船体构件下料
船体型材下料图形系统的研究与实现的开题报告

船体型材下料图形系统的研究与实现的开题报告一、选题背景船舶作为人类重要的水上交通工具,其制造从设计到建造都需要高度精细,其中船体型材的下料是船舶建造过程中十分重要的一个环节。
当前,传统的手工下料方式存在效率低、精度不高、人力成本高等问题,因此采用计算机辅助下料系统可以提高生产效率,提高下料精度,降低人力成本。
二、研究内容1. 对船舶制造中常见的型材进行研究,并分析各种型材在船体结构中的作用。
2. 研究常用的数控下料设备,包括钢铁加工数控下料机、氧气割切机等,并分析其工作原理及优缺点。
3. 研究并实现船体型材下料系统,包括图形展示、下料路径规划、下料程序生成等模块,实现船体型材的智能下料功能。
4. 对系统进行测试及优化,优化算法,提高系统效率和下料精度。
三、研究意义1. 提高船舶制造生产效率和下料精度,降低人工成本。
2. 为船体下料工艺的全面数字化提供实现方案,推动制造业数字化升级。
3. 为船舶结构设计和智能制造提供技术支持。
四、研究方法1. 在深入研究相关文献基础上,对常见的船体型材进行了解,分析其在船体结构中的作用。
2. 学习和研究数控下料设备及其工作原理,并根据工作原理设计下料系统。
3. 利用相关数学知识,设计下料系统下料路径规划算法,实现下料程序生成。
4. 对下料系统进行测试和优化。
五、论文结构第一章:绪论①选题背景②研究意义③国内外研究现状第二章:船体型材下料系统的总体设计①系统架构②下料系统流程③下料系统功能第三章:船体型材的选取及下料路径规划①常见船体型材的形状和用途②船体型材的下料路径规划第四章:船体型材下料系统的实现①船体型材下料系统核心模块设计②系统界面设计③下料程序生成算法第五章:系统的测试分析与优化①测试环境②测试数据及分析③优化方法第六章:总结与展望①本文的主要工作及贡献②不足之处③未来研究方向参考文献。
船体施工工艺

本船将主船体划为5个立体分段,分别为101、102、103、104、105分段;主甲板室划分为2个立体分段,分别为201、202分段。
上甲板室划分为1个立体分段,301分段。
2.3分段建造简介胎架采取反造甲板胎架(模板每2~3肋位设置)主船体分段以主甲板为基准面进行反造;上层建筑分段分别以各层甲板为基准面进行反造。
各分段采取各构件按铺板贴胎、板缝焊接、划线、结构安装、验收、焊接的工艺顺序进行制作全船板材采用数控切割下料,型材采用手工下料。
2.4分段合拢根据本船分段划分特点,本船将按下列合拢顺序进行本船的船台合拢:分段组装先后顺序序分段名备注号1 102分段定位分段上船台2 101、103分段分别与102分段合拢3 104分段与103分段合拢4 105分段与104分段合拢悉有关的工艺和技术文件,按要求施工。
4.3工艺要求4.3.1小组立4.3.1.1小组立工艺流程4.3.1.2小组立作业标准a) 构件对划线(理论线)<1.5mm~2.0mmb) 平整度<4mm~6mmc) 小零件对大零件垂直度<2 mmd) 平面板架:L<±4mm B<±4mme) 对角线差值:L1-L2<4mm4.3.2中组立4.3.2.1 中组立工艺流程4.3.2.2 中组立作业标准a) 构件对合线(理论线或对合线)偏移<1.5mmb) 主要平面不平度<4mmc) 小零件对大零件垂直度<2mmd) 框架四角水平<±4mme) 纵骨端面平面度<±4mmf) 两对角线中点间距≤2mm4.3.3大组立4.3.3.1 客船双层底大组立4.3.3.1.1工艺流程4.3.3.1.2装配作业标准a) 分段长:L <±4mmb) 分段宽:B <±4mmc) 分段高:H <±3mmd) 分段方正度:<4mm (内、外底板对角线差值)e) 分段扭曲度:<±8mm (内底板四角水平)f) 纵骨端平面度:<±4mmg) 内、外底板中心线偏差<±3mmh) 内、外底板肋位线偏差<±3mm4.3.3.2机舱大组立4.3.3.2.1机舱工艺流程4.3.3.2.2装配作业标准a) 分段长L <±4mmb) 分段宽B <±4mmc) 分段高H <±4mmd) 分段方正度(内底板四角水平)<±8mm4.3.3.3其它立体分段大组立4.3.3.3.1分段工艺流程4.3.3.3.2装配作业标准a) 分段长<±4mmb) 分段宽<±4mmc) 分段高<±4mmd) 纵横舱壁垂直度<0.1%h,且小于10mme) 分段两端平面<±4mm4.3.3.4艉部分段大组立4.3.3.4.1艉部分段工艺流程4.3.3.4.2装配作业标准a) 前后尾轴管偏心<3mm (施工中焊接变形进行监控)b) 尾尖舱壁水平<±4mmc) 和铸钢件相焊焊缝铸钢件和钢板预热。
船体整体建造施工工艺设计

船体整体建造施工工艺A、船体建造程序一、准备工作:1、清理打扫水泥船台;2、船台中心部位涂带状红漆;3、用激光经纬仪在红漆带上打(画)出中心线并作为永久标记;4、同时测量并计算出该船台实际倾斜度。
二、排墩1、在中心线位置排放中心墩;2、确定墩位前后倾斜度(一般不超过7/1000);3、墩距不超过2m;4、确定艏艉中心线,做上记号及标杆,以便以后测量船的直线度,测定轴中心的正确度,即舵筒中心的正确度用;5、做好中心各墩的高度。
三、样台及放样样台可用角铁上铺铁板,也可直接铺放在平整地面上,拼好并到好油漆,按型值放样,放样必须准确,否则装配合会有难度。
四、下料在船台墩排好,材料进场后,底板以下构件及扶强材开始下料,如实肋板、水密补板、边纵桁、舭肘桁等,下料样板尺寸要准,划线明确准确,切割力求光顺、平整、无毛刺,较长平直部位,尽量用半自动机切割,并归堆待用。
做好记录。
五、上K桁板在中心墩排好,测量倾斜度后开始上K桁板,船中先上向首、尾铺开,在上K珩板时,板的对接缝不要在墩子上,K桁板对接缝采用刨边机或半自动切割开坡口后焊前打磨,并要用507焊条。
也要注意对接外板缝不能在舱壁或肋部位,最佳位置在距舱壁或肋骨100—150mm以。
在装K桁板同时,着手下双层底的构件,如实肋板、纵桁材,节点肘板,支撑,衬板等。
在装K桁板同时,未装肋板之前,把船肿两边底板A、B、C行板,预先在船台到位,并纵向拼好板缝用自动焊焊好(横向不要焊),此时拍片检查施焊情况。
拼板时焊缝两端安装好引、熄弧极。
六、上纵珩,划K板上的中纵桁安装线K板安装完成后,可上中纵桁,中纵桁下料后,四边坡口,打磨(自动割刀开坡口),用507拼装,与K板必须垂直并固定。
在上主龙筋前除划好主龙筋安装线外,还需划好肋位线,在划肋位线时,一般每道肋位放大1mm~1.5mm,防止焊接收缩面造成船总长缩短。
上中纵桁,按K桁板上的肋距线划肋位线垂直线,K桁斑上肋位线与主龙筋肋位线都是从船中向艏艉进行。
船舶下料工艺标准[精品]
![船舶下料工艺标准[精品]](https://img.taocdn.com/s3/m/cd1f5cd4caaedd3382c4d355.png)
船舶下料工艺标准[精品]范围:本守则适用于船舶、海工平台原材料、型材和管材的划线、下料及矫正。
适用于以火焰切割及等离子切割作为切割方式的切割下料过程。
1 钢材管理1.1 钢材进厂应该对证件,并进行外观质量检查。
1.2 钢材应按规格、牌号分类平整堆放。
1.3 钢材应根据生产加工计划按钢料单发料。
1.4 钢材进入生产线前进行表面质量检查。
1.5 钢材管理的质量控制要点。
a) 规格、牌号、炉号、批号;b) 板材、型材厚度负偏差;c) 表面质量;d) 大型铸锻件缺陷。
1.6 钢板表面缺陷的限定按表1-6-1。
表 1-6-1 钢板表面缺陷的限定项目要求1. A范围为优良区只包含深度为0.15mm以下的不必修整的表面缺陷。
麻2. B范围为合格区,包含允许存在不点需修整的表面缺陷,在实线范围内厚度、剥为20mm以下的板;虚线范围内(含实落线范围)厚度为20,50mm的板。
、结3. ,范围为修整区,即存在不允许存疤在的表面缺陷,应修整。
、刻缺陷修整方法: 痕<0.07t,且d?3mm,磨平; d00、气 0.07t?d?0.2t,焊补后磨平; 0孔如果缺陷的深度大于板厚的20%,面积超过板面积的2%,则这部分板需按表1-8-1中“严重夹层”进行更换。
1.7 钢板厚度负偏差要求按表1-7-1。
表1-7-1 钢板厚度负偏差项目要求钢板厚度负偏差最大为0.3mm 1.8 钢板夹层处理按表1-8-1.表 1-8-1 钢板夹层处理项目要求1. 夹层面积小于钢板面积的2%,深度小于板厚的20%时,可批除后再焊补,如(a)所局示。
2. 夹层的面积小于钢板面积的2%,且缺陷部接近钢材表面,则进行焊补,如(b)所示。
夹 3. 如果夹层焊补长度超过钢板边缘长度的层20%,则应用无损探伤检查焊补质量。
1. 如果夹层面积大雨钢板面积的2%,且深度大雨板厚的20%时,则可更换一张钢板的一部分。
2. 更换的钢板,其最小宽度或长度: 严外板和强力甲板:重在舯0.6L区域内为1600mm,L为船长;在舯0.6L区域外为800mm; 夹其他结构件为300mm或板厚的10倍,取其最大者。
第四章 船体放样与号料
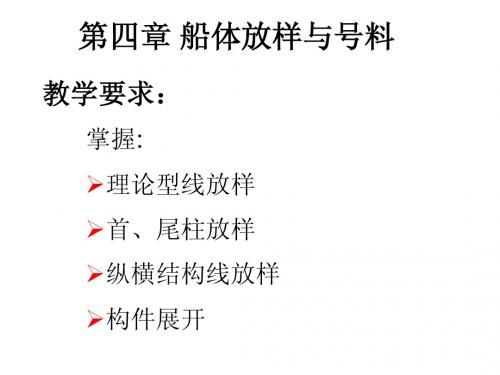
2.理论线型放样
(1)首、尾轮廓线 ) 按船体线型图和首、尾柱图上的 要求,将各水线上的外形点与首尾垂 线间的距离确定后,用木制样条光顺 地连接各点即得首、尾轮廓线。 但应 注意,除首、尾轮廓线中首至尾总长 两点和两柱间长两点及尾部推进部位 的高度不应变动外,其它各点均可光 顺调动。
(2)甲板线 ) 甲板通常均有双向曲度,甲板的 横向挠度称为梁拱,甲板的纵向挠曲 度称为舷弧。如果船上不仅有一层甲 板,放样时就应先和将主甲板放出, 等主甲板线最后修光顺后,再根据各 层甲板与主甲板间的高度距离依次画 出其余各层甲板。下面叙述双向曲度 型甲板的放样步骤。
(2)作其它格子线 )
1)站线画法 ) 站线就是将船舶的两柱间长分成若 干等分的垂直于基线和水平面的垂线, 干等分的垂直于基线和水平面的垂线, 一般分成十等分或二十等分, 一般分成十等分或二十等分,由于首 尾部分线型曲率较大, 尾部分线型曲率较大,因此要加设辅 助站线, 助站线,即在原等分站线间加入半号 站线,其作法如下: 站线,其作法如下:
4)作横剖面甲板边线;取一样条A,上画一准线, 与侧面最高水线对齐,将已调顺的的侧面甲板边线 与各站号的交点录取在样条A上,然后将样条A移 至横剖面中心线和半宽线上,并使样条的准线对准 横剖面上的最高水线。用粉线将各站号线上的甲板 边线高度点相连并弹成直线。另取一样条B,上面 画一准线,与平面中心线对齐,录取已调顺的甲板 半宽曲线与各站线的交点,然后将样条B移至横剖 面上,以中心线为基准,上下移动样条,使各站线 半宽点与各相应站线高度平直线相交,再用样条将 这些高、宽的交点连成光顺的曲线,即为甲板高、 宽边线,当高、宽边线有修改点时,应将修改后的 新高、宽点用样条A或B重新录下来并移至侧面或 平面,直到三面曲线都光顺为止。
1.船体整体建造施工工艺

船体整体建造施工工艺A、船体建造程序一、准备工作:1、清理打扫水泥船台;2、船台中心部位涂带状红漆;3、用激光经纬仪在红漆带上打(画)出中心线并作为永久标记;4、同时测量并计算出该船台实际倾斜度。
二、排墩1、在中心线位置排放中心墩;2、确定墩位前后倾斜度(一般不超过);3、墩距不超过2m;4、确定艏艉中心线,做上记号及标杆,以便以后测量船的直线度,测定轴中心的正确度,即舵筒中心的正确度用;5、做好中心各墩的高度。
三、样台及放样样台可用角铁上铺铁板,也可直接铺放在平整地面上,拼好并到好油漆,按型值放样,放样必须准确,否则装配合会有难度。
四、下料在船台墩排好,材料进场后,内底板以下构件及扶强材开始下料,如实肋板、水密补板、边纵桁、舭肘桁等,下料样板尺寸要准,划线明确准确,切割力求光顺、平整、无毛刺,较长平直部位,尽量用半自动机切割,并归堆待用。
做好记录。
五、上K桁板在中心墩排好,测量倾斜度后开始上K桁板,船中先上向首、尾铺开,在上K珩板时,板的对接缝不要在墩子上,K桁板对接缝采用刨边机或半自动切割开坡口后焊前打磨,并要用507焊条。
也要注意对接外板缝不能在舱壁或肋部位,最佳位置在距舱壁或肋骨100—150mm以内。
在装K桁板同时,着手下双层底内的构件,如实肋板、纵桁材,节点肘板,支撑,衬板等。
在装K桁板同时,未装肋板之前,把船肿两边底板A、B、C行板,预先在船台到位,并纵向拼好板缝用自动焊焊好(横向不要焊),此时拍片检查施焊情况。
拼板时焊缝两端安装好引、熄弧极。
六、xx,划K板上的中纵桁安装线K板安装完成后,可上中纵桁,中纵桁下料后,四边坡口,打磨(自动割刀开坡口),用507拼装,与K板必须垂直并固定。
在上主龙筋前除划好主龙筋安装线外,还需划好肋位线,在划肋位线时,一般每道肋位放大1mm~1.5mm,防止焊接收缩面造成船总长缩短。
上中纵桁,按K桁板上的肋距线划肋位线垂直线,K桁斑上肋位线与主龙筋肋位线都是从船中向艏艉进行。
船舶建造流程(3)船体放样号料与钢材预处理

船舶建造流程(3)船体放样号料与钢材预处理船舶建造流程(3)船体放样号料与钢材预处理首先说明船体建造流程1船体放样与号料,就是将设计部门设计的型线图、结构图按比例进行放样展开,以得到船体构件的真实形状和实际尺寸,然后再将这些已经展开的零件,通过样板、图纸()、数控等不同的号料方法,实尺画(割)在钢板或型材(球扁钢、角钢)上。
船体放样和号料目前已全部由手工转为计算机(样板制作依然需手工完成,不过依据的图纸也是由计算机完成的)制作,主要是利用相关生产设计或专门放样得软件进行展开,给出零件套料图(一般以分段为单位,方便后续零件的堆放和转运)、数控切割程序(切割机下料使用)、以及零件加工数据。
一般分为结构线生成、零件生成和套料。
2钢材预处理。
供船体结构使用的板材和型材,由于轧制和运输堆放过程中的各种影响,会产生变形和锈蚀,为保证质量,在切割前需要进行除锈,喷涂车间底漆,矫正,这个过程叫做钢材预处理。
常用的除锈方法有抛丸除锈(使用离心式抛丸机的旋转叶轮将铁丸或其他的磨料高速喷射到钢板的表面使氧化皮和锈斑剥离)、化学除锈(使用某些酸液将氧化皮和锈斑反应掉,应用范围广,可以对铝板等除锈)。
目前常用的除锈和涂漆是由钢材预处理流水线完成的。
钢材预处理流水线是由钢材的除锈、喷漆、烘干等工序形成的自动作业流水线。
钢材预处理流水线的工艺流程:(1)先用电磁吊将钢材吊放到输送辊道上。
(2)辊道以3-4m/min的速度送入加热炉,使钢材温度达40~60℃,目的是去除钢板表面的水份,并使氧化皮、锈斑疏松,便于除去,同时可增加漆膜的附着性。
(3)钢板进入抛丸除锈机,抛丸装置自动地向钢板两面抛射丸粒(丸粒可回收再使用),并用热风除去钢板表面的灰尘。
一般要求除锈等级要达到Sa2.5级,及钢板表面应不可见油腻、污垢、氧化皮、锈皮、油漆、氧化物、腐蚀物、和其它外来物质(不包括疵点),但疵点限定为不超过每平方米表面的5%,可包括轻微暗影;少量因疵点、锈蚀引起的轻微脱色;氧化皮及油漆疵点。
造船的步骤——精选推荐

假如钢板什么的你都买了接下来的造船步骤船舶的建造材料——船舶的焊接——船体放样与号料——船体钢料的加工——船体构件装焊——船体分(总)的装焊——上层建筑和烟筒的装焊——船舶舾装的涂装——船舶管系的安装——船舶的总装——船舶下水——船舶试验与交船
1.钢板预处理,将钢板除锈、涂油漆、烘干,矫正,则预处理完毕(作用;
2.将预处理的钢板按设什图纸的要求切割成各种形状的零件,工厂叫做下料。
3.下料第一块钢板之时,就是造船正
式开工之日,也是造船综合日程表上标明的开工日期
4.造船不可能一路下来造一条所以要分段,可怎么分不同的船厂有不同的分法,因为每个厂的龙门吊都不同要看自己厂的实际能力。
- 1、下载文档前请自行甄别文档内容的完整性,平台不提供额外的编辑、内容补充、找答案等附加服务。
- 2、"仅部分预览"的文档,不可在线预览部分如存在完整性等问题,可反馈申请退款(可完整预览的文档不适用该条件!)。
- 3、如文档侵犯您的权益,请联系客服反馈,我们会尽快为您处理(人工客服工作时间:9:00-18:30)。
船体构件下料工艺
一、适用范围
1、适用于船体组装、分段制作前的电脑下料。
2、适用于船体组装、分段制作前的手工下料。
二、工艺内容
1、船体构件下料
船舶构件下料分为电脑数控下料和手工下料
1.1 电脑数控下料
1.1.1 电脑结构编程人员接到施工图纸后须先熟悉图纸,发现疑问或差错速与设计部
门联系,切不可不管图纸对错盲目施工。
1.1.2 电脑结构编程人员在熟悉图纸的情况下进行结构线布置,全船或某分段需特殊
定义的结构线进行布置。
(结构线定义方法详见HD-船体建造系统-结构子系
统使用说明)
1.1.3 结构线布置完后进行结构零件生成,编程人员应对零件的数量、厚度、材料进
行认真核对。
每个分段结构生成结束后在图纸上标明哪些结构为电脑下料,并
与手工下料者交代清楚手工下料构件,避免重复下料。
(结构零件生成编程方
法详见HD-船体建造系统-结构子系统使用说明)
1.1.4 零件生成后必须对每一块零件外形尺寸进行复查,把零件转换成CAD图形后调
到分段图中,若该零件与分段图中所画外形吻合,则零件外形尺寸正确。
这样
校对零件的前提是设计部门所画图形的每根线型均是正确的,并且画图时用
1:1来画。
1.1.5 数控套料前先对套料结构进行分类,不同等级板材的结构归类后在套料时输入
正确的板材等级号。
套料原则上先套大的构件,然后套小构件,尽量利用材料。
1.1.6 套料板余料在1㎡以上均应编写余料板号,按板材等级进行余料归类,以便
下次补料或手工下小构件时使用。
余料应由专人管理,由样台统一支配余料,
避免板材流失。
1.1.7 套料零件间隙为7mm,切割起始点为左上角,割缝为3mm。
因板材下端为固定
端,所以在套料时应注意构件排列,一般容易产生变形的构件放在板材上端,
所有构件应尽量往上靠,不要往固定端靠,防止引起大的变形。
1.1.8 在号料中要认真字迹要清晰,对切割中有明显缺陷的要进行修复,割渣毛刺
清除干净。
验收合格后方可进入下道工序。
1.2 手工下料
1.2.1 原则上手工下料的零件为电脑编程不能处理的、以及可用剪刀车剪切的小肘
板。
1.2.2 手工下料各种样板与样台型线偏差:标准范围±1.0
结构放样位置线偏差:标准范围±1.0
允许极限±1.5
结构尺寸偏差:标准范围±1.0
允许极限±1.5
表1:零件划线尺寸偏差表单位:(mm)
1.3 结构余量
1.3.1 外板K行板不放余量,A行板至R转角板下口放30mm,R转角板上下各放30mm,
R转角板至舷侧顶板上口各放余量30mm,各行外板每块端接缝口各一头放余量
30mm,大接缝的长端一边放余量50mm,仅嵌装外板两边板口各放余量30mm。
1.3.2 内部构件如中内龙骨、旁内龙骨、中纵、边舱壁、舷侧纵桁,甲板纵桁等靠大
接缝的长端处的构件放余量50mm。
2、零件运输及堆放
2.1 零件运输及堆放是造成材料流失的关键,每次补料时一查套料图零件已下过,但怎
么找也找不到,往往等补料后或分段造好后才在某个角落里发现。
这样即浪费材料,又延误进度,造成不必要的损失。
2.2 每块钢板的零件切割结束移交给运输人员时均应按套料图进行签收,然后进行分类
堆放,同时按套料图再次核对零件数量。
若为手工下料零件也应进行登记,零件移交给内场加工人员时也要进行登记,发现遗漏应及时反映,及时补料。
每个环节做到清楚明白,所有登记签收资料应有专人保管,以便备查,登记表中应注明材料堆放流向。
(注:素材和资料部分来自网络,供参考。
请预览后才下载,期待你的好评与关注!)。