精益生产——持续改善7步骤精品PPT课件
合集下载
精益管理七大流程图生产现场课件
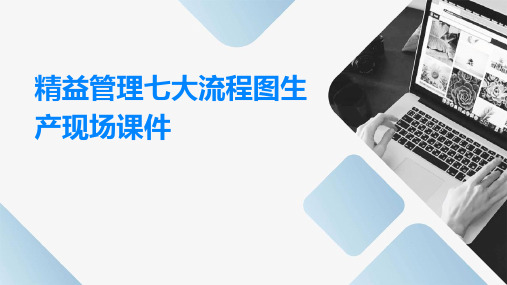
意义
物料流程图能够帮助企业全面了解生产现场的物料流动情况 ,发现和改善物料管理中的问题,提高生产效率,降低成本 ,提升产品质量。
物料流程图的组成要素
设备
各种生产设备、搬 运设备等。
信息流
生产过程中的各种 信息,如计划、调 度、库存等。
物料
包括原料、半成品 、成品等在生产过 程中流动的物料。
人员
现场操作人员、管 理人员等。
对绘制好的流程图进行审核和 优化,确保流程图的准确性和 易读性。
现场信息管理提升措施
建设完善的信息管理系统, 实现信息的自动化采集、存 储、传递和处理,提高信息
处理效率。
1
加强现场信息的实时监控和 预警,及时发现和解决问题 ,避免信息流动中的瓶颈和
延误。
对现场管理人员进行信息管 理的培训和素质提升,提高 其对信息管理的重视度和能 力水平。
原则
精益管理基于五大原则,包括定义价 值、识别价值流、流动、拉动和追求 卓越。这些原则指导企业如何优化流 程、减少浪费,并持续改进。
精益思想与生产管理
以客户需求为导向
精益思想强调通过深入理解客户 需求,避免过度生产和库存积压
,使生产紧密围绕需求进行。
消除浪费
精益思想倡导不断识别和消除生产 过程中的浪费,如等待、运输、过 度加工、库存、不必要的动作等, 以提高效率。
促进持续改进
七大流程图是持续改进的 基础工具,企业可在此基 础上不断寻求提升,实现 精益管理的长远目标。
七大流程图的相互关系
互补关系
七大流程图各有侧重,但彼此之 间存在互补关系,综合运用能更 好地满足生产现场的管理需求。
流程衔接
七大流程图在生产过程中相互衔 接,形成一个完整的管理体系,
物料流程图能够帮助企业全面了解生产现场的物料流动情况 ,发现和改善物料管理中的问题,提高生产效率,降低成本 ,提升产品质量。
物料流程图的组成要素
设备
各种生产设备、搬 运设备等。
信息流
生产过程中的各种 信息,如计划、调 度、库存等。
物料
包括原料、半成品 、成品等在生产过 程中流动的物料。
人员
现场操作人员、管 理人员等。
对绘制好的流程图进行审核和 优化,确保流程图的准确性和 易读性。
现场信息管理提升措施
建设完善的信息管理系统, 实现信息的自动化采集、存 储、传递和处理,提高信息
处理效率。
1
加强现场信息的实时监控和 预警,及时发现和解决问题 ,避免信息流动中的瓶颈和
延误。
对现场管理人员进行信息管 理的培训和素质提升,提高 其对信息管理的重视度和能 力水平。
原则
精益管理基于五大原则,包括定义价 值、识别价值流、流动、拉动和追求 卓越。这些原则指导企业如何优化流 程、减少浪费,并持续改进。
精益思想与生产管理
以客户需求为导向
精益思想强调通过深入理解客户 需求,避免过度生产和库存积压
,使生产紧密围绕需求进行。
消除浪费
精益思想倡导不断识别和消除生产 过程中的浪费,如等待、运输、过 度加工、库存、不必要的动作等, 以提高效率。
促进持续改进
七大流程图是持续改进的 基础工具,企业可在此基 础上不断寻求提升,实现 精益管理的长远目标。
七大流程图的相互关系
互补关系
七大流程图各有侧重,但彼此之 间存在互补关系,综合运用能更 好地满足生产现场的管理需求。
流程衔接
七大流程图在生产过程中相互衔 接,形成一个完整的管理体系,
精益生产——持续改善7步骤

设备的闲置,设备的空转,计划外 的停机,不必要的测试,不正确的 操作……
过度搬运,过度库存,过量文案工 作,损坏或丢失物品……
04
加工本身的浪费
05
库存的浪费
06
动作的浪费
07
不良品生产的浪费
没完没了的修饰,额外的加工 工序,生产效率降低,较长的 制造周期……
额外大量返工,额外仓储与搬 运,过量文案工作,信息流程 阻塞,盘点困难……
什么是根本原因?
根本原因,又可以分为系统原因和执行原因两种,系统原因即流程、标准
的问题;执行原因即解决问题是在能力范围之内但不作为。我们应该先解
决系统原因,再解决执行原因,系统出现问题,就建立、完善标准或改善 流程;执行出现问题则需通过防呆措施来解决,防呆措施又包括两方面: 做错比做对难,做错很容易被发现。
以上四个过程不是运行一次就结束,而是周而复始的进行 一个循环完了,解决了一些问题,未解决的问题进入下一个循环。
THANK YOU
参与5S,享受5S
7
追求卓越
A-Action处理
对检查的结果进行处理,并标准化 总结失败的教训,归纳没有解决的问题
P
P-Plan计划
包括方针和目标的确定, 以及活动规划的制定。
A
20%
D
D-Do执行
根据已知信息,设计具体方案 再根据设计的方案,进行具体运作
C-Check检查
总结执行计划的结果 明确效果,找出问题
C
02
SECOND
为何要持续改善
狮子和羚羊的故事
在非洲大草原上生活着狮子和羚羊,每天早
上醒来,羚羊想的第一件事就是:我必须跑
得比最快的狮子还要快,否则我就会被吃掉。 而狮子也同时在想:我必须跑得比最慢的羚 羊快,否则我会被饿死。弱肉强食、优胜劣
精益持续改善PPT课件
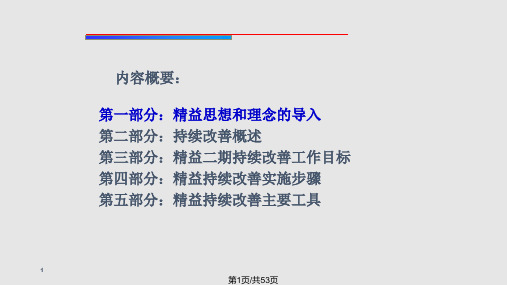
2.创造易于劳动的工作场所 不断发现问题点 不断进行改善 使劳动场所趋于完美
3.提高工作场所的活力 提案活动加强上下沟通 (上司与下属
提案者之间)
4.创造出成果 通过改善使企业直接获得效益
第14页/共53页
15
第二部分:持续改善概述
7、“改善提案” 作用和意义
(1)改善效果 改善作业方法 创造易于劳动的场所 降低成本 提高安全意识 提高品质 事务的合理化,高效率化
30
第30页/共53页
第四部分:持续改善活动实施步骤
2、持续改善工作要点
改善重在观念建立 改善重在全员参与 改善重在过程管理 改善重在持续不断
持续改善是以上模块内部能力的提升,是 模块之间交互的加强,可以说持续改善决定精 益总体推进的成败。
22
第22页/共53页
3、持续改善专项方案
持续改善
改善手法运用
目标设定
培养员工的改善意识 消除浪费、降低成本 持续改善、提高生产 效率 改善环境
培训工作开展
■改善意识培训 ■员工能力开发
现场改善
■生产现场改善 ■物流改善 ■交货期改善
20
第20页/共53页
第三部分:精益二期持续改善专项工作目标
2、持续改善在精益推进中的作用和地位
实现精益
生产管理 TPM
物流
5S/目视化 品质管理
21
第21页/共53页
第三部分:精益二期持续改善专项工作目标
2、持续改善在精益推进中的作用和地位 精益是体系建设,是系统工程,涉及生产、
工艺、设备、品质、物流、现场、成本、人力 资源、5S与目视化等方面。
27
第27页/共53页
第四部分:持续改善活动实施步骤
精益生产现场管理和改善ppt课件
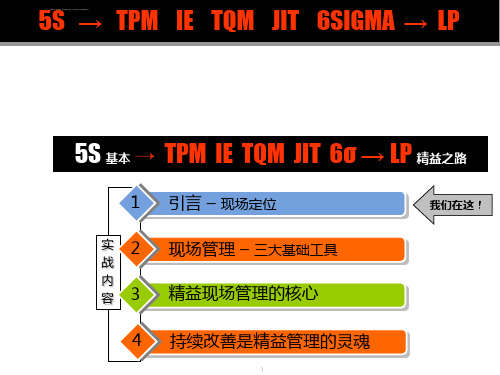
目视工作现场的建立
讨论 目视化工作现场的建立
现在有哪些目视管理
识别哪些地方需要建立目视管理
讨论确定如何和怎样去建立目视管理
实施和跟踪
5S 基本 → TPM IE TQM JIT 6σ → LP 精益之路
实 战 内 容
看板是如何提升管理的精度?
1
看板有哪些,如何确定?
2
围绕看板,构建目标管理运作平台
3
管理看板是发现问题、解决问题的非常有效且直观的手段
确定谁将要做什么 使之目视控制 在适当的位置进行目视控制
目视化工作现场的建立
制订目视化控制计划
协调和标准化目视控制
创建和实施目视控制
检验和修正目视控制
建立目视化控制持续改进计划
在流程中自己进行检查控制 邀请另外一个团队审计目视控制 邀请参与各方审计控制设备 按要求休整目视控制设备
目视化工作现场的建立
人
机
料
法
环
目视管理常用工具及制作要领 (二)、目视管理工具的基本要素
1、提高工作环境的改善 2、提高安全管理的措施 3、提高品质管理的水准 4、提高设备TPM的水准 5、提高现物管理精度
通过彻底5S的实施 安全、舒适的工作环境,人人都按标准办 大家都来做改善
目视管理5项直接效果及其常见措施
制订目视化控制计划
协调和标准化目视控制
创建和实施目视控制
检验和修正目视控制
建立目视化控制持续改进计划
确定后续活动 确定谁在什么时候将要做什么 决定谁将得到信息及如何的到 实施改进计划
目视工作现场的建立
必须取得高层领导的支持
要从流程和人/机/料/法/环方面综合考虑
要坚持用同一个标准
讨论 目视化工作现场的建立
现在有哪些目视管理
识别哪些地方需要建立目视管理
讨论确定如何和怎样去建立目视管理
实施和跟踪
5S 基本 → TPM IE TQM JIT 6σ → LP 精益之路
实 战 内 容
看板是如何提升管理的精度?
1
看板有哪些,如何确定?
2
围绕看板,构建目标管理运作平台
3
管理看板是发现问题、解决问题的非常有效且直观的手段
确定谁将要做什么 使之目视控制 在适当的位置进行目视控制
目视化工作现场的建立
制订目视化控制计划
协调和标准化目视控制
创建和实施目视控制
检验和修正目视控制
建立目视化控制持续改进计划
在流程中自己进行检查控制 邀请另外一个团队审计目视控制 邀请参与各方审计控制设备 按要求休整目视控制设备
目视化工作现场的建立
人
机
料
法
环
目视管理常用工具及制作要领 (二)、目视管理工具的基本要素
1、提高工作环境的改善 2、提高安全管理的措施 3、提高品质管理的水准 4、提高设备TPM的水准 5、提高现物管理精度
通过彻底5S的实施 安全、舒适的工作环境,人人都按标准办 大家都来做改善
目视管理5项直接效果及其常见措施
制订目视化控制计划
协调和标准化目视控制
创建和实施目视控制
检验和修正目视控制
建立目视化控制持续改进计划
确定后续活动 确定谁在什么时候将要做什么 决定谁将得到信息及如何的到 实施改进计划
目视工作现场的建立
必须取得高层领导的支持
要从流程和人/机/料/法/环方面综合考虑
要坚持用同一个标准
精益生产——持续改善7步骤PPT课件

15
4 合理化建议
精选ppt
16
合理化建议
以积极的心态,通过一定的方式 向一定的组织或人员,以书面形式提出。
积少成多
企业的管理 是“点点滴滴合理化”的过程
全员努力
发挥全员智慧和潜力 推动企业进步
员工作用ቤተ መጻሕፍቲ ባይዱ
企业员工 对现场和本职最清楚和了解
增进交流
激励员工 参与企业内部的沟通和交流
不良点标签和合理化建议,是现场管理最有效的工具
精选ppt
什么是根本原因?
根本原因,又可以分为系统原因和执行原因两种,系统原因即流程、标准 的问题;执行原因即解决问题是在能力范围之内但不作为。我们应该先解 决系统原因,再解决执行原因,系统出现问题,就建立、完善标准或改善 流程;执行出现问题则需通过防呆措施来解决,防呆措施又包括两方面: 做错比做对难,做错很容易被发现。
05 库存的浪费
额外大量返工,额外仓储与搬 运,过量文案工作,信息流程 阻塞,盘点困难……
06 动作的浪费
过长的行走距离,人员或设备 的等候,寻找工具或材料,过 度伸展或弯腰……
07 不良品生产的浪费
材料不良,加工不良,生产不 良……
精选ppt
11
2 小组活动
精选ppt
12
小组活动
通过小组活动来实现5S和持续改善 所追求的,激发人的积极性,全员 的参与和全面提高生产领域的效率
10
生产现场常见的浪费
01 过盈生产
过量的原材料,额外的工作,过度 占用空间,信息管理复杂化,过度 搬运与处理……
02 等待的浪费
设备的闲置,设备的空转,计划外 的停机,不必要的测试,不正确的 操作……
03 搬运的浪费
4 合理化建议
精选ppt
16
合理化建议
以积极的心态,通过一定的方式 向一定的组织或人员,以书面形式提出。
积少成多
企业的管理 是“点点滴滴合理化”的过程
全员努力
发挥全员智慧和潜力 推动企业进步
员工作用ቤተ መጻሕፍቲ ባይዱ
企业员工 对现场和本职最清楚和了解
增进交流
激励员工 参与企业内部的沟通和交流
不良点标签和合理化建议,是现场管理最有效的工具
精选ppt
什么是根本原因?
根本原因,又可以分为系统原因和执行原因两种,系统原因即流程、标准 的问题;执行原因即解决问题是在能力范围之内但不作为。我们应该先解 决系统原因,再解决执行原因,系统出现问题,就建立、完善标准或改善 流程;执行出现问题则需通过防呆措施来解决,防呆措施又包括两方面: 做错比做对难,做错很容易被发现。
05 库存的浪费
额外大量返工,额外仓储与搬 运,过量文案工作,信息流程 阻塞,盘点困难……
06 动作的浪费
过长的行走距离,人员或设备 的等候,寻找工具或材料,过 度伸展或弯腰……
07 不良品生产的浪费
材料不良,加工不良,生产不 良……
精选ppt
11
2 小组活动
精选ppt
12
小组活动
通过小组活动来实现5S和持续改善 所追求的,激发人的积极性,全员 的参与和全面提高生产领域的效率
10
生产现场常见的浪费
01 过盈生产
过量的原材料,额外的工作,过度 占用空间,信息管理复杂化,过度 搬运与处理……
02 等待的浪费
设备的闲置,设备的空转,计划外 的停机,不必要的测试,不正确的 操作……
03 搬运的浪费
DMAIC精益生产持续改善PPT课件

世界级的质量是公司生存的重要机会 18
困惑?------我们应该怎么做
1. 开展与业务密切相关的项目 2. 高层领导的重视--自上而下的推动 3. 全员参与的培训和实践--边学边做 4. 必要的投入带来高额的回报
开展6 Sigma 的关键成功因素 19
Equipment Delivery Quality 设备交货的质量 Modality Installation And Warranty Costs 装机和保修的成本 Design For Six Sigma 用Six Sigma设计 Uptime 开机时间
6 Sigma-世界 一 流 公 司 的 工 作 方 17
为什么要迈向6 Sigma?
• 代表了几近完美的质量水平 • 低成本的投入带来高质量的产出 • 使工作更轻松,更容易
• 许多公司 (Motorola, Allied Signal) 都通过 6 sigma 显著
地提高了质量水平 /客户满意度/生产效率 • 在激烈的经营环境中具竞争性优势
MCAConeonaantlsyrtuozrleorel
• Translated Learning 经验转化-学习
• Celebrate!
小组庆祝
8
两条路径供选择 : 2) 新过程
持续改进的过程
DFSS
用六西格玛设计
新过程的发展 设计六西格玛的过程能力
9
DMADV过程
DMADV方法的五个阶段
确立目标,并加以展开 了解客户需求,并明确可量化指标的设计要求(CTQ)
第一章
6 Sigma管理模式的实施方法
1
什么是六西格玛
什么是六西格玛?
➢提高质量的方法
六西格玛是基于统计的质量项目. 它是一套改善过程控制的严格的方法体系.
困惑?------我们应该怎么做
1. 开展与业务密切相关的项目 2. 高层领导的重视--自上而下的推动 3. 全员参与的培训和实践--边学边做 4. 必要的投入带来高额的回报
开展6 Sigma 的关键成功因素 19
Equipment Delivery Quality 设备交货的质量 Modality Installation And Warranty Costs 装机和保修的成本 Design For Six Sigma 用Six Sigma设计 Uptime 开机时间
6 Sigma-世界 一 流 公 司 的 工 作 方 17
为什么要迈向6 Sigma?
• 代表了几近完美的质量水平 • 低成本的投入带来高质量的产出 • 使工作更轻松,更容易
• 许多公司 (Motorola, Allied Signal) 都通过 6 sigma 显著
地提高了质量水平 /客户满意度/生产效率 • 在激烈的经营环境中具竞争性优势
MCAConeonaantlsyrtuozrleorel
• Translated Learning 经验转化-学习
• Celebrate!
小组庆祝
8
两条路径供选择 : 2) 新过程
持续改进的过程
DFSS
用六西格玛设计
新过程的发展 设计六西格玛的过程能力
9
DMADV过程
DMADV方法的五个阶段
确立目标,并加以展开 了解客户需求,并明确可量化指标的设计要求(CTQ)
第一章
6 Sigma管理模式的实施方法
1
什么是六西格玛
什么是六西格玛?
➢提高质量的方法
六西格玛是基于统计的质量项目. 它是一套改善过程控制的严格的方法体系.
CIP-持续改善PPT教学课件
2020/12/10
18
7.确定解决方案
• 对消除浪费的每条改进方案进行分析, 以确定其可行性,通过效益比较确定最 佳解决方案。
• 方案选优是一个决策过程,选优方案一 定要有可行性。
2020/12/10
19
8.制订措施表
• 经全体成员同意后,把最佳方案描述在 统一规定的措施表上。
• 确定具体的工作任务。
• 为什幺发生故障 线路板烧坏
• 为什幺线路板烧坏 降温不好
• 为什幺降温不好
空气流通不畅
• 为什幺空气流通不畅 数控机床外空气进不去
• 为什幺空气进不去 滤网上结尘
2020/12/10
24
通过追根究底地提问,找到了问题的症结 ,确认故障原因是:数控机床下面有一只 滤网,是防灰尘的。灰尘积在滤网上使外 面空气不能进入机床,从而使机床内空气 散热不良,温度升高,造成线路板烧坏。 3)CIP措施:每半个月清扫一次滤网 4)CIP成果:备件每年节约10个,设备故 障率下降83%.
2020/12/10
12
1.小组活动的准备
• 一切改善活动都是由人进行的。 • 包括确定活动人员、改进流程的范围、
活动场所及其布置等,主要由主持者负 责。
2020/12/10
13
2.小组活动的引言
• 主持者首先要向小组成员说明CIP的含义 、目的和具体工作方法,并激发全体成 员参与到CIP活动中来。
2020/12/10
20
9.实施措施
• 要求参加人员共同负责,并亲自动手, 尽快解决
• 动手解决问题是关键。
2020/12/10
21
10.汇报成果
• 每次活动的有形成果都要用金钱来计算 ,无形成果应说明其改进的意义。
精益生产现场改善PPT课件
物料
工具
第10页/共15页
物流距离
物流布局应以总物流负载 最小为最佳方案(总物 流负载=距离*对应的物 流量的总和)。
十二 设备优化与摆放
1>按工序布置 2>“U”形、逆时针布置 3>设备布置“三不”原则(不落地生根,不寄人篱下, 不离群索居) 4>设备间距小 5>设备功能够用就好(不追求大而全)
第11页/共15页
十三 产线布局优化
第12页/共15页
传统流水线
适合大订单,大 批量生产。
单元生产线
适合大小订单, 小批量生产。
精简CELL线 适合少量多样,
柔性生产。
十四 现场员工关系管理的秘诀
和谐的员工关系
• 员工工作责任心强 • 工作积极性高 • 企业生产效率高 • 员工稳定,流失率低 • 管理层和员工有效沟通
提高流程的效率,改善平面布置图 去掉时间浪费,缩短生产周期
第9页/共15页
加工 搬运 检查
停滞
十一 物流距离的优化原则
传统物流
供货商
大仓库
IQC
线边仓
生产线
物料员
成品仓
客户
精益物流 供货商
供货商端驻点IQC
生产线
成品仓
客户
三角形原理
物料或工具的放置点、产 品组装点、操作者的 位置形成的三角形的 边长越小越好。
简化(Simplify):经过取消、合并、重组之后,再对该项工作作进一步更深
入的分析研究,使现行方法尽量地简化,以最大限度地缩短作业时间,提高工作效率。
第6页/共15页
八 动作经济的16原则
1
关于人体动作方面: 1 双手并用原则 2 对称反向原则 3 排除合并原则 4 降低动作等级原则 5 减少动作限制原则 6 避免动作突变原则 7 保持轻松节奏原则 8 利用惯性原则 9 手脚并用原则
精益生产现场管理和改善ppt课件
34
目视工作现场的建立
在实施前得到相关方面的认同 要坚持用同一个标准 要从流程和人/机/料/法/环方面综合考虑 必须取得高层领导的支持
35
目视工作现场的建立
讨论 目视化工作现场的建立
实施和跟踪 讨论确定如何和怎样去建立目视管理 识别哪些地方需要建立目视管理 现在有哪些目视管理
36
5S 基本 → TPM IE TQM JIT 6σ → LP 精益之路
透明化、显现化、立即化
作业标准化
基准化 管理基础
透明化 降低难度
管理看板
看板化 增加精度
13
什么叫目视管理
工作区域不解自明 自动调节/自我改进 使问题无处可藏
3
标准化
原 视觉化 则 透明化
14
目视管理的理念
• 哲学——促进[走动管理]的效果 • 目的——塑造[一目了然]的工作场所
企业信息中心
Business Objectives
1. 在流程中自己进行检查控制 2. 邀请另外一个团队审计目视控制 3. 邀请参与各方审计控制设备 4. 按要求休整目视控制设备
33
目视化工作现场的建立
建立目视化控制持续改进计划 检验和修正目视控制 创建和实施目视控制 协调和标准化目视控制 制订目视化控制计划
1. 确定后续活动 2. 确定谁在什么时候将要做什么 3. 决定谁将得到信息及如何的到 4. 实施改进计划
•对企业的影响
– 减少(时间和精力上的)浪费,提高劳动生产率 – 营造“以人为本”的工作环境,提高可靠性和稳定性 – 突出工作场所危险,提高安全性和减少停机时间 – 为业绩改善政策和做法提供支持(如:标准作业、6S、
快速换线、预防性维护)
•对员工的影响
持续改进工作“七步法”
图2 PDCA小循环
第一步: 现状把握的方法。
现状把握------找出问题所在点
(1)根据问题意识, 从“实际值”与“期待值”的差异中敏 锐洞察问题点。(图3)
计划完成率
★ 20%的差异
期待值: 100%
90% 85%
实际值: 80%
80% 时间
图3 从“实际值”与“期望值”的差异中把握现 状
(2)依据公司的方针目标, 以及本部门职责、本岗位的要 求, 对比现状找出问题点。(见图4)
4 对定位孔彻底清扫,确保 孔中无灰尘
◎
【冲压车间前端盖铆接不合格的改进案例】
一、现状把握
(1)近期冲压车间前端盖板铆接不合格件数上升。(见图16) (2)因前盖板铆接不合格, 组装线多次停线, 而且前盖板采购 单价高, 发生不合格后无法修复, 报废金额大。(见图17)
不合格
41 15
8
停线(分)
16
55 28
5月 6月 7月 图16
5月 6月 7月 图17
停机时间126分钟,具体停 机原因:
60 40 15 11
故障 物料 准备 其他
图13 柏拉图工具
(5)针对问题的类型不同, 展开对应分析。(见图14)
突发异常
慢性不良
(上限) (下限)
周期异常 图14 突发异常、周期异常和慢性不良
第四步: 研讨对策的办法
研讨对策------研究问题解决措施的办法
16 8
28 15
5月 6月
改进前 55
41
改进后
3 0
7月
8月
图23 效果确认
2 0
9月
2 0
10月
七、效果巩固
- 1、下载文档前请自行甄别文档内容的完整性,平台不提供额外的编辑、内容补充、找答案等附加服务。
- 2、"仅部分预览"的文档,不可在线预览部分如存在完整性等问题,可反馈申请退款(可完整预览的文档不适用该条件!)。
- 3、如文档侵犯您的权益,请联系客服反馈,我们会尽快为您处理(人工客服工作时间:9:00-18:30)。
02 等待的浪费
设备的闲置,设备的空转,计划外 的停机,不必要的测试,不正确的 操作……
03 搬运的浪费
过度搬运,过度库存,过量文案工 作,损坏或丢失物品……
04 加工本身的浪费
没完没了的修饰,额外的加工 工序,生产效率降低,较长的 制造周期……
05 库存的浪费
额外大量返工,额外仓储与搬 运,过量文案工作,信息流程 阻塞,盘点困难……
单点课是否能发挥效果,领导的重视很重要。
21
7 追求卓越
22
A-Action处理
对检查的结果进行处理,并标准化 总结失败的教训,归纳没有解决的问题
A
20%
C-Check检查
总结执行计划的结果 明确效果,找出问题
P C
P-Plan计划
包括方针和目标的确定, 以及活动规划的制定。
D
D-Do执行
根据已知信息,设计具体方案 再根据设计的方案,进行具体运作
15
4 合理化建议
16
合理化建议
以积极的心态,通过一定的方式 向一定的组织或人员,以书面形式提出。
积少成多
企业的管理 是“点点滴滴合理化”的过程
全员努力
发挥全员智慧和潜力 推动企业进步
员工作用
企业员工 对现场和本职最清楚和了解
增进交流
激励员工 参与企业内部的沟通和交流
不良点标签和合理化建议,是现场管理最有效的工具
20
单点课
由员工自己编写 用于交流经验和自我学习使用
OPL的目的
1、提高成员的热情和参与度 2、帮助交流和分享有关知识 3、随时为团队提供重要信息
OPL的准则
由员工自己挖掘、编写 向其他员工解释
与他人共同讨论以改进提高
OPL的类型
基础知识 改善案例 问题解决
OPL的来源
日常故障处理 现场的改善 操作员的妙手偶得
You Know, The More Powerful You Will Be
Thank You
在别人的演说中思考,在自己的故事里成长
Thinking In Other People‘S Speeches,Growing Up In Your Own Story
讲师:XXXXXX XX年XX月XX日
1
目录content
01持续改善的概念 02持续改善的必要性 03持续改善7步骤
2
FIRST
01 何为持续改善
3
持续改善
Kaizen方法最初是一个日本管理概念,指逐渐、 连续地增加改善。是日本持续改善之父今井正明 在《改善——日本企业成功的关键》一书中提出 的。Kaizen意味着改进,涉及每一个人、每一环 节的连续不断的改进,从最高的管理部门,管理 人员到一线工人。“持续改善”的策略是日本管 理部门中最重要的概念,是日本人竞争成功的关 键。
06 动作的浪费
过长的行走距离,人员或设备 的等候,寻找工具或材料,过 度伸展或弯腰……
07 不良品生产的浪费
材料不良,加工不良,生产不 良……
11
2 小组活动
12
小组活动
通过小组活动来实现5S和持续改善 所追求的,激发人的积极性,全员 的参与和全面提高生产领域的效率
营造宽松气氛,避免主题不清 接受各种观点,以开放式进行讨论 活动形式丰富多样,并做好记录
5W1H法
Why——为什么 What——什么 Who——谁 Where——哪里 When——什么时候 How——怎么样
ECRS法
E——Elimination取消 C——Combination合并 R——Rearrangement重排 S——Simplification简化
19
19
6 标准化、单点课
以上四个过程不是运行一次就结束,而是周而复始的进行 一个循环完了,解决了一些问题,未解决的问题进入下一个循环。
23
写在最后
经常不断地学习,你就什么都知道。你知道得越多,你就越有力量 Study Constantly, And You Will Know Everything. The More
4
SECOND
02 为何要持续改善
5
狮子和羚羊的故事
在非洲大草原上生活着狮子和羚羊,每天早 上醒来,羚羊想的第一件事就是:我必须跑 得比最快的狮子还要快,否则我就会被吃掉。 而狮子也同时在想:我必须跑得比最慢的羚 羊快,否则我会被饿死。弱肉强食、优胜劣 汰的自然法则在这里体现得淋漓尽致。 无论是狮子还是羚羊,每天都必须提高自己 的奔跑速度,否则就无法生存。
什么是根本原因?
根本原因,又可以分为系统原因和执行原因两种,系统原因即流程、标准 的问题;执行原因即解决问题是在能力范围之内但不作为。我们应该先解 决系统原因,再解决执行原因,系统出现问题,就建立、完善标准或改善 流程;执行出现问题则需通过防呆措施来解决,防呆措施又包括两方面: 做错比做对难,做错很容易被发现。
活动目的 活动准则
领导是关键
组建活动小组,确定活动日程 选择活动主,控制活动时间 制订活动计划,回报活动成果
如何活动
我们将要做什么,为什么要这么做 我们要达到什么目的,如何达到 活动顺序是什么,期待的结果是什么
13
3 4M、5Why分析
14
5Why 分析法
为了解决反复出现的现场管理难题,如:1S 活动中反复出现的非必需品、2S活动中必需 品目视化暴露的问题、3S活动中发现的跑冒 滴漏、影响设备OEE的问题……我们可以采 用5Why分析法。通过5Why分析,对问题进 行刨根问底、追根溯源,找到问题的根本原 因,从源头上解决问题。
为了生存,我们必须改善。
6
改善的关键
改善重在观念建立 改善重在全员参与 改善重在过程管理 改善重在持续不断
7
THIRD
03 如何持续改善
8
1 锁定浪费
9
什么是浪费?
浪费=活动+低效工作
活动:不为产品创造价值的所有行为。 工作:为产品创造附加价值的行为
10
生产现场常见的浪费
01 过盈生产
过量的原材料,额外的工作,过度 占用空间,信息管理复杂化,过度 搬运与处理……
17
5 改善
18
改善的技法
头脑风暴法
一个人作为领导提出问题后 其他人自由发表自己的idea 原则:1、严禁批评
2、自由奔放 3、量比质重要 4、借用别人的想法
检查单法
在实际解决问题的过程中,根 据需要改善的对象或需要解决 的问题,先列出有关问题,再 加以讨论、研究,从中获得解 决问题的方法和改善的思路