形位误差检测原则
形位误差的检测

2.测量特征参数原则 用该原则所得到的形位误差值与按定义确定的形位误差值 相比,只是一个近似值,但应用此原则,可以简化过程和 设备,也不需要复杂的数据处理,故在满足功能的前提下, 可取得明显的经济效益。在生产现场用得较多。如:以平 面上任意方向的最大直线度来近似表示该平面的平面度误 差;用两点法测圆度误差;在一个横截面内的几个方向上 测量直径,取最大、最小直径差之半作为圆柱度误差。
用刀口尺和被测要素相接触,使刀口尺和被测要素之间最大光隙为最 小时,这样估读出的最大光隙值就是被测直线/平面的直线度误差。
(2)平面度误差的测量
指示器法 将被测零件支撑在平板上,平板工作面为测量基准,按一定的方式布 点,用指示器对被测表面上各测点进行测量并记录所测数据,然后, 按一定的方法评定其误差值。
公差配合与测量技术
形位误差的检测
一、形位误差的检测原则
1.与理想要素比较的原则 即将被测要素与其理想要素相比较,用直接或间接测量 法测得形位误差值应用最为广泛的一种方法,理想要素 可用不同的方法获得,如用刀口尺的刃口,平尺的工作 面,平台和平板的工作面以及样板的轮廓面等实物体现, 也可用运动轨迹来体现,如:精密回转轴上的一个点 (测头)在回转中所形成的轨迹(即产生的理想圆)为 理想要素,还可用束光、水平面(线)等体现。
如图所示,图A为被测工件通过心轴安装在两同轴顶尖之间,两同轴顶 尖的中心线体现基准轴线; 图B为V形块体现基准轴线,测量中,当被测工件绕基准回转一周中,指 示表不作轴向(或径向)移动时,可测得圆跳动,作轴向(或径向)移 动时,可测得全跳动。
5.控制实效边界原则
按最大实体要求给出形位公差时,要求被测实体不 得起过最大实体边界,判断被测实体是否超过最大 实体边界的有效方法就是用位置量规。
形状和位置公差检测规定

图8
18、基准轴线(基准中心线):由实际轴线(中心线)建立基准线(中心线)时,基准轴线(中心线)为该实际轴线(中心线)的理想轴线(中心线),如图9所示。
图9
注:①实际轴线为实际回转体各横截面测得轮廓的中心点的连线,如下图所示。测得轮廓的中心点是指该轮廓的理想圆的圆心。
测量直角坐标值
3
测量特征参
数原则
测量被测实际要素上具有代表性的参数(即特征参数)来表示形位误差值
两点法测量圆度特征参数
编号
检测原则名称
说明
示例
4
测量跳动原则
被测实际要素绕基准轴线回转过程中,沿给定方向测量其对某参考点或线的变动量。
变动量是指指示器最大与最小读数之差。
测量径向跳动
5
控制实效边
界原则
检验被测实际要素是否超过实效边界,以判断合格与否
图21
图22
图23
在满足零件功能要求的前提下,当第一、第二基准平面与基准实际要素间为非稳定接触时,允许其自然接触。
五、仲裁
28、当发生争议时,用分析测量精度的方法进行仲裁。
29、当由于采用不同方法评定形位误差值而引争议时,对于形状、定向、定位误差分别以最小区域、定向最小区域和定位最小区域的宽度(或直径)所表示的误差作为仲裁依据。
由L形架体现的轴线
给基
定准
位轴
置线
的
公
共
同轴两顶尖的轴线
续表3
基准示例
模拟方法示例
基
准
平
面
与基准实际表面接触的平板或平台工作面
基
准
中
实验二 形状和位置误差测量

实验二形状和位置误差测量1.实验目的(1)掌握用指示表和平台测量平面的形位误差的方法;(2)掌握平面的平面度、平行度和位置度三种形位误差的评定方法和数据处理方法。
2.原理本实验三种形位误差的检测原理均为与理想要素比较原理:(1)平面度误差的测量原理用平台的工作表面模拟理想平面,将实际被测平面与模拟理想平面相比较,用指示表测出其差别。
平面可看成由许多直线构成,因此可用几个有代表性的直线的直线度误差来综合反映该平面的平面度误差。
(2)面对面平行度误差的测量原理用平台的工作表面模拟模拟基准平面和理想平面。
(3)面对面位置度误差的测量原理用平台的工作表面模拟基准平面和理想平面,并用量块组的尺寸体现图样上标注的理论正确尺寸。
3.试剂和仪器设备(1)百分表;(2)磁力表座;(3)试件;(4)平台(,1级);(5)量块(83块/套)。
4.实验步骤(1)将被测工件以其实际基准表面放置在测量平台的工作表面上;(2)按图样上标注的理论正确尺寸选取量块组,并将其放置在测量平台的工作表面上;(3)用量块组调整指示表的示值零位;(4)按选定的布点方式在实际被测表面上标出各测点位置;(5)移动测量架,逐点测量各测点至测量平台工作表面的距离。
5.实验数据及其处理(1)测量数据为各测点指示表的示值;(2)按对角线平面法和最小条件求解平面度误差值;(3)按定向最小区域求解平行度误差值;(4)按定位最小区域求解位置度误差值;(5)按图样上标注的形位公差值判断被测要素的合格性。
6.问题讨论(1)按对角线平面法和最小条件评定平面度误差值各有何特点?(2)面对面平行度误差的定向最小包容区域的判别准则是什么?(3)面对面位置度误差的定位最小包容区域的判别准则是什么?。
第3章4节形状和位置公差及检测选择标注、检测)-2

方便,可规定径向圆跳动(或全跳动)公差代替同轴度公差。
2、基准要素的选择
(1)基准部位的选择 选择基准部位时,主要应根据设计和使用要求,零件的 结构特征,并兼顾基准统一等原则进行。 1)选用零件在机器中定位的结合面作为基准部位。例如箱 体的底平面和侧面、盘类零件的轴线、回转零件的支承轴颈 或支承孔等。 2)基准要素应具有足够的大小和刚度,以保证定位稳定可 靠。例如,用两条或两条以上相距较远的轴线组合成公共基 准轴线比一条基准轴线要稳定。 3)选用加工比较精确的表面作为基准部位。 4)尽量使装配、加工和检测基准统一。这样,既可以消除 因基准不统一而产生的误差;也可以简化夹具、量具的设计 与制造,测量方便。
f
(2) 中心要素 最小条件就是理想要素应穿过实际中心要素,并使实 际中心要素对理想要素的最大变动量为最小。
如图 所示, 符 合最小条件的理想 轴线为L1 ,最小直 径为φf=φd1。
被测实际要素 L2
d1
L1
最小条件是评定形状误差的基本原则,在满足零件功能 要求的前提下,允许采用近似方法评定形状误差。当采 用不同评定方法所获得的测量结果有争议时,应以最小 区域法作为评定结果的仲裁依据。
(4) 考虑零件的结构特点
(5) 凡有关标准已对形位公差作出规定的,都应按相应的标准确 定。如与滚动轴承相配的轴和壳体孔的圆柱度公差、机床导轨 的直线度公差、齿轮箱体孔的轴线的平行度公差等。
表3-4 直线度、平面度公差等级的应用
表3-5 圆度、圆柱度公差等级的应用
表3-6 平行度、垂直度、倾斜度、端面跳动公差等级的应用
(2) 基准数量的确定 一般来说,应根据公差项目的定向、定位几何功能要求 来确定基准的数量。 定向公差大多只要一个基准,而定位公差则需要一个或 多个基准。例如,对于平行度、垂直度、同轴度公差项目, 一般只用一个平面或一条轴线做基准要素;对于位置度公差 项目,需要确定孔系的位置精度,就可能要用到两个或三个 基准要素。
形状与位置公差及检测

形状公差
▪ 单一要素对其理想要素允许的变动量。其 公差带只有大小和形状,无方向和位置的 限制。
▪ 直线度 ▪ 平面度 ▪ 圆度 ▪ 圆柱度
4/29/2010
直线度公差
▪ 直线度公差用于控制直线和轴 线的形状误差,根据零件的功 能要求,直线度可以分为在给 定平面内,在给定方向上和在 任意方向上三种情况。
至于定位误差,则理想要素置于相对于基准某一确定有位置上,其定 位条件可称为定位最小条件。
4/29/2010
跳动:
跳动的分类: 它可分为圆跳动和全跳动。
圆跳动:是指被测实际表面绕基准轴线作无轴向移动 的回转时,在指定方向上指示器测得的最大读数差。
全跳动:是指被测实际表面绕基准轴线无轴向移动的 回转,同时指示器作平行或垂直于基准轴线的移动,在 整个过程中指示器测得的最大读数差。
▪ 在给定平面内的直线度 ▪ 在给定方向内的直线度 ▪ 任意方向上的直线度
4/29/2010
在给定平面内的直线度
▪ 其公差带是距离为公差值t的 两平行直线之间的区域。如图 所示,圆柱表面上任一素线必 须位于轴向平面内,且距离为 公差值0.02mm的两平行直线之 间。
4/29/2010
在给定方向内的直线度
4/29/2010
垂直度(一)
▪ 当两要素互相垂直时,用垂直 度公差来控制被测要素对基准 的方向误差。当给定一个方向 上的垂直度要求时,垂直度公 差带是距离为公差值t,且垂直 于基准平面(或直径、轴线) 的两平行平面(或直线)之间 的区域。
4/29/2010
垂直度(二)
▪ 当给定任意方向时,平行度 公差带是直径为公差值t, 且垂直于基准平面的圆柱面 内的区域。如图所示, ød孔 轴线必须位于直径公差值ø 0.05mm,且平行于基准平面 的圆柱面内。
形位误差的检测原则
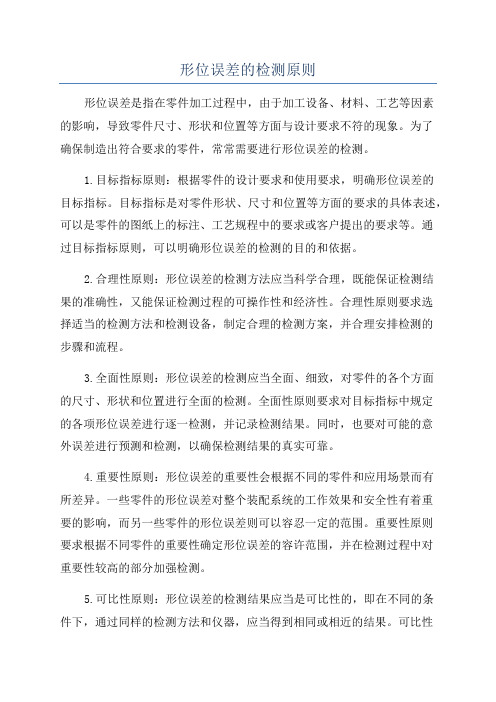
形位误差的检测原则形位误差是指在零件加工过程中,由于加工设备、材料、工艺等因素的影响,导致零件尺寸、形状和位置等方面与设计要求不符的现象。
为了确保制造出符合要求的零件,常常需要进行形位误差的检测。
1.目标指标原则:根据零件的设计要求和使用要求,明确形位误差的目标指标。
目标指标是对零件形状、尺寸和位置等方面的要求的具体表述,可以是零件的图纸上的标注、工艺规程中的要求或客户提出的要求等。
通过目标指标原则,可以明确形位误差的检测的目的和依据。
2.合理性原则:形位误差的检测方法应当科学合理,既能保证检测结果的准确性,又能保证检测过程的可操作性和经济性。
合理性原则要求选择适当的检测方法和检测设备,制定合理的检测方案,并合理安排检测的步骤和流程。
3.全面性原则:形位误差的检测应当全面、细致,对零件的各个方面的尺寸、形状和位置进行全面的检测。
全面性原则要求对目标指标中规定的各项形位误差进行逐一检测,并记录检测结果。
同时,也要对可能的意外误差进行预测和检测,以确保检测结果的真实可靠。
4.重要性原则:形位误差的重要性会根据不同的零件和应用场景而有所差异。
一些零件的形位误差对整个装配系统的工作效果和安全性有着重要的影响,而另一些零件的形位误差则可以容忍一定的范围。
重要性原则要求根据不同零件的重要性确定形位误差的容许范围,并在检测过程中对重要性较高的部分加强检测。
5.可比性原则:形位误差的检测结果应当是可比性的,即在不同的条件下,通过同样的检测方法和仪器,应当得到相同或相近的结果。
可比性原则要求消除人为因素对检测结果的影响,确保各次检测的可比性。
同时,也要求在需比较不同零件或不同批次零件的形位误差时,能够确保结果的可比性。
以上是形位误差的检测原则,通过遵循这些原则,可以确保形位误差的检测结果真实可靠,并保证制造出符合要求的零件。
形位公差基础知识

(1)实际要素 即零件上实际存在的要素,可以通过测量 反映出来的要素代替。
(2)理想要素 它是具有几何意义的要素;是按设计要求 ,由图样给定的点、线、面的理想形态,它不存在任 何误差,是绝对正确的几何要素。
3. 按所处地位分类
(1)被测要素 图样中给出了形位公差要求的要素,是测 量的对象。
之间。
4.圆柱度
圆柱度公差带是半径差为公差值t的 两同轴圆柱面之间的区域。如图所示, 被测实际圆柱表面必须位于半径差为公 差值0.05mm的两同轴圆柱面之间。
圆柱度和圆度的区别:圆柱度是相对于整个圆柱面 而言的,圆度是相对于圆柱面截面的单个圆而言的 ,圆柱度包括圆度,控制好了圆柱度也就能保证圆 度,但反过来不行。
形状公差是以要素本身的形状为研究对象 ,而位置公差则是研究要素之间某种确定的方 向或位置关系。
1. 按结构特征分类
(1)轮廓要素 构成零件外形为人们直接感觉到的点、 线、面。
(2)中心要素 轮廓要素对称中心所表示的点、线、面 。其特点是它不能为人们直接感觉到,而是通过相 应的轮廓要素才能体现出来。
(1)公差特征符号
根据零件的工作性能要求,由设计者从表 中选定。
(2)公差值
用线性值,以mm为单位表示。如果公差 带是圆形或圆柱形的,则在公差值前面加注φ ;如果是球形的,则在公差值前面加注Sφ。
(3)基准
基准符号如下图所示。相对于被测要素 的基准,由基准字母表示。为不致引起误解, 字母E、I、J、M、O、P、L、R、F不采用。
(2)基准要素 用来确定被测要素方向和位置的要素。基 准要素在图样上都标有基准符号或基准代号。
4. 按功能关系分类
(1)单一要素 仅对被测要素本身给出形状公差的要素。 (2)关联要素 与零件基准要素有功能要求的要素。
互换性与测量技术基础考试复习资料
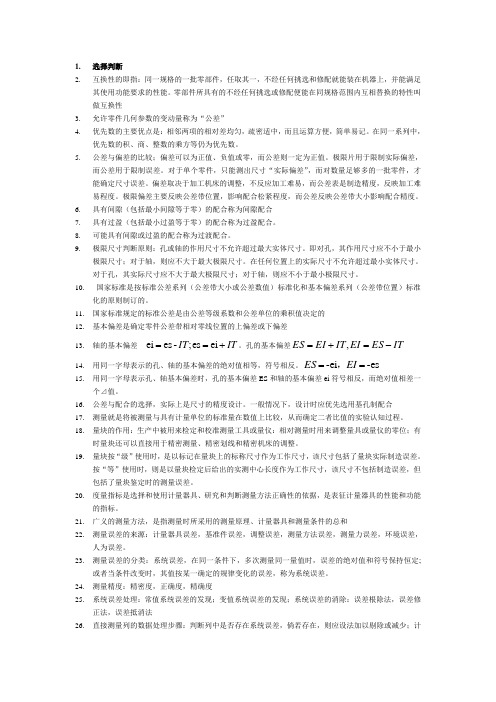
1.选择判断 2. 互换性的即指:同一规格的一批零部件,任取其一,不经任何挑选和修配就能装在机器上,并能满足其使用功能要求的性能。
零部件所具有的不经任何挑选或修配便能在同规格范围内互相替换的特性叫做互换性3.允许零件几何参数的变动量称为“公差” 4.优先数的主要优点是:相邻两项的相对差均匀,疏密适中,而且运算方便,简单易记。
在同一系列中,优先数的积、商、整数的乘方等仍为优先数。
5. 公差与偏差的比较;偏差可以为正值、负值或零,而公差则一定为正值。
极限片用于限制实际偏差,而公差用于限制误差。
对于单个零件,只能测出尺寸“实际偏差”,而对数量足够多的一批零件,才能确定尺寸误差。
偏差取决于加工机床的调整,不反应加工难易,而公差表是制造精度,反映加工难易程度。
极限偏差主要反映公差带位置,影响配合松紧程度,而公差反映公差带大小影响配合精度。
6.具有间隙(包括最小间隙等于零)的配合称为间隙配合 7.具有过盈(包括最小过盈等于零)的配合称为过盈配合。
8.可能具有间隙或过盈的配合称为过渡配合。
9. 极限尺寸判断原则:孔或轴的作用尺寸不允许超过最大实体尺寸。
即对孔,其作用尺寸应不小于最小极限尺寸;对于轴,则应不大于最大极限尺寸。
在任何位置上的实际尺寸不允许超过最小实体尺寸。
对于孔,其实际尺寸应不大于最大极限尺寸;对于轴,则应不小于最小极限尺寸。
10. 国家标准是按标准公差系列(公差带大小或公差数值)标准化和基本偏差系列(公差带位置)标准化的原则制订的。
11. 国家标准规定的标准公差是由公差等级系数和公差单位的乘积值决定的12. 基本偏差是确定零件公差带相对零线位置的上偏差或下偏差13. 轴的基本偏差IT IT +==ei es ;-es ei 。
孔的基本偏差IT ES EI IT EI ES -=+=,14. 用同一字母表示的孔、轴的基本偏差的绝对值相等,符号相反。
-es -ei ==EIES , 15. 用同一字母表示孔、轴基本偏差时,孔的基本偏差ES 和轴的基本偏差ei 符号相反,而绝对值相差一个⊿值。
- 1、下载文档前请自行甄别文档内容的完整性,平台不提供额外的编辑、内容补充、找答案等附加服务。
- 2、"仅部分预览"的文档,不可在线预览部分如存在完整性等问题,可反馈申请退款(可完整预览的文档不适用该条件!)。
- 3、如文档侵犯您的权益,请联系客服反馈,我们会尽快为您处理(人工客服工作时间:9:00-18:30)。
第六节
形位误差的评定及检测
一、形位误差的评定
1.形状误差的评定
1)最小条件
评定形状误差的基本原则是“最小条件”:即被测实际要素对其理想要素的最大变动量为最小。
(1) 轮廓要素(线、面轮廓度除外)
最小条件就是理想要素位于实体之外与实际要素接触,并使被测要素对理想要素的最大变动量为最小。
(2) 中心要素
最小条件:就是理想要素应穿过实际中心要素,并使实际中心要素对理想要素的最大变动量为最小。
Ⅰ
最小区域
f 1
Ⅱ
被测实际要素
Ⅲ
图4-24 轮廓要素的最小条件
L2
被测实际要素
d1
L1
2
图4-25中心要素的最小条件
2)最小包容区(简称最小区域)
最小包容区(简称最小区域):是指包容被测实际要素时,具有最小宽度f或直径 f的包容区域。
形状误差值用最小包容区(简称最小区域)的宽度或直径表示。
按最小包容区评定形状误差的方法,称为最小区域法。
最小条件是评定形状误差的基本原则,在满足零件功能要求的前提下,允许采用近似方法评定形状误差。
当采用不同评定方法所获得的测量结果有争议时,应以最小区域法作为评定结果的仲裁依据。
被测实际要素
S
S
a) 评定直线度误差
图4-26 最小包容区示例
被测实际要素
被测实际要素
S
S
c) 评定平面度误差
b) 评定圆度误差
2.定向误差的评定
定向误差值用定向最小包容区域(简称定向最小区域)的宽度或直径表示。
定向最小包容区域是按理想要素的方向来
包容被测实际要素,且具有最小宽度f或
直径 f的包容区域。
S
被测实际要素
基准
图4-27 定向最小包容区域示例
被测实际要素
S
被测实际要素
基准
S
基准
α
图4-27 定向最小包容区域示例
3.定位误差的评定
评定形状、定向和定位误差的最小包容区域的大小一般是有区别的。
如
图4-29所示,其关系是:f 形状< f 定向< f 定位
当零件上某要素同时有形状、定向和定位精度要求时,则设计中对该要素所给定的三种公差(T 形状、T 定向和T 定位)应符合:
T 形状<T 定向<T 定位
基准A
被测实际要素F
S
L
h 1
P
P S
基准A
O
L y
L x
基准B
f
图4-28 定位最小包容区域示例
H
A
A
A
t1
t2
t3
a) 形状、定向和定位公差
标注示例:t1 < t2 < t3
A
H
f形状
b) 形状、定向和定位误差评定的
最小包容区域:f形状< f定向< f定位
图4-29 评定形状、定向和定位误差的区别
f
定
向
f
定
位
二、形位误差的检测原则1.与理想要素
比较原则
与理想要
素比较原则是指测量时将被测实际要素与其理想要素作比较,从中获得数据,以评定被测要素的形位误差值。
这些检测数据可由直接法或间接法获得。
该检测原理在形位误差测量中的应用最为广泛。
被测零件
刀口尺(理想要素)
被测零件
平板(理想要素)
2.测量坐标值原则
测量坐标值原则是指利用计量器具的固有坐标,测出实际被测要素上各测点的相对坐标值,再经过计算或处理确定其形位误差值。
3.测量特征参数原则
测量特征参数原则是指测量实际被测要素上具有代表性的参数(即特征参数)来近似表示形位误差值。
4.测量跳动原则此原则主要用于跳
动误差的测量,因跳动公差就是按特定的测量方法定义的位置误差项目。
其测量方法是:被测实际要素(圆柱面、圆锥面或端面)绕基准轴线回转过程中,沿给定方向(径向、斜向或轴向)测出其对某参考点或线的变动量(即指示表最大与最小读数之差)。
顶尖被测零件心轴图4-31 径向和端面圆跳动测量
5.控制实效边界原则
控制实效边界原则的含义是检验被测实际要素是否超过实效边界,以判断被测实际要素合格与否。
d M =φ50被测零件功能量规
d M V =φ25.04
图4-32用功能量规检验同轴度误差
A A 50250-0.05
50E 0.04M 42
M
-0.05
小结
1.形位误差的研究对象是几何要素,根据几何要素特征的不同可分为:理想要素与实际要素、轮廓要素与中心要素、被测要素与基准要素以及单一要素与关联要素等;国家标准规定的形位公差特征共有14项,熟悉各项目的符号、有无基准要求等。
2.形位公差是形状公差和位置公差的简称。
形状公差是指实际单一要素的形状所允许的变动量。
位置公差是指实际关联要素相对于基准的位置所允许的变动量;形位公差带具有形状、大小、方向和位置四个特征。
形位公差带分为形状公差带、定向公差带、定位公差带和跳动公差带四类。
应熟悉常用形位公差特征的公差带定义、特征(形状、大小、方向和位置),并能正确标注。
3.公差原则是处理形位公差与尺寸公差关系的基本原则,它分为独立原则和相关要求两大类。
应了解有关公差原则的术语及定义,公差原则的特点和适用场合,能熟练运用独立原则、包容要求。
4.了解形位误差的评定方法。
掌握形状误差(f形状)、定向误差(f定向)和定位误差(f定位)之间的关系:f形状< f定向< f定位,即定位误差包含了定
向误差和形状误差,定向误差包含了形状误差。
当零件上某要素同时有形状、定向和定位精度要求时,则设计中对该要素所给定的三种公差(T形状、T定
向和T定位)应符合:T形状<T定向<T定位。
各项形位公差的控制功能不尽相同,应建立某些定向和定位公差具有综合控制功能的概念。
5.正确选择形位公差对保证零件的功能要求及提
高经济效益都十分重要。
应了解形位公差的选择依据,初步具备形位公差特征、基准要素、公差等级(公差值)和公差原则的选择能力。
6.形位误差的检测原则。