生产管理流程
生产管理流程

生产管理流程一、前言生产管理是现代企业管理的核心之一。
它是指将企业的生产活动有序地组织起来,通过不断提高生产效率和质量水平,实现企业的竞争优势。
本文将围绕着生产管理的流程展开阐述,包括生产计划、采购管理、生产调度、生产控制和成品检验等环节。
希望本文能够为广大企业提供一些有益的参考。
二、生产计划生产计划是生产管理的第一步,也是最重要的一步。
它是指根据市场需求和生产能力,合理安排生产计划,明确生产目标。
一般来说,生产计划的制定需要遵循以下原则:1.充分了解市场需求和生产条件,明确生产目标。
2.合理安排生产计划,确保生产的连续性和稳定性。
3.合理配备生产资源,确保生产能力的满足。
生产计划的制定与实施需要多个部门协同合作,主要包括以下环节:1.销售部门提供市场需求信息,并制定销售计划。
2.生产部门据此确定生产计划。
3.采购部门负责采购所需原材料,并做好库存管理。
4.质量部门负责进行质量监管,确保产品符合规定标准。
5.人力资源部门负责招聘和管理生产工人,确保生产力量的稳定性。
三、采购管理采购管理是生产管理中的一个关键环节。
它是指通过合理的采购计划,从可靠的供应商处获取原材料、设备和服务等物资,确保生产能力的满足。
例如,一个制造汽车轮毂的企业在采购时需要注意以下事项:1.选择优质的原材料供应商,并与其建立长期的合作关系。
2.与供应商签订正式合同,明确交货期、价格和质量要求等内容。
3.定期检查供应商的生产能力和交货情况,确保原材料的稳定供应。
四、生产调度生产调度是指将生产计划和生产能力有效地结合起来,合理分配生产任务,达到生产效率和质量水平的最优化。
例如,在一个跑鞋制造企业中,生产调度主要包括以下几个过程:1.根据生产计划和订单要求,确定各生产环节的生产任务和工时配额。
2.根据生产车间的工人数量和特点,分配具体的生产任务。
3.及时发现和解决生产中出现的问题,确保生产进度和质量。
五、生产控制生产控制是指对生产过程进行有效监控和管理,确保生产的正常进行和高质量的产品输出。
生产管理的流程范文

生产管理的流程范文生产管理是指对生产活动进行组织、计划、协调、控制并进行决策的管理活动,其目的是实现高效率、高质量的生产过程。
下面将介绍生产管理的一般流程,包括生产计划、生产调度、生产控制和生产评估等环节。
一、生产计划生产计划是生产管理的第一步,它是根据市场需求和公司资源状况制定的指导生产活动的计划。
生产计划的主要内容包括产品的种类、数量、质量要求及交货期限等。
生产计划的编制需要综合考虑市场需求、原材料的供应情况、设备的利用率和人力资源等因素,确定合理的生产目标。
生产计划的具体过程包括:1.市场调研:了解市场需求情况,包括产品需求量、季节性需求变化等。
2.生产能力评估:评估企业的生产能力,包括设备利用率、劳动力配备情况等。
3.产品策划:根据市场需求和生产能力,确定产品的种类、规格和质量要求。
4.生产计划编制:制定具体的生产计划,包括产品数量、交货期限和生产工艺等。
6.生产计划发布:将生产计划发布给相关部门和生产人员,供其参考和执行。
二、生产调度生产调度是根据生产计划,合理安排生产资源和生产活动的过程。
生产调度的主要任务是协调各部门之间的工作,保证生产活动的有序进行。
生产调度的主要内容包括生产资源的调配、生产任务的分解和生产进度的控制等。
生产调度的具体过程包括:1.生产资源调配:根据生产计划,合理安排生产资源的分配,包括设备、人力和原材料等。
2.生产任务分解:将生产计划拆解成具体的生产任务,分配给各个生产车间或工作组。
3.生产进度控制:监控生产活动的进度,及时发现并解决生产过程中的问题,确保按时完成生产任务。
4.生产报表编制:收集和整理生产过程中的各类数据,并编制相应的生产报表,为生产评估提供依据。
三、生产控制生产控制是通过有效的控制手段,对生产活动进行监控和管理的过程。
生产控制的主要任务是确保生产过程的高效率和高质量。
生产控制的内容包括生产现场管理、质量控制和成本控制等。
生产控制的具体过程包括:1.生产现场管理:指对生产现场进行管理,包括设备维护、工作环境管理和安全生产等。
公司生产管理流程

公司生产管理流程公司生产管理流程是指在生产过程中,通过合理的规划、组织、指导和控制等功能,实现对生产活动的有效管理,确保生产任务按时按质完成,提高生产效率和产品质量。
生产管理流程的设计和执行对于一个企业的生产效率和竞争力具有重要意义。
下面将详细介绍公司生产管理流程的主要内容和步骤:一、生产计划阶段1.确定生产目标和需求:根据市场需求和销售计划,确定具体的生产目标和需求,包括生产数量、生产周期等。
2.编制生产计划:根据生产目标和需求,制定具体的生产计划,包括生产任务分配、生产进度计划等。
3.调度生产资源:确定生产所需的人力、物资、设备等资源,合理调度和安排生产任务,确保资源的充分利用。
二、生产执行阶段1.生产准备工作:进行生产前的准备工作,包括设备检查、材料准备、人员培训等,确保生产顺利进行。
2.执行生产计划:按照生产计划的要求,组织生产活动,指导员工进行生产操作,确保生产任务按时完成。
3.监控生产过程:通过监控生产现场和生产数据,及时掌握生产情况,发现和解决生产过程中的问题,确保生产进度和质量符合要求。
三、生产控制阶段1.生产进度控制:及时调整生产计划和资源,确保生产进度得以控制,避免产能浪费和交货延误。
2.质量控制:通过质量检测和质量管理,控制产品的质量,提高产品合格率和客户满意度。
3.成本控制:通过成本核算和成本分析,控制生产成本,提高生产效益和利润水平。
四、生产总结阶段1.生产数据分析:对生产过程和结果进行数据分析,了解产能利用率、生产效率、成本效益等指标,为生产管理提供依据。
2.总结经验教训:总结生产过程中的经验教训,发现问题和改进空间,提高生产管理水平和工作效率。
3.改进优化措施:根据总结分析的结果,制定改进优化措施,优化生产流程和方法,提高生产效率和产品质量。
综上所述,公司生产管理流程是一个系统的管理体系,需要全员参与和协作,涉及生产计划、生产执行、生产控制和生产总结等多个环节。
只有不断优化和改进生产管理流程,才能提高生产效率和产品质量,增强企业的竞争力和市场地位。
生产管理流程
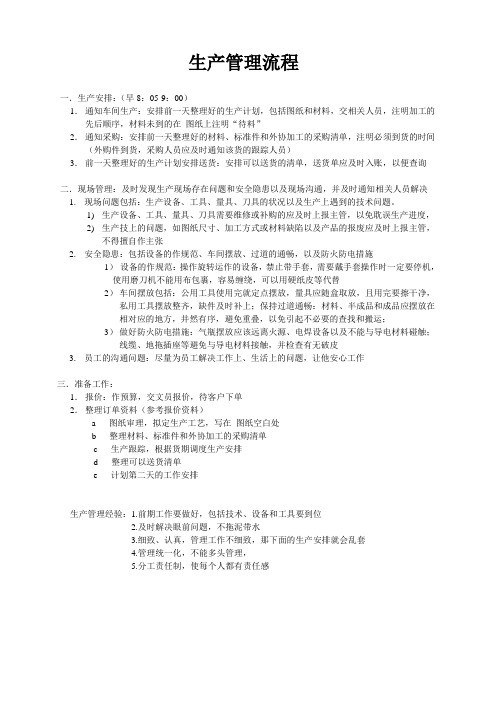
生产管理流程一.生产安排:(早8:05-9:00)1.通知车间生产:安排前一天整理好的生产计划,包括图纸和材料,交相关人员,注明加工的先后顺序,材料未到的在图纸上注明“待料”2.通知采购:安排前一天整理好的材料、标准件和外协加工的采购清单,注明必须到货的时间(外购件到货,采购人员应及时通知该货的跟踪人员)3.前一天整理好的生产计划安排送货:安排可以送货的清单,送货单应及时入账,以便查询二.现场管理:及时发现生产现场存在问题和安全隐患以及现场沟通,并及时通知相关人员解决1.现场问题包括:生产设备、工具、量具、刀具的状况以及生产上遇到的技术问题。
1)生产设备、工具、量具、刀具需要维修或补购的应及时上报主管,以免耽误生产进度,2)生产技上的问题,如图纸尺寸、加工方式或材料缺陷以及产品的报废应及时上报主管,不得擅自作主张2.安全隐患:包括设备的作规范、车间摆放、过道的通畅,以及防火防电措施1)设备的作规范:操作旋转运作的设备,禁止带手套,需要戴手套操作时一定要停机,使用磨刀机不能用布包裹,容易缠绕,可以用硬纸皮等代替2)车间摆放包括:公用工具使用完就定点摆放,量具应随盒取放,且用完要擦干净,私用工具摆放整齐,缺件及时补上;保持过道通畅:材料、半成品和成品应摆放在相对应的地方,井然有序,避免重叠,以免引起不必要的查找和搬运;3)做好防火防电措施:气瓶摆放应该远离火源、电焊设备以及不能与导电材料碰触;线缆、地拖插座等避免与导电材料接触,并检查有无破皮3.员工的沟通问题:尽量为员工解决工作上、生活上的问题,让他安心工作三.准备工作:1.报价:作预算,交文员报价,待客户下单2.整理订单资料(参考报价资料)a 图纸审理,拟定生产工艺,写在图纸空白处b 整理材料、标准件和外协加工的采购清单c 生产跟踪,根据货期调度生产安排d 整理可以送货清单e 计划第二天的工作安排生产管理经验:1.前期工作要做好,包括技术、设备和工具要到位2.及时解决眼前问题,不拖泥带水3.细致、认真,管理工作不细致,那下面的生产安排就会乱套4.管理统一化,不能多头管理,5.分工责任制,使每个人都有责任感。
生产管理流程

生产管理流程1 生产管理流程生产管理流程是企业开展生产经营活动的基础性工作,是企业生产管理活动的核心要素,涉及到企业中多个部门。
很多生产企业都会根据自身的特性,比如产品类别、品质要求、客户期望及公司整体发展等,量身订做不同的生产管理流程,以确保企业的生产基础系统的有序、高效的运行。
1.1 生产管理流程体系企业的生产管理流程可以归结为五大基本流程:计划、发料、制造、检验和质量控制。
第一步是计划,即企业制定年度或季度的生产目标、订单、产出量及其他生产要素。
第二步是发料,指企业为满足生产需求而发放原料、零件、半成品、设备等。
第三步是制造,指企业按照预期的标准和工艺进行产品生产。
第四步是检验,指检查预期质量的过程。
也就是生产过程中,企业的检查人员会对已生产的产品进行全面的检验,从而确定产品是否符合质量要求。
最后一步是质量控制,指企业运用管理技术实施质量控制,以确保产品质量持续满足质量标准。
1.2 生产管理流程落实企业要实施好生产管理流程,首先要制定生产管理操作规范,分层明确每一项任务就任权利和责任,建立有力的监督机制和考核激励机制,提高企业的质量控制能力;其次要把握生产的节拍,认清行业发展趋势,及时根据市场需求和成本变化调整生产管理流程;再次是建立信息化管理平台,运用ERP、MRP等管理信息系统,以及智能管控系统,充分实现信息化管理,从而控制产品的质量和数量,实现企业各部门间的协调与比配等。
做好生产管理流程,对于企业的发展有非常重要的作用,它关系到企业质量的稳定性、风险的防范性以及成本的控制等,是保障企业正常运行的重要因素。
因此,企业应当认真落实生产管理流程,用有效的方式管理生产,及时调整生产计划,促进企业效率提高及实现有效的目标管理。
工厂生产管理流程
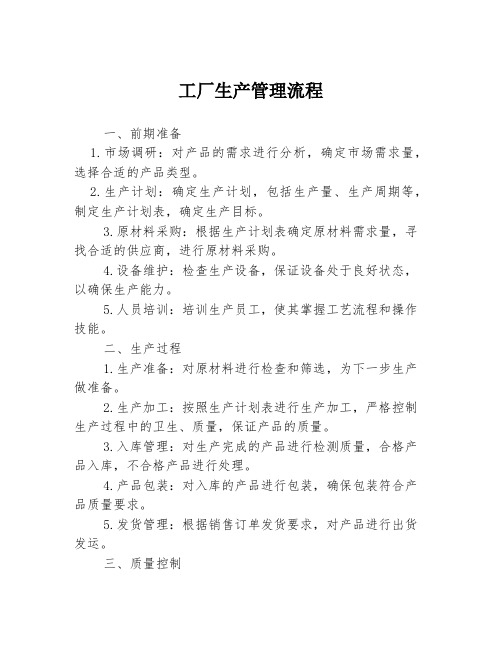
工厂生产管理流程一、前期准备1.市场调研:对产品的需求进行分析,确定市场需求量,选择合适的产品类型。
2.生产计划:确定生产计划,包括生产量、生产周期等,制定生产计划表,确定生产目标。
3.原材料采购:根据生产计划表确定原材料需求量,寻找合适的供应商,进行原材料采购。
4.设备维护:检查生产设备,保证设备处于良好状态,以确保生产能力。
5.人员培训:培训生产员工,使其掌握工艺流程和操作技能。
二、生产过程1.生产准备:对原材料进行检查和筛选,为下一步生产做准备。
2.生产加工:按照生产计划表进行生产加工,严格控制生产过程中的卫生、质量,保证产品的质量。
3.入库管理:对生产完成的产品进行检测质量,合格产品入库,不合格产品进行处理。
4.产品包装:对入库的产品进行包装,确保包装符合产品质量要求。
5.发货管理:根据销售订单发货要求,对产品进行出货发运。
三、质量控制1.质检管理:对生产环节进行检测,控制质量,并根据生产情况及时调整生产过程。
2.损耗管理:对生产过程中的物料、人力和设备进行计算,控制损耗。
3.客户服务:对销售订单进行跟踪,并及时反馈客户反馈信息,对生产过程中出现的问题进行改进和调整。
四、成本控制1.成本分析:对生产环节中的费用进行分析和统计,寻找成本控制的方式和方法。
2.设备使用效率:优化生产过程,提高设备使用效率,提高生产效率。
3.减少不良品率:控制生产过程原材料、工艺等,减少成品不良率,降低成本。
五、信息化管理1.数据分析:对生产环节的数据进行分析,寻找生产过程中的瓶颈,优化生产环节。
2.追踪监控:利用信息化手段,对生产环节中的生产进程进行追踪监控,快速解决生产过程中出现的问题。
3.生产调度:利用信息化管理对生产计划表进行管理,实现生产调度的自动化。
六、安全管理1.生产安全:保证生产过程中人员和设备的安全,严格执行安全规定,预防和控制生产事故的发生。
2.环境保护:保护生产环境,控制工业废水、废气、废渣等排放量,减少对环境的影响。
生产管理流程及制度
生产管理流程及制度生产管理流程及制度是指在企业的生产过程中,为了更加规范化、标准化和科学化的管理生产流程和制定规范的管理制度,以便提高生产效率和质量,并保证产品生产符合相应的标准和规范。
在这个文档中,我们将详细介绍生产管理流程及制度,以及如何实施这些制度。
一、生产管理流程生产管理流程是整个生产过程中,从原材料采集到成品交付期间需要经过的步骤和程序。
生产管理流程可以分为以下几个环节:1、原材料采购:原材料是整个生产过程中最基本的元素,采购原材料的过程需要经过核实供应商、把发票与订单核对、货物检验、及时入库等环节,保证材料的质量和数量是符合标准的。
2、物料备货:根据订单需求,及时准确地准备好所需的物料,让生产过程不间断。
3、生产制造:从原材料投入到成品的生产加工,需要遵守相关的程序和规范,以确保生产过程的良性运作。
4、品质保证:在生产制造的过程中,不可避免地会出现品质问题,如何避免或尽量减少缺陷产生,确保合格率100%,并确保产品经过了严格的检测,符合标准要求。
5、生产过程监控:监控整个生产过程并实施相应的调整6、包装、存储、发货:保证产品在生产过程中的安全存储、恰当包装,也须确保产品按时、完好无损地发货到客户手中。
二、生产管理制度生产管理制度是企业组织和管理生产过程中必须遵循及执行的规则和标准。
一个不完善的生产管理制度会影响企业的生产效率,客户满意度,同时也会降低企业在市场中的竞争力。
生产管理制度通常包括如下几个方面:1、工艺流程和产品标准:从采购原材料到成功交付过程中,工艺流程必须严格遵照制定的标准和质量控制方案进行。
2、质量标准与质量保证:规范不同环节需要遵守的质量标准、品质保证和管理要求。
3、生产设备与安全保障:安全生产、生产环境卫生、消防、急救等方面的设备与保障措施。
4、人员管理与培训:合适的人员管理方案和培训计划,确保生产环节中人员配备足够、素质和技术能力符合生产要求。
5、生产资源与耗材管理:如何活用自身生产资源,降低内部生产成本,保证生产的效益。
企业生产管理流程
企业生产管理流程一、市场需求分析与订单确认企业首先需要进行市场需求分析,了解市场对产品的需求情况。
根据市场需求情况,企业进行产品定价、品种规划等决策,并与客户进行沟通,确认订单情况。
二、生产计划编制根据订单情况和生产能力,企业编制生产计划。
生产计划包括产品的生产数量、生产时间、生产线安排等内容。
同时,还需要制定原材料采购计划和生产设备调度计划。
三、原材料采购与供应链管理根据生产计划,企业进行原材料的采购。
通过供应链管理,确保原材料供应的准时和稳定,避免因原材料短缺导致生产计划延误。
四、生产调度与设备管理企业根据生产计划和订单情况进行生产调度。
通过合理安排生产设备的使用,调整生产顺序,提高生产效率,并确保设备运转的正常和稳定。
五、生产过程控制与质量管理企业在生产过程中需要进行生产过程控制和质量管理。
通过制定生产标准和工艺流程,监控生产过程中的关键环节,保证产品质量符合要求。
六、成品包装与仓储物流完成生产的产品需要进行包装,确保产品的安全运输和储存。
同时,还需要进行仓储物流管理,确保产品的库存充足,避免缺货和积压。
七、销售配送与售后服务完成产品包装后,企业需要进行销售配送。
通过与销售渠道的沟通,安排产品的销售和配送工作。
同时,还需要提供售后服务,解决客户在使用产品过程中的问题。
八、生产数据分析与改进措施企业需要对生产过程进行数据统计和分析,评估生产过程的效率和质量水平,发现存在的问题和改进的空间。
根据分析结果,制定相应的改进措施,优化生产管理流程。
九、员工培训与绩效评估企业需要对生产管理人员进行培训,提高他们的管理水平和专业技能。
同时,还需要进行员工的绩效评估,根据评估结果进行激励和奖惩,提高员工的工作积极性和生产效率。
十、环境保护与安全管理企业在进行生产管理过程中需要注意环境保护和安全管理。
通过合理的资源利用和废物处理,减少对环境的负面影响。
同时,还需要加强安全管理,确保生产过程中不发生事故和安全事故。
生产管理流程
生产管理流程生产管理流程是企业内部对于生产过程进行组织和控制的一套规范化管理方法。
它涉及到从原材料采购到成品出厂的整个流程,旨在优化生产效率、提高产品质量,并确保生产与市场需求的高度匹配。
在这篇文章中,我们将详细探讨生产管理流程。
一、生产计划生产计划是生产管理的起点,它根据市场需求和企业资源状况,制定一份合理的生产计划。
首先,企业需要对市场需求进行调研和分析,了解产品的需求量、种类和时间安排。
然后,结合企业内部的产能和资源情况,制定出生产计划。
这个计划一般包括原材料采购计划、生产线排产计划、设备维护计划等。
二、原材料采购一旦生产计划制定好,企业就需要开始采购原材料。
原材料采购是保证生产正常进行的重要环节之一。
企业需要根据生产计划中的原材料需求量,进行供应商的选择和谈判。
同时,还需要制定一套完善的采购流程,包括采购申请、审批、合同签订、物流安排等。
通过合理的采购安排,企业可以确保原材料的及时供应和优质品质。
三、生产准备在原材料到达企业后,就需要进行生产准备工作。
生产准备包括设备准备、生产线调试、员工培训等。
首先,企业需要确保生产所需的设备能够正常运行。
这包括设备的检修、维护和更换等工作。
其次,生产线的调试也是必不可少的,以确保产品的质量和生产效率。
最后,对员工进行培训,使其了解生产过程和操作注意事项,提高工作效率和质量。
四、生产控制生产控制是生产管理流程中的核心环节,旨在确保生产按照计划进行,并且达到预期的质量标准。
在生产控制中,企业需要精确监控生产过程中各个环节的进展情况。
这包括设备的运行状态、原材料的投放、产出品质的检查等。
如果发现任何异常情况,企业需要立即采取措施进行调整和修正,以确保生产的顺利进行。
五、质量控制质量控制是生产管理流程中不可或缺的一环。
企业需要制定一套完善的质量控制流程,包括原材料的检验、生产过程的监控和成品的抽样检测。
通过严格的质量控制,企业可以减少不良品的产生,提高产品的合格率,并且降低产品召回和质量问题带来的损失。
生产管理流程
●一.工作流程:接受业务订单→生产负荷分析→生产制造令→备料→产前送样→物料发放及领用→生产、外协作业→生产、外协进度追踪→生产、外协作业变更→生产数据分析及计划达成率统计→产品入库→出货●二、生产部接到业务订单后,进行生产负荷分析,根据产能状态及订单数量、交期,决定是否需要加班生产或委外加工。
●三.根据业务订单制定《生产制造单》并发各部门、车间。
●四.根据库存材料情形,填写《材料申购单》经上级领导批准后,再交给采购部。
●五.根据订单交期和设备产能,制定月生产计划及周生产排程。
●六.根据估计消耗备料,原则上,按订单数量90%备料,完成后据实补足余额,以减少库存品。
●七、经客户或业务部肯定产前样后,再进行批量生产。
●八、物料的发放要做到先到先出,按单发放,不能逾额发放。
●九、调查并记录各车间每天完成的数量及积存完成的数量,以了解生产进度情形并加以控制(逐日实际产量与估计产量比照)。
●十、找出实际进度与计划进度产生差异的原因,并采取相应措施。
●十一、显现人员、设备有工作负荷过量、过少或负荷不均之情形,超负荷时,可调其他部门或车间人员或设备支援;负荷不足时,适当增加其工作量,减少浪费。
●十二、检查并督促各工序作业人员根据《作业指导书》及《安全操作规程》从事作业。
●十三、协助品管部门做好在制品质量检测,对不良品及时处理,并采取适当措施保证后续在制品质量。
●十四、因客户变更订单内容或因生产非常造成生产作业更换,应及时调剂生产计划。
●十五、根据生产进度及生产日报表掌控逐日生产之进度、效益及品质,做好生产数据分析及计划达成率统计。
●十六、委外加工作业流程1. 根据需委外加工产品的数量、质量等要求寻觅良好的加工厂商。
2. 厂商经评定合格后,方可签订《托付加工合同》。
其上必须写明:品名加工数量、规格、质量要求、金额、交期、包装方式、运输方式、结算方式、违约责任等内容。
3. 《托付加工合同》必须经公司领导审核签名方有效。
- 1、下载文档前请自行甄别文档内容的完整性,平台不提供额外的编辑、内容补充、找答案等附加服务。
- 2、"仅部分预览"的文档,不可在线预览部分如存在完整性等问题,可反馈申请退款(可完整预览的文档不适用该条件!)。
- 3、如文档侵犯您的权益,请联系客服反馈,我们会尽快为您处理(人工客服工作时间:9:00-18:30)。
生产管理流程1、联合车间熔化控制点2、联合车间锡槽控制点3、联合车间退火控制点4、联合横切质量控制点5、联合采装班质量控制点原料车间质量控制点1. 运输控制:1.1车体及车斗必须清理干净,以防止有杂质混入其中;1.2拉料换料时必须将车体残料都清理干净,以防止原料之间的参杂; 1.3拉料点必须准确,倒料位置不能出现错误;1.4运输途中必须防止雨淋,以免导致原料结块或水分不均匀。
2. 粒度控制:对进堆场或倒料口的各个原料,必须先进行粒度检查,对不合格的料予以 退回处理。
原料名称 粒度要求 硅砂 20目全通过 白云石 8目全通过 长石 24目全通过 石灰石 8目全通过 纯碱 无结块,8目全通过 芒硝无结块,8目全通过1、 原料工艺流程硅 砂: 汽车运输 白云石:汽车运输长 石: 汽车运输 石灰石:汽车运输纯 碱: 汽车运输 芒 硝: 汽车运输 碎玻璃: 汽车运输卜堆场 *堆场•斗提•吊篮 —> 堆场 一k 倒料口 一 斗提 一振动筛 一 >堆场*振动筛 料仓 料仓 料仓 料仓 料仓 料仓 ►倒料口窑头料仓呻 2、 原料车间质量控制点:>斗提混合吗 称量*料仓 4称量3. 堆场质量控制:3.1 堆场必须清扫干净,对有可能引入水泥等杂质的墙体和地面要进行铺钢板处理;3.2 要保证各个原料的准确堆放,严防原料之间的混放;3.3 对个种原料要做到先放先检验先进库,并做好各个原料进厂时间,名称等备注;3.4 对来不及进库的料要进行掩盖,防止料的飞散或参杂。
4. 斗提及各镏子4.1 在各个原料入库前必须检查斗提是否处于能正常运行状态,要检查是否掉斗子,是否跑偏等其它机械故障等;4.2 斗提地坑无积水,无积料;4.3 各下料镏子要保证耐磨材料的完整,无脱落,无堵塞现象;4.4 在打料过程中要保证入库的准确性,各分料器指向是否到位,是否漏料等;4.5 在纯碱和白云石更换入库前要保证斗提和除尘都清理干净,准确入库;5. 石灰石、长石、芒硝入库系统5.1 进料前要对堆场和吊篮清理干净;5.2 进料时要做到不交替吊料;5.3 每进完一种料要对堆场、库顶、吊篮清理干净,并对各个份库进行封盖。
6. 碎玻璃系统6.1 检查碎玻璃堆场是否有杂质混入碎玻璃中;6.2 对碎玻璃运输车辆进行清扫,以保证无杂质混入;6.3 严禁外来碎玻璃入库;三. 岗位操作控制点1. 加工班1.1 要严格按照《原料车间加工系统操作规程》及《原料车间加工系统安全操作规程》操作;1.2 把好各个原料准确进堆场或倒料口关口,做到不错料,不混料;1.3 打料前要仔细检查相关设备的运行情况,有无清理干净,有无堵料,有无人员在检修等;1.4打料过程中要每隔15分钟检查斗提的运行情况,载料情况,时刻监视电机电流情况;1.5硅砂进库时每隔15分钟清理除铁器一次,同时检查下料镏子是否有堵料现象;1.6打纯碱时,每隔15分钟要检查一次筛网,出现断丝或破损要及时停车更换,同时对筛上物要及时清理装袋,每周要对振动筛筛网更换一次;1.7做好岗位的巡视工作,每天对设备的巡视次数不能低于10次,发现问题要及时上报;1.8严格控制各个原料库存量,下班前要保证库存量为:1.9及时清理堆场及操作间的卫生和杂物,保持环境的干净整洁。
2称量系统2.1要严格按照《原料车间称量系统技术操作规程》及《原料车间称量系统安全操作规程》操作;2.2各种原料的干基量配方必须根据中心化验室提供的《配料单》进行设定,任何人不得随意变更。
2.3配合料准确性的控制:要求称量工每班开车配料前对2#秤和3#秤进行开门清理,以保证秤斗里无粘料,并对每个秤用8个砝码进行校秤,如超出允许误差范围,则检查软连接是否积料过多;给料机是否碰到秤斗或其他设备;传感器数据是否正确;秤斗挂钩是否正常;经再次校秤后还没有达到要求,必须重新标定。
校秤时各秤的误差范围为:2#秤(石灰石、长石、芒硝)土0.1kg、3#秤(白云石、纯碱)± 0.2kg、4#秤(硅砂)± 0.2kg、5#秤(碎玻璃)土0.5kg。
2.4称量配料前,要求称量工对料单、PLC数据进行校对,二者数据必须一致。
2.5 化验室需要更改原料水分,填写配料卡,称量房及时更改配料数据和加水量。
2.6 配料时,称量工应密切注意各原料的加料情况,及时调整喂料速度,发现超差严重的原料,称量工须立即进行配料暂停,对超出量进行处理。
各原料的超差允许范围为:硅砂v 2公斤,白云石v 1公斤,石灰石v 0.3公斤, 长石v 0.3公斤,纯碱v 1公斤,芒硝v 0.1公斤,对2#车秤如果芒硝或长石超差太多,则该秤的料做废料处理。
2.7 要严格执行配合料的排料顺序(放料顺序为:4#秤---3# 秤---2# 秤---5#秤)。
排料时须严格按照各秤的延时时序进行排料,以保证原料均匀覆盖,无拖尾现象。
严禁打手动,如用手动必须经车间领导同意,并有技术员在场。
2.8 每班交班前要对每个秤斗进行清理,防止秤斗和软连接粘料,同时搞好岗位卫生以待接班检查。
3. 混合系统3.1 要严格按照《原料车间混合系统操作规程》及《原料车间混合系统安全操作规程》操作;3.2 配合料水份的控制:配合料的水份对配合料的均匀度、原料熔化质量、窑内的粉尘量有较大影响。
应严格控制在 3.5%-4.0%之间(随季节变化,及时调整)。
3.4 配合料温度的控制:料温指的是配合料的温度。
合理的控制配合料的温度可以提高原料熔化的质量、降低油耗、避免纯碱和芒硝因温度低生成结晶水使配合料形成料蛋。
配合料的料温控制在43C--46 C,以加水温度和量来控制料温和配合料水分,同时在气温比较低的时候适量加入一定时间的蒸汽以提高料温。
3.5 配合料均匀度的控制。
均匀度是指对混合料中碳酸钠、碳酸钙、碳酸镁、硫酸钠、酸不溶物等含量分布的均匀性。
均匀度是玻璃生产的一个重要因素,主要以碳酸钠含量的均方差来判断配合料的均匀性,要求均方差小于0.30 。
(取样不低于20个)3.5.1 称量房配料时须严格按照配料要求配料,排料时要求保证纯碱均匀覆盖于其他原料的表面。
3.5.2 混合房要保证混合时间,干混115秒,湿混95秒,每班配完料后,及时排废,并按要求定时清理混合机,定期倒机,及时调试好备用混合机以便能随时倒机。
3.6 混合机的操作执行《原料车间混合技术操作规程》4. 化验:凡进厂原料和厂内原料,应按五点取样法采集样品。
4.1 原料化验室负责对各种原料水份的测定:硅砂每班测4次;纯碱每班2 次;长石每班测 2 次;石灰石,白云石,芒硝每班一次。
对同班次同种原料所测得水分波动较大时要适当多测并上报给车间领导,如超出水份允许波动范围,必须立即修改小料单并通知称量房进行相应数据的更改。
各原料水份允许波动范围:硅砂± 0.3 %白云石± 0.2 %石灰石± 0.2 %纯碱± 0.2%长石粉± 0.2%芒硝± 0.2 %。
4.2 原料化验室负责对配合料水份的测定:化验当班人员每班对配合料测2 次水份,目标值± 0.5 %,发现异常立即通知车间工艺员以上人员,及时调整。
4.3 中心化验室每半个月对配合料做一次半分析和全分析,并做好记录,发现问题立即汇报车间工艺员以上人员。
4.4 配合料均匀度的控制:均匀度是指对混合料中碳酸钠、碳酸钙、碳酸镁、硫酸钠、酸不溶物等含量分布均匀性。
均匀度是玻璃生产的一个重要因素,主要以碳酸钠含量的均方差来判断配合料的均匀性,要求均方差小于0.30 。
要求每两周一次对均匀度进行全分析化验。
平时每班测两次碱含量,目标值±0.7 %,超范围立即通知车间技术员及主任。
4.5 配合料中各原料超细粉的控制:化验室每星期对各种原料的超细粉含量作一次分析,并作好记录。
发现严重超范围现象,须及时通知车间领导,查找原因。
4.6 水分及配合料均匀度检验的方法按《原料车间化验站检验操作规程》执行。
三、燃气车间工艺质量控制点放空t空气—►空压机一►预冷机一►纯化器—►分馏塔一►氮气循环水I富氧气汽化器tl I ”液氨 i 大罐i 中罐* # 分解炉净化炉联合车间0#油罐—卸油泵—油罐—油过滤器—供油泵—加热器燃气车间质量控制点1空压机1.1大气中的空气经过空气过滤器其灰尘等杂质后,在空压机中被压缩到所需的压力进入预冷机,压缩产生的热量由冷却水带走;1.2对正在运行的空压机,经常检查油位、各级压力、吸排气温度、水压是否在规定范围内:一级排气:<0.24MPa;二级排气压力:<0.55MPa 冷却水压力:0.15〜0.30 MPa ; 润滑油压:0.15〜0.30 MPa;油温:w 70C ;各级排气温v 170C ;后冷出口温度w 60C ;各轴瓦温度w 55T ;定子电流w 629A1.3 15分钟吹除各级油水一次;1.4明确哪台空压机向哪台塔供气,遇空压机紧急停车时,立即紧急停塔,并上报领导。
紧急停车有:1.4.1空压机任何一部分温度超过允许值;1.4.2冷却水突然断水;1.4.3各级吸、排气压力突然超过极限值;1.4.4 油压突然降至0.1 MPa 以下或断油;1.4.5 电动机负荷突然超过允许值;1.4.6 空压机或电机有异常响声;1.4.7 压缩机严重漏气、漏油;1.5 进行设备检修时一定要切断电源;1.6 空压机切换:先将备用空压机正常启动,关闭各级吹除阀,放空阀,当二级压力达到正常工作压力时,进行阀门开关操作,操作过程要协调,保持纯化器、分馏塔压力的稳定;1.7气体出后冷的温度须小于60C,否则切换空压机,通知钳工清洗冷凝器;1.8 空压机切换时,注意膨胀机转速变化,以防断气损坏膨胀机;1.9 空压机的启动、停车按《空压机操作规程》执行。
2. 预冷机2.1 压缩空气进入预冷机蒸发器内与低温低压液体-制冷剂氟利昂进行冷热交换后,经过油水分离器除去油、水份,降温进入纯化器;而氟利昂在冷热交换后,再经过压缩机压缩成高温高压气体,进入冷凝器中与冷却水进行冷热交换,经过过滤器、膨胀阀-节流膨胀为低温低压液体再进入蒸发器,如此循环使用;2.2 观察冷媒高、低压表是否正常,两表应在一定压力下达到平衡:蒸发压力:0.4 〜0.6MPa,冷凝压力:1.1 〜1.8MPa;2.3 尽量避免机组长时间在无负荷状态下运转;2.4 禁止开关的连续切换,以免过载继电器跳脱;2.5 检查压缩机是否正常,有无异响,温度是否偏高,否则须切换并通知钳工检修;2.6 正常使用过程中,为自动吹除阀;2.7 预冷机关机时,应先关闭空气源,再按红色按钮将预冷机关闭,并切断电源。
2.8 预冷机的启动和切换按《预冷机操作规程》执行3. 纯化器3.1 气体在纯化器中被分子筛介质吸附水、二氧化碳和乙炔等成分,而得到较为纯净、干燥的空气进入分馏塔;。