沉淀硫酸钡生产工艺技术改造
改性沉淀硫酸钡项目可行性研究报告
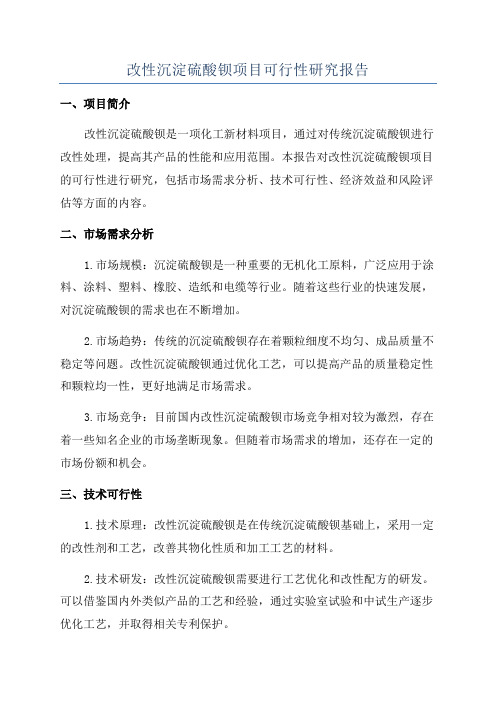
改性沉淀硫酸钡项目可行性研究报告一、项目简介改性沉淀硫酸钡是一项化工新材料项目,通过对传统沉淀硫酸钡进行改性处理,提高其产品的性能和应用范围。
本报告对改性沉淀硫酸钡项目的可行性进行研究,包括市场需求分析、技术可行性、经济效益和风险评估等方面的内容。
二、市场需求分析1.市场规模:沉淀硫酸钡是一种重要的无机化工原料,广泛应用于涂料、涂料、塑料、橡胶、造纸和电缆等行业。
随着这些行业的快速发展,对沉淀硫酸钡的需求也在不断增加。
2.市场趋势:传统的沉淀硫酸钡存在着颗粒细度不均匀、成品质量不稳定等问题。
改性沉淀硫酸钡通过优化工艺,可以提高产品的质量稳定性和颗粒均一性,更好地满足市场需求。
3.市场竞争:目前国内改性沉淀硫酸钡市场竞争相对较为激烈,存在着一些知名企业的市场垄断现象。
但随着市场需求的增加,还存在一定的市场份额和机会。
三、技术可行性1.技术原理:改性沉淀硫酸钡是在传统沉淀硫酸钡基础上,采用一定的改性剂和工艺,改善其物化性质和加工工艺的材料。
2.技术研发:改性沉淀硫酸钡需要进行工艺优化和改性配方的研发。
可以借鉴国内外类似产品的工艺和经验,通过实验室试验和中试生产逐步优化工艺,并取得相关专利保护。
3.设备投资:改性沉淀硫酸钡的生产设备相对简单,主要包括反应釜、分离设备和干燥设备等。
投资成本相对较低,易于实现。
四、经济效益1.投资收益:改性沉淀硫酸钡项目的投资周期相对较短,一般可以在3-5年内实现投资回收。
由于该产品的应用广泛,销售前景乐观。
2.市场定价:改性沉淀硫酸钡的市场价格相对传统产品有一定的溢价空间,可以根据产品的独特性和优势进行合理定价。
五、风险评估1.市场竞争风险:当前市场竞争激烈,需要根据自身的优势和产品特点确定市场定位,积极寻求市场空白点和新业务领域。
2.技术不稳定风险:改性沉淀硫酸钡的工艺和配方需要通过实验室试验和中试生产进行验证,可能存在技术不稳定的风险,需要做好技术研发和产业化推进。
医用沉淀硫酸钡的研制
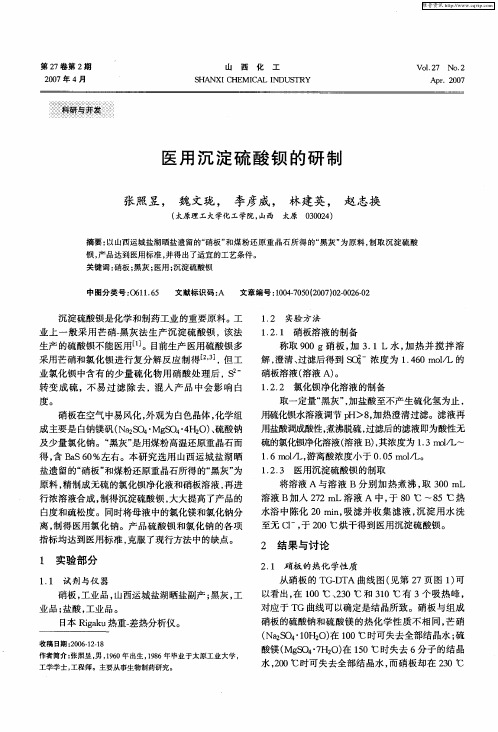
本研究通过利用山西运城盐湖晒盐遗留的“硝板”和煤粉还原重晶石所得的“黑灰”作为原料,成功研制出医用沉淀硫酸钡。通过精制成无硫的氯化钡净化液和硝板溶液,再进行浓溶液合成,最终制得高品质的沉淀硫酸钡。该产品不仅白度和疏松度大大提高,而且各项指标均达到医用标准。此外,研究过程中还将母液中的氯化镁和氯化钠进行分离,进一步得到医用氯化钠,实现了资源的综合利用。医用沉淀硫酸钡在化学和制药工业中具有重要作用,尤其是在医学影像检查中作为造影剂,能够帮助医生更清晰地观察患者体内情况,提高诊断准确性。本研究的果为医用沉淀硫酸钡的制备提供了一种新的、有效的方法,克服了现行方法中的缺点,具有良好的应用前景。
涂料中沉淀硫酸钡的生产工艺
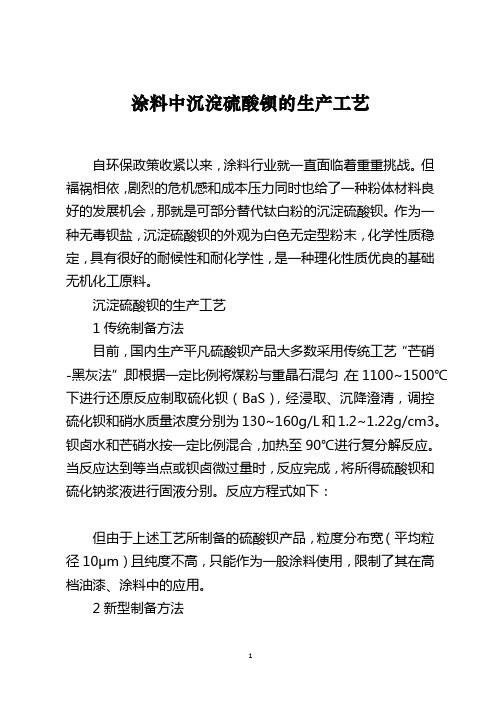
涂料中沉淀硫酸钡的生产工艺自环保政策收紧以来,涂料行业就一直面临着重重挑战。
但福祸相依,剧烈的危机感和成本压力同时也给了一种粉体材料良好的发展机会,那就是可部分替代钛白粉的沉淀硫酸钡。
作为一种无毒钡盐,沉淀硫酸钡的外观为白色无定型粉末,化学性质稳定,具有很好的耐候性和耐化学性,是一种理化性质优良的基础无机化工原料。
沉淀硫酸钡的生产工艺1传统制备方法目前,国内生产平凡硫酸钡产品大多数采用传统工艺“芒硝-黑灰法”,即根据一定比例将煤粉与重晶石混匀,在1100~1500℃下进行还原反应制取硫化钡(BaS),经浸取、沉降澄清,调控硫化钡和硝水质量浓度分别为130~160g/L和1.2~1.22g/cm3。
钡卤水和芒硝水按一定比例混合,加热至90℃进行复分解反应。
当反应达到等当点或钡卤微过量时,反应完成,将所得硫酸钡和硫化钠浆液进行固液分别。
反应方程式如下:但由于上述工艺所制备的硫酸钡产品,粒度分布宽(平均粒径10μm)且纯度不高,只能作为一般涂料使用,限制了其在高档油漆、涂料中的应用。
2新型制备方法为了使沉淀硫酸钡性能得到良好发挥,国内外的研究学者们一直寻求各种方法来调控BaSO4颗粒的粒径分布和形貌。
目前主要有直接沉淀法、络合沉淀法、微乳液法、微反应器法、离子交换法、表面活性剂法等。
①直接沉淀法直接沉淀法是将反应物在容器中直接混合发生反应生成悬浮物或沉淀,经过滤或离心、洗涤、干燥、研磨制得产品。
这种方法工艺简便、易于掌握、成本较低。
沉淀法制备超细粒子一般是由四个过程构成:一是晶核的形成过程,成为成核过程;二是晶核的长大过程,称为生长过程;三是颗粒团聚和聚集过程;四是干燥过程。
当成核速率小于生长速率时,有利于形成大而少的粗粒子;相反,当成核速率大于生长速率时,有利于行程超细粒子。
另外在反应体系中添加EDTA 能够有效阻挡硫酸钡团聚,从而降低硫酸钡粒径。
②络合沉淀法络合沉淀法是利用乙二胺四乙酸(EDTA)强络合剂与Ba2+鳌合,削减游离Ba2+的同时生成相对稳定的EDTA-Ba络合物。
沉淀硫酸钡生产工艺技术改造

综合利用盐泥的探讨太原化学工业集团有限公司化工厂秦晋明盐泥是氯碱行业原盐精制过程中所产生的废物。
对于各氯碱厂选用的原盐不同,所产生的盐泥也有所不同。
比如:国外的氯碱企业多选用优质盐或洗涤盐为原料,其产生的盐泥很少,一般用于钙塑材料的添加剂,也有用于水泥,钙镁肥料的生产等。
而且国内的氯碱企业所用的原盐质量较差,产生的盐泥量要大得多,以年产10万t烧碱计,排放盐泥达7千余t。
据调查,全国大多数氯碱企业的盐泥均为弃置堆放,不仅造成环境的污染,资源的浪费还占用大量场所,直接威胁人们的健康。
以海盐为主要原料的氯碱企业所排放的盐泥主要成份是镁盐;以岩盐为主要原料的氯碱企业所排放的盐泥主要成份是钡盐。
本文探讨的是以岩盐为主要原料的氯碱企业所排放盐泥的综合利用,本文以太原化工厂所排放盐泥为对象,采用酸解法,把其中的酸溶性物质与酸不溶物分开,以达到综合利用的目的,经小试、中试得到了比较满意的效果。
1、基本原理盐泥是一种颗粒细小,易于浆化,主要成分为钡、钙、镁的沉淀混合物。
其化学组成见表1。
表 1根据盐泥的化学组成,采用盐酸酸解的方法可将盐泥中的钙、镁等酸溶性沉淀与其中的硫酸钡、泥土等分开。
而不同的金属离子形成的氢氧化物在水中的溶解度有较大差别;在一定的酸碱条件下,使一部分进入溶液,另一部分形成沉淀。
利用这一原理,对酸解液中的钙镁等离子进行分离、Ca(OH)2、Mg(OH)2的溶度积分别为5.5×10-6、1.8×10-11,根据溶度积理论,Ca2+在较浓的OHˉ存在下才能形成Ca(OH)2沉淀,而Mg(OH)2沉淀可在较淡的OHˉ存在下形成。
所以在酸碱溶液中引进适当的OHˉ,并控制适当的酸碱度,使镁离子首先形成沉淀来达到分离钙镁等离子的目的。
2、实验部分2.1酸解处理根据盐泥中的钙镁等离子的含量,计算出酸解盐泥所需的盐酸总量。
将盐泥置于酸解液中,加入适量的水,搅拌成糊状,在搅拌下缓缓加入适量的工业盐酸最终控制适当的酸碱度,其主要化学反应为:CaCO3+HCL CaCL2+CO2+H2OMgCO3+HCL MgCL2+ CO2+ H2O将酸解液的乳浊液通过压滤器进行分离,清液即为含钙、镁等金属离子的液体,用做下一步的分离。
沉淀硫酸钡生产工艺

沉淀硫酸钡生产工艺
沉淀硫酸钡是一种重要的无机化工产品,广泛应用于橡胶、塑料、涂料、造纸等领域。
以下是沉淀硫酸钡的生产工艺介绍。
首先,原料准备。
生产沉淀硫酸钡的主要原料为钡盐和硫酸。
常用的钡盐有硫酸钡、氯化钡等,硫酸可由硫磺氧化得到。
根据生产规模的不同,可以适量调整原料的投入比例。
其次,反应过程。
将硫酸和钡盐以一定的比例加入反应釜中,然后进行搅拌混合并控制反应温度。
通常反应温度为60~90℃,反应时间为2~4小时。
反应完成后,通过过滤将产生的沉淀分离出来。
为了提高沉淀的纯度,可以对沉淀进行多次洗涤。
接下来,沉淀处理。
将分离得到的沉淀加入脱水烘箱中进行干燥处理。
通常沉淀的干燥温度为100~120℃,持续时间为2~4
小时。
干燥后的沉淀可根据需要进行精细加工,如进一步研磨或分级。
最后,产品包装与质检。
将沉淀硫酸钡进行包装,常见的包装方式有编织袋、纸箱等。
同时还需要进行质量检查,主要包括外观质量、化学成分、物理性能等指标的检测,确保产品达到标准要求。
需要特别注意的是,在整个生产过程中需要严格控制各个环节的操作条件,保证反应温度、时间和原料比例的准确性,以提高产品的质量和产量。
同时,要加强生产现场的安全管理,避免发生意外事故。
总之,沉淀硫酸钡的生产工艺包括原料准备、反应过程、沉淀处理、产品包装与质检等环节。
通过科学的工艺控制和质量管理,可以获得高品质的沉淀硫酸钡产品。
【精品文章】涂料行业的“宠儿”-沉淀硫酸钡的制备与应用

涂料行业的“宠儿”:沉淀硫酸钡的制备与应用
自环保政策收紧以来,涂料行业就一直面临着重重挑战。
但福祸相依,强烈的危机感和成本压力同时也给了一种粉体材料良好的发展机会,那就是可部分替代钛白粉的沉淀硫酸钡。
作为一种无毒钡盐,沉淀硫酸钡的外观为白色无定型粉末,化学性质稳定,具有很好的耐候性和耐化学性,是一种理化性质优良的基础无机化工原料。
但所谓出名全凭实力,由于粉体的结构和形貌等因素将直接影响粉体性能的发挥,所以沉淀硫酸钡想要成为大众情人,就需要提高自身品质。
譬如说球形硫酸钡颗粒可提高在有机高聚物材料中的分散性和流动性;平均粒径小于0.2μm的硫酸钡粉体可作为有色颜料的分散剂,使之色调鲜明有光泽——上文提到的硫酸钡可部分取代钛白粉,正是因为它在钛白粉颗粒间有阻隔效果,使钛白颗粒彼此有间隔,提高钛白粉的使用效率,因此涂料行业可借此来缓解钛白粉带来的成本压力。
由于粉体的性能与生产过程密切相关,也就是说生产工艺决定成败。
因此下文便来了解一下沉淀硫酸钡的各种制备工艺及其应用。
一、沉淀硫酸钡的生产工艺
1.传统制备方法
目前,国内生产普通硫酸钡产品大多数采用传统工艺“芒硝-黑灰法”,即按照一定比例将煤粉与重晶石混匀,在1100~1 500℃下进行还原反应制取硫化钡(BaS),经浸取、沉降澄清,调控硫化钡和硝水质量浓度分别为130~160 g/L和1.2~1.22 g/cm3。
钡卤水和芒硝水按一定比例混合,加热至90℃进行复分解反应。
当反应达到等当点或钡卤微过量时,反应完成,将。
改性超细沉淀硫酸钡生产操作规程(修订版)要点
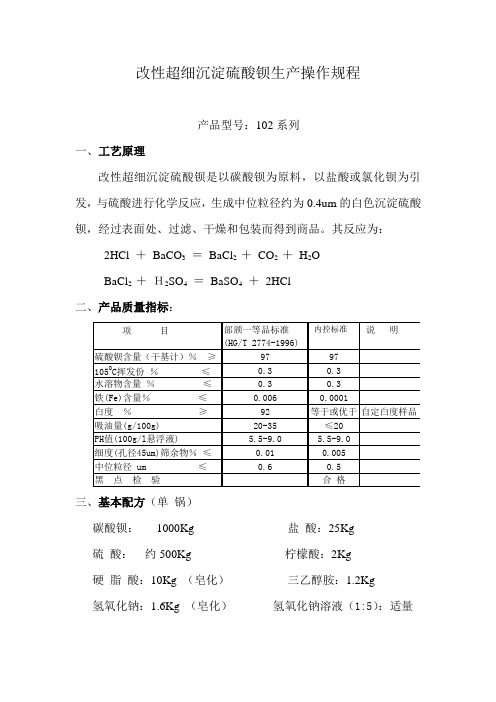
改性超细沉淀硫酸钡生产操作规程产品型号:102系列一、工艺原理改性超细沉淀硫酸钡是以碳酸钡为原料,以盐酸或氯化钡为引发,与硫酸进行化学反应,生成中位粒径约为0.4um的白色沉淀硫酸钡,经过表面处、过滤、干燥和包装而得到商品。
其反应为:2HCl +BaCO3=BaCl2 +CO2 +H2OBaCl2 +H2SO4=BaSO4+2HCl二、产品质量指标:项目部颁一等品标准内控标准说明(HG/T 2774-1996)硫酸钡含量(干基计)% ≥ 9797105O C挥发份 % ≤0.30.3水溶物含量%≤0.30.3铁(Fe)含量% ≤0.0060.0001白度 % ≥92等于或优于自定白度样品吸油量(g/100g)20-35≤20PH值(100g/l悬浮液) 5.5-9.0 5.5-9.0细度(孔径45um)筛余物% ≤ 0.010.005中位粒径 um ≤0.60.5黑 点 检 验合 格三、基本配方(单锅)碳酸钡:1000Kg 盐酸:25Kg硫酸:约500Kg 柠檬酸:2Kg硬脂酸:10Kg (皂化)三乙醇胺:1.2Kg氢氧化钠:1.6Kg (皂化)氢氧化钠溶液(1:5):适量四、生产操作规程1、浆化往浆化槽里加水12M3。
启动搅拌器,在搅拌下徐徐投加3000Kg碳酸钡原料,投料完成后继续搅20分钟。
搅拌下用泵将悬浮液泵至反应锅。
2、合成反应①将浆化好的含1000Kg碳酸钡悬浮液(约4.3M3)在搅拌下泵到反应锅内,加水至6M3,开动反应锅搅拌器。
②打开硫酸贮槽阀门,将硫酸放至中转槽。
启动硫酸泵,将硫酸泵到高位槽;启动吸收塔引风机和反应锅循环泵,往反应锅中倒入25公斤盐酸(或一包氯化钡)(25㎏),③打开硫酸阀门,在搅拌下将硫酸慢慢加入反应锅中,当PH=2-2.2时,停止投加硫酸(控制加酸时间在20-25分钟内完成),开循环泵,继续搅拌观察PH值有无变化,如PH值升高则补加硫酸,至PH值稳定在终点PH=2后再搅拌30分钟。
沉淀硫酸钡制作工艺介绍

Author:沉淀硫酸钡制作工艺介绍沉淀硫酸钡碳酸钡可从碳酸钡矿或通过合成沉淀获得,其用途和硫酸钡相似。
“铝水化物”也叫作氢氧化铝,或“轻质氧化铝水化物”,通常是在硫酸铝溶液中加过量的碱沉淀制得。
铝水化物的主要用途是作为基料,在其上沉淀印刷油墨生产中用到的染料和有机调色剂。
铝水化物具有较高的吸油量,化学性质非常活泼,价格较贵,在纺织品和纸张的涂料、以及橡胶的填料中有一定程度的应用。
亮白是25%铝水化物和75%硫酸钡粉的复合颜料,具有较细的组织和耐腐蚀性,主要用在印刷油墨中。
缎白为铝水化物和硫酸钙的共沉淀物,主要用在纸的涂装。
丝白是用氯化钙和钠氧化硅反应制得,主要用于印刷油墨。
除上述各种体质颜料外,还有一种在特殊涂料(如交通标志涂料)中作为填料的玻璃珠,对入射光有相当程度的反射。
当涂料表面磨蚀后,玻璃珠就曝露出来,成为微小的反光球,使夜晚交通标志线的能见度大为改善。
通常的品级有100%过70号筛、85~ 100%过80号筛、15 ~ 55%过1440号筛和0 ~ 10%过230号筛,相对应的粒径分别为0.21、0.177、0.105和0.063 mm。
玻璃珠还可以在广告板、邮箱、方向指针等的涂料中起填料的作用。
合成硫酸钡粉是用含有硫酸离子的水溶液和含有钡离子的水溶液反应制得,其性质和重晶石颜料相似,相对密度为4.18~ 4.40,吸油量为13 ~ 30 g/100 g。
因为合成硫酸钡粉的填充率较低,在涂料的应用中是比较贵重的一种填料。
硫酸钡粉与重晶石颜料一样易于快速沉淀,因此需要注意调节涂料的配方。
其作为涂料的填料对最终产品亮度的影响很小,在印刷油墨、油毡、油布和橡胶中也有一定的应用。
Author:。
- 1、下载文档前请自行甄别文档内容的完整性,平台不提供额外的编辑、内容补充、找答案等附加服务。
- 2、"仅部分预览"的文档,不可在线预览部分如存在完整性等问题,可反馈申请退款(可完整预览的文档不适用该条件!)。
- 3、如文档侵犯您的权益,请联系客服反馈,我们会尽快为您处理(人工客服工作时间:9:00-18:30)。
BaS +4CO2 BaCO 3+SO 2 +3CO
BaSO3 +1/ 2S2 BaS2O3
以上多种酸溶性钡在浸取 BaS 之后将随渣被抛
弃掉 。 所以在配料之前 , 需对重晶石进行水洗 、分
拣 , 除去泥沙及混入的 石英石等 , 优选低杂质 重晶
石 。煤炭选用低硫煤 , 分拣出煤矸石 。当重晶石及
Байду номын сангаас工艺
w (出饼 水分)/ %
操作 状态
w (滤液含 固)/ %
板框压滤
35
间歇
浑浊(3)
卧螺分离
20
连续 清澈(0 .05)
注 :钡浆进料水分质量分数为 45 %~ 55 %。
滤液
不可回用 可回用
表 5 不 同干燥方式的干燥效果
干燥 w (物料含 方式 水)/ %
热源
传热
w (出料含 水)/ %
料床温 度/ ℃
3 .2 .8 工艺系统按功能化产品结构进行优化配置 设计“一个龙头 , 多条龙尾” 的工艺配置方案 。
针对涂料行业的多元化产品结构 , 设计硫酸钡产品 的多元化产出 。 在工艺流程中设计不同的接口 , 以 方便随市场需 求调整添加剂的加入及 工艺条件控 制 。产品功能化结构图见图 1 。
表 4 采用不同分离机钡浆的分离效果
表 3 不同反应条件下硫酸钡的粒径分布
反应条件 粒径分布/μm 分布状态 D97 D50 VMD
形貌
釜式反应 10 .78 1 .74 3 .09 正态分布(宽) 不规则
强化反应 1 .21 0 .47 0 .64 正态分布(窄) 较规则
3 .2 .3 分离 、洗涤工艺条件的改善 传统工艺对化合完成液采用叶片抽滤 , 操作过 程易污染物料 , 且滤饼含 水量高(质 量分数为 35 % ~ 45 %), 影响碱液回收率 , 运行费用亦高 。 经强化 反应后由于粒子细小 , 叶片透滤严重 。引入 LW420 ×1680 卧式螺旋卸料沉降式分离机(简称卧螺 , 下 同), 进行反应完成液的分离洗涤 , 可在提高分离效 率的前提下 , 碱液质量分数提高 1 .5 %, 回收率提高 到 90 %以上 , 洗涤用水耗量减少 28 %以上 。 3 .2 .4 酸化条件的设定
1 技术改造的方向和目标
作控制参数 , 见表 1 。
1)降低生产运行成本 ;2)提高产品品质 ;3)产品 结构系列化 ;4)实现生产工艺装备的经济科学合理 配置 。
2 传统工艺存在的问题
1)重晶石利用率低 , 仅达 70 %;2)系统 热利用 率低 , 不足 60 %;3)产品品质低 , 即指标不稳定 , 批 次差异大 , 杂质含量高 , 泛黄 , 黑 、黄点多 , 分散性差 ; 4)工艺装置老化 , 跑 、冒 、滴 、漏严重 , 运行成本高 ;5) 系统工艺配置不合理 , 难以达到产品 系列化 、功能 化 ;6)产品结构不能适应市场发展要求 , 品种单一 , 难以应对市场的变化 ;7)副产碱液回收利用率低 , 仅 达 60 %;8)物料消耗高 , 成本高 。
晶石的转化率 。 灰分中的 SiO2 , Al2O3 , Fe2O3 同样与 硫酸钡发生反应生成酸溶性钡而“吃掉”钡 。 煤中的
硫在焙烧炉中会形成 SO2与生成的 BaS 反应生成水 不溶性的硫酸钡和碳酸钡 。
BaS +2SO2 BaSO 4+S2
BaS +SO2 +H2O
BaSO 3+H2S
BaSO 3+CO 2 BaCO3 +SO2
Abstract :In view of the problems existing in the production of precipitated barium sulfate by traditional method, such as low utilizing rate of barytes and heat in the sy stem , obsolate equipments, bad quality of the product and single variety etc., the process improvements for the traditional precipitated barium sulfate are carried out .As a result, the quality of the product is improved , the operation cost is decreased and the optimum distribution of product structure is realized. Key words:barium sulfate ;technological improvement ;process
2BaSO4 +2Ba2SiO4
2Ba3SiO5 + 2SO3
同样矿石中的 Al2O3 ,Fe2O3也会发生类似的反应 , 生
成[ BaO·Al2O3] 和[ BaO·Fe2O3] ;氧化铁与硫化钡作
用还可生成硫代铁酸钡 , 这些不溶于水的钡盐的生
成 会“ 吃 掉” 硫酸钡 和硫 化钡 而使 重晶 石的 利用 率降
矿体 形态
配料比
粉碎粒 操作
黑灰 黑灰品质
度/ mm 温度/ ℃ w (BaS)/ % 增量/ %
热液 型矿
100 ∶(20 ~
25)
3~ 5
980 ~ 1 050
68 .34 +10 .00
沉积 型矿
100 ∶(25 ~
30)
2~ 3
1 050~ 1 200
69 .98
+12 .00
注 :配料比为重晶石与煤灰的质量比 。
出料条件下黑灰成分分析见表 2 。
工艺 直接出料 经过贮仓
表 2 不同出料条件黑灰成分分析
%
w (BaS) w (酸溶性钡) w (其它) 黑灰品质增量
58 .57
24 .38
17 .05
0 .00
63 .34
19 .64
12 .02
+5 .00
4)合理回收烟道灰 。焙烧炉尾 Ⅰ , Ⅱ , Ⅲ级重力 捕集室捕集到的 烟道灰平均含有质量分数为 25 % ~ 30 %的 BaSO4和 10 %的 C 为可利用成分 。 在加入 钡泥(后部工序洗涤粉碎及跑冒滴漏收集到的残钡) 及粘合剂后 , 经混合 、造粒 、烘干(利用烟道气)后投 入炉内重烧 , 常规情况下每 t 产品可回收 80 ~ 100 kg 可利用的烟道灰 。
42
无机盐工业 第 36 卷第 4 期
3 .2 .5 脱水 、干燥工艺条件的改善 选用 LW420 ×1680 卧螺机代替传统板框压滤 ;
选用 GY5000SM 型 空心桨叶 干燥机取 代回转干 燥 机 , 使干燥效率及产品品质得以提高 。 板框压滤与 卧螺分离的效果比较见表 4 。 回转干燥与桨叶干燥 的效果比较见表 5 。
3 生产工艺装备的技术改造内容
3 .1 提高重晶石利用率的技改措施 1)调整焙烧炉的控制参数 。 重晶石由于矿体结 构的不同表现出的晶体及组成差异很大[ 1] , 必须科 学地调整配料及原料的粒径范围 , 有针对性地修正 焙烧炉的操作控制条件 。 经试验 , 调整焙烧炉的操
表 1 焙烧炉的操作控制条件
经过改造运 行 , 重晶 石的 利用 率由 改 造前 的 63 %提高到 88 %。
3 .2 提高产品品质的技改措施 3 .2 .1 BaS 液 、NaSO4液及软化水的净化
BaS 液从溶浸槽分离后必须在保温密闭的贮罐 中进行静置澄清 , 目的是防止液面与空气接触 , BaS 与空气中的 CO2 反应生成 BaCO3(消化 掉部分硫化 钡 ;BaCO3晶粒进入化合后会形成以碳酸钡为晶核的 包覆产物使硫酸钡的系统成核及粒径分布不均匀)。 用芒硝(Na2SO 4·10H2O)制备 Na2SO4溶液 , 在加入 Na2 CO3及稀碱液 Na2S 除去 Ca2+ , Mg2+ 后 , 经过微孔过 滤除去不溶性 杂质 , 保持 透明度在25 mm 以上 。 洗 涤用水经离子交换后经微孔过滤使用 。原料液在进 入计量罐前 、软化水进入贮罐前 、增设49 μm滤网过 滤 , 保证原料液洁净无杂 。 3 .2 .2 化合条件的改善 化合反应在控制等量化合 、钡微过量操作的条 件下引入撞击流反应器及超重力反应技术 , 使液 — 液反应传质得以强化 , 极大地改善了 BaSO4晶体的 分布状态和晶型 , 不同反应条件下硫酸钡的粒径分 布(化合完成液)见表 3 。
煤中 SiO2含量高时 , 可在炉料中加入石灰石 , 使之生 成不溶性的 CaSiO3 , 减少酸溶性硅酸盐的生成 。 3)营造良好的还原气氛 。重晶石焙烧应保持还
原气氛 , 当以喷煤提供热源时 , 由于高压风的引入可
能破坏还原气氛 , 所以对炉头必须进行良好的密封 ,
防止冷空气的进入 , 否则将有如下反应发生 :
40
INORGANIC
无机盐工业 CHEM ICALS
INDUSTRY 第230604卷年第7 月4 期
沉淀硫酸钡生产工艺技术改造
文建章
(山西南风化工 集团有限公司技术中心 , 山西运城 044000)
摘要 :针对传统沉淀硫酸钡生产工艺存在的问 题 , 如 :重 晶石利 用率低 、系统 热利用 率低 、产品 品质低 、工艺 装 备老 化 、产品品种单一等 , 对传统沉淀硫酸钡生产工艺实 施了全 过程的 技术改 造 , 使 产品品 质得以 提高 , 运行成 本 明显降低 , 实现了工艺系统按照产品结构功能化 的优化配置 。 关键词 :硫酸钡 ;技术改造 ;生产工艺 中图分类号 :TQ132 .35 文献标识码 :A 文章编 号 :1006-4990(2004)04-0040-03