航空发动机宽弦空心风扇叶片的发展及应用
航空发动机叶片关键技术发展现状分析
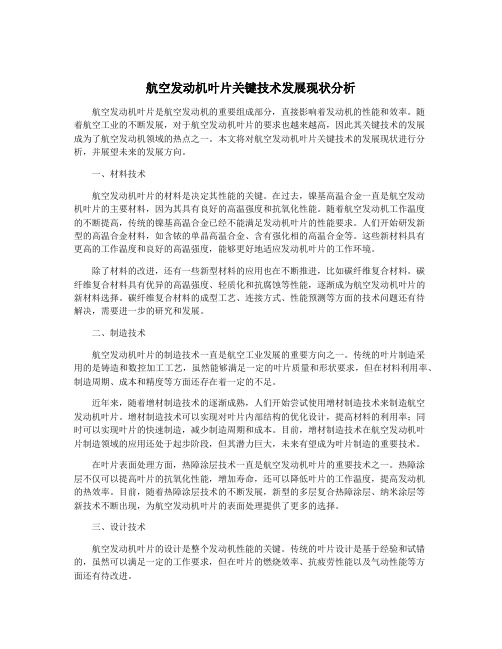
航空发动机叶片关键技术发展现状分析航空发动机叶片是航空发动机的重要组成部分,直接影响着发动机的性能和效率。
随着航空工业的不断发展,对于航空发动机叶片的要求也越来越高,因此其关键技术的发展成为了航空发动机领域的热点之一。
本文将对航空发动机叶片关键技术的发展现状进行分析,并展望未来的发展方向。
一、材料技术航空发动机叶片的材料是决定其性能的关键。
在过去,镍基高温合金一直是航空发动机叶片的主要材料,因为其具有良好的高温强度和抗氧化性能。
随着航空发动机工作温度的不断提高,传统的镍基高温合金已经不能满足发动机叶片的性能要求。
人们开始研发新型的高温合金材料,如含铱的单晶高温合金、含有强化相的高温合金等。
这些新材料具有更高的工作温度和良好的高温强度,能够更好地适应发动机叶片的工作环境。
除了材料的改进,还有一些新型材料的应用也在不断推进,比如碳纤维复合材料。
碳纤维复合材料具有优异的高温强度、轻质化和抗腐蚀等性能,逐渐成为航空发动机叶片的新材料选择。
碳纤维复合材料的成型工艺、连接方式、性能预测等方面的技术问题还有待解决,需要进一步的研究和发展。
二、制造技术航空发动机叶片的制造技术一直是航空工业发展的重要方向之一。
传统的叶片制造采用的是铸造和数控加工工艺,虽然能够满足一定的叶片质量和形状要求,但在材料利用率、制造周期、成本和精度等方面还存在着一定的不足。
近年来,随着增材制造技术的逐渐成熟,人们开始尝试使用增材制造技术来制造航空发动机叶片。
增材制造技术可以实现对叶片内部结构的优化设计,提高材料的利用率;同时可以实现叶片的快速制造,减少制造周期和成本。
目前,增材制造技术在航空发动机叶片制造领域的应用还处于起步阶段,但其潜力巨大,未来有望成为叶片制造的重要技术。
在叶片表面处理方面,热障涂层技术一直是航空发动机叶片的重要技术之一。
热障涂层不仅可以提高叶片的抗氧化性能,增加寿命,还可以降低叶片的工作温度,提高发动机的热效率。
目前,随着热障涂层技术的不断发展,新型的多层复合热障涂层、纳米涂层等新技术不断出现,为航空发动机叶片的表面处理提供了更多的选择。
航空发动机风扇 压气机叶片激光冲击强化技术的发展与应用
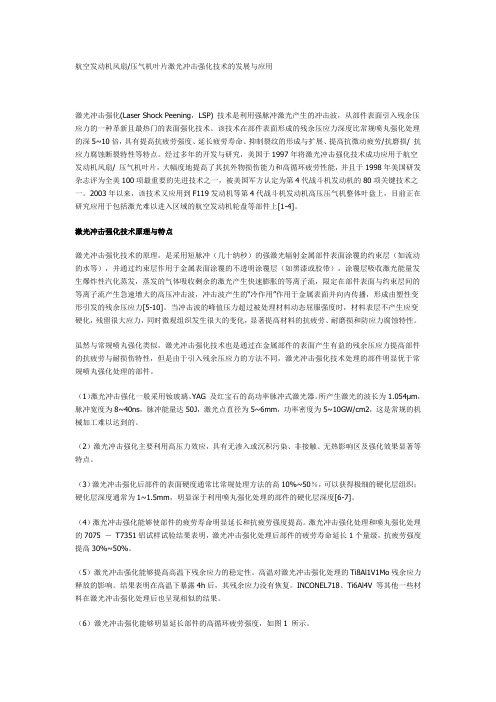
航空发动机风扇/压气机叶片激光冲击强化技术的发展与应用激光冲击强化(Laser Shock Peening,LSP) 技术是利用强脉冲激光产生的冲击波,从部件表面引入残余压应力的一种革新且最热门的表面强化技术。
该技术在部件表面形成的残余压应力深度比常规喷丸强化处理的深5~10倍,具有提高抗疲劳强度、延长疲劳寿命、抑制裂纹的形成与扩展、提高抗微动疲劳/抗磨损/ 抗应力腐蚀断裂特性等特点。
经过多年的开发与研究,美国于1997年将激光冲击强化技术成功应用于航空发动机风扇/ 压气机叶片,大幅度地提高了其抗外物损伤能力和高循环疲劳性能,并且于1998年美国研发杂志评为全美100项最重要的先进技术之一,被美国军方认定为第4代战斗机发动机的80项关键技术之一。
2003年以来,该技术又应用到F119发动机等第4代战斗机发动机高压压气机整体叶盘上,目前正在研究应用于包括激光难以进入区域的航空发动机轮盘等部件上[1-4]。
激光冲击强化技术原理与特点激光冲击强化技术的原理,是采用短脉冲(几十纳秒)的强激光辐射金属部件表面涂覆的约束层(如流动的水等),并通过约束层作用于金属表面涂覆的不透明涂覆层(如黑漆或胶带),涂覆层吸收激光能量发生爆炸性汽化蒸发,蒸发的气体吸收剩余的激光产生快速膨胀的等离子流,限定在部件表面与约束层间的等离子流产生急速增大的高压冲击波,冲击波产生的“冷作用”作用于金属表面并向内传播,形成由塑性变形引发的残余压应力[5-10]。
当冲击波的峰值压力超过被处理材料动态屈服强度时,材料表层不产生应变硬化,残留很大应力,同时微观组织发生很大的变化,显著提高材料的抗疲劳、耐磨损和防应力腐蚀特性。
虽然与常规喷丸强化类似,激光冲击强化技术也是通过在金属部件的表面产生有益的残余压应力提高部件的抗疲劳与耐损伤特性,但是由于引入残余压应力的方法不同,激光冲击强化技术处理的部件明显优于常规喷丸强化处理的部件。
(1)激光冲击强化一般采用钕玻璃、YAG 及红宝石的高功率脉冲式激光器。
航空发动机叶片知多少(一)——风扇叶片简介

航空发动机叶⽚知多少(⼀)——风扇叶⽚简介如果经常坐飞机,那肯定都知道,飞机发动机前⾯有⼀圈很⼤很⼤的叶⽚。
没错,通常通过发动机外观我们只能看到发动机的风扇叶⽚(涡扇发动机)或者涡桨叶⽚(涡桨发动机),也就是我们通常在飞机前⾯能看到的很⾼很⼤的叶⽚。
那飞机发动机上究竟是不是只有我们看到的风扇叶⽚啊?如果你只见树⽊,不见森林,那就错了,风扇叶⽚论数量只占到发动机中叶⽚总数的2%左右,还有很多叶⽚是什么呢?下⾯跟着⼩编⼀起来看看发动机上的叶⽚类型,以及每种叶⽚不同的⼯作原理。
今天我们先来说说——修长的风扇叶⽚!就风扇叶⽚⽽⾔,⽬前世界上⽬前最⼤风扇叶⽚是GE9X的风扇叶⽚它的叶尖直径为3.4m,采⽤GE公司的第4代碳纤维复合材料制成。
3.4m是什么概念,也就是说单个叶⽚安在发动机上,它的半径⼏乎相当于成年⼈的⾝⾼。
GE9X叶⽚钛合⾦风扇叶⽚风扇叶⽚是最容易观察到的叶⽚。
风扇叶⽚的直径⼀般⽐较⼤,从⼀⽶到三⽶多不等。
风扇叶⽚的主要作⽤是把进⼊发动机的空⽓进⾏初步压缩,压缩后的⽓体分两路,⼀路进⼊内涵道进⾏继续压缩,⼀路流进外涵道直接⾼速排出,产⽣巨⼤的推⼒。
可能觉得不可思议,其实涡扇发动机80%以上的推⼒都是由直接排出外涵道的⽓体提供的。
风扇叶⽚⼀般是由钛合⾦以及复合材料制成。
其中,GE的风扇叶⽚⼀般都是碳纤维复合材料。
复合材料的⽐强度很⾼,所以发动机转速,⽐较⾼的复合材料是不存在强度问题。
GE90发动机复合材料风扇叶⽚:直径达3.124m.叶⾝与叶根⽤IM7中长碳纤维与韧性好的8511-7环氧树脂组成的被称为”⼤⼒神”的8511-7/IM7复合材料制成⼀整体。
在叶⾝的压⼒⾯上喷涂聚胺酯防腐涂层,在叶背上涂有聚胺酯漆。
为提⾼叶⽚抗⼤鸟撞击的能⼒,叶⽚前缘从上⾄下包有钛合⾦薄⽚,在叶盆尾缘位于叶尖1/3的⾯积上也包有钛合⾦薄⽚。
钛合⾦薄⽚是⽤3MAF191胶粘到复合材料的叶⾝上的。
为防⽌叶⽚在叶尖与尾缘处材料脱层,⽤Kevlar材料制成的线在叶尖与尾缘处进⾏了缝合。
航空发动机风扇叶片预制体研发现状及趋势

航空发动机风扇叶片预制体研发现状及趋势1 研究背景在航空领域高速发展的今天,我国航空发动机研发技术的落后,限制了航空领域的发展,而国外对我国实行技术封锁,也成为了我国发展的制约力。
发展提高发动机制造技术已成为我国迫切需要解决的问题,而发动机风扇叶片的性能对发动机性能提升起到了关键的作用。
因此,对发动机风扇叶片的研究就显得尤为重要。
目前,发动机已经发展到了第四代,应用复合材料及先进的工艺技术,增强体主要为3D编织物或3D机织物。
风扇叶片预制体主要有3种制备工艺,分别是预浸料铺层工艺、3D编织工艺以及3D机织工艺。
预浸料铺层形成的风扇叶片厚度方向没有纤维连接会使叶片在受到外力冲击时,容易造成分层而导致叶片整体失效。
这种技术制备的材料,层间黏结性较3D编织物、3D机织物差,但其自动化程度高、技术相对简单,且对于形状各异的构件来说,后期加工方便。
随着技术进步,此项技术实现了自动化,被称为自动铺丝工艺,并成功应用于预制体的制备当中,Rolls-Royce公司的TRENT系列发动机风扇叶片就是应用此项技术实现了预制体的自动化生产。
风扇叶片是一种结构较复杂的构件,3D编织可实现其结构的近净成型,后期加工简单。
在编织风扇叶片预制件时,可通过工艺结构设计和适当的增减纱技术来实现叶片厚度的变化,通过一次成型实现风扇叶片预制件的完整编织。
目前,国内的3D编织技术还停留在半自动化水平,与国外相比差距较大,由此造成了编织结构件的成本较高,发展速度缓慢。
在采用3D机织工艺进行风扇叶片预制体织造时,其核心技术是如何实现风扇叶片厚度的连续变化和一次成型。
通过设计,可形成两种工艺,第一种是通过减少经纱层的方式来实现厚度变化[1],这种方式存在织物中经纱断头的现象,织物完整性差;第二种是通过结构设计的方式实现,这种方式织成的构件完整性较好,且一次成型,对工艺结构设计要求较高。
2 国内外风扇叶片预制体制备技术研究现状2.1 国外制备技术发展现状预制体结构和制备技术成熟度影响着复合材料最终的性能,作为复合材料风扇叶片制造的关键技术之一,国外许多国家已经采用了多种复合材料风扇叶片预制体制备技术并实现了较高程度的自动化。
航空发动机空心风扇叶片的超塑成形和扩散连接制造技术

1
发动机的风扇叶片多采用钛合金材料,而钛合金在常温下屈服强度极高,塑性很差, 而且容易产生回弹,常规的金属工艺成形出的发动机叶片大多尺寸精度难以保证,而且 费时费力,不能很好地保证其性能。超塑成形/扩散焊接技术(Superplastic Forming and Diffusion Bonding,简称 SPF/DB)是利用材料在超塑性状态下良好的固态粘合性能而 发展起来的一种组合加工技术,采用 SPF/DB 工艺制造钛合金的多层板结构具有极大优 越性,该工艺可利用钛合金优良的超塑性和扩散连接性,用于制造钛合金多层结构件, 成本和重量约节省 30%~50%,它能节省工时,节约原料,提高效率,加工出重量轻而 结构刚度好的各种结构件。目前该工艺已成功地应用于成形航空航天钛合金的夹层结构 件,较为典型的如航空发动机的空心风扇叶片[1]。
2.1 超塑成形/扩散连接的概念 ........................................................................................ 2 2.1.1 超塑形(SPF) .................................................................................................... 2 2.1.2 扩散连接(DB) ................................................................................................. 3 2.1.3 超塑成形/扩散连接(SPF/DB) ........................................................................ 3
航空发动机空心风扇叶片扩散连接焊缝建模与优化分析技术

航空发动机空心风扇叶片扩散连接焊缝建模与优化分析技术The Modeling and Optimization for Diffusion Bonding Seam of Hollow Fan Blade in AeroEngine柴象海1,2,侯亮1,2(1.中航商用航空发动机有限责任公司设计研发中心,上海市200241;2.上海商用飞机发动机工程技术研究中心,上海市200241)摘要: 扩散连接钛合金空心瓦伦结构已经被成功地应用于航空发动机零部件,如风扇叶片、导流叶片等结构。
研究发现,瓦伦结构的几何特征对零件的抗冲击强度,例如抗鸟撞性能,有很大的影响,通过优化设计空心瓦伦结构来提升零件的抗冲击性能一直是工业界追求的目标。
本文针对典型的用于发动机空心风扇叶片的三层板空心瓦伦结构,采用HyperWorks工具包,通过基于试验的仿真优化研究了几个重要的瓦伦结构特征参数对抗冲击性能的影响。
首先通过有限元数值模拟和逆向分析的手段估算出钛合金空心瓦伦焊缝的失效强度。
然后通过数值模拟的结果得到了相邻瓦伦夹角、焊缝长度与扩散连接焊焊缝在冲击载荷下失效强度之间的关系。
本项研究可以为钛合金空心瓦伦结构零部件设计和抗冲击强度校核提供参考。
关键词:扩散连接;碰撞试验;HyperWorks建模优化;鸟撞;瓦伦结构Abstract: Diffusion-bonded titanium hollow components with a Warren girder internal structure, such as fan blade, OGV, etc., has been successfully used on aircraft engines. It was found that the geometric features of such Warren girder structure have significant effect on the impact strength of the component. Such design has provided the possibility for the designer to improve bird-strike resistance of the component by optimizing its internal Warren girder structure based HyperWorks. At first, a set of ballistic impact tests with titanium hollow panels with various internal geometric parameters were conducted, and the failure stresses of the diffusion-bonding area of the hollow structure were estimated through an inverse method based on test-analysis correlation. Then, a qualitative relation between the failure stress of the diffusion bonds and two important geometric parameters, skew angle of the girder and length of the diffusion bond, was established through numerical simulations. This study provided useful reference for the optimal design of components with Warren girder hollow structures.Key words:diffusion bonding; impact test; HyperWorks simulation optimizasition; bird-strike; warren structure1 概述伴随着涡轮喷气式发动机的研究与发展,扩散连接钛合金空心瓦伦结构零部件在国内外各大航空发动机中得到了越来越广泛的应用。
IAE国际航空V2500发动机图文介绍(最新整理)

IAE国际航空发动机图文介绍-V2500系列发动机V2500发动机的起源则来自其股东公司的发动机,比如罗罗公司的RB211发动机和普惠公司的PW4000发动机。
V2500最引人注目的特点之一就是它的风扇叶片,而这也是一个很好的例子来说明其股东公司所贡献的已被验证的先进技术。
V2500采用的是由罗罗公司设计和发展的无凸台宽弦空心叶片。
它的制造是在两块钛合金薄板之间放入同样是用钛合金作成的蜂窝状结构的材料,然后通过活性扩散焊接的方法将其连成一体。
这种叶片以极轻的重量获得了极大的强度,可以抗击外来物的击伤。
另外,由于其宽弦叶片本身的性质,跑道上的细小碎片和尘土可以被甩到旁路管道,因此同普通窄弦叶片相比,它可以使由于外来物击伤而导致的发动机拆卸减少4倍。
当V2500开始进入服役时,这种独特的叶片已经在罗罗RB211系列发动机上积累了5年的经验。
到今天为至,这种空心结构的宽弦叶片已在全球累积了1亿小时的服务经验。
普惠公司的“浮壁”燃烧室是另外一项贡献给V2500的技术。
燃烧室壁是由金属层板外壳组成的,里面挂有合金扇形块。
这些扇形块 “浮”在它们和外壳之间的冷空气上。
这样的设计提高了冷却效率,消除了压力,并且这些铸件都可以单独更换,因而减少了维修费。
高效的燃油率也是V2500的一大特点:例如,在一架典型的A321飞机的运营中,V2500可比竞争者减少3%的燃油,相当于每年每架飞机可节省4100桶的燃油。
这种全面费用的降低得益于以下几个方面:升级的宽弦叶片使空气流量达到最大,阻力达到最小;10级高压压气机、2级高压涡轮和5级低压涡轮的应用都提高了效率。
A5 发动机统计数据: 在役的飞机数量: 发动机小时数: 发动机循环数: 最高发动机小时: 最高发动机循环: 超过 1129 架 超过 36,000,000 超过 19,000,000 46,263 25,017对于空客A319,A320和A321来说,没有比V2500系列发动机更好的动力装置选择。
航空发动机叶片关键技术发展现状分析
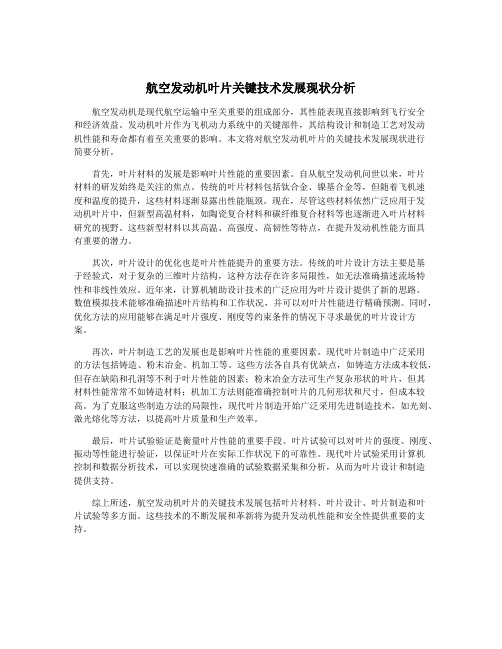
航空发动机叶片关键技术发展现状分析航空发动机是现代航空运输中至关重要的组成部分,其性能表现直接影响到飞行安全和经济效益。
发动机叶片作为飞机动力系统中的关键部件,其结构设计和制造工艺对发动机性能和寿命都有着至关重要的影响。
本文将对航空发动机叶片的关键技术发展现状进行简要分析。
首先,叶片材料的发展是影响叶片性能的重要因素。
自从航空发动机问世以来,叶片材料的研发始终是关注的焦点。
传统的叶片材料包括钛合金、镍基合金等,但随着飞机速度和温度的提升,这些材料逐渐显露出性能瓶颈。
现在,尽管这些材料依然广泛应用于发动机叶片中,但新型高温材料,如陶瓷复合材料和碳纤维复合材料等也逐渐进入叶片材料研究的视野。
这些新型材料以其高温、高强度、高韧性等特点,在提升发动机性能方面具有重要的潜力。
其次,叶片设计的优化也是叶片性能提升的重要方法。
传统的叶片设计方法主要是基于经验式,对于复杂的三维叶片结构,这种方法存在许多局限性,如无法准确描述流场特性和非线性效应。
近年来,计算机辅助设计技术的广泛应用为叶片设计提供了新的思路。
数值模拟技术能够准确描述叶片结构和工作状况,并可以对叶片性能进行精确预测。
同时,优化方法的应用能够在满足叶片强度、刚度等约束条件的情况下寻求最优的叶片设计方案。
再次,叶片制造工艺的发展也是影响叶片性能的重要因素。
现代叶片制造中广泛采用的方法包括铸造、粉末冶金、机加工等。
这些方法各自具有优缺点,如铸造方法成本较低,但存在缺陷和孔洞等不利于叶片性能的因素;粉末冶金方法可生产复杂形状的叶片,但其材料性能常常不如铸造材料;机加工方法则能准确控制叶片的几何形状和尺寸,但成本较高。
为了克服这些制造方法的局限性,现代叶片制造开始广泛采用先进制造技术,如光刻、激光熔化等方法,以提高叶片质量和生产效率。
最后,叶片试验验证是衡量叶片性能的重要手段。
叶片试验可以对叶片的强度、刚度、振动等性能进行验证,以保证叶片在实际工作状况下的可靠性。