外文翻译-模具型腔数控加工计算机辅助刀具选择和研究
数控机床刀具设计论文中英文资料外文翻译文献综述
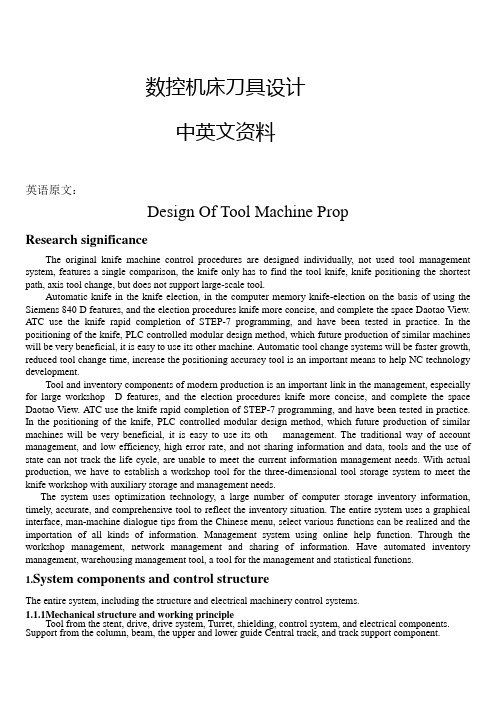
数控机床刀具设计中英文资料英语原文:Design Of Tool Machine PropResearch significanceThe original knife machine control procedures are designed individually, not used tool management system, features a single comparison, the knife only has to find the tool knife, knife positioning the shortest path, axis tool change, but does not support large-scale tool.Automatic knife in the knife election, in the computer memory knife-election on the basis of using the Siemens 840 D features, and the election procedures knife more concise, and complete the space Daotao View. ATC use the knife rapid completion of STEP-7 programming, and have been tested in practice. In the positioning of the knife, PLC controlled modular design method, which future production of similar machines will be very beneficial, it is easy to use its other machine. Automatic tool change systems will be faster growth, reduced tool change time, increase the positioning accuracy tool is an important means to help NC technology development.Tool and inventory components of modern production is an important link in the management, especially for large workshop D features, and the election procedures knife more concise, and complete the space Daotao View. ATC use the knife rapid completion of STEP-7 programming, and have been tested in practice. In the positioning of the knife, PLC controlled modular design method, which future production of similar machines will be very beneficial, it is easy to use its oth management. The traditional way of account management, and low efficiency, high error rate, and not sharing information and data, tools and the use of state can not track the life cycle, are unable to meet the current information management needs. With actual production, we have to establish a workshop tool for the three-dimensional tool storage system to meet the knife workshop with auxiliary storage and management needs.The system uses optimization technology, a large number of computer storage inventory information, timely, accurate, and comprehensive tool to reflect the inventory situation. The entire system uses a graphical interface, man-machine dialogue tips from the Chinese menu, select various functions can be realized and the importation of all kinds of information. Management system using online help function. Through the workshop management, network management and sharing of information. Have automated inventory management, warehousing management tool, a tool for the management and statistical functions.1.System components and control structureThe entire system, including the structure and electrical machinery control systems.1.1.1Mechanical structure and working principleTool from the stent, drive, drive system, Turret, shielding, control system, and electrical components. Support from the column, beam, the upper and lower guide Central track, and track support component.1) Drive for the system chosen VVVF method. Cone used brake motors, with VVVF by Cycloid reducer through sprocket drive.2) Drag a variable frequency drive system and control technology. VVVF adopted, will speed drive shaft in the normal range adjustment to control the speed rotary turret to 5 ~ 30mm in, the drive shaft into two, two under through sprocket, the two profiled rollers Chain driven rotating shelves. Expansion chain adopted by the thread tight regulation swelling, swelling the regular way. - Conditi D features, and the election procedures knife more concise, and complete the space Daotao View. ATC use the knife rapid completion of STEP-7 programming, and have been tested in practice. In the positioning of the knife, PLC controlled modular design method, which future production of similar machines will be very beneficial, it is easy to use its at six other Des V oeux a knife, can be categorized with some of knife auxiliary equipment, such as bits, such as turning tools.1.1.2.Electrical Control SystemThis tool storage systems is the main electrical control their shelves for operational control and position control. Operational control equipment, including operation of the start of braking control. Position Control is the main location and address of the shelves for testing.1) Electric Transmission horizontal rotary tool storage systems are the mechanical movements are repeated short-term work system. And the run-time system needs some speed, speed transmission needs, the system will use VVVF method can be used simple structure, reliable operation of the motor and frequency inverter.2) Control of the system is divided into two kinds of manual control and automatic control, manual control as a general reserve and debugging methods of work; ways to the system control computer (IPC) and the control unit (inverter contactor , etc.) consisting of a control system.3) location and positioning accuracy of the system automatically identify the site and location using a detection device tion, timely, accurate, and comprehensive tool to reflect the inventory situation. The entire system uses a graphical interface, man-machine dialogue tips from the Chinese menu, select various functions can be realized and the importation of all kinds of information. Management system using online help function. Through the workshop management, network management and sharing of information. Have automated inventory management, warehousing management tool, a tool for the management and statistical fu as proximity switches, relays through the plate-point isolation and the number plate recorded close to the switching signal acquisition and operation of Hutchison with a Optimal Path addressable identify the current location and shelves of the purpose of the shelf location. In order to enable a more accurate positioning system, adopted two photoelectric switches, to detect the two shelves of the two films.1.2.The functions of the knifeknife The is the role of reserves a certain number of tools, machine tool spindle in hand to achieve the fungibility a disc sc knife in the library with discoid knife, cutting tool along See how vertical arrangement (including radial and axial from knife from knife), along See how radial array into acute or arranged in the form of the knife. Simple, compact, more applications, but are ring-cutter, low utilization of space. Figure 2.7 a) to c). D features, and the election procedures knife more concise, and complete the space Daotao View. ATC use the knife rapid completion of STEP-7 programming, and have been tested in practice. In the positioning of the knife, PLC controlled modular design method, which future production of similar machines will be very beneficial, it is easy to use its. If the knife cutter knife is the type of library, the chain knives, and other means, in the form of the knifeand capacity according to the Machine Tool to determine the scope of the process.s, but are ring-cutter, low utilization of space. Figure 2.7 a) to c). D features, and the election procedures knife more concise, and com mon typesThe knife is a tool storage devices, the common knife mainly in the following forms:(1) the turret knifeIncluding the first level turret vertical turret and the first two, see Figure 2.6 a) and b):(2) the disc cutterDisc knife in the library with discoid knife, cutting tool along See how vertical arrangement (includingradial and axial from knife from knife), along See how radial array into acute or arranged in the form of theknife. Simple, compact, more applications, but are ring-cutter, low utilization of space. Figure 2.7 a) to c).D features, and the election procedures knife more concise, and complete the space Daotao View. ATC use theknife rapid completion of STEP-7 programming, and have been tested in practice. In the positioning of theknife, PLC controlled modular design method, which future production of similar machines will be verybeneficial, it is easy to use its. If the knife storage capacity must be increased to increase the diameter of theknife, then the moment of inertia also increased correspondingly, the election campaign long knife. Toolnumber not more than 32 general. Cutter was multi-loop order of the space utilization knife, but inevitablygiven the knife from complex institutions, applicable to the restricted space Machine Tool storage capacity andmore occasions. Two-disc structure is two smaller capacity knife on both sides of the sub-spindle place, morecompact layout, the number ofapply to small and medium-sizedprocessing center.(3) the chain knife Includingsingle-and multi-ring chain ringchain, chain link can take many forms change, see Figure 2.8 a) to c), the basic structure shown in Figure 2. 8 doFeatures: knife apply to the larger capacity of the occasion, the space of the small number of generally applicable to the tool in the 30-120. Only increase the length of the chain tool will increase the number should not be increased circumferential speed of its moment of inertia of the knife does not increase the disc as large.(4) linear combination knife and the knife libraryThe linear knife simple structure in Figure 2.9, tool single order, the capacity of small knife, used for CNC lathe and drill press on. Because the location of fixed knife, ATC completed action by the spindle without manipulator. The cutter knife is generally the turret combination turret with a combination of the disc cutter knife and the chain combination. Every single knife the knife certificates of smaller, faster tool change. There are also some intensive drum wheel, and the lattice-type magazine for the knife, the knife-intensive though.Small footprint, but because of structural constraints, basically not used for single processing center, the concentration used for FMS for the knife system.1.4 Tool storage capacityTool storage capacity of the first to consider the needs of processing, from the use of point of view,generally 10 to 40 knives, knife will be the utilization of the high, and the structure is compact.1.5 Tool options(1) choose to order processing tool according to the order, followed Add to the knife every knife in the Block. Each tool change, the order of rotation of a cutter knife on location, and remove the need knives, has been used by the cutter knife can be returned to the original Block, can also order Add Block, a knife. However, as the knife in the tool in different processes can not be repeated use of the knife must increase the capacity and lower utilization rate.(2) most of the arbitrary choice of the current system of using arbitrary NC election knives, divided into Daotao coding, coding and memory-cutter, three. Daotao coding tool code or knives or Daotao need to install the code used to identify, in accordance with the general principle of binary coding coding. Tool knife election coding method uses a special knife handle structure, and each of the coding tool. Each of the tool has its own code, thereby cutting tool can be in different processes repeatedly used, not to replace the tool back at the original knife, the knife capacity can be reduced accordingly. Memory-election this paper knife, in this way can knives and knife in the position corresponding to the Daotao memory of the PLC in the NC system, no matter which tool on the Inner knife, tool information is always there in mind, PLC . On the knife with position detection devices, will be the location of each Daotao. This tool can be removed and sent back to arbitrary. On the knife is also a mechanical origin, every election, the nearest knife selection.1.6.Control of the knife(1) the knife as a system to control the positioning axis. In the ladder diagram in accordance with the instructions for computing T code comparison of the output angle and speed of instructions to the knife the knife servo drive servo motor. Tool storage capacity, rotation speed, and / deceleration time, and other system parameters can be set in such a manner free from any outside influence positioning accurate and reliable but the cost is higher.(2) knife from the hydraulic motor drives, fast / slow the points, with proximity switches count and positioning. In comparison ladder diagram of the current storage system knife (knife spindle) and goals knife (pre-knife) and computing, then output rotation instructions, judging by the shortest path rotation in place. This approach requires sufficient hydraulic power and electromagnetic valve knife the rotational speed can be adjusted through the throttle. But over time may be oily hydraulic, oil temperature and environmental factors impact the change in velocity and accuracy. Not generally used in large and medium-sized machine tool change frequently.(3) the knife from AC asynchronous motor driven cam mechanism (Markov institutions), with proximity switches count, which means stable operation, and generally accurate and reliable positioning cam used in conjunction with a mechanical hand, ATC fast-positioning.2. ATC, the main types, characteristics, and the scope of application2.1 Auto Rotary ToolRotary Tool automatically on the use of CNC machine tool is a simpleinstallation of automatic tool change, the Quartet and 47.60 Turret Tool various forms, such as rotary turret were installed on four, six or more of the Tool , NCinstructions by ATC. Rotary Tool has two vertical and horizontal, relatively simple structure, applicable to economic CNC lathe.Rotary Tool in the structure must have good strength and stiffness, resistance to bear rough Cutting Tool in the cutting force and reduce the role of deformation and improve processing accuracy. Rotating Tool to choose reliable positioning programme structure and reasonable position, in order to ensure that each rotary turret to a higher position after repeated positioning accuracy (typically 0.001 to 0.005mm). Figure 2.1 shows the spiral movements of the Quartet Turret.Auto Rotary Tool in the simplest of ATC, is 180 º rotary ATC devices, as shown in Figure 2.2 ATC instructions received, the machine control system put ATC spindle control to the designated location at the same time, the tool movement to the appropriate location, ATC, with the rotary axis and at the same time, the knives matching tool; drawbars from Spindle Cutting Tools rip, ATC, will be the tool from their position removed; ATC, 180 º rotary tool spindle and the tool and tool away; ATC, the Rotary At the same time, thetool refocusing its position to accept Spindle removed from the cutting tool; Next, ATC, will be replaced with the cutter knives were unloaded into the spindle and tool: Finally, back to the original ATC, "standby" position. At this point, ATC completed procedures to continue to run. This ATC, the main advantage of simple structure,the less movement, fast tool change. The main disadvantage is that knives must be kept in parallel with the axis of the plane, and after the home side compared to the tool, chip and liquid-cutting knife into the folder, it is necessary to the tool plus protection. Cone knife folder on the chip will cause ATC error, or even damage knife folders, and the possibility of spindle. Some processing centre at the transfer, and the tool side. When the ATC command is called, the transfer-cutter knives will be removed, the machine go forward, and positioning with the ATC, in line with the position. 180 º "Rotary ATC devices can be used horizontal machine, can also be used for vertical machining centers.2. 2 ATC head-turret installedWith rotating CNC machine tool often used such ATC devices, with a few turret head spindle, each with a spindle on both knives, the first tower interim process can be automatic tool change-realization. The advantage is simple structure, tool change time is short, only about 2 s. However, due to spatial constraints, the number of spindle can not be too much, usually only apply to processes less, not to high precision machine tools, such as the NC drill, such as CNC milling machine. In recent years there has been a mechanical hand and the turret head with a knife for the automatic tool change ATC devices, as shown in Figure 2.3. It is in fact a turret head ATC, and the knife-ATC device combination. The principle is as follows:5 turret on the first two tool spindle 3 and 4, when using the tool spindle 4 processing tool, the manipulator 2 will be the next step to the need for the tool does not work on the tool spindle 3 until after the completion of this process , the first rotary turret 180 º, ATC completed. ATC most of their time and processing time coincidence, the only real tool change time turret transposition of the first time, this approach mainly used for ATC and NC NC drilling file bed.2. 3.Daidao system for the automatic tool changeFigure 2.4 shows the knife and the whole machine tool CNC machine tools for the appearance of Fig. Figure 2.5 shows the knife and split-type machine to the appearance of CNC machine tool plans.At this point, knife storage capacity, a heavier tool can, and often additional transport unit to complete the knife between the spindle and cutting tool transport.Daidao the knife from the ATC, the election knives, automatic loading and unloading machine tool and tool exchange institutions (manipulator), composed of four parts, used widely.Tool Automatic Tool Change When CNC tool code and the code in line with directives of the tool selected, the rotary cutter knives will be sent to the ATC position, waiting to grab manipulator. Random knife election is the advantage of the cutter knife in the order has nothing to do with the processing sequence, the same tool can be used repeatedly. Therefore, the relatively small number of knives, knife the corresponding smaller. Random elections knife on the tool must be coded to identify. There are three main coding.1. Tool coding. Adopt special knife handle structure coding, the drawbars on the knife handle back-endpackages such as spacing of the coding part of the lock-nut fixed. Coding diameter ring diameter of a size two,respectively, said that binary "1" and "0" to the two rings are different, can be a series of code. For example, there are six small diameter of the ring can be made to distinguish between 63 (26-1 = 63) of the coding tool. All of 0 normally not allowed to use the the manipulator system, the whole process more complicated ATC. We must first used in the processing of all installed in the standard tool on the knife handle in the machine outside the pre-size, according to a certain way Add to the knife. ATC, selected first in the knife knife, and then from ATC, from the knife from the knife or spindle, exchange, the new knife into the spindle, the old knife back into the knife.ATC, as the former two knives to accommodate a limited number can not be too many, can not meet the needs of complex parts machining, CNC machine tool Automatic Tool Change Daidao the use of the automatic tool change devices. The knife has more capacity, both installed in the spindle box side or above. As for the automatic tool change Daidao device CNC machine tool spindle box only a spindle, spindle components to high stiffness to meet the machining requirements. The number of establishments in larger knife, which can meet the more complex parts of the machining processes, significantly improving productivity. Daidao system for the automatic tool change applied to drilling centres and CNC machining centers. The comparison drawn Daidao automatic tool change system is the most promising.3.PLC control of the knife random mode of election3. 1Common methods of automatic election knifeAutomatic control of the knife CNC refers to the system after the implementation of user instructions onthe knife library automation process, including the process to find knives and automatic tool change [(63,71]. CNC Machining Center device (CNC) directive issued by the election knife , a knife, the tool required to take the knife position, said the election automatic knife. automatically elected knife There are two ways: randomsequence election knives and knife election method.3.1.1 order election knifeTool Selection order is the process tool according to the sequence of the insert knife, the use of knives in order to take place, used knives back at the original knife, can also order Add Block, a knife. In this way, no need Tool identification devices, and drive control is a relatively simple, reliable and can be used directly from the points of the knife machinery to achieve. But the knives in each of the tool in different processes can not be reused, if the tool is installed in accordance with the order of the knife, there will be serious consequences. Theneed to increase the number of knives and knife the capacity of the tool and reduce the utilization of the knife.3.1.2Random election knifeRandom election under the knife is arbitrary instructions to select the required tools, then there must be tool identification devices. Tool knife in the library do not have the processing in accordance with the order of the workpiece can be arbitrary storage. Each of the tool (or knife blocks) are for a code, automatic tool change, the rotary cutter, every tool have been the "tool identification device" acceptable identification. When CNCtool code and the code in line with directives of the tool selected, the rotary cutter knives will be sent to the ATC position, waiting to grab manipulator. Random knife election is the advantage of the cutter knife in the order has nothing to do with the processing sequence, the same tool can be used repeatedly. Therefore, the relatively small number of knives, knife the corresponding smaller. Random elections knife on the tool must be coded to identify. There are three main coding.1. Tool coding. Adopt special knife handle structure coding, the drawbars on the knife handle back-end packages such as spacing of the coding part of the lock-nut fixed. Coding diameter ring diameter of a size two, respectively, said that binary "1" and "0" to the two rings are different, can be a series of code. For example, there are six small diameter of the ring can be made to distinguish between 63 (26-1 = 63) of the coding tool. All of 0 normally not allowed to use the code, to avoid the cutter knife Block did not confuse the situation.2. Knife Block coding. On the knife Block coding, coding tool, and tool into line with the number of knives in the Block. ATC knife when the rotation, so that each knife seats followed through knowledge knife, knife found blocks, knives stopped the rotation. At this time there is no knife handle encoding part of the knife handle simplified.3. Annex coding methods. This style of coding keys, coded cards, coding and coding-disc, which is the most widely used coding keys. First to knives are attached to a tool of the show wrapped coding keys, and when the cutter knife to the store at knife in, so put the number of keys to remember knife Block Road, will be inserted into key to the coding Block next to the key hole in the seat for the knife to the numbers. ConclusionFocused on in today's manufacturing environment tool storage and management of new models and methods, practical application of good results in systems integration and optimization, and other aspects of operations will be further explored, so that it has a higher theoretical and practical level.译文:机床刀具设计课题研究意义机床原来的刀库控制程序是单独设计的,没有采用刀具管理系统,功能也比较单一,只实现了刀库刀具的找刀、刀库最短路径定位、主轴换刀,而且不支持大型刀具。
外文翻译---注塑模具设计的一种智能型腔设计系统

International Journal of CAD/CAM V ol. 2, No. 1, pp. 69~75 (2002)An Intelligent Cavity Layout Design System for Injection Moulds Weigang Hu and Syed Masood*Industrial Research Institute Swinburne (IRIS), Swinburne University of Technology, Hawthorn, Melbourne, Australia 3122AbstractLayout Design System (ICLDS) for multiple cavityinjection moulds. The system is intended to assist mould designers in cavity layout design at concept design stage. Thecomplexities and principles of cavity layout design as well as various dependencies in injection mould design are introduced.The knowledge in cavity layout design is summarized and classified. The functionality, the overall structure and generalprocess of ICLDS are explained. The paper also discusses such issues as knowledge representation and case-based reasoningused in the development of the system. The functionality of the system is illustrated with an example of cavity layout designproblem.Keywords: Intelligent design, cavity layout design, injection mould design, case-based reasoning, design support system1. IntroductionIn manufacturing, the injection moulding is one of the most widely used production processes for producing plastic parts with high production rate and little or no finishing required on plastic products. The process consists of injecting molten plastic material from a hot chamber into a closed mould, allowing the plastic to cool and solidify and ejecting the finished product from the mould. For each new plastic product, the injection moulding machine requires a new injection mould. Design and manufacture of injection mould is a time consuming and expensive process and traditionallyrequires highly skilled tool and mould makers. An injection mould consists of several components, which include mould base, cavities, guide pins, a sprue, runners, gates, cooling water channels, support plates, slides and ejector mechanism [1]. Design of mould is also affected by several other factors such as part geometry, mould material, parting line and number of cavities per mould. With the advances in computer technology and artificial intelligence, efforts have been directed to reduce the cost and lead time in the design and manufacture of an injection mould. Injection mould design has been the main area of research since it is a complex process involving several sub-designs related to various components of the mould, each requiring expert knowledge and experience. Mould design also affects the productivity,mould maintenance cost, manufacturability of mould, and the quality of the moulded part. Most of the work in mould design has been directed to the application of expert systems, knowledge based systems and artificial intelligence to eliminate or supplement the vast amount of human expertise required in traditional design process. Kruth and Willems [2] developed an intelligent support system for the design of injection moulds integrating commercial CAD/CAM, a relational database and an expert system. Lee et. al. [3] proposed a systematic methodology and knowledge base for injection mould design in a concurrent engineering environment. Raviwongse and Allada [4] developed a neural networkbased design support tool to compute the mould complexity index to help mould designers to assess their proposed mould design on mould manufacturability. Kwong and Smith [5] developed a computational system for the process design of injection moulding based on the blackboard-based expert system and the case-based reasoning approach, which includes mould design, production scheduling, cost estimation and determination of injection moulding parameters. Britton et. al. [6] discussed the injection mould design from a functional perspective using functional design knowledge and a number ofknowledge libraries. Mok et. al. [7] developed an interactive knowledge-based CAD system for injection mould design incorporating computational, knowledge and graphic modules. Several studies have also been made on improving the design of specific components of an injection mould. Ong et. al. [8] developed a knowledge-based and objectoriented approach for the design of the feed system for injection moulds, which can efficiently design the type, location and size of a gating system in the mould. Irani et. al. [9] also developed a software system for automatic design of gating and runner systems for injection moulds and provide evaluation of gating design based on specified performance parameters. Nee et. al. [10] proposed a methodology for determination of optimal. parting directions in injection mould design based on automatic recognition and extraction of undercut features. Chen and Chou [11] developed algorithms for selectinga parting line in mould design by computing the undercutvolumes and minimising the number of undercuts. Parkand Kwon [12] worked on the design of cooling systemsin injection moulds and proposed an optimal designbased on thermal analysis and design sensitivity analysisof the cooling stage of the injection moulding process.Lin [13] worked on the use of gate size and gate position as the major parameters for simulated injection mould performance prediction. One area in injection mould design, which has received little attention, is the design of cavity layout in a multiple cavity injection mould. Cavity layout design affects the whole process of injection moulding directly, since it is one of the most important phases in mould design process. Consideration of cavity layout design in injection mould at concept design stage will improve the quality of injection moulded products because it is associated with the determination of many key factors affecting the design and quality of mould. Such factors include number of cavities; parting line; type of mould; type and position of gate; runner system; cooling system and ejection system. Some of these factors are difficult to build astrue mathematical models for analysis and design. This paper presents the development of a design support system, called Intelligent Cavity Layout Design System (ICLDS), for multiple-cavity injection moulds based on knowledge based and object oriented approaches. It uses the case-based and ruled-based reasoning in arriving at the layout solution [14]. It is based on the commercial software system named “RETE++”, which is an integrated development platform for customers to develop their own knowledge-based systems [15]. The objective is to make full use of available techniques in artificial intelligence in assisting mould designers at concept design stage. 2. Cavity Layout Design in Injection MouldsCurrent practice for injection mould design, especially cavity layout design, depends largely on designers’ experiences and knowledge. It would therefore be desirable to use knowledge engineering, artificial intelligence and intelligent design techniques in generating an acceptable cavity layout design in injection mould accurately and efficiently. In mould design, most of patterns of cavity layout and rules and principles of cavity layout design can also be easily represented in the form of knowledge, which can be used in most of knowledge-based design systems. the criteria to select the suitable layout pattern for design are mainly dependent on working environments, conditions and requirements of customer and are mainly based on designer’s skill and experience. To make a choice of contradictory factors will rely obviously on designer’s knowledge and experiences. It is rather suitablefor intelligent design techniques to be used in systems designed for such situations, especially for routine or innovation design.Design of injection mould mainly involves consideration of design of the following elements or sub-systems:(1) mould type(2) number of cavities(3) cavity layout(4) runner system(5) ejector system(6) cooling system(7) venting(8) mounting mechanismMost of the elements are inter-dependent such that it is virtually impossible to produce a meaningful flow chart covering the whole mould design process. Obviously, in injection mould design, it is difficult for designer to monitor all design parameters. Cavity design and layout directly affects most of other activities.The application of advanced knowledge based techniques to assist designer in cavity layout design at conceptdesign stage will greatly assist in the development of a comprehensive computer-aided injection mould design and manufacturing system. Higher the number of cavities of mould, higher the productivity of the injection mould. But this may lead to difficulties with issues such as balancing the runners or products with the complicated cavity shapes, which in turn may lead to problems of mould manufacturability. It is also possible that the number of cavities and the pattern of cavity layout will influence the determination of parting line, type of gate, position of gate, runner system and cooling system. Most of the main activities of mould design are therefore linked to cavity layout design. The cavity layout design problem therefore depends upon a number of functionalities of the overall mould design system, which includes:(1) definition of design specifications includinganalysis and description of characteristics of(2) determination of mould type(3) determination of number of cavities(4) determination of orientation of product(5) determination of runner type and runnerconfiguration(6) determination of type and position of gate(7) cavity layout conceptual design(8) evaluation of ejection ability, manufacturingability and economic performances(9) determination of cooling system(10) graphic results display and output3. Structure of ICLDS and the Design ProcessThe structure of the Intelligent Cavity Layout Design System (ICLDS) is based on case-based reasoning andruled-based reasoning designed around the RETE++ The design process starts with the definition of design specifications. The ICLDS system retrieves similar cases from case base by computing the similarity between the cases and the new case. If the solution is satisfactory, then results are displayed graphically. If the solution is not satisfactory, then ICLDS will use rule-based reasoning with forward or backward chaining or a mixture of both to arrive at a solution. Ifthe solution is still unsatisfactory, then the user has to modify some of the initial design specifications. The use of case-based technology in the design process in ICLDS allows the user to obtain the solution(s) of design problem more quickly and flexibly. The structure of knowledge base and database used in the development of ICLDS is based on the underlying knowledge base and database structure from the RETE++ software system, which is a commercially available software development platform.4. Development of ICLDS4.1. Classifications of KnowledgeFor various logic and steps involved in layout design, there are different kinds of knowledge that needs to be described and represented in cavity layout design. The types of knowledge can be classified into five kinds based on object oriented (OO) concept as described below:(1) Design instance/case: previous design cases and current design instances(2) Relation: superclass-class-subclass relation, classinstance relation(3) Attribute: design variables, features, attributes of design problem(4) Rule: general design rules, design experiences(5) Procedure and/or model: numeric calculation, mathematical modeling, analysis, evaluation andprocedures.4.2. Knowledge RepresentationsTo describe each of these types of knowledge, the internal data structures of the ECLIPSE language, included in RETE++ inherently, can be used to make the object orientated representation of the design process as explained earlier. Some other considerations in knowledge representation are as follows:(1) For “design instance/case”, we combine “fact definition” and “relation definition” plus database and case base to represent it(2) The “attribute” are represented as instances of“template definition” and/or “relation definition”(3) For “relation”, we use “relation definition” to describe it(4) For “rule”, we combine “rule definition” and“rule set definition” to represent it(5) The “procedure/model” are defined by external routines using C++ language Furthermore, “goal definition” and “goal generation”techniques are used to fulfil backward chaining reasoning, and “case-based reasoning” is used to carry out casebased design.4.3. Case-based ReasoningCase-Based Reasoning (CBR) is dependent firstly on case retrieved. Case-based retrieval is based on “Similarity Metric”. Therefore, how to calculate the similarity is obviously the key technique in CBR, and it is described in detail as below. Similarity metric is a weighted distancefunction in a multi-dimensional space where each dimension corresponds to a field whose value is specified in the query (new case) and which has a non-missing value in the case being ranked. The distance between the case and the query (which corresponds to a point in this multi-dimensional space) is computed differently for ordinal and nominal fields. An ordinal field is a field whose values are ordered or sorted. A nominal field is one whose values represent qualitative information for which sorting makes no sense. In general, ordinal fields include dates, integers, and real numbers while nominal fields include Boolean, Symbols, and Text.关于CAD/CAM的国际性杂志注塑模具设计的一种智能型腔设计系统摘要:本文展示了注塑模具多腔设计的智能型腔设计的发展,这个系统可以帮助模具设计者提供流道设计的观念,介绍了复杂的型腔设计原则和多样的设计理念,以及型腔版面设计的概述、分类、功能,全面地构造和智能化腔孔版面设计的程序使用方法的解释说明。
CNC机床加工中的刀具选型与切削参数优化

CNC机床加工中的刀具选型与切削参数优化CNC(Computer Numerical Control)机床是一种能够按照预先输入的程序指令进行自动化加工的机床。
在CNC机床加工中,刀具选型与切削参数的选择对于加工质量和效率起着至关重要的作用。
本文将就CNC机床加工中的刀具选型与切削参数优化进行探讨。
一、刀具选型在CNC机床加工中,刀具的选型要根据加工材料、加工要求以及加工方式来选择,常用的刀具选型有以下几种:1.硬质合金刀具硬质合金刀具具有优异的耐磨性和高硬度,适用于加工硬度较高的材料,如铸铁、合金钢等。
同时,硬质合金刀具还能够提供较好的切削性能和切削稳定性,因此在高速切削中得到广泛应用。
2.高速钢刀具高速钢刀具是热处理过的优质合金钢,具有较高的硬度和耐磨性。
高速钢刀具适用于一般加工材料的加工,价格相对较低,是较为经济实用的刀具选型。
3.立铣刀具立铣刀具适用于铣削工艺,能够完成平面铣削、开槽、镗孔等加工操作。
立铣刀具具有较高的刚性和切削性能,能够提高加工效率和加工精度。
4.钻孔刀具钻孔刀具用于钻孔加工,分为普通钻头和中心钻头两类。
普通钻头适用于常规钻孔操作,而中心钻头则适用于加工前的定位孔。
二、切削参数优化在CNC机床加工中,刀具的切削参数选取直接关系到加工效率和加工质量,合理的切削参数优化能够提高加工效率和延长刀具寿命。
下面分别从切削速度、进给量、切削深度等几个方面进行优化探讨。
1.切削速度切削速度是指刀具在加工过程中的旋转速度,需要根据材料硬度和刀具类型来选择合适的转速。
过高的切削速度会导致切削过程中的高温和过量磨损,而过低的切削速度则会影响加工效率。
因此,在确定切削速度时,需要考虑加工要求和刀具特性,以达到切削效果和刀具寿命的平衡。
2.进给量进给量是指刀具在加工过程中沿工件表面前进的距离,选择合适的进给量可以控制加工负荷,保证加工质量。
过小的进给量会导致切削效率低下,过大的进给量则容易引起振动和过度磨损。
数控车削加工中的刀具选择 毕业论文

题目:数控车削加工中的刀具选择中文摘要理想的加工程序不仅应保证加工出符合图样的合格工件,同时应能使数控机床的功能得到合理的应用和充分的发挥。
数控机床是一种高效率的自动化设备,它的效率高于普通机床的2~3倍,要充分发挥数控机床的这一特点,必须在编程之前对工件进行工艺分析,根据具体条件,选择经济、合理的工艺方案。
数控加工工艺考虑不周是影响数控机床加工质量、生产效率及加工成本的重要因素。
本文从生产实践出发,探讨和总结一些数控车削过程中的工艺问题。
英文摘要The ideal processing procedure should not only guarantee the machining for the workpiece, meanwhile the pattern should be qualified to make numerically-controlled machine tool's function get reasonable application and sufficient play. Nc machine is a kind of efficient automation equipment, it is more efficient than the conventional machine tools of 2 ~ 3 times, to give full play to the characteristics of CNC programming, must be in process analysis of workpiece before, according to the specific conditions, the choice of economic and reasonable process scheme. Nc machining process thoughtfulness is the effect of nc machine tools machining quality, production efficiency and machining cost of important factor. This article from the production practice, discusses and summarizes some of the numerical control turning process process problems.关键词(Keywords):工序划分,刀具选择,生产实践目录第一章前言 (3)第二章数控机床的组成和工作原理 (4)2.1孔加工刀具类 (4)2.2数控铣刀类 (4)2.3拉削刀具类 (5)2.4其它刀具 (5)第三章控刀具及选用 (6)3.1数控机床刀具的特点 (6)3.2金属切削刀具的主要角度 (6)3.3刀具常用材料 (6)3.4 数控机床刀具分类 (9)3.5常用数控刀具结构 (9)3.6数控机床刀具的选择 (10)3.7数控加工刀具选择的典型实例 (12)第四章数控刀具材料新产品科技近况与发展趋势 (13)4.1超硬材料领域 (13)4.2W、C O类涂层和细颗粒(超细颗粒)硬质合金材料领城 (14)4.3含CO类粉末冶金高速钢材料领城 (14)第五章结论 (16)参考文献 (17)致谢 (18)前言毕业设计(论文)是学生在导师指导下,就其某一学术课题在实验性、理论性或观察上具有新的科学研究成果或创新见解和知识的科学记录;或是某种已知原理应用于实际中取得新进展的科学总结。
数控刀具知识常用英文
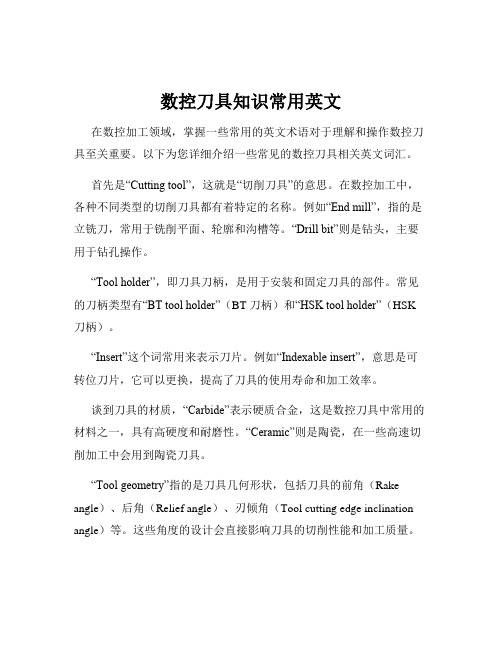
数控刀具知识常用英文在数控加工领域,掌握一些常用的英文术语对于理解和操作数控刀具至关重要。
以下为您详细介绍一些常见的数控刀具相关英文词汇。
首先是“Cutting tool”,这就是“切削刀具”的意思。
在数控加工中,各种不同类型的切削刀具都有着特定的名称。
例如“End mill”,指的是立铣刀,常用于铣削平面、轮廓和沟槽等。
“Drill bit”则是钻头,主要用于钻孔操作。
“Tool holder”,即刀具刀柄,是用于安装和固定刀具的部件。
常见的刀柄类型有“BT tool holder”(BT 刀柄)和“HSK tool holder”(HSK 刀柄)。
“Insert”这个词常用来表示刀片。
例如“Indexable insert”,意思是可转位刀片,它可以更换,提高了刀具的使用寿命和加工效率。
谈到刀具的材质,“Carbide”表示硬质合金,这是数控刀具中常用的材料之一,具有高硬度和耐磨性。
“Ceramic”则是陶瓷,在一些高速切削加工中会用到陶瓷刀具。
“Tool geometry”指的是刀具几何形状,包括刀具的前角(Rake angle)、后角(Relief angle)、刃倾角(Tool cutting edge inclination angle)等。
这些角度的设计会直接影响刀具的切削性能和加工质量。
“Cutting speed”是切削速度,它表示刀具在切削过程中旋转的线速度。
“Feed rate”则是进给速度,即刀具在加工过程中沿工件移动的速度。
“Depth of cut”是切削深度,指的是刀具在一次走刀中切入工件的深度。
在刀具的测量和精度方面,“Tool diameter”表示刀具直径,“Tool length”是刀具长度。
“Tool runout”指的是刀具跳动,它对加工精度有重要影响。
“Tool coating”是刀具涂层,常见的涂层有“TiN coating”(氮化钛涂层)、“TiAlN coating”(氮化铝钛涂层)等,涂层可以提高刀具的耐磨性和切削性能。
UG加工模块中英对照

UG加工模块中英对照mill-planar 平面铣模块平面和垂直侧面,主要加工模具或零件中的平面区域mill-contour 轮廓铣/曲面铣模块可加工存在斜面或是曲面的工件,根据模具或零件的形状进行加工,包括型腔铣加工、等高轮廓铣加工和固定轴区域轮廓铣加工等mill-multi-axis 多轴铣模块在多轴机床上利用工作台的运动和刀轴的旋转实现多轴加工。
Drill 孔加工模块在模具中钻孔,使用的刀具为钻头。
Turning 车加工模块Wire-edm 线切割加工模块在线切割机上利用铜线放电的原理切割零件或模具Solid-tool 铸造加工模块A:-Mill_Planar平面铣1. FACE_MILLING_AREA 面铣削“面铣削区域”有部件几何体、切削区域、壁几何体、检查几何体和自动壁面选择。
2. FACE_MILLING 面铣加工面铣削基本的面切削操作,用于切削实体上的平面。
(适用于平面区域的精加工,使用的刀具多为平底刀)3. FACE_MILLING_MANUAL 面铣削混合切削模式,各个面上都不同。
其中的一种切削模式是手动,它使您能够把刀具正好放在所需的位置,就像教学模式一样。
4. PLANAR_MILL 表面加工平面铣基本的平面铣操作,它采用多种切削模式加工二维边界,以及平底面。
(适用于加工阶梯平面区域,使用的刀具多为平底刀)5.PLANAR_PROFILE 平面铣特殊的二维轮廓铣切削类型,用于在不定义毛坯的情况下轮廓铣。
常用于修边6.ROUGH_FOLLOW 平面铣使用跟随工件切削模式的平面铣。
7.ROUGH_ZIGZAG 平面铣使用往复切削模式的平面铣。
8. ROUGH_ZIG 平面铣使用单向轮廓铣切削模式的平面铣。
9. CLEANUP_CORNERS 平面铣使用来自于前一操作的二维IPW,以跟随部件切削类型进行平面铣。
常用于清除角,因为这些角中有前一刀具留下的材料。
10. FINISH_WALLS 平面铣将余量留在底面上的平面铣。
数控模具加工中的刀具选型与刀具磨削

数控模具加工中的刀具选型与刀具磨削在数控模具加工中,刀具的选型和磨削是非常重要的环节。
合理的刀具选型和精确的刀具磨削可以提高加工效率和产品质量,降低生产成本。
本文将从数控模具加工的特点、刀具选型和刀具磨削技术等方面进行探讨。
一、数控模具加工的特点数控模具加工是利用计算机控制的数控机床进行的模具加工。
相比传统的手工加工和普通机床加工,数控模具加工具有以下特点:1. 高精度要求:模具加工通常需要达到较高的精度要求,以保证模具的质量和加工件的精度。
2. 复杂形状加工:模具通常具有复杂的形状和结构,需要进行多轴、多面、多角度的加工。
3. 加工难度大:模具材料通常较硬,如钢、合金等,加工难度大,对刀具的性能要求高。
二、刀具选型刀具选型是数控模具加工中的关键环节。
合理的刀具选型可以提高加工效率和产品质量。
1. 刀具材料选择:对于模具加工,通常选择硬质合金刀具。
硬质合金刀具具有高硬度、高耐磨性和高热稳定性等特点,适合加工硬材料。
2. 刀具形状选择:根据加工件的形状和结构,选择合适的刀具形状。
常见的刀具形状有平头刀、球头刀、锥度刀等。
3. 刀具刀尖半径选择:刀尖半径的选择直接影响加工表面的质量。
一般情况下,刀尖半径越小,加工表面的质量越好,但同时也会增加刀具的易损性。
4. 刀具刃数选择:刀具刃数的选择要根据具体的加工要求和加工材料来确定。
刃数越多,加工效率越高,但刀具的稳定性和切削力也会增加。
三、刀具磨削技术刀具磨削是刀具维护和修复的重要环节。
合理的刀具磨削技术可以延长刀具的使用寿命,提高加工质量。
1. 磨削工艺选择:根据刀具的不同形状和材料,选择合适的磨削工艺。
常见的磨削工艺有平面磨削、外圆磨削、内圆磨削等。
2. 磨削参数控制:在磨削过程中,控制好磨削参数对于刀具的磨削质量至关重要。
磨削参数包括磨削速度、进给速度、磨削厚度等。
3. 刀具修复技术:对于损坏的刀具,可以通过修复技术进行修复。
常见的刀具修复技术有热处理修复、电火花修复等。
数控机床外文翻译----刀具和刀夹

数控机床外文翻译----刀具和刀夹CUTTING TOOLS AND TOOLHOLDERSTo machine a workpiece successfully you must have :1.the correct kind of cutting tool or tool bit2.the right type of toolholder3.a tool with a sharp cutting-edge4.the cutting tool set or adjusted to the correct height and position.Cutting-tool materialsTool bits used on the lathe are made form one of six basic materials:water-hardening steels,high-speed steels,hard-cast,nonferrous alloys,sintered (cemented) carbides,ceramics,and diamonds. The selection of the material used depends upon many factors including:tool cost,size and design oftool ,metal-removal rate ,length of run ,finish and tolerance of part,and condition and capability of the machine tool . Because of these factors ,material selection is more often based on general experience than on precise evaluation . There are, however ,certain general characteristics of the different cutting-tool materials you should understand.Water-hardening Steels.These include the high-carbon tool steels (either plain carbon or those with minor additions of chromium , vanadium,or tungsten) .The different grades of water-hardening tool steels are classed as W steels in American Iron and Steel Institute’s system of classification . Tools made from these materials have very sharp ,smooth cutting-edges when properlyheat-treated. They are adequate for limited turning at arelatively low cutting speed or when old ,low-speed equipment ,such as a flat-belt lathe , is used .The main limitation of tools made form water-hardening steels is that they soften if the cutting-edge temperature exceeds approximately 300-400F during sharpening or cutting .A second disadvantage is low resistance to edge wear . High-speed Steels. High-speed steels offer great improvement in cutting efficiency over water-hardening tool steels .Tools made from high-speed steels retain enough hardness to machine at rapid rates even when the tool temperature reaches 1050F . They can be used even though they become dull red with heat . Upon cooling to room temperature , the original hardness of these steels does not change .Wear resistance of high-speed steels is much better than that of the carbon or alloy steels . This is due to the high carbide content ,especially in thehigher-alloy types of high-speed steel . Fully hardened , high-speed steels have greater resistance to shock than carbides or hard-cast alloys .There are two main types of high-speed steels designated in the American Iron and Steels Institute system , M steels (molybdenum base and T steels tungsten base . Tool bits made from these materials can be purchased already ground to various shapes . Unground tool bits called tool-bit blanks can also be purchased . These tool-bit blanks are made in standard size to fit the commonly used lathes . The common sizes are 3/16in square by 1 in long ,1/4in square by 2inlong ,5/16in square by 2-1/2in long ,and 3/8in square by 3in long . High-speedsteel tool bits are the type most used in the school machineshop .Hard-cast Alloy . These materials do not contain sufficient iron to be classed as steels . Rather , they are mainly alloys of cobalt , chromium , and tungsten with other elements added for special purpose . They reach full hardness in the as-cast condition , without heat treatment . The must be ground to size after casting . In terms of resistance to heat , wear ,shock ,and initial cost , cast alloys rank between high-speed steels and carbides .Hard-cast alloys are weaker in tension and more brittle than high-speed steels and thus are not suitable for severe shock loads . They are known by such commercial names as stellite , Rex alloy ,and tantung .Sintered Carbides . For efficient and high-speed machining ,best results can be obtained with sintered carbide tools . Carbide tools are available in solid form and as inserts which are either brazed or clamped in toolholders . Clamped inserts are usually round , square , or triangular in shape and have all edge is always available . These inserts can be rotated so that a sharp edge is always available . With modern machine tools and the proper grade of cemented carbide , it is possible to use cutting speeds 10 to 30 time faster than those feasible with high-speed steels .Carbides are suitable for most machining operations such as single-point turning , drilling ,milling , thread cutting, and reaming . Carbides should be used only when they can be supported rigidly and when the machine tool has adequate power and speed to enable their efficient use .Ceramic . With the exception of industrial diamonds , ceramic inserts are the hardest and strongest inserts available . They resistabrasive wear , chipping , and breakage . These inserts work best on very rigid machine tools and onwell-supported workpieces . For most operations , cutting fluids are not needed . Diamonds . Industrial diamonds that have either circular or facetedcutting-edges are used for light finishing cuts when an extremely high-quality surface finish required . Although a very smooth finish can be achieved using other cutting-tool materials , diamond turning can provide even smoother finishes with very small tolerances .TOOLHOLDERSThe toolholder holds the cutting tool rigid during cutting operations . Four types of toolholders are in general use .1 . The tool post with standard toolholders . The tool too post is comprised of the post , screw , washer , collar , and rocker . The washer fits the top slidee piece slot . The collar and the rocker elevate or lower the point of too . The screw clamps the toolholder in place .The standard toolholder for high-speed steel cutter bits comes in three common shapes : straight , right-hand offset or shank , and left-hand offset or shank . You can identify right-hand and left-hand offset holders by holding the setscrew end in your hand . If the shank bends to the right , it is a left-hand offset holder . The straight toolholder is fused for most work . The left-hand toolholder is used when you need to cut close to the chuck or lathe dog . The right-hand holder isused when feeding toward the tailstock of the lathe . The cutting-tool bit is held in each of these toolholders at an angle of 14 to 16.5 degrees . This is called the toolholder angle .Carbide toolholders also come in three styles and are similarin appearance to those mentioned above . The hole for the cutter bit , however , is parallel to the bottom edge of the holder .2. The open-side or heavy-duty tool block holds one tool ata time and consists of a T-slot clamp , a C-shaped block , and two or more tool clamping screws . Because this unit is very rigid , it is especially useful for heavy cuts . A tool bit can be mounted directly in the tool block or some type of carbide tooolholder can be used .3. The turret tool block or four-way toolholder consists of a swiveling block in which the tools are clamped Common turret block hold four tools . Each can be quickly swiveled into cutting position and clamped in place . Some turret blocks have eight tool stations . Frequently ,an open-side-type tool block is also mounted on the rear of the cross slide to add one additional cutting operation . With this arrangement , anywhere form five to nine different kinds of tools can be mounted and operated in sequence for turning , forming ,facing ,knurling , and cutting off duplicate parts .4. The quick-change-type tool system holds only one tool ata time , but three different sides can be used to position the tool . It consists of a quick-change tool post with a clamping lever and a series of toolholders for turning , facing ,boring , cutting off , threading , knurling , and thread cutting .Single-point Cutting ToolsTool Parts . Before you can grind a tool bit , you must become acquainted with some of the terms used to describe the various parts of the cutting tool .1 . The face is the top of the tool bit . It is the surface on which a part of the chip attaches as it is cut away form the workpiece .2. The cutting-edge is that part of the cutter bit which actually does the cutting .3. The nose is the corner or are formed by the side and end cutting-edge .4. The flank is the surface below the cutting-edge .5. The point is the part of the tool bit which is shaped to form the cutting-edge and face .Tool Angles .The following are important tool angles used for all single-point cutting tools .1.The side relief angle is the angle between the ground surface and the verticalside of the tool bit before it is ground . This angle was formerly called side clearance , and many machinists still use this term .The side relief angleprovides clearance between the cut surface of the work and the flank of tool .Tool wear reduces the effective side clearance angle .If the angle is too small, the cutter will rub and heat . If the angle is too large , the cutting-edge will be weak and the tool will have a tendency to dig into the workpiece.2.The end relief angle is the angle formed between the end of the cutting-edgeand a vertical line. It was formerly called front clearance. The end reliefangle provides clearance between the finished surface of the work and the tool. If this angle is too small, the tool will rub on the finished surface and produce a poor finish. Wear tends to reduce this angle. If the angle is too large , the tool may dig into the work , chatter, and fail through chipping . An angle of 8 to 15 is recommened for steel tools and 6 to 8 for carbide tools .If thetool is set above the center of rotation , the effective clearance angle is reduce . This must be considered in choosing the proper angle .3.The end cutting-edge angle provides clearance between the cutter and thefinished surface of the work .If this angle is too small, it may cause chatter. A small angle of about 6 is desirable on light finishing cuts, however, in order to produce a smooth finish .4.The side cutting-edge angle turns the chip away form the finishedsurface .Recommended angles are between 5 and 15 .5.The nose radius removes the fragile corner of the tool , prolongs tool life ,and improves finish . The radius may be large for maximum-strengthrough-cutting tools and may be reduced for light feeds . The larger the nose radius ,the better the finish as long as chatter dose not occur .Recommended nose radii are 0.010 to 0.030 in . or more for finishing cuts , and 1/30 to 1/2 in for roughing cuts .6.To help shape the cutting-edge and face , it is necessary to grind rake angleson a tool bit .Rake is an inclination form the vertical or horizontal .The two rake angles are back rake and side rake .Back rake , in a single-point feeding to the side , turns the chip away form the finished work and gives the tool a slicing action .A zero back rack tends to make a spiral chip , and a back rake angle greater than zero tends to stretch the spiral chip out into a helix . A back-rake angle of form 5 to 15 is used to keep chips form scratching the workpiece . High-speed steel tool bits are always ground with a positive rake .However , cementedcarbide tools may have either a positive or negative rake .Negative rake increases the shear angle at which the chip is formed , providing for a good chip and a good surface finish .Negative rake tools are generally used on a heavy-duty lathe that is operated at high speed with a heavy feed .Side rake refers to the angle between the face of the tool and a line that would represent the top of the unground tool bit as viewed form the end . Side rake controls the type of chip produced during machining as well as the direction in which the chip will travel .A tool with a small side-rake angle will produce shorter chips than one with a large rake angle .7 .The nose angle is the angle between the side-cutting edge and the end-cutting edge .Classes of Single-point T oolsDifferent shapes of tool bits are needed to do certain machining operations . Most tool bits are ground to cut in one direction only .The two common types are referred to as right cut and left cut .These were formerly called right-hand and left-hand tool bits .A right-cut single-point tool is one that , when viewed form the point end with the face up , has its cutting-edge on the right side .When the tool bits is placed in the lathe , the cutting-edge is on the left side .This tool bit cuts form the right to the left , or form the tailstock end toward the headstock of the lathe .A left-cut tool bit has the cutting-edge on the left when viewed form the point end with the face up . This tool bit is ground to cut form the left to the right or toward the tailstock of the lathe .Commonly used types of tool bits include the following:1.A roughing tool is a tool bit designed to take heavyroughing cuts to reducethe diameter of a workpiece to approximate size . Because finish is notimportant when roughing work , such a tool bit may be ground to almost a sharp point . However , the point is usually rounded very slightly to prevent its breaking down .2.A finishing tool is one that has a keenly ground cutting-edge which may behoned with an oilstone to produce a very smooth finish ,A finish toolgenerally has a larger rounded nose than a roughing tool .3.A roundnose cutting tool is a general-purpose tool used for many types ofwork .When ground flat on the top , it can be used for both right and left cuts and for turning brass . It may also be used to form a radius at the corner of a shoulder . Roundnose tool bits are used as finishing tools .4.The square-nose tool cuts on the end only . It is used for chamfering and forroughing cuts to square a shoulder .5.A cutoff or parting tool cuts on the end only and is used for cutting off stockor workpieces held in a chuck .6.Side-facing tools or side tools , as they are often called , are used forfinishing the ends of work square and smooth .A right-cut side-facing tool is always used to finish the end of a shaft . A left-cut side-facing tool may be used to finish the left side of a shoulder .Chip BreakersTo eliminate the problem of a continuous chip , a chip breaker is often ground on a high-speed steel tool bit .Chip breakers can either be ground on an off-hand grinding wheel , or in the case of the grooved chip breaker , it can be done with a thin grinding wheel on a surface grinder .A separate chip breaker is often used with insert-type carbide tools .Cutting ActionIn lathe turning , there are three basic cutting forces , the longitudinal force of the workpiece against the side of the tool , the radial force of the workpiece against the front of tool , and the tangential force of the workpiece against the top of the tool . The tangential cutting force is by far the greatest and has the most influence on the cutting action . This tremendous force is exerted against the cutting-edge . Pressures as great as a quarter-million pounds per square foot have been measured on large metal-cutting lathes . If the tool is shaped incorrectly or set at an incorrect angle ,it will dull rapidly .Here is what actually happens when cutting on the lathe ,As the workpiecemeets the cutting-edge of the tool bit , chips or a continuous ribbon of metal are wedged away from the material being machined ,On soft , ductile material , this wedging is continuous. On harder materials , the wedging force causes the metal to compress . Compression continues until a shearing point is reached , and the compressed metal is separated from the workpiece . This is repeated throughout the cutting operation .The shape is much more important than the actual sharpness of a cutting-edge . Lack of clearance permits the tool to drag on the workpiece , greatly increasing the pressure on the cutting-edge and interfering withtool performance .Too-large clearance angles make the tool weak and do not edge breaks off or wears out rapidly .Grinding a High-speed Steel Tool BitA tool bit is ground:1.To provide a sharp cutting-edge2. To obtain the correct or best shape for a particular operation3. To provide clearance away form the end of the tool bit4. To provide clearance away form the side of the tool bit5. To provide good chip movement over the face of the tool bit and away the cutting-edgeHere is the correct procedure for grinding a right-cut roundnose tool bit :1.Check the grinding wheels to make certain the faces of the wheels aredressed properly. It is difficult to grind good cutting tools on wheels that areuneven or have grooves in them. Use a bench or floor grinder that is used only for grinding cutting tools. Such a grinder should have a coarse-gritaluminum-oxide wheel on one side and a fine-grit wheel on the other side.Use the coarse-grit wheel for finishing the tool bit to shape. Then use thefine-grit wheel for finishing the tool bit.2.The tool grinder should be equipped with tool rests. Rest your hands on themto control the movement of the tool bit. Hold the tool bit firmly to keep itform bouncing around on the wheel. Do not grip it so tightly,however, that you have difficulty move it.3.Grind the side-relief angle to form the side-cutting-edge angle by holding thetool bit against the wheel, as shown in Fig 18. This angle should be about 6 for mild steel. Hold the tool bit against the wheel, and tilt the bottom inward to get this angle. As you grind, move the tool bit back and forth across the face of the wheel without changing its position. This helps to grind the tool faster and prevents grooving the wheel. As the tool bit heats up, dip it inwater to cool it. A beginner often makes the mistake of moving the tool bit up and down. This forms many different angles on the flank, and it becomesvery irregular. To avoid this, hold the tool bit in affixed position on the wheel.Move it back and forth, but never up or down.4.Grind the side-relief angle on the opposite side to form the shape of the toolbit, as shown in.5.To grind the end-relief angle, holds the tool with the and up. Swing the shankof the tool bit in a semicircle. Try to blend the end radius to meet the sides neatly and cleanly. Always ease up on the pressure when grinding theroundnose of the tool bit. If you fail to so this, you woll grind a largerroundnose tool than desired.6.To grind side rake for a right-cut tool bit, hold the tool bit, face or top, atright angles to the right side of the grinding wheel. Tilt thetool inward at the bottom. Hold it in this position until the wheel cleans up the entire face to the cutting-edge. To grind the side-rake angle for a left-cut tool bit, hold the tool bit at the left side of the grinding wheel. Tilt the bottom inward, and let the grinding wheel clean up the entire face to the cutting-edge. There is noreason to grind the face of the tool bit below the shank at the front end. To do so wastes the expensive tool bit and results in a poorly shaped cutting tool.7.It is good practice to hone tool bits used for finishing work. Select amedium-fine oilstone. Apply a little kerosene or lard cutting oil to theoilstone. Move the cutting-edge back and forth against the oilstone. Be sure to hold the bit flat so as not to change any anglesWith a little practice, you will be able to grind a tool bit correctly. Remember, a well-ground bit is one that has proper tool angles together with flat, evenly ground surface.CARE OF LATHESKeep the lathe clean and well lubricated at all times. Like any precision machine, the lathe requires careful treatment. It will operate better and do accurate work as long as you care for it properly. Do not make the mistake of relying upon others to keep the lathe oiled and in good repair. Your own personal safety depends upon your ability to keep the lathe in a safe operating condition. The proper care of a lathe includes such things as cleaning, oiling, adjusting, and making minor repairs.Cleaning the latheClean the lathe thoroughly after each work period. Whenchips and dirt are left on ways, gears, and other moving parts, the surfaces become roughened and dented. This causes fast wear and makes it difficult to operate the parts. The following procedure is recommended for cleaning a lathe:1. Use a brush first to remove all chips.Most chips are razor sharp, so never use your hands.A 2in paintbrush or a small bench brush is convenient for this purpose. Move the tailstock to the right end of the bed.2. Wipe off all painted surfaces with a clean cloth or cotton waste. Oil left on the painted surfaces becomes hardened and steins the paint.3. Using the same cloth or cotton waste, remove oil and grease form all machined surfaces.4. Brush all chips form the chip pan, them wipe it clean.5. Before mounting a chuck, clean its inside threads with a wore thread cleaner. Wipe off the spindle threads, and place a drop or two of oil on them.6. Clean the spindle holes and taper shanks of centers before mounting them in place. If centers have burrs or rough spots on them, use a file or an oilstone to remove them before placing the centers in the spindle holes.7. Occasionally, clean the thread grooves of the lead screw with a piece lf cord. Place the cord around the lead screw. Adjust the gears to turn the lead screw at a medium sped. Start the lathe, and with the lead screw turning, move the cord back end forth as it feeds along the screw.8. When oiling a lathe, wipe off any oil that may spill or drip on the painted surfaces.9. Always make certain there is a light film of oil on the ways before you start to work.10. Adjust the cross-feed and compound slide gib screws to remove looseness or play between the parts. When you can move the cross-feed by grasping the tool post with your hand and moving it back and forth, it means the gib screws are too loose. Adjust each of the gib screws until a smooth movement is obtained on the cross-feed handle. When they are properly adjusted, it will not be possible to move the cross-feed by pulling or pushing on the tool post.11. Never lay tools or workpieces on the ways of a lathe. To do so destroys the accuracy of these precision handscraped surfaces.place your tools on to lathe board.12.When using a tool-post grinder, always protect the machined surfaces of the lathe by covering them. Abrasive particles from the grinding wheel can become imbedded in the surface bearings end soon destroy the accuracy of the lathe if surfaces are not covered during the grinding operation.13. Once a week wipe down the entire lathe with a Clean cloth dampened with kerosene. Do the painted surfaces first, then the machined surfaces. Wipe dry, and place a thin film of clean oil over all machined surfaces.Oiling and Greasing the LatheIt is important that the lathe be properly lubricated. An oiling or lubrication chart comes with each machine. Be sure to use the grades and kinds of oil and grease called for in the chart. Form the habit of oiling your lathe each day before you start work. Certain parts require daily oiling. Other parts should be oiled weekly or monthly as the chart says. Too often, when several persons use the same lathe, each one depends on the other, and the result is that no one does the oiling or maintenance.刀具和刀夹想顺利的加工工件,就必须做到:1.刀具或刀片的种类要恰当。
- 1、下载文档前请自行甄别文档内容的完整性,平台不提供额外的编辑、内容补充、找答案等附加服务。
- 2、"仅部分预览"的文档,不可在线预览部分如存在完整性等问题,可反馈申请退款(可完整预览的文档不适用该条件!)。
- 3、如文档侵犯您的权益,请联系客服反馈,我们会尽快为您处理(人工客服工作时间:9:00-18:30)。
Mould type of numerical control process computer assist the cutter choose and studyForewordNumerical control include cutter production and cutter of orbit choose two key problems process ,. The first problem has been got and studied extensivly and deeply over the past 20 years, a lot of algorithms developed have already got application in commercial CAD/ CAM system. Most CAM systems can produce the cutter orbit automatically after users input relevant parameters at present. Comparatively speaking , it is still not ripe to regard quality , efficiency as the research of choosing the problem of cutter of optimizing the goal correctly, do not have commercial CAM system that can offer the preferred decision support tool of cutter at present, therefore it is difficult to realize the integrating automatically and organically of CAD/ CAM.. The cutter is chosen to usually include cutter type and cutter size. Generally speaking , suitable for one processing cutter of target for much kind , one cutter can finish different processing tasks, so it is easier to only consider meeting the cutter that basically processes the requirement and choose, especially to geometirc characteristics of model such as the hole , trough ,etc.. But in fact, it is common for cutter to choose and sure optimization goal interrelate, for instance most heavy to cut efficiency , process time , minimum process cost , longest service life ,etc. at least, so the cutter is chosen it is a complicated optimization question. Such as mould type one of parts, because the geometirc form is complicated (usually include curved surface of freedom and island), influence geometry that cutter choose it restrains from to be can explicit to say among CAD model, need to design the corresponding algorithm to draw, therefore choose the cutter specification suitable and cutter association , it is not easy things by improving efficiency and quality processed in numerical control.Mould type generally with preparation method that numerical control mill, usually including rough machining, half finish machining , precise process of processing etc.. The principle of rough machining is to spare no effort to remove the surplus metal with high efficiency, therefore hope to choose the larger cutter, but the cutter is oversized, may cause the increase of the crude volume ; Half finish machining of tasks to remove rough machining leave over step that get off mainly; Finish machining mainly guarantees size of the part and surface quality. Consider , go on , select exist , sure by computer difficult automatically totally up till now, therefore assist the cutter to choose in the computer that we developed (Computer Aided Tool Selection , CATS) among the system, base on , provide one aid decision tool for user, rough machining , half finish machining , precise to process etc., the real policy-making power is still left to users, in order to give full play to the advantages of computer and people.1 Basic structure of the systemCATS system is CAD model, output for cutter type , cutter specification , mill depth of sharpening , enter the giving amount , rotational speed of main shaft (cut the pace ) and process six parameters such as time (such as Fig. 1), including choosing the aid decision tool in cutter type, rough machining cutter choose aid decision tool, half finish machining cutter choose aid decision tool and finish machining cutter choose aid decision tool ,etc.Given the rough machining in Xingqiang processing of the important position (usually rely time 5~10 times), rough machining, the system automatically optimize portfolio with cutlery functions to enhance overall processing efficiency. In addition to the decision-making tools, the system also has a detailed look cutlery norms, based on the type and size cutlery recommended processing parameters and assess the function of processing time, the last generation of the overall results of choice cutlery statements (figure 2). All the data and knowledge systems cutlery done by the background database support.2Key technologies and algorithms2.1C utlery type choiceAccording to Assistant Xingqiang digital processing practice, Xingqiang Xi state general processing cutlery into milling cutter, milling cutter radius milling cutter and the first three balls. D based cutlery diameter, radius radius r when r=0 for milling cutter, 0<RCutlery can be divided into the overall style and embed films ceremony. For inlay film style, the key is to select the materials razor blades, razor blades materials choice depends on three elements : the processing of working materials, machine tools and cutlery jig stability of the state structures. Processing system will be translated into material steel, stainless steel, cast iron, nonferrous metals, materials and hard to cut materials six groups. Machine tool jig stability into good, better and less than three levels. Cutlery investigation into the short and long cantilever structures two, the system automatically reasoning on the basis of the specific circumstances of razor blades materials, decision-making knowledge from Walter cutlery manual system by the users first choice cutlery type in the world. To embed film style cutlery, a rules-based automated reasoning suitable razor blades materials. For example, if the final processing of materials for the "steel", machine tool jig for good stability, cutlery cantilever structures for short, razor blades materials for W AP25.Rough machining cutlery portfolio optimizationXingqiang rough machining the aim is to maximize the removal of excess metal normally used milling cutter, take-cutting approach. Thus, 3D mould Xingqiang the rough machining process, is actually a series of 2.5D components Xingqiang processing. Cutlery optimization is to find a group of cutlery portfolio, allowing for maximum efficiency removal of most metals. Cutlery portfolio optimized basic methods as follows :A.To do some long step into knife in the direction of a group of vertical and horizontal search Xingqiang another entity to form a search layer.B.Derive closed to the contours.C.Calculated between Central and outside the island or islands andthe distance between the key that affect cutlery choice geometric constraints algorithm flow As shown in figure 3D.According to the principle of the merger (adjacent to the critical distance will be smaller than the difference between the threshold) to search layer merger, graphic processing and identifying viable cutlery sets, a processing layer.E.Determine the use of each processing layer cutlery, cutlery Xingqiang processing portfolio.F.According cutlery recommended processing parameters (cutting speed, depth and into Xianxiao to speed), the calculation of material removal.G.According to the actual removal of the volume processing layer, the processing time for each processing layer.H.Xingqiang calculating the total processing time and residual volume.I.The overall portfolio of the Group cutlery processing efficiency assessment.J . Repeat a~i until derive optimal mix of cutlery. If time is the goal, called for the entire processing time t Xingqiang shortest portfolio to optimize cutlery.2.2Semi-finished cutlery choiceThe main purpose is to remove semi-finished rough machining residual contours of the new warrants. To completely remove height, depth must be greater than Xianxiao parts of each level to the surface distance x. Its algorithm steps are as follows :Step 1:entity models from parts of two adjacent to the cross section of the surface contours and the corresponding length;Step 2: The average length of contours;Step 3:calculate its width;Step 4 : calculating height floor to the surface of parts to the law distance x; Step 5 : steps 1~ repeat steps 4, each level of decision Xianxiao depth;Step 6 : calculate cutlery diameter D, by or under cutlery experience D=x/0.6manual recommended;steps7 : choose Xianxiao x depth than the smallest cutlery.2.3fine cutlery choiceFine cutlery choice is the basic principle : cutlery parts surface radius smaller than the smallest size R curve radius r, the general admission R= (0.8~0.9) r. Its algorithm steps are as follows :Step 1 : from the smallest curve radius calculation model parts entities;Step 2 : From cutlery database search radius of less than a cutlery calculated radius of the curve all cutlery;Step 3 : select the best cutlery meet the above requirements;Step 4 : If all cutlery than the smallest curve radius, the smallest chosen as a recommended cutlery.4 summary and discussionMould type of craft of processing plan , need high technology and experience very usually, prepare NC time of data nearly and process time to be large. So person who produce of craft of processing plan and NC process demand of the order right away seem further more urgent automatically.This text system research mould type of craft cutter plan , choose problem, put forward mould of rough machining , half finish machining , finish machining principle and method that cutter chooses, the realization algorithm with corresponding structure , and has carried on the realization of preliminary programming under the environment of UG/OPEN API, have developed CATS prototype system. In cutter type and on the foundation that the specification is fixed, system also can recommend parameter of processing according to cutter manual (cut pace , mill , sharpen depth , enter person who give ,etc.), evaluate corresponding processing time. Final purpose its to realize integration of CAD/CAM really , produce through aftertreatment numerical control process the order.Need to point out , should improve the mould type totality of and process efficiency, need it from the rough machining , half finish machining , consideration on the whole of finish machining , make up and optimize manytargets, this will be work that we want to carry on nex模具型腔数控加工计算机辅助刀具选择和研究引言数控加工中包括刀具轨迹的产生和刀具选择两个关键问题。