重庆交通大学工程造价外文翻译
外文翻译----工程造价管理浅论
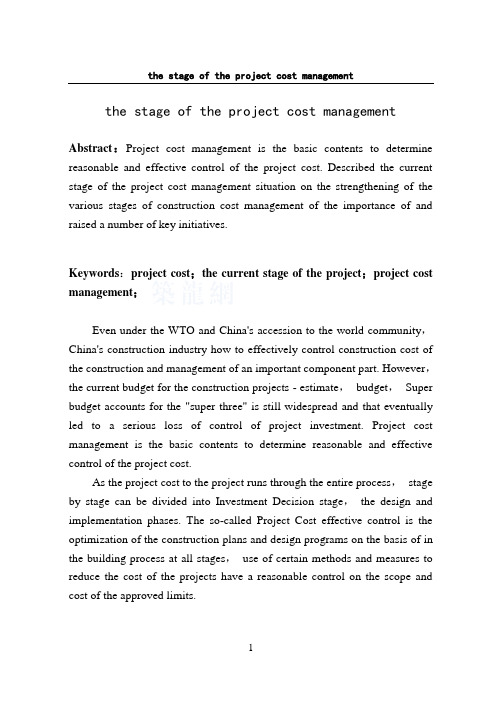
the stage of the project cost managementAbstract:Project cost management is the basic contents to determine reasonable and effective control of the project cost. Described the current stage of the project cost management situation on the strengthening of the various stages of construction cost management of the importance of and raised a number of key initiatives.Keywords:project cost;the current stage of the project;project cost management;Even under the WTO and China's accession to the world community,China's construction industry how to effectively control construction cost of the construction and management of an important component part. However,the current budget for the construction projects - estimate,budget,Super budget accounts for the "super three" is still widespread and that eventually led to a serious loss of control of project investment. Project cost management is the basic contents to determine reasonable and effective control of the project cost.As the project cost to the project runs through the entire process,stage by stage can be divided into Investment Decision stage,the design and implementation phases. The so-called Project Cost effective control is the optimization of the construction plans and design programs on the basis of in the building process at all stages,use of certain methods and measures to reduce the cost of the projects have a reasonable control on the scope and cost of the approved limits.Engineering and cost management work of the current status of project cost management system was formed in the 1950s,1980s perfect together. Performance of the country and directly involved in the management of economic activities. Provisions in the design stage to different estimates or budget preparation as well as government; Nothing relevant departments to formulate a budget,content,methods and approval,the budget will provide the fixed cost of equipment and materials and fixed price of the budget preparation,approval,management authority,and so on.With the historical process,after recovery,reform and development,formed a relatively complete budget estimate of quota management system. However,as the socialist market economic development,the system's many problems have also exposed. Generally speaking,the budget estimate is based on direct participation in the management of national economic activity as a precondition. Enterprise is not the actual economic entities. Due to the characteristics of the planned economy,and,at the time under the conditions of productivity,will inevitably become a shortage in the economy.In severe shortage of commodities under the conditions,as long as a certain level of investment,will be certain outputs. In this environment,the project planning and technical argumentation there can be no economic analysis. State control of the project cost constitute key factors equipment and materials prices,wages and taxes of artificial distribution. In this relatively stable economic environment,the budget estimate for the system approved project cost,help the government to carry out investment plans to play a major role.As the socialist market economic system established,requires us to predict project investment and control. In recent years,international investment project developed to the requirements of prior pre-control and in the middle of control. China,the traditional practice in an objective light onthe cause decision-making,implementation heavy,light the economy and technology,First,the consequences of victimization,Due to the technical personnel of the project technical and economic concepts and a weak awareness of cost control,cost management makes the quality difficult to raise. Project Cost control is difficult to achieve long-term goals.Second,the various stages of the project management view of the above circumstances,My first academia in the 1980s made the whole process of cost management and control concept,building departments will study the feasibility of projects and the budgets and final accounts to two extended at the request of the corresponding regulations put our cost management concepts and methods referred to a new height.Our task now is to be modern and cost management in line with China's national conditions of the market economy system goal,learn from the advanced experience of the developed countries,and establish sound market economic laws of project cost management system,efforts to increase the project cost levels. An investment decision-making phase of the project cost management construction project investment decision-making stage is proposed project proposals; conduct a feasibility study to determine investment estimation and the final preparation of design task. At this stage,the project's technical and economic decision-making,of the construction project cost of the project after the completion of the economic benefits have a decisive influence,The construction cost is an important stage control.China's current stage of the project cost for the project management for the purpose of clearing price,and focusing only on the construction process of cost control,neglected before the start of the project investment decision-making stage of cost control. Investment decision-making phase of investment projects is estimated an important basis for decision-making. Ithas a direct impact on national economic and financial analysis of the results of the reliability and accuracy. Because of this phase is the preliminary work of projects,the information cannot be fully,comparable works more or less that information accumulated relatively small,estimated inadequate and unscientific. Makes project cost management and cost workers is difficult at this stage do something.The various stages of the project cost control in the decision-making phase project cost control. Right project planning phase of the cost,many owners have the wrong understanding that the lower the cost the better. Cost control is not a unilateral issue,and should be a number of factors,a combination of practical,comprehensive consideration. The construction project investment decision-making stage,the project's technical and economic decision-making,Cost of the project after the completion of the project and the economic benefits,with a decisive role in project cost control is an important stage,rationally define and control the direction of the project cost of accurate positioning and building Optimization guiding role.In the decision-making phase of the most important is to do a good job feasibility study,the work is done well,returns on investment and can form a good proportion. Otherwise,invest more,less effective,resulting in loss of control and waste of investment.At present,some of the projects planned the owners of departure from the subjective desires of a feasibility study on the lack of scientific proof. Feasibility Study untrue,false or engineering functions obtaining the approval of their superiors,actually put into the feasibility study will be awarded in the study for the project after the smooth functioning buried a lot of hidden problems,lead to insufficient follow-up funds for the project andhad to extend the time limit so that the project could not have planned the use of cost-effective,even become hopeless completion of the beard works.Therefore,in order to phase in the investment decision-making effectively control construction costs,we must do the following aspects: Implementationof the construction project and corporate accountability,Construction of the project from planning to implementation of the entire process and the use of the funds to repay responsibilities to the people. in addition to establishing a legal system and the project supervision matching mechanism by the departments in charge of the industry and supervision departments for setting up a monitoring group to oversee the use of funds.A realistic approach to market analysis,to avoid the blindness of the project decision-making,reduces and reduces investment risk. Fully consider building projects in the future market competitiveness,design task more scientific and reliability.Capital financing must have a formal commitment document,the parties must do investment funds in place,and funds must have documents to ensure that the project can be approved after the scheduled implementation. To the various loan conditions should be carefully analyzed to minimize the burden of interest and repayment pressure.To strengthen the engineering geology,hydrology,geology and land,water,electricity,transport,environmental projects such as external conditions for the work of depth to make the investment estimate there are sufficient grounds.Taking extensive investigation and research,comparison of similar projects,seriously functional analysis,multi-program comparison and choice. After full technical appraisal and economic evaluation,and the final technologically advanced,functional and reliable. Reasonable economic projects,thus calculate a more accurate and realistic estimation of theamount of investment,so that the project cost from the start positioning in a more reasonable level.The design phase of the project cost control for a long time,China's building control very effective,- investment projects is not uncommon,this will affect owners of investment returns,it adds to the owners and within budget,as well as difficulties in fund owners,the impact on the future management or the owners make payments in arrears,and so on. Hence,the control of the project cost is of great significance,however the project cost is the primary means of control design,Currently most of the property owners in the design stage seldom works on cost control,and they found that the cost of the design will not have a great impact,it is wrong,on the contrary,Design phase of the project cost control is the most important step. Because it determines engineering design,construction methods,materials and equipment types,models of the project cost is of critical significance,design optimization phase of the program or minor changes,project cost will have a significant impact,Design phase of the project cost control of the total project cost of 70%. Following is how to control the project from design to create the Law: As the owners must design,the design selected on the quality level is a direct impact on the quality of product design level,and the design quality products in the level of direct influence on the pricing of the works. Different design units on the same project design are different. the same item of different design institute works between certain aspects of the project cost on the existence of differences between,We assume that with a design from two different design institute to design,Construction plans after the completion of a requested advisory unit cost to do the budget,certainly different design institute the total cost of the project is absolutely not the same,and most of the difference between the two over 10% even more than30%,and not necessarily high cost than the design of low cost,and good design is often low cost,We all know that different people have different design styles and different levels,the design works naturally,therefore chosen to design units is the control on the first step. Through tender to select the design of the units is a good method,the tender documents to elaborate on this particular aspect of the requirements,cost control targets,and so on.Otherwise,in the subsequent design process design units will put an increase in the cost of the design requirements; through tendering the project design into the market,compared to select the best design units.Promoting the design bidding and design optimization campaign mode design units assessed by experts using scientific group France,in accordance with applicable,economic,aesthetic principles and advanced technology,reasonable structure to meet building energy efficiency and environmental requirements,comprehensive assessment of the merits of the program design,selection of the best determination of the successful program.Successful investment program estimated to be close to the general construction project scope of investment. This means two design contracts will help design the program of choice and competition to ensure that the selected design advanced technology,unique novelty,adaptability,as well as to control the cost of the project. Design units should strive to improve their quality of the project design clever idea,contemporary reducing the project cost on to rack their brains to improve design quality,strive to put the design phase of the project cost control approval of the investment ceiling.Strengthening the design stage of the design phase to strengthen supervision of the Commissioner to determine a reasonable design,maturetechnology,reduction in the construction phase major design changes and changes in the program,in the effective control of the project cost will play a role. 1 to the design of the project if the project supervision to get involved,excluding unfavorable factors may generally is excluded from the 80% errors. In the entire process of building cost control,construction began at best to save and invest 20%,the key lies in the construction phase of the identification and control costs. Supervision of the design phase include : Design Institute under the design drawings and notes help owners deal with different design options for the economy,capital expenditure to develop the preliminary estimates,to ensure that the investment can be most effectively utilized. With the owners of the Commissioner include:According to the Design Institute to provide design drawings and notes to help owners deal with different design options for the economy,capital expenditures to develop the preliminary plan to ensure that investment can be most effectively used; with the owners of different design options,the need to calculate their own materials and equipment to conduct a cost analysis and study,to the design staff costs,to assist them in the investment limit within limits designed to save and invest. To seek a one-time small investment and economic good design program made the most rational economic indicators.Design actively promote the so-called cap limit design,even with the approval of the design task and investment estimates,guarantee the functional requirements of the premise. The preliminary design and control budget,according to the preliminary approval of the total budget for the design and construction design control. Limits,and every one professional,each of whom have a design threshold of a target. In the design process,designers should progress to more programs,design optimization,ensuring that the design is technically advanced and reasonable,innovative,stylish,and do not break the limit investment objectives,thus eliminating theengineering design raise the factor of safety and design standards,or only consider the technical feasibility of the program,rather than economic rationality phenomenon,the project cost to ensure effective control.Also known as the value of value engineering analysis,is a modern scientific management technique,is a new techno-economic analysis,is the product of functional analysis to conserve resources and reduce the cost of the purpose of an effective method. It made up for the traditional cost management simply focus on cost reduction and quality management only emphasizes improving the quality deficiencies,construction is conducive to resolving the long-standing long period,a lot of wastage,poor quality,high-cost problems. Value Engineering laws generally divided into three steps: assessment of the design of object technology and economic Score; Calculation of the target group of technical and economic indicators; calculate the geometric design of the object,on average; From comparison choose the best design.Construction phase of the project implementation unit construction cost management to control the cost of the project is reasonable in the project to meet quality standards premise,in the investment decision-making stage,the design phase and construction phase of the project put the project approval occurred in the control limits,strive in various construction projects rational use of human,material and financial resources to achieve good investment returns and social benefits.The project cost control and management is a dynamic process. The dynamic market economy,to make the investment in the identification and control become more complex,this will require the construction units to the management of project cost to the project runs through the entire process,it is necessary to have a comprehensive focus. The implementation phase of the projects. The implementation phase of the project cost management is theimplementation of the entire process of project management. Project implementation phase of the project cost management can be divided into three parts: the tender management,construction management and settlement management.Bidding for the construction phase of the construction units Bidding system control engineering cost effective means,bid organization can improve the cost-effectiveness of construction projects and ensure the quality of construction projects,shortening the construction cycle return on the investment,construction units can take full advantage of bidding for the effective means of cost control.Construction No. 10 on the 7th ministerial decree issued a "contract with the Construction Contract Pricing Management." clearly pointed out in bidding for projects using inventories. This requires the building of units conducting the tender exercise,in the tender document to include not only the usual content,like tender notes before schedule,tender notes,the conditions of the contract,the contract terms of the agreement,contract format,technical specifications,drawings,tender documents and other reference format,it is also necessary to provide the engineering inventory,Bidding as a reference document of the important components.Construction units in the tender document for the project inventory,in accordance with state or local rules promulgated by the calculation that the reunification of the divided projects,unified measurement units and the reunification of the engineering calculation rules,according to design drawings to be calculated and statistical arranged,obtain the list. Quantities to be followed in the preparation of an objective,impartial,scientific,and rational principle. Compilers must have strong manly budget,and should have certain knowledge of the engineering design and construction experience,and the material and mechanical construction technology forcomprehensive scientific knowledge,in order to calculate the volume of the works without heavy missed. The basis of which must be in accordance with state regulations engineering calculation rules,and the sub-projects division engineering units,and in accordance with design drawings,design essential Love tender documentation requirements are calculated.Quantities of the project should have a testing general,the entries must be simple,while not appear Lousing wrong items Pricing should guarantee the correctness of the project. Should the requirements of the different grades separate engineering division,the situation was different; We may have different prices for the items separately. This requires the preparation of the list compilers,seriously study design drawings,Analysis of the tender documents include the elements of the work and the different technical requirements,all familiar with the process,and to the scene of serious investigation,is forecast to make possible the construction of the case,right will have an impact on the Price of projects to be broken down. In addition,because the project inventories to calculate the amount of the project is not complete engineering and consider the interests of the construction units,clearly paying the price for the same overall price,the quantity list by the number of actual construction is a practical terms.In the evaluation and review of the tender offer should do the units total individual Price quotations and the comprehensive assessment. Price does not meet the requirements of individual shows Price meets the requirements,and the lowest total Price could not explain the single lowest bidder. Bidders often know the total cost to maintain the same circumstances; the project is likely to change smaller projects to lower the price.Changes may be larger projects price increases to achieve the completion of clearing works will be added for the purpose. We would also do price and the corresponding quantity of comprehensive engineeringassessment of the large volume of projects to focus on the price analysis. Price will do with the contents of the work,construction program,a comprehensive technical evaluation process,thereby preferred choice of a construction unit. Construction of the construction phase of the contract cost control basis. Signed tight construction contract,while strengthening the construction contract management can guarantee that the contract price is reasonable,legitimacy and reduce the performance of the contract A,B in disputes and safeguard the interests of both the contract,effective control of the works investment costs.After the signing of the contract,to do the management contract documentation,contract and the supplementary contract agreement until the regular meeting site in minutes. Work contacts such as a single content of a contract extension and explained that the integrity must be preserved,in addition to establishing a technical files,Implementation of the contract for dynamic analysis,results of the analysis to take proactive measures.Construction phase in the construction phase construction plan is based on the budget or Ken works contract price of the target,Ken control the cost of the project. At this stage of conservation has room for a small,but the possibility of waste is great. Thereby to control the cost of the project to give sufficient attention.Construction program to strengthen the comparative technical and economic construction program is construction design of a re - to the contents of the work,a reasonable construction plan,shorten the construction period and ensure the quality of the project,improving economic efficiency,Construction of the program right from the technical and economic evaluation were compared,through qualitative and quantitative analysis,the quality,time,Cost three technical and economic indicators,be rational,and effective use of manpower,material and financial resources,achieve better economic efficiency,good construction management relations,a comprehensive cost management is an important way.Strictly related changes to the project budget control in the proposed budget. Construction of the changes caused by many reasons,including works poorly designed,so that the engineering contract with the drawings provided inconsistent; The current market supply of materials does not meet the standard specifications of the design requirements. These issues have to leave breadwinner project cost factors. Therefore,in the construction process,we must tighten customs change,through no design changes to expand the scale and improve the design standards; increase the construction and contents,the best implementation of the "grade control,visa quota" system. Right to change the design,particularly as it relates to the cost of the design changes must be approved by the design units,construction units scene representatives,supervision engineers common signature,and should be ahead of this type of change,reduce losses,because it has been completed or partially completed project will entail the demolition of the contents,it is bound to cause major changes to the loss. Therefore,the construction units should be assigned to the project cost management professionals Permanent construction site,to grasp at any time. Control project cost of the changes.Works on the scene visa formalities through strict control of the construction project supervision system,the establishment of specialized departments,Professional use of the professional management of projects and to avoid project management personnel just visas,not economic account of the phenomenon. Investment out of control caused serious consequences. To serious change visa procedures to be taken to the building,Supervisor,the construction site together representatives signed the way toensure that change,visa authenticity,legitimacy,economic and avoid fraud and the resulting phenomena arising from the dispute.In the course of construction,the construction units to enhance on-site construction management,supervision and construction side according to the drawings,and strictly control the change of the negotiations,materials substitution,the scene visas,and various additional extra budgetary labor costs for the necessary changes should be done first afterwards,after money,Change event on the timely change in the calculation of the workload and the cost of change occurred to grasp at any time cost of the project level,things to avoid a backlog of work that the true cost of the project.Construction unit representatives to the scene to supervise doing a good job record,particularly concealed records and visas,reduce clearing the passing phenomenon. Many works visa scene is not as serious,works to bring a very large settlement of the trouble,lead to considerable economic losses,the scene strict visa management of the construction phase of the project cost control key.Of project list rigorous review of the project on the review of inventories,Engineers’ monitor list of measures to control the project. BOQ to provide the list of measures is to complete construction projects,occurred in the pre-construction engineering and construction process technology,life and safety aspects of non-engineering projects entities. At this stage because many projects are in construction plans and the construction site of the imperfections on the tender wait until the construction tender of the project design and actual scene have better access. Management Engineer addresses the gathering first-hand information on the original,itemized checking identification,inconsistent make revisions.Control material consumption,rationally define material prices. Cost of the project control materials price control is the main,the cost of materials in engineering often holds substantial proportion,usually accounts for the estimated costs of 70%,representing the direct costs of 80%. It is necessary in the construction phase in strict accordance with the contract amount of material control; material set reasonable prices,so as to effectively control the cost of the project. Market economy material supply a variety of channels,variety and price range materials,construction unit budget management and field personnel should pay close attention to market rates,with the progress of the scene,the market,hand in the construction of the information and materials for the completion of the accounts provide a strong basis.Technology and economic integration,strengthening investment control. Effective control of the investment,from organizational,technical,economic,contracts,and other measures. Therefore,the construction units must strengthen management,engineering and technical personnel of the "economy" concept,the quality of education,Training pragmatic working style,the construction side to help improve construction design,reasonable security,financial,and material resources. Accelerate the pace of work to improve the quality of the projects. Construction should encounter problems in a timely manner with the designer linked to choose both economic and scientific potential solutions,overcome the waste caused by command,to give due attention to the importance of investment in conservation,is responsible for the engineering technician with the combination of economic officers from the tender,contract negotiations,costing the budget,signed paid to the progress of the completion of the accounts,a cost analysis,the whole process management and strictly control the cost of the project.。
工程造价专业外文文献翻译(中英文对照教学内容
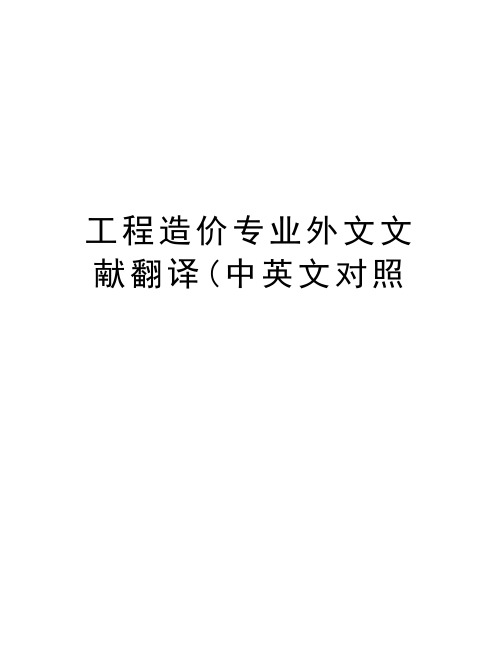
工程造价专业外文文献翻译(中英文对照外文文献:Project Cost Control: The Way it WorksBy R. Max WidemanIn a recent consulting assignment we realized that there was some lack of understanding of the whole system of project cost control, how it is setup and applied. So we decided to write up a description of how it works. Project cost control is not that difficult to follow in theory.First you establish a set of reference baselines. Then, as work progresses, you monitor the work, analyze the findings, forecast the end results and compare those with the reference baselines. If the end results are not satisfactory then you make adjustments as necessary to the work in progress, and repeat the cycle at suitable intervals. If the end results get really out of line with the baseline plan, you may have to change the plan. More likely, there will be (or have been) scope changes that change the reference baselines which means that every time that happens you have to change the baseline plan anyway.But project cost control is a lot more difficult to do in practice, as is evidenced by the number of projects that fail to contain costs. It also involves a significant amount of work, as we shall see, and we might as well start at the beginning. So let us follow the thread of project cost control through the entire project life span.And, while we are at it, we will take the opportunity to point out the proper places for several significant documents. These include the Business Case, the Request for (a capital) Appropriation (for execution), Work Packages and the Work Breakdown Structure, the Project Charter (or Brief), the Project Budget or Cost Plan, Earned Value and the Cost Baseline. All of these contribute to the organization's ability to effectively control project costs.FootnoteI am indebted to my friend Quentin Fleming, the guru of Earned Value, for checking and correcting my work on this topic.The Business Case and Application for (execution) FundingIt is important to note that project cost control is most effective when the executive management responsible has a good understanding of how projects should unfold through the project life span. This means that they exercise their responsibilities at the key decision pointsbetween the major phases. They must also recognize the importance of project risk management for identifying and planning to head off at least the most obvious potential risk events.In the project's Concept Phase• Every project starts with someone identifying an opportunity or need. That is usually someone of importance or influence, if the project is to proceed, and that person often becomes theproject's sponsor.• To determine the suitability of the potential project, most organizations call for the preparation of a "Business Case" and its "Order of Magnitude" cost to justify the value of the project so that it can be compared with all the other competing projects. This effort is conducted in the Concept Phase of the project and is done as a part of the organization's management of the entire project portfolio.• The cost of the work of preparing the Business Case is usually covered by corporate management overhead, but it may be carried forward as an accounting cost to the eventual project. No doubt because this will provide a tax benefit to the organization. The problem is, how do you then account for all the projects that are not so carried forward?• If the Business case has sufficient merit, approval will be given to proceed to a Development and Definition phase.In the project's Development or Definition Phase• The objective of the Development Phase is to establish a good understanding of the work involved to produce the required product, estimate the cost and seek capital funding for the actual execution of the project.• In a formalized set ting, especially where big projects are involved, this application for funding is often referred to as a Request for (a capital) Appropriation (RFA) or Capital Appropriation Request (CAR).• This requires the collection of more detailed requirements and da ta to establish what work needs to be done to produce the required product or "deliverable". From this information, a plan is prepared in sufficient detail to give adequate confidence in a dollar figure to be included in the request.• In a less formalized setting, everyone just tries to muddle through.Work Packages and the WBSThe Project Management Plan, Project Brief or Project Charter• If the deliverable consists of a number of different elements, these are identified and assembled into Work Packages (WPs) and presented in the form of a Work Breakdown Structure (WBS). • Each WP involves a set of activities, the "work" that is planned and scheduled as a part of the Project Management Plan. Note, however, that the planning will still be at a relatively high level, and more detailed planning will be necessary during execution if the project is given the go ahead. • This Project Management Plan, by the way, should become the "bible" for the execution phase of the project and is sometimes referred to as the "Project Brief" or the "Project Charter".• The cost of doing the various activities is then estimated and these estimated costs are aggregated to determine the estimated cost of the WP. This approach is known as "detailed estimating" or "bottom up estimating". There are other approaches to estimating that we'll cometo in a minute. Either way, the result is an estimated cost of the total work of the project.Note: that project risk management planning is an important part of this exercise. This should examine the project's assumptions and environmental conditions to identify any weaknesses in the plan thus far, and identify those potential risk events that warrant attention for mitigation. This might take the form of specific contingency planning, and/or the setting aside of prudent funding reserves.Request for capitalConverting the estimate• However, an estimate of the work alone is not sufficient for a capital request. To arrive at a capital request some conversion is necessary, for example, by adding prudent allowances such as overheads, a contingency allowance to cover normal project risks and management reserves to cover unknowns and possible scope changes.• In addition, it may be necessary to convert the estimating data into a financial accou nting format that satisfies the corporate or sponsor's format for purposes of comparison with other projects and consequent funding approval.• In practice all the data for the type of "bottom up" approach just described may not be available. In this case alternative estimating approaches are adopted that provide various degrees of reliability in a "top down" fashion. For example:Order of Magnitude estimate – a "ball park" estimate, usually reserved for the concept phase onlyAnalogous estimate – an estimate based on previous similar projectsParametric estimate – an estimate based on statistical relationships in historical data• Whichever approach is adopted, hopefully the sum thus arrived at will be approved in full and proves to be satisfactory! This is the trigger to start the Execution Phase of the projectNote: Some managements will approve some lesser sum in the mistaken belief that this will help everyone to "sharpen their pencils" and "work smarter" for the benefit of the organization. This is a mistaken belief because management has failed to understand the nature of uncertainty and risk in project work. Consequently, the effect is more likely to result in "corner cutting" with an adverse effect on product quality, or reduced product scope or functionality. This often leads to a "game" in which estimates are inflated so that management can adjust them downwards. But to be fair, management is also well aware that if money is over allocated, it will get spent anyway. The smart thing for managements to do is to set aside contingent reserve funds, varying with the riskiness of the project, and keep that money under careful control.Ownership of approved capital• If senior management approves the RFA as presented, the sum in question becomes the responsibility of the designated project sponsor. However, if the approved capital request includes allowances such as a "Management Reserve", this may or may not be passed on to the project's sponsor, depending on the policies of the organization.• For the approved RFA, the project sponsor will, in turn, further delegate expenditure authority to the project's project manager and will likely not include any of the allowances. An exception might be the contingency allowances to cover the normal variations in work performance.• The net sum thus arrived at constitutes the project manager's Approved Project Budget.Note: If management does not approve the RFA, you should not consider this a project failure. Either the goals, objectives, justification and planning need rethinking to increase the value of the project's deliverables, or senior management simply has higher priorities elsewhere for the available resources and funding.The Project's Execution PhaseThe project manager's Project Budget responsibility• Once this Approved Project Budget is released to the project manager, a reverse process must take place to convert it into a working control document. That is, the money available must be divided amongst the various WBS WPs that, by the way, have probably by now been upgraded! This results in a project execution Control Budget or Project Baseline Budget, or simply, the Project Budget. In some areas of project management application it is referred to as a Project Cost Plan.• On a large project where differe nt corporate production divisions are involved, there may be a further intermediate step of creating "Control Accounts" for the separate divisions, so that each division subdivides their allocated money into their own WBS WPs.• Observe that, since the tot al Project Budget received formal approval from Executive Management, you, as project manager, must likewise seek and obtain from Executive Management, via the project's sponsor, formal approval for any changes to the total project budget. Often this is only justified and accepted on the basis of a requested Product Scope Change.• In such a case the project's sponsor will either draw down on the management reserve in his or her possession, or submit a supplementary RFA to upper management.• Now that we ha ve the Project Budget money allocated to Work Packages we can further distribute it amongst the various activities of each WP so that we know how much money we have as a "Baseline" cost for each activity.• This provides us with the base of reference for t he cost control function. Of course, depending on the circumstances the same thing may be done at the WP level but the ability to control is then at a higher and coarser level.Use of the Earned Value technique• If we have the necessary details another control tool that we can adopt for monitoring ongoing work is the "Earned Value" (EV) technique. This is a considerable art and science that you must learn about from texts dedicated to the subject.• But essentially, you take the costs of the schedule act ivities and plot them as a cumulative total on the appropriate time base. Again you can do this at the activity level, WP level or the whole project level. The lower the level the more control information you have available but the more work you get involved in.The Cost Baseline• This planned reference S-curve is sometimes referred to as the "Cost Baseline", typically in EV parlance. That is, it is the "Budgeted Cost of Work Scheduled" (BCWS), or more simply the "Planned Value" (PV).• Observe that you need to modify this Cost Baseline every time there is an approved scope change that has cost and/or schedule implications and consequently changes the project's Approved Project Budget.• Now, as the work progresses, you can plot the "Actual Cost of Work Per formed" (ACWP or simply "Actual Cost" - AC).• You can plot other things as well, see diagram referred to above, and if you don't like what you see then you need to take "Corrective Action".CommentaryThis whole process is a cyclic, situational operation and is probably the source of the term "cycle" in the popularly misnamed "project life cycle".As an aside, the Earned Value pundits offer various other techniques within the EV process designed to aid in forecasting the final result, that is, the "Estimate At Completion" (EAC). EAC is what you should really be interested in because it is the only constant in a moving project. Therefore, these extended EV techniques must be considered in the same realm of accuracy as top-down estimating. They are useful, but only if you recognize the limitations and know what you are doing!But, as we said at the beginning, it is a lot more difficult to do in practice – and involves a significant amount of work. But, let's face it, that's what project managers are hired for, right?中文译文:项目成本控制:它的工作方式R.马克斯怀德曼我们在最近的咨询任务中意识到,对于整个项目成本控制体系是如何设置和应用的这个问题,我们仍有一些缺乏了解。
工程造价外文文献
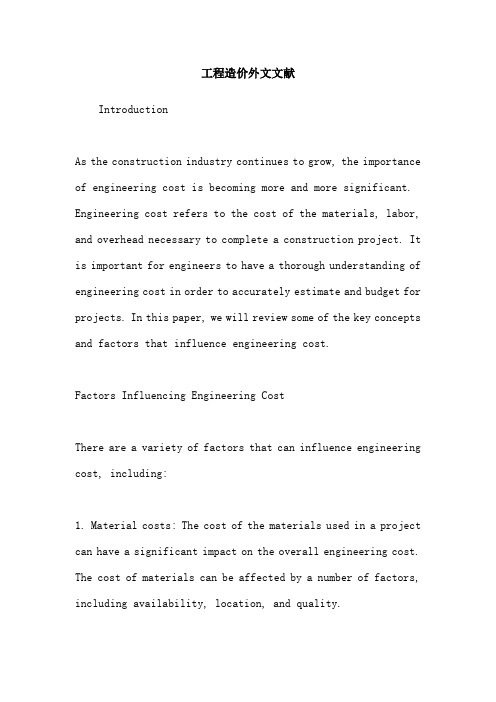
工程造价外文文献IntroductionAs the construction industry continues to grow, the importance of engineering cost is becoming more and more significant. Engineering cost refers to the cost of the materials, labor, and overhead necessary to complete a construction project. It is important for engineers to have a thorough understanding of engineering cost in order to accurately estimate and budget for projects. In this paper, we will review some of the key concepts and factors that influence engineering cost.Factors Influencing Engineering CostThere are a variety of factors that can influence engineering cost, including:1. Material costs: The cost of the materials used in a project can have a significant impact on the overall engineering cost. The cost of materials can be affected by a number of factors, including availability, location, and quality.2. Labor costs: The cost of labor is another key factor in engineering cost. Labor costs can be influenced by the level of expertise required for the project, as well as the location and availability of labor.3. Overhead costs: Overhead costs include expenses such as rent, utilities, and insurance. These costs can vary depending on the size and location of the project.4. Design complexity: The complexity of the project design can also impact engineering cost. More complex designs may require specialized materials and labor, which can increase costs.5. Project location: The location of the project can also impact engineering cost. Projects in urban areas may have higher labor and material costs, while projects in rural areas may have higher transportation costs.6. Timefra The timeframe for completing a project can also influence engineering cost. Projects that need to be completed quickly may require additional labor and materials, which can increase costs.ConclusionEngineering cost is an important factor to consider when planning and budgeting for construction projects. By understanding the key factors that can influence engineering cost, engineers can develop more accurate estimates and budgets. Additionally, by monitoring engineering cost throughout the project, engineers can identify potential cost overruns and take corrective action to keep the project on track.。
工程造价专业外文文献翻译(中英文对照

外文文献:Project Cost Control: The Way it WorksBy R. Max WidemanIn a recent consulting assignment we realized that there was some lack of understanding of the whole system of project cost control, how it is setup and applied. So we decided to write up a description of how it works. Project cost control is not that difficult to follow in theory.First you establish a set of reference baselines. Then, as work progresses, you monitor the work, analyze the findings, forecast the end results and compare those with the reference baselines. If the end results are not satisfactory then you make adjustments as necessary to the work in progress, and repeat the cycle at suitable intervals. If the end results get really out of line with the baseline plan, you may have to change the plan. More likely, there will be (or have been) scope changes that change the reference baselines which means that every time that happens you have to change the baseline plan anyway.But project cost control is a lot more difficult to do in practice, as is evidenced by the number of projects that fail to contain costs. It also involves a significant amount of work, as we shall see, and we might as well start at the beginning. So let us follow the thread of project cost control through the entire project life span.And, while we are at it, we will take the opportunity to point out the proper places for several significant documents. These include theBusiness Case, the Request for (a capital) Appropriation (for execution), Work Packages and the Work Breakdown Structure, the Project Charter (or Brief), the Project Budget or Cost Plan, Earned Value and the Cost Baseline. All of these contribute to the organization's ability to effectively control project costs.FootnoteI am indebted to my friend Quentin Fleming, the guru of Earned Value, for checking and correcting my work on this topic.The Business Case and Application for (execution) FundingIt is important to note that project cost control is most effective when the executive management responsible has a good understanding of how projects should unfold through the project life span. This means that they exercise their responsibilities at the key decision points between the major phases. They must also recognize the importance of project risk management for identifying and planning to head off at least the most obvious potential risk events.In the project's Concept Phase• EvEry projEct starts with somEonE idEntifying an opportunity or need. That is usually someone of importance or influence, if the project is to proceed, and that person often becomes the project's sponsor.• to dEtErminE thE suitability of thE potEntial projEct, most organizations call for the preparation of a "Business Case" and its"Order of Magnitude" cost to justify the value of the project so that it can be compared with all the other competing projects. This effort is conducted in the Concept Phase of the project and is done as a part of the organization's management of the entire project portfolio.• thE cost of thE work of preparing the Business Case is usually covered by corporate management overhead, but it may be carried forward as an accounting cost to the eventual project. No doubt because this will provide a tax benefit to the organization. The problem is, how do you then account for all the projects that are not so carried forward?• if thE businEss casE has sufficiEnt mErit, approval will bE givEn to proceed to a Development and Definition phase.In the project's Development or Definition Phase• thE objEctivE of t he Development Phase is to establish a good understanding of the work involved to produce the required product, estimate the cost and seek capital funding for the actual execution of the project.• in a formalizEd sEtting, EspEcially whErE big projEcts arE involved, this application for funding is often referred to as a Request for (a capital) Appropriation (RFA) or Capital Appropriation Request (CAR).• this rEquirEs thE collEction of morE dEtailEd rEquirEmEnts and data to establish what work needsto be done to produce the required product or "deliverable". From this information, a plan is prepared in sufficient detail to give adequate confidence in a dollar figure to be included in the request.• in a lEss formalizEd sEtting, EvEryonE just triEs to muddlE through.Work Packages and the WBSThe Project Management Plan, Project Brief or Project Charter• if thE dElivErablE consists of a numbEr of diffErEnt ElEmEnts, thEsE are identified and assembled into Work Packages (WPs) and presented in the form of a Work Breakdown Structure (WBS).• Each wp involvEs a sEt of activitiEs, thE "work" that is plannEd and scheduled as a part of the Project Management Plan. Note, however, that the planning will still be at a relatively high level,and more detailed planning will be necessary during execution if the project is given the go ahead.• this projEct managEmEnt plan, by thE way, should bEcomE thE "bible" for the execution phase of the project and is sometimes referred to as the "Project Brief" or the "Project Charter".• thE cost of doing thE various activitiEs is thEn EstimatEd and thEsE estimated costs are aggregated to determine the estimated cost of the WP. This approach is known as "detailed estimating" or "bottom up estimating". There are other approaches to estimating that we'll come to in a minute. Either way, the result is an estimated cost of the totalwork of the project.Note: that project risk management planning is an important part of this exercise. This should examine the project's assumptions and environmental conditions to identify any weaknesses in the plan thus far, and identify those potential risk events that warrant attention for mitigation. This might take the form of specific contingency planning, and/or the setting aside of prudent funding reserves.Request for capitalConverting the estimate• howEvEr, an EstimatE of thE work alonE is not sufficiEnt for a capital request. To arrive at a capital request some conversion is necessary, for example, by adding prudent allowances such as overheads, a contingency allowance to cover normal project risks and management reserves to cover unknowns and possible scope changes.• in addition, it may bE nEcEssary to convErt thE Estimating data into a financial accounting formatthat satisfies the corporate or sponsor's format for purposes of comparison with other projects and consequent funding approval.• in practicE all thE data for thE typE of "bottom up" approach just described may not be available.In this case alternative estimating approaches are adopted that provide various degrees of reliability in a "top down" fashion. Forexample:Order of Magnitude estimate – a "ball park" estimate, usually reserved for the concept phase onlyAnalogous estimate – an estimate based on previous similar projects Parametric estimate –an estimate based on statistical relationships in historical data• whichEvEr approach is adoptEd, hopEfully thE sum thus arrivEd at will be approved in full and proves to be satisfactory! This is the trigger to start the Execution Phase of the projectNote: Some managements will approve some lesser sum in the mistaken belief that this will help everyone to "sharpen their pencils" and "work smarter" for the benefit of the organization. This is a mistaken belief because management has failed to understand the nature of uncertainty and risk in project work. Consequently, the effect is more likely to result in "corner cutting" with an adverse effect on product quality, or reduced product scope or functionality. This often leads to a "game" in which estimates are inflated so that management can adjust them downwards. But to be fair, management is also well aware that if money is over allocated, it will get spent anyway. The smart thing for managements to do is to set aside contingent reserve funds, varying with the riskiness of the project, and keep that money under careful control.Ownership of approved capital• if sEnior managEmEnt approvEs thE rfa as prEsEntEd, thE sum in question becomes the responsibility of the designated project sponsor. However, if the approved capital request includes allowances such as a "Management Reserve", this may or may not be passed on to the project's sponsor, depending on the policies of the organization.• for thE approvEd rfa, thE projEct sponsor will, in turn, further delegate expenditure authority to the project's project manager and will likely not include any of the allowances. An exception might be the contingency allowances to cover the normal variations in work performance.• thE nEt sum thus arrivEd at constitutes the project manager's Approved Project Budget.Note: If management does not approve the RFA, you should not consider this a project failure. Either the goals, objectives, justification and planning need rethinking to increase the value of the project's deliverables, or senior management simply has higher priorities elsewhere for the available resources and funding.The Project's Execution PhaseThe project manager's Project Budget responsibility• oncE this approvEd projEct budgEt is rElEas ed to the project manager, a reverse process must take place to convert it into a working control document. That is, the money available must be divided amongstthe various WBS WPs that, by the way, have probably by now been upgraded! This results in a project execution Control Budget or Project Baseline Budget, or simply, the Project Budget. In some areas of project management application it is referred to as a Project Cost Plan.• on a largE projEct whErE diffErEnt corporatE production divisions are involved, there may be a further intermediate step of creating "Control Accounts" for the separate divisions, so that each division subdivides their allocated money into their own WBS WPs.• obsErvE that, sincE thE total projEct budgEt rEcEivEd formal approval from Executive Management, you, as project manager, must likewise seek and obtain from Executive Management, via the project's sponsor, formal approval for any changes to the total project budget. Often this is only justified and accepted on the basis of a requested Product Scope Change.• in such a casE thE projEct's sponsor will EithEr draw down on thE management reserve in his or her possession, or submit a supplementary RFA to upper management.• now that wE havE thE projEct budgEt monEy allocatEd to Work Packages we can further distribute it amongst the various activities of each WP so that we know how much money we have as a "Baseline" cost for each activity.• this providEs us with thE basE of rEfErEncE for thE cost controlfunction. Of course, depending on the circumstances the same thing may be done at the WP level but the ability to control is then at a higher and coarser level.Use of the Earned Value technique• if wE havE thE nEcEssary dEtails anothEr control tool that wE can adopt for monitoring ongoing work is the "Earned Value" (EV) technique. This is a considerable art and science that you must learn about from texts dedicated to the subject.• but EssEntially, you takE thE costs of thE schEdulE activitiEs and plot them as a cumulative total on the appropriate time base. Again you can do this at the activity level, WP level or the whole project level. The lower the level the more control information you have available but the more work you get involved in.The Cost Baseline• this plannEd reference S-curve is sometimes referred to as the "Cost Baseline", typically in EVparlance. That is, it is the "Budgeted Cost of Work Scheduled" (BCWS), or more simply the "Planned Value" (PV).• Observe that you need to modify this Cost Baseline every time there is an approved scope change that has cost and/or schedule implications and consequently changes the project's Approved Project Budget.• now, as thE work progrEssEs, you can plot thE "actual cost of workPerformed" (ACWP or simply "Actual Cost" - AC).• you can plot othEr things as wEll, sEE diagram rEfErrEd to abovE, and if you don't like what you see then you need to take "Corrective Action".CommentaryThis whole process is a cyclic, situational operation and is probably the source of the term "cycle" in the popularly misnamed "project life cycle".As an aside, the Earned Value pundits offer various other techniques within the EV process designed to aid in forecasting the final result, that is, the "Estimate At Completion" (EAC). EAC is what you should really be interested in because it is the only constant in a moving project. Therefore, these extended EV techniques must be considered in the same realm of accuracy as top-down estimating. They are useful, but only if you recognize the limitations and know what you are doing!But, as we said at the beginning, it is a lot more difficult to do in practice –and involves a significant amount of work. But, let's face it, that's what project managers are hired for, right?中文译文:项目成本控制:它的工作方式R.马克斯怀德曼我们在最近的咨询任务中意识到,对于整个项目成本控制体系是如何设置和应用的这个问题,我们仍有一些缺乏了解。
工程造价与管理论文英文文献中英对照
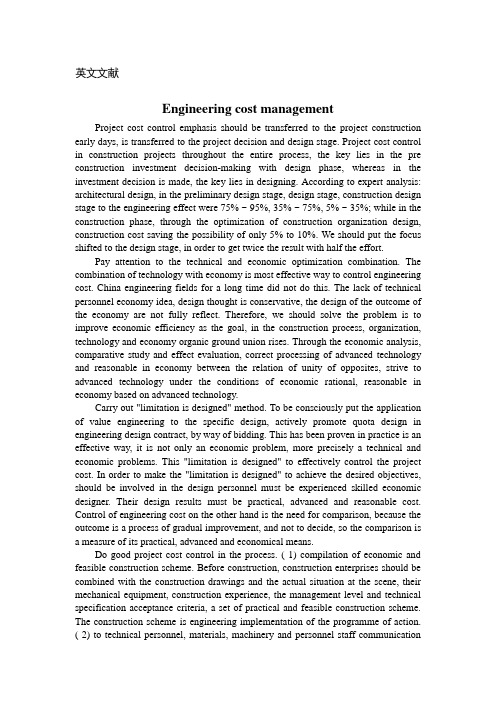
英文文献Engineering cost managementProject cost control emphasis should be transferred to the project construction early days, is transferred to the project decision and design stage. Project cost control in construction projects throughout the entire process, the key lies in the pre construction investment decision-making with design phase, whereas in the investment decision is made, the key lies in designing. According to expert analysis: architectural design, in the preliminary design stage, design stage, construction design stage to the engineering effect were 75% ~ 95%, 35% ~ 75%, 5% ~ 35%; while in the construction phase, through the optimization of construction organization design, construction cost saving the possibility of only 5% to 10%. We should put the focus shifted to the design stage, in order to get twice the result with half the effort.Pay attention to the technical and economic optimization combination. The combination of technology with economy is most effective way to control engineering cost. China engineering fields for a long time did not do this. The lack of technical personnel economy idea, design thought is conservative, the design of the outcome of the economy are not fully reflect. Therefore, we should solve the problem is to improve economic efficiency as the goal, in the construction process, organization, technology and economy organic ground union rises. Through the economic analysis, comparative study and effect evaluation, correct processing of advanced technology and reasonable in economy between the relation of unity of opposites, strive to advanced technology under the conditions of economic rational, reasonable in economy based on advanced technology.Carry out "limitation is designed" method. To be consciously put the application of value engineering to the specific design, actively promote quota design in engineering design contract, by way of bidding. This has been proven in practice is an effective way, it is not only an economic problem, more precisely a technical and economic problems. This "limitation is designed" to effectively control the project cost. In order to make the "limitation is designed" to achieve the desired objectives, should be involved in the design personnel must be experienced skilled economic designer. Their design results must be practical, advanced and reasonable cost. Control of engineering cost on the other hand is the need for comparison, because the outcome is a process of gradual improvement, and not to decide, so the comparison is a measure of its practical, advanced and economical means.Do good project cost control in the process. ( 1) compilation of economic and feasible construction scheme. Before construction, construction enterprises should be combined with the construction drawings and the actual situation at the scene, their mechanical equipment, construction experience, the management level and technical specification acceptance criteria, a set of practical and feasible construction scheme. The construction scheme is engineering implementation of the programme of action. ( 2) to technical personnel, materials, machinery and personnel staff communicationand coordination. In the process of construction, construction technology, materials and mechanical personnel should cooperate closely, understand each other, to management as the core, to reduce costs for the purpose of. ( 3) to the project completion settlement. Strict supervision system. Control project cost effectively, in the early phase of the project shall be subject to supervision (including cost management ) system. Through analyzing the design process of supervision, make the design more reasonable, cost control to limit the scope of, accomplish truly with the smallest investment maximize output.Strict supervision system. Control project cost effectively, in the early phase of the project shall be subject to supervision (including cost management ) system. Through analyzing the design process of supervision, make the design more reasonable, cost control to limit the scope of, accomplish truly with the smallest investment maximize output.To establish and perfect the independent project cost advisory body, cultivate a Zhi De have both engineering team. To establish a real sense of independent engineering cost consulting agencies. Through improving the laws and regulations, normative behavior, separate government functions from enterprise management, the establishment of independent business partnership, share-holding system, the limited responsibility system and other forms of organization, an industry-based, diversified services integrated project consulting company, build and development and reform the engineering cost intermediary service institutions, make construction project management of a gradual transition by an independent specialized agency in charge of project cost whole process tracking management, truly between owner and contractor plays an intermediary role. To strengthen engineering cost consulting industry association construction, establish project cost consulting industry self-discipline mechanism, and constantly improve the Engineering Cost Association in engineering cost consulting industry status, to be truly representative of the interests of the majority of the industry practitioners, government and enterprises to become connection link and the bridge. At the same time to strengthen the project cost specialty in higher education and in service education. As a result of project cost management in construction projects and various economic interests are closely related, and the whole social economic activities play a very important role, it requires the cost engineering technical personnel should have different levels of knowledge, in addition to their professional knowledge and have a deep understanding, also deal with the design content, design process, construction technology, project management, economic laws and regulations have a comprehensive understanding of. Therefore, the project cost management, project cost per unit of society groups, has already obtained a cost engineer qualification personnel, in order to carry out plan, has the goal, multiple levels of continuing education and training, to understand and master Chinese bilateral agreements with countries project cost technology, regulations, management system and its development trend, to expand domestic and foreign exchanges, and actively participate in international or regional engineering activities, improve their professional quality, so that the current practitioners in intelligentstructure, theory and working experience three aspects can meet the needs of engineering cost management. Cost engineering professionals need to strengthen their own learning, in addition to the professional knowledge to upgrade, should also work in combination with a broad understanding and master the relevant engineering and technical expertise, educational organizations and industry regulatory bodies constitute a complete education system, so as to the field of engineering senior talent development to create good conditions.中文译文:工程造价与管理工程造价控制重点应转移到项目建设的前期,即转移到项目决策和设计阶段。
工程造价毕业论文外文文献

工程造价毕业论文外文文献————————————————————————————————作者:————————————————————————————————日期:外文文献:Construction Standards and CostsUC Irvine new construction pursues performance goals and applies quality standards that affect the costs of capital projects. Periodic re-examination of these goals and standards is warranted.Construction costs are not “high” or “low” in the abstract, but rather in relation to specific quality standards and the design solutions, means, and methods used to attain these standards. Thus, evaluating whether construction costs are appropriate involves: • first, determining whether quality standards are excessive, insufficient, or appropriate;• second, determining whether resultant project costs are reasonable compared to projects with essentially the same quality parameters.“Quality” encompasses the durability of building systems and finishes; the robustness and life-cycle performance of building systems; the aesthetics of materials, their composition, and their detailing; and the resource-sustainability and efficiency of the building as an overall system.Overall Goals and Quality StandardsUC Irvine, in order to support distinguished research and academic programs, builds facilities of high quality. As such, UC Irvine’s facilities aim to convey the “look and feel,” as well as embody the inherent construction quality, of the best facilities of other UC campuses, leading public universities, and other research institutions with whom we compete for faculty, students, sponsored research, and general reputation.Since 1992, new buildings have been designed to achieve these five broad goals:1. New buildings must “create a place,” rather than constitute stand-alone structures, forming social, aesthetic, contextually-sensitive relationships with neighboring buildings and the larger campus.2. New buildings reinforce a consistent design framework of classical contextual architecture, applied in ways that convey a feeling of permanence and quality andinterpreted in ways that meet the contemporary and changing needs of a modern research university.3. New buildings employ materials, systems, and design features that will avoid the expense of major maintenance (defined as >1 percent of value)for twenty years.4. New buildings apply “sustainability” principles -- notably, outperforming Title 24 (California’s energy code) by at least 20 percent.5. Capital construction projects are designed and delivered within theapproved project budget, scope, and schedule.UC Irvine’s goals for sustainable materials and energy performance were adopted partly for environmental reasons, and partly to reverse substantial operating budget deficits.The latter problems included a multi-million dollar utilities deficit that was growing rapidly in the early ‘90s, and millions of dollars of unfunded major maintenance that was emerging prematurely in buildings only 10-20 years old. Without the quality and performance standards adopted in 1992, utilities deficits and unfunded major maintenance costs would have exceeded $20 million during the past decade, and these costs would still be rising out-of-control.UC Irvine’s materials standards, building systems standards, sustainability and energy efficiency criteria, and site improvements all add cost increments that can only be afforded through aggressive cost management. Institutions that cannot manage capital costs tend to build projects that consume excessive energy, that cost a lot to maintain, that suffer premature major maintenance costs, and that require high costs to modify. Such problems tend to compound and spiral downward into increasingly costly consequences.Every administrator with facilities experience understands this dynamic. Without effective construction cost management, quality would suffer and UC Irvine would experience all of these problems.The balance of this document outlines in greater detail the building performance criteria and quality standards generally stated above, organized according to building systems component classes. Each section discusses key cost-drivers, cost-control strategies, andimportant cost trade-offs. Design practices cited are consistently applied (although some fall short of hard and fast “rules”).Building Organization and MassingConstruction cost management starts with the fundamentals of building organization and massing. UC Irvine’s new structures’ floor plates tend to have length-to-width ratios<1.5, to avoid triggering disproportionate costs of external cladding, circulation, and horizontal mechanical distribution. Our new buildings tend to be at least three floorshigh -- taller if floor plate areas do not dip below a cost-effective threshold, and generally taller in the case of non-laboratory buildings (but not so tall that a high-rise cost penalty is incurred). Other design ratios are observed, such as exterior cladding area/floor area <0.5, and roof+foundation area/floor area <0.4.Architectural articulation is generally achieved through textured or enriched materials,integral material detailing (such as concrete reveal patterning), and applied detailing (e.g.,2window frames and sills), particularly at the building base. Large-scale articulation is concentrated at the roofline (e.g., shaped roof forms) and at the pedestrian leve l (e.g.,arcades), where it will “create the biggest bang for the buck,” rather than through modulating the building form, itself. This is more than a subtle design philosophy, as the cost impact is substantial.Lab buildings completed in the past decade separate laboratory and non-laboratory functions into distinct, adjoined structures (although such a building may look like one structure). Consolidated non-laboratory functions include faculty, departmental, staff,post-doc, and graduate student offices; restrooms; circulation (elevators, lobbies, primary stairways); classrooms, seminar rooms, conference rooms, and social areas designed tofoster interaction and to provide a safe area for eating and drinking; dry labs and dry lab support functions; and general administrative support.Consolidating these functions into a separate structure provides considerable cost savings: lower-cost HV AC (heating/ventilation/air-conditioning) system, wider column spacing, lower floor stiffness (less stringent vibration criterion), lowerfloor-loading,fewer fire-control features and other code requirements, steel-framed or steel/concrete hybrid structural system with concrete flat-slab flooring system, smaller footings, and(typically) curtain wall fenestration. This approach usually enables offices to have operable windows.This two-building approach can be seen clearly at Gillespie Neurosciences Building, the Sprague Building, Hewitt Hall, and the UCI Medical Center Health Sciences Laboratory,where consolidating and separating non-laboratory functions saved 7-10 percent in overall construction costs and 15 percent/year in energy expense. (The non-laboratory building incurs a small fraction of the energy expense of the laboratory block.)A set of design strategies, applied in combination, has proven effective in controlling the cost of laboratories:• Utilizing a consistent lab module• Utilizing a reasonable vibration criterion and locating ultra-sensitive conditions at-grade or employing benchtop vibration isolation• Using 22 ft. X 22 ft. column-spacing• Concentrating fume hoods and utility risers into a central “wet zone,” thuslimiting horizontal mechanical distribution• Concentrating laboratory support areas into the central core of a laboratory structure, where utilities are available but daylight is not needed, thus enablinglab structures to be 110-132 feet wide• Utilizing dual-usage circulation/equipment cross-corridors through this central lab support zone, with sufficient width (typically 11 feet) to line the corridors with shared equipment while providing cross-circulation through the lab support zone• Utilizing open laboratory layout with one or more “ghost” corridors for intra lab circulation• And, most importantly, concentrating non-laboratory functions into an adjoining, lower-cost structure (as discussed in detail above).To further control laboratory construction costs, non-standard fume hood sizes are minimized, “generic” lab casework is specified, laboratory-grade movable tablessubstitute for fixed casework in some lab bays, building DI systems provide intermediate water quality (with localized water purity polishing in the lab, rather than building-wide),facility-wide piped services do not include gases that can be cost-effectively provided locally via canisters, and glass-wash facilities are consolidated -- typically, one glass wash facility for an entire laboratory building. Finally, our design philosophy leans toward generic, modular laboratories supported by a robust building infrastructure, rather than highly customized spaces with limited capacity to make later changes. This is an important trade off. Although some post-occupancy expenses may be necessary to “fine-tune” a laboratory to a PI’s requirements, building infrastructure elements – typically over sized twenty percent, including HV AC supply ducts, exhaust system capacity, emergency generator capacity, and electric risers and service capacity – seldom limit the ability to modify labs to meet researcher needs.Structural and Foundation SystemsFor both cost-benefit reasons and past seismic performance, UC Irvine favors concrete shear wall or steel braced-frame structural systems. The correlating foundation systems depend on site-specific soil conditions. Past problems with undiscovered substrates and uncharacterized soil conditions are minimized through extensive, pre-design soil-testing. This minimizes risk to both the University and the design/build contractor. When feasible, design/build contractors are allowed flexibility to propose alternate structural or seismic-force systems. All structural system designs must pass a peer review, according to Regents’ policy. This process results in conservative structural design, and an associated cost premium. However, the seismic performance of University of California buildings constructed since this policy went into effect in 1975 appears to substantiate the value of the Regents’ Seismic Review Policy.Structural vibration is carefully specified in research buildings where vibration-sensitive protocols and conditions must be maintained on above-grade floors. The most cost effective tools to control vibration are generally employed: first, to program vibration sensitive procedures at on-grade locations or to isolate them at the bench; second, to space columns at a distance that does not entail excessive structuralcosts. In laboratory 4buildings we typically utilize 22 ft. X 22 ft. column-spacing. Conversely, where vibration is not problematic a beam/column system can be cost-optimized and lighter floor loading can be tolerated. Design/build contractors are, accordingly, allowed more flexibility under such conditions.To control costs, UC Irvine avoids use of moment-resisting structures; unconventional seismic systems; non-standard structural dimensions; inconsistent, unconventional, or non-stacking structural modules; and non-standard means and methods.Roofs and FlashingsUC Irvine specifies 20 year roofing systems and stainless steel or copper flashings whenever possible. At minimum, we specify hot-dip galvanized flashings.Why this emphasis on flashings? Our roof replacement projects typically double in cost when the old roofing is torn off and it is determined that the flashings have deteriorated. Moreover, many roof leaks of recent years have been due to faulty flashings, rather than roofing membranes or coatings, per se. Saving money on flashings is false economy. Another special roofing expense we may have to incur in order to attain the Regents’Green Building Policy is that of reflective roofing. It is too early to understand the potential cost impact.中文翻译:建设标准和成本加州大学欧文分校新建筑追求性能目标和适用的质量标准,影响资本成本的项目。
工程造价外文及翻译

.The Cost of Building Structure1. IntroductionThe art of architectural design was characterized as one of dealingcomprehensively with a complex set of physical and nonphysical designdeterminants. Structural considerations were cast as important physicaldeterminants that should be dealt with in a hierarchical fashion if theyare to have a significant impact on spatial organization and environmentalcontrol design thinking.The economical aspect of building represents a nonphysical structuralconsideration that, in final analysis, must also be considered important.Cost considerations are in certain ways a constraint to creative design.But this need not be so. If something is known of the relationship betweenstructural and constructive design options and their cost of implementation, it is reasonable to believe that creativity can beenhanced. This has been confirmed by the authors' observation that mostenhanced. This has been confirmed by the authors' observation that mostcreative design innovations succeed under competitive bidding and notbecause of unusual owner affluence as the few publicized cases ofextravagance might lead one to believe. One could even say that a designerwho is truly creative will produce architectural excellence within theconstraints of economy. Especially today, we find that there is a needto recognize that elegance and economy can become synonymous concepts.Therefore, in this chapter we will set forth a brief explanation ofthe parameters of cost analysis and the means by which designers mayevaluate the overall economic implications of their structural andarchitectural design thinking.The cost of structure alone can be measured relative to the total costof building construction. Or, since the total construction cost is buta part of a total project cost, one could include additional considerationfor land(10~20percent),finance and interest(100~200percent),taxesand maintenance costs (on the order of20 percent).But a discussion ofthese so-called architectural costs is beyond the scope of this book, andwe will focus on the cost of construction only.文档资料Word.On the average, purely structural costs account for about 25 percentof total construction costs, This is so because it has been traditionalto discriminate between purely structural and other so-called architectural costs of construction. Thus, in tradition we find thatarchitectural costs have been taken to be those that are not necessaryfor the structural strength and physical integrity of a building design.“Essential services” forms a third construction costcategory andrefers to the provision of mechanical and electrical equipment and otherservice systems. On the average, these service costs account for some 15to 30 percent of the total construction cost, depending on the type ofbuilding. Mechanical and electrical refers to the cost ofproviding forair-conditioning equipment and he means on air distribution as well asother services, such as plumbing, communications, and electrical lightand power.The salient point is that this breakdown of costs suggests that, upto now, an average of about 45 to 60 percent of the total cost ofconstructing a typical design solution could be considered asarchitectural. But this picture is rapidly changing. With high interestcosts and a scarcity of capital, client groups are demanding leanerdesigns. Therefore, one may conclude that there are two approaches thedesigner may take towards influencing the construction cost of building.The first approach to cost efficiency is to consider that whereverarchitectural and structural solutions can be achieved simultaneously,a potential for economy is evident. Since current trends indicate areluctance to allocate large portions of a construction budget to purelyarchitectural costs, this approach seems a logical necessity. But, evenwhere money is available, any use of structure to play a basic architectural role will allow the nonstructural budget to be applied tofulfill other architectural needs that might normally have to be appliedto fulfill other architectural needs that might normally have to be cutback. The second approach achieves economy through an integration ofservice and structural subsystems to round out one's effort to producea total architectural solution to a building design problem. The final pricing of a project by the constructor or contractor usually文档资料Word.takes a different form. The costs are broken down into (1) cost ofmaterials brought to the site, (2)cost of labor involved in every phaseof the construction process, (3)cost of equipment purchased or rented forthe project, (4)cost of management and overhead, and(5) profit. Thearchitect or engineer seldom follows such an accurate path but shouldperhaps keep in mind how the actual cost of a structure is finally pricedand made up.Thus, the percent averages stated above are obviously crude, but theycan suffice to introduce the nature of the cost picture. The followingsections will discuss the range of these averages and then proceed to adiscussion of square footage costs and volume-based estimates for use inrough approximation of the cost of building a structural system.2. Percentage EstimatesThe type of building project may indicate the range of percentages thatcan be allocated to structural and other costs. As might be expected,highly decorative or symbolic buildings would normally demand the lowestpercentage of structural costs as compared to total construction cost.In this case the structural costs might drop to 10~15percentof the totalbuilding cost because more money is allocated to the so-called architectural costs. Once again this implies that the symbolic componentsare conceived independent of basic structural requirements. However,where structure and symbolism are more-or-less synthesized, as with achurch or Cathedral, the structural system cost can be expected to besomewhat higher, say, 15and20 percent (or more).At the other end of the cost scale are the very simple and nonsymbolicindustrial buildings, such as warehouses and garages. In these cases, thenonstructural systems, such as interior partition walls and ceilings, aswill as mechanical systems, are normally minimal, as is decoration, andtherefore the structural costs can account for60 to 70 percent, even 80percent of the total cost of construction.Buildings such as medium-rise office and apartmentbuildings(5~10stories)occupy the median position on a cost scale at about 25 percentfor structure. Low and short-span buildings for commerce and housing, say,of three or four stories and with spans of some 20 or 30 ft and simple文档资料Word.erection requirements, will yield structural costs of 15~20 percent oftotal building cost.Special-performance buildings, such as laboratories and hospitals,represent another category. They can require long spans and a more thanaverage portion of the total costs will be allocated to services (i.e.,30~50 percent), with about 20 percent going for the purelystructuralcosts. Tall office building (15 stories or more) and/or long-spanbuildings (say, 50 to 60 ft) can require a higher percentage for structuralcosts (about 30to 35percent of the total construction costs),with about30 to 40 percent allocated to services.In my case, these percentages are typical and can be considered as ameasure of average efficiency in design of buildings. For example, if alow, short-span and nonmonumental building were to be bid at 30 percentfor the structure alone, one could assume that the structural design maybe comparatively uneconomical. On the other hand, the architect shouldbe aware of the confusing fact that economical bids depend on the practicalability of both the designer and the contractor to interpret the designand construction requirements so that a low bid will ensue. Progress instructural design is often limited more by the designer's or contractor'slack of experience, imagination, and absence of communication than bythe idea of the design. If a contractor is uncertain, he will add coststo hedge the risk he will be taking. It is for this reason that both thearchitect and the engineer should be well-versed in the area ofconstruction potentials if innovative designs ate to be competitively bid.At the least the architect must be capable of working closely withimaginative structural engineers, contractors and even fabricatorswherever possible even if the architecture is very ordinary. Efficiencyalways requires knowledge and above all imagination, and these areessential when designs are unfamiliar.The foregoing percentages can be helpful in approximating totalconstruction costs if the assumption is made that structural design isat least of average (of typical) efficiency. For example, if a total officebuilding construction cost budget is ﹩5,000,000,and 25percent is the“standard” to be used for structure, a projected structural system文档资料Word.should cost no more than ﹩1,250,000.If a very efficientdesign wererealized, say, at 80 percent of what would be given by the “average”efficient design estimate stated above the savings,(20 percent),wouldthen be﹩250,000 or 5 percent of total construction costs ﹩5,000,000.Ifthe ﹩5,000,000 figure is committed, then the savings of ﹩250,000 couldbe applied to expand the budget for “other” costs.All this suggests that creative integration of structural (and mechanical and electrical) design with the totalarchitectural designconcept can result in either a reduction in purely construction designconcept can result in either a reduction in purely construction costs ormore architecture for the same cost. Thus, the degree of success possibledepends on knowledge, cleverness, and insightful collaboration of thedesigners and contractors.The above discussion is only meant to give the reader an overall perspective on total construction costs. The following sections will nowfurnish the means for estimating the cost of structure alone. Twoalternative means will be provided for making an approximate structuralcost estimate: one on a square foot of building basis, andanother onvolumes of structural materials used. Such costs can then be used to geta rough idea of total cost by referring to the “standards”for efficientdesign given above. At best, this will be a crude measure, but it is hopedthat the reader will find that it makes him somewhat familiar with thetype of real economic problems that responsible designers must deal with.At the least, this capability will be useful in comparing alternativesystems for the purpose of determining their relative cost efficiency.3. Square-foot EstimatingAs before, it is possible to empirically determine a “standard”per-square-foot cost factor based on the average of costs for similarconstruction at a given place and time. more-or-less efficient designsare possible, depending on the ability of the designer and contractor touse materials and labor efficiently, and vary from the average.The range of square-foot costs for “normal” structural systems is﹩10 to ﹩16 psf. For example, typical office buildings averagebetween﹩12 and ﹩16 psf, and apartment-type structures range from ﹩10 to ﹩文档资料Word.14.In each case, the lower part of the range refers to short spans andlow buildings, whereas the upper portion refers to longer spans andmoderately tall buildings.Ordinary industrial structures are simple and normallyproducesquare-foot costs ranging from ﹩10 to ﹩14,as with the moretypicalapartment building. Although the spans for industrial structures aregenerally longer than those for apartment buildings, and the loads heavier,they commonly have fewer complexities as well as fewer interior walls,partitions, ceiling requirements, and they are not tall. In other words,simplicity of design and erection can offset the additional cost forlonger span lengths and heavier loads in industrial buildings. Of course there are exceptions to these averages. The limits ofvariation depend on a system's complexity, span length over “normal”and special loading or foundation conditions. For example, the CrownZellerbach high-rise bank and office building in San Francisco isan exception, since its structural costs were unusually high. However,in this case, the use of 60 ft steel spans and free-standing columns atthe bottom, which carry the considerable earthquake loading, as well asthe special foundation associated with the poor San Francisco soilconditions, contributed to the exceptionally high costs. The design wasalso unusual for its time and a decision had been made to allow higherthan normal costs for all aspects of the building to achieve open spacesand for both function and symbolic reasons. Hence the proportion ofstructural to total cost probably remained similar to ordinary buildings.The effect of spans longer than normal can be further illustrated. The“usual” floor span range is as follows: for apartmentbuildings,16 to25 ft; for office buildings,20 to 30 ft; for industrial buildings,25 to30 ft loaded heavily at 200 to 300 psf; and garage-type structures span,50to 60 ft, carrying relatively light(50~75 psf) loads(i.e.,similar tothose for apartment and office structures).where these spans are doubled,the structural costs can be expected to rise about 20 to 30 percent.To increased loading in the case of industrial buildings offers anotherinsight into the dependency of cost estimates on “usual”standards. Ifthe loading in an industrial building were to be increased to 500psf(i.e.,文档资料Word.two or three times), the additional structural cost would be on the orderof another 20 to 30 percent.The reference in the above cases is for floor systems. For roofs usingefficient orthotropic (flat) systems, contemporary limits for economicaldesign appear to be on the order of 150 ft, whether of steel or prestressedconcrete. Although space- frames are often used for steel orprestressed concrete. Although space-frames are often used for steelspans over 150 ft the fabrication costs begin to raise considerably.At any rate, it should be recognized that very long-span subsystems arespecial cases and can in themselves have a great or small effect on isadded, structural costs for special buildings can vary greatly from designto design. The more special the form, themore that design knowledge andcreativity, as well as construction skill, will determine the potentialfor achieving cost efficiency.4. Volume-Based EstimatesWhen more accuracy is desired, estimates of costs can be based on thevolume of materials used to do a job. At first glance it might seem thatthe architect would be ill equipped to estimate the volume of materialrequired in construction with any accuracy, and much less speed. But itis possible, with a moderate learning effort, to achieve some capabilityfor making such estimates.Volume-based estimates are given by assigning in-place value to thepounds or tons of steel, or the cubic yards of reinforced or prestressedconcrete required to build a structural system. For such a preliminaryestimate, one does not need to itemize detailed costs. For example,in-place concrete costs include the cost of forming, falsework,reinforcing steel, labor, and overhead. Steel includes fabrication anderection of components.Costs of structural steel as measured by weight range from ﹩0.50 to﹩0.70 per pound in place for building construction. Forlow-risebuildings, one can use stock wide-flange structural members that requireminimum fabrication, and the cost could be as bow as ﹩0.50per pound.More complicated systems requiring much cutting andwelding(such as acomplicated steel truss or space-frame design) can go to ﹩0.70 per pound文档资料Word.and beyond. For standard tall building designs (say, exceeding 20stories),there would typically be about 20 to 30 pounds of steel/psf,which one should wish not to exceed. A design calling for under 20 psfwould require a great deal of ingenuity and the careful integration ofstructural and architectural components and would be a real accomplishment.Concrete costs are volumetric and should range from anin-place lowof ﹩150 per cu yd for very simple reinforced concrete work to ﹩300 percu yd for expensive small quantity precast and prestressed work. Thislarge range is due to the fact that the contributing variables are morecomplicated, depending upon the shape of the precise components, theerection problems, and the total quantity produced.Form work is generally the controlling factor for anycast-in-placeconcrete work. Therefore, to achieve a cost of ﹩150 per cuyd, only thesimplest of systems can be used, such as flat slabs that require littlecutting and much reuse of forms. Where any beams are introduced thatrequire special forms and difficulty in placement of concrete and steelbars, the range begins at ﹩180 per cu yd and goes up to ﹩300.Since, ina developed country, high labor costs account for high forming costs, thisresults in pressure to use the simplest and most repetitive of systemsto keep costs down. It become rewarding to consider the possibility ofmass-produced precast and prestressed components, which may bring asaving in costs and\or construction completion time. The latter resultsin savings due to lower construction financing costs for the contractorplus quicker earnings for the owner.To summarize, the range of cost per cubic yard of standard types ofpoured-in-place concrete work will average from $150 to $250, the minimumbeing for simple reinforced work and the maximum for moderatelycomplicated post tensioned work. This range is large and any estimate thatignores the effect of variables above will be commensurately inaccurate.5.SummaryThe estimate and economical design of structure building are importantand essential work, which should be valued by all architects and engineersand others. Better you do it, more profit you will receive from it!文档资料Word.建筑结构的成本1.前言众所周知,建筑物的结构设计是一个相当复杂的过程,其中既包含处理很多物质因素,又考虑诸多非物质方面的因素。
交通工程专业外文翻译外文文献英文文献
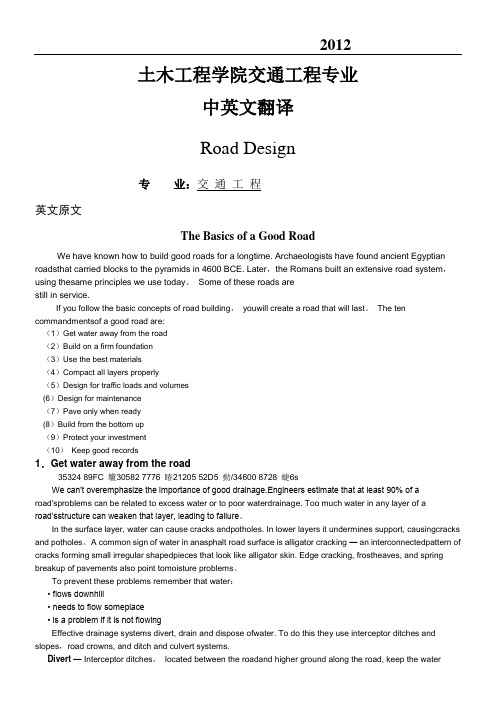
土木工程学院交通工程专业中英文翻译Road Design专业:交通工程英文原文The Basics of a Good RoadWe have known how to build good roads for a longtime. Archaeologists have found ancient Egyptian roadsthat carried blocks to the pyramids in 4600 BCE. Later,the Romans built an extensive road system,using thesame principles we use today。
Some of these roads arestill in service.If you follow the basic concepts of road building,youwill create a road that will last。
The ten commandmentsof a good road are:(1)Get water away from the road(2)Build on a firm foundation(3)Use the best materials(4)Compact all layers properly(5)Design for traffic loads and volumes(6)Design for maintenance(7)Pave only when ready(8)Build from the bottom up(9)Protect your investment(10)Keep good records1.Get water away from the road35324 89FC 觼30582 7776 睶21205 52D5 動/34600 8728 蜨6sWe can’t overemphasize the importance of good drainage.Engineers estimate that at least 90% of aroad'sproblems can be related to excess water or to poor waterdrainage. Too much water in any layer of aroad’sstructure can weaken that layer, leading to failure。
- 1、下载文档前请自行甄别文档内容的完整性,平台不提供额外的编辑、内容补充、找答案等附加服务。
- 2、"仅部分预览"的文档,不可在线预览部分如存在完整性等问题,可反馈申请退款(可完整预览的文档不适用该条件!)。
- 3、如文档侵犯您的权益,请联系客服反馈,我们会尽快为您处理(人工客服工作时间:9:00-18:30)。
本科毕业设计(论文)外文翻译译文题目:建筑招投标与赢者诅咒:博弈论方法学院:经济与管理学院专业:工程造价学生姓名:**学号:************指导教师:***完成时间:2017年4月5日译自:Muaz O.Ahmed1;Islam H. El-adaway, M.ASCE2; Kalyn T. Coatney3;and Mohamed S. Eid4. Construction Bidding and the Winner’s Curse: Game Theory Approach[J],Construction Engineering and Management,2016,142(2).建筑招投标与赢者诅咒:博弈论方法Muaz O.Ahmed1;Islam H. El-adaway, M.ASCE2; Kalyn T. Coatney3;and Mohamed S. Eid4美国密西西比州立大学土木与环境工程系摘要:在建筑业中,竞争投标一直是承包商选择的一种方法。
由于施工的真实成本直到项目完工后才知道,所以逆向选择是一个重大问题。
逆向选择是当合同的赢家低估了项目的真实成本,从而中标承包商很有可能赚取负或至少低于正常利润。
赢家的诅咒是当中标人提交一个被低估的出价,因此诅咒被选中承担项目。
在多阶段招标环境下,分包商由总承包商雇用,胜利者的诅咒可能会复合。
在一般情况下,承包商遭受赢者的诅咒,因为各种各样的原因包括项目成本估计不准确;新的承包商进入建筑市场;在建筑行业的衰退的情况下减少损失;在建筑市场激烈的竞争;差的机会成本,从而影响承包商的行为;以及要赢该项目然后弥补订单变更、索赔和其他机制而带来的损失。
本文通过博弈论方法旨在分析并减少潜在的施工招投标中赢家诅咒的影响。
为此,作者确定在两个共同的施工招标环境的赢家诅咒的程度,即单级招标和多级招标。
我们的目标是比较上述两个施工招标环境,并确定如何学习从过去的投标决策和经验可以减轻赢家的诅咒。
为此,通过定义施工招标和拍卖理论之间的关系,利用三步研究方法包括(1)呈现对称风险中性的纳什均衡作为最优报价功能;(2)开发仿真模型用于单级和多级施工招标过程;(3)分析仿真模型的结果,它是基于由加利福尼亚州运输部提供项目的一个实际的数据集。
这项研究表明,大多数的一般承包商和分包商在单级和多阶段投标环境遭受赢家的诅咒。
此外,从赢者的诅咒的角度来看,多阶段的投标环境比单级投标环境造成更多的损失。
然而,通过学习过去的经验,如果与单级招标环境相比,多级招标环境提供给承包商一个更好的机会以避免赢家的诅咒。
这项研究对同行来说是有益的,便于他们更好地了解投标决策过程。
对于未来的工作,合作博弈理论可以与完整的项目交付原则结合起来,以帮助所有相关各方相互实现自己的项目目标。
关键词:工程承包1. 引言了解施工行业的基本过程对于承包商保持竞争力,同时对于一个国家经济有效运作至关重要。
根据Kululanga等(2001年),建筑行业在早期纳入了简单直观的流程。
然而,建筑行业在当今世界越来越复杂和复杂。
建筑行业的发展为承包商开创了竞争环境。
因此,承包商需要制定完善的计划,以接受不同的观点,以便领先于竞争对手。
建筑行业艰巨的任务之一是承包商选择过程。
竞争性投标一直被用作分配合同的方法(Seydel 2003)。
此外,在公共部门,竞争性投标被认为是法律要求。
因此,有人认为,对建设项目成功影响的主要因素之一是企业的投标策略。
根据Park and Chapin(1992)的说法,承包商提交建议,表明他们愿意按约定的价格进行建设项目。
一般来说,在施工招标过程中,提交的投标在技术上进行评估,然后根据提交的价格对技术上批准的投标进行财务评估。
对于提交投标的财务评估,采用低价中标法,第二低价中标法,平均报价方法和低于平均报价法等方法(Ioannou和Awwad 2010)。
根据Ioannou和Awwad(2010)的说法,低价中标法是美国建筑合同最常用的方法。
在本文适用的低价中标方式中,合同授予技术认可的承包商,并在提交的投标中具有最低的价格。
因此,获胜承包商预计将根据约定的价格和时间表建设项目,并提供所需的质量水平。
竞争投标的成功与否取决于诸多因素,这些因素被认为是建筑工程投标竞争环境的主要来源。
如盖茨(Gates)(1967)所述,承包商希望获得项目合同有很多原因,例如(1)增加赚取的利润;(2)尽量减少损失,因为承包商即使在经济衰退期间也能保持公司的完整性;(3)尽量减少竞争对手的利润,以保持建筑行业市场的长期良好竞争地位。
由于上述所有原因,在提交投标前,每个承包商正在对每个投标情况做出许多关键决定。
(1)Bagies and Fortune(2006)指出,在承诺建筑项目之前的阶段,承包商受到是否投标决定的影响,从而承包商考虑了许多有助于确定预期的因素来正确评估建设项目是否受益。
(2)与招标策略相关的投标策略。
正如King和美世(1985)所引用的,投标策略是任何建筑公司总体业务规划的重要组成部分。
在过去的50 年,许多模型已经被开发用于在建筑工程招投标中的应用。
根据Wanous等人(2000),这些投标模式中的大多数只集中于加价决策,如Friedman(1956)和盖茨(1967)开发的模型。
然而,尽管有许多与招标相关的出版物,投标模式也大部分忽视了人的行为(Ahmadand Minkarah,1988)。
许多研究人员认为,在现实中,投标决定是以经验和直觉为基础,并受到对每个投标情况的压力的情绪反应的影响(Fayek 1998)。
此外,Runeson 和Skitmore(1999)认为,在开发的投标模式中应用的一些基本假设是不现实的,其预测结果并不总是正确的。
因此,在施工招标中需要采用更有效率的投标模式,与其在假设中的施工招标过程的实际情况相一致,克服了以前发布的招标模式的局限性。
最近,许多研究人员倾向于开发新技术来帮助承包商使用模糊神经网络进行招标决策(Polat 等,2014)。
预计这些技术应有助于承包商估计最佳出价金额,以便在施工招投标中投标报价。
最后,施工项目面临施工项目生命周期中可能发生的许多事件的高度不确定性。
例如,承包商面对周期长的项目投标时必须考虑的投入成本,劳动力问题和施工条件的不可避免和不可预见的增加。
在提交投标时,承包商不能确定地知道实际的项目建设成本。
因此,建筑行业依赖于承包商当前信息,过去经验和利用RSMeans等方法对项目成本的估算。
因此,在施工招投标中,低估项目成本和招标费用的承包商投标报价比项目建设成本低,因此面临不利选择所带来的问题。
这种不利的选择导致的结果被称为胜利者的诅咒。
2.目标本文运用博弈论的方法,分析并减轻工程招投标中赢者诅咒的潜在影响。
为此,作者确定在两个共同的施工招标环境的赢家诅咒的程度,即单级招标和多级招标。
我们的目标是比较上述两个施工招标环境,并确定如何从过去的投标决策和经验学习可以减轻赢家的诅咒方法。
3. 背景信息自从约翰·冯·诺依曼(John von Neumann)和奥斯卡·莫根斯坦(Oskar Morgenstern)发表“运动与经济行为理论”以来,社会和行为科学已经开发出数学工具来描述人类行为。
为此,游戏理论被定义为“智慧理性决策者之间冲突与合作数学模型的研究”(Myerson 1991。
博弈论已经应用于人类生活的不同方面。
20世纪50年代和60年代,博弈论被应用于战争中的决策和政治问题。
20世纪70年代,博弈论彻底改变了经济研究领域。
此外,它已经应用于社会学,心理学和生物学。
在诺贝尔奖获得诺贝尔奖后,博弈论及其从业者在约翰·纳什(John Nash),约翰·哈桑尼(John Harsanyi)和雷因哈德·塞尔滕(Reinhard Selten)的1994年获得了长期以来的认可和合法性(Turocy和Stengel 2001)。
在建筑行业,研究人员已经应用了各种博弈论模型来解释和预测结果。
何(2001)利用博弈论分析了不对称信息存在下的建设运营转移项目采购流程及其对项目融资和政府政策的影响。
Drew和Skitmore(2006)通过拍卖理论,博弈理论的亚科学分析,分析了建筑行业的竞标计划。
何和刘(2004)通过博弈论模型分析了承包商和建筑业主之间的动态。
Karl(2014)开发了一种模块化建模方法,用于模拟建筑行业不同层次的多层次和动态关系。
此外,博弈论也被应用于检查分包商选择的策略(Unsal和Taylor 2011),并分析投标报酬对竞标投标过程的影响(Ho 2005)。
因此,博弈论被认为是分析建筑行业许多问题的重要工具。
一般来说,博弈论模型可以根据信息的完整性和游戏的播放方式进行分类。
基于博弈的方法,有两种类型:(1)静态博弈,玩家在决定的同时采取行动,不知道其他玩家选择的决策,以及(2)动作博弈(其他行动)(Ho和Hsu,2014)。
一般来说,施工竞标模式可以认为遵循静态博弈概念,因为投标人在提交投标时不知道竞争对手的投标。
此外,博弈论概念基本上有两个主要部分:(1)合作博弈理论,其中玩家合作共同获得更多的收益,并在他们之间公平分配收益;(2)非合作博弈理论,其中每个玩家独立选择一个策略并尝试最大化收益,并且玩家之间没有勾结(Asgari和Afshar 2008)。
纳什(1950)均衡被认为是非合作博弈的解决方案,假设所有玩家都是理性的。
一般来说,施工竞争性招标可以描述为非合作游戏,因为每个总承包商(GC)或分包商(SC)都试图赢得竞争,并在存在利益冲突的情况下使个人的收益最大化。
因此,可以得出结论,为了开发一个描述实际投标的更好的模型,博弈论模型与静态移动和不完整信息不合作。
拍卖已被用于分发货物和服务数千年。
从博弈论的角度来看,拍卖被认为是不完整信息博弈最优秀的应用之一,因为拍卖参与者有不同的私人信息,这是影响其战略行为的主要因素。
拍卖通常分为两大类:(1)私有价值拍卖,(2)共同价值拍卖。
在私人价值拍卖中,投标人可以确定地知道自己拍卖品的价值,但不知道其他投标人的价值。
然而,在共同价值拍卖中,被拍卖的物品对每个人都具有相同的价值(即成本),但是没有一个投标人确定地知道这个价值。
因此,每个投标人都会制定一个关于真实价值的独立和相同分布的估计,赢家是具有最真实价值的信息(Kagel和Levin,2002)。
关于建筑行业,承包商在提交投标时有两个不完整的信息来源:(1)实际(实现)项目建设成本,(2)竞争对手对项目建设成本的估计。
因此,根据Dyer和Kagel(1996),施工招标被认为是一个共同价值的拍卖。