过程审核风险评分表
过程审核检查表范例
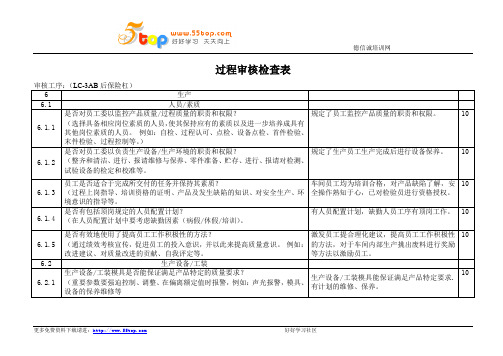
德信诚培训网过程审核检查表6 生产6.1 人员/素质6.1.1 是否对员工委以监控产品质量/过程质量的职责和权限?(选择具备相应岗位素质的人员,使其保持应有的素质以及进一步培养成具有其他岗位素质的人员。
例如:自检、过程认可、点检、设备点检、首件检验、末件检验、过程控制等。
)规定了员工监控产品质量的职责和权限。
106.1.2 是否对员工委以负责生产设备/生产环境的职责和权限?(整齐和清洁、进行、报请维修与保养、零件准备、贮存、进行、报请对检测、试验设备的检定和校准等。
规定了生产员工生产完成后进行设备保养。
106.1.3 员工是否适合于完成所交付的任务并保持其素质?(过程上岗指导、培训资格的证明、产品及发生缺陷的知识、对安全生产、环境意识的指导等。
车间员工均为培训合格,对产品缺陷了解,安全操作熟知于心,已对检验员进行资格授权。
106.1.4 是否有包括顶岗规定的人员配置计划?(在人员配置计划中要考虑缺勤因素(病假/休假/培训)。
有人员配置计划,缺勤人员工序有顶岗工作。
106.1.5 是否有效地使用了提高员工工作积极性的方法?(通过绩效考核宣传,促进员工的投入意识,并以此来提高质量意识。
例如:改进建议、对质量改进的贡献、自我评定等。
激发员工提合理化建议,提高员工工作积极性的方法,对于车间内部生产挑出废料进行奖励等方法以激励员工。
106.2 生产设备/工装6.2.1 生产设备/工装模具是否能保证满足产品特定的质量要求?(重要参数要强迫控制、调整、在偏离额定值时报警,例如:声光报警,模具、设备的保养维修等生产设备/工装模具能保证满足产品特定要求.有计划的维修、保养。
106.2.2 在批量生产使用的检测、试验设备是否能有效地监控质量要求?(测量精度/检具能力调查、数据采集和分析、检具检定的证明等检测、试验设备能有效地监控质量要求. 106.2.3 生产工位、检验工位是否符合要求?(工作环境条件(包括返工/返修工位)必须符合于产品及工作内容,以避免污染、损伤、混批、说明错误。
VDA6.3-2010_过程风险评分表
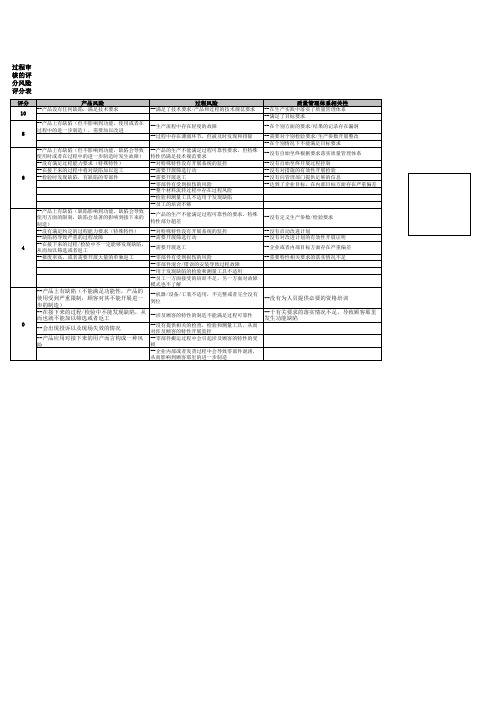
4
--产品上有缺陷(缺陷影响到功能,缺陷会导致 使用方面的限制,缺陷会显著的影响到接下来的 制造) --没有满足约定的过程能力要求(特殊特性) --缺陷将导致严重的过程故障 --在接下来的过程/检验中不一定能够发现缺陷, 从而加以筛选或者返工 --报废率高,或者需要开展大量的单独返工
--没有定义生产参数/检验要求 --没有启动改进计划 --没有对改进计划的有效性开展证明 --企业或者内部目标方面存在严重偏差 --重要特性相关要求的落实情况不足
过程审核的评分风险评分表
评分 10 产品风险
--产品没有任何缺陷,满足技术要求 --产品上有缺陷(但不影响到功能,使用或者在 过程中的进一步制造),需要加以改进
过程风险
--满足了技术要求/产品和过程的技术规范要求 --生产流程中存在轻度的故障 --过程中存在薄弱环节,管理体系 --满足了目标要求 --在个别方面的要求/结果的记录存在漏洞 --需要对个别检验要求/生产参数开展整改 --在个别情况下不能满足目标要求 --没有自始至终根据要求落实质量管理体系 --没有自始至终开展过程控制 --没有对措施的有效性开展检验 --没有向管理部门提供足够的信息 --达到了企业目标,在内部目标方面存在严重偏差
8
6
--产品上有缺陷(但不影响到功能,缺陷会导致 使用时或者在过程中的进一步制造时发生故障) --没有满足过程能力要求(特殊特性) --在接下来的过程中将对缺陷加以返工 --检验时发现缺陷,有缺陷的零部件
--产品的生产不能满足过程可靠性要求,但特殊 特性仍满足技术规范要求 --对特殊特性没有开展系统的监控 --需要开展筛选行动 --需要开展返工 --零部件有受到损伤的风险 --整个材料流转过程中存在过程风险 --检验和测量工具不适用于发现缺陷 --员工的培训不够 --产品的生产不能满足过程可靠性的要求,特殊 特性部分超差 --对特殊特性没有开展系统的监控 --需要开展筛选行动 --需要开展返工 --零部件有受到损伤的风险 --零部件混合/错误的安装导致过程故障 --用于发现缺陷的检验和测量工具不适用 --员工一方面接受的培训不足,另一方面对故障 模式也不了解
VDA6.3过程审核评分矩阵表(标准模板)

当前程度
6.1.2 E P6 #DIV/0!
6.1.3
6.1.4
6.2.4
6.2.5
6.6.1
6.6.2
6.6.3
###### ###### ###### ###### ######
###### ###### ###### ###### ###### ######
###### ###### ######
6.1.2
6.1.3
6.1.4
6.2.4
6.2.5
6.6.1
6.6.2
6.6.3
过程分析中的子要素的分析评估(1-n的平均数) 6.1.1 6.1.2
当前程度
6.1.3
目标程度
6.1.4
最高程度
6.1.5
当前程度
6.2.1
6.2.2
6.2.3
当前程度
6.2.4
目标程度
6.2.5
最高程度
6.2.6
当前程度 当前程度
n.e. 当前程度 目标程度 最高程度 当前程度
#DIV/0!
######
EPzR
######
5.2
5.3
5.4*
5.5*
5.6
5.7
n.e.
当前程度
目标程度
最高程度
当前程度
E P5
#DIV/0!
工序落实程度[%]
运输和零部件处置
E1 #DIV/0! E2 #DIV/0! E3 #DIV/0! E4 #DIV/0! E5 #DIV/0! E6 #DIV/0! E7 #DIV/0! E8 #DIV/0! E9 #DIV/0! E10 #DIV/0!
###### ###### ###### ######
风险评估表格模板

项目风险评估表
项目名称:
编号:填写人Fra bibliotek填写日期审核人
序号
风险名称
汇总评估
风险
得分
风险等级
备注
发生可能性(P)
影响程度(E)
评估分数
1-5分
评估分数
1-5分
1
2
3
4
5
6
注:
1.风险评分填写要求(对已识别风险以及新增/修改风险均需进行评分):
1)发生可能性(P)评估打分:需根据评估标准的发生可能性标准,根据发生可能性的由低至高,对应评估分数1-5分;
2)影响程度(E)评估打分:结合企业及个人项目管理经验,判断此风险若发生对项目整体全过程执行、工期、阶段性里程碑目标、经济损失、企业声誉等方面造成的后果,按照造成后果由低至高,对应对应评估分数1-5分。);
3风险得分=风险影响程度分值E×风险发生可能性分值P(说明:对于综合影响分值不高但影响程度重大的风险,可在评估后调高风险等级)
4)风险等级确认:
极高风险:风险等分为20 / 25分;高风险:风险等分为12 / 15 / 16分;中等风险:风险等分为5 / 8 / 9 / 10分;
低风险:风险等分为3 / 4 / 6分;极低风险:风险等分为1 / 2 分
VDA6.3-2016过程审核检查表及评分矩阵
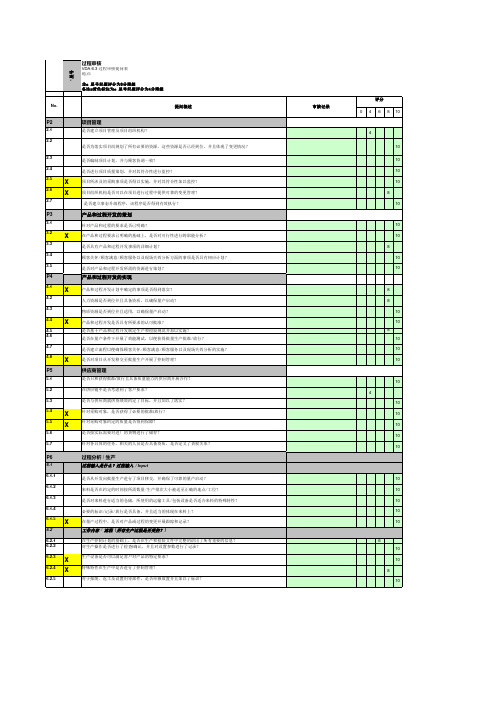
10 10 10
10 10 10 10
10 10 10 0
10 10 10 10
10 10 10 10 10
审核记录
评分 0 4 6 8 10
4 10 10 10 10
8 10
10 10 8 10 10
8 8
10 10 8 10 10 10
10 4
10 10 10 10 10
10 10 10 10 10
6 10 10
8 10
6.3
x 6.3.1
6.3.2
6.3.3
6.4
x 6.4.1
6.4.2
x 6.4.3
产品和过程开发计划中确定的事项是否得到落实? 人力资源是否到位并且具备资质,以确保量产启动? 物质资源是否到位并且适用,以确保量产启动? 产品和过程开发是否具有所要求的认可批准? 是否基于产品和过程开发制定生产和检验规范并加以实施? 是否在量产条件下开展了效能测试,以便获得批量生产批准/放行? 是否建立流程以便确保顾客关怀/顾客满意/顾客服务以及现场失效分析的实施? 是否对项目从开发移交至批量生产开展了控制管理? 供应商管理 是否只和获得批准/放行且具备质量能力的供应商开展合作? 在供应链中是否考虑到了客户要求? 是否与供应商就供货绩效约定了目标,并且加以了落实? 针对采购对象,是否获得了必要的批准/放行? 针对采购对象约定的质量是否得到保障? 是否按实际需要对进厂的货物进行了储存? 针对各具体的任务,相关的人员是否具备资质,是否定义了责权关系?
6.4.4
6.4.5 6.5
6.5.1
6.5.2
x 6.5.3
6.5.4
6.6
6.6.1
6.6.2
6.6.3
VDA6.3过程审核评分准则

--零部件有受到损伤的风险
--零部件混合/错误的安装导致过程故障
--用于发现缺陷的检验和测量工具不适用
--员工一方面接受的培训不足,另一方面对故障
模式也不了解
--产品上有缺陷(不能满足功能性,产品的 使用受到严重限制,顾客对其不能开展进一 步的制造)
--机器/设备/工装不适用,不完整或者完全没有 到位
--没有定义生产参数/检验要求 --没有启动改进计划 --没有对改进计划的有效性开展证明 --企业或者内部目标方面存在严重偏差 --重要特性相关要求的落实情况不足
--没有为人员提供必要的资格培训
--于有关要求的落实情况不足,导致顾客那 里发生功Biblioteka 缺陷过程审核的评分风险评分表
评分 10 8 6
4
0
产品风险 --产品没有任何缺陷,满足技术要求
过程风险 --满足了技术要求/产品和过程的技术规范要求
--产品上有缺陷(但不影响到功能,使用或者在 过程中的进一步制造),需要加以改进
--生产流程中存在轻度的故障
--过程中存在薄弱环节,但被及时发现和排除
--产品上有缺陷(但不影响到功能,缺陷会导致 使用时或者在过程中的进一步制造时发生故障) --没有满足过程能力要求(特殊特性) --在接下来的过程中将对缺陷加以返工 --检验时发现缺陷,有缺陷的零部件
--产品的生产不能满足过程可靠性的要求,特殊 特性部分超差
--没有满足约定的过程能力要求(特殊特性) --对特殊特性没有开展系统的监控
--缺陷将导致严重的过程故障
--需要开展筛选行动
--在接下来的过程/检验中不一定能够发现缺陷, 从而加以筛选或者返工
--需要开展返工
--报废率高,或者需要开展大量的单独返工
过程审核评分表
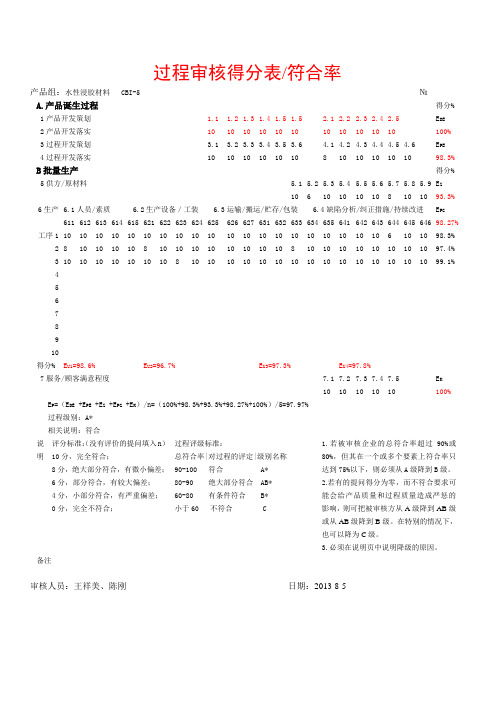
过程审核得分表/符合率产品组:水性浸胶材料 CBI-5 №A.产品诞生过程得分%1产品开发策划2产品开发落实1.1 1.2 1.3 1.4 1.5 1.5 2.1 2.2 2.3 2.4 2.5 E DE 10 10 10 10 10 10 10 10 10 10 10 100%3过程开发策划4过程开发落实3.1 3.2 3.3 3.4 3.5 3.6 4.1 4.2 4.3 4.4 4.5 4.6 E PE10 10 10 10 10 10 8 10 10 10 10 10 98.3%B批量生产得分% 5供方/原材料 5.1 5.2 5.3 5.4 5.5 5.6 5.7 5.8 5.9 E Z10 6 10 10 10 10 8 10 10 93.3% 6生产 6.1人员/素质 6.2生产设备/工装 6.3运输/搬运/贮存/包装 6.4缺陷分析/纠正措施/持续改进E PG98.27%611 612 613 614 615 621 622 623 624 625 626 627 631 632 633 634 635 641 642 643 644 645 646工序1 10 10 10 10 10 10 10 10 10 10 10 10 10 10 10 10 10 10 10 10 6 10 10 98.3%2 8 10 10 10 10 8 10 10 10 10 10 10 10 10 8 10 10 10 10 10 10 10 10 97.4%3 10 10 10 10 10 10 10 8 10 10 10 10 10 10 10 10 10 10 10 10 10 10 10 99.1%45678910得分% E U1=98.6% E U2=96.7% E U3=97.3% E U4=97.8%7服务/顾客满意程度7.1 7.2 7.3 7.4 7.5 E K10 10 10 10 10 100%E P=(E DE +E PE +E Z +E PG +E K)/n=(100%+98.3%+93.3%+98.27%+100%)/5=97.97%过程级别:A*相关说明:符合说明评分标准:(没有评价的提问填入n)10分,完全符合;8分,绝大部分符合,有微小偏差;6分,部分符合,有较大偏差;4分,小部分符合,有严重偏差;0分,完全不符合;过程评级标准:总符合率|对过程的评定|级别名称90-100 符合 A*80-90 绝大部分符合 AB*60-80 有条件符合 B*小于60 不符合 C1.若被审核企业的总符合率超过90%或80%,但其在一个或多个要素上符合率只达到75%以下,则必须从A级降到B级。
最新VDA6.3过程审核检查表及评分标准
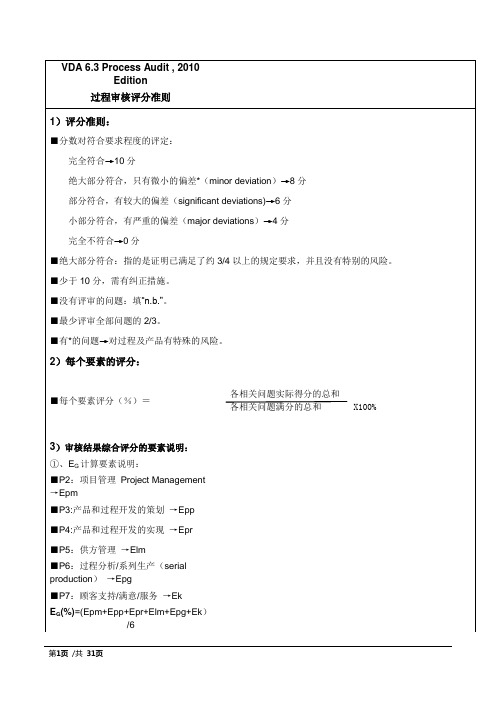
■项目计划=>关键路径则(critical path)
■质量管理计划(QM plan) :项目计划的组成部分。
P2.4
项目组织是否在项目进程中提供了可靠的变更管理?考虑要点,如:
■变更管理需要满足特定的顾客要求。
■变更的可行性检验(manufacturing feasibility check)
EG(%)=(Epm+Epp+Epr+Elm+Epg+Ek)/6
②、过程分析/管理—乌龟图(P6:生产)各要素说明:
■Eu1:输入
■Eu1:工作内容
■Eu3:支持过程
■Eu4:材料、资源
■Eu5:效率
■Eu6:输出/结果
■Eu7:零件运输(Transport/Parts Handling)
4)审核结果的综合评分Overall Assessment:
VDA 6.3 Process Audit , 2010 Ed分数对符合要求程度的评定:
完全符合→10分
绝大部分符合,只有微小的偏差*(minor deviation)→8分
部分符合,有较大的偏差(significant deviations)→6分
小部分符合,有严重的偏差(major deviations)→4分
:记录
■定义的过程[记录所有变更]
■说明变更(highlight)
■和顾客协商沟通、评价
■影响到产品质量的变更=>风险评价
■供方(关键群体)参与
■对变更停止的时间点:明确的定义、遵守
■如果不能遵守,则在顾客和供方之间必须以书面形式加以记录。
■SOP之前的变更时间段:不会影响到产品质量。
- 1、下载文档前请自行甄别文档内容的完整性,平台不提供额外的编辑、内容补充、找答案等附加服务。
- 2、"仅部分预览"的文档,不可在线预览部分如存在完整性等问题,可反馈申请退款(可完整预览的文档不适用该条件!)。
- 3、如文档侵犯您的权益,请联系客服反馈,我们会尽快为您处理(人工客服工作时间:9:00-18:30)。
--零部件有受到损伤的风险
--达到了企业目标,在内部目标方面存在严 重偏差
--整个材料流转过程中存在过程风险
--检验和测量工具不适用于发现缺陷
--员工的培训不够
--产品上有缺陷(缺陷影响到功能,缺陷会 导致使用方面的限制,缺陷会显著的影响到 接下来的制造)
--产品的生产不能满足过程可靠性的要求,特 殊特性部分超差
--在个别方面的要求/结果的记录存在漏洞
--过程中存在薄弱环节,但被及时发现和排除 --需要对个别检验要求/生产参数开展整改
--在个别情况下不能满足目标要求
--产品上有缺陷(但不影响到功能,缺陷会 导致使用时或者在过程中的进一步制造时发 生故障)
--产品的生产不能满足过程可靠性要求,但特 殊特性仍满足技术规范要求
--报废率高,或者需要开展大量的单独返工 --零部件有受到损伤的风险
--重要特性相关要求的落实情况不足
--零部件混合/错误的安装导致过程故障
--用于发现缺陷的检验和测量工具不适用
--员工一方面接受足功能性,产品的 使用受到严重限制,顾客对其不能开展进一 步的制造)
--机器/设备/工装不适用,不完整或者完全没 有到位
--没有为人员提供必要的资格培训
--在接下来的过程/检验中不能发现缺陷,从 而也就不能加以筛选或者返工
--涉及顾客的特性的制造不能满足过程可靠性
--于有关要求的落实情况不足,导致顾客那 里发生功能缺陷
--会出现投诉以及现场失效的情况
--没有提供相关的检查,检验和测量工具,从 而对涉及顾客的特性开展监控
--没有定义生产参数/检验要求
--没有满足约定的过程能力要求(特殊特性) --对特殊特性没有开展系统的监控
--没有启动改进计划
--缺陷将导致严重的过程故障
--需要开展筛选行动
--没有对改进计划的有效性开展证明
--在接下来的过程/检验中不一定能够发现缺 陷,从而加以筛选或者返工
--需要开展返工
--企业或者内部目标方面存在严重偏差
--产品应用对接下来的用户而言构成一种风险
--零部件搬运过程中会引起涉及顾客的特性的 受损
--企业内部或者发货过程中会导致零部件混
淆,从而影响到顾客那里的进一步制造
过程审核的评分风险评分表
评分 10 8 6
4
0
产品风险
过程风险
质量管理体系相关性
--产品没有任何缺陷,满足技术要求
--满足了技术要求/产品和过程的技术规范要求 --在生产实践中落实了质量管理体系
--满足了目标要求
--产品上有缺陷(但不影响到功能,使用或 者在过程中的进一步制造),需要加以改进
--生产流程中存在轻度的故障
--没有自始至终根据要求落实质量管理体系
--没有满足过程能力要求(特殊特性)
--对特殊特性没有开展系统的监控
--没有自始至终开展过程控制
--在接下来的过程中将对缺陷加以返工
--需要开展筛选行动
--没有对措施的有效性开展检验
--检验时发现缺陷,有缺陷的零部件
--需要开展返工
--没有向管理部门提供足够的信息