煤加氢直接液化工艺
神华煤直接液化工艺及PU情况介绍-神华舒歌平

• 停留时间:0.37t/m3h Residence time: 0.37t/m3h • 油收率:37% Oil Yield Rate: 37%
煤直接液化工艺发展概况
Development of DCL Process
油收率 45% 44% 51% 58% 54% 58%
日本 日本
BCL NEDOL
50 150
煤直接液化工艺发展概况
Development of DCL Process
煤直接液化工艺发展经历了三个阶段的 革命性进步。
DCL Process has reached 3 milestones
主要特征表现在循环溶剂制备工艺上, 即固液分离工艺和溶剂加工技术。
煤炭直接液化工艺发展概况
Development of Direct Coal Liquefaction (DCL) Process
煤炭直接液化工艺 DCL Process
煤炭直接液化技术1913年德国人发明,二战期间,德 国的煤直接液化工厂生产能力达到年产423万吨成品油。 DCL technology was invented in 1913 in Germany, during World WarⅡ, the country’s DCL capacity reached 4.23 million ton oil per year 目标是破坏煤的有机结构,并进行加氢,使其成为液 体产物。虽然开发了多种不同种类的煤炭直接液化工 艺,但就基本化学反应而言,它们非常接近。 There are several DCL technologies, but the basic chemical reactions are similar that destroy the to Coal’s organic structure and then hydrogenation
煤直接液化技术现状与发展趋势
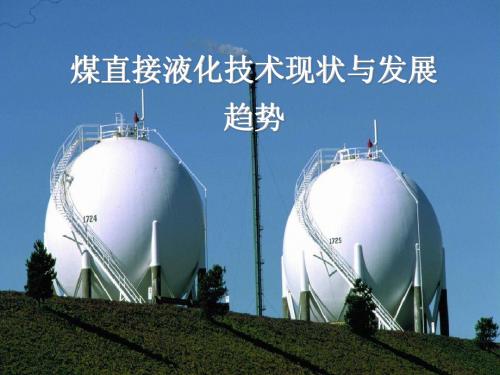
醚键和杂
(2)脱硫反应 煤有机结构中的硫以硫醚、硫醇和噻吩等形式存在,脱硫反应 与上述脱氧反应相似。由于硫的负电性弱,所以脱硫反应更容易进行。 (3)脱氮反应 煤中的氮大多存在于杂环中,少数为氨基,与脱硫和脱氧相比,脱 氮要困难得多。一般脱氮需要激烈的反应条件和有催化剂存在时才能 进行,而且是先被氢化后再进行脱氮,耗氢量很大。
(4)降低循环油中沥青烯含量 (5)缩短反应时间
11
五、煤加氢液化催化剂种类
(1)金属氧化物催化剂 对煤加氢液化催化活性大小顺序: SnO2、ZnO2、GeO2、MoO3、PbO、 Fe2O3、TiO2、 Bi2O3、V2O5. (2)铁系催化剂 主要为三氯化铁、硫酸亚铁、或者加入无水氧化铁,有的加硫 或者不加硫。 (3)卤化物催化剂 使用卤化物催化剂有两种方式: 一种是使用少量催化剂;另一种是使用大量催化剂,熔融金属 卤化物,催化剂与煤的质量比可高达1。
要将煤转化为液体产物,首先要将煤的大分子裂解为较小 的分子,而要提高H/C原子比,降低O/C比,就必须增加H 原子或减少C原子。 煤液化的实质就是在适当温度、氢压、溶剂和催化剂条件 下,比提高H/C ,使固体煤转化为液体的油。
6
直接液化
制 氢 煤制备 油煤浆 制 备 加氢液化
450OC,20MPa
煤 浆 预 热 器 煤浆
2014-4-3
第 一 反 应 器
第 二 反 应 器
高 温 分 离 器
中 温 分 离 器
低 温 分 离 器
常 减 压 蒸 馏
加 氢 反 应 装 置
常 压 蒸 馏
煤直接液化
残渣
循环溶 剂去制 15 15 煤浆
工艺特点:
①采用两段反应,反应温度455℃、压力19M Pa,提高了煤浆空速; ②采用人工合成超细铁基催化剂 ③固液分离采用成熟的减压蒸馏; ④循环溶剂全部加氢,提高溶剂的供氢能力; ⑤液化粗油精制采用离线加氢方案。
煤直接液化和煤间接液化综述
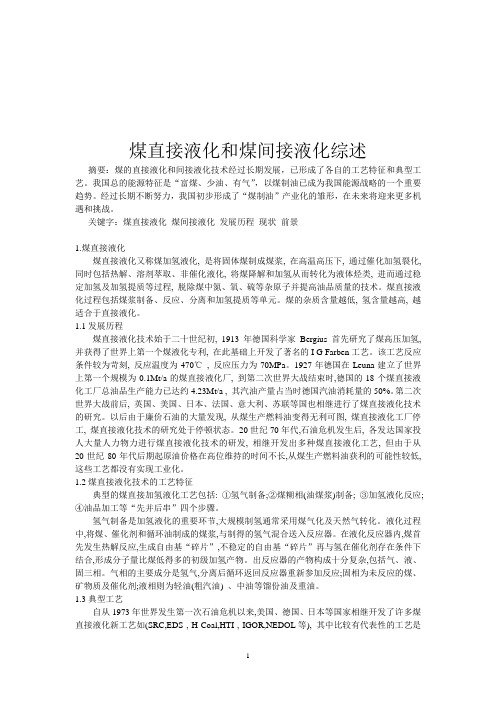
煤直接液化和煤间接液化综述摘要:煤的直接液化和间接液化技术经过长期发展,已形成了各自的工艺特征和典型工艺。
我国总的能源特征是“富煤、少油、有气”,以煤制油已成为我国能源战略的一个重要趋势。
经过长期不断努力,我国初步形成了“煤制油”产业化的雏形,在未来将迎来更多机遇和挑战。
关键字:煤直接液化煤间接液化发展历程现状前景1.煤直接液化煤直接液化又称煤加氢液化, 是将固体煤制成煤浆, 在高温高压下, 通过催化加氢裂化, 同时包括热解、溶剂萃取、非催化液化, 将煤降解和加氢从而转化为液体烃类, 进而通过稳定加氢及加氢提质等过程, 脱除煤中氮、氧、硫等杂原子并提高油品质量的技术。
煤直接液化过程包括煤浆制备、反应、分离和加氢提质等单元。
煤的杂质含量越低, 氢含量越高, 越适合于直接液化。
1.1发展历程煤直接液化技术始于二十世纪初, 1913年德国科学家Bergius首先研究了煤高压加氢, 并获得了世界上第一个煤液化专利, 在此基础上开发了著名的I G Farben工艺。
该工艺反应条件较为苛刻, 反应温度为470℃, 反应压力为70MPa。
1927年德国在Leuna建立了世界上第一个规模为0.1Mt/a的煤直接液化厂, 到第二次世界大战结束时,德国的18个煤直接液化工厂总油品生产能力已达约4.23Mt/a , 其汽油产量占当时德国汽油消耗量的50%。
第二次世界大战前后, 英国、美国、日本、法国、意大利、苏联等国也相继进行了煤直接液化技术的研究。
以后由于廉价石油的大量发现, 从煤生产燃料油变得无利可图, 煤直接液化工厂停工, 煤直接液化技术的研究处于停顿状态。
20世纪70年代,石油危机发生后, 各发达国家投人大量人力物力进行煤直接液化技术的研发, 相继开发出多种煤直接液化工艺, 但由于从20世纪80年代后期起原油价格在高位维持的时间不长,从煤生产燃料油获利的可能性较低, 这些工艺都没有实现工业化。
1.2煤直接液化技术的工艺特征典型的煤直接加氢液化工艺包括: ①氢气制备;②煤糊相(油煤浆)制备; ③加氢液化反应;④油品加工等“先并后串”四个步骤。
煤的直接加氢液化技术

自由基碎片加氢(一)
可用如下方程式表示加氢反应
R-CH2-CH2-R’→ RCH2·+R’CH2· RCH2·+R’CH2·+2H·→ RCH3+R’CH3
煤加氢液化过程包括一系列的顺序反应和平行反 应,但以顺序反应为主,每一级反应的分子量 逐级降低,结构从复杂到简单,杂原子含量逐 级减少,H/C原子比逐级上升。
直接液化工艺流程简图
催
化
剂
H2
煤煤
反
浆
应
分
提
离
质
循环溶剂
残渣
汽油 柴油
其它
工艺过程
该工艺是把煤先磨成粉,再和自身组的部分液 化油(循环制剂)配成煤浆,在高温(450oC) 和高压(20—30MPa)下直接加氢,获得液化油, 然后再经过提质加工,得到汽油柴油等产品.1t 无水无灰煤可产500—600Kg油,加上制氢用 煤,约3—4t原料煤产1t油。
催化剂作用
催化剂的作用是吸附气体中的氢分子,并将其 活化成活性氢以便被煤的自由基碎片接受。一 般选用铁系催化剂或镍、钼和钴类催化剂。硫 是煤直接液化的助催化剂,有些煤本身含有较 高的硫,可少加或不加助催化剂。
催化剂的影响
催化剂是煤直接液化过程的核心技术 优良的催化剂可以降低煤液化温度,减少副
煤的直接加氢液化技术
煤直接液化反应机理
把固体煤转化为液体油,就必须采用增加温 度或其他化学方法以打碎煤的分子结构,使大 分子物质变成小分子物质,同时外界要供给足 够量的氢,提高其H/C原子比。
煤直接液化反应比较复杂,大致可分为热解、 氢转移、加氢三个反应步骤
氢源
煤在热解过程中外界不提供氢 煤在热解过程中外界不提供氢,煤热解
俄罗斯低压液化工艺

俄罗斯低压液化工艺前苏联在20世纪70~80年代对煤炭直接液化技术进行了十分广泛的研究,主要研究工作针对世界上最大的、露天开采的坎斯克-阿钦斯克、库兹涅茨(西伯利亚)煤田的煤质特点,开发了低压(6~10MPa )煤直接液化工艺。
该工艺采用乳化钼催化剂,反应温度425~435℃,液相加氢阶段反应时间为30~60min 。
1983年在图拉州建成了处理煤炭5~10t/d 的“CT-5”中试装置,实验工作进行了7年。
在此基础上前苏联先后完成了处理煤炭75t/d 的“CT-75”和500t/d 的“CT-500”的大型中试厂的详细工程设计。
其中“CT-75”已开始建设,后因苏联解体未完成。
俄罗斯低压液化工艺采用高活性的乳化钼催化剂,并掌握了Mo 的回收技术,可使95%~97%的Mo 得以回收再利用。
该工艺对煤种的要求较高,最适合灰分低于10%,惰性组分低于5%,反射率在0.4%~0.75%之间的年轻高活性未氧化煤,而且对煤中灰的化学成分也有较高的要求,要求(O K O Na 22+)<3%、(3232SO TiO MgO CaO O Fe ++++)/(O K O Na 22+)>2。
对于惰性组分>15%,煤灰中(O K O Na 22+)>6%、3232SO TiO MgO CaOO Fe ++++)/(O K O Na 22+)<1的煤,则不适合该工艺。
俄罗斯低压液化工艺之所以能在较低压力(6~10MPa )和较低的温度(425~435℃)下实现煤的有效液化,主要取决于煤的品质和催化剂。
下图为俄罗斯低压煤直接加氢液化工艺流程图。
俄罗斯低压液化工艺“CT-5”流程:原料煤粉碎至小于3mm 后,进入涡流仓。
在涡流仓内,煤被惰性气体快速加热(加热速度在1000℃/min以上),发生爆炸式的水分分离、气孔爆裂,经过多级涡流仓热裂解脱除水分后,进入细磨机,最后得到尺寸小于0.1~0.2mm,水分小于1.5%~2.0%的粉煤。
煤炭液化

液化过程的氢耗量与煤自由氢含量关系
• 加氢液化过程中的耗量与原料 煤中的自由氢含量成反比关系。 • 泥炭的自由氢最低(3.2g/100g 碳),褐煤(4.1~4.3),烟煤 (4.0~4.4)
• 氢气占煤液化成本的比例很高,一 般为30%或更高。
溶剂的作用
• 煤炭的加氢液化中一般要使 用溶剂,因为溶剂在煤炭液 化过程中有下列左右:①热 溶解煤;②溶解氢气;③供 氢作用;④溶剂直接与煤质 反应。
催化剂在煤炭加氢液化中的作用
• ①催化剂活化反应物,加速加氢反应速度, 提高煤炭液化的转化率和油收率 • ②促进溶剂的再加氢化和氢源与煤之间的 氢传递 • ③选择性作用 • 适合于作煤加氢液化催化剂的物质很多, 铁系催化剂,Co、Mo、Ni等金属氧化物催 化剂及金属卤化物催化剂。
催化剂的活性
• 各种催化剂的活性是不相同的。造成 催化剂活性不同的决定性因素是催化 剂的化学性质和结构。催化剂在使用 过程中显示出活性的大小与下列因素 有关:①催化剂用量;②催化剂加入 方式;③煤中矿物质;④溶剂的影响; ⑤ 炭 沉 积 和 蒸 汽 烧 结 。
• 影响煤加氢难易程度的 因素是煤本身的稠环芳 烃结构,稠环芳烃结构 越密和相对分子质量越 大,加氢越难。
脱氧、硫、氮杂原子反应
• 加氢液化过程,煤结 构中的一些氧、硫、 氮也产生断链分别生 成气体而脱除。
缩合反应
• 缩合反应会生成半焦和焦炭, 使液化产率降低。为了提高 液化效率,必须严格控制反 应条件和采取有效措施,抑 制缩合反应,加速裂解、加 氢 等 反 应 。
第三阶段
• 1982年至今,煤液化新工艺的研究 期。1982年后期石油市场供大于求, 石油价格不断下跌,各大煤液化试 验工厂纷纷停止试验.但是各发达国 家的实验室研究工作及理论研究工 作仍在大量的进行。如近年来开发 出来的煤油共处理新工艺和超临界 抽提煤工艺等。
煤温和加氢液化制高品质液体燃料关键技术与工艺

煤温和加氢液化制高品质液体燃料关键技术与工艺引言在当前全球能源供应紧张的背景下,开发和利用高品质液体燃料成为了国际能源领域的研究热点之一。
煤温和加氢液化技术作为一种重要的液体燃料制备方法,具有资源成本低、适用范围广的优势,对我国能源战略和经济发展具有重要意义。
本文将从煤温和加氢液化的原理、关键技术及工艺流程等方面进行综合分析和探讨。
原理煤温和加氢液化是一种将固体煤转化为液体燃料的技术。
其原理是通过高温和高压的条件下,将煤在氢气的催化作用下进行化学反应,使煤中的高分子化合物裂解,并生成液体燃料。
这一过程主要包括三个步骤:煤的热解、煤的气化和煤的加氢。
煤的热解煤的热解是指将煤暴露在高温环境中,使煤中的有机质在没有氧气的条件下发生热解反应,生成气体和液体产物。
热解过程中,煤中的高分子化合物会发生裂解,生成低分子量的化合物,如烃类等。
煤的气化煤的气化是指将煤中的热解产物(如烃类)在高温和高压的条件下与氢气反应,生成更高价态的化合物。
在气化过程中,煤中的烃类会与氢气发生反应,生成一系列的液体和气体产物,其中液体产物就是液体燃料的主要来源。
煤的加氢煤的加氢是指将煤中的气化产物在高温和高压的条件下与氢气进一步反应,将气体产物中的不饱和化合物加氢饱和,生成高品质的液体燃料。
加氢反应可以提高液体燃料的氢碳比,增加其能量密度,提高其燃烧效率。
关键技术煤温和加氢液化制高品质液体燃料的关键技术包括催化剂选择、温度和压力控制、反应器设计等。
催化剂选择催化剂的选择对煤温和加氢液化的反应效果和产物质量起到关键作用。
优质的催化剂应具有高催化活性、良好的稳定性和选择性,能够在适宜的温度下催化反应进行。
常用的催化剂包括铁、镍、钼等金属催化剂以及复合催化剂。
温度和压力控制温度和压力是影响煤温和加氢液化反应进行的重要因素。
适当的温度和压力可以促进反应物的转化率和产物的质量。
一般来说,较高的温度和压力有利于提高反应速率和产品收率,但过高的温度和压力会增加能源消耗和设备投资。
煤的直接液化

4、操作条件 温度和压力是影响煤直接液化反应进行的 两个因素,也是直接液化工艺两个最重要 的操作条件。 煤的液化反应是在一定温度下进行的,不 同工艺的所采用的温度大体相同,一般为 440~460º C。当温度超过450º C时,煤转化 率和油产率增加较少,而气产率增多,因 此会增加氢气的消耗量,不利于液化。
2、直接液化的溶剂 在煤液化过程中,溶剂起着溶解煤、溶 解气相氢向煤或催化剂表面扩散、供氢或 传递氢、防止煤热解的自由基碎片缩聚等 作用。 煤的直接液化必须有溶剂存在,这也是 与加氢热解的根本区别。 通常认为在煤的直接液化过程中,溶 剂能起到如下作用:
a)将煤与溶剂制成浆液的形式便于工艺过程 的输送。同时溶剂可以有效地分散煤粒、 催化剂和液化反应生成的热产物,有利于 改善多相催化液化反应体系的动力学过程。 b)依靠溶剂能力使煤颗粒发生溶胀和软化, 使其有机质中的键发生断裂。 c) 溶解部分氢气,作为反应体系中活性氢的 传递介质;或者通过供氢溶剂的脱氢反应 过程,可以提供煤液化需要的活性氢原子。
d)在有催化剂时,促使催化剂分散和萃取出 在催化剂表面上强吸附的毒物。 在煤液化工艺中,通常采用煤直接液化后 的重质油作为溶剂,且循环使用,因此又 称为循环溶剂。
3、催化剂 选用合适的催化剂对煤的直接液化至关重要, 一直是技术开发的热点之一,也是控制工艺成 本的重要因素。 催化剂的作用机理,有两种观点:(1)催化剂 的作用是吸附气体中的氢分子,并将其活化成 为易被煤的自由基团接受的活性氢;(2)催化 剂是使煤中的桥键断裂和芳环加氢的活性提高, 或是使溶剂加氢生成可向煤转移氢的供氢体等。
对压力而言,理论上压力越高对反应越有 利,但这样会增加系统的技术难度和危 险性,降低生产的经济性,因此,新的 生产工艺都在努力降低压力条件。 早期液化反应(如德国工艺)压力 高达 30~70MPa ,目前常用的反应压力 已经降到了 17~25MPa ,大大减少了设 备投资和操作费用。
- 1、下载文档前请自行甄别文档内容的完整性,平台不提供额外的编辑、内容补充、找答案等附加服务。
- 2、"仅部分预览"的文档,不可在线预览部分如存在完整性等问题,可反馈申请退款(可完整预览的文档不适用该条件!)。
- 3、如文档侵犯您的权益,请联系客服反馈,我们会尽快为您处理(人工客服工作时间:9:00-18:30)。
? 1973年后,由于中东战争,石油价格暴涨,煤直接液化技 术的开发又开始活跃起来。德国、美国、日本、前苏联等 国的煤化学家相继开发了煤炭液化新工艺。
1.3 煤直接液化工艺开发过程
? 煤直接液化工艺的开发过程要经历一系列逐步放大的装置 的实验。根据工艺发明原理确定工艺路线后,要通过反复 的装置试验来验证工艺的可行性,以降低日后工业放大及 商业化的风险。
? 产品产率 在糊相加氢阶段,当氢耗量为 7%时,100t 高挥发分烟
煤(daf )可得到13.8t 汽油、47.7t 中油和24.3t C1~C4 气 态烃产品。每生产1t 汽油和液化气需要煤3.6t,其中38% 用于制氢、27%用于动力和约35%用于液化本身,故液化 效率约为44%。 ? 可见,德国煤直接加氢液化的老工艺能源转化效率低,再 加上反应条件苛刻,缺乏竞争性,人们纷纷寻求降低反应 压力和提高过程效率,最终降低液化过程成本的新工艺。
煤加氢直接液化工艺
姓名: **** 导师: **** 时间: 2013.12.28
主要 内容
煤加氢液化技术的开发过程 煤直接液化基本工艺流程 德国煤加氢液化老工艺 典型煤直接液化工艺 煤-油共处理
1、煤加氢液化技术的开发过程
1.1 煤加氢直接液化的定义
在较高温度( >400℃)、高压( >6MPa )、氢 气(或CO+H 2、CO+H 2O)、催化剂和溶剂作用 下将煤进行解聚、裂解加氢,直接转化为液体油 的加工过程。
54
2、煤直接液化基本工艺流程
?煤直接液化工艺流程简图
催化剂
氢气 氢循环
煤
煤浆制
备单元
反应 单元
分离 单元
循环溶剂
煤: <0.2mm 催化剂: Fe-S 系
420-470 oC 17-30 MPa
提质加 工单元
气体
汽油 柴油 航空燃料
残渣
380-390 oC 15-18 MPa
3、德国煤加氢液化老工艺
3.1 工艺流程
第一段液相加氢
30~70 MPa
470~480℃
第二段气相加氢
32MPa
360~450℃
3.2 工艺特点
? 温度和压力 德国煤直接加氢液化老工艺的煤糊加氢段的压力高达
30~70MPa ,因煤种和所用催化剂的不同而异,反应塔温 度470~480℃,煤糊预热器的出口温度比预定反应温度低 20~60℃;液化粗油的气相加氢段反应温度为 360~450℃, 催化加氢反应系统压力大约32MPa 。 ? 催化剂 煤糊加氢主要采用拜尔赤泥、硫化亚铁和硫化钠,后者的 作用是中和原料煤中的氯,以防止在加氢过程中生成氯化 氢引起设备腐蚀。
3.2 工艺特点
? 固液分离 该工艺的固液分离采用过滤分离,从热分离器底部流出
的淤浆在140~160℃温度下直接进入离心过滤机分离。对 1000kg 干燥无灰基烟煤而言,当液化转化率为 70%时,淤浆 总质量为1130kg ,固体残渣重340kg ;而液化转化率为 96% 时,淤浆和固体残渣质量分别减少 270kg 和80kg 。
过滤分离得到的滤液,即重质油,含有较多的沥青烯和 2%~12% 的固体,作为煤浆加氢循环溶剂,其供氢能力较差 ,沥青烯积累会使煤浆黏度上升,这正是德国老工艺需要 70MPa 反应压力的主要原因之一;滤饼含固体38%~40% , 为回收滤饼中的油,对滤饼进行干馏,可回收滤饼中约 30% 的油。
3.2 工艺特点
? 德国是世界上第一家拥有煤直接加氢液化工业化生产经验 的国家。其第一套生产装置由德国I.G.Farbenindustrie( 燃 料公司)在1927年建成,也被称为IG 工艺。德国煤加氢液 化老工艺是世界其他国家开发同类工艺的基础。
? 德国的IG 工艺可分为两段加氢过程,第一段加氢是在高 压氢气下,煤加氢生成液体油(中质油等),又称煤浆液 相加氢。第二段加氢是以第一段加氢的产物为原料,进行 催化气相加氢制得成品油,又称中油气相加氢,所以 IG 法也常称作两段加氢法。
? 日处理吨级煤炭的中试连续试验装置 日本称为:PSU (process support unit) 美国称为:PDU (process development unit) 目的:进一步验证BSU确立的工艺流程、考察放大效应。
为降低费用,PDU 运转过程发现问题可能要回到 BSU中进一 步研究解决。 ? 工艺开发的最后的一个步骤,是将BSU和PDU装置的各项
运转成果全部集中于一个大型的工业性试验装置,通常称 为PP 装置(Pilot Plant )上。工业性试验装置的规模处理 煤约数百t/d 左右,工艺流程和操作条件已基本固定。
1.3 煤直接液化工艺开发过程
? 发达国家完成PP 装置验证的煤直接液化工艺及运行情况:
国家 美国 美国 美国 德国 日本 日本
1.2 国外煤加氢直接液化的发展背景
? 1913年,德国化学家诺贝尔奖获得者柏吉斯(Bergius ) 首先研究了煤的高压加氢,并获得了专利,从而为煤加氢 液化技术奠定了基础。
? 1927年在德国莱那(Leuna )建立了世界第一个煤直接液 化工厂,第二次世界大战期间又建 11套煤直接液化装置, 到1944年,总生产能力达到4.23Mt/a ,为德国提供了发动 战争用油。
? 实验室规模试验装置 日本称为: BSU( bench scale unit) 美国称为: CFU (continuous flow unit) 目的:每天处理煤炭数千克至数百千克:验证工艺的可操
作性、确定产物产率构成和产物分析检验方法、提供动力学 数据和催化剂、煤种适应性等数据。
1.3 煤直接液化工艺开发过程
工艺 H-COAL SRC- Ⅱ
EDS IGOR NEDOL BCL
规模 /( t/d) 200~600
50 250 200 150 50
使用期
1980~1982 年 (3年)
1976~1981 年 (5年)
1980~1982 年 (2.5 年)
1981~1987 年 (6年)
1997~1998 年 (2年)
1987~1990 年 (4年)
连续进煤 (1321h)
208d (5000h)
80d (1920h)
73d (1760h)
累计进煤 —
油收率 /% 51
— 44
445d
(10692h)
45
917d 58
(22000h)
259d 58
(6200h)
417d
(10000h)