自动化车床管理问题模型
自动化车床管理

40组 xzd zzx cjc自动化车床管理摘要本文是为解决自动化车床连续加工中出现的故障及更换刀具的问题。
有效的发现并解决故障,可以提高自动化车床生产加工的效率,减少生产成本以及优化企业生产管理。
为解决题目中三个问题,我们建立了三个优化模型。
对于问题一,我们把每个零件损失费的期望F确定为评价指标,建立了一个离散型随机优化模型。
首先,我们对已知数据进行合理性分析,并通过卡方拟合优度检验,认为刀具寿命服从正态分布。
然后,我们利用计算机枚举出所有换刀间隔与检查策略,求得最优解即每个零件损失费期望最小值为2.9696元/件。
此时检查间隔n为251件,刀具更换间隔m为524件。
最后,我们还对结果进行了可行性分析,发现方案符合实际。
对于问题二,考虑到零件的检查工作存在误差,势必使总的损失费用增加,我们在模型一的基础上建立模型二。
首先根据实际,我们分四种情况计算了刀具故障损失费。
然后,我们假定其它故障服从均匀分布,计算了其它故障损失费。
最后,我们以每个零件损失费期望最小为目标函数,建立了一个单目标优化模型,并通过计算机穷举出所有方案,求的最优解为9.5229元/件。
此时,检查间隔n为18件,刀具更换间隔m为540件。
对于问题三,考虑到误检停机损失费远高于一次检查费,我们在模型二的基础上调整了检查方案建立了模型三。
其中新检查分案为:若一次检查零件合格,则再检查一次,若仍然合格,则认为工序无故障,否则认为出故障;若一次检查零件不合格,则认为出故障。
首先,我们对以上新检查方案进行了简要评估,发现其有效降低了误检率。
然后,我们用类似问题二的解决方法,求得最优解为7.8711元/件,最小损失费比模型二减少了17.35%。
此时检查间隔n为58件,刀具更换间隔m为522件。
最后,我们从五方面对模型三进行了灵敏性分析。
我们分别单独把零件损失费、检查费、调节恢复费、换刀费、误检停机损失费降为200元、10元、2000元、1000元、1000元,发现每个零件损失费期望值各降低了16.85%、4.75%、2.06%、4.13%、1.45%.虽然参数变化幅度不相同,但我们还是能明显看出零件损失费和换刀费对总损失费的影响是很大的,调节恢复费对损失费期望影响很小。
数学建模竞赛-自动化车床管理

自动化车床管理一道工序用自动化车床连续加工某种零件,由于刀具损坏等原因该工序会出现故障,其中刀具损坏故障占95%, 其它故障仅占5%。
工序出现故障是完全随机的, 假定在生产任一零件时出现故障的机会均相同。
工作人员通过检查零件来确定工序是否出现故障。
现积累有100次刀具故障记录,故障出现时该刀具完成的零件数如附表。
现计划在刀具加工一定件数后定期更换新刀具。
已知生产工序的费用参数如下:故障时产出的零件损失费用f=200元/件;进行检查的费用t=10元/次;发现故障进行调节使恢复正常的平均费用d=3000元/次(包括刀具费);未发现故障时更换一把新刀具的费用k=1000元/次。
1)假定工序故障时产出的零件均为不合格品,正常时产出的零件均为合格品, 试对该工序设计效益最好的检查间隔(生产多少零件检查一次)和刀具更换策略。
2)如果该工序正常时产出的零件不全是合格品,有2%为不合格品;而工序故障时产出的零件有40%为合格品,60%为不合格品。
工序正常而误认有故障仃机产生的损失费用为1500元/次。
对该工序设计效益最好的检查间隔和刀具更换策略。
3)在2)的情况, 可否改进检查方式获得更高的效益。
附:100次刀具故障记录(完成的零件数)459362624542509584433748815505 612452434982640742565706593680 9266531644877346084281153593844 527552513781474388824538862659 775859755649697515628954771609402960885610292837473677358638 699634555570844166061062484120 447654564339280246687539790581 621724531512577496468499544645 764558378765666763217715310851三、问题的假设条件1关于刀具寿命x:由于故障出现的随机性,刀具寿命x是一个随机变量。
自动化车床管理的数学模型

(D ep a rtm en t of M a them a tics, T a iyuan T eacher Co llege, T a iyuan 030012) Abstract: T h is p ap er ana lyzes the p rob lem A of 99 CM CM in deta il and g ive tw o k ind s of m odel w ith geom etrica l d istribu tion and exponen tra l d istribu tion. M eanw h ile, W e b la in the . app rox i m a te so lu tion s of p a rt p rob lem A w ith si m p le p robab ility m ethod s Keywords: radom va riab le; geom etrica l d istribu tion; exponen tra l d istribu tion
散变量时的近似结果, 与另一途径, 零件个数是连续变量时的近似结果相近 . 2) 本模型在建立、 计算时, 根据题设数据, 将尽可能使检查周期内工序故障概率很小, 更换刀具周期内不发生刀具故障, 但由于生产任一产品时, 都有可能出现故障, 因此计算结 果仅表示长期以来平均意义下的最优值. 3) 由于模型的数学关系式较为复杂, 算出的值不太精确, 特别是对于问题 2) 的情况, 仅得出离散型时 T 的模型, 对其他情况, 思路类似, 本文予以省略 . 4) 对问题 3) 没有进行严格建模运算, 仅给出直观判断 . 5) 根据题目给出的 100 次刀具的样本统计, 用指数分布建模并不是太恰当的 . 本文仅 做试探.
自动化车床管理的优化问题详解
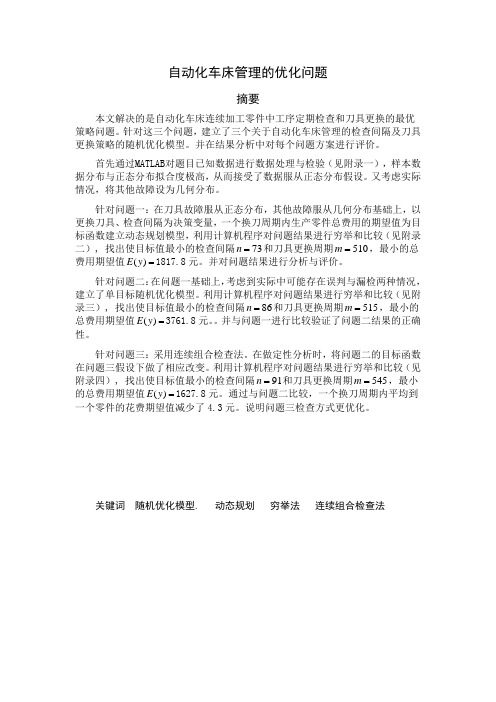
自动化车床管理的优化问题摘要本文解决的是自动化车床连续加工零件中工序定期检查和刀具更换的最优策略问题。
针对这三个问题,建立了三个关于自动化车床管理的检查间隔及刀具更换策略的随机优化模型。
并在结果分析中对每个问题方案进行评价。
首先通过MATLAB 对题目已知数据进行数据处理与检验(见附录一),样本数据分布与正态分布拟合度极高,从而接受了数据服从正态分布假设。
又考虑实际情况,将其他故障设为几何分布。
针对问题一:在刀具故障服从正态分布,其他故障服从几何分布基础上,以更换刀具、检查间隔为决策变量,一个换刀周期内生产零件总费用的期望值为目标函数建立动态规划模型,利用计算机程序对问题结果进行穷举和比较(见附录二), 找出使目标值最小的检查间隔73=n 和刀具更换周期510=m ,最小的总费用期望值=)(y E 1817.8元。
并对问题结果进行分析与评价。
针对问题二:在问题一基础上,考虑到实际中可能存在误判与漏检两种情况,建立了单目标随机优化模型。
利用计算机程序对问题结果进行穷举和比较(见附录三), 找出使目标值最小的检查间隔86=n 和刀具更换周期515=m ,最小的总费用期望值=)(y E 3761.8元。
并与问题一进行比较验证了问题二结果的正确性。
针对问题三:采用连续组合检查法。
在做定性分析时,将问题二的目标函数在问题三假设下做了相应改变。
利用计算机程序对问题结果进行穷举和比较(见附录四), 找出使目标值最小的检查间隔91=n 和刀具更换周期545=m ,最小的总费用期望值=)(y E 1627.8元。
通过与问题二比较,一个换刀周期内平均到一个零件的花费期望值减少了4.3元。
说明问题三检查方式更优化。
关键词 随机优化模型. 动态规划 穷举法 连续组合检查法1.1 问题背景用自动化车床连续加工某种零件,通过检查零件来确定工序是否出现故障。
故障包括刀具损坏故障和其它故障,分别占90%与10%。
工序出现故障是完全随机的,假定在生产任一零件时出现故障的机会均相同。
第一组.自动化车床管理finish

自动化车床管理模型摘要本题是对自动化车床管理问题进行了讨论,将检查间隔和刀具更换策略的确定归结为单个零件期望损失最小的一个优化问题,并提供了有效算法。
对问题一,得到检查间隔18,定期换刀间隔342,相应的单个零件期望损失费用为4.7944元。
对于问题二,在问题一模型的基础上深入考虑工序正常时产出的零件不全是合格品,有2%为不合格品和工序故障时产出的零件有40%为合格品,60%为不合格品对单个零件期望的影响,最后用MATLAB7.1编程得到检查间隔为93,定期换刀时间为279,相应单个零件损失费9.6846元。
对于问题三,可以降低问题二中工序正常而误认有故障的概率。
关键字:期望、优化问题、检查间隔、刀具更换策略问题重述零件加工中刀具损坏故障占95%, 其它故障仅占5%。
工序出现故障完全随机, 假定在生产任一零件时出现故障的机会均相同。
工作人员通过检查零件来确定工序是否出现故障。
现积累有100次刀具故障记录,故障出现时该刀具完成的零件数如附表。
现计划在刀具加工一定件数后定期更换新刀具。
问题1), 对该工序设计出效益最好的检查间隔(生产多少零件检查一次)和刀具更换策略。
问题2)如果该工序正常时产出的零件不全是合格品,有2%为不合格品;而工序故障时产出的零件有40%为合格品,60%为不合格品。
对该工序设计效益最好的检查间隔和刀具更换策略.问题3)在2)的情况, 改进检查方式获得更高的效益。
模型假设1 单个零件加工时间为12 第一问中5%的其他故障不考虑3 开始生产加工时,机器和刀具都是新的4 不考虑检测和换刀时间5 相邻两次刀具更换时间为一个周期6 生产任意零件出现故障的概率相同7 定期换刀时间和检查周期呈线性关系变量说明f故障时产出的零件损失费用t 进行检查的费用d 发现故障进行调节使恢复正常的平均费用k 未发现故障时更换一把新刀具的费用c工序正常而误认有故障停机产生的损失费用T 无故障工作时间x 定期换刀时间a 为x y 线性关系系数,x=ayy 检查周期H 换刀周期(相邻两次换刀时间)G(T)分布函数g(T) 概率密度E(F)周期平均费用E(H) 平均周期S 单个零件的平均损失问题分析问题一,为了方便讨论,把相邻两次刀具更换时间为一个周期,只要工作人员检查时发现不合格品就换刀,否则按照定期换刀时间换刀。
数学建模 自动化车床管理

数学建模自动化车床管理数学建模:自动化车床管理一、引言自动化车床管理是现代制造业中的重要环节,通过合理的管理和优化,可以提高生产效率和产品质量。
为了实现自动化车床管理的科学化、规范化和高效化,需要进行数学建模分析,以便找到最优的管理策略和决策方案。
二、问题描述在自动化车床管理中,存在以下几个关键问题需要解决:1. 生产计划优化问题:如何合理安排车床的生产计划,以最大程度地提高生产效率和资源利用率?2. 设备故障预测问题:如何通过数学建模分析,提前预测车床的故障情况,以便及时进行维修和更换?3. 零部件供应链优化问题:如何通过数学建模分析,优化零部件的供应链管理,以确保及时供应和减少库存成本?三、数学建模方法针对上述问题,可以采用以下数学建模方法进行分析和求解:1. 线性规划模型:通过建立生产计划优化的线性规划模型,考虑生产能力、设备利用率、订单需求等因素,以最大化产量和利润为目标,确定最优的生产计划。
2. 时间序列分析模型:通过对历史数据进行时间序列分析,建立车床故障预测的模型,包括趋势分析、季节性分析、残差分析等,以便提前预测故障情况,采取相应的维修和更换措施。
3. 随机优化模型:通过建立供应链的随机优化模型,考虑供应商的可靠性、交货时间、库存成本等因素,以最小化总成本为目标,确定最优的零部件供应链管理策略。
四、数据收集和处理为了进行数学建模分析,需要收集和处理以下数据:1. 生产数据:包括车床的生产能力、设备利用率、订单需求等数据。
2. 故障数据:包括车床的故障记录、维修时间和维修费用等数据。
3. 供应链数据:包括供应商的可靠性、交货时间、库存成本等数据。
通过对以上数据进行整理和处理,可以得到适用于数学建模的数据集。
五、模型求解和结果分析根据收集和处理的数据,运用上述数学建模方法,可以进行模型求解和结果分析。
具体步骤如下:1. 建立数学模型:根据问题描述,建立相应的数学模型,包括目标函数、约束条件等。
自动化车床管理数学模型

自动化车床管理数学模型
(原创实用版)
目录
一、引言
二、自动化车床管理的数学模型
1.模型建立
2.模型解法
三、结论
正文
一、引言
随着制造业的迅速发展,自动化车床在生产过程中发挥着越来越重要的作用。
如何有效地管理自动化车床,提高生产效率,降低生产成本,成为了许多企业亟待解决的问题。
为此,本文针对 1999 年全国大学生数学建模竞赛 A 题——自动化车床管理问题,建立了一个完整的数学模型,
并给出了该数学模型的解。
二、自动化车床管理的数学模型
1.模型建立
在分析自动化车床管理问题的基础上,我们首先建立了一个数学模型。
该模型主要包含以下要素:
(1)车床数量:假设有 n 台车床;
(2)加工零件:每个车床可以加工不同类型的零件;
(3)加工时间:每台车床加工不同类型零件所需的时间不同;
(4)优先级:考虑不同类型零件的优先级,优先级高的零件优先加工。
基于以上要素,我们建立了一个线性规划模型,以最小化生产总时间为目标函数,以每台车床加工每种零件的时间为约束条件。
2.模型解法
为了求解该数学模型,我们采用了线性规划方法。
具体步骤如下:(1)根据约束条件,构建不等式约束条件表示的生产可行域;
(2)在可行域内寻找使目标函数最小化的最优解;
(3)求解最优解对应的生产方案,即每台车床加工哪些零件。
通过以上步骤,我们得到了最优的生产方案,从而实现了自动化车床的有效管理。
三、结论
本文针对自动化车床管理问题,建立了一个线性规划数学模型,并求解了该模型。
通过该模型,企业可以有效地管理自动化车床,提高生产效率,降低生产成本。
自动化车床的管理问题数学建模解析

2017年数学建模论文第 5 套论文题目:自动化车床管理专业班级姓名:专业班级姓名:专业班级姓名提交日期:2017.7.19自动化车床管理摘要本文研究了自动化车床的管理问题,将检查间隔和刀具更换策略的确定归结为单个零件期望损失最小的一个优化问题,我们利用原始数据在matlab中进行处理,建立了以期望损失费用为目标函数的数学模型。
首先对于题目中给出的100次刀具故障记录的数据在matlab中画出频率直方图,我们可以看出,数据基本是符合正态分布的,我们借用jbtext函数对这些数据进行处理和正态性校验,可以得出样本符合正态分布的假设,然后我们用求得概率密度函数的期望和标准差,然后得出刀具寿命的正态分布函数。
对于问题(1),我们首先建立以单个零件分摊的费用的损失函数为目标函数,然后我们用概率论及数理统计来建立出非线性优化模型,每个零件分摊的费用记为L,L包括预防保全费用L1,检查费用L2,和故障造成的不合格品损失和修复费用L3.在matlab中进行求解得出最优检查间隔为23个,最优刀具更新间隔为352个,合格零件的平均损失期望为7.61元对于问题(2),根据题目信息,不管工序是否正常都有可能出现正品和次品,我们在问题一上,加入检查间隔中的不合格品带来的损失,同时还有误检带来的损失,然后建立出每个零件的期望损失费用作为目标函数的优化模型,在matlab 中用穷举法进行求解得出最优检查间隔为30个,最优刀具更新间隔为308个,合格零件的平均损失期望为10.07元。
对于问题(3),我们将第二题的模型,改变为如果检查为合格品时多检查一次,如果第二次仍然为合格品,我们则判定为工序正常,否则认为故障,改变第二问中的L2和L3,优化模型进行求解得出最优检查间隔为20个,最优刀具更新间隔为375个,合格零件的平均损失期望为9.50元。
对于第三问我们一直是固定检查间隔,我们也可以利用刀具发生故障的函数模型,对检查的间隔也进行调整,检查间隔随函数变换,这一问还没有具体讨论。
- 1、下载文档前请自行甄别文档内容的完整性,平台不提供额外的编辑、内容补充、找答案等附加服务。
- 2、"仅部分预览"的文档,不可在线预览部分如存在完整性等问题,可反馈申请退款(可完整预览的文档不适用该条件!)。
- 3、如文档侵犯您的权益,请联系客服反馈,我们会尽快为您处理(人工客服工作时间:9:00-18:30)。
自动化车床管理问题模型摘要本文主要研究的是自动化车床生产工序中刀具的检验和更换问题。
本文将生产该零件的效益作为衡量检查间隔和刀具更换策略好坏的标准,因此能否设计出最优的检查间隔和道具更换策略是解决这个问题的关键。
为此我们分别建立了三个模型来解决这个问题。
针对问题一:该问题属于优化问题中的数理统计问题。
通过对所给数据进行统计分析得知,在刀具发生故障时零件的完成个数符合正态分布。
因此我们建立了连续性随机模型,通过MATLAB编程求解出最终的结果为换刀周期(个)检查周期(个)平均费用(元)525 263 2.3550 针对问题二:该问题间建立的也是随机优化模型。
和问题一不同的是工序正常时,会产生不合格产品,工序不正常时会产生合格产品。
因此工序正常时增加了因误检停机的费用,工序故障时增加了因误检而产生的次品损失费用。
通过MATLAB编程求解出最终的结果为工序检查间隔为换刀周期(个)检查周期(个)平均费用(元)524 75 3.1831 针对问题三:该问题是在问题二的模型基础上将检查方式近一步优化。
我们在问题三中运用了连续检查法,每次连续检查两个产品,这样就会降低误判的概率,其他的条件不变,最终建立了以平均损失期望为目标函数的随机优化模型。
利用MATLAB编程求解出最后的结果为换刀周期(个)检查周期(个)平均费用(元)521 58 3.00091.问题重述1.1问题背景自动化机床行业是国际公认的基本装备制造业,是国民经济的脊柱产业。
而其中数控技术的使用不但给传统制造业带来了革命性的变化使制造业成为工业化的象征,而且随着数控技术的不断发展和使用领域的扩大。
国内机床企业大力实施技术创新,在产品结构调整上取得了较大进展。
为适应市场需求变化,许多机床企业压缩了低档、普通产品生产,加快经济型数控机床升级换代步伐,着力发展中高档数控机床及生产线等。
在工业生产中,自动化车床刀具的检测和磨损是比较常检见的问题,如何测何时更换刀具将直接影响生产成本。
1.2问题的相关信息一道工序用自动化车床连续加工某种零件,由于刀具损坏等原因该工序会出现故障,其中刀具损坏故障占90%,其它故障仅占10%。
工序出现故障是完全随机的,假定在生产任一零件时出现故障的机会均相同。
工作人员通过检查零件来确定工序是否出现故障。
现积累有150次刀具故障记录,故障出现时该刀具完成的零件数见表。
现计划在刀具加工一定件数后定期更换新刀具。
548 571 578 582 599 568 568 578 582 517 603 594 547 596 598 595 608 589 569 579 533 591 584 570 569 560 581 590 575 572 581 579 563 608 591 608 572 560 598 583 567 580 542 604 562 568 609 564 574 572 614 584 560 560 617 621 615 557 578 578 588 571 562 573 604 629 587 577 596 572 619 604 557 569 609 590 590 548 587 596 569 562 578 561 581 588 609 586 571 615 599 587 595 572 599 587 594 561 613 591 544 591 607 595 610 608 564 536 618 590 582 574 551 586 555 565 578 597 590 555 612 583 619 558 566 567 580 562 563 534 565 587 578 579 580 585 572 568 592 574 587 563 579 597 564 585 577 580 575 641 故障时产生的零件损失费用f=300元/件;进行检查的费用t=20元/次;发现故障进行调节使恢复正常的平均费用d=3000元/次(包括刀具费);未发现故障时更换一把新刀具的费用k=1200元/次。
1.3所要解决的问题问题一:假定工序故障时产出的零件均为不合格品,正常时产出的零件均为合格品,试对该工序设计效益最好的检查间隔(生产多少零件检查一次)和刀具更换+策略。
问题二:如果该工序正常时产出的零件不全是合格品,有1%为不合格品;而工序故障时产出的零件有25%为合格品,75%为不合格品。
工序正常而误认有故障停机产生的损失费用为1500元/次。
对该工序设计效益最好的检查间隔和刀具更换策略问题三:在问题二的情况,可否改进检查方式获得更高的效益。
2.问题假设和符号说明2.1问题假设假设一:其他故障的概率同刀具故障的概率相互独立;假设二:假定所有的检查都为等间隔检查;假设三:工序的检查和换刀时间忽略不记;假设四:每次检查都检查本周期内的全部产品。
()E s每个零件损失费用的期望()E w一个周期内损失费用期望总和()E n生产合格零件的期望值()1E w换刀前不出现故障的损失费用期望()2E w换刀前出现故障的损失费用期望1w换刀前不出现故障的损失费用2w换刀前出现故障的损失费用ip第i种情况发生的概率()1p x刀具损坏故障的概率密度函数()1E n换刀前不出现故障生产的合格产品的期望()2E n换刀前不出现故障生产的合格产品的期望in换刀前第i种情况生产的合格产品的件数n每生产n个产品检查一次sn换刀前出现故障是生产的零件数m每生产m个零件换一次刀,即换刀周期f故障时产生的零件损失费用t进行检查的费用d发现故障,进行调节使恢复正常的平均费用k未发现故障时,更新一把刀的费用()f x刀具寿命的概率密度函数22()21()2xf x eμδπδ--=()F x刀具寿命的分布函数22()21()2xxf x e dxμδπδ--=⎰h误检停机费用3.问题分析本文主要研究的是自动化车床生产工序中刀具的检验和更换问题。
题中给出了150次刀具的故障记录以及所需的一些生产工序的费用参数。
通过这些已知条件我们来建立数学模型来求解题目中的三个问题。
问题一的分析:问题一所要解决的是在工序故障时产出的零件均为不合格品,正常时产出的零件均为合格品的条件下,设计出效益最好的检查周期和换刀周期策略的问题。
分析得刀具故障符合正态分布,因此我们建立了一个连续性随机模型。
问题一分换刀前工序正常和换刀前工序故障这两种情况。
分别求出两种情况下的一个周期内的损失费用总和和生产合格零件的期望值,在求和所出每个零件的损失费用。
然后通过MATLAB编程求解出每个零件的损失费用最小的情况下检查周期和换刀周期策略。
问题二的分析:问题二所要解决的是在无论工序正常还是故障时,都会产生合格品和不合格品的条件下,设计出效益最好的检查周期和换刀周期策略的问题。
问题一样,建立随机优化模型。
由题目可知,在工序正常时的不合格品有1%,而工序故障时的合格品有25%,所以在工序正常时会增加因误检停机的损失费用,在工序故障时也会产生误判,从而会增加次品损失费用。
问题二在分析时同样分为换刀前工序正常和换刀前工序故障这两种情况。
分别求出在问题二条件下的一个换刀周期内总的损失费用和总的生产合格零件的期望值,由此来求出目标函数每个零件的平均最小损失费用。
然后就可通过编程求解出检查周期和换刀周期的最优方案。
问题三的分析:问题三所要解决的问题是在问题二所建立的优化模型的基础上近一步在检查方式上进行改进优化。
在这里我们建立了一个新的检查方法,即组合检查法。
先以两个零件为一个组合,如果两个零件均为合格,则认为是没有故障的;如果两个零件均为不合格品,则认为是有故障的;如果两个零件中有一个是合格的一个是不合格的,在这种情况下我们再将下一个零件纳入此组合内,看第三个零件是否合格,如第三个零件合格,这认为是没有故障的,如第三个为不合格则认为是有故障的。
这样就可以算出误检的概率。
在此检查法的基础上来建立以每个零件的平均最小损失费用为目标函数的数学模型。
然后通过MATLAB 编程求解出近一步优化后的检查间隔和道具更换周期。
4.数据分析通过对150次刀具故障的记录, matlab软件处理数据可得:图一由于在自动化车床连续加工零件的过程中,工序故障发生是完全随机的。
而故障出现时该刀具完成的零件数如上表。
我们在MATLAB中,用normplot命令画出样本图,在画出的样本图中,如果样本值都分布在一条直线上,则表明样本来自正态分布,否则是非正态分布。
数据用normplot中画出(源程序见附录一)得到的样本图4-1由图一可以假设刀具分布函数使服从正态分布的,由图二可以看出点绝大多数在一条直线上,进而可以验证刀具故障分布函数服从正态分布2~(,)x Nμδ。
根据记录数据可以求出15015011222581.18,()20.5115015011x x x xi ii iμδ====-=∑∑==,则有2()22()2xf xμδπδ--=发现这150次刀具故障时完成的零件数近似服从2~(581.18,20.51)x N的正态分布。
5.问题一模型的建立和求解在问题一中我们假定工序故障时产出的零件均是不合格品,正常时产出的零件均为合格品,在此基础上来设计出效益最好的检查间隔(生产多少零件检查一次)和刀具更换策略。
为此我们需要设定一个评价指标,在此我们以在一个周期内的每个零件损失费用的期望值()E s 作为评价指标。
5.1模型一的建立目标函数的确定:确立的评价指标()E s 为一个换刀周期内的损失费用期望总和()E w 和生产的合格零件的期望值()E n 之比,而每个零件损失费用的期望是越小,则效益越好,即:()()()min E w E s E n = 损失费用的期望总和()E w 为换刀前不出现故障的损失费用期望和()1E w 和换刀前出现故障的损失费用期望和()2E w 之和:()22()11E w E w w p i i i i i ==∑∑== 同理得到换刀前生产合格零件的期望值()E n 的表达式为:()22()11E n E n n p i i i i i ==∑∑== 第一种情况:换刀前不出现故障,损失费用1w 为检查费m t n ⎡⎤⎢⎥⎣⎦和换刀费k 之和: 1m w t k n ⎡⎤=+⎢⎥⎣⎦其中m n ⎡⎤⎢⎥⎣⎦为一个换刀周期内的检查次数; 由题目所给的数据分析知:故障时生产的零件数近似服从2~(581.18,20.51)x N 的正态分布。
故刀具寿命的概率密度函数可表示为:2()22()2x f x μδπδ--=则第一种情况下的事件发生的概率为:2()2221110.9x m i p μδπδ--∑==-则换刀前不出现故障的损失费用期望为:()111E w w p = 第二种情况:即换刀前出现故障,设出现故障之前已经生产了s n 个零件,则损失费2w 为检查费1n s t n ⎛⎫⎡⎤ ⎪+⎢⎥ ⎪⎢⎥⎣⎦⎝⎭、故障维修费d 和零件损失费1n s f n n s n ⎧⎫⎛⎫⎡⎤⎪⎪ ⎪+-⎢⎥⎨⎬ ⎪⎢⎥⎪⎪⎣⎦⎝⎭⎩⎭三者之和 ,其表达式为:112n n s s w t d f n n s n n ⎧⎫⎛⎫⎛⎫⎡⎤⎡⎤⎪⎪ ⎪ ⎪=++++-⎢⎥⎢⎥⎨⎬ ⎪ ⎪⎢⎥⎢⎥⎪⎪⎣⎦⎣⎦⎝⎭⎝⎭⎩⎭第二种情况下发生的概率2p 也就是第1s n +个零件恰好为坏的概率,即2(1)22()22211220.92n sx e n s p n s μμδδπδπδ+----+=≈⎰则换刀前出现故障的损失费用期望为:2221()1m E w w p n s-=∑= 综上,一个周期内的损失费用的期望总和为:1211221()()()1m E w E w E w w p w p n s-=+=+∑=同理可得生产合格零件的期望值为:()()()()12121m E n E n E n mp n p s n s=+=+∑= 综上所述,问题一的最优模型为:()()()min E w E s E n = 1()11221..()()121m E w w p w p n s s t m E n mp n p s n s -⎧=+∑⎪⎪=⎪⎨⎪=+∑⎪=⎪⎩5.2模型一的求解通过对问题一在工序故障时产出的零件均为不合格品,正常时产出的零件均为合格品的条件下进行分析建模,然后通过MATLAB 进行编程(程序见附录二)换刀周期(个) 检查周期(个) 平均费用(元)525 263 2.35505.3 由题意可知,在工序正常时生产出来的零件均为合格品,而工序故障时生产的产品均为不合格品。