可追溯性过程流程图
IATF16949-2016过程流程图
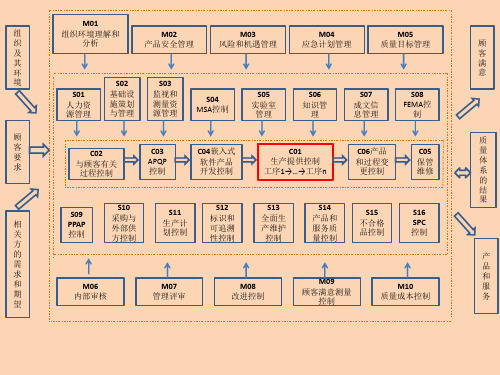
C02 与顾客有关 过程控制
C03
APQP 控制
C04嵌入式 软件产品 开发控制
C01 生产提供控制
工序1→…→工序n
C06产品 和过程变 更控制
C05 保管 维修
量 体 系
的
结
果
相 关
S09
PPAP 控制
S10 采购与 外部供 方控制
S11 生产计 划控制
S12 标识和 可追溯 性控制
S13 全面生 产维护 控制
M01
组
组织环境理解和
M02
M03
M04
M05
织
分析
产品安全管理
风险和机遇管理
应急计划管理
质量目标管理
顾
及
客
其
满
环
意
境
S02
S03
S01 人力资 源管理
基础设 施策划 与管理
监视和 测量资 源管理
S04 MSA控制
பைடு நூலகம்
S05 实验室 管理
S06 知识管
理
S07 成文信 息管理
S08 FEMA控
制
顾
质
客 要 求
S14 产品和 服务质 量控制
S15 不合格 品控制
S16
SPC 控制
方
的
产
需
品
求 和 期 望
M06 内部审核
M07 管理评审
M08 改进控制
M09 顾客满意测量
控制
M10 质量成本控制
和 服 务
标识与可追溯性控制程序
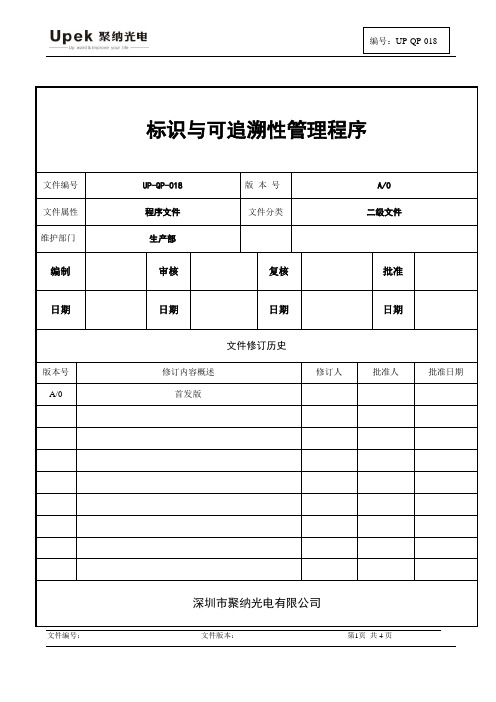
文件编号:文件版本:第1页共4页标识与可追溯性控制程序1 目的通过对物料、半成品、成品进行标识,防止造成误用,对有可追溯性要求的场合实现追溯。
2 适用范围适用于产品实现过程中物料和成品、半成品状态标识及可追溯性要求。
3 职责3.1供应链管理部负责对成品、收回的物料保管、标识并保持其标识状态。
3.2品管部负责对物料、成品进行检验和状态的标识以及对不良原因的追溯。
3.3生产部对过程中的物料、半成品、成品进行标识,负责生产过程中不良物料的收集和标识.3.4研发部对生产使用的仪器、设备使用状态和校验情况进行标识并予以保持,并提供生产需要的作业指导书.3.5 生产部对生产现场的物料、产品、工序、质量控制点进行标识。
4 工作程序4.1物料的标识4.1.1供应链管理部要求仓库的物料保持:包括生产厂商名称、物料编码、物料名称、数量、物料生产日期等贴于包装箱上。
4.1.2物料入库时以收料单为依据详细登记该批物料的名称、规格、批次、入库日期,做到帐、物相符,并将其放置在有待检标识的区域。
4.1.3生产部物料员上料前按照作业流程或作业指导书对照物料标识,将对应的物料装在料盒里,备好的物料应标识物料编号、规格、工位号.4.1.4无铅物料、辅料应摆放在专门的区域,使用时应标识绿色环保标签.4.1.5不良物料应保持来料的包装方式并标明物料名称、物料编码、生产厂商、数量等,单个不良物料应标识其不良现象和原因.如果供应商有要求的按照供应商要求执行.4.1.6 经检验判定不合格的物料直接在外箱贴上红色标签,标明不良原因,样品数量等情况,不良样品标识不良原因、位置,集中放在一个包装箱或包装袋内,外包装上标识内有不良品.4.2 生产过程产品的标识4.2.1SMT部产品转到生产部生产前应在外箱上做好标识并进行区域性转移。
4.2.2生产中QC检出的不合格品,在不合格部位贴上皱纹胶纸或箭头纸注明不良内容,由修理工修理,来不及修理的不合格品装入带有“不合格品”标识的周转箱内待处理,未经QC工位检测和不明状态的过程产品放白色现品票标识的周转箱中。
产品鉴别与追溯管理程序
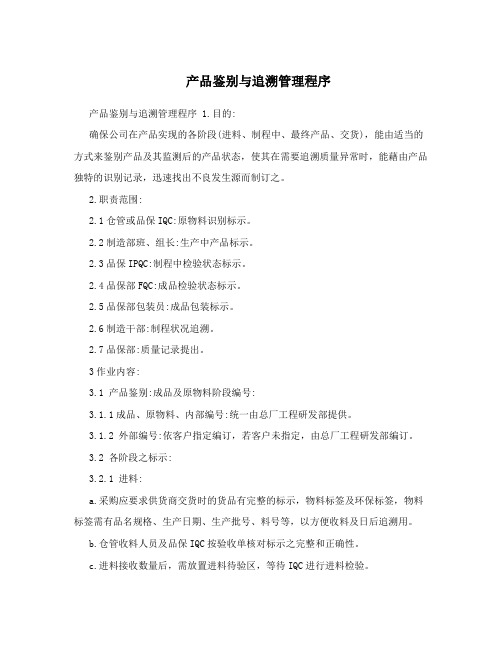
产品鉴别与追溯管理程序产品鉴别与追溯管理程序 1.目的:确保公司在产品实现的各阶段(进料、制程中、最终产品、交货),能由适当的方式来鉴别产品及其监测后的产品状态,使其在需要追溯质量异常时,能藉由产品独特的识别记录,迅速找出不良发生源而制订之。
2.职责范围:2.1仓管或品保IQC:原物料识别标示。
2.2制造部班、组长:生产中产品标示。
2.3品保IPQC:制程中检验状态标示。
2.4品保部FQC:成品检验状态标示。
2.5品保部包装员:成品包装标示。
2.6制造干部:制程状况追溯。
2.7品保部:质量记录提出。
3作业内容:3.1 产品鉴别:成品及原物料阶段编号:3.1.1成品、原物料、内部编号:统一由总厂工程研发部提供。
3.1.2 外部编号:依客户指定编订,若客户未指定,由总厂工程研发部编订。
3.2 各阶段之标示:3.2.1 进料:a.采购应要求供货商交货时的货品有完整的标示,物料标签及环保标签,物料标签需有品名规格、生产日期、生产批号、料号等,以方便收料及日后追溯用。
b.仓管收料人员及品保IQC按验收单核对标示之完整和正确性。
c.进料接收数量后,需放置进料待验区,等待IQC进行进料检验。
d.经检验合格者,贴合格标签签,注明检验者、检验日期和盖环保合格章。
e.经检验不合格者,贴不合格标签,仓库移转到退货区。
f.经判定为特采者,贴特采标签,并注明。
g.合格入库时,仓管贴进料季度颜色标签,以方便先进先出。
h.仓管发料依【工单发料表】作业。
3.2.2制程阶段:a.各项原物料于领发料时,应于账册内注明生产单号;在量产前各班组长需填写【人机追溯单】对人员、机台进行定位。
b.制程中用标示牌或标签标示,如注明机种、存放状况、生产状况等。
c.制程中在制品,使用蓝色胶框(盒)内,并标示清楚、区隔存放。
d.制程中成品(良品),使用绿色胶框(盒)内,并标示清楚、区隔存放。
e.制程中产生不良品时,放置于红色胶框(盒)内,并标示清楚、区隔存放。
ISO9001生产过程控制程序(含流程图)

生产过程控制程序(ISO9001-2015)1.0目的对直接影响产品质量的生产、安装和服务的过程进行有效识别及控制,确保这些过程在受控状态下进行,并对其进行持续不断地改进。
2.0范围本程序适用于公司内所有用于产品生产的过程。
3.0定义与术语特殊过程:a.产品质量不能通过后续的测量和监控加以验证的工序;b.产品质量需进行破坏性试验或采用昂贵的方法才能测量或只能进行间接监控的工序;c.该工序产品仅在产品使用或服务交付后不合格的质量特性才能暴露出来。
4.0职责a.研发部:负责产品工艺流程、工艺标准的制订与确认;b.生管课:负责生产计划采购计划的编制,以及生产进度及交货期的协调与控制工作;c.品管课:负责生产过程的巡回检查以及进行有关指标的检验,反馈,正确做出结论;d.采购课:负责生产原、辅材料的采购;e.生产各课:负责按生产计划要求进行准备、按工艺要求、设备操作规范要求安排生产;负责生产工具的设备的请购、维护及生产现场环境的维护;f.总务部:负责人员的招聘与培训。
5.0作业流程5.1生产计划生产单位及相关单接到生管的《生产排程》及每周《生产计划表》进行生产前的准备工作。
5.2生产前准备a.相关部门接到《生产排程表》及每周《生产计划表》后,依计划表时程,进行人员、生产设备、工装夹具、检测设备及所有有关此产品的工艺技术、检验文件的准备。
b.生产车间组长根据《生产排程表》及每周《生产计划表》安排员工到仓库领料。
c.在做生产准备同时,生产组长须事先对生产操作员工解说相关产品特性及质量要求水准,以利过程质量的控制。
5.3首件生产a.新、旧产品首件加工完毕后由生产组长填写《首件确认表》进行送检工作按《例行检验及成品确认检验控制程序》执行。
b.如新产品首检不合格,生产车间须通知相关研发技术人员、品管人员解决异常原因后,须重新生产首件交品管及研发部门确认。
c.如首检不合格,因异常原因影响生产计划时,生产车间须通知生管课,由生管课作出生产调整。
产品质量检验流程图

产品质量检验流程图产品质量检验流程图一、目的本流程图旨在明确产品质量检验的全过程,确保产品质量符合规定要求,以便公司在各个业务环节中有效控制和管理工作质量。
二、流程图1、原材料检验(1)采购部门根据需求进行原材料采购,并建立采购档案。
(2)原材料到货后,质量检验部门进行抽样检验,合格后方可入库。
(3)入库的原材料需进行标识,记录相关信息,保证可追溯性。
2、半成品检验(1)生产部门根据生产计划进行半成品生产。
(2)质量检验部门对半成品进行抽样检验,合格后方可进入下一道工序。
(3)对不合格的半成品,质量检验部门需出具不合格报告,并跟踪处理结果。
3、成品检验(1)生产部门完成成品生产后,将产品提交给质量检验部门进行成品检验。
(2)质量检验部门按抽样方案进行抽样检验,并出具检验报告。
(3)检验报告需记录详细信息,包括产品名称、规格、数量、检验日期、检验人员等。
4、不合格处理(1)若在检验过程中发现不合格品,质量检验部门需立即通知相关部门。
(2)相关部门需对不合格品进行评估,决定是否让步接收、返工或报废等处理措施。
(3)质量检验部门对处理结果进行跟踪,确保措施有效。
5、质量数据分析(1)质量检验部门定期收集检验数据,进行质量数据分析。
(2)根据数据分析结果,找出产品质量存在的问题和改进的空间,制定相应的改进措施。
(3)将质量数据分析结果反馈给相关部门,促进持续改进。
6、质量体系改进(1)根据质量数据分析结果和改进措施,对公司的质量管理体系进行评估和完善。
(2)对质量管理体系的改进需经过试运行和验证,确保改进的有效性。
(3)持续关注质量管理体系的运行情况,进行监控和调整,以提高公司的整体质量管理水平。
三、流程图说明本流程图旨在清晰地描述产品质量检验的过程,确保产品质量符合规定要求。
各个步骤紧密相连,形成一体化的质量检验流程。
在实际操作中,可根据具体情况对流程进行调整和优化。
总结:本流程图明确了产品质量检验的全过程,包括原材料检验、半成品检验、成品检验、不合格处理、质量数据分析和质量体系改进等环节。
物料的可追溯性管理制度

6流程图
无
7.0相关文件
《原料验收规程》
《包材验收规程》
8.0记录
《入库单》
《特采单》
《车间暂存入库单》
《待检单》
《出库单》
《领料单》
《合格单》
《不合格单》
9.0附件
无
制定
审查
批准
分发:生产部、仓库部、品控部、行政部各1份
仓管员按检验结果分类储存堆放分别存放放于合格品区不合格品区经检测不合格的原料由iqc填写不合格品处理报告原材料交品控经理审批处理意见如其他部门有异议时需由总经办或管理者代表做出最终决议
1.目的
通过对原材料、半成品和成品的出入库全过程进行标识和批次管理,确保当产品出现问题或需要时可实现追溯。
2.范围
适用于本公司仓库原材料、半成品和成品的批次管理和标识。
5.1批次编号的编制:按当天完成包装的生产日期后六位为批次,例如:2013年4月18日生产的产品,批次为130418。
5.2半成品和成品的批次编制由生产部完成,并填写《入库单》交仓管员。仓管员确认《入库单》和《车间暂存入库单》上名称、型号、数量和批次与实物一致,确认无误后签名确认输入仓手续,并加贴上《待检单》标识。
5.2原ห้องสมุดไป่ตู้料的标识
物料入厂时仓管员应核对供应商、数量、包装外观质量(无破损),放入待检区,对入库物料进行批次标识,并加上《待检单》,填写报检单通知IQC对物料进行检验。IQC对原料进行检验后在报检单上注明检验结果,将报检单交回仓管员,并在已检验原料上贴上相应的《合格单》或《不合格单》。仓管员按检验结果分类储存、堆放(分别存放放于合格品区,不合格品区)。
物料的可追溯性管理规定

编号的原则:编号由三部分组成,第一部分是物料类别代码(原料为R,包材为B,其他非生产物料为Q),第二部分为入库时的年月日,第三部分是入库时的流水号,从001,002,003…….依次类类推。例如2013年4月18日入库的第一批原料,批次编号为R001。
物料的可追溯性管理规定
1.目的
通过对原材料、半成品和成品的出入库全过程进行标识和批次管理,确保当产品ቤተ መጻሕፍቲ ባይዱ现问题或需要时可实现追溯。
2.范围
适用于本公司仓库原材料、半成品和成品的批次管理和标识。
3.定义
可追溯性:根据记载的批次、数量信息等准确追踪产品所用的全部物料信息。
4.职责
仓库部:负责对仓库原材料的批次进行标识和管理,负责对半成品和成品的产品数量和批次的填写和核实。
生产部:负责对半成品/成品进行批次标识制定和管理。
品控部:负责批次管理的监控。
5.工作程序
管理原则:对物料运用批次进行跟踪,对入仓的物料按批次进行管理,保证产品实现可追溯性。
原材料的标识
物料入厂时仓管员应核对供应商、数量、包装外观质量(无破损),放入待检区,对入库物料进行批次标识,并加上《待检单》,填写报检单通知IQC对物料进行检验。IQC对原料进行检验后在报检单上注明检验结果,将报检单交回仓管员,并在已检验原料上贴上相应的《合格单》或《不合格单》。仓管员按检验结果分类储存、堆放(分别存放放于合格品区,不合格品区)。
如发料时需要发放至少两个批次的物料时,则不同批次的原料分开填写,分别记录批次和数量。
半成品和成品的批次管理:
批次编号的编制:按当天完成包装的生产日期后六位为批次,例如:2013年4月18日生产的产品,批次为130418。
质量追溯体系建设方案

质量追溯体系建设方案一、引言质量追溯体系是企业对产品质量的全过程管理和控制的重要手段,通过建立起一套完整的质量追溯体系,可以帮助企业实现对产品质量的溯源和追踪,加强质量管控,提升产品质量和客户满意度。
本文档将介绍质量追溯体系的建设方案,包括流程设计、信息采集和管理等方面的内容。
二、流程设计1. 质量追溯流程质量追溯流程是质量追溯体系的核心,它主要包括以下环节:1.产品信息采集:在产品制造过程中,记录关键工序的输入、输出和工艺参数等相关信息,对每一个产品都建立起唯一的标识。
2.质量数据采集:对每个关键工序的质量数据进行采集,包括工艺参数、检测结果等,并与产品进行关联。
3.数据存储和管理:将采集到的质量数据进行存储和管理,建立起完整的质量数据库,方便后续的追溯和分析。
4.质量追溯:在产品出现质量问题时,可以通过质量追溯流程,快速定位问题源头,并采取相应的纠正措施。
2. 流程图下图展示了质量追溯流程的基本流程图:graph TD;A[产品信息采集] -- 关联标识 --> B[质量数据采集]B -- 存储和管理 --> C[质量数据库]C -- 追溯和分析 --> D[质量追溯]D -- 纠正措施 --> E[质量改善]三、信息采集和管理1. 产品信息采集产品信息采集主要包括以下内容:•产品型号、批次、生产时间等基本信息;•关键工序的输入和输出信息;•工艺参数和设备运行状态等相关信息。
通过对产品信息的采集,可以为质量追溯提供准确的数据依据,方便后续的追溯和分析工作。
2. 质量数据采集质量数据采集主要包括以下内容:•关键工序的质量检测结果;•工艺参数的采集和记录;•不良品数和不良现象的统计。
质量数据的采集应确保数据的准确性和完整性,可以通过自动化设备和传感器来实现数据的实时采集。
3. 数据存储和管理质量数据的存储和管理是质量追溯体系中非常重要的一环,可以采用数据库来存储质量数据,确保数据的安全性和可靠性。