硫化物的脱除
硫化物脱除工艺

硫化物脱除工艺
工艺概述
硫化物脱除工艺的主要步骤包括:预处理、吸附和再生。
1. 预处理
在吸附之前,首先需要对含有硫化物的物质进行预处理。
这可
以包括去除杂质、调整pH值等操作,以提高后续吸附过程的效果。
2. 吸附
吸附是硫化物脱除工艺的核心步骤。
一种常用的吸附剂是活性炭,它能有效吸附硫化物。
将活性炭投加到含有硫化物的物质中,
经过一定时间的接触,硫化物将被吸附在活性炭上。
3. 再生
吸附剂饱和后,需要进行再生。
再生的过程可以通过多种方法进行,如热解、酸碱洗等。
再生后的吸附剂可以继续用于下一轮吸附,降低成本和资源消耗。
工艺优势
该硫化物脱除工艺具有以下优势:
1. 简单:工艺步骤简单明了,易于操作和控制。
2. 高效:吸附剂能够有效地吸附硫化物,提高去除效率。
3. 可再生:吸附剂可以通过再生过程得到回收和再利用,提高资源利用率。
4. 无法确认的引用:我们不引用未经证实的内容,确保文档的准确性和可信度。
结论
硫化物脱除工艺是一项重要的环保工艺,该工艺通过预处理、吸附和再生步骤,能有效去除硫化物污染物。
该工艺具有简单、高效和可再生的优势,可在实际应用中发挥重要作用。
请注意:以上所述内容仅为概述,具体实施时需根据不同情况进行调整和优化。
浅析天然气脱硫主要方法

浅析天然气脱硫主要方法天然气脱硫是指去除天然气中的硫化物的过程,以达到符合环境和工业要求的气体品质。
硫化物是一类具有强烈刺激性气味和剧毒性的化合物,对人体和环境都有害。
天然气脱硫是天然气处理过程中的一个重要环节。
目前,主要的天然气脱硫方法有以下几种:1. 物理吸附脱硫:物理吸附脱硫是利用多孔吸附材料对天然气中的硫化物进行吸附分离的方法。
常用的吸附材料有活性炭、硅胶、分子筛等。
通过将天然气经过吸附剂床层,硫化物会被吸附剂表面的孔隙陷著,从而实现脱除。
这种方法具有简单、操作方便、适用范围广等优点,但是吸附剂容易受到杂质的污染,需要定期更换吸附剂。
2. 化学吸收脱硫:化学吸收脱硫是利用酸性溶液对天然气中的硫化物进行化学反应,将其转化为易溶于水的化合物,然后从天然气中分离脱除的方法。
常用的吸收剂有氨水和醇胺溶液。
在吸收剂中,硫化物与吸收剂发生反应,生成相应的盐和硫化物,然后通过分离装置分离脱除。
这种方法具有脱硫效果好、适用范围广的特点,但需要使用大量的吸收剂,吸收剂的再生和处理也是一个重要的问题。
3. 生物脱硫:生物脱硫是利用特定的微生物对天然气中的硫化物进行降解和转化的方法。
这些微生物可以利用硫化物作为能源来生长和繁殖。
常用的微生物有厌氧细菌和嗜硫细菌等。
通过将天然气和含有微生物的培养液接触,微生物可以分解和转化硫化物为硫酸盐和硫磺等物质。
生物脱硫方法具有环保、节能等优点,但操作复杂,需要控制培养液的温度、氧气供应、pH值等条件。
天然气脱硫的主要方法包括物理吸附脱硫、化学吸收脱硫、生物脱硫和氧化吸附脱硫。
不同的方法具有不同的优点和适用范围,选择适合的脱硫方法需要考虑天然气的成分、硫化物的含量、处理量、处理效果和成本等因素。
未来,随着技术的进步和环保要求的提高,可能还会出现更多新的天然气脱硫方法。
化学工艺学 合成气中硫化物和二氧化碳的脱除

合成气中硫化物和二氧化碳的脱除1.1合成气中硫化物的脱除在制气时,所用的气、液、固三类原料均含硫化物。
在制气时转化成硫化氢和有机硫气体,它们会使催化剂中毒,腐蚀金属管道和设备,危害很大,必须脱除,并回收利用这些硫资源。
1.1.1硫化物的危害硫化物是制气过程中最常见、最重要的催化剂毒物,极少量硫化物就会使催化剂中毒,使催化剂活性降低直至完全失活。
硫化物主要有硫化氢和有机硫化物,后者在高温和水蒸气、氢气作用下也转变成硫化氢。
用天然气或轻油制气时,为避免蒸汽转化催化剂中毒,已预选将原料彻底脱硫,转化生成的气体中无硫化物。
煤或重质油制气时,氧化过程不用催化剂,不用对原料预脱硫,因此产生的气体中有硫,在下一步加工前必须进行脱脱硫。
1.1.2硫化物脱除的方法分类脱硫方法要根据硫化物的含量、种类和要求的净化度来选定,还要考虑技术条件和经济性,有时可用多种脱硫方法组合来达到对脱硫净化度的要求。
按脱硫剂状态来分,有干法、湿法两大类。
干法脱硫可分为吸附法和催化转化法,湿法脱硫可分为化学吸收法、物理吸收法、物理-化学吸收法和湿式氧化法。
下面主要介绍湿法脱硫中的物理吸收法(NHD)。
1.1.3 NHD脱硫方法湿法脱硫剂为液体,一般用于含硫量高、处理量大的气体的脱硫。
其中物理吸收法是利用有机溶剂在一定压力下进行物理吸收脱硫,然后减压而释放出硫化物气体,溶剂得以再生。
主要有冷甲醇法、此外还有碳酸丙烯酯法、N-甲基吡啶烷酮法、NHD法等,主要介绍NHD法。
1.1.3.1原理及工艺流程NHD溶剂是一种有机溶剂(聚乙二醇二甲醚),它对气体中硫化物和二氧化碳具有较大的溶解能力,尤其是对硫化氢有良好的选择吸收性,NHD溶剂物化性能稳定,蒸气压低,挥发损失小,无气味、无毒、不腐蚀、不分解。
该工艺能耗低、消耗低、成本低,运转时溶剂耗损少,是一种较理想的物理吸收剂,适合于以煤(油)为原料,酸气分压较高的合成气等的气体净化,脱硫时需消耗少量热量,脱碳时需消耗少量冷量,属低能耗的净化方法。
生物质锅炉钠基干法 sds 脱硫技术工艺原理

生物质锅炉钠基干法 sds 脱硫技术工艺原理
生物质锅炉钠基干法SDS脱硫技术工艺原理是利用钠基干法对生物质燃烧过程中产生的硫化物进行脱除的技术。
其主要原理包括以下几个方面:
1. 钠基干法:钠基干法是一种将钠盐与硫化物进行化学反应生成硫醇的方法。
该方法通过在燃烧过程中添加含有钠盐的添加剂,使得硫化物与钠盐反应生成硫醇,从而达到脱硫的效果。
2. 生物质燃烧产生的硫化物:生物质燃烧过程中会产生一些硫化物,如硫化氢、二硫化碳等,这些硫化物对环境和人体健康都具有一定的危害性。
3. 添加剂的选择:钠基干法中所选用的添加剂通常为钠碱或钠盐。
添加剂的选择要根据生物质燃烧过程中产生的硫化物种类和含量来确定。
4. 反应机理:添加钠盐后,钠离子与硫化物发生反应,生成可溶性硫醇。
硫醇可在烟气中通过传质作用而被液相吸收,达到脱硫效果。
总的来说,生物质锅炉钠基干法SDS脱硫技术是通过添加钠盐的方式将燃烧产生的硫化物转化为硫醇,并通过液相吸收的方式从烟气中去除硫化物,达到脱硫的效果。
这种技术具有操作简单、成本低、脱硫效率高等优点,因此在生物质锅炉的脱硫过程中得到了广泛应用。
石油化工脱硫方法

石油化工脱硫方法随着环保和市场对石化产品中硫含量要求越来越苛刻,石油化工中硫化物脱除,尤其是较难脱除的有机硫化物脱除方法已成为各石化企业和研究者关注的热点。
本文就近年来有机硫化物脱除方法的研究进展进行综述,介绍了加氢转化、生物脱除技术、超生婆脱硫、沸石脱硫、液相吸附脱硫、离子液脱硫等,展望了有机硫脱除技术发展远景。
关键词:有机硫;脱除;石油化工随着世界范围环保要求日益严格,人们对石油产品质量要求也越来越苛刻,尤其是对燃烧后形成SO2、SO3继而与大气中水结合形成酸雾、酸雨严重影响生态环境和人们日常生活的硫化物含量限制。
世界各国对燃油中的硫提出了越来越严格的限制,以汽油为例,2005年欧美要求含硫质量分数降低到30×10-6~50×10-6,至2006年,欧洲、德国、日本、美国等国家和地区要求汽油中硫含量低于10~50µg/g,甚至提出生产含硫质量分数为5×10-6~10×10-6的“无硫汽油;”自2005年起,我国供应北京、上海的汽油招待相当于欧洲Ⅲ排放标准的汽油规格,即含硫质量分数低于150×10-6。
为了满足人们对石油产品高质量的要求和维护生产安全稳定进行,石油化工各生产企业不断改进生产过程中的脱硫工气。
石油化工生产过程中涉及到的硫化物可分为无机硫化物和有机硫化物,无机硫化物较容易脱除,本文就比较难脱除的有机硫脱除技术新进展进行综述。
1 加氢转化脱硫天然气、液化气、炼厂气、石脑油及重油中常含有二硫化碳、硫醇、硫醚、羰基硫和噻吩等有机硫化物,热分解温度较高,且不易脱除。
加氢转化脱硫技术是最有效的脱除手段之一。
有机硫在加氢转化催化剂作用下加氢分解生成硫化氢(H2S)和相应的烷烃或芳烃,生成的H2S可由氧化锌等脱硫剂脱除达到很好的脱除效果。
近年来,国外开发出几种典型的催化裂化(FCC)汽油脱硫新工艺,如ExxonMobil公司的SCANFining工艺和OCTGAIN工艺、LFP公司的Prime-G+工艺和UOP公司的ISAL工艺;在中内,中国石化抚顺石油化工研究院(FRIPP)针对我国FCC汽油的不同特点,开发出了OCT-M、FRS和催化裂化(FCC)汽油加氢脱硫/降烯烃技术并在国内石化企业得到成功应用;还开发了FH-DS柴油深度加氢脱硫催化剂,成功应用于福建炼油化工有限公司柴油加氢装置[1,2],此外洛阳石油化工工程公司工程研究院开发出催化裂化汽油加氢脱硫及芳构化工气技术Hydro-GAP[3]。
粗原料气的净化—硫化物的脱除(合成氨生产)

由脱随塔流出的富液,送至脱硫闪蒸槽而后进人H2S提浓塔,塔顶进液 为脱硫贫液,中部进液为脱硫富液。在H2S提浓塔后还有一个闪蒸槽。 闪 蒸气压缩后作为H2S提浓塔的气提气。由H2S提浓塔出来的气体含H2S25% 左右,可直接送至克劳斯法制硫装置。由脱碳闪蒸槽出来的闪蒸气含CO2 99%左右,可作尿素生产原料之用。
本书仅对近年来备受人们关注的Slexol怯(中国称为NHD法)脱硫作简介。此法 1965 年首先由美国Alied Chenical公司采用,至今已有 40多套装置在各国运 行。脱硫剂的主体成分为聚乙二醇二甲醒,商品名为Selexol。它是一种聚乙 二醇二甲醚同系物混合体。分子式为CH3O CH-O- CH2 nCH。 式中n为3-9。 平均相对分子质量为22-242。各种同系物的质量分数,%大致如下。
3、脱硫剂活性好,容易再生,定额消耗低
脱硫剂活性好,容易再生,可以降低生产的费用,符合工业生 产的经济性。
4、不易发生硫堵
硫堵:进脱硫塔气体的成分不好,杂志耗量较高;反应时析出的 硫不能及时排出;脱硫塔淋喷密度不够;再生空气量不足,吹风强度 低等原因造成硫堵。
5、脱硫剂价廉易得
采用最多的是廉价的石灰、石灰石和用石灰质药剂配制的碱性溶 液。以提高生产的经济性。
酞菁钴价格昂贵,但用量很少,脱硫液中PDS含量仅在数十个cm3/ m3左右。PDS的吨氨耗量一般在1.3-2.5g左右,因而运行的经济效益也较 显著。
此法也可脱除部分有机硫。若脱硫液中存在大量的氰化物,仍能导致 PDS中毒,但约经60h靠其自身的排毒作用,其脱硫活性可以逐渐恢复。 PDS对人体无毒,不会发生设备硫堵,无腐蚀性。
再
较高的温度有利于硫磺的分离,使析出的硫易于凝聚,
生
甲醇生产技术第三章脱硫

第三章 脱硫
这几种主要硫化物的性质如下。 1.硫化氢(H2S) 无色气体,有毒,溶于水呈酸性,与碱作用生成盐,可
被碱性溶液脱除,能与某些金属氧化物作用,氧化锌脱
硫就是利用这一性质。 2.硫氧化碳(COS) 无色无味气体,微溶于水,与碱作用缓慢生成不稳定盐, 高温下与水蒸气作用转化为硫化氢与二氧化碳。
四、开停车操作
(二)停车 1.短期停车 2.紧急停车 3.长期停车
四、开停车操作
(三)倒车 ①按正常开车步骤启动备用机,待运转正常后,逐渐关 小其回路阀,提高出口压力,当备用机出口压力与系统
压力相等时,逐渐开启其出口阀;同时开启在用机回路
阀,关闭其出口阀。 ②停在用机,关闭其出口阀。 ③倒车过程中开、关阀门应缓慢、以保证系统气体压力、 流量的稳定。防止抽负或系统压力突然升高及气量波动 。
面上,以便捕集,溢流回收硫磺。
③空气作用同时将溶解在吸收液中二氧化碳吹除出来, 从而提高溶液PH,实际生产1kg硫化氢约需60~ 110m3/(m2·h)空气,再生时间维持在8~12min。
二、湿法脱硫
3.栲胶法工艺流程
图2 —2
湿法脱硫工艺硫程
二、湿法脱硫
(三)其他脱硫法简介 1.ADA法 (1)脱硫塔中的反应
②经常注意罗茨机进出口压力变化,防止罗茨机和高压
机抽负。 ③保持贫液槽和脱硫塔液位正常,防止泵抽空。
三、操作要点
(四)防止带液和跑气 控制冷却塔液位不要过高,以防气体带液,液位不要过 低,以防跑气。
(五)巡回检查
①根据记录报表,按时做好记录。 ②每15min检查一次气柜高度。 ③每15min检查一次系统各点压力和温度。 ④每半小时检查一次各塔液位。
(1)原因
工艺方法——水泥SO2脱除方法
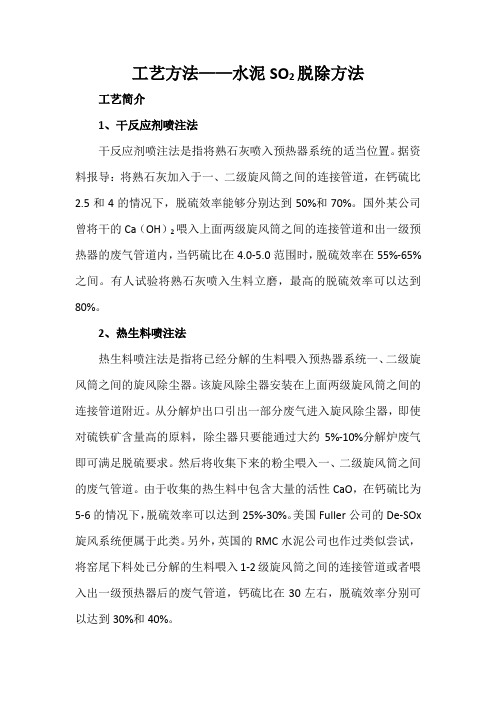
工艺方法——水泥SO2脱除方法工艺简介1、干反应剂喷注法干反应剂喷注法是指将熟石灰喷入预热器系统的适当位置。
据资料报导:将熟石灰加入于一、二级旋风筒之间的连接管道,在钙硫比2.5和4的情况下,脱硫效率能够分别达到50%和70%。
国外某公司曾将干的Ca(OH)2喂入上面两级旋风筒之间的连接管道和出一级预热器的废气管道内,当钙硫比在4.0-5.0范围时,脱硫效率在55%-65%之间。
有人试验将熟石灰喷入生料立磨,最高的脱硫效率可以达到80%。
2、热生料喷注法热生料喷注法是指将已经分解的生料喂入预热器系统一、二级旋风筒之间的旋风除尘器。
该旋风除尘器安装在上面两级旋风筒之间的连接管道附近。
从分解炉出口引出一部分废气进入旋风除尘器,即使对硫铁矿含量高的原料,除尘器只要能通过大约5%-10%分解炉废气即可满足脱硫要求。
然后将收集下来的粉尘喂入一、二级旋风筒之间的废气管道。
由于收集的热生料中包含大量的活性CaO,在钙硫比为5-6的情况下,脱硫效率可以达到25%-30%。
美国Fuller公司的De-SOx 旋风系统便属于此类。
另外,英国的RMC水泥公司也作过类似尝试,将窑尾下料处已分解的生料喂入1-2级旋风筒之间的连接管道或者喂入出一级预热器后的废气管道,钙硫比在30左右,脱硫效率分别可以达到30%和40%。
3、喷雾干燥脱硫法喷雾干燥脱硫法是一种湿法与干法相结合的脱硫方法,石灰消解后形成的浆液由喷雾装置喷入吸收塔,脱硫效率可以达到50%-90%。
RMC公司曾将石灰消解后喷入增湿塔。
增湿塔中喷雾嘴分为两组,一组用来喷入石灰浆液,另一组用来喷入冷却水。
被雾化成细小液滴的脱硫剂与烟气中的SO2发生化学反应,从而脱除烟气中的SO2。
烟气中未反应的石灰颗粒和反应生成物等随烟气带出增湿塔,进入除尘器被收集下来。
该脱硫系统存在两个控制回路,一个用来控制增湿塔出口气体温度,另一个用来控制烟囱SO2的排放浓度。
该脱硫剂浆液中悬浮着很多微细Ca(OH)2颗粒,通常在3-10μm,SO2气体易溶于浆液并与其发生反应。
- 1、下载文档前请自行甄别文档内容的完整性,平台不提供额外的编辑、内容补充、找答案等附加服务。
- 2、"仅部分预览"的文档,不可在线预览部分如存在完整性等问题,可反馈申请退款(可完整预览的文档不适用该条件!)。
- 3、如文档侵犯您的权益,请联系客服反馈,我们会尽快为您处理(人工客服工作时间:9:00-18:30)。
一些定性结论如下:温度上升,硫容增加;空速增加,硫容降低;汽气比上 升,硫容下降。
2.钴(Co)钼(Mo)加氢-氧化锌脱硫 ①钴(Co)钼(Mo)加氢 原理:在 300-400 ℃温度下,采用钴钼加氢脱硫催化剂,使有机硫与氢
湿法脱硫:化学吸收法、物理吸收法和物理化学吸收法。湿法脱硫具有吸收 速率快,生产强度大,脱硫过程连续,溶液易再生,硫磺可回收等特点,适用于 硫化氢含量较高,净化度要求不太高的场合。
(一)概述: 1、优点:(1)脱硫剂是便于输送的液体物料;且再生简单,可循环使用(2) 脱硫剂可以再生并能回收富有价值的化工原料硫磺;(3)湿法脱硫吸收速度快, 硫容大,适合脱除气体中的高硫。 2、分类:化学吸收法、物理吸收法和物理化学吸收法。物理法是利用脱硫 剂对原料气中硫化物的物理溶解作用将其吸收,如低温甲醇法。化学法是利用了 碱性溶液吸收酸性气体的原理吸收硫化氢,如氨水液相催化法。物理化学法是指 脱硫剂对硫化物的吸收既有物理溶解又有化学反应。如环丁砜烷基醇胺法。 3、直接氧化法脱硫:氧化态的催化剂将硫化氢氧化为单质硫,其自身是还
E E lg S H 2S
S H2S
0.059 2
a
2 H
aH2S
E E lg Q H 2Q
Q H2Q
0.059 2
aQ
a
2 H
a H 2Q
E O2
OH
0.401V
当氧化反应达平衡时:
E E (lg lg ) 0.0295 lg S H2S
Q H2Q
0.059 2
a
2 H
1.氧化锌法 氧化锌脱除有机硫的能力很强,可使出口硫含量<0.1ppm,当原料气硫含量 <50×10-6 时,仅用它一步脱硫就行了。若硫含量较高,可先用湿法,再用此 法。其基本原理如下:
ZnO(s)+H2S(g)=ZnS(s)+H2O(g) ZnO(s)+C2H5SH(g)=ZnS(s)+C2H5OH(g) ZnO(s)+ C2H5SH(g)= ZnS(s)+C2H4(g)+H2O(g) 有氢存在,还有下列反应:
2NaHS+4NaVO3+H2O→Na2V4O9+4NaOH+2S C、 氧化态 ADA 与 Na2V4O9 的熟化反应: Na2V4O9+2ADA(氧化态)+2NaOH+H2O →4NaVO3+2ADA(还原态) 以上析硫和熟化反应是在脱硫塔底部和富液槽中同时进的。 D、还原态 ADA 在再生槽中被空气中氧氧化的再生反应:
作者单位:合肥学院化学与材料工程系 关键词:原料气;湿法脱硫;干法脱硫;催化剂 Abstrct: Keywords:
正文:原料气中的硫化物:主要是硫化氢,其次是二硫化碳(CS2)、硫氧化 碳(COS)、硫醇(RSH)、硫醚(RSR’)和噻吩(C4H4S)等有机硫。脱硫的方法: 根据硫化物的含量、种类和要求的净化度、技术条件和经济性,可选用一种或多 种脱硫方法来进行脱硫。按脱硫剂状态来分,有干法、湿法两大类。
0.000025 0.00055 0.005
0.0008 0.018 0.16
400°C 0.009 0.20 1.80
实际上天然气等原料中水蒸气含量很低,所以即使温度在 400℃也可满足 S 含量<0.1× 10-6 的要求。 200℃含水 20%时,S<0.005× 10-6,因此氧化锌 也用在变换工序作变换催化剂的保护剂。
原态。还原态的催化剂在再生时被空气中的氧氧化后恢复氧化能力,如此循环使 用。此过程可表示为:
载氧体(氧化态)+硫化氢=载氧体(还原态)+S↓ 载氧体(还原态)+1/2O2(空气)=载氧体(氧化态)+H2O 4、催化剂的选择 选择适宜的催化剂是湿式氧化法的关键。这种催化剂必须既能氧化硫化氢, 又能被空气中的氧所氧化。 选择原则:(1)必须能满足特定工艺对脱硫要求的净化度。 (2)硫容量大 所谓硫容量(简称硫容)是指脱硫过程中,单位溶液体 积所吸收 H2S 的净值(△S),单位为 mg/L。当脱硫负荷一定时,它与脱硫溶液 量有如下关系:
50℃。
(3)氧化脱硫是指在活性炭表面上吸附的硫化氢在碱性溶液的条件下和气
L
V (gH2S
g' H2S
)/
S
x1000
m3
/
h
式中
V-----气体(标准状况下)流量, m3 / h
;
gH2S
,
g' H2S
---分别为脱
硫塔进口、出口气体(标准状况下)中的硫化物含量, m3 / h 。
由公式可以看出来,硫容值 越大,所需脱硫溶液量越少,脱硫及再生泵的
运转电费也越少。
(3)脱硫剂活性好,容易再生,且消耗定额低。
当氧化反应达平衡时,由文献查得:设再生槽液面的再生剩余氧为原空气中 氧的 3/4。故得 pO2=0.21*3/4=0.0157Mpa,
E O2
OH
0.401V
当脱硫液的
pH=8
时,
E O2
OH
0.401
0.059 4
lg
0.0157 0.101325
0.059 lg1014
0.059pH
E O2
(4)不易发生硫堵。
(5)脱硫剂价廉易得。
(6)无毒性、无污染或污染小。
(二)湿法氧化还原脱硫的原理
在我国中小化肥厂湿法脱硫中,氧化还原法占优势,其中以醌-氢醌型脱硫
剂最普遍。用 Q 代表醌态(氧化态)催化剂,用 H2Q 代表酚态(还原态)催化剂。
H2S 被氧化过程表示为
H2S 2e+2H++S
Q + 2H++2e H2Q
2ADA(还原态)+O2→2ADA(氧化态)+H2O E、可能发生的副反应如下: a.硫氢化钠遇氧会发生过氧化反应生成硫代硫酸钠
b.当气相中存在 CO2 和氰化氢时,也可能发生下列副反应:
(4)工艺条件: A、溶液组成 a.总碱度 是指溶液溶液中 NaHCO3 和 Na2CO3 的含量之和。工业上通
合肥学院
Hefei University
系别 课程名称 专业 班级 姓名 学号
化学与材料工程系 无机化工工艺学 化学工程与工艺 12 级化工
硫化物的脱除
摘要:半水煤气中,因煤的种类不同而含有数量不等的硫化物。这些硫化 物对含合成氨生产有着严重危害,必须首先予以除去,以保证后工段工作顺利进 行。在合成氨生产中,要求经过脱硫后的半水煤气中 H2S 含量在 0.07g.m3(标) 以下,碳化气中 H2S 含量在 0.01g/m3(标)以下。脱硫方法很多,可分为干法和湿 法两大类,其中湿式氧化法脱硫多用于半水煤气和变换气的一次脱硫,而干法脱 硫多用于变换气脱硫和碳化气的精脱硫。
d.ADA 浓度 因为 ADA 有几种不同结构形式,作为脱硫用的 ADA 以 2, 7-ADA 为好。一般 ADA 浓度在 2-6g/L 左右。高压法在 10 g/L 左右。
B、温度。温度高对硫化氢的吸收不利但可加速脱硫反应速度,对还原 态 ADA 的氧化再生有利。如温度大于 60℃时,溶液中硫代硫酸钠的生成量将剧 增,而且此时硫泡沫易破裂形成悬浮硫,有可能诱发“硫堵”。工业上一般脱硫 塔的操作温度以低于 40℃为宜。再生槽温度不超过 45℃为宜。
工艺条件:操作条件,温度一般在 300~400℃,压力 0.7~7.0MPa,入 口气空间速度为 500~2000h-1,液态烃空速 0.5-6h-1,加氢量一般按照保持反 应后气体中有 5~10%氢为准。
3.活性炭法脱硫 1.基本原理 活性炭常用于脱除天然气、油田气以及经湿法脱硫后,气体中的微量硫。根 据反应机理不同可分为吸附、氧化和催化三种方式。
反应生产容易脱除的硫化氢和烃。再用氧化锌吸收硫化氢,即可达到较好的 脱硫效果。
反应:RSH+H2=RH+H2S RSR’+2H2=RH+R’H+ H2S COS+H2=CO+H2S CS2+4H2=CH4+2H2S
钴钼加氢法还可将烯烃加氢转变成饱和烷烃,从而减少蒸汽转化工序析 碳的可能。
催化剂:以氧化铝(Al2O3)为载体,由氧化钴(CoO)和氧化钼(MoO3)组成。 Mo 含量为 5~13%,Co 含量为 1~6%。经硫化后的活性组分主要为 MoS2,Co9S8 防止 MoS2 微晶聚集长大。
b. pH 值 pH 值上升,对吸收硫化氢有利,但对转化成单质硫不利。且 pH 过大,再生困难,溶液粘度增加,动力消耗增大。为操作稳定,吸收剂一般 应选择 PH=8.5~9.2 左右的碱性缓冲溶液。
c.钒酸盐含量 钒酸盐的用量与多种因素有关,一般应使 ADA 与偏钒酸 盐的比为 1 比 1.3 左右。钒酸盐通常以钒酸铵、钒酸钠或偏钒酸钠的形式加入。
C、压力 加压和常压均可,取决于流程其它工序对压力的要求。 D、再生空气用量和再生时间 满足 ADA 需要且使硫呈泡沫状悬浮以 便回收。一般持续时间在半小时时左右。
干法脱硫:氧化铁法、活性炭法、钴—钼加氢和氧化锌法等。干法脱硫具有 脱硫效率高、操作简便、设备简单、维修方便等优点。但干法脱硫所用脱硫剂的 硫容量(单位质量或体积的脱硫剂所能脱除硫的最大数量)有限,且再生较困难, 需定期更换脱硫剂,劳动强度较大。干法脱硫一般适用于含 S 量较低、净化度要 来较高的情况。
(1)吸附脱硫是由于活性炭具有很大的比表面积,对某些物质具有较强的
吸附能力。如吸附有机硫中的噻吩很有效,而对挥发性大的硫氧化碳的吸附很差;
对原料气中二氧化碳和氨的吸附强、而对挥发性大的氧和氢吸附较差。