加工中心刀具知识
加工中心刀具怎么选择合适的?

加工中心刀具怎么选择合适的?加工中心刀具怎么选择合适的?加工中心刀具主要分为铣削刀具和孔加工刀具两大类。
铣削刀具的选择主要是铣刀型别和铣刀尺寸的选择。
铣刀型别应与工件表面形状与尺寸相适应。
加工较大的平面应选择面铣刀;加工凹槽或者是较小的台阶及平面轮廓时应选择立铣刀;加工曲面应选择球头铣刀;加工模具型腔或凸模成形表面等多选用模具铣刀;加工封闭的键槽选择键槽铣刀;加工变斜角面应选用鼓形铣刀;加工各种直的或圆弧形的凹槽、斜角面、特殊孔等应选用成形铣刀。
当粗铣或铣不重要的加工平面时,可使用粗齿铣刀;当精铣时,可选用密齿铣刀,用小进给量达到低的表面粗糙度;当铣材料较硬的金属时,必须选用密齿铣刀,同时进给量要小,以防止振动。
铣刀尺寸也应与被加工工件的表面尺寸和形状相适应。
刀具直径的选用主要取决于装置的规格和工件的加工尺寸,另外还要考虑刀具所需功率应在机床功率范围之内。
粗铣时铣刀直径要小些,精铣时铣刀直径要尽量大些,最好能够包容整个加工宽度。
表面要求高时,还可以选择使用具有修光效果的刀片。
而孔加工刀具可分为钻孔刀具、镗孔刀具、扩孔刀具和铰孔刀具。
(1)钻孔刀具较多,主要有普通麻花钻、可转位浅孔钻以及扁钻。
用加工中心钻孔通常都会采用普通麻花钻,普通麻花钻主要由工作部分和柄部组成的。
刀具柄部分为直柄和锥柄两种。
直柄工具的刀柄主要是弹簧夹头刀柄,其具有自动定心、自动消除偏摆的优点,所以小规格的刀具最好选用该型别。
而工作部分包括切削部分和导向部分,所示,麻花钻的切削部分有2个主切削刃、2个副切削刃、1个横刃。
麻花钻的导向部位起导向、修光排屑和输送切削液作用。
麻花钻一般用于精度较低孔的粗加工,由于加工中心所用夹具没有钻套定心导向,钻头在高速旋转切削时容易会发生偏摆运动,而且钻头的横刃长,所以在钻孔时,要用中心钻打中心孔,用以引正钻头。
(2)镗削的主要特点是获得精确的孔的位置尺寸,得到高精度的圆度、圆柱度和表面粗糙度,所以,对精度较高的孔可用镗刀来保证。
加工中心常用刀具参数

加工中心常用刀具参数加工中心是一种用来进行金属材料的数控加工的机床,常用刀具参数是决定加工质量和效率的重要因素之一、以下是一些常用的加工中心刀具参数。
1.刀柄类型:加工中心常用的刀柄类型有普通刀柄、卡盘刀柄和棒料刀柄。
普通刀柄适用于一般的加工需求,卡盘刀柄适用于需要多次换刀的加工,棒料刀柄适用于棒料材料的加工。
2. 刀具直径:刀具直径是指刀具刃部的直径,常用的刀具直径有2mm、4mm、6mm等。
刀具直径的选择要根据加工件的尺寸、加工深度和加工材料的硬度等因素确定。
3.切削长度:切削长度是指刀具的刃部可以进入工件的深度。
切削长度的选择主要根据加工件的尺寸和形状来确定。
4.刀具材料:常用的刀具材料有硬质合金、高速钢和陶瓷等。
硬质合金的刀具具有较高的硬度和耐磨性,适用于加工硬度较高的材料;高速钢的刀具耐热性较好,适用于高速加工;陶瓷刀具具有良好的耐磨性和耐高温性,适用于高精度加工。
5.刀具涂层:刀具涂层可以提高刀具的耐磨性和切削性能。
常用的刀具涂层有涂层碳化物、涂层氮化物和涂层氧化物等。
不同的刀具涂层适用于不同的加工材料和加工工艺。
6.切削速度:切削速度是指刀具在切削过程中切削的线速度。
切削速度的选择要根据加工材料的硬度、刀具的材料和刀具的刃数等因素确定。
7.进给速度:进给速度是指刀具在切削过程中每分钟进给的长度。
进给速度的选择要根据加工材料的硬度、刀具的材料和加工质量要求等因素确定。
8.加工参数:加工参数是指切削深度、切削宽度和进给量等加工过程中的参数。
加工参数的选择要根据加工材料的硬度、刀具的材料和加工质量要求等因素确定。
常用刀具参数的选择要根据具体的加工要求和材料特性等因素来确定,可以通过试刀和实验等方式来确定最佳的刀具参数。
刀具参数的正确选择可以提高加工效率和加工质量,减少加工成本和损耗。
加工中心刀具进给参数

加工中心刀具进给参数1. 引言加工中心是一种多功能机床,广泛应用于各种工业领域。
刀具进给参数是加工中心加工工艺中一个重要的参数,它直接影响到加工效率和加工质量。
本文将介绍加工中心刀具进给参数的定义、常用参数及其影响因素。
2. 刀具进给参数的定义刀具进给参数是指在加工过程中,刀具在工件上的运动速度和方向。
它由进给速度和进给方式组成。
2.1 进给速度进给速度是指刀具在单位时间内移动的距离。
通常用毫米/分钟(mm/min)或英寸/分钟(in/min)来表示。
进给速度的大小与切削速度、主轴转速和刀具直径等参数有关。
2.2 进给方式进给方式是指刀具在加工过程中的运动路径。
常见的进给方式有直线进给、螺旋进给和往复进给等。
不同的进给方式适用于不同的加工要求,可以实现直线、弧线、螺旋和曲线等不同形状的加工。
3. 常用刀具进给参数3.1 进给速度常用的进给速度参数有以下几种:•快进速度(Rapid feed rate):用于刀具在空载情况下迅速移动到目标位置,一般较高。
•工作进给速度(Cutting feed rate):用于实际切削过程中,根据加工要求选择的刀具运动速度。
3.2 进给方式常用的进给方式有以下几种:•直线进给(Linear feed):刀具在直线上匀速运动,适用于直线加工。
•螺旋进给(Helical feed):刀具在加工过程中同时进行旋转和直线进给,适用于螺纹加工。
•往复进给(Reciprocating feed):刀具在加工过程中来回运动,适用于曲线加工。
4. 影响刀具进给参数的因素刀具进给参数的选择受到多种因素的影响,包括材料性质、加工方式、刀具类型、加工机床性能等。
4.1 材料性质不同材料具有不同的硬度、韧性和切削性能,对刀具进给参数的要求也不同。
比如硬质材料通常需要较低的进给速度和较小的进给量,以避免过大的切削力和切削温度。
4.2 加工方式加工方式主要指切削模式和切削类型。
根据不同的加工方式,刀具进给参数的选择也会有所不同。
加工中心刀具工作原理详解
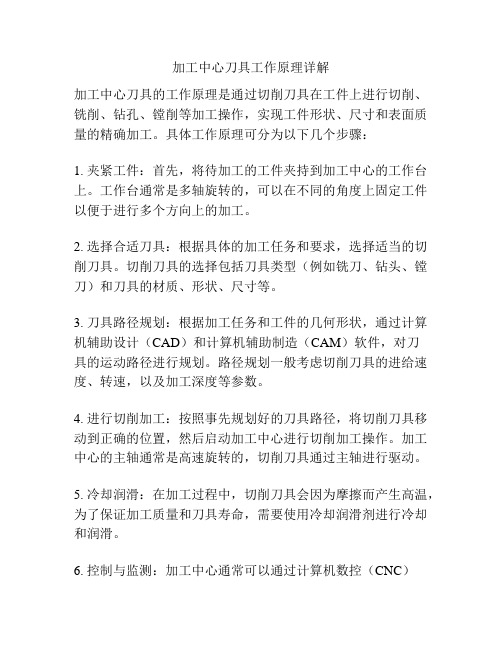
加工中心刀具工作原理详解
加工中心刀具的工作原理是通过切削刀具在工件上进行切削、铣削、钻孔、镗削等加工操作,实现工件形状、尺寸和表面质量的精确加工。
具体工作原理可分为以下几个步骤:
1. 夹紧工件:首先,将待加工的工件夹持到加工中心的工作台上。
工作台通常是多轴旋转的,可以在不同的角度上固定工件以便于进行多个方向上的加工。
2. 选择合适刀具:根据具体的加工任务和要求,选择适当的切削刀具。
切削刀具的选择包括刀具类型(例如铣刀、钻头、镗刀)和刀具的材质、形状、尺寸等。
3. 刀具路径规划:根据加工任务和工件的几何形状,通过计算机辅助设计(CAD)和计算机辅助制造(CAM)软件,对刀
具的运动路径进行规划。
路径规划一般考虑切削刀具的进给速度、转速,以及加工深度等参数。
4. 进行切削加工:按照事先规划好的刀具路径,将切削刀具移动到正确的位置,然后启动加工中心进行切削加工操作。
加工中心的主轴通常是高速旋转的,切削刀具通过主轴进行驱动。
5. 冷却润滑:在加工过程中,切削刀具会因为摩擦而产生高温,为了保证加工质量和刀具寿命,需要使用冷却润滑剂进行冷却和润滑。
6. 控制与监测:加工中心通常可以通过计算机数控(CNC)
系统进行精确控制。
CNC系统可以控制刀具的运动路径、进给速度、切削力等参数,以及对加工过程实时监测和检测,如工件尺寸、表面粗糙度等。
通过以上步骤,加工中心刀具可以对工件进行精确高效的加工操作。
加工过程中,刀具的切削、铣削、钻孔等操作可根据具体的工件需求进行不同的组合,实现各种复杂的形状和结构的加工。
加工中心对刀具的基本要求

加工中心对刀具的基本要求⑴高刚度、高强度为提高生产效率,往往采用高速、大切削用量的加工,因此加工中心采用的刀具应具有能承受高速切削和强力切削所必须的高刚度、高强度。
⑵高耐用度加工中心可以长时间连续自动加工,但若刀具不耐用而使磨损加快,轻则影响工件的表面质量与加工精度,增加换刀引起的调刀与对刀次数,降低效率,也会使工作表面留下因对刀误差而形成的接刀台阶,重则因刀具破损而发生严重的机床乃至人身事故。
除上述两点之外,与普通切削一样,加工中心刀具的切削刃的几何角度参数的选择及排屑性能等也非常重要,积屑瘤等弊端在数控铣削中也是十分忌讳的.⑶刀具精度随着对零件的精度要求越来越高,对加工中心刀具的形状精度和尺寸精度的要求也在不断提高,如刀柄、刀体和刀片必须具有很高的精度才能满足高精度加工的要求。
总之,根据被加工工件材料的热处理状态、切削性能及加工余量,选择刚性好、耐用度高、精度高的加工中心刀具,是充分发挥加工中心的生产效率和获得满意加工质量的前提。
3.2.2 加工中心刀具的材料⑴高速钢(High Speed Steel)自1906 年Taylor 和White 发明高速钢以来,通过许多改进至今仍被大量使用着,大体上可分为W系和MO系两大类。
其主要特征有:合金元素含量多且结晶颗粒比其他工具钢细,淬火温度极高(12000C)而淬透性极好,可使刀具整体的硬度一致。
回火时有明显的二次硬化现象,甚至比淬火硬度更高且耐回火软化性较高,在6000C仍能保持较高的硬度,较之其他工具钢耐磨性好,且比硬质合金韧性高,但压延性较差,热加工困难,耐热冲击较弱。
因此高速钢刀具仍是数控机床刀具的选择对象之一。
目前国内外应用WMO、WMOAI、WMOCO为主,其中WMOAI是我国所特有的品种。
⑵硬质合金(Cemented Carbide)硬质合金是将钨钻类WC,钨钦钻类WC-TiC ,钨钦钽(铌)钻类WC TiC-TaC 等硬质碳化物以CO为结合剂烧结而成的物质,于1926年由德国的Krupp公司发明,其主体为WC-CO 系在铸铁、非铁金属和非金属的切削中大显身手。
数控铣(加工中心)的刀具选用

千里之行,始于足下。
数控铣(加工中心)的刀具选用
在数控铣床(加工中心)中,刀具的选择对加工效率和加工质量有着重要的
影响。
下面将就刀具材料、刀具形状、刀具涂层等几个方面来探讨数控铣床刀
具的选用。
1. 刀具材料:常见的刀具材料有高速钢、硬质合金和刚玉等。
高速钢刀具具有较好的塑性和切削性能,适用于切削材料比较软的工件;硬质合金刀具具
有较高的硬度和耐磨性能,适用于切削材料比较硬的工件;刚玉刀具则在超硬
材料加工中具有较好的切削性能。
2. 刀具形状:常见的刀具形状有平头刀、球头刀、角形刀和弧形刀等。
平头刀适用于平面铣削和侧面铣削,常用于粗加工;球头刀适用于曲面加工和球
面加工,常用于精加工;角形刀适用于开槽和切割等操作;弧形刀适用于轮廓
加工和复杂曲线加工。
3. 刀具涂层:刀具涂层能够提高刀具的硬度、耐磨性和润滑性,从而延长刀具寿命和提高加工质量。
常见的刀具涂层有TiN、TiC、TiCN、AlTiN等。
TiN 涂层主要用于加工不锈钢、铸铁和铝合金等材料;TiC涂层适用于加工高硬度
材料;TiCN涂层具有较好的耐磨性和润滑性能;AlTiN涂层具有良好的耐热性
和耐磨性能,适用于高温和高硬度材料加工。
在选择刀具时,还需考虑工件材料、加工要求和加工稳定性等因素。
另外,刀具的刃数、刀具直径和切削参数等也需要根据具体情况进行选择。
在刀具的
使用过程中,还需注意及时更换磨损的刀具、合理设置刀具余量和刀具进给速
度等,以保证加工效率和加工质量。
第1页/共1页。
加工中心刀具补偿
刀具补偿
1、刀具长度补偿:G43刀具正补偿,G44刀具负补偿,G49刀具长度取消。
G43在Z轴第一次
走刀时用,即下到Z10安全平面的时候使用,如:G43 G00 Z10 H01。
当该把刀程序执行完全结束后用G49G00Z100取消长度补偿。
2、刀具半径补偿:G41刀具左补偿,外轮廓加工:顺时针走刀,顺铣时沿刀具进刀方向看,刀具与工件左侧铣削。
内轮廓加工:逆时针走刀,G41G01X-25F200D01。
G42刀具右补偿(一般不使用)。
3、G40刀具半径补偿取消。
1、加工尺寸不正确时,修改G41半径补偿的方法:
如:要求加工100×100mm的凸台,实测为102×102mm。
参数OFFET/SETTING→刀偏(补正)→形状D→-1→+输入。
如:要求加工100×100mm的凸台,实测为98×98mm。
参数OFFET/SETTING→刀偏(补正)→形状D→1→+输入。
加工中心常用刀具和基本参数
加工中心常用刀具和基本参数
粗铣:将整块工件依电脑三维造型为基础切削成毛胚,粗铣主要注重于加工速度而不讲究加工表面,通常留有0.2-0.5mm的余量,以便后续的半精加工和精加工。
半精加工:将粗铣没有切削到的剩余部分继续加工,使毛胚的余量基本均匀,为精加工做准备,也称二次开粗。
主要分为整体半精加工和局部半精加工两种。
精加工:将毛胚的表面余量去除掉,使加工的表面变得光亮,工件的尺寸符合三维造型的要求。
要想得到较好的加工表面,精加工的切削深度和宽度应该控制在
0.15-0.25mm之间。
光平面:也属于精加工的范畴,是指零件上所有水平面的加工。
清角:利用较小的刀具清除精加工没有铣到的角落。
点孔:利用数控铣床将零件上有孔位要求的中心位置点标记出来。
加工中心刀具使用技巧
加工中心刀具使用技巧包括以下几个方面:
刀具的选择:根据加工需求选择合适的刀具类型和规格,例如刀具材料、切削刃、刀尖半径等。
同时,需要确保刀具的安装和固定牢固,防止加工过程中出现松动或振动。
切削参数的设定:切削参数包括切削速度、进给量、切削深度等,需要根据材料、刀具和加工要求进行合理设定。
合理的切削参数可以提高加工效率,同时减少刀具磨损和加工误差。
刀具的预热:在进行加工前,可以对刀具进行预热,以减少加工过程中的热变形和刀具磨损。
预热可以通过空转或使用预热器进行。
切削液的使用:切削液可以起到冷却、润滑和排屑的作用,有助于提高加工效率和刀具寿命。
需要根据加工需求选择合适的切削液,并确保其供应充足。
刀具的监控与维护:在加工过程中,需要实时监控刀具的磨损和状态,及时更换磨损严重的刀具,并进行维护和保养。
同时,还需要记录刀具的使用情况,以便进行后续分析和优化。
安全操作规程:在操作加工中心时,需要遵守安全操作规程,确保人员和设备的安全。
例如穿戴好防护用具、避免操作失误等。
以上是加工中心刀具使用技巧的几个方面,希望能对您有所帮助。
在使用过程中,还需根据实际情况进行调整和优化,以提高加工效率和精度。
加工中心刀具的选用
加工中心刀具的选用一般意义上的加工中心是指带刀库和换刀装置的数控镗铣床。
刀具的选择是数控加工工艺中的重要内容。
数控加工中的刀具选择是在人机交互状态下完成的,这就要求编程人员必须掌握刀具选择的基本原则,在编程时充分考虑数控加工的特点。
本文从加工中心的特点出发对数控编程中必须面对的刀具选择问题进行探讨,给出若干原则和建议。
一、加工中心的工艺特点1. 加工精度高而稳定,表面质量好。
2. 软件适应性强。
3. 效率高。
二、加工中心主要加工对象加工中心最适宜加工形状复杂、加工内容多、精度要求高、需多种机床及多种刀具且需多次装夹才能完成的零件。
主要的加工对象有以下几种:1. 既有孔系又有平面的零件。
2. 结构形状复杂、普通机床难以加工的零件。
3. 外形不规则的异形件。
4. 精度要求高的小批量零件。
5. 新产品试制件。
三、加工中心刀具及其选择1.对加工中心刀具的基本要求。
由于加工中心主轴转速高出普通机床2~5倍,因此加工中心所用刀具必须具有更高的强度、刚度与耐磨性。
选择刀具时先要选择适当的材料,然后选择合理的刀具几何参数。
对材料的选择,一般选硬质合金;刀具几何参数选择要考虑刀具材料、工件材料、工件形状、加工方式等多方面因素。
2.加工中心常用刀具及其选择。
加工中心刀具种类较多,应用最广的是各种表面及孔加工刀具。
平面、曲面的加工刀具多用各种型式的铣刀,而孔加工刀具根据所加工孔的形状、位置、精度要求等可选择钻头、扩孔钻、铰刀、镗刀等。
加工中心刀具选择总的原则是:安装调整方便、刚性好、耐用度和精度高。
在满足加工要求的前提下,尽量选择较短的刀柄,以提高刀具加工的刚性。
本文仅讨论铣刀选择的原则与方法,并对部分孔加工刀具作一简介。
(1)铣刀的选择。
主要是选择结构类型及几何参数。
铣刀类型的选择:选择时主要考虑零件表面形状与尺寸:如大平面加工选择面铣刀;平面零件周边轮廓的加工,常采用立铣刀;铣削平面时,应选硬质合金刀片铣刀;加工凸台、凹槽时,选高速钢立铣刀;加工模具型腔、空间曲面多选模具铣刀;加工封闭键槽用键槽铣刀;对一些立体型面和有较大转接凹圆弧的过渡加工多选用球形铣刀;加工变斜角面应选鼓形铣刀;加工特殊孔及各种型面应用成型铣刀等。
- 1、下载文档前请自行甄别文档内容的完整性,平台不提供额外的编辑、内容补充、找答案等附加服务。
- 2、"仅部分预览"的文档,不可在线预览部分如存在完整性等问题,可反馈申请退款(可完整预览的文档不适用该条件!)。
- 3、如文档侵犯您的权益,请联系客服反馈,我们会尽快为您处理(人工客服工作时间:9:00-18:30)。
D=2R
加工中心刀具知识
一、切削速度Vc
切削最基本的概念就是賦予切削刀刃以及被切削材相對速度,當刀刃材質
R D
如左圖所示,底部刀刃為一球形狀的銑刀為球刀。球刀在目前的 模具加工使用上相當的頻繁,尤其是在銑削3D的模具時,球刀更 是不可缺少的工具。與前者-端銑刀比起來,因為球刀沒有像端 銑刀底部為尖點的刀刃,而是帶有R角的刀刃,所以球刀的刀刃 更為強壯,不易崩壞;換句話說,球刀的壽命會比端銑刀更為穩 定。除此之外,球刀與工件接觸的區域為R角的刀刃,因此在精 加工時刀間距可用更大的數值,加工面也有極佳的效果。
a、c兩點時其切削速度穩定,所
以此區域為刀刃在切削工件,可 以得到良好之加工面。而在b、d a
兩點時會因切削速度太低甚至沒有
1
切削速度導致刀刃在磨擦工件,加工 面品質當然會大受影響。
b c
3
2
加工中心刀具知识
d
二、刀具損耗
球刀在銑削較平坦的區域時,如下:此時與工件接觸的位置大部分都為 a、b、c這幾個位置。所以其實是用球刀的底部在銑削工件。當整個工 件這類的區域範圍很大時,球刀底部除了切削速度低外,底部的刀刃也 會很快的磨損,兩側的刀刃其實並沒有用到,所以加工面不僅品質低落 而且因為刀具損耗的關係,加工面的精度也會受到影響。
加工中心刀具知识
R=0
D
所以在模具加工中,端銑刀一般會被用來加工模具中的2D區域,如:垂直 面以及水平面或是模具中尖角的區域會用端銑刀將之加工出來。而在傳統 方式的模具加工中,端銑刀也會被用來作粗加工。下面圖示為端銑刀的實 際加工範例。
工銑
輪
件削 袋 形
廓 加
工
銑
銑
削
削
溝
壁垂
槽
直
加工中心刀具知识
球形銑刀
由於銑刀在目前的切削加工中,幾乎可取代大部分之傳統切削刀具,故無 論在銑刀之材料、造型、結構…等等之設計製造上,不但種類極為繁多而 且複雜。現在僅就下列一般模具銑削加工中常用之銑刀種類作說明介紹。
Ⅰ、依幾何形狀區分- a、 b、球刀 c、圓鼻刀
Ⅱ、依刀具結構區分- a、捨棄式刀具 b、整體式刀具
加工中心刀具知识
a
b
c
a
b
c
加工中心刀具知识
球刀在模具加工中最常用來銑削3D的模具,尤其是在精加工以及清角加工 時,但不適合用於銑削較平坦之區域,因與工件接觸面積小,無法加大刀 間距。下面圖示為球刀的實際加工範例。
粗 加 工
精
加
工
加工中心刀具知识
圓
鼻
刀
如左下圖所示,圓鼻刀的外型與端銑刀類似,均為平坦的底部設計,所不 同的是圓鼻刀的底部為帶有R角的刀刃而不是尖點的刀刃,所以刀刃的強 度比端銑刀好,不易崩壞,因此刀具的壽命會比端銑刀要好。
加工中心刀具知识
端
銑
刀
端銑刀之外形如右圖所示,銑刀之外緣及底面均有銑齒以構 成切刃,所以可以用來銑削工件之垂直面以及垂直面。端銑 刀之刀形變化非常複雜,適用於各類加工,如:銑平面、溝 槽或輪廓面…等等,可說是被運用最為廣泛的一種銑刀。一 般來說端銑刀非常適用於2D形狀的工件,但是應用於3D形狀 的模具加工時,就不是那麼的適用。我們就以下原因說明端 銑刀應用於模具加工時所發生的問題:
除此之外,圓鼻刀比球刀、端銑刀有更佳的加工效率,尤其是 在粗加工時。因為圓鼻刀底部是平的,圓鼻刀的水平刀間距可 以用的比球刀更大。在精加工時,它同樣擁有與球刀一樣的優 點,所以刀間距也可以可用更大的數值。因此圓鼻刀不論是用 於粗加工以至於精加工,都是非常合適的選擇。
在銑削3D模具時,圓鼻刀還有另外一項優點是使用球刀所比不
上的。球刀本身會隨著與工件接觸的位置不同,切削速度而有
非常大的變化,所以加工面品質不穩定。圓鼻刀雖然也有這樣
的情形,不過它的切削速度的變化並不像球刀那樣有極大的變
D
R 化。因此使用圓鼻刀加工的工件,品質當然穩定。以下說明圓
銑刀種類
銑削為各種切削方式中變化最大,用途最廣的切削方式。所以無論是槽孔 銑削、凹切、平面以至於各種造型之面皆可加工,而且經由銑削加工可獲 得表面光度極佳與精準之尺寸。銑刀是一種多刃口的圓形刀具,銑削的原 理為應用銑刀之多刃旋轉產生切削作用,所以雖然刀具切入工件甚深,但 每一切刃之切削量並不大,因此每一切刃之切削厚度仍可維持很薄,所得 之加工面亦佳,且刀具壽命能維持甚久。切削效率佳,用途廣泛,所以銑 刀在目前金屬加工中佔有極高之份量。
比被切削材硬而且切削速度達到時,被切削材與刀刃接觸的區域就會被移 除。因此切削速度對於刀具的切削效果非常重要,如果切削速度不夠或太 低,那麼刀刃就不是在切削工件,而是在磨工件。為了產生切削速度,所
以在車削中就是旋轉工件產生切削速度;在銑削中就是旋轉刀具產生切削
速度。左下圖中所顯示的球刀,當在旋轉時,1、2、3點的位置其對應的 切削速度均不相同,甚至2這一點的切削速度幾乎等於0。因此球刀的缺點 就是切削速度不穩定。以右下圖範例來說,你可以看到球刀在銑削3D的工 件時刀刃與工件接觸的位置會不斷的改變,因此切削速度一直在改變。在
Ⅰ、依幾何形狀區分
在模具銑削加工中,由於模具本身即是有複雜造型之工件,在考慮切 削效率、刀具壽命以及工件形狀…等的因素下,因此要只使用單一種 形狀之銑刀便可將模具加工完成是不可能的。所以在模具加工中常會 需要用到不同形狀的銑刀來加工模具,一般模具加工最普遍使用的銑 刀有以下三種:
a、端銑刀〈End Mill〉 b、球刀〈Ball-nose Cutter〉 c、圓鼻刀〈Toroidal Cutter〉
一、如右圖框框所指出的區域,你可以看到此處為一尖點。 所 以甚為脆弱,一但此處尖點崩壞,那麼銑刀壽命也就隨之 完結。所以端銑刀的壽命不甚穩定。
二、在銑削2D形狀的工件時,由於與工件接觸的區域為外緣 與底面,所以不論是刀間距或是切削深度都可以使用極有效 率的數值。反之如果用於銑削3D形狀的模具時,你可以發現 與工件接觸的區域幾乎都是靠近尖點的部位,所以你必須要 減少刀間距或是切削深度,因此加工效率降低。