感应加热表面淬火.
感应淬火设备原理
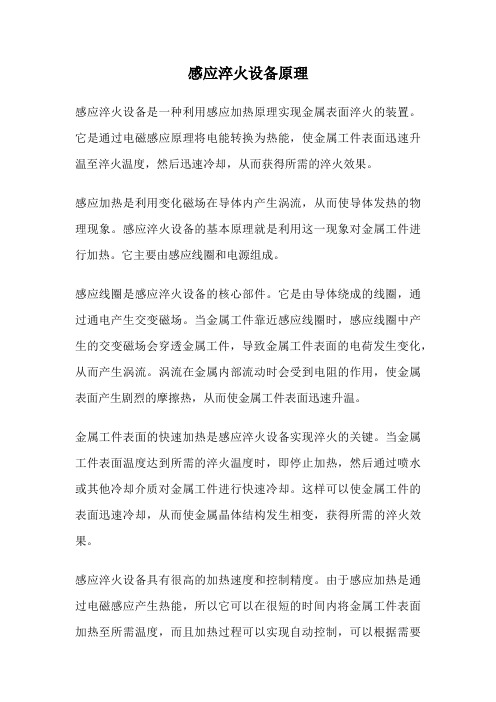
感应淬火设备原理感应淬火设备是一种利用感应加热原理实现金属表面淬火的装置。
它是通过电磁感应原理将电能转换为热能,使金属工件表面迅速升温至淬火温度,然后迅速冷却,从而获得所需的淬火效果。
感应加热是利用变化磁场在导体内产生涡流,从而使导体发热的物理现象。
感应淬火设备的基本原理就是利用这一现象对金属工件进行加热。
它主要由感应线圈和电源组成。
感应线圈是感应淬火设备的核心部件。
它是由导体绕成的线圈,通过通电产生交变磁场。
当金属工件靠近感应线圈时,感应线圈中产生的交变磁场会穿透金属工件,导致金属工件表面的电荷发生变化,从而产生涡流。
涡流在金属内部流动时会受到电阻的作用,使金属表面产生剧烈的摩擦热,从而使金属工件表面迅速升温。
金属工件表面的快速加热是感应淬火设备实现淬火的关键。
当金属工件表面温度达到所需的淬火温度时,即停止加热,然后通过喷水或其他冷却介质对金属工件进行快速冷却。
这样可以使金属工件的表面迅速冷却,从而使金属晶体结构发生相变,获得所需的淬火效果。
感应淬火设备具有很高的加热速度和控制精度。
由于感应加热是通过电磁感应产生热能,所以它可以在很短的时间内将金属工件表面加热至所需温度,而且加热过程可以实现自动控制,可以根据需要对加热时间和温度进行精确控制。
这使得感应淬火设备在工业生产中得到广泛应用。
感应淬火设备在金属加工行业有着重要的应用价值。
它可以提高金属零件的硬度和耐磨性,改善其力学性能和表面质量,延长使用寿命。
特别是对于大型和复杂形状的工件,感应淬火设备具有独特的优势,可以实现对工件表面的局部加热,避免了整体加热带来的变形和损坏。
感应淬火设备利用感应加热原理实现金属表面淬火,通过电磁感应产生的交变磁场使金属工件表面迅速加热至淬火温度,然后通过快速冷却获得所需的淬火效果。
它具有加热速度快、控制精度高等优点,在金属加工行业得到广泛应用。
感应加热淬火热处理

感应加热淬火热处理一、引言感应加热淬火热处理是一种常见的金属材料加工技术,它通过感应加热将金属材料加热到高温状态,然后迅速冷却以改变其物理和化学性质。
该技术广泛应用于汽车、航空航天、机械制造等领域,以提高材料的硬度、强度和耐腐蚀性能。
二、感应加热原理感应加热是一种非接触式电磁加热方式,其原理是利用高频电流在金属导体内产生涡流,并使导体内部发生自发加热。
感应加热设备由高频电源、线圈和工件组成。
高频电源将交流电转换成高频电流,线圈将高频电流传递到工件中,工件在涡流作用下发生自发加热。
三、淬火原理淬火是指将金属材料从高温状态迅速冷却以改变其物理和化学性质的过程。
淬火可使钢材表面形成硬度较高的马氏体组织,并增强钢材的强度和耐腐蚀性能。
淬火过程中,金属材料的温度迅速下降,导致其组织结构发生相变。
淬火介质通常为水、油或空气。
四、感应加热淬火工艺感应加热淬火工艺是将感应加热和淬火技术结合起来的一种金属材料加工方式。
该工艺通常分为以下几个步骤:1. 准备工作:对待处理的金属材料进行清洗、去除表面污垢和氧化物等预处理。
2. 加热:将待处理的金属材料放置在感应加热设备中,通过高频电流产生涡流并使其自发加热到所需温度。
3. 保温:在达到所需温度后,保持一定时间使其均匀受热并达到稳定状态。
4. 淬火:在保温结束后,将金属材料迅速浸入淬火介质中进行冷却。
淬火介质的选择取决于待处理材料的类型和要求。
5. 清洗:将已经淬火完成的金属材料从淬火介质中取出,并进行清洗以去除表面污垢和残留的淬火介质。
6. 回火:在淬火后,金属材料的硬度较高,容易产生裂纹和变形。
因此,需要进行回火处理以消除内部应力和改善其塑性。
五、应用领域感应加热淬火工艺广泛应用于汽车、航空航天、机械制造等领域。
在汽车制造中,感应加热淬火技术常用于制造发动机零部件、传动轴和齿轮等;在航空航天领域,该技术则用于制造高强度金属材料的部件;在机械制造中,感应加热淬火技术可提高钢材的硬度和强度,以满足不同工作环境下的使用要求。
感应加热表面淬火
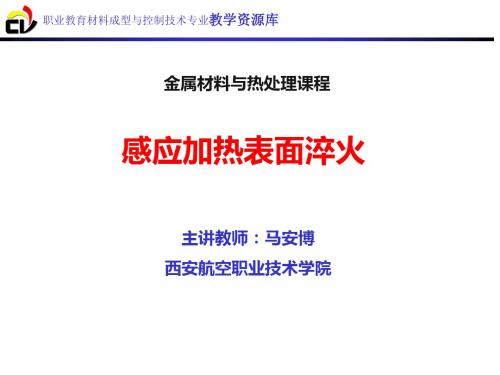
感应加热表面淬火原理
零件处于交变磁场(感应线圈产生)中产
生涡流,从而产生热量(零件阻抗通电流产生
的热量)使零件被加热,随后冷却淬火。
感应加热频率越高,淬硬层越浅,但加热 速度越快。
金属材料与热处理
职业教育材料成型与控制技术专业教学资与控制技术专业教学资源库
金属材料与热处理
职业教育材料成型与控制技术专业教学资源库
金属材料与热处理课程
感应加热表面淬火
主讲教师:马安博 西安航空职业技术学院
职业教育材料成型与控制技术专业教学资源库
感应加热表面淬火
感应加热表面淬火定义
利用交变电流在工件表面感应巨大涡流,
使工件表面迅速加热的方法。
金属材料与热处理
职业教育材料成型与控制技术专业教学资源库
感应加热表面淬火分类
加热方法 频率(KHz)
功率密度 (102W×cm-2) 0.1~1
<5 2~10 100~300
工频
中频 高频、超音频 超高频脉冲
50
<10 20~1000 27120
金属材料与热处理
职业教育材料成型与控制技术专业教学资源库
感应加热表面淬火特点
加热速度快,热效率高达60%以上,生产率高; 产品质量高,工件变形小,不易氧化及脱碳; 易实现批量产品的机械化和自动化,无污染; 设备投资大,不适于复杂形状零件和小批量生产。
感应加热表面淬火方法
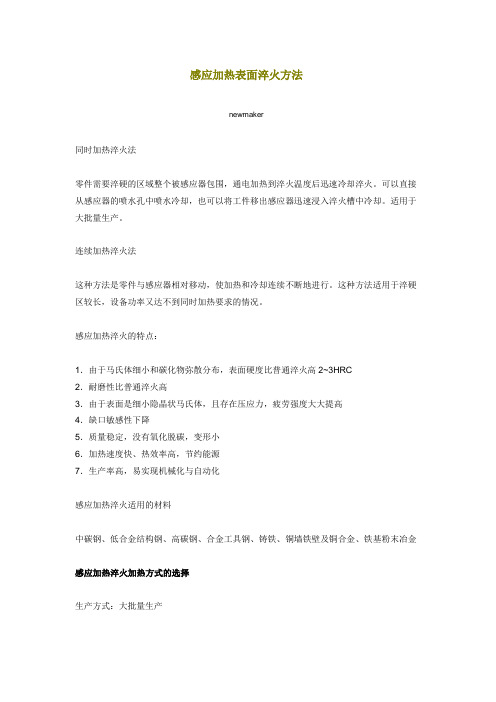
感应加热表面淬火方法
newmaker
同时加热淬火法
零件需要淬硬的区域整个被感应器包围,通电加热到淬火温度后迅速冷却淬火。
可以直接从感应器的喷水孔中喷水冷却,也可以将工件移出感应器迅速浸入淬火槽中冷却。
适用于大批量生产。
连续加热淬火法
这种方法是零件与感应器相对移动,使加热和冷却连续不断地进行。
这种方法适用于淬硬区较长,设备功率又达不到同时加热要求的情况。
感应加热淬火的特点:
1.由于马氏体细小和碳化物弥散分布,表面硬度比普通淬火高2~3HRC
2.耐磨性比普通淬火高
3.由于表面是细小隐晶状马氏体,且存在压应力,疲劳强度大大提高
4.缺口敏感性下降
5.质量稳定,没有氧化脱碳,变形小
6.加热速度快、热效率高,节约能源
7.生产率高,易实现机械化与自动化
感应加热淬火适用的材料
中碳钢、低合金结构钢、高碳钢、合金工具钢、铸铁、铜墙铁壁及铜合金、铁基粉末冶金
感应加热淬火加热方式的选择
生产方式:大批量生产
同时加热:工件淬火加热表面积与比功率的乘积≤设备功率时采用
连续加热:工件淬火加热表面积与比功率的乘积>设备功率时采用
生产方式:小批,单件生产
同时加热:在满足工件淬火加热表面积与比功率的乘积≤设备功率的条件下,视工件形状酌情选用
连续加热:
轴类、杆类及尺寸较大平面加热淬火时采用
工件淬火加热表面积与比功率的乘积>设备功率时采用(end)。
感应加热表面淬火基本原理
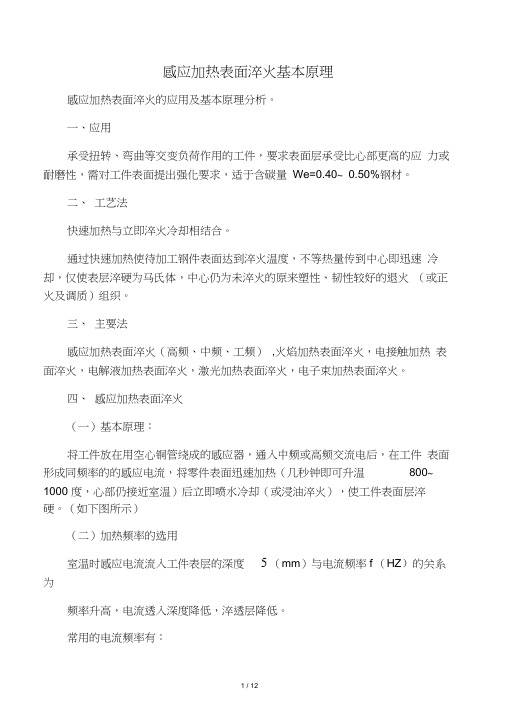
感应加热表面淬火基本原理感应加热表面淬火的应用及基本原理分析。
一、应用承受扭转、弯曲等交变负荷作用的工件,要求表面层承受比心部更高的应力或耐磨性,需对工件表面提出强化要求,适于含碳量We=0.40~ 0.50%钢材。
二、工艺法快速加热与立即淬火冷却相结合。
通过快速加热使待加工钢件表面达到淬火温度,不等热量传到中心即迅速冷却,仅使表层淬硬为马氏体,中心仍为未淬火的原来塑性、韧性较好的退火(或正火及调质)组织。
三、主要法感应加热表面淬火(高频、中频、工频),火焰加热表面淬火,电接触加热表面淬火,电解液加热表面淬火,激光加热表面淬火,电子束加热表面淬火。
四、感应加热表面淬火(一)基本原理:将工件放在用空心铜管绕成的感应器,通入中频或高频交流电后,在工件表面形成同频率的的感应电流,将零件表面迅速加热(几秒钟即可升温800~ 1000 度,心部仍接近室温)后立即喷水冷却(或浸油淬火),使工件表面层淬硬。
(如下图所示)(二)加热频率的选用室温时感应电流流入工件表层的深度 5 (mm)与电流频率f (HZ)的关系为频率升高,电流透入深度降低,淬透层降低。
常用的电流频率有:1、高频加热:100〜500KHZ常用200〜300KHZ为电子管式高频加热,淬硬层深为0.5〜2.5mm,适于中小型零件。
2、中频加热:电流频率为500〜10000HZ 常用2500〜8000HZ 电源设备为机械式中频加热装置或可控硅中频发生器。
淬硬层深度〜10m m。
适于较大直径的轴类、齿轮等。
3、工频加热:电流频率为50H乙采用机械式工频加热电源设备,淬硬层深可达10〜20mm,适于大直径工件的表面淬火。
(三)、感应加热表面淬火的应用与普通加热淬火比较具有:1、加热速度极快,可扩大A 体转变温度围,缩短转变时间。
2、淬火后工件表层可得到极细的隐晶马氏体,硬度稍高(2〜3HRC。
脆性较低及较高疲劳强度。
3、经该工艺处理的工件不易氧化脱碳,甚至有些工件处理后可直接装配使用。
感应加热表面淬火进行加工处理的工艺路线
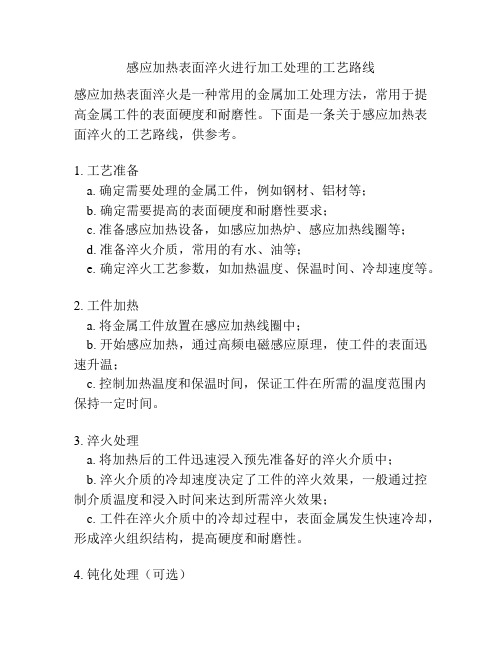
感应加热表面淬火进行加工处理的工艺路线
感应加热表面淬火是一种常用的金属加工处理方法,常用于提高金属工件的表面硬度和耐磨性。
下面是一条关于感应加热表面淬火的工艺路线,供参考。
1. 工艺准备
a. 确定需要处理的金属工件,例如钢材、铝材等;
b. 确定需要提高的表面硬度和耐磨性要求;
c. 准备感应加热设备,如感应加热炉、感应加热线圈等;
d. 准备淬火介质,常用的有水、油等;
e. 确定淬火工艺参数,如加热温度、保温时间、冷却速度等。
2. 工件加热
a. 将金属工件放置在感应加热线圈中;
b. 开始感应加热,通过高频电磁感应原理,使工件的表面迅速升温;
c. 控制加热温度和保温时间,保证工件在所需的温度范围内保持一定时间。
3. 淬火处理
a. 将加热后的工件迅速浸入预先准备好的淬火介质中;
b. 淬火介质的冷却速度决定了工件的淬火效果,一般通过控制介质温度和浸入时间来达到所需淬火效果;
c. 工件在淬火介质中的冷却过程中,表面金属发生快速冷却,形成淬火组织结构,提高硬度和耐磨性。
4. 钝化处理(可选)
a. 钝化处理主要是为了增强工件的耐腐蚀性能;
b. 钝化处理一般使用酸洗、电解等方法进行,可以去除表面
氧化层,并形成一层致密的钝化膜。
5. 适当退火
a. 对于部分工件,可能需要进行适当的退火处理以减轻应力、改善材料的硬度和韧性;
b. 退火温度和时间根据工件材料进行选定。
在实际的工艺操作过程中,还需要根据具体的工件材料、要求和实际情况进行调整和控制。
感应加热表面淬火工艺路线可以根据不同的加工需求进行相应的优化和改进,以达到更好的处理效果和工件性能提升。
高频感应加热表面淬火-验证
高频感应加热表面淬火一、实验目的1、了解感应加热的原理;2、了解电流透入深度与材料电阻率及电流频率之间的关系;3、了解淬硬层深度的测定方法;4、掌握高频感应加热淬火的方法。
二、实验原理1.电磁感应当感应线圈通以交流电时,在感应线圈的内部和周围同时产生与电流频率相同的交变磁场,将工件置于高频感应线圈内,受电流交变磁场的作用,在工件内相应地产生感应电流,这种感应电流在金属工件内自行闭合,称为涡流。
其感应电动势瞬时值为:τφd d K e -=式中,K-比例系数;ф-工件上感应电流回路包围面积上的总磁通;d ф/d τ-磁通量变化率;负号表示感应电动势方向与磁通量变化率方向相反。
工件中感应出来的涡流方向,在每一瞬时和感应线圈中的电流方向相反。
涡流强度I f 取决于感应电动势(e)及工件涡流回路的电抗(Z),而电抗Z 由电阻R 和感抗(X L )组成,则涡流强度:22Lf X R e Ze I +== 2.表面效应涡流强度I f 随高频电磁场强度由工件表面向内层逐渐减小而相应减小的规律称为表面效应或集肤效应。
离表面x 处的涡流强度:∆-⋅=x x e I I 0式中,I 0-表面最大的涡流强度;x -到工件表面的距离;Δ-与工件材料物理性质有关的系数。
所以,当x =0时,I x = I 0当x >0时,I x <I 0当x =Δ时,00368.01I eI I x =⋅= 工程规定,当涡流强度从表面向内层降低到表面最大涡流强度的36.8%(即eI 10⋅)时,由该处到表面的距离Δ称为电流透入深度。
在感应加热实践中,钢中电流透入深度的计算常常使用下列简化公式:在20℃时:)(2020mm f ≈∆在800℃时:)(50020mm f≈∆式中,f -感应线圈交流电频率。
3.淬硬层深度工件经感应加热淬火后的金相组织与加热温度沿截面分布有关,一般可分为淬硬层、过渡层及心部组织三部分。
还与钢的化学成分、淬火规范、工件尺寸等因素有关;如果加热层较深,在淬硬层中存在马氏体+贝氏体或马氏体+贝氏体+屈氏体+少量铁素体混合组织。
感应加热表面淬火原理
《感应加热表面淬火是咋回事呢?》嘿,朋友!今天咱来唠唠感应加热表面淬火原理。
这玩意儿听起来挺高深,其实啊,也不难理解。
咱先说说啥是淬火哈。
淬火呢,就像是给金属来个“大改造”。
把金属加热到一定温度,然后快速冷却,让它变得更硬、更结实。
就像咱锻炼身体一样,经过一番磨练,就更强壮了。
那感应加热表面淬火又是啥呢?简单来说,就是用一种特别的方法给金属表面淬火。
这种方法可神奇啦!它是通过感应线圈来加热金属的。
感应线圈就像一个魔法棒。
当电流通过感应线圈的时候,就会产生磁场。
这个磁场可厉害了,它能让金属内部产生感应电流。
感应电流会让金属发热,就像在金属里面点了一把火。
但是呢,这个火可不是随便烧的哦。
它只在金属的表面烧得旺,里面却不怎么热。
这是为啥呢?因为感应电流主要集中在金属的表面嘛。
所以,这种方法就叫感应加热表面淬火。
当金属表面被加热到一定温度的时候,就赶紧用水或者油来冷却它。
这一冷一热的,金属表面就变得特别硬啦。
就像给金属穿上了一件坚硬的铠甲。
感应加热表面淬火有很多好处呢。
比如说,它可以让金属表面变得很耐磨,不容易被磨损。
这样,用这种金属做的零件就能用得更久啦。
而且啊,这种方法还很精准。
可以只对金属的表面进行淬火,不会影响到里面的结构。
这样就能根据不同的需要,给金属“定制”不同的硬度。
你想想,要是没有感应加热表面淬火,那很多东西都做不好呢。
比如汽车的零件、机器的部件等等。
这些东西都需要很坚硬、很耐磨,才能用得长久。
感应加热表面淬火原理虽然有点复杂,但是真的很有用哦。
它让我们的生活变得更方便,更美好。
感应热处理技术标准有哪些
感应热处理技术标准有哪些感应热处理技术标准主要包括以下几个方面:1. 表面感应淬火技术标准:涉及到对材料表面进行感应加热,并进行淬火处理的技术要求和工艺参数,例如淬火介质的选择、淬火温度和淬火速度等。
2. 表面感应回火技术标准:涉及到对感应淬火后的材料进行回火处理的技术要求和工艺参数,包括回火温度和时间等。
3. 表面感应淬火退火技术标准:涉及到对感应淬火后的材料进行退火处理的技术要求和工艺参数,包括退火温度和时间等。
4. 表面感应硬化技术标准:涉及到对材料表面进行感应加热,使其形成硬层的技术要求和工艺参数,包括硬化深度和硬化层的硬度等。
5. 表面感应脱碳技术标准:涉及到对材料表面进行感应加热,使其表面脱碳的技术要求和工艺参数,包括脱碳温度和脱碳时间等。
以上只是一些常见的感应热处理技术标准,具体还会根据不同材料和应用领域考虑。
6. 感应热处理设备和工艺参数的标准:涉及到感应热处理设备的技术要求和性能指标,包括功率、频率、温度控制等方面的标准。
同时还包括感应热处理的工艺参数的标准,如加热时间、加热温度的稳定性等。
7. 感应热处理材料的选择标准:涉及到选择适合感应热处理的材料的标准,包括材料的导电性、磁导率等物理特性的要求。
8. 感应热处理工艺流程和操作规范:给出感应热处理的完整工艺流程和操作规范,包括前处理、感应加热、淬火、回火等环节的要求和注意事项。
9. 感应热处理工作环境和安全标准:涉及到感应热处理的工作环境和操作安全的要求,包括通风要求、设备操作安全、热处理返修等方面的标准。
10. 感应热处理质量检验标准:涉及到对感应热处理后材料质量的检验和评定的标准,包括硬度检测、金相组织分析、非破坏检测等各项指标和方法。
上述标准是比较常见的感应热处理技术标准,实际应用中可能还有其他一些特定材料或工艺的标准。
感应加热表面淬火常见缺陷分析及预防方法 (1)
感应加热表面淬火常见缺陷分析及预防方法硬度不足火软点、软带1.淬火件含碳量过低应预先化验材料化学成分,保证淬火件ωc>0.4%2.表面氧化、脱碳严重淬火前要清理零件表面的油污、斑迹和氧化皮3. 加热温度太低或加热时间太短正确调整电参数和感应器与工件件相对运动速度,以提高加热温度和延长保温时间。
可以返淬,但淬前应进行感应加热退火。
4.零件旋转速度和零件(感应器)移动速度不协调而形成软带调整零件转速和零件(或感应器)移动速度。
5.感应圈高度不够火感应器中有氧化皮适当增加感应圈高度,经常清理感应器。
6.汇流条之间距离太大调整汇流条之间距离为1-3mm。
7.淬火介质中优杂质或乳化剂老化更滑淬火介质。
8.冷却水压力太低锅冷却不及时增加水压,加大冷却水流量,加热后及时喷水冷却。
9.零件在感应器中的位置偏心或零件弯曲严重调整零件和感应器的相对位置,使个边间隙相等;如是零件弯曲严重,淬火钱应进行校直处理。
淬硬层深不足1.频率过高导致涡流透入深度过浅调整电参数,降低感应加热频率。
2.连续淬火加热时零件与感应器之间相对运动速度过快采用预热-加热淬火。
3.加热时间过短可以返淬,但返淬前应金属感应加热退火。
淬硬层剥落产生的原因是表面淬硬层硬度梯度太大,或硬化层太浅,表面马氏体组织导致体积膨胀等。
应对措施是正确调整电参数,采用预热-加热淬火,加深过渡层深度。
淬火开裂1.钢中碳和锰的含量偏高可在试淬试调整工艺参数,也可调整淬火介质,2.钢中夹杂物多、呈网状或成分有偏析或含有有害元素多检查非金属夹杂物含量和分布状况,毛坯需要反复锻造。
3.倾角处或键槽等尖角处加热时出现瞬时高温而淬裂中尖角倒圆,淬火前用石棉绳火金属棒料堵塞沟槽、空洞。
4.冷却速度过大而且不均匀降低水压,减少喷水量,缩短喷水时间。
5. 淬火介质选择不当更具工艺要求选择合适的淬火介质。
6.回火不及时或回火不足淬火后应及时回火,淬火与回火之间的停留时间,对于碳钢或铸件不应超过4h,合金钢不应超过0.5h。
- 1、下载文档前请自行甄别文档内容的完整性,平台不提供额外的编辑、内容补充、找答案等附加服务。
- 2、"仅部分预览"的文档,不可在线预览部分如存在完整性等问题,可反馈申请退款(可完整预览的文档不适用该条件!)。
- 3、如文档侵犯您的权益,请联系客服反馈,我们会尽快为您处理(人工客服工作时间:9:00-18:30)。
心部具有足够的塑形和韧性。
5
表面淬火后的残余应力
热应力:淬火冷却时体积收缩,表面热应力为拉应力。 组织应力:形成马氏体时体积膨胀,在表面形成压应力。
6
感应加热表面淬火原理 简介:工件在感应线 圈中,在高频交流磁场 的作用下,产生很大的 感应电流(涡流),并 因集肤效应而集中分布 于工件表面,使受热区 迅速加热到钢的相变临 界温度Ac3或Acm之上 (奥氏体化),然后在冷 却介质中快速冷却,使 工件表层获得马氏体。
主要研究的是浅硬化层的疲劳强度以及其 疲劳断裂机制。
12
A:0.13s 0.7mm B:0.30s 1.2mm C: 0.37s 1.5mm D:0.67s 1.8mm E:1.5s
硬化层受加热时间的影响,同时硬化层也影响着残 余压应力的分布。
13
疲劳强度随着硬化层的 深度增加而增加。
表面压应力一般能提高 材料的抗疲劳性能,A, B样品的的残余压应力在 1000Mpa左右,他们的 抗疲劳性能相对于原样 品却没有提高多少!
18
参考文献
[1] Komotori J, Shimizu M, Misaka Y, et al. Fatigue strength and fracture mechanism of steel modified by super-rapid induction heating and quenching[J]. International journal of fatigue, 2001, 23: 225-230. [2] Kristoffersen H, Vomacka P. Influence of process parameters for induction hardening on residual stresses[J]. Materials & Design, 2001, 22(8): 637-644. [3] Coupard D, Palin-luc T, Bristiel P, et al. Residual stresses in surface induction hardening of steels: Comparison between experiment and simulation[J]. Materials Science and Engineering: A, 2008, 487(1): 328339. [4] 刘尚超. 感应深度加热表面淬火工艺与低淬透性钢的应用[J]. 汽 车工艺与材料, 1998 (8): 17-21. [5] 潘邻. 表面改性热处理技术进展[J]. 金属热处理, 2005, 30(C00):23-29. [6] 齐晓华, 魏冠义. 金属零件感应加热表面淬火的应用研究[J]. 漯 河职业技术学院学报, 2011, 10(5): 2感应加热淬火技术特点
优 点
热能集中工件表面层,加热速度快; 加热时间短,表面氧化、脱碳轻微; 淬火质量好。得到极细马氏体,表面硬 度高,耐磨性好,疲劳强度高; 淬硬层深度易于控制,易实现机械化和 自动化。
局 限 性
与普通淬火相比,设备的成本较高。 感应加热时,容易使零件的尖角棱边处过 热,即导致所谓“尖角效应”。 对一些形状复杂的零件,感应加热淬火难 以保证所有的淬火面都能够获得均匀的表面 淬硬层。 10
感应加热表面淬火
胡洋 13721584
目录
第一章 第三章 感应加热表面淬火概述 感应加热表面淬火技术展望
第二章 相关文献阅读 第四章 参考文献
2
第一章 概述
表面淬火:将钢表面快速加热到Ac3
(亚共析钢)或Ac1 (过共析钢)以上,然 后使之迅速冷却并转变为马氏体。
分类
表 面 淬 火
火 激光加热表面淬火 电子束加热表面淬火 电接触加热表面淬火 电解液加热表面淬火
感应加热淬火工艺
硬化层深度,零件 技术条件:工件材料,表面硬度,淬硬层深度,硬化区分布,形变量, 尺寸等。硬化层深 表面裂纹,和金相组织等。 中碳,高碳,合金 钢,调质预处理。 度为电流透入深度 一半左右时,频率 最佳。 与钢成分原始 组织有关;同 时加热;连续 加热。
材质及预 先热处理 确定回 火工艺
7
基本原理: (1)电磁感应
自感电抗
(2)集肤效应
电流透入 深度
8
感应加热分类
频率范围 高频感应加热 中频感应加热 工频感应加热 200~300kHz 1~10kHz 50Hz
淬硬层深度 0.5~2mm 2~8mm
应
用
举
例
摩擦条件下工作的 零件小齿轮、小轴 承受扭矩、压力载荷 的零件,曲轴、大齿 轮、 承受扭矩、压力载荷的 大型零件 ,如冷轧辊等
图:旋转弯曲疲劳测试结果 14
内断裂 模式
硬化层断 裂模式
图:样品B(硬化层1.2mm)断裂表面 的特征。
图:样品D(硬化层2.2mm)断裂表面 的特征。 15
图:随着硬化深度的增加,断裂模式转变示意图 16
实验结论
硬化层的深度可以通过调整加热时间来进行控制。 尽管一些样品具有高的表面压应力,但是对于极浅的 硬化层却表现出不太高的疲劳强度,主要是由于裂纹 产生于硬化层下方的非硬化层区域。
设备(频 率和功率) 确定冷却 方式和冷 却介质
根据钢材,零件形状与尺 寸,加热方法等综合考虑 决定。水,聚乙烯醇水溶 液,油,乳化液等。
加热速度温度 和方式
感应器设计
(结构和电参 数)形状与被 加热零件外形 相适应。
低温回火,降 低残余应力和 脆性。
11
第二章 文献阅读
超快速感应加热淬火钢的疲劳强度和断裂机制研究
火焰加热表面淬 火 感应加热表面淬
3
表面淬火组织与性能特点
钢的成分,淬火 前的原始组织及 淬火加热时截面 的温度梯度有关。
T8钢 45钢
淬硬层 Ⅰ 硬化层 Ⅱ 过渡层 Ⅲ 心部 图:表面加热淬火后组织和硬度的分布 4
性能特点
高硬度
耐磨性好
高的疲劳强 度
表面有限深度具有高硬度,强度和耐磨性。
特殊需求零件 (齿轮,轴承等)
随着硬化层厚度的增加,材料断裂模式从内断裂模式
变为了硬化层断裂模式。对于浅硬化层样品,断裂裂 纹从材料内部产生,对相对厚的样品,疲劳裂纹从样 品硬化层夹杂处产生。
17
第三章 感应加热淬火展望
表面感应加热是一种最经济也最节能的 热处理工艺。感应加热技术在零件表面改 性方面取得了广泛的应用,而且其在理论 与应用方面的发展也很迅速。当前在基础 研究方面最活跃的领域是应用计算机模拟 感应加热温度场,磁场的变化。今后,如 果能够将感应加热的热效应和温度场,磁 场等随时间变化,并结合表面加热相变, 冷却相变,残余应力分布,零件变形与性 能预测等用软件结合起来,必然会推动感 应表面技术向一个新的层次发展。