees) rearward of the H-point. On the HPM, the D-point is the lowest point on the centerline of the bottom of the cushion pan in the installed position. (See Figure 5.)3.6.4H-P OINTThe H-point is located on an H-point device. However, when an H-point device is properly positioned within a vehicle – either in CAD or in an actual physical property – the location of the H-point within the vehicle can be used as a vehicle reference point. Unless otherwise noted, this is how the term H-point is used in this practice.On an H-point device, the H-point is at the pivot center of the back pan and cushion pan assemblies, on the lateral centerline of the device. The H-point is also the intersection of the cushion line and the back line. (See Figure 5.)3.6.4.1Actual H-Point, Actual H-Point Travel PathThis refers to H-points measured in physical properties usinga properly positioned H-point machine.3.6.4.2Design H-Point, Design H-Point Travel PathThis refers to H-points defined during design using an H-point design tool and appropriate procedures. 3.6.4.3H-Point Travel PathAll possible locations of the H-point provided by the full range of seat adjustments (horizontal, vertical or rotational) for a given designated seating position. Only seat adjustments intended for driving and riding are included. Seat adjustments intended to facilitate entry, egress, cargo storage, etc. are excluded.3.6.5K-P OINT OR K NEE P IVOT P OINTA point located at the pivot center between the thigh and lower leg segments on the H-point devices.3.6.6L OWER L EG L INEA line connecting the K-point (Knee Pivot) to the ankle pivot center on the H-point devices.3.6.7S EATING R EFERENCE P OINT (S G RP)SgRP is a specific and unique H-point for a given designated seating position. Although adjustable seats will have many design H-points within their design H-point travel path, there is one –and only one –H-point defined as the SgRP for any seat/seating position.The SgRP is established early in the vehicle design process, and is the rearmost normal design driving and riding position of any designated seating position. The most critical SgRP is the one defined for the driver. It is used in positioning many other design tools, defining a number of key vehicle dimensions (e.g, legroom, shoulder room, etc.), and is referenced by several national andinternational standards and regulations.For HPM SgRP determination, see SAE J1516/1517.For HPM-II SgRP determination, see SAE J4004.3.6.7.1SgRP – FrontSgRP of the driver, unless otherwise specified.3.6.7.2SgRP – SecondSgRP of the second row outboard passenger on the driver side of the vehicle, unless otherwise specified.3.6.7.3SgRP – ThirdSgRP of the third row outboard passenger on the driver side of the vehicle, unless otherwise specified. 3.6.7.4SgRP – Fourth SgRP of the fourth row outboard passenger on the driver side of the vehicle, unless otherwise specified.3.6.7.5SgRP – FifthSgRP of the fifth row outboard passenger on the driver side of the vehicle, unless otherwise specified.3.6.8T HIGH L INEA line in side view connecting the H-point to the K-point (knee pivot).3.7Shoe Reference Points and Definitions (See SAE J826/J4002)HPM-II has a separate shoe tool that is necessary for the proper positioning of its legs in a vehicle (in CAD or in a physical property). For the J826 HPM, the shoe and lower leg are a single integral assembly.3.7.1A CCELERATOR H EEL P OINT (AHP)A point on the shoe located at the intersection of the heel of shoe and the depressed floor covering, when the shoe tool is properly positioned. (Essentially, with the ball of foot contacting the lateral centerline of the undepressed accelerator pedal, whilethe bottom of shoe is maintained on the pedal plane). (See Figure 5.)3.7.2B ALL OF F OOT (BOF)A point on the lateral centerline of the shoe 200 mm (J4002 and J4004) from the heel (HOS). See Figure 5.NOTE—For pedals designed according to SAE J826 and J1516, a distance of 203mm from BOF to AHP is permitted.3.7.3B ARE F OOT F LESH L INEA line in side view, 6.5 degrees from the bottom of shoe. The origin of the angle is 286.9 mm forward of the heel of shoe on a line from AHP through the BOF.3.7.4B OTTOM OF S HOE (BOS)The underside of the shoe, used in side view to establish planes or angles. Only the flat section of the BOS, from AHP to BOF, is of concern.NOTE—For the shoe described in SAE J826, construct the flat section by connecting the AHP to BOF.3.7.5F LOOR P LANE AND F LOOR P LANE A NGLE (FPA)A plane normal to the Y-Plane, established by the bottom of shoe contacting the floor, with the heel of shoe on the depressed floor covering at the floor reference point. The floor plane angle is the angle of the floor plane measured from the horizontal.3.7.6F LOOR R EFERENCE P OINT (FRP)-P ASSENGERSFRP is established using the shoe of an H-point device. It is the intersection of the heel of shoe and the depressed floor covering, with the bottom of shoe resting on the depressed floor covering. t is determined within 127 mm. to either side of centerline of occupant, with the shoe and/or lower leg segment moved forward to rest against the seat in front (contacting the underseat structure, lower portion of the seat back trim, etc.).(See Figure 5.)NOTE 1—For long-coupled seating, the FRP and FPA are established using a maximum ankle angle of 130 degrees.NOTE 2—The HPM-II lower leg may be attached to the shoe and detached from the H-point device to aid in positioning the shoe when determining the FRP. No interference is permitted below the ankle pivot circumference. Interference above the ankle pivot circumference is ignored. (SeeFigure 3A)NOTE 3—For short-coupled seating, where the shoe cannot be fitted between the seats, the rear of the shoe is moved as far rearward as possible, with the front of the shoe intruding into the preceding seat trim and/or structure. (See Figure 3B)3.7.7H EEL OF S HOE (HOS)A point on the shoe tool, located at the lateral centerline, bottom-back of the shoe.6.3Pedal Reference Point (PRP) CoordinatesThese dimensions apply only to the driver’s position. For definitions, see Table 10. For additional information, see Section 3.7.9 and SAE practices J4002, J4003, J4004 and J826.6.4Floor Reference Point (FRP) CoordinatesFor definitions, see Table 11. For additional information, see Section 3.7.6 and SAE practices J4002, J4003, J4004 and J826.6.5Additional CoordinatesFor definitions of additional coordinates used in this practice, see Table 12.7.Cargo Dimensions and Cargo Volume IndicesThe cargo dimensions and cargo volume indices provide estimates of cargo compartment size. As with all measurements in this document, they were developed to assist during the design and engineering of a vehicle.Discrete measurements of irregular spaces –such as the point to point measurements made of a vehicle’s interior – are often ambiguous to interpret. Further, different values can result from minor and local variations.T ables 25 through 27 provide the codes and definitions for cargo dimensions. Table 28 lists the codes and formulas for cargo volume indices.7.1Cargo Dimensions, LengthSee Table 25. For cargo lengths measured along the floor, the cargo surface to the rear of the forward measurement point should be unobstructed. Seats to the rear of the forward measurement point must be in their stowed or cargo optimized position. If there is an obstruction, such as that caused by a second row seat being folded up to the rear of the front seat, the measurement is taken from the most rearward surface of the limiting obstruction.7.2Cargo Dimensions, WidthSee Table 26.7.3Cargo Dimensions, HeightSee Table 27.7.4Cargo Volume Indices (CVI)The intent of the cargo volume indices is to provide reasonable estimates of the cargo compartment stowage potential. They do not yield actual cargo volumes. Further, although due care has been taken to clarify the dimensions used in the calculations, it is possible that innovations to interiordesign will result in equivocal interpretations.The indices are all calculated using the same basic formula: Liters 10HeightWidth Length 6=×× (Eq. 1)The definitions provided in Table 28 indicate the L dimensions to use for length, the W dimensions to use for width and the H dimensions to use for height. Measurements are taken in millimeters.In the formulas, the suffix indicating measurement row is separated from the code by a tilde (~) rather than a dash (i.e., L204~1, W3~2 rather than L204-1 or W3-2) to avoid confusion with a minus sign. NOTE—In order to calculate the CVIs in English units, the formula is:3ft 1728hes)Height(inc es)Width(inch hes)Length(inc =×× (Eq. 2)Or if dimensions were measured in metric units use: Liters / 28.32 = ft 3 8. Luggage Capacity DimensionsThe luggage set is defined in Table 29. Luggage capacity, as defined in Table 30, is determined with all vehicle standard equipment, including spare tires, convertible tops, tool kits, etc., in place and in their intended stored locations. Randomly place as many A through G luggage pieces as possible in the compartment to be measured. H-boxes are then used to complete the loading. One or more pieces of the standard luggage set may be removed to place H-boxes, provided the removed luggage pieces can be replaced. For large compartment spaces, one entire set of luggage (A through G) must be used before adding pieces from a subsequent set. I f space is available,more than the standard set of 20 H-boxes may be used. The trunk lid or other access door must close and latch freely after the luggage is fitted.9. ISO Cargo VolumesSO uses modules of various lengths, widths, and heights to determine cargo volume and luggage capacity. The modules, procedures for use, and dimensions used in reporting can be found in ISO 3832. 10. Glass Area Dimensions See Table 31 for codes. 11. FiguresFigures are provided at the back of this document in numerical order. 12. Dimension IndicesThis revision builds on the coding scheme introduced in 2002, which resulted in new codes for many dimensions. To assist the user, several conversion tables are provided in the Appendix (see Tables A1 through A19).。
sae j1100机动车辆尺寸中文版总布置必学标准

sae j1100机动车辆尺寸中文版总布置必学标准sae j1100机动车辆尺寸中文版总布置必学标准1. 引言在车辆设计和制造过程中,了解和遵守相关的尺寸标准是非常重要的。
SAE J1100标准是一个重要的标准,它规定了机动车辆的尺寸和布置相关要求。
本文将以SAE J1100标准为主题,深入探讨机动车辆尺寸中文版总布置必学标准,帮助读者全面理解和应用该标准。
2. SAE J1100标准概述SAE J1100标准是由美国汽车工程师协会(SAE)制定的,旨在规定机动车辆的尺寸和布置要求,以确保车辆设计符合相关的安全、可靠性和性能标准。
该标准包括车身长度、宽度、高度、轴距、悬挂高度、悬挂系统、轮胎尺寸、车轮轴距、悬挂系统等内容,涵盖了车辆的各个方面。
3. 深度解读SAE J1100标准3.1 车身长度、宽度和高度SAE J1100标准对车身长度、宽度和高度进行了详细的规定,包括整车长度、最大宽度和最大高度等。
这些尺寸的合理设计对于车辆的操控性、空气动力学性能和行驶稳定性有着重要的影响,因此必须严格遵守标准要求。
3.2 轴距和悬挂高度轴距和悬挂高度是影响车辆乘坐舒适性和操控稳定性的重要参数,SAE J1100标准对这些参数的设计和测量方法进行了详细说明,以确保车辆在不同路况下的稳定性和平顺性。
3.3 轮胎尺寸和车轮轴距轮胎尺寸和车轮轴距的合理设计对车辆的抓地力、悬挂系统和悬挂几何性能有着重要的影响,这些参数也是SAE J1100标准所关注的重点内容之一。
4. 总结与展望通过对SAE J1100标准的深度解读,我们可以更好地理解和应用机动车辆尺寸中文版总布置必学标准。
遵守这些标准可以确保车辆在设计和制造过程中达到相关的安全、可靠性和性能要求,同时也有助于提高车辆的操控性、舒适性和环保性能。
未来,我们可以进一步深入探讨该标准的应用和发展,为车辆制造和设计提供更好的参考和依据。
5. 个人观点与理解在我看来,SAE J1100标准作为国际上公认的标准之一,极大地推动了机动车辆制造和设计行业的发展。
saej20v004

SAE Technical Standards Board Rules provide that: “This report is published by SAE to advance the state of technical and engineering sciences. The use of this report is entirely voluntary, and its applicability and suitability for any particular use, including any patent infringement arising therefrom, is the sole responsibility of the user.”SAE reviews each technical report at least every five years at which time it may be reaffirmed, revised, or cancelled. SAE invites your written comments and suggestions.TO PLACE A DOCUMENT ORDER; +1 724-776-4970 FAX: +1 724-776-0790SAE WEB ADDRESS Copyright 2002 Society of Automotive Engineers, Inc.2.1.3ISO P UBLICATION—Available from ANSI, 11 West 42nd Street, New York, NY 10036-8002.ISO 9001—Quality systems—Model for quality assurance in design, development, production, installation and servicing2.1.4A UTOMO TIVE I NDUSTRY P UB LICATION—Available from AIAG, 26200 Lasher Road, Suite 200, Southfield, MI48034-7100.QS 9000—Quality System Requirements2.2Related Publications—The following publications are provided for information purposes only and are not arequired part of this document.2.2.1SAE P UBLICATIO NS—Available from SAE, 400 Commonwealth Drive, Warrendale, PA 15096-0001.SAE J20-1—Coolant Hose (Supplement to SAE J20 for Government Use Replacing Part of MS51230)SAE J20-2—Coolant Hose—Normal Service Type Convoluted, Wire Support Hose(Supplement to SAE J20 for Government Use Replacing Part of MS51008)3.Definitions of Hose Types3.1SAE 20R1—Heavy-duty type for service in heavy-duty application. This type is available in two wallthicknesses as indicated in 6.3.3.2SAE 20R2—Flexible heavy-duty wire embedded type for the same service as SAE 20R1.3.3SAE 20R3—Heater hose for normal service.3.4SAE 20R4—Radiator hose for normal service.3.5SAE 20R5—Convoluted wire supported type for normal service.3.6Hose Special Designators for SAE 20RXY—X Refers to the hose type. Y designators may be used forhoses with special features. Multiple Y designators may be used if needed.3.6.1HT—This High Temperature designation is for any hose type, SAE 20R1 to SAE 20R5, which is required tooperate in an environment above 125 °C. (See Section 11.)3.6.2EC—This Electrochemical designation is for any hose type SAE 20R1 to SAE 20R5 which is required tohave electrochemical resistance as defined by SAE J1684. (See Section 12.)3.6.3LT—This Low Temperature designation is for any hose type SAE 20R1 to SAE 20R5 which is required tooperate in an environment down to –55 °C. (See Section 13.)3.7Hose Classes—Compounds based on different synthetic rubber grades are specified and designated (see 5.2for test methods):Class A—high-temperature resistantClass B—high oil resistantClass C—medium oil resistantClass D-1—low oil resistant, improved serviceClass D-2—low oil resistant, standard serviceClass D-3—low oil resistant, high-temperature resistant, premium serviceClass E—low oil resistant, fiber elastomer compositePhysical characteristics for each hose class are shown in Table 1.3.8Marking—The outer cover will be printed with the designation SAE 20RXY (the X being the hose type and Y any special designator(s) such as “LT”), class, size of the inside diameter in millimeters, hose manufacturer’s code marking, and any other identification as agreed upon between user and manufacturer/supplier. It is recommended that this marking shall appear on the outer cover of the hose at intervals not greater than 380mm.3.8.1S MALL ID O R S HORT H OSE —If there is insufficient space on the hose for the required marking due to size or configuration, the marking shall be agreed upon by the customer and the manufacturer/supplier.4.Dimensional Requirements—Geometric Dimensioning and Tolerancing requirements are outlined in SAE J2370. The following requirements are minimal standards:4.1Tube and Cover Thickness—Minimum thickness shall be 1.6 mm for the tube and 0.8 mm for the cover.NOTE—This requirement does not apply for hoses without distinctive tube and cover construction.TABLE 1—COOLANT SYSTEM HOSE ELASTOMERIC MATERIAL, PHYSICAL PROPERTIESSAE Designation Typical Elastomer Class A Silicone Class B NBR Class C CR Class D–1EPDM Class D–2EPDM Class D–3EPDM Class E EPDM/Fiber Typical Temperature Range, °C –55 to 175–40 to 100–40 to 100–40 to 125–40 to 125–40 to 150–40 to 125Original PropertiesDurometer, points Shore A 55 to 7555 to 7555 to 7555 to 7555 to 7555 to 7565 to 85 Tensile, min, MPa 5.58.57.07.0 5.07.0 5.0 Elongation, min, %200250200300150300100Oven Aging Conditions and Change Limits, Hours/°C 70/17570/10070/10070/12570/125168/15070/125 Durometer, points Shore A +10+15+20+15+15+15+15 Tensile, max %–15–15–20–20–20–35–20 Elongation, max, %–40–50–50–50–50–65–50Oil Immersion Change Limits ASTM No. 3 Oil or IRM 903 (IRM 903 is being phased in to replace ASTM No. 3) Hours/°C 70/10070/10070/100———— Volume, max, %0 to +45–5 to +25+80———— Tensile, max, %–40–20–50————Coolant Immersion (Tube only)Change Limits Hours/at Boiling Point 707070707016870 Volume, %0 to +400 to +200 to +20–5 to +20–5 to +20–5 to +20–5 to +20 Durometer, points Shore A –10 to +10–10 to +10–10 to +10–10 to +10–10 to +10–10 to +10–10 to +10Tensile, max, %–30–20–20–20–20–20–20 Elongation, max, %–25–40–40–50–25–25–25Compression Set °C 125100100125125125125 70 h, max, %40507575857585Cold Flexibility (°C)(1)1.LT designator extends the low temperature flexibility to –55 °C.–40–40–40–40–40–40–404.2Length Tolerancea.Straight Hose—Unless otherwise specified by the customer or manufacturer, Commercial Tolerances will be used. See Table 2.b.Curved Hose—The tolerances on arm lengths, measured from end to intersection of nearest centerline, shall be as shown in Table 3.4.3General Layout Tolerances, Curved Hose—Dimensions locating bend intersections and centerline radii are to establish the theoretical design centerline of the hose. Actual outside contour of hose must be held within a total range of 9.6 mm of all planes with respect to theoretical outside contour of hose. For hose check, hose ends should first be placed in theoretical design position before checking (hose may have to be flexed to correct for any distortion caused by handling or during shipment). SAE arm length tolerances shall apply.Tolerances apply to all arm and body lengths in addition to contour tolerances. Dimensions covering more than one arm or body length are reference only and have no tolerances. The wall thickness within bends of a curved hose may differ from the wall thickness of the straight by no more than 33%.When an alignment mark is required for assembly operations, the basic identifier in Figure 1 is recommended:FIGURE 1—ALIGNMENT MARKLocation of the alignment mark and/or additional information shall be determined by the customer and the manufacturer.4.4Enlarged Ends—When the ID of one end of the hose is enlarged, normally the ID of the enlarged end should not exceed the ID of the rest of the hose by more than 33%. Enlarged ends should be considered arm lengths for tolerance purposes. The wall thickness normally changes with enlarged ends.TABLE 2—LENGTH TOLERANCELength mm Precision TolerancemmCommercial Tolerancemm0–300±3.2+9.7–3.2>300±1%+3%–1%TABLE 3—TOLERANCE ON ARM LENGTHArm Lengthmm Precision TolerancemmCommercial Tolerancemm0–300.0±4.0±6.4300.1–610.0±4.8±7.2610.1–910.0±6.4±9.7910.1–1220.0±9.7±11.21220.1–1830.0±12.7±15.9over 1830±1%±2%4.5End Squareness—All points on the hose end surface must lie within a tolerance zone consisting of twoparallel planes perpendicular to the hose axis. The tolerance zone is determined by Table 4.TABLE 4—END SQUARENESSHose ID Precision Tolerance Commercial Tolerance25.4 mm and larger10% of ID15% of IDsmaller than 25.4 mm 2.54 mm 3.75 mm4.6Finish and Roundness on Connections—Users of coolant hose should take every precaution to obtainconnections as smooth and round as practical. (Reference SAE J1231)4.7Clamps—Refer to SAE J1508 for available clamp types.5.Physical Test Requirements and Procedures5.1Finished Product5.1.1A DHES IO N. When applicable, use test procedure ASTM D 413. The minimum requirement is 1400 N/mbetween all elastomer or elastomer-coated plies.5.1.2C OLD F LEX IB ILITY. The following procedure shall be used:For hose 25.4 mm ID and smaller, specimen shall consist of a complete hose of length sufficient to perform bend test described as follows: the hose shall be placed in a cold box for 5 h at the temperature specified in Table 1. The hose shall then be flexed in the cold chamber through 180 degrees from the centerline to a diameter of ten times the maximum outside diameter of the hose within 4 s. The hose shall not fracture and shall not show any cracks or breaks in the tube or cover.For hose larger than 25.4 mm ID, specimens are to be 25.4 mm long sections of the complete hose. The specimen and test fixture shall be placed in a cold box for 5 h at the temperature specified in Table 1. The specimen is then compressed to 50% of its original inside diameter between parallel plates within 4 s. The specimen shall not crack or break. The testing fixture shall be in the cold box during the entire test.NOTE—For LT hose, refer to Section 13 for specific cold flexibility requirements.5.1.3O ZONE T EST AND R EQ UIREMENTS. The following test and requirements apply:When applicable, use test procedure ASTM D 1149.For hose 25.4 mm ID and smaller, a specimen of hose of sufficient length shall be bent around a mandrel with an outside diameter equal to eight times the specified OD of the sample. The two ends shall be tied at their crossing with enameled copper or aluminum wire. After mounting, the specimen shall be allowed to rest in an ozone-free atmosphere for 24 h at standard laboratory test temperature. The mounted specimen shall be placed in a test chamber containing ozone at a partial pressure of 50 mPa ± 5 mPa at a temperature of 40°C ± 1 °C.After 100 h of exposure, the specimen shall be removed and allowed to cool to standard laboratory test temperature and then be inspected visually under 7X magnification. The sample must not show any cracks except for the area immediately adjacent to the wire, which shall be ignored.For hose larger than 25.4 mm ID, prepare a specimen by cutting a strip of the whole hose 12.7 mm x 100mm and tie specimen (cover out) around a 12.7 mm diameter mandrel. Condition in the same manner as specified previously for the whole hose and apply the same conditions and requirements. This test applies to the cover only and cracks in the exposed tube or cut edges of the cover shall be ignored.5.1.4K INK T EST . This test applies to SAE 20R3 hose only. (Not recommended for formed hoses.)5.1.4.1Test Procedure. Condition specimen length of hose at standard laboratory test temperature for at least 2h. Measure the minimum OD at the approximate center of the specimen length. When a sufficient length of hose is available, it is permissible and suggested that a length in excess of the specimen length be used in an effort to minimize the handling variable and overbending. Insert one end of the hose into one hole of the specified test fixture, carefully bend the hose (in direction of natural curvature) and insert the other hose end into the second test fixture hole. Do not overbend or bend hose with sharp motion to prevent excessive kinking or collapse. Within 30 s, measure the minimum diameter at the point of greatest collapse.5.1.4.2Test Fixture. Shall consist of 25.4 mm thick flat plate drilled with holes not to exceed the hose OD by more than 1.6 mm and separated by the specified center distances.5.1.4.3Test Requirements. See Table 5.5.1.5V ACUUM C O LLA PSE T EST . When practical, the entire hose shall be tested as specified in Tables 6A and 6B.The minimum outside diameter shall decrease by no more than 20% during application of vacuum for 15 s and not to exceed 30 s.5.1.6B URST . This test shall be performed on a straight length of hose in accordance with ASTM D 380 to meet the requirement in Tables 6A and 6B.For curved 20R3 and 20R4 hose, the same reference applies, except that the test shall be performed on the individual curved hose with one end free and unrestrained and the rate of application of pressure shall be not less than 2.0 MPa nor more than 7.0 MPa/min. The aged burst requirement (11.2.2) will apply to all HT hoses.5.1.7P RESSURE V IBRATIO N AND T E MP ERATURE OR P RE SSURE AND T EMPE RATURE T EST . This test shall be used when agreed upon between customer and manufacturer/supplier, using SAE J1610 as the referenced test method. If required, test limits can be modified if agreed upon by the customer and manufacturer/supplier.TABLE 5—KINK TEST REQUIREMENTS FOR SAE 20R3 HOSENominal Hose ID mmSpecimen LengthmmCenter DistancemmCollapse of Hose Allowed, %15 and larger 24 x ID 10 x ID 25smaller than 1524 x ID8 x ID25TABLE 6A—BURST AND VACUUM VALUES(20R1 AND 20R2)NominalSizemm20R1Heavy-DutyStandard WallMinBurstMPa20R1Heavy-DutyStandard WallMinVacuumkPa20R1Heavy-DutyHeavy WallMinBurstMPa20R1Heavy-DutyHeavy WallMinVacuum,kPa20R2WireInsertedMinBurstMPa20R2WireInsertedMinVacuumkPa10 3.2933.813 2.9333.816 2.5927.019 2.2427.022 2.2423.625 2.0623.6 2.0684.429 2.0620.332 1.9016.9 3.4533.8 1.9084.435 1.9013.538 1.7210.1 3.1033.8 1.7284.441 1.72 6.844 1.55 3.4 2.7616.9 1.5584.451 1.38 2.4110.1 1.3884.457 1.21 2.41 3.4 1.2184.460 1.2164 1.03 2.06 1.0384.4700.86 1.720.8684.4 760.60 1.720.6984.4 83890.52 1.380.5284.4 1020.34 1.030.3484.4 NOTE—For hose sizes between sizes listed, use the values for the next larger size.5.2Physical Properties are to be Obtained from Specimens Removed from Hose—See ASTMD380 for pro-cedure.NOTE—For 20R5 hoses, test specimens are to be taken from the cuffs.5.2.1D UROMETER H ARDNESS —Hardness shall be measured with a Shore A Durometer according to ASTM D 2240.5.2.2T ENSILE S TRENGTH AND E LONGATION —Test according to ASTM D 412.5.2.3O VE N A GING —Shall conform to ASTM D 573.TABLE 6B—BURST AND VACUUM VALUES(20R3, 20R4, AND 20R5)Nominal Size mm 20R3Heater Min Burst MPa 20R3Heater Min Vacuum kPa 20R4Radiator Min Burst MPa20R4Radiator Min Vacuum kPa20R5Wire SupportedMin Burst MPa20R5Wire SupportedMin Vacuum kPa5 1.7233.86 1.7233.87 1.7233.8 8 1.7233.89 1.7233.8 10 1.7233.8 1.24 13 1.7233.8 1.17 16 1.7227.0 1.10 19 1.3823.6 1.03 22 25 1.2120.30.970.97 29 32 1.2116.90.900.90 35 380.830.83 41 440.760.76 510.690.69 570.620.62 60 640.550.55700.48 760.41 830.34 890.27102NOTE—For hose sizes between sizes listed, use the values for the next larger size.5.2.4C OOLANT I MMERS ION—Volume change, tensile, elongation, and durometer changes shall be observed afterimmersion in the following mixture maintained at the boiling point under a water-cooled reflux condenser.Maintain the fluid level during the test by adding distilled water as needed.a.1/2 by volume, distilled waterb.1/2 by volume, ethylene glycol-based coolant agreed to between supplier and customerMeasurements of tensile, elongation, durometer, and volume change shall be made in accordance with appropriate ASTM methods.5.2.5O IL I MME RSIO N—Shall conform to ASTM D 471.5.2.6C OMPRESSION S E T—Test to be performed per ASTM D 395, Method B. For cover specimens, ply to 8.9 mm± 1 mm, not to exceed 7 plies where applicable. For tube specimens, ply to 12.7 mm ± 1 mm, not to exceed7 plies. When unable to meet the required thickness, use standard ASTM slabs cured at similar cureconditions as the hose.NOTE—SAE J1638 may be considered as an alternate test method with criteria to be agreed upon between customer and manufacturer.6.SAE 20R1 Heavy-Duty Type6.1Scope—This type of hose is primarily for heavy-duty service of which the diesel-locomotive application is atypical example. The hose is intended to withstand the effects of higher pressure systems. When desired, hose with one class of material in the tube and another in the cover may be obtained. In such cases, the physical properties specified for respective parts shall apply.6.2Reinforcement—The reinforcement may consist of multiple plies of woven or cord fabric, or ply or plies ofbraided, knit, or spiraled yarn and shall be such that the hose meets the minimum burst and vacuum requirements as given in Table 6A.6.3Dimensions—The ID Tolerance is ±0.8 mm for sizes smaller than 51 mm and ±1.6 mm for sizes 51 mm andlarger. The Wall Thickness Range for Standard Wall Thickness hose is 4.3 to 5.6 mm. The Wall Thickness Range for Heavy Wall Thickness Hose is 5.8 to 7.1 mm. These dimensions shall be measured at a section not including a lap.7.SAE 20R2 Heavy-Duty Wire Embedded Type7.1Scope—This is similar to SAE 20R1 hose except that it utilizes wire helix or helices built into the wall of thehose. The hose is intended to withstand high vacuum and/or some forced curvature.7.2Reinforcement—The reinforcement is typically multiple plies of woven or cord fabric or ply or plies of braidedor knot yarn and wire helix or helices such that the hose will meet the minimum vacuum and burst requirements as given in Table 6A.7.3Dimensions—The ID Tolerance is ±0.8 mm for sizes smaller than 51 mm and ±1.6 mm for sizes 51 mm andlarger. The Wall Thickness Range at hose ends exclusive of wire gauge is 4.3 to 6.4 mm.8.SAE 20R3 Heater Hose8.1Scope—This type of hose is used in connecting heater systems and other components in the coolantcirculating systems of ground vehicles.8.2Reinforcement—The reinforcement typically consists of one or more plies of woven, braided, knit, or spiraled yarn, or class E material, and shall be such that the hose will meet the minimum burst and vacuum requirements in Table 6B.8.3Dimensions and Tolerances—Target dimensions and tolerances are shown in Table 7. Measurement method must be agreed upon by manufacturer and customer. Since expanded ends may cause wall thickness to change, ODs and tolerances for the expanded ends must also be agreed upon by the manufacturer and customer. Tolerances and dimensions other than those listed as follows must be agreed upon by manufacturer and customer. The values in Table 7 are standard wall dimensions and commercial tolerances.If thin-wall dimensions or precision tolerances are required, refer to SAE J2387.9.SAE 20R4 Radiator Hose Normal Service Type9.1Scope—This is a hose for coolant circulating systems of automotive type engines, commonly known as radiator hose. When resistance to vacuum collapse is a requirement, an inserted wire helix may be specified if desired.9.2Reinforcement—The reinforcement typically consists of one or more plies of woven, braided, knit, or spiraled yarn, or Class E material, and shall be such that the hose will meet the minimum burst and vacuum requirements in Table 6B.9.3Dimensions—Target dimensions and tolerances are shown in 9.3.1. Measurement method must be agreed upon by manufacturer and customer. Since expanded ends may cause wall thickness to change, ODs and tolerances for the expanded ends must also be agreed upon by the manufacturer and customer. Tolerances and dimensions other than those listed as follows must be agreed upon by the manufacturer and customer.Since the wall thickness may change due to bends near the end of hoses, the wall thickness reported will be the average of 4 readings taken 90 degrees apart. The values in 9.3.1 are standard wall dimensions and commercial tolerances. If thin-wall dimensions or precision tolerances are required, refer to SAE J2387.9.3.1D IME NSIO NS AND T OLERANCES —The ID tolerance is ±0.8 mm for hose sizes smaller than 70 mm and ±1.6mm for hose sizes 70 mm and larger. The wall thickness and tolerance is 4.95 mm ± 0.65 mm (4.3 to 5.6mm) for hose sizes smaller than 50.8 mm and 5.35 mm ± 1.05 mm (4.3 to 6.4 mm) for hose sizes 50.8mm and larger.TABLE 7—STANDARD DIMENSIONS AND COMMERCIAL TOLERANCES FOR SAE 20R3ID mm IDTolerance,mmTarget OD (1)mm1. The target OD should be measured over a plug gauge equal to the specified maximum ID.OD Tolerance mm Reference Wall mmMaximum Wall ThicknessVariation mm5.0 to <9.0±0.8Maximum ID Plus 7 mm ±0.8 3.5 1.09.0 to <25.4±0.8Maximum ID Plus 8 mm±0.8 4.0 1.025.4±0.834.0±1.2 4.3 1.0>25.4±0.8Maximum ID Plus 9.9 mm±1.64.951.010.SAE 20R5 Normal Service Type Convoluted, Wire Supported Hose10.1Scope—This is a wire reinforced hose for coolant circulating systems of automotive type engines, commonlyknown as universal type hose. This hose consists of a convoluted section with plain ends. The hose shall contain a wire helix or helices in the convoluted section.10.2Reinforcement—The reinforcement is typically a ply or plies of woven or cord fabric, braided, knot, or spiraledyarn. The hose must meet the minimum burst requirements listed in Table 6B.10.3Dimensions—The ID Tolerance is +0.8 to –1.6 mm. The Wall Thickness Range is 3.6 to 4.8 mm.11.High-Temperature Service Hose HT11.1Scope—Any hose type SAE 20R1 to SAE 20R5 which is required to be operated in an environment above125°C. The letters HT will be used to designate this new requirement, for example, SAE 20R1 HT Class A standard wall.11.2Requirements11.2.1T UBE AND C OVER—The tube and cover compounds must be Class A or Class D-3.11.2.2A GED B URST—The reinforcement yarn or fabric must be such that the hose passes the minimum burstrequirements given on the appropriate table after aging 168 h at 150 °C in a hot air oven.12.Electrochemical Resistant Hose EC12.1Scope—Any hose type SAE 20R1 to SAE 20R5 which is required to have electrochemical resistance. Theletters EC will be used to designate this requirement, for example SAE 20R1 EC.12.2Requirement—Hoses shall be tested in accordance with SAE J1684. Test method 1 shall be utilized todetermine the electrochemical resistance of the hose assembly.13.Low-Temperature Service Hose LT13.1Scope—Any hose type SAE 20R1 to SAE 20R5 and any hose class which is required to be operated in anenvironment down to –55 °C. The letters LT will be used to designate this requirement, for example, SAE 20R1LT Class A standard wall.13.2Requirements—Test frequency is a minimum of annually, per QS 9000.13.2.1R ESISTA NCE TO V IBRATION—This applies to SAE 20R2 wire embedded hoses only. The requirements of5.1.7 shall apply, using SAE J1610, Test Procedure #1, as the recommended practice.13.2.2P ROOF P RESSURE—This test shall be performed on a straight length of hose in accordance with ASTM D 380with the pressure being equal to 50% of the Burst Pressure requirement in Tables 6A and 6B. For curved 20R3 and 20R4 hose, the same reference applies, except that the test shall be performed on the individual curved hose with one end free and unrestrained and the rate of application of pressure shall be not less than2.0 MPa/min nor more than 7.0 MPa/min.13.2.3C OLD F LEX IB ILITY—The test temperature shall be –55 °C. Test per 5.1.2.14.Notes14.1Marginal Indicia—The change bar (l) located in the left margin is for the convenience of the user in locatingareas where technical revisions have been made to the previous issue of the report. An (R) symbol to the left of the document title indicates a complete revision of the report.PREPARED BY THE SAE COOLANT HOSE COMMITTEERationale—Sections 13.3 to 13.4 were removed to be in accordance with military requirements. Relationship of SAE Standard to ISO Standard—Not applicable.Application—This SAE Standard covers reinforced and flexible hoses intended for use in water and ethylene glycol-based engine-coolant system applications.Reference SectionSAE J20-1—Coolant Hose (Supplement to SAE J20 for Government Use Replacing Part of MS51230) SAE J20-2—Coolant Hose—Normal Service Type Convoluted, Wire Support Hose(Supplement to SAE J20 for Government Use Replacing Part of MS51008)SAE J1231—Formed Tube Ends for Hose Connections and Hose FittingsSAE J1508—Hose Clamp SpecificationSAEJ1610—Test Method for Evaluating the Sealing Capability of Hose Connections with a PVT Test FacilitySAE J1638—Compression Set of Hoses or Solid DiscsSAEJ1684—Test Method for Evaluating the Electrochemical Resistance of Coolant System Hoses and MaterialsSAE J2370—Geometric Dimensions and Tolerancing for Curved HoseSAE J2387—Dimensions and Tolerances for Coolant System HosesASTM D 380—Methods of Testing Rubber HoseASTM D 395—Test Methods for Rubber Property Compression SetASTM D 412—Test Method for Rubber Properties in TensionASTM D 413—Test Methods for Rubber Property Adhesion to Flexible SubstrateASTM D 471—Test Method for Rubber Property Effect of LiquidsASTM D 573—Test Method for Rubber Deterioration in an Air OvenASTMD1149—Test Method for Rubber Deterioration Surface Ozone Cracking in a Chamber (FlatSpecimens)ASTM D 2240—Test Method for Rubber Property Durometer HardnessDeveloped by the SAE Coolant Hose Committee。
SAEJ11002002汽车尺寸标准中文版.pdf

汽车车身推荐标准1、范围—美国汽车工程师协会(SAE)操作规程建议定义了一套关于车辆尺寸参数的测量和标准步骤。
尺寸参数最初用来测量在设计环境下设计车辆(例如,CAD)。
在本标准中所有的尺寸参数都可用这种方法测量的。
除此之外,一些尺寸参数可在实际车辆中使用。
如果考虑物理特性,在数值上会有一些不同。
但是,要注意衡量标准不要与设计目的弄混。
除非特别说明,除了只适用于地面有关的尺寸,所有的尺寸在与三维参考系中都可以正常测量(见SAEJ182),。
所有的尺寸都是在整备质量下测量的,除非另有说明。
所有尺寸测量于基本型车辆,不包括正规生产选择方案(RPO)或者配件,指定尺寸例外。
即使有许多术语和尺寸用人体部位来命名,它们的各种布置、性能和舒适度与之无关。
2. 参考文献2.1 适用书刊——以下书刊为本标准一部分指定范围的延伸说明。
除非另有说明,否则SAE最新版刊行即将实施这些标准。
2.1.1 SAE书刊——SAE J182-机动车辆基准点SAE J287-驾驶员人工操纵SAE J826-用于定义和测量车辆座椅位置的装置SAE J941-机动车辆驾驶员视角范围SAE J1052-启动车辆驾驶员和乘客的头部位置SAE J1516-参考点工具的布置SAE J1517-驾驶员选择座椅位置2.1.2 国际标准化组织(ISO)刊物——许可由美国国家标准学会(ANSI),纽约市25ISO 3832——乘用车——长途客车——测量基准2.2 相关刊物——以下内容只提供目标信息,并不是本标准规定的一部份。
2.2.1国际标准化组织(ISO)刊物——许可由美国国家标准学会(ANSI),纽约市25ISO 1176 道路车辆:词汇及代码ISO3833道路车辆:分类及定义ISO4133道路车辆:乘用车尺寸代码3.定义3.1 机动车辆3.1.1 乘用车——机动车辆载重最多10人,包含摩托车和拖车。
车辆的种类包括轿车、货车、运动型多用途车(SUV)和多用途乘用车(MPV)。
SAEJ1100-2009-中文版

J1100 2009年11月International地上车辆推荐标准签发日期:1973年9月修改时间:2009年11月被替换标准编号:J1100 SEP2005(R)机动车辆尺寸基本原理2009版J1100在内容上进行重大修改。
具体而言,尺寸步骤和定义:●与全球汽车生产商信息交换(GCIE)相容;●与其他美国汽车工程师学会乘坐车厢标准修订版本相协调;●与国际标准化组织(ISO)出版的相关定义同步,包括使用HPM-II;●根据美国环保署(EPA)定义的规管程序进行正规化;●与美国国家公路交通安全管理局(NHTSA)规定的联邦法规中的部分定义保持一致。
在本版本标准中,回复了部分先前删除的SAE J1100尺寸,以及一些更老版本的SAE J1100尺寸定义(例如W27)。
此外还采用了很多新的定义、尺寸和图。
因此对文件结构重新进行了调整,以保持更好的一致性,并涵盖进行了修改的内容。
最显而易见的是,无论是否在容量指数中使用行李厢,均加入了与行李厢相关的尺寸,例如长度表——行李厢尺寸长度表——行李厢地面长度从外部尺寸中被去除——L505。
使用第二个后缀以便更有逻辑的整理尺寸编码。
与前两版SAE J1100相同,位置或指定座椅位置由一级后缀决定。
二级后缀用于给出条件或进行说明。
在第4节中有更详细的说明。
为方便查找所需要的信息,增加了一个详细的目录列表。
进行了重大修改的内容如下所述。
在过去,在任何载荷条件下,所有与地面相关的尺寸均与地平面垂直。
对这个定义进行了编辑性修改以澄清这一点。
SAE J1100也重新引入了“EPA-净重”情况,并阐述了在该载荷条件下的特定尺寸。
此外,文件还给出了在生产商声明的车辆总重条件下测量的新尺寸,同时增加了从已被取消了的SAE J689中摘取的尺寸。
《SAE技术标准委员会规范》中指出:“本报告由SAE发布,以推动工程技术科学的发展。
用户使用本报告是完全自愿的,如果由于某种特殊使用而出现报告的适用性问题(包括由此产生的任何专利侵权问题),则其责任应完全由用户承担。
SAE J1100-2002 汽车尺寸标准【中文版】

汽车车身推荐标准1、范围—美国汽车工程师协会(SAE)操作规程建议定义了一套关于车辆尺寸参数的测量和标准步骤。
尺寸参数最初用来测量在设计环境下设计车辆(例如,CAD)。
在本标准中所有的尺寸参数都可用这种方法测量的。
除此之外,一些尺寸参数可在实际车辆中使用。
如果考虑物理特性,在数值上会有一些不同。
但是,要注意衡量标准不要与设计目的弄混。
除非特别说明,除了只适用于地面有关的尺寸,所有的尺寸在与三维参考系中都可以正常测量(见SAEJ182),。
所有的尺寸都是在整备质量下测量的,除非另有说明。
所有尺寸测量于基本型车辆,不包括正规生产选择方案(RPO)或者配件,指定尺寸例外。
即使有许多术语和尺寸用人体部位来命名,它们的各种布置、性能和舒适度与之无关。
2. 参考文献2.1 适用书刊——以下书刊为本标准一部分指定范围的延伸说明。
除非另有说明,否则SAE最新版刊行即将实施这些标准。
2.1.1 SAE书刊——SAE J182-机动车辆基准点SAE J287-驾驶员人工操纵SAE J826-用于定义和测量车辆座椅位置的装置SAE J941-机动车辆驾驶员视角范围SAE J1052-启动车辆驾驶员和乘客的头部位置SAE J1516-参考点工具的布置SAE J1517-驾驶员选择座椅位置2.1.2 国际标准化组织(ISO)刊物——许可由美国国家标准学会(ANSI),纽约市25ISO 3832——乘用车——长途客车——测量基准2.2 相关刊物——以下内容只提供目标信息,并不是本标准规定的一部份。
2.2.1国际标准化组织(ISO)刊物——许可由美国国家标准学会(ANSI),纽约市25ISO 1176 道路车辆:词汇及代码ISO3833道路车辆:分类及定义ISO4133道路车辆:乘用车尺寸代码3.定义3.1 机动车辆3.1.1 乘用车——机动车辆载重最多10人,包含摩托车和拖车。
车辆的种类包括轿车、货车、运动型多用途车(SUV)和多用途乘用车(MPV)。
SAE J标准目录中文
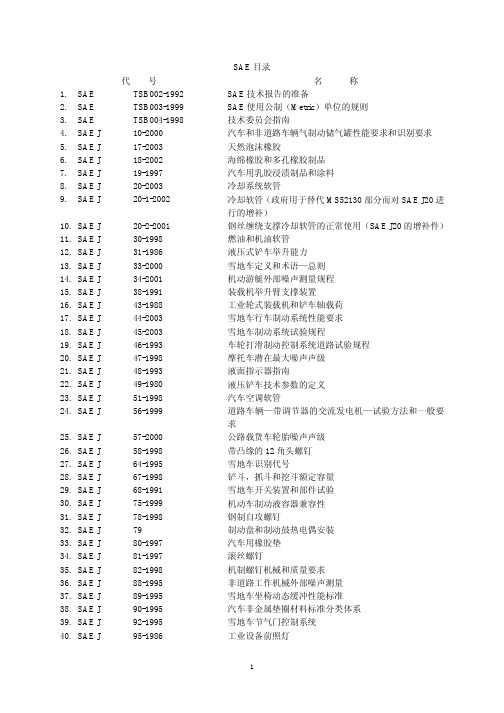
代号 180-2002 182-1997 183-2002 184-1998 185-2003 187 188-2003 189-1998 190-1998 191-2003 192-2003 193-1996 195-1988 198-2003 200-2001 201-1997 207-1985
名
称
机械制动灯开关
合成树脂塑料密封胶—不干型
前照灯开关
废气排放测量用仪器和测量技术
商用车制动器额定功率要求
点火开关
视野术语
柴油机燃油喷嘴总成—8,9,10 和 11 型
乘用车和轻型载货车稳态方向控制试验规程
车轮/轮辋—载货车—性能要求和试验规程
摩托车后视镜
车辆识别号码体系
乘用车识别号码体系
悬架弹簧额定承载能力
技术委员会指南
汽车和非道路车辆气制动储气罐性能要求和识别要求
天然泡沫橡胶
海绵橡胶和多孔橡胶制品
汽车用乳胶浸渍制品和涂料
冷却系统软管
冷却软管(政府用于替代 MS52130 部分而对 SAE J20 进
行的增补)
钢丝缠绕支撑冷却软管的正常使用(SAE J20 的增补件)
燃油和机油软管
液压式铲车举升能力
雪地车定义和术警报灯
通用工业机械人员防护
公路上使用的工业设备灯光和标志
A 类车辆风窗玻璃阴影区域
汽车鼓式制动器液力分泵
摩托车操纵件和显示器
摩托车制动系统试验代码
摩托车和动力驱动自行车行车制动系统性能要求
电动风窗玻璃刮水器开关
冷拔机械弹簧钢丝和弹簧
座椅安全带织带磨损性能要求
安全标志
纤维板褶皱弯曲试验
淬硬和回火螺纹紧固件的脱碳
中国铁路现役机车介绍

中国铁路现役内燃中国铁路现役内燃&&电力机车介绍电力机车介绍东风4B 货运型绰号:西瓜娘家:大连机车厂目前状况:国内铁路货运的绝对主力。
东风4B 系列生产了三四千台。
而且过去六七十年代生产的老东风4基本型,也都翻新成了BF4-B,不过翻新的一般被称为:假西瓜。
技术参数:用途:干线客、货运轨距:1435mm限界:GB146.1-83(车限1A、1B)传动方式:交-直流电传动轴式:Co-Co轮径:1050mm轴重:23±3%t整备重量:138±3%t通过最小曲线半径:145m最大运用速度:120km/h持续速度:28.5km/h起动牵引力:327kN持续牵引力:243kN柴油机型号:16V240ZJB柴油机装车功率:2430kW主发电机型号:TQFR-3000硅整流装置型号:GTF4800/770牵引电动机型号:ZQDR-410车钩型式:改进下开式三号车钩或TB1595-85下开式转向架轴距:1800×2mm 机车外形尺寸:21100×3309×4755mm东风4B客运型绰号:桔子娘家:大连机车厂柴油机装车功率:2430kW状况:昔日客运主力,但是随着铁路提速,已经力不从心,一部分转到山区对速度要求不高的地区继续服役,其余的改变了齿轮传动比,刷上绿色图装,改成了“西瓜”去拉货车。
也有老东风翻新的假桔子。
型号:东风4D货运型绰号:乌克兰娘家:大连机车厂功率:2940KW型号:东风4D绰号:花老虎娘家:大连机车厂功率:2940KW图装识别:DF4D-0****,为提速型客运机车,构造速度145KM/H 涂装:枣红和白DF4D-3****,为准高速型客运机车,构造速度170KM/H,涂装:枣红和白状况:无数“花老虎”拉着特快列车和快速列车飞驰在祖国的大江南北,长城内外,两只老虎,两只老虎,跑地快,跑地块……技术参数:用途:干线客、货运轨距:1435mm限界:GB146.1-83(车限 1A、1B)传动方式:交-直流电传动轴式:Co-Co轮径:1050mm轴重:23±3%t整备重量:138±3%t通过最小曲线半径:145m最大运用速度:客:145km/h 货:100km/h持续速度:客:39km/h 货:24.5km/h起动牵引力:客:302.6kN 货:480.48kN持续牵引力:客:214.8kN 货:341.15kN柴油机型号:16V240ZJD柴油机装车功率:2940kW主发电机型号:TQFR-3000E硅整流装置型号:GTF5100/1250牵引电动机型号:ZD109B车钩型式:TB1595-85下开式转向架轴距:1800×2mm机车外形尺寸:21100×3309×4755mm东风4DJ型铁路干线客货运内燃机车,是西门子公司大连机车车辆厂合作研制的,与我国第一代应用交流电传动技术的铁路干线内燃机车。
- 1、下载文档前请自行甄别文档内容的完整性,平台不提供额外的编辑、内容补充、找答案等附加服务。
- 2、"仅部分预览"的文档,不可在线预览部分如存在完整性等问题,可反馈申请退款(可完整预览的文档不适用该条件!)。
- 3、如文档侵犯您的权益,请联系客服反馈,我们会尽快为您处理(人工客服工作时间:9:00-18:30)。
奇瑞汽车有限公司
SAEJ1100V004-Motor Vehicle Dimensions
(V01)
编制:冯国庆
审核:
批准:
乘用车工程研究一院
整车技术部
初版:1973年9月修订:2002年7月
代替J1100FEB2001
机动车辆尺寸
1 范围
这个SAE工业标准定义了一整套关于车辆尺寸的测量方法和标准程序。
这些尺寸是在车辆设计环境下用来测量车辆前期设计目标的。
所有在这个范围内的尺寸都能按照这些方法测量。
2 规范性引用文件
下列文件中的条款通过本标准的引用而成为本标准的条款。
凡是注日期的引用文件,其随后所有的修改单(不包括勘误的内容)或修订版均不适用于本标准,然而,鼓励根据本标准达成协议的各方研究是否可使用这些文件的最新版本。
凡是不注日期的引用文件,其最新版本适用于本标准。
SAE J182—Motor Vehicle Fiducial Marks机动车辆坐标点
SAE J287—Driver Hand Control Reach驾驶员手伸区域
SAE J826—Devices for Use in Defining and Measuring Vehicle Seating Accommodation用于测量车辆座椅调节的设备
SAE J941—Motor Vehicle Driver’s Eye Range机动车辆驾驶员视野范围
SAE J1052—Motor Vehicle Driver and Passenger Head Position机动车辆驾驶员和乘客头部位置SAE J1516—Accommodation Tool Reference Point调节工具坐标点
SAE J1517—Driver Selected Seat Position驾驶员调节座椅位置
3 术语和定义
3.1 整车整备质量Complete Vehicle Kerb Mass
定义见GB/T3730.2
3.2 最大允许总质量Maximum Authorized Total Mass
定义见GB/T3730.2
3.3 设计质量Design Mass
整车整备质量与乘员质量(每人按68㎏计算)之和的车辆质量。
乘员分配如下:对于2座和3座汽车:第一排坐2人;
对于4座和5座汽车:第一排坐2人,第二排坐1人;
对于6座和7座汽车:第一排坐2人,第二排坐2人;
对于8座和9座汽车:第一排坐2人,最后排坐3人。
当最后排座上只有2个座位,1人应坐在倒数第二排。
3.4 X、Y和Z基准平面zero X、Y and Z planes
见附录A
3.5 基准点尺寸
见附录A
3.6 x、y和z 平面x、y and z planes
平行于其相关的X、Y和Z基准平面的平面
3.7 C点(Cowl Point)
沿汽车Y—O平面,发动机罩的最高点,具体见图1
3.8 D点(Deck Point)
沿汽车Y—O平面,行李箱盖的最高点,具体见图1
3.9 人体中心线(Centerline Of Occupant)
在指定的位置上,人体的横向中心线
3.10 窗玻璃透光部分(Daylight Opening DLO)
窗玻璃透光部分就是绕过金属薄板密封条、装饰框、彩色条纹、丝网印品等的限制,可以看清外景玻璃上透明的部分,像遮阳板、风窗上的彩色条纹、窗玻璃制造者的标记等均属例外,刮水器也不考虑遵守透明的规定
3.11 眼椭圆
见SAE J941 (R)Motor V ehicle Driver's Eye Locations
3.12 头部轮廓线
见SAE J1052 (R)motor vehicle driver and passenger head position
3.13 H点确定
见SAE J826 (R)H-Point Machine and Design Tool Procedures and Specifications
4 代码系统
本标准中的每一尺寸给定一个代码,该代码由尺寸类型,数字和后缀三部分组成
4.1 尺寸类型
下列大写字母表示所标注尺寸的分类代码:
L —长度
H —高度
W —宽度
A —角度
PW —与踏板相关的宽度尺寸
PL —与踏板相关的长度尺寸
PH —与踏板相关的高度尺寸
SL —与座椅相关的长度尺寸
SW —与座椅相关的宽度尺寸
SH —与座椅相关的高度尺寸
D —直径
S —面积
V —体积
4.2 数字
数字分段规定如下:
1~99 用于内部尺寸
100~199 用于外部尺寸
4.3 后缀
-1 (第一排)在驾驶员指定座位处测量
-2 (第二排)在第二排最外侧乘员指定座位处测量
-3 (第三排)在第三排最外侧乘员指定座位处测量
-4 (第四排)在第四排最外侧乘员指定座位处测量
注:若两侧对称,可只测其中一侧
5 度量单位制
5.1 单位
本尺寸单位是以下列国际单位制作基础的:
长、宽、高mm
面积mm2
容积mm3
角度º
5.2 测定值
测定值取数方法:
长、宽、高取整数
面积到小数点后4位
容积到小数点后3位
角度到小数点后1位
6 三维坐标系和关键点尺寸
三维坐标系和关键点尺寸定义见表1,表2
注:表中所列载荷状态
“K”表示整车整备质量
“A”表示最大允许总质量
“D”表示设计质量
“—”表示对载荷状态不做要求
6.1 三维坐标系尺寸(见表1)
通过三维坐标系尺寸可反映整车在三种载荷状态下的姿态角
表1 三维坐标系尺寸
6.2 关键点尺寸
对于关键点坐标的标注采用集中标注。
具体见表2
表2 关键点尺寸
7 外部尺寸
关于外部尺寸分别从长,宽,高,角度这四个方面考虑,具体见表3,表4,表5,表6。
表5 外部尺寸—高度
8 内部尺寸
关于外部尺寸分别从长,宽,高,角度以及与假人这五个方面考虑,具体见表7,表8,表9,表10,表11,表12,表13
表9 内部尺寸—高度
9 其他尺寸
主要是玻璃面积尺寸,最小转弯直径和行李箱容积,具体见表14,表15,表16
表16 行李箱容积
3 V3*行李箱最大容积用测量六面体来测量。
在这里,载货
高度由汽车顶盖来限定。
这里的座椅
和第二排座椅靠背按制造厂的设计是
可折叠的。
前边界为前座椅和/或者第
二排座椅靠背的背面。
前边界在前座
椅靠背上方,由其背面至顶盖的X平
面形成
—21
10 附图
图1 主视图图 2 俯视图
图3 俯视图图4 俯视图
图 5 主视图图 6 底盘主视图
图7 侧风窗玻璃后视图图8A 主视图
图8B 主视图
图9 主视图
图10A 后视图
图10B 头部轮廓后视图
图11A 主视图
图11B 头部轮廓后视图
图12 主视图图13 主视图
图14 方向盘与眼椭圆图15 踏板的主视图
图16 踏板的后视图
图17 座椅主视图图18 座椅尺寸
图19 H点行程的主视图(4向,6向座椅)图20 H点行程的主视图(2向座椅)
图21 行李箱容积
附录A
(规范性附录)
三维坐标系和基准点——定义
A.1 三维坐标系:指在产品最初设计阶段确定的三个正交平面组成的坐标系统(见图A.1)。
这三个基准平面是:
Y基准平面:车辆纵向对称平面;
X基准平面:垂直于Y基准平面的铅垂平面;
Z基准平面:垂直于Y和X基准平面的水平面。
注1:除相对于支承平面的尺寸外,车辆上每一个点均以三维坐标系中的三个坐标X、Y和Z来标定位置。
注2:规定X基准平面的前方,Y基准平面的左方和Z基准平面的下方为负值。
A.2 基准点:在车体上由公司规定的三个或更多的实际点(孑L、面有特征的部位和压坑)。
注:这些点按三维坐标系确定其坐标尺寸,亦可用于表示在各种载荷下车辆对于支承平面的位置。
图A.1 三维坐标系示意图。