工艺设计要点之反应器
化工设计-13 反应器
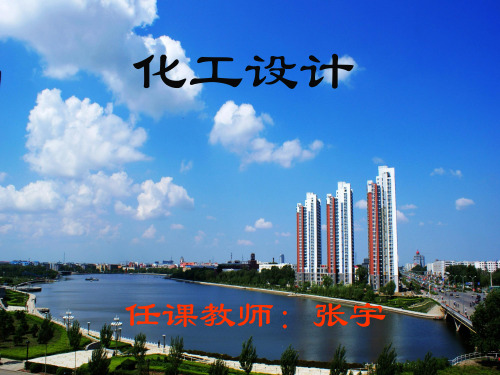
用途: 已知反应历程和平衡反应的反应方程式,
不考虑动力学可行性,计算同时达到化学 平衡和相平衡的结果。
REquil — 连接
REquil — 模型参数
REquil 模块有四组模型参数:
1、模型设定 (Specifications) 2、化学反应 (Reactions) 3、收敛 (Convergence)
△P代表选定组分 (selected) P的生成摩尔数; △A代表参照组分 (reference) A的消耗摩尔数; real 代表反应器内的实际情况; ideal 代表只有 A→P 一个反应发生时的情况。
RStoic — 示例(1)
甲烷与水蒸汽在镍催化剂下的转化反应为:
CH 4 2H2O CO2 4H2
原料气中甲烷与水蒸汽的摩尔比为14,流量为 100 kmol/hr。 若反应在恒压及等温条件下进行,系统总 压为0.1013 MPa,温度为 750 ℃,当反应器出 口处 CH4 转化率为 73% 时, CO2 和 H2 的产量是 多少?反应热负荷是多少?
RStoic — 示例(2)
反应和原料同示例 (1) ,若反应在恒压 及绝热条件下进行,系统总压为0.1013 MPa, 反应器进口温度为 950 ℃,当反应器出口处 CH4 转化率为 73% 时,反应器出口温度是多 少?
RYield — 产率
产率设置有四个选项: 1、组分产率 (Component yields) 2、组分映射 (Component mapping) 3、石油馏分表征 (Petro characterization) 4、用户子程序 (User subroutine)
RYield — 组分产率
RStoic — 化学反应
定义RStoic中进行的每一个化学反应的编 号、化学计量关系、产物生成速率或反应物转 化率。并指明计算多个反应的转化率时是否按 照串联反应方式计算。
化工厂装置中的反应器原理与设计要点

化工厂装置中的反应器原理与设计要点化工工业是现代工业的重要组成部分,而反应器作为化工厂装置中的核心设备,起着至关重要的作用。
反应器的原理和设计要点对于化工工业的发展和产品质量具有重要影响。
本文将探讨反应器的原理和设计要点,希望能够对相关领域的专业人士和学生有所帮助。
一、反应器的原理反应器是进行化学反应的装置,其原理主要包括反应动力学和传质过程。
反应动力学研究反应速率与反应物浓度之间的关系,以及反应速率与温度、压力等因素的关系。
传质过程则研究反应物在反应器中的传质现象,包括质量传递和热量传递。
在反应动力学方面,反应速率常常符合反应速率方程,该方程描述了反应速率与反应物浓度的关系。
在设计反应器时,需要根据反应速率方程确定反应物的投入量和反应时间,以达到预期的反应效果。
同时,反应速率还受到温度和压力等因素的影响,因此在设计反应器时需要考虑这些因素的控制。
在传质过程方面,反应物在反应器中的传质现象对反应速率和反应效果同样具有重要影响。
传质过程包括质量传递和热量传递,其中质量传递主要指反应物在相界面上的传递,而热量传递则指反应过程中的热量交换。
在设计反应器时,需要考虑传质过程的效率和速率,以确保反应物能够充分接触并发生反应。
二、反应器的设计要点1. 反应器的选择:根据反应物的性质和反应条件选择合适的反应器类型。
常见的反应器类型包括批式反应器、连续流动反应器和固定床反应器等。
不同类型的反应器适用于不同的反应条件和反应物种类,因此在设计反应器时需要充分考虑这些因素。
2. 反应器的尺寸和比例:反应器的尺寸和比例对于反应效果和生产能力具有重要影响。
反应器的尺寸需要根据反应物的投入量和反应速率来确定,同时还需要考虑传质过程的效率和速率。
反应器的比例则需要根据反应器的类型和工艺要求来确定,以确保反应物能够充分接触并发生反应。
3. 反应器的控制系统:反应器的控制系统对于反应过程的稳定性和安全性至关重要。
控制系统包括温度、压力和反应物投入量等参数的监测和调节。
化学工程中的反应器与工艺设计

化学工程中的反应器与工艺设计在化学工程中,反应器是一个关键的装置,用于制造化学物质和药品。
由于各种不同的物理和化学反应条件的影响,反应器的设计非常复杂。
化学工程师需要确保反应器能够正确地执行所需的反应,从而在制造过程中获得最高的效率和最佳的质量。
一、反应器的类型反应器的类型包括batch反应器、连续流反应器和半连续流反应器。
Batch反应器是将所有原料添加到反应器中,进行一次完整的反应,然后将产物分离出来。
连续流反应器是通过将原料连续添加到反应器中,以获得一个流通的反应。
半连续流反应器则将实验室规模的batch反应器与连续流反应器的设计结合起来,以使其具有一定程度的自动化功能。
二、反应器选择的重要因素反应器的设计与选择需要考虑多种条件,包括反应物的性质和浓度、反应物的读数和速率、反应器的能力和效率、反应的催化剂和溶剂、反应器的设计和尺寸、反应器的材料和使用环境等。
此外,重要的因素还包括反应器的成本、维护和操作复杂性、反应对环境的影响和群体的安全性。
因此,反应器的选择需要考虑到应用的需求、成本效益、环境安全和风险管理。
三、反应器的设计要素在反应器的设计中,需要考虑多种因素。
例如:反应器的材料和形状、搅拌器和加热/冷却设备、反应器的容积和形状、管道和进出口设备和反应器的控制系统。
在考虑反应器的材料时,需要选择对所需反应物质质量和反应物质性质不敏感的材料。
在设定反应器的搅拌器和加热/冷却设备时,需要根据反应动力学和反应物质性质来优化设计。
反应器的容积和形状也需要根据应用来优化,以确保反应物质能够充分反应,而不会因为催化剂过多而造成浪费。
管道和进出口设备需要根据应用来优化,以确保反应物能够快速和有效地流过反应器。
控制系统可以自动调整反应器的参数以保证反应的佳效果,从而在生产多种不同的化学物质时降低成本并提高质量。
四、反应器的工艺设计反应器的工艺设计包括两个部分:物理设计和化学设计。
物理设计需要考虑反应器的结构、框架、埋地设备、运输布局,以及其他相关和次要设备等。
第六章_固定床反应器的工艺设计

第六章_固定床反应器的工艺设计固定床反应器是一种广泛应用于化工领域的反应设备,其工艺设计的主要目的是在满足反应物转化率和产品选择性的同时,考虑到反应器的稳定性、可操作性和经济性。
本文将从固定床反应器的工艺选择、反应器尺寸设计和操作条件优化三个方面进行详细讨论。
首先,在固定床反应器的工艺选择中,需要考虑反应物质的特性以及反应过程的要求。
例如,对于多相反应系统,可选择固液、固气或固液气等不同形式的反应器。
对于固液反应系统,通常采用固定床(如活性炭床)作为催化剂载体,而对于固气反应系统,常使用填充物(如陶瓷珠)来提供大表面积。
此外,还需要考虑反应物料的物理性质,如粘度、密度和颗粒大小等,以确定反应器的类型和结构。
其次,在固定床反应器尺寸设计中,主要考虑的是反应器的长径比、催化剂的活性、反应器的有效体积等因素。
反应器的长径比是一个重要的设计参数,过大的长径比会导致反应物料的流速过小,影响转化率;过小的长径比则会增加压力损失和催化剂层的温度梯度。
催化剂的活性直接影响反应速率,一般需要选择活性高、稳定性好的催化剂。
反应器的有效体积要足够大,以保证反应物集流时间足够,从而提高转化率。
最后,在操作条件优化方面,需要考虑反应温度、压力和流速等参数。
反应温度会直接影响反应速率和选择性,一般需要根据催化剂的特性和反应动力学进行调整。
反应压力主要考虑固定床压降和反应平衡的影响,需要在考虑反应速率和选择性的同时,保持固定床的稳定性。
流速则涉及反应物料的传质和传热问题,需要通过实验和模拟计算等方法进行优化。
综上所述,在固定床反应器的工艺设计中,需要综合考虑反应物质的特性、反应器尺寸和操作条件等因素,以达到高效、稳定、经济的反应过程。
在实际工程应用中,还需要结合实际生产中的具体要求和限制条件,进行合理的优化设计。
通过合理的工艺设计,可以提高产品的转化率和选择性,降低生产成本,提高生产效益。
化工工艺中的反应器设计原理

化工工艺中的反应器设计原理引言在化工领域中,反应器是实施化学反应的关键设备。
反应器的设计原理直接影响反应的效率、产品质量以及能源消耗等方面。
本文将从反应器的类型、反应动力学、传热与传质以及反应器的尺度放大等方面,探讨化工工艺中的反应器设计原理。
一、反应器的类型反应器的类型多种多样,常见的包括批量反应器、连续流动反应器以及半批量反应器等。
批量反应器适用于小规模生产和实验室研究,连续流动反应器适用于大规模连续生产,而半批量反应器则结合了两者的优点。
不同类型的反应器在设计原理上存在差异,需要根据具体情况选择合适的类型。
二、反应动力学反应动力学研究反应速率与反应物浓度、温度、压力等因素之间的关系。
了解反应的动力学特性对反应器的设计至关重要。
在反应动力学的基础上,可以确定反应的最佳温度、反应物的进料浓度以及反应器的体积等参数,从而提高反应效率和产品质量。
三、传热与传质在反应器中,传热与传质是不可忽视的因素。
传热与传质的效果直接影响反应速率和反应物的分布。
常用的传热方式包括对流传热、辐射传热和传导传热,而传质则通过扩散和对流等方式进行。
在反应器设计中,需要考虑传热与传质的方式和效果,选择合适的传热与传质设备,以提高反应的效率和产物的纯度。
四、反应器的尺度放大从实验室到工业生产,反应器的尺度放大是一个重要的过程。
在尺度放大过程中,需要考虑反应器的动力学特性、传热与传质效果以及设备的可行性等因素。
合理的尺度放大设计可以保证反应器在大规模生产中的稳定性和效率。
五、反应器的安全性设计反应器的安全性设计是化工工艺中的重要环节。
在设计中,需要考虑反应器的压力、温度、反应物的性质以及可能的副反应等因素,以确保反应器的运行安全。
采用合适的安全措施,如压力释放装置、温度控制装置和反应物泄漏检测装置等,可以有效降低事故风险。
六、反应器的优化设计反应器的优化设计旨在提高反应效率、降低能源消耗和改善产品质量。
常用的优化方法包括反应条件的调整、催化剂的选择以及反应器结构的优化等。
连续化反应器及工艺设计
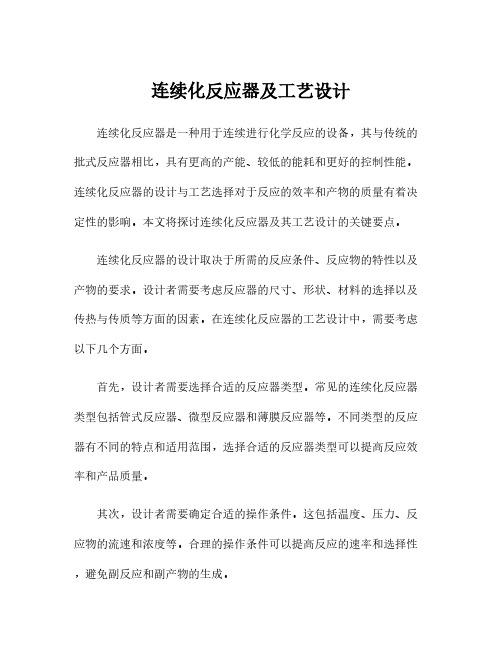
连续化反应器及工艺设计连续化反应器是一种用于连续进行化学反应的设备,其与传统的批式反应器相比,具有更高的产能、较低的能耗和更好的控制性能。
连续化反应器的设计与工艺选择对于反应的效率和产物的质量有着决定性的影响。
本文将探讨连续化反应器及其工艺设计的关键要点。
连续化反应器的设计取决于所需的反应条件、反应物的特性以及产物的要求。
设计者需要考虑反应器的尺寸、形状、材料的选择以及传热与传质等方面的因素。
在连续化反应器的工艺设计中,需要考虑以下几个方面。
首先,设计者需要选择合适的反应器类型。
常见的连续化反应器类型包括管式反应器、微型反应器和薄膜反应器等。
不同类型的反应器有不同的特点和适用范围,选择合适的反应器类型可以提高反应效率和产品质量。
其次,设计者需要确定合适的操作条件。
这包括温度、压力、反应物的流速和浓度等。
合理的操作条件可以提高反应的速率和选择性,避免副反应和副产物的生成。
第三,设计者需要考虑反应器的传热与传质性能。
连续化反应器通常需要提供良好的传热条件,以保持反应物在适宜的温度范围内进行反应。
传质性能的优化可以提高反应物的溶解度和反应的速率。
第四,设计者需要选择适当的催化剂或催化剂载体。
催化剂在化学反应中起到催化作用,可以加快反应速率和提高选择性。
选择合适的催化剂和催化剂载体可以改善连续化反应器的性能。
最后,设计者还需要考虑反应器的控制策略和安全性。
连续化反应器需要实现对温度、压力、流量和浓度等参数的精确控制。
同时,反应器的安全性也是设计者需要重视的方面,包括防止反应失控、爆炸和环境污染等问题。
总之,连续化反应器及其工艺设计是一项复杂的工程任务。
设计者需要综合考虑多个因素,并进行合理的选择和优化。
通过合理的设计和工艺控制,连续化反应器可以实现高效、节能、安全和环保的化学反应过程。
化学工艺中的反应器设计与运行优化

化学工艺中的反应器设计与运行优化在化学工艺中,反应器设计与运行优化是非常重要的环节。
反应器是化学反应进行的场所,反应器的设计和运行质量直接关系到反应的效果和产品质量。
因此,在化学工艺中,反应器设计和运行需要特别重视。
一、反应器设计的重要性反应器设计是决定反应速率、选择性、收率以及产物成分和结构的关键因素。
好的反应器设计可以提高反应速率,增加反应废物的再利用率,减少反应废物的污染,提高反应的选择性和收率,保证生产中产物的质量。
反应器的设计需要考虑多种因素,例如反应废物的产生与再利用,催化剂的选择和使用,反应物的浓度,反应器的温度和压力等等。
这些因素的合理考虑和设计可以提高反应的效率和产物的质量,降低反应的能耗和废物的排放。
二、反应器运行的重要性在反应器运行中,需要考虑反应废物的处理,产品的分离、纯化和质量控制,以及反应率的控制和稳定性。
反应器的运行关系到反应的效果和产物的质量。
反应器的运行需要考虑多种因素,例如反应废物的处理技术,反应器的加热、冷却、搅拌和控制系统,产品的分离、纯化和质量控制技术等等。
这些技术的合理运用和优化可以提高反应的效率和产物的质量,降低能源的消耗和废物的排放。
三、反应器设计和运行的优化反应器设计和运行的优化需要考虑多种因素,并且需要我们从反应的整个过程中进行科学分析和仔细研究。
反应器设计的优化需要从反应器结构、催化剂的选择、反应器温度和压力的调节、反应器控制系统的优化等角度进行考虑和研究。
例如我们可以考虑采用多级反应器、流化床反应器、手性催化剂等方式来提高反应效率和产物的选择性。
同时可以考虑采用先进的反应器控制技术,例如模型预测控制和模糊控制等方式来提高反应器的稳定性和控制质量。
反应器运行的优化需要从反应器的控制程序、加热、冷却、搅拌等方面入手。
我们可以考虑采用优化化反应器运行程序、采用优化加热、冷却、搅拌等方式来提高反应器的效率和稳定性。
同时可以考虑采用先进的质量控制技术,例如在线反应检测监测和质量分析技术,保证生产过程的质量和稳定性。
连续化反应器及工艺设计

连续化反应器及工艺设计
连续化反应器是一种在工业生产过程中被广泛应用的化学反应器。
该反应器可以实现连续流动的反应物料。
与批量反应器相比,连续化反应器具有许多优点,如反应物料的持续供应、高反应速率、较低的能量消耗和较小的设备占地面积等。
在连续化反应器的工艺设计中,一般需要考虑以下几个方面:
1. 反应物料的选择:根据反应的性质和要求,选择合适的反应物料,包括催化剂、溶剂和辅助剂等。
2. 反应器的类型:根据反应过程的要求,选择适合的反应器类型,如管式反应器、塔式反应器、微反应器等。
3. 反应温度的控制:根据反应物料的热力学性质和反应速率,确定合适的反应温度,以实现较高的反应速率和较好的选择性。
4. 反应物料的流动方式:选择合适的流动方式,如稠化流动、湍流流动或混合流动等,以提高反应物料的混合程度和传质效果。
5. 反应物料的控制与分离:在连续化反应器中,需要考虑反应物料的控制和分离,以实现高纯度的产物和高回收率。
6. 反应器的尺寸与可扩展性:根据反应物料的产量要求和生产规模,确定合适的反应器尺寸,同时考虑反应器的可扩展性,以适应未来的生产需求。
总之,连续化反应器及工艺设计需要综合考虑反应物料的选择、反应器类型、反应温度控制、反应物料的流动方式、控制与分离、尺寸与可扩展性等方面的因素,以最大程度地实现反应过程的高效、高选择性和高产量。
- 1、下载文档前请自行甄别文档内容的完整性,平台不提供额外的编辑、内容补充、找答案等附加服务。
- 2、"仅部分预览"的文档,不可在线预览部分如存在完整性等问题,可反馈申请退款(可完整预览的文档不适用该条件!)。
- 3、如文档侵犯您的权益,请联系客服反馈,我们会尽快为您处理(人工客服工作时间:9:00-18:30)。
【MeiWei 81重点借鉴文档】
工艺设计要点之二十:反应器
1。
反应速率数据必须由实验室的研究工作得出,停留时间和空速数据的最终确定必须在试验台上取得。
2。
催化剂颗粒的尺寸:流化床一般为0.1 mm泥浆床一般为1mm 固定床一般为2~5mm
3。
对于均相全混釜反应器,输入搅拌浆的功率应该为0.1〜0.3kW/m3。
然而如果有传热发生,则所需功率应该三倍于上述数值。
4。
当平均停留时间达到组分均一所需时间的5~10倍时,就达到了CSTR的理想状态。
适当设计的搅拌约500〜20RR次旋转,才能达到组分均一。
5。
液体或者淤浆介质间相当慢的反应,通常最经济的配置应该采用3~5个全混釜反应器串联。
6。
平推流反应器的典型应用,在高流率产岀物及短停留时间,当需要明显的热量传递时选择它7。
当达到平衡条件下 95%的转化率时,一个5级全混釜反应器相当于一个活塞流反应器的性能。
8。
温度升高10o C,通常反应速率会加快一倍。
9。
非均相反应的反应速率经常是由传热或传质因素控制的,而不是化学动力学。
10。
有时,改善催化剂选择性能比增加反应速率更有效。
【MeiWei 81重点借鉴文档】。