加工工艺点检表
工艺纪律检查表

5
3.工装夹具是否定期保养?是否按工艺文件对其进行检查清理?
1.没有定期保养记录
2.没有检查清理记录
5
4.量具、检具、仪表等是否有校验标识?是否超期使用?
现场没有量具
3
生产
51是否按要ຫໍສະໝຸດ 进行自检,检验方法是否正确?有自检(没有核对自检记录)
5
2.是否进行了首检?
有首检(没有核对首检记录)
5
3.出现不合格时的流程是否熟悉?
熟悉不合格品流程
5
4.操作员工是否按照工艺文件操作,操作是否规范?
实际使用自动装夹设备,但文件描述使用旧工装手动装夹
4
物流
5
1.物料是否有标识?是否填写产品流转卡?产品区域是否清楚不易混料?
1物料有标识;
2没有产品流转卡
3.产品区域清楚
5
2.产品区域是否清楚并不易混料?
5
3.工艺文件是否符合现场加工?是否有指导性?
实际使用自幼装夹设备,但文件描述使用旧工装手动装夹
5
4.作业流程是否清楚?
清楚
5
5.生产记录单是否记录规范、正确?
没有生产记录单
2
备装具设工检
5
1.设备是否按规定进行定期维护和点检?是否每日点检和记录?
没有每日点检记录,没有其他记录
5
2.设备是否悬挂操作规程?
工艺纪律检查表
被检查班组:被检查工位:检查人:检查时间:
序号
检查项目
标准分
检查内容
检查结果
被检查人
实得分
1
文件资料
5
1.是否悬挂有效工艺文件或图纸?是否完好清晰?是否理解和被执行?
生产工装管理要求点检表(TS16949要求))
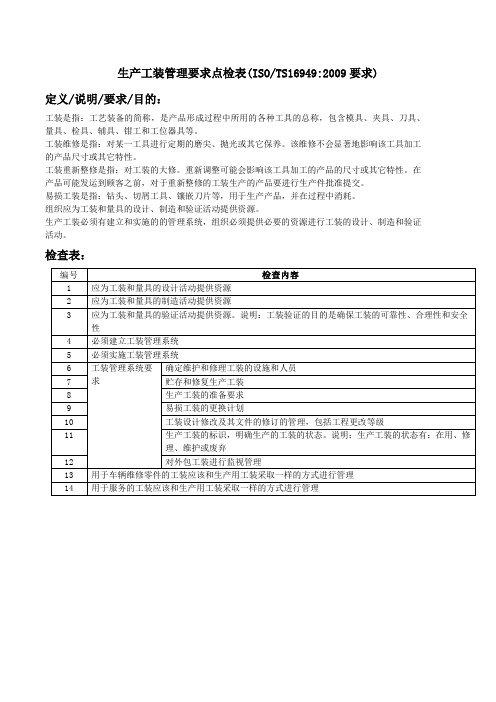
生产工装管理要求点检表(ISO/TS16949:2009要求)
定义/说明/要求/目的:
工装是指:工艺装备的简称,是产品形成过程中所用的各种工具的总称,包含模具、夹具、刀具、量具、检具、辅具、钳工和工位器具等。
工装维修是指:对某一工具进行定期的磨尖、抛光或其它保养。
该维修不会显著地影响该工具加工的产品尺寸或其它特性。
工装重新整修是指:对工装的大修。
重新调整可能会影响该工具加工的产品的尺寸或其它特性。
在产品可能发运到顾客之前,对于重新整修的工装生产的产品要进行生产件批准提交。
易损工装是指:钻头、切屑工具、镶嵌刀片等,用于生产产品,并在过程中消耗。
组织应为工装和量具的设计、制造和验证活动提供资源。
生产工装必须有建立和实施的的管理系统,组织必须提供必要的资源进行工装的设计、制造和验证活动。
检查表:。
《工艺纪律检查表》
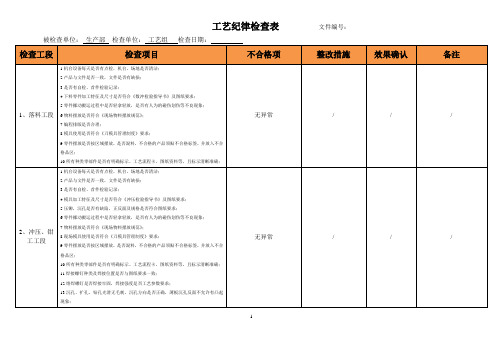
被检查单位:生产部检查单位:工艺组检查日期:
检查工段
检查项目
不合格项
整改措施
效果确认
备注
1、落料工段
1.机台设备每天是否有点检,机台、场地是否清洁;
2.产品与文件是否一致,文件是否有缺损;
3.是否有自检、首件检验记录;
4.下料零件加工特征及尺寸是否符合《数冲检验指导书》及图纸要求;
5.零件挪动搬运过程中是否轻拿轻放,是否有人为的碰伤划伤等不良现象;
6.物料摆放是否符合《现场物料摆放规范》;
7.编程排版是否合理;
8.模具使用是否符合《刀模具管理制度》要求;
9.零件摆放是否按区域摆放,是否混料,不合格的产品须贴不合格标签,并放入不合格品区;
10.所有种类零部件是否有明确标示、工艺流程卡、图纸资料等,且标示清晰准确;
7.物料摆放是否符合《现场物料摆放规范》;
8.现场模具使用是否符合《刀模具管理制度》要求;
9.零件摆放是否按区域摆放,是否混料,不合格的产品须贴不合格标签,并放入不合格品区;
10.所有种类零部件是否有明确标示、工艺流程卡、图纸资料等,且标示清晰准确;
11.焊接螺钉种类及焊接位置是否与图纸要求一致;
12.熔焊螺钉是否焊接牢固,焊接强度是否工艺参数要求;
无异常
/
/
/
6、装配工段
1.流水线设备及工具每天是否有点检,机台、场地是否清洁。
2.生产产品与文件是否一致,文件是否有缺损,且技术资料是否为最新版本。
3.是否有自检、首件检验记录。
4.是否有区域规划,零件摆放是否按区域摆放,零件是否有保护,物料摆放是否有标识,标识是否准确。
5.电镀产品是否戴手套操作。
工序检查表

标段工程师 :
年月日
工程项目名称:
模板安装工程质量检查验收表
施工单位:
验收部位:施工ຫໍສະໝຸດ 量检查项目检 查 内 容检查情况
检查人
1
模板支承体系必须按照相关技术要求设置
2
出现高支模情况,必须按所报高支模方案实施
3
模板和支架完好,清理干净,起皮和变形模板不得使用
4
模板拼装顺序:后拆的先支,先拆的后支
14
高压水枪试水
30~45min
监理(建设)单位验收结论
标段工程师 :
年月日
工程项目名称:
模板分项工程复线、测量检查验收表
施工单位:
检查部位:
检查项目
检 查 内 容
检查情况
检查人
1
轴线位置
2
底模上表面标高
3
截面内部尺寸
柱、梁、墙
4
层高垂直度
不大于
5M
大于5M
5
相邻两表板
表面高低差
6
表面平整度
7
每五层检查层高及垂直度
吊模、边模加固及顺直
14
结构施工图中的反梁和飘窗模板平面位置及标高检查
监理(建设)单位
验收结论
标段工程师:
年月日
5
模板拼缝是否符合相关技术
要求
6
避免隔离剂沾污
7
检查柱模垂直度、梁侧模垂直度符合相关技术要求
8
检查梁、板底模标高 是否符合相关技术要求
9
检查梁、墙柱轴线定位是否符合相关技术要求
10
柱模的拉紧螺栓、木方箍等设置间距是否符合相关技术
11
柱模根处是否设置清扫口是否订压脚板
工厂过程工艺检查表
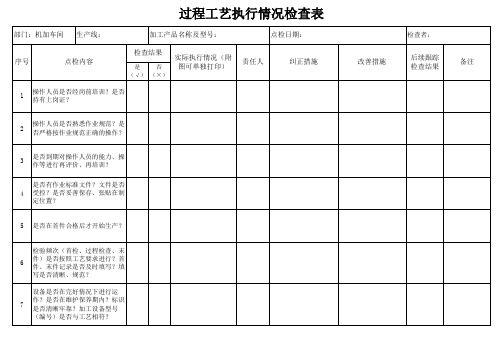
3
是否到期对操作人员的能力、操 作等进行再评价、再培训? 是否有作业标准文件?文件是否 受控?是否妥善保存、张贴在制 定位置?
4
5
是否在首件合格后才开始生产?
6
检验频次(首检、过程检查、末 件)是否按照工艺要求进行?首 件、末件记录是否及时填写?填 写是否清晰、规范? 设备是否在完好情况下进行运 作?是否在维护保养期内?标识 是否清晰牢靠?加工设备型号 (编号)是否与工艺相符?
过程工艺执行情况检查表
部门:机加车间 生产线: 加工产品名称及型号: 检查结果 序号 点检内容
是 否 (√) (×)
点检日期:
检查者:
实际执行情况(附 图可单独打印)
责任人
纠正措施
改善措施
后续跟踪 检查结果
备注
1
操作人员是否经岗前培训?是否 持有上岗证?
2
操作人员是否熟悉作业规范?是 否严格按作业规范正确的操作?
7
8
工具是否摆放至指定位置?
9
在线产品是否定置、定量管理? 待、已加工产品是否摆放至指定 位置?产品是否采取防护措施? 废弃物、废料是否放在指定位 置?是否及时处理?
10
11
不合格品(不良品)标识是否明 确?是否及时处理? 在线量具、检具是否完好、齐 全?是否在合格期内使用?是否 放在指定位置? 卡盘夹持力是否与工艺要求相 符?
12
13
14
工装夹具是否与工艺要求相பைடு நூலகம்?
15
走刀路线、走刀次数、进给量是 否与工艺要求相符?
16
刀体、刀片型号是否与工艺要求 相符?
17
刀具更换频次是否与工艺要求相 符?是否及时记录?
备注:1、每周现场技术员、质量工程师车间主任对机加现场工艺执行情况进行检查,每周一次;2、点检不符合内容传责任单位限期整改。
机器加工分层审核检查清单表格模板(可修改)
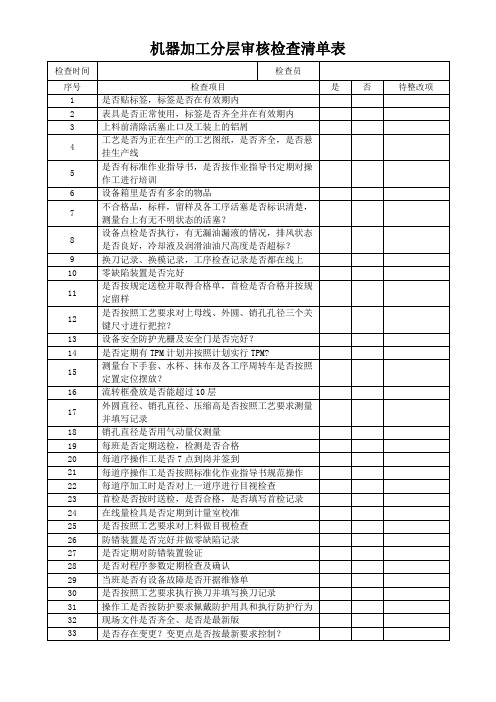
检查时间
检查员
序号
检查项目
是
否
待整改项
1
是否贴标签,标签是否在有效期内
2
表具是否正常使用,标签是否齐全并在有效期内
3
上料前清除活塞止口及工装上的铝屑
4
工艺是否为正在生产的工艺图纸,是否齐全,是否悬挂生产线
5
是否有标准作业指导书,是否按作业指导书定期对操作工进行培训
6
设备箱里是否有多余的物品
20
每道序操作工是否7点到岗并签到
21
每道序操作工是否按照标准化作业指导书规范操作
22
每道序加工时是否对上一道序进行目视检查
23
首检是否按时送检,是否合格,是否填写首检记录
24
在线量检具是否定期到计量室校准
25
是否按照工艺要求对上料做目视检查
26
防错装置是否完好并做零缺陷记录
27
是否定期对防错装置验证
13
设备安全防护光栅及安全门是否完好?
14
是否定期有TPM计划并按照计划实行TPM?
15
测量台下手套、水杯、抹布及各工序周Leabharlann 车是否按照定置定位摆放?16
流转框叠放是否能超过10层
17
外圆直径、销孔直径、压缩高是否按照工艺要求测量并填写记录
18
销孔直径是否用气动量仪测量
19
每班是否定期送检,检测是否合格
7
不合格品,标样,留样及各工序活塞是否标识清楚,测量台上有无不明状态的活塞?
8
设备点检是否执行,有无漏油漏液的情况,排风状态是否良好,冷却液及润滑油油尺高度是否超标?
9
换刀记录、换模记录,工序检查记录是否都在线上
模具验收点检表
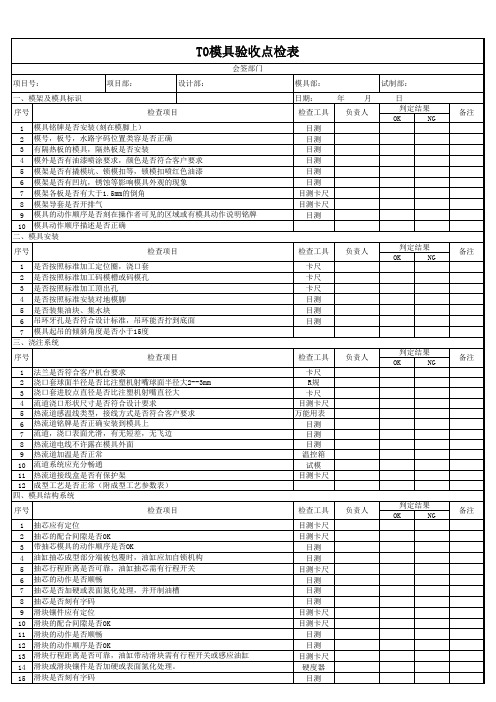
八、液压、电子、控制
T0模具验收点检表
会签部门 项目号: 一、模架及模具标识 序号 检查项目 项目部: 设计部: 模具部: 日期: 检查工具 目测 目测 目测 目测 目测 目测 目测卡尺 目测卡尺 目测 年 月 负责人 试制部: 日 判定结果 OK NG
备注
1 模具铭牌是否安装(刻在模脚上) 2 模号,板号,水路字码位置类容是否正确 3 有隔热板的模具,隔热板是否安装 4 模外是否有油漆喷涂要求,颜色是否符合客户要求 5 模架是否有撬模坑、锁模扣等,锁模扣喷红色油漆 6 模架是否有凹坑,锈蚀等影响模具外观的现象 7 模架各板是否有大于1.5mm的倒角 8 模架导套是否开排气 9 模具的动作顺序是否刻在操作者可见的区域或有模具动作说明铭牌 10 模具动作顺序描述是否正确 二、模具安装 序号 检查项目
检查工具 目测卡尺 目测卡尺 目测 目测 目测卡尺 目测 目测 目测 目测卡尺 目测卡尺 目测 目测 目测卡尺 硬度器 目测
负责人
判定结果 OK NG
备注
16 斜顶配合间隙是否OK 17 斜顶胶位面应抛光,斜顶顶面低于型芯面 18 斜顶的动作是否顺畅 19 斜顶是否刻有字码 20 模具镶件的配合间隙是否OK 21 模具镶件是否需要加硬或表面氮化处理 22 顶块配合间隙是否OK 23 顶块是否需要加硬或表面氮化处理 24 顶块是否刻有字码 25 各活动部件压条、耐磨片是否加硬处理并开制油槽 26 各导向块、导向座是否加硬或表面氮化处理 27 各装配零部件是否有字码,周边非成型边倒C角 28 所有螺牙长度是否有1.5倍螺丝直径 29 大滑块,镶件,抽芯是否有吊装螺孔 五、顶出系统 序号 1 2 3 4 5 6 7 8 检查项目 顶针与滑块是否干涉,有干涉的是否有先复位机构,是否安装行程开关 顶出时应顺畅、无卡滞、无异常声响。 顶出距离应用限位块进行限位。 所有顶杆、顶块应有止转定位,每个顶杆、顶块都应进行编号,顶杆, 顶块不应上下串动 顶杆上加倒钩,倒钩的方向应保持一致,倒钩易于从制品上去除 顶杆孔与杆的配合间隙,封胶段长度,顶杆孔的表面粗糙度应符合客户要求 制品顶出时易跟着斜顶走,顶杆上应加槽或蚀纹 固定在顶杆上的顶块,应牢固可靠,四周非成型部分应加工3-5°的斜面, 下底部周边倒角
PCB点检表(增加工艺审查)

PCB点检表设计规范的附录A兀器件种类及名称文字符号兀器件种类及名称文字符号变压器T 接触器KM测试点(焊盘) TP 晶体振荡器、谐振器Y插头、插座J 开关S电池GB 滤波器Z电感器、磁珠L 模块电源MP电容器 C 熔断器FU电阻器R 三极管Q电位器RP 二极管、稳压二极管 D排阻RR 发光二极管DL热敏电阻RT 指示灯HL压敏电阻RV 继电器K蜂鸣器VD 集成电路、三端稳压块U光耦ISO TVS管TVS跳线器、拨码开关JUMP 数码管LVDS电流互感器CT 电压互感器PT设计规范的附录B器件间距要求PLCG QFR SOP各自之间和相互之间间隙》2.5mm( 100mil )。
PLCC QFP SOP与 Chip、SOT之间间隙 >1.5mm (60mil )回流焊:Chip、SOT各自之间和相互之间的间隙可以小至0.3mm(12mil)。
波峰焊:Chip、SOT相互之间的间隙 R8mm(32mil )和 1.2mm (47mil ),钽电容在前面时,间隙应 >2.5mm (100mil )。
见下图:BGA外形与其他元器件的间隙 >5mm(200mil )PLCC表面贴转接插座与其他元器件的间隙>3mrm( 120mil )。
表面贴片连接器与连接器之间应该确保能够检查和返修。
一般连接器引线侧应该留有比连接器高度大的空间。
元件到喷锡铜带(屏蔽罩焊接用)应该 2mm(80mil)以上。
元件到拼板分离边需大于1mm(40mil)以上。
如果B面(焊接面)上贴片元件很多、很密、很小,而插件焊点又不多,建议插件引脚离开贴片元件焊盘 5mm 以上,以便可以采用掩模夹具进行局部波峰焊。
注:其中间隙一般指不同元器件焊盘间的间隙,器件体大于焊盘时,指器件体的间隙)设计规范的附录C丝印字符大小参考值)设计规范的附录F 器件封装制作要求器件封装制作要求:。