汽轮机振动超标故障分析及现场动平衡
汽轮机异常振动原因分析及解决对策

汽轮机异常振动原因分析及解决对策近年来,汽轮机作为重要的动力设备,在各个领域得到越来越广泛的应用。
然而,在使用过程中,汽轮机的异常振动问题却时有发生,给安全生产带来了很大的威胁。
本文将针对汽轮机异常振动问题,从原因分析和解决对策两个方面进行详细的讨论。
1、零件间间隙不均匀汽轮机中的零部件间隙不均匀也是常见的振动原因之一。
当零部件之间的间隙不均,会引起轴承座的变形,从而使得轴承与轴承座的匹配失调,导致旋转部件的振动。
2、轴承损坏或老化汽轮机中的轴承在高速旋转的过程中,需要承受较大的负荷和高温环境,难免会出现损坏和老化的情况。
当轴承损坏或老化时,会导致汽轮机的振动加剧。
3、机械失衡机械失衡是汽轮机振动的另一个重要原因。
失衡可以产生离心力,使得机器的旋转部分发生额外的振动,从而导致汽轮机振动加重。
4、结构强度不足汽轮机的结构设计也是影响振动的重要因素。
结构设计不当,材料强度不足,都有可能导致汽轮机的振动加重甚至出现故障。
1、加强检修和保养为了避免汽轮机的异常振动,首先要加强检修和保养。
定期检查汽轮机的各个部件,及时发现并解决问题,从而避免振动的产生。
2、加强轴承维护轴承是汽轮机中的重要部件,对它的维护保养应该特别重视。
定期更换轴承,检查轴承的磨损情况,并进行润滑,可以有效避免轴承老化或损坏导致的振动。
3、平衡校正当机械失衡时,就需要进行平衡校正。
可以通过添加或削减重物的方法,使得汽轮机达到动平衡状态,从而避免失衡带来的振动。
为了避免汽轮机的振动,还需要在结构设计方面下功夫。
应当根据不同的应用场景和需求,进行合理的结构设计,并选择合适的材料,加强结构强度,并避免因结构设计不当造成的振动。
结论:总之,汽轮机异常振动问题的解决并非一蹴而就,需要通过持续的检测、检修和维护来确保机器的稳定运行。
只有不断地优化并加强汽轮机的性能和质量,才能更好地保障生产安全,提高设备的使用寿命,减少不必要的轻微损耗,提高资源利用效率。
汽轮机异常振动原因分析及解决对策
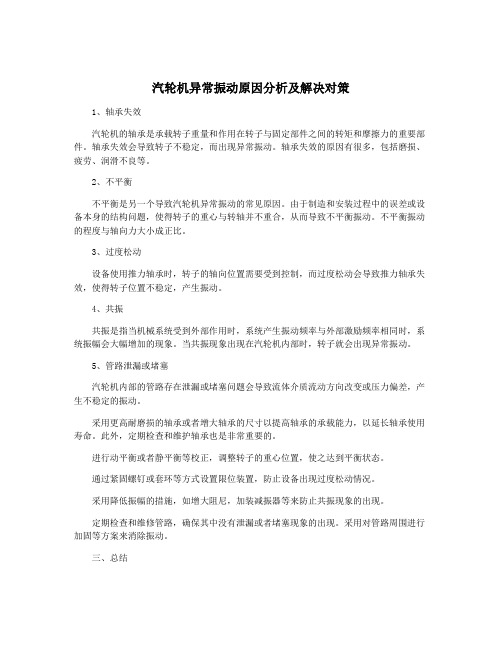
汽轮机异常振动原因分析及解决对策1、轴承失效汽轮机的轴承是承载转子重量和作用在转子与固定部件之间的转矩和摩擦力的重要部件。
轴承失效会导致转子不稳定,而出现异常振动。
轴承失效的原因有很多,包括磨损、疲劳、润滑不良等。
2、不平衡不平衡是另一个导致汽轮机异常振动的常见原因。
由于制造和安装过程中的误差或设备本身的结构问题,使得转子的重心与转轴并不重合,从而导致不平衡振动。
不平衡振动的程度与轴向力大小成正比。
3、过度松动设备使用推力轴承时,转子的轴向位置需要受到控制,而过度松动会导致推力轴承失效,使得转子位置不稳定,产生振动。
4、共振共振是指当机械系统受到外部作用时,系统产生振动频率与外部激励频率相同时,系统振幅会大幅增加的现象。
当共振现象出现在汽轮机内部时,转子就会出现异常振动。
5、管路泄漏或堵塞汽轮机内部的管路存在泄漏或堵塞问题会导致流体介质流动方向改变或压力偏差,产生不稳定的振动。
采用更高耐磨损的轴承或者增大轴承的尺寸以提高轴承的承载能力,以延长轴承使用寿命。
此外,定期检查和维护轴承也是非常重要的。
进行动平衡或者静平衡等校正,调整转子的重心位置,使之达到平衡状态。
通过紧固螺钉或套环等方式设置限位装置,防止设备出现过度松动情况。
采用降低振幅的措施,如增大阻尼,加装减振器等来防止共振现象的出现。
定期检查和维修管路,确保其中没有泄漏或者堵塞现象的出现。
采用对管路周围进行加固等方案来消除振动。
三、总结汽轮机异常振动必须得到及时的发现和解决,以确保设备的正常运行和使用效果。
在汽轮机的运行过程中,要加强设备的监测和维护,定期检查和管理设备的轴承、管路等,保证设备处于良好的运行状态。
汽轮机振动故障的原因分析与处理

汽轮机振动故障的原因分析与处理汽轮机振动故障是指汽轮机在运行过程中出现的振动现象,会导致设备损坏、工作不正常甚至发生事故。
下面对汽轮机振动故障的原因分析和处理进行详细介绍。
一、原因分析1. 设备设计缺陷:汽轮机的设计缺陷可能导致振动故障。
叶片的几何形状不合理、叶栅的位置安装不准确等都会影响汽轮机的平衡性和稳定性,从而引发振动故障。
2. 设备安装问题:汽轮机安装不当也是引起振动故障的原因之一。
底座没有正确调整、冷却水管道接口位置不准确等都会导致汽轮机出现振动现象。
3. 运行环境问题:运行环境的变化也会引发汽轮机振动故障。
温度变化大、湿度过高、颤振现象等都会对汽轮机的运行稳定性产生不利影响。
4. 润滑和冷却系统故障:润滑和冷却系统的故障会导致汽轮机部件过热、磨损增加,从而引发汽轮机振动故障。
5. 设备老化和磨损:长时间运行或使用过久的设备容易出现磨损和老化,从而引起汽轮机振动故障。
二、处理方法1. 设备检修和维护:定期对汽轮机进行检修和维护,及时处理存在的问题,及时更换老化和磨损的部件,从源头上减少振动故障的发生。
2. 设备平衡和校正:对叶片和叶栅等关键部位进行平衡和校正,提高汽轮机的稳定性和平衡性,减少振动现象的出现。
5. 加强润滑和冷却系统的管理:定期检查润滑和冷却系统的工作情况,确保系统正常运行,从而减少振动故障的发生。
汽轮机振动故障的原因分析与处理需要综合考虑设备设计、设备安装、运行环境、润滑和冷却系统等多方面因素。
通过定期检修和维护,加强设备平衡和校正,合理管理运行环境和润滑冷却系统,可以减少振动故障的发生,提高汽轮机的工作效率和安全性。
汽轮机运行振动的大原因分析及应对措施
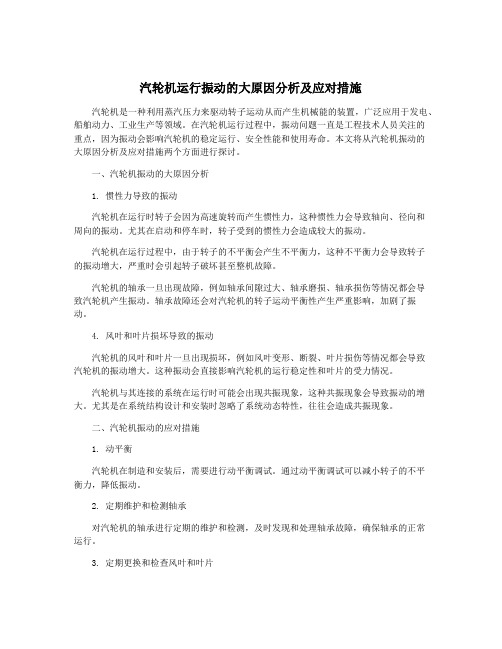
汽轮机运行振动的大原因分析及应对措施汽轮机是一种利用蒸汽压力来驱动转子运动从而产生机械能的装置,广泛应用于发电、船舶动力、工业生产等领域。
在汽轮机运行过程中,振动问题一直是工程技术人员关注的重点,因为振动会影响汽轮机的稳定运行、安全性能和使用寿命。
本文将从汽轮机振动的大原因分析及应对措施两个方面进行探讨。
一、汽轮机振动的大原因分析1. 惯性力导致的振动汽轮机在运行时转子会因为高速旋转而产生惯性力,这种惯性力会导致轴向、径向和周向的振动。
尤其在启动和停车时,转子受到的惯性力会造成较大的振动。
汽轮机在运行过程中,由于转子的不平衡会产生不平衡力,这种不平衡力会导致转子的振动增大,严重时会引起转子破坏甚至整机故障。
汽轮机的轴承一旦出现故障,例如轴承间隙过大、轴承磨损、轴承损伤等情况都会导致汽轮机产生振动。
轴承故障还会对汽轮机的转子运动平衡性产生严重影响,加剧了振动。
4. 风叶和叶片损坏导致的振动汽轮机的风叶和叶片一旦出现损坏,例如风叶变形、断裂、叶片损伤等情况都会导致汽轮机的振动增大。
这种振动会直接影响汽轮机的运行稳定性和叶片的受力情况。
汽轮机与其连接的系统在运行时可能会出现共振现象,这种共振现象会导致振动的增大。
尤其是在系统结构设计和安装时忽略了系统动态特性,往往会造成共振现象。
二、汽轮机振动的应对措施1. 动平衡汽轮机在制造和安装后,需要进行动平衡调试。
通过动平衡调试可以减小转子的不平衡力,降低振动。
2. 定期维护和检测轴承对汽轮机的轴承进行定期的维护和检测,及时发现和处理轴承故障,确保轴承的正常运行。
3. 定期更换和检查风叶和叶片风叶和叶片是汽轮机的重要零部件,应定期进行更换和检查,避免因为风叶和叶片的损坏导致振动的增大。
4. 振动监测系统安装振动监测系统,可以实时监测汽轮机的振动情况,一旦发现异常振动,及时进行处理。
5. 结构设计和安装时考虑系统共振问题在汽轮机的结构设计和安装时,要考虑系统的动态特性,避免因为共振现象导致振动的增大。
汽轮机异常振动原因分析及解决对策
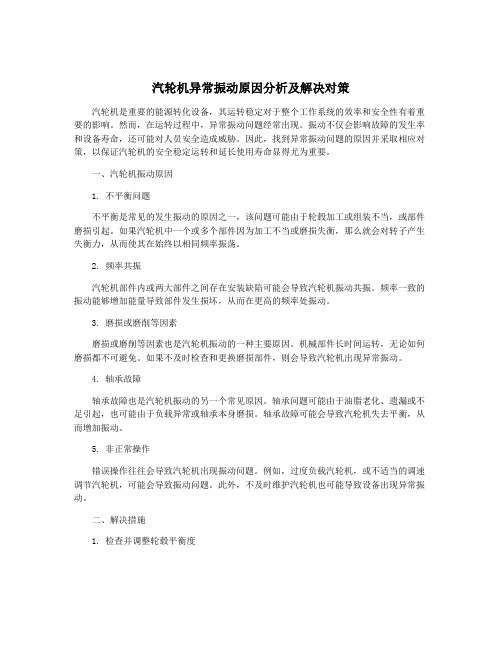
汽轮机异常振动原因分析及解决对策汽轮机是重要的能源转化设备,其运转稳定对于整个工作系统的效率和安全性有着重要的影响。
然而,在运转过程中,异常振动问题经常出现。
振动不仅会影响故障的发生率和设备寿命,还可能对人员安全造成威胁。
因此,找到异常振动问题的原因并采取相应对策,以保证汽轮机的安全稳定运转和延长使用寿命显得尤为重要。
一、汽轮机振动原因1. 不平衡问题不平衡是常见的发生振动的原因之一,该问题可能由于轮毂加工或组装不当,或部件磨损引起。
如果汽轮机中一个或多个部件因为加工不当或磨损失衡,那么就会对转子产生失衡力,从而使其在始终以相同频率振荡。
2. 频率共振汽轮机部件内或两大部件之间存在安装缺陷可能会导致汽轮机振动共振。
频率一致的振动能够增加能量导致部件发生损坏,从而在更高的频率处振动。
3. 磨损或磨削等因素磨损或磨削等因素也是汽轮机振动的一种主要原因。
机械部件长时间运转,无论如何磨损都不可避免。
如果不及时检查和更换磨损部件,则会导致汽轮机出现异常振动。
4. 轴承故障轴承故障也是汽轮机振动的另一个常见原因。
轴承问题可能由于油脂老化、遗漏或不足引起,也可能由于负载异常或轴承本身磨损。
轴承故障可能会导致汽轮机失去平衡,从而增加振动。
5. 非正常操作错误操作往往会导致汽轮机出现振动问题。
例如,过度负载汽轮机,或不适当的调速调节汽轮机,可能会导致振动问题。
此外,不及时维护汽轮机也可能导致设备出现异常振动。
二、解决措施1. 检查并调整轮毂平衡度如果汽轮机出现不平衡问题,则需要定期检查轮毂平衡度。
对于失衡的轮毂,需要检查其对称性并进行调整以提高平衡度。
如果轮毂无法进行调整,则可能需要更换其失衡的部分。
共振是比较容易处理的汽轮机振动原因,其解决方法是通过控制汽轮机的运转速度来排除振荡的频率。
如果发现汽轮机出现频率共振问题,则需要尽快采取措施定位和解决振动问题。
3. 定期检查和更换磨损部件定期检查并更换磨损部件对于汽轮机的正常运转至关重要。
汽轮发电机振动分析及现场动平衡处理

汽轮发电机振动分析及现场动平衡处理大多数的汽轮发电机振动故障可以用现场高速动平衡的方法进行处理。
本文介绍了柔性转子的振动特性,阐述了现场校正一、二、三阶转子不平衡所采用的方法。
通过实例证明对称加重法虽然可能使汽轮发电机存在的三阶不平衡得到一定的校正,但是灵敏度低,且可能破坏一阶平衡状态;而在转子外伸端的联轴器加重时一般会取得较好的效果。
所取得的振动治理经验对同型机组类似振动故障的诊断及现场处理有一定的借鉴意义。
关键词:汽轮发电机;柔性转子;振动;现场动平衡引言汽轮发电机是火力发电厂的核心设备,振动水平是衡量机组安全可靠性最重要的指标。
剧烈的振动容易导致设备部件的疲劳损坏,一些重大的毁机事故直接或间接地与振动有关。
在汽轮发电机的各种振动故障中,不平衡引起的振动占到70%以上,还有部分故障也可以通过平衡的手段使振动得到改善,因此现场动平衡是消除振动的主要手段[1]。
由于汽轮发电机组轴系是多转子系统,相互之间有一定影响;而且在现场受加重位置的限制,有时无法在计算好的位置加重;此外大型机组启动一次的费用高达十万元以上,启动次数和时间受到了限制,因此现场高速动平衡是振动处理中十分重要而又有一定难度的环节。
随着汽轮发电机容量的增大,转子轴向长度及其重量也不断增加,而转子径向尺寸因受到材料强度限制增长不大,这样就迫使采用工作转速大于第一临界转速和第二临界转速的柔性转子[2]。
汽轮发电机转子均属于柔性转子,一般200 MW及以下的发电机工作转速在一、二阶临界转速之间,大多数300MW及以上的发电机工作转速在二、三阶临界转速之间。
这两类转子的平衡方法存在较大的差异,因此在现场动平衡时应采取针对性的处理方案才能取得理想的效果。
1 柔性转子的振动特性在不平衡作用下柔性转子的振动可表示为:柔性转子平衡主要根据其振型正交原理进行。
所谓正交是指在平衡某一阶振型时,不影响其他振型的平衡状态。
现场动平衡时通常一阶不平衡采用对称加重的方法,它与二阶振型是正交的;二阶不平衡采用反对称加重的方法,它与一阶不平衡是正交的。
汽轮机异常振动原因分析及解决对策
汽轮机异常振动原因分析及解决对策分析异常振动的原因是解决问题的关键。
异常振动的原因可以分为机械因素和系统因素两类。
机械因素主要包括以下几个方面:1. 涡轮叶片的磨损和失衡:由于长期使用和磨损,涡轮叶片可能会出现失衡问题,导致振动加剧。
此时,需要对叶片进行修复或更换,同时进行动平衡调整。
2. 轴承的损坏和疲劳:轴承是汽轮机运转中重要的支撑和支承部件,如果轴承损坏或疲劳,会导致振动异常。
解决方法包括更换损坏的轴承,并加强对轴承的维护和润滑。
3. 牵引机构的松动:牵引机构是提供动力输出的关键部分,如果机构松动或连接螺栓松动,会引起振动变得更加明显。
此时,需要加强对牵引机构的检查和维护,及时调整和紧固螺栓。
系统因素主要包括以下几个方面:1. 系统的不平衡:汽轮机运行中,如果系统不平衡,比如过热、过冷或压力不稳定,都可能引起振动异常。
此时,需要对系统进行调整和检修,保持系统的平衡和稳定。
2. 风阻力和涡流:汽轮机运行过程中,风阻力和涡流也会产生一定的振动。
解决方法包括优化设计,减小阻力和涡流的影响,并加强对振动的监测和控制。
3. 噪音和共振:汽轮机运行时产生的噪音和共振也会引起振动。
解决方法包括增加隔音措施,减少共振频率,避免共振现象的发生。
针对以上分析,可以采取以下几个对策来解决异常振动问题:1. 加强设备的维护和检修工作,定期检查涡轮叶片、轴承和牵引机构的情况,及时进行修复和更换损坏部件。
2. 优化系统的设计和运行参数,保持系统的平衡和稳定,在运行过程中及时调整和修正系统的工况和参数,减小不平衡和阻力的影响。
3. 加强对振动的监测和控制,安装振动传感器和监测系统,及时发现振动问题,并采取相应的控制措施。
4. 加强运行人员的培训和技能提升,提高他们对汽轮机异常振动问题的认识和解决能力,及时处理异常振动事件,保证设备的安全和可靠运行。
针对汽轮机异常振动问题,要进行详细的原因分析,找出问题的根源,然后采取相应的解决对策。
汽轮机运行振动的大原因分析及应对措施
汽轮机运行振动的大原因分析及应对措施1. 引言1.1 引言汽轮机是一种常见的能源装置,其运行过程中可能会出现振动问题。
振动不仅会影响汽轮机的运行效率,还会加速部件的磨损,甚至引发安全事故。
了解汽轮机运行振动的原因并采取有效的应对措施非常重要。
本文将首先分析汽轮机运行振动的大原因,并重点讨论不平衡、轴承故障和叶片磨损等常见原因。
随后,我们将探讨振动问题的应对措施,包括平衡调整、轴承更换和叶片维修等方法。
我们将总结文章内容并提出建议。
通过本文的研究,读者将深入了解汽轮机运行振动的原因和应对措施,有助于他们更好地保养和维护汽轮机,提高其运行效率和安全性。
希望本文能为相关工程技术人员提供参考,使他们能够更好地应对汽轮机振动问题,确保设备的正常运行。
2. 正文2.1 振动的大原因分析振动是汽轮机运行中常见的现象,其大原因分析涉及多个方面。
不平衡是引起振动的主要原因之一。
汽轮机在运行过程中,由于零部件的制造或安装不够精准,导致转子的质量分布不均匀,引起转子偏心,从而产生不平衡振动。
轴承故障也是导致振动的原因之一。
轴承在长时间运行后会出现磨损或损坏,导致转子在转动时发生不稳定,产生振动现象。
叶片磨损也会导致汽轮机振动。
叶片是汽轮机中的重要部件,其磨损程度直接影响到汽轮机的运行稳定性。
如果叶片磨损严重,会导致气流不规则,引起振动现象。
在汽轮机运行中,需要注意叶片的定期检查和更换,以减少振动带来的影响。
汽轮机振动的大原因分析涉及不平衡、轴承故障和叶片磨损等多个方面。
为了有效应对这些问题,需要加强汽轮机的定期检查和维护管理,及时发现问题并进行修复,以确保汽轮机的安全稳定运行。
2.2 不平衡汽轮机运行时出现振动问题,其中不平衡是导致振动的重要原因之一。
不平衡主要包括动平衡和静平衡两种情况。
动平衡是指转子在高速旋转时因质量不均匀而导致的振动问题。
这可能是由于转子上的零部件在制造或装配过程中质量不均匀,或者由于磨损、腐蚀等原因导致质量失衡。
汽轮机异常振动的分析和治理
汽轮机异常振动的分析和治理汽轮机是一种重要的能源转换设备,其在发电、船舶、化工等领域都有着广泛的应用。
由于各种原因,汽轮机在运行过程中会出现异常振动问题,严重影响设备的安全性和稳定运行。
对汽轮机异常振动进行分析和治理是非常重要的。
本文将就汽轮机异常振动的原因、分析方法和治理措施进行详细介绍。
一、汽轮机异常振动的原因1. 设备磨损汽轮机在长时间运行过程中,由于受到高温高压的影响,设备的部件会出现磨损现象,导致不平衡性增大,从而引起振动。
2. 设备失衡汽轮机的转子在制造、安装、维护等环节可能出现不平衡,导致设备在运行过程中出现振动问题。
4. 轴承故障汽轮机的轴承是支撑设备转子的重要部件,一旦轴承出现故障,就会导致设备振动问题的发生。
1. 振动信号分析通过设备安装振动传感器,对汽轮机运行时的振动信号进行实时监测和分析,找出振动的频率、幅值、相位等参数,并与设备的标准数据进行对比分析,确定振动的原因。
2. 谐振分析对汽轮机的转子、叶片等关键部件进行有限元分析,找出其固有频率,并结合振动实测数据进行对比分析,确定是否存在谐振现象。
4. 涡轮叶片频谱分析对汽轮机涡轮叶片的频谱进行分析,找出频率分布规律,确定是否存在叶片损坏、失衡等问题。
1. 设备维护保养对汽轮机进行定期的维护保养工作,包括清洗设备、更换润滑油、检查轴承等,确保设备处于良好的工作状态。
2. 涡轮平衡对汽轮机的转子进行动平衡调整,消除不平衡性,减小振动幅值。
3. 螺栓检查定期对汽轮机设备的螺栓进行检查,确保其紧固状态良好,避免因螺栓松动导致的振动问题。
5. 涡轮叶片修复对汽轮机的涡轮叶片进行定期的检测,发现问题及时进行修复,避免因叶片损坏引起的振动。
汽轮机异常振动是影响设备安全性和稳定运行的重要问题,需要引起重视。
对汽轮机异常振动进行分析和治理,可以有效提高设备的运行稳定性,保证设备安全运行,延长设备的使用寿命。
汽轮机的用户和相关工作人员应对异常振动问题进行重视,采取有效措施确保设备的安全稳定运行。
汽轮机异常振动原因分析及解决对策
汽轮机异常振动原因分析及解决对策汽轮机是一种重要的发电设备,但在运行过程中可能出现异常振动问题。
本文将对汽轮机异常振动的原因进行分析,并提出相应的解决对策。
汽轮机的异常振动主要有以下几个原因:1. 不平衡:汽轮机的转子由多个叶片和转子组成,在制造和装配过程中可能存在不平衡的问题。
当转子旋转过程中存在不平衡时,会引发振动。
解决对策:对汽轮机进行动平衡处理,即通过在转子上添加均匀分布的补平块,使转子达到平衡状态。
动平衡处理需按照严格的规程进行,确保处理效果达到要求。
2. 纵向不稳定:汽轮机在运行过程中,由于叶片的磨损或其他原因,可能出现纵向失稳的情况。
纵向不稳定会导致振动增加,对设备的安全性和性能产生不利影响。
解决对策:在汽轮机的叶片上设计合理的固定结构,增加叶片的刚度,从而提高汽轮机的纵向稳定性。
定期检查叶片的磨损情况,及时更换磨损严重的叶片。
3. 噪声和谐振:汽轮机在运行过程中会产生噪声,而这些噪声可能与机械元件的固有振动频率达到共振,增大振动幅值。
解决对策:在汽轮机的设计中,要充分考虑噪声与振动的影响,采取合适的隔音和吸振措施,降低噪声和共振的风险。
对于发生共振的机械元件,可以通过改变其结构或减小其质量,避免共振发生。
4. 摩擦和磨损:汽轮机的轴承和密封件在运行过程中会产生摩擦和磨损,导致振动增加。
解决对策:定期检查和更换汽轮机的轴承和密封件,确保其良好的工作状态。
在设计和制造过程中,选择合适的轴承和密封件,减小摩擦和磨损的发生。
解决汽轮机异常振动问题的关键在于:定期检查和维护设备,采取合适的措施预防振动的发生,及时处理已经发生的振动问题。
除了上述的对策,还应加强对汽轮机操作人员的培训和管理,提高其对振动问题的认识和处理能力。
只有做到全方位的振动预防和处理工作,才能确保汽轮机的安全、高效运行。
- 1、下载文档前请自行甄别文档内容的完整性,平台不提供额外的编辑、内容补充、找答案等附加服务。
- 2、"仅部分预览"的文档,不可在线预览部分如存在完整性等问题,可反馈申请退款(可完整预览的文档不适用该条件!)。
- 3、如文档侵犯您的权益,请联系客服反馈,我们会尽快为您处理(人工客服工作时间:9:00-18:30)。
空载时 3 #轴瓦垂直方向振动速度频谱图如图 3, 其振动速度的时域波形接近正弦曲线。
速度/(mm/s)
6
4
2
0
0
10000200003000040000频率/Hz
图 3 空载时 3 #瓦振动速度频谱图
2. 振动数据分析 从升降速各轴瓦波德图可以看出,机组在 1500 ~
China 中国 Plant 设备
Engineering 工程
1600r/min 时达到了一阶临界转速,而设计时机组的 一阶临界转速为 1800r/min,说明轴系的刚度发生了变 化。而从表 1 的各测点振动数据可以发现,2 #、3 #、 4 #测点振动较大,尤其 3 #垂直方向振动最大,达到了 64μm,超过 50μm 的报警值,且频谱图中占优势的 是转速的一倍频,时域波形也接近标准的正弦波,说 明 3 #瓦振动性质为普通强迫振动。而其他几个测点的 振动情况也与之非常接近。
(收稿日期:2016-01-04)
中国设备工程 2016.03
71
Research and Exploration 研究与探索 ·监测与诊断·
1#
2#
汽轮机
3# 发电机
4# 励磁机
图 1 轴系结构简图
二、事故经过 1. 更换 4 #轴瓦 自 2005 年 8 月测量振动以来,1 #汽轮机 4 #瓦振 动一直比较大,振动速度有效值保持在 4 ~ 6mm/s 之间, 而 ISO10816-1 中同类设备的参考报警值为 7.1mm/s 有效值;振动位移保持在 30 ~ 40μm 之间,汽轮机振 动经验报警值为 50μm。而进入 2007 年之后振动速度 有效值就一直超过 6mm/s,且始终在 6 ~ 7mm/s 之间 波动,十分接近报警值。其他几个轴瓦振动值则都在 良好的水平。由于汽轮机组属于电厂的关键设备,对 于整个公司的生产稳定有着异常重要的作用,于是利 用 2007 年全厂设备大修机会,对汽轮机整个轴系进行 了仔细的检查。 检查中发现 4 #瓦巴氏合金有一块约 1cm2 的剥落, 旁边隐约可以看到一条裂纹,长度约为 20mm。于是对 4 #瓦进行了更换,其他部分未做大的变动,只是重新 调整了轴瓦的间隙及对中数据。 2. 更换 3 #轴瓦 大修结束重新开车之后,4 #瓦振动值稍有减小, 再次降到 6mm/s 以下,检修效果仍旧不太理想。值得 注意的是,此次检修之后其他几个轴瓦振动均有明显 上升,其中 3 #瓦垂直方向的振动速度有效值达到了 8mm/s 以上,超过了报警值。在坚持开了一段时间未 见好转之后,决定再次停车对几个轴瓦进行仔细检查。 检查中发现 3 #轴瓦巴氏合金有大片的剥落现象。还有 一个现象值得注意:脱开联轴器时发现柱销被卡死在 销孔之内,很难取出。于是更换了 3 #轴瓦并对联轴器 重新进行了对中,其他部位未做改动。 检修之后重新开车,升速过程中,经过一阶临界 转速时振动超过了 7μm 的允许值,按照规定无法继续 升速,于是将机组停下来再次检查轴瓦。此次检查, 除了联轴器柱销仍旧很紧之外,轴瓦各项安装数据均 在允许范围之内。另外检查滑销系统也未发现异常。 检查之后重新开车,升速过程中振动仍旧超标。 三、事故分析及诊断 由于始终无法准确找到引起振动的最初源头,所 以决定请专业检测机构对汽轮机振动事故进行系统的 诊断和处理。 第三方检测机构技术人员到厂后,立即召开了一 个简短的事故研讨会。我方技术人员对事故的整个经
2 #轴承支撑汽轮机转子,3 #、4 #轴承支撑发电机 转子。汽轮机与发电机通过刚性联轴器连接,发电 机与励磁机同轴连接。整个轴系支撑结构简图如图 1 所示。
轴上产生挠度、运输过程中受到冲击导致精度不良等 几个因素有关。
过大载荷和润滑不良会引起轴承面积较大且无规 律的磨损,但现场调研并未发现此现象;轴承内外圈 倾斜和轴上产生挠度虽然会导致卡伤,但同时由于受 力不均,会磨损轴承内最脆弱的保持架,但从现场调 研结果来看,该轴承保持架并未出现相应磨损;而在 加工和运输过程中,由于轴承必须平放,会导致轴承 外圈内侧产生一道轴向划痕,在现场调研时未发现有 轴向划痕,遂排除该可能。由于该划痕的位置特殊, 恰好接触了轴承的滚子和外圈内侧,所以分析认为导 致划痕产生的主要原因是坚硬异物的进入,使异物与 滚子一起在轴承外圈内侧做圆周运动,将其划伤导致 轴承损坏、振动和冲击值的增大。磨损监测元素光谱 分析污染元素硅、磨损元素铬元素含量的异常变化, 表明造成轴承异常磨损的来源及程度。
关键词:汽轮机;轴瓦;振动;动平衡
中图分类号:TK263.6+1
文献标识码:B
文章编号:1671-0711(2016)03-0071-03
一、设备概述 1# 汽轮发电机组是型号为 CN12 - 3.43/0.49 的单抽凝汽式汽轮机,额定功率为 12MW,由南 京 汽 轮 电 机 厂 制 造 。机 组 共 有 4 个 轴 承 ,其 中:1 #、
图 4 1 #机组 1 #~ 4 #轴承第一次加重后振动波德图
图 5 1 #机组 1 #~ 4 #轴承第二次加重后振动波德图
五、结语 通过此次故障分析及处理过程,发现了如下几点 值得注意,这也正是转子不平衡故障的具体表现。首先, 更换 4 #瓦之后,4 #瓦振动没有明显改善,却将振动波 及了整个轴系上的其他各点,说明并不是 4 #轴瓦的安 装问题;其次,由于机组振动较大,经过一段时间的 运行 3 #瓦巴氏合金出现了大片剥落,经过更换之后振 动仍未解决,说明主要症结也不在 3 #瓦;第三,每次 检查时都发现联轴器柱销卡得很紧,虽经重新找正之 后,再次开车仍旧会继续发生,说明如果一味地强制 找正,会将轴系平衡再次破坏,而开车后轴系会自行 回复到自由位置。 此次案例,汽轮机在整个轴系的检查以及轴瓦更 换过程中,应认真记录下各项原始安装数据。如果以 往运行良好,最好不要尝试改变这些数据,否则有可 能会造成整个轴系平衡的破坏,如果正好和以往的不 平衡量相互叠加,会对其进一步放大,而导致整个机 组振动的超标。
表 1 汽轮机组各测点 3000r/min 空载振动数据表 μm ∠ deg,μm
轴称号
1#
2#
3#
4#
垂直 4 ∠ 167,6 40 ∠ 160,43 57 ∠ 150,64 18 ∠ 235,20
水平 19 ∠ 81,22 20 ∠ 205,23 45 ∠ 206,45 41 ∠ 1,44
轴向 11 ∠ 25,12 28 ∠ 321,31 26 ∠ 331,30 30 ∠ 69,32
表 2 1 #机组动平衡过程及振动值表
μm
工况
测点
1#
2#
3#
4#
垂直
6
43
64
20
3000r/min 空载 水平
22
23
45
44
轴向
12
31
30
32
垂直
5
29
40
14
第一次加重
P3=301g
水平
22
14
21
28
∠ 330°
轴向
10
23
14
20
第二次加重: 垂直
5
8
18
8
取前次,改加: P3=587.5g
三、故障处理及对策 本次机组检修,根据设备故障检查及评估,对该 挤压机主减速箱轴承故障,采取更换损坏的 23060CC/ C3W33 轴承的措施。 对后续挤压机的日常操作与维护,首先要对挤压机 主减速箱 1 轴进行彻底清理,查找并整改其余可能导致
振动、冲击增大的因素,例如磨损、腐蚀、载荷过大等。 其次,进一步加强挤压机组振动与磨损的状态监测,实 现机组状态维护与状态维修,确保机组安稳长周期运行。
1. 第一次升降速试验 2007 年 9 月 9 日,在机组升速过程中进行了振动 检测。其中 1 #~ 4 #轴瓦振动升降速波德图如图 2。
图 2 2007 年 9 月 9 日 1 #~ 4 #瓦升降速波德图
在机组达到额定转速 3000r/min 空载运行时,对 机组几个轴瓦各方向振动进行了巡测,测试数据如表 1。
72
中国设备工程 2016.03
过进行了详细的描述,对方初步认为是换瓦之后机组 发生了共振。于是立即着手进行汽机的升速试验,进 行进一步的验证。第三方技术人员所使用的仪器为美 国本特立公司 208-P DAIU 振动测试仪,速度传感器, 分别测取机组 1 #~ 4 #轴瓦垂直方向的振动。键相探 头为成都昕亚科技有限公司生产的 LK3 型光电传感器。
(收稿日期:2015-12-15)
中国设备工程 2016.03
73
水平
12
7
9
13
∠ 315°
轴向
15
12
11
17
垂直
3
4
9
8
负荷 8.30MW 水平
10
7
12
10
轴向
7
9
7
10
两次加重后各轴瓦的振动波德图如图 4、5 所示。 可见,两次加重振动均有明显的好转,转子的一 阶临界转速已经基本恢复到 1700 ~ 1800r/min 之间, 且在经过一阶临界转速时的振动上升的不明显。目前 机组的振动已经达到了正常良好的水平。
3. 诊断结论 由于更换 4 #轴瓦之后其它几个轴瓦测点振动也有 明显上升,且转子动刚度发生了变化,轴瓦振动性质表 现为普通强迫振动,结合以往的检修经历,做出了如下 的诊断结论:1 #汽轮机组振动超标事故原因为更换轴 瓦之后改变了轴系的动刚度,导致了轴系的不平衡。 四、振动故障的处理 针对以上诊断结论,决定对电动机转子进行现场 动平衡试验。现场共进行两次加重,之后各测点振动 恢复到了良好的水平。动平衡过程及前后的振动数据 如表 2。
China 中国 Plant 设备
Engineering 工程
汽轮机振动超标故障分析及现场动平衡
闫志勇 (中海石油化学股份有限公司,北京 100029)