注塑成型常见不良现象及处理措施精编
注塑成型各种缺陷的现象及解决方法【范本模板】
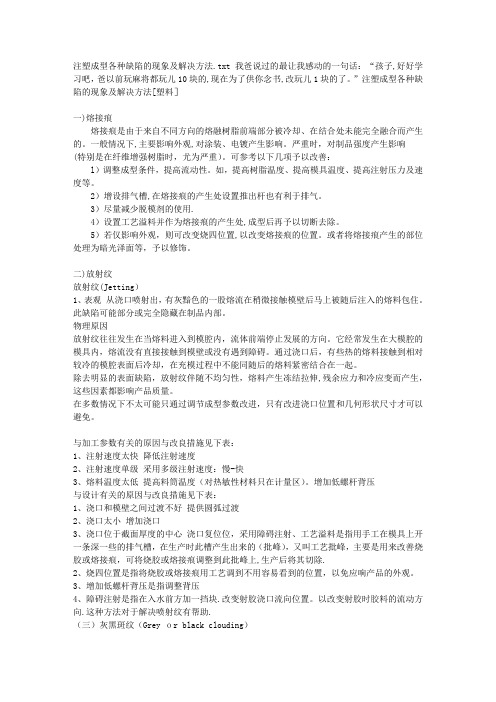
注塑成型各种缺陷的现象及解决方法.txt我爸说过的最让我感动的一句话:“孩子,好好学习吧,爸以前玩麻将都玩儿10块的,现在为了供你念书,改玩儿1块的了。
”注塑成型各种缺陷的现象及解决方法[塑料]一)熔接痕熔接痕是由于来自不同方向的熔融树脂前端部分被冷却、在结合处未能完全融合而产生的。
一般情况下,主要影响外观,对涂装、电镀产生影响。
严重时,对制品强度产生影响(特别是在纤维增强树脂时,尤为严重)。
可参考以下几项予以改善:l)调整成型条件,提高流动性。
如,提高树脂温度、提高模具温度、提高注射压力及速度等。
2)增设排气槽,在熔接痕的产生处设置推出杆也有利于排气。
3)尽量减少脱模剂的使用.4)设置工艺溢料并作为熔接痕的产生处,成型后再予以切断去除。
5)若仅影响外观,则可改变烧四位置,以改变熔接痕的位置。
或者将熔接痕产生的部位处理为暗光泽面等,予以修饰。
二)放射纹放射纹(Jetting)1、表观从浇口喷射出,有灰黯色的一股熔流在稍微接触模壁后马上被随后注入的熔料包住。
此缺陷可能部分或完全隐藏在制品内部。
物理原因放射纹往往发生在当熔料进入到模腔内,流体前端停止发展的方向。
它经常发生在大模腔的模具内,熔流没有直接接触到模壁或没有遇到障碍。
通过浇口后,有些热的熔料接触到相对较冷的模腔表面后冷却,在充模过程中不能同随后的熔料紧密结合在一起。
除去明显的表面缺陷,放射纹伴随不均匀性,熔料产生冻结拉伸,残余应力和冷应变而产生,这些因素都影响产品质量。
在多数情况下不太可能只通过调节成型参数改进,只有改进浇口位置和几何形状尺寸才可以避免。
与加工参数有关的原因与改良措施见下表:1、注射速度太快降低注射速度2、注射速度单级采用多级注射速度:慢-快3、熔料温度太低提高料筒温度(对热敏性材料只在计量区)。
增加低螺杆背压与设计有关的原因与改良措施见下表:1、浇口和模壁之间过渡不好提供圆弧过渡2、浇口太小增加浇口3、浇口位于截面厚度的中心浇口复位位,采用障碍注射、工艺溢料是指用手工在模具上开一条深一些的排气槽,在生产时此槽产生出来的(批峰),又叫工艺批峰,主要是用来改善烧胶或熔接痕,可将烧胶或熔接痕调整到此批峰上,生产后将其切除.2、烧四位置是指将烧胶或熔接痕用工艺调到不用容易看到的位置,以免应响产品的外观。
注塑成型缺陷及解决方法

注塑成型缺陷及解决方法注塑成型是一种常用的塑料制品生产工艺,但在实际操作过程中,难免会出现一些缺陷。
下面将介绍几种常见的注塑成型缺陷及其解决方法。
1.短射:短射指的是塑料在模腔中注入不完全,导致制品形状不完整或缺少一部分。
短射可能由于注射速度过快或进气不畅引起。
解决方法是调整注塑机的注射速度和压力,确保塑料充分进入模腔,并检查进气口是否畅通。
2.气泡:气泡是指制品表面或内部出现空洞。
气泡的形成可能由于塑料中含有水分、模具开放不当等原因。
解决方法是在注塑前将塑料干燥处理,确保塑料中不含水分,并检查模具密封性以防止气体进入模腔。
3.缩短:缩短是指制品尺寸比设计要小,可能由于塑料收缩不均匀或模具温度不稳定引起。
解决方法是通过调整模具温度和冷却系统,使塑料在注塑过程中均匀收缩,并确保模具温度稳定。
4.色差:色差是指制品表面颜色不均匀,可能由于塑料熔融不充分、颜料添加不均匀等原因。
解决方法是加长塑料的熔化时间,确保塑料充分熔融,并确保颜料充分混合均匀。
5.枝晶:枝晶是指制品表面出现树枝状的纹理,可能由于注塑温度过高或冷却时间不足引起。
解决方法是降低注塑温度,延长冷却时间,确保塑料在注塑过程中充分凝固。
6.毛刺:毛刺是指制品表面出现刺状的尖突物,可能由于模具间隙过大或模具磨损引起。
解决方法是调整模具间隙,确保模具紧密结合,并定期检查模具磨损情况。
7.烧焦:烧焦是指塑料在注塑过程中受热过度,产生发黑或炭化的现象。
烧焦可能由于注塑温度过高或注射速度过快引起。
解决方法是降低注塑温度,调整注射速度,确保塑料受热均匀。
总结起来,解决注塑成型缺陷的关键是调整注塑机参数、保证模具质量和稳定性,以及进行适当的后处理工艺。
此外,及时发现和修复模具的损坏也是避免缺陷的重要措施。
注塑成型不良现象及解决方法
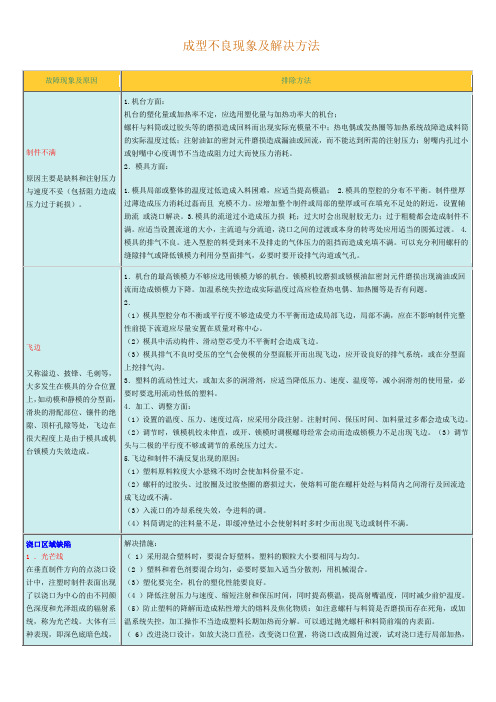
(4)对薄件应提高温度,保证料流畅顺,对厚壁制件应降低模温。
(5)浇口要对称开设,尽量开设在制件厚壁部位,应增加冷料井容积。
3.塑料方面:
结晶性的塑料比非结晶性塑料收缩历害,加工时要适当增加料量,或在塑料中加成换剂,以加快结晶,减少收缩凹陷。
4.加工、调整方面:
(1)设置的温度、压力、速度过高,应采用分段注射。注射时间、保压时间、加料量过多都会造成飞边。(2)调节时,锁模机铰未伸直,或开、锁模时调模螺母经常会动而造成锁模力不足出现飞边。(3)调节头与二极的平行度不够或调节的系统压力过大。
5.飞边和制件不满反复出现的原因:
(1)塑料原料粒度大小悬殊不均时会使加料份量不定。
分析如下:
1.加工方面:
(1)加工压力过大、速度过快、充料愈多、注射、保压时间过长,都会造成内应力过大而开裂。
(2)调节开模速度与压力防止快速强拉制件造成脱模开裂。
(3)适当调高模具温度,使制件易于脱模,适当调低料温防止分解。
2.
(1)模具型腔分布不衡或平行度不够造成受力不平衡而造成局部飞边,局部不满,应在不影响制件完整性前提下流道应尽量安置在质量对称中心。
(2)模具中活动构件、滑动型芯受力不平衡时会造成飞边。
(3)模具排气不良时受压的空气会使模的分型面胀开而出现飞边,应开设良好的排气系统,或在分型面上挖排气沟。
3.塑料的流动性过大,或加太多的润滑剂,应适当降低压力、速度、温度等,减小润滑剂的使用量,必要时要选用流动性低的塑料。
成型不良现象及解决方法
故障现象及原因
注塑成型常见不良及对策
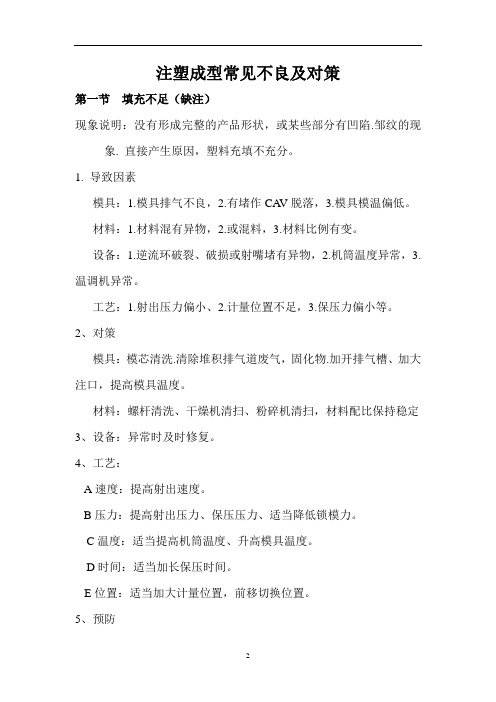
注塑成型常见不良及对策第一节填充不足(缺注)现象说明:没有形成完整的产品形状,或某些部分有凹陷.邹纹的现象. 直接产生原因,塑料充填不充分。
1. 导致因素模具:1.模具排气不良,2.有堵作CA V脱落,3.模具模温偏低。
材料:1.材料混有异物,2.或混料,3.材料比例有变。
设备:1.逆流环破裂、破损或射嘴堵有异物,2.机筒温度异常,3.温调机异常。
工艺:1.射出压力偏小、2.计量位置不足,3.保压力偏小等。
2、对策模具:模芯清洗.清除堆积排气道废气,固化物.加开排气槽、加大注口,提高模具温度。
材料:螺杆清洗、干燥机清扫、粉碎机清扫,材料配比保持稳定3、设备:异常时及时修复。
4、工艺:A速度:提高射出速度。
B压力:提高射出压力、保压压力、适当降低锁模力。
C温度:适当提高机筒温度、升高模具温度。
D时间:适当加长保压时间。
E位置:适当加大计量位置,前移切换位置。
5、预防A、产前模具分解清洗,产后及时防锈保养,生产过程中定时清洗。
B、现场异常处理必须防止金属物掉入螺杆。
C、材料管理操作,不可混料。
D、模具温度、成形条件定时点检。
第二章飞边现象说明:产品外围或内围形成薄膜状、超出完整产品形状。
产生原因:塑料充填过多或模芯缺损、配合间隙大、模芯腐蚀而造成。
1、飞边形成:A、模具本身(设计)缺陷产生飞边。
如:本司“408”B、型修后,配合间隙大,导致飞边。
2、正常量产出现飞边,主要有以下几点:A、材料干燥不充分,导致飞边。
B、产品压模,二次成形造成飞边。
如:本司PDIC BASE,产品压模,合模面受损,导致飞边。
C、模芯腐蚀,清洗后导致飞边。
如:82机种890产品。
D、模芯进胶:如本司“389”柱子合模线飞边(进胶造成)E、粉末、拉丝二次成形导致飞边,主要表现在二分模。
如:818F、混料:因材料流动指数变异导致飞边。
如90混有900P等G、材料比例(原:再):变更导致飞边。
H、设备异常:如计量不稳定,机筒温度异升高,模温升高。
注塑成型常见不良现象及处理措施

注塑成型常见不良现象及处理措施注塑成型常见的不良现象有以下几种:
1. 短射:指注塑料进模型中未充满模腔,导致产品缺陷。
处理措施:增加注射
压力、延长注射时间、增加料缸温度、增加模具温度、增加模具出料口直径等。
2. 气泡:指产品表面或者内部浮现气泡,影响产品质量。
处理措施:增加注射
压力、延长注射时间、增加模具温度、增加料缸温度、增加模具出料口直径、增加模具排气孔等。
3. 热熔线:指产品表面浮现细小的线状缺陷,通常是由于注射速度过快导致的。
处理措施:减小注射速度、增加模具温度、增加模具出料口直径等。
4. 毛刺:指产品表面浮现细小的凸起,通常是由于模具设计不合理或者模具磨
损导致的。
处理措施:修复模具、修改模具设计、增加模具温度、增加模具出料口直径等。
5. 缩水:指产品尺寸缩小,通常是由于注射压力不足或者冷却时间不足导致的。
处理措施:增加注射压力、延长冷却时间、增加模具温度等。
6. 毛洞:指产品表面或者内部浮现凹陷,通常是由于注射速度过快或者模具设
计不合理导致的。
处理措施:减小注射速度、修改模具设计、增加模具温度等。
处理不良现象的关键是找到问题的根源,然后针对性地采取相应的处理措施。
同时,注塑成型过程中的参数控制和模具维护也是关键的因素,需要进行定期检查和调整。
注塑成型不良现象及解决方法
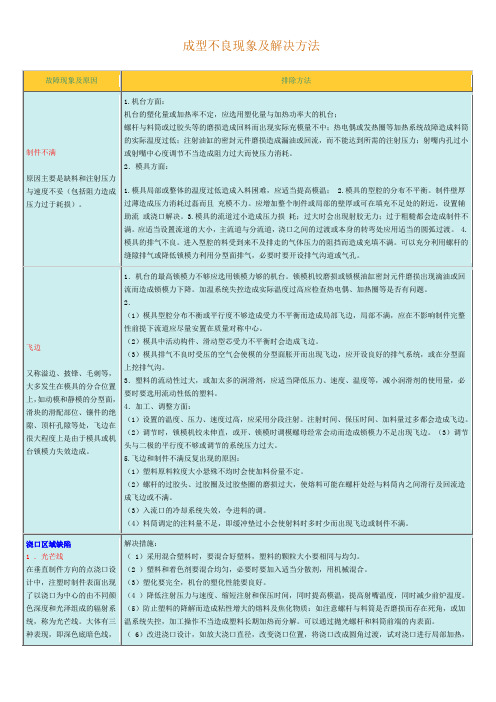
(1)设置的温度、压力、速度过高,应采用分段注射。注射时间、保压时间、加料量过多都会造成飞边。(2)调节时,锁模机铰未伸直,或开、锁模时调模螺母经常会动而造成锁模力不足出现飞边。(3)调节头与二极的平行度不够或调节的系统压力过大。
5.飞边和制件不满反复出现的原因:
(1)塑料原料粒度大小悬殊不均时会使加料份量不定。
(3)对结晶型塑料,尽量使制件各部分的冷却速度一致,对于壁厚差异大的制件,可用着色剂来掩蔽色差,对于壁厚较均匀的制件要固定好料温和模温。
(4)制件的造型和浇口形式,位置对塑料充填情况有影响,使制件的某些局部产生色差,必要时要进行修改。
白霜
有些聚苯乙烯类制件,在脱模时,会在靠近分型面的局部表面发现附着一层薄薄的白霜样物质,大多经抛光后能除去。这些白霜样物质同样会附在型腔表面,这是由于塑料原料中的易挥发物或可溶性低分子量的添加剂受热后形成气态,从塑料熔体释出,进入型腔后被挤迫到靠近有排气作用的分型面附近,沉淀或结晶出来。这些白霜状的粉末和晶粒粘附在模面上,不单会刮伤下一个脱模制件,次数多了还将影响模面的光洁度。不溶性填料和着色剂大多与白霜的出现无关。白霜的解决方法:加强原料的干燥,降低成型温度,加强模具排气,减少再生料的掺加比例等,在出现白霜时,特别要注意经常清洁模面。
2.模具方面:
1.模具局部或整体的温度过低造成入料困难,应适当提高模温;2.模具的型腔的分布不平衡。制件壁厚过薄造成压力消耗过磊而且充模不力。应增加整个制件或局部的壁厚或可在填充不足处的附近,设置辅助流或浇口解决。3.模具的流道过小造成压力损耗;过大时会出现射胶无力;过于粗糙都会造成制件不满。应适当设置流道的大小,主流道与分流道,浇口之间的过渡或本身的转弯处应用适当的圆弧过渡。4.模具的排气不良。进入型腔的料受到来不及排走的气体压力的阻挡而造成充填不满。可以充分利用螺杆的缝隙排气或降低锁模力利用分型面排气,必要时要开设排气沟道或气孔。
注塑成型常见不良现象和处理措施方案
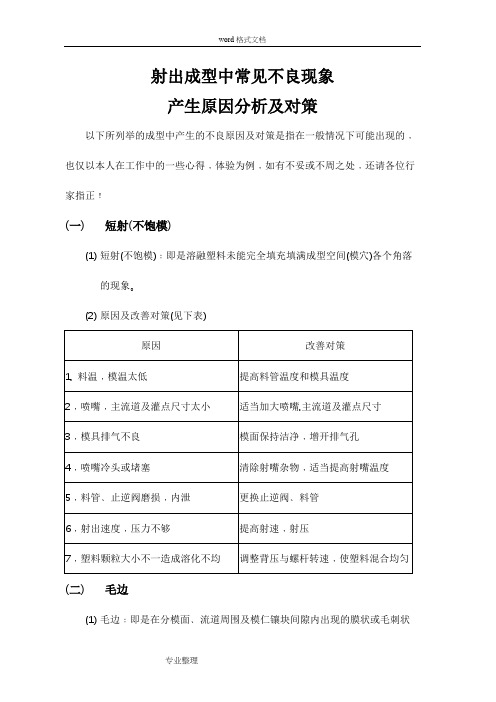
射出成型中常见不良现象产生原因分析及对策以下所列举的成型中产生的不良原因及对策是指在一般情况下可能出现的﹐也仅以本人在工作中的一些心得﹐体验为例﹐如有不妥或不周之处﹐还请各位行家指正﹗(一)短射(不饱模)(1)短射(不饱模)﹕即是溶融塑料未能完全填充填满成型空间(模穴)各个角落的现象。
(2)原因及改善对策(见下表)(二)毛边(1)毛边﹕即是在分模面﹑流道周围及模仁镶块间隙内出现的膜状或毛刺状的多余胶料。
(2)原因及改善对策(见下表)*注﹕成型时间过长﹐模温过低而采用高压﹐高速射出也是产生毛边的常见原因(三)银线(1)银条(银线)即是在成型产品表面或表面附近﹐沿塑料流动方向﹐呈放射状的银白色条纹。
(2)原因及改善对策(见下表)(四)成品光泽度低(1)成品光泽度低是指成品表面光泽达不到质量要求﹐表面无折光度。
(2)原因及改善对策(见下表)(五)变形(1)变形可分为对角线的扭曲及平行边沿的曲翘两种﹐是成品成型中发生的不规则弯曲现象。
(2)原因及发善对策(见下表)(六)顶白(1)顶白(也叫白化)是指成品在脱模之际﹐在顶针或其它脱模部位出现白色痕迹。
(2)原因及改善对策(见下表)(七)结合线(1)结合线是指在成型中﹐二道或多道熔融材料融合时出现的细线状。
(2)原因及改善对策(见下表)(八)冲料痕(1)冲料痕是指熔融材料在进料点附近﹐以浇口为中心而呈现的条纹状。
(2)原因及改善对策(九)异色(黑纹)(1)异色(黑纹)是指在成型过程中﹐在成品表面出现的黑色或其它深色条纹。
(2)原因及改善对策(见下表)(十)气泡(1)气泡是熔融塑料中的水份﹐挥发气体于成型过成中被封入内部而残留的空动现象。
(2)原因及改善对策(见下表)射出换料要诀在射出成型作业中﹑换料﹑换色的问题﹐值得吾入深入探讨﹒如何以最快速的方法完成换料﹑换色﹐除可节省时间外﹐并可降低一笔相当可观的生产成本。
一﹑同一材料之换色1﹒1同一材料的换色时﹐原则上从淡色材料换为深浓色材料﹐较从不透明材料换为透明材料容易。
注塑产品常见的13种质量缺陷原因分析及解决办法
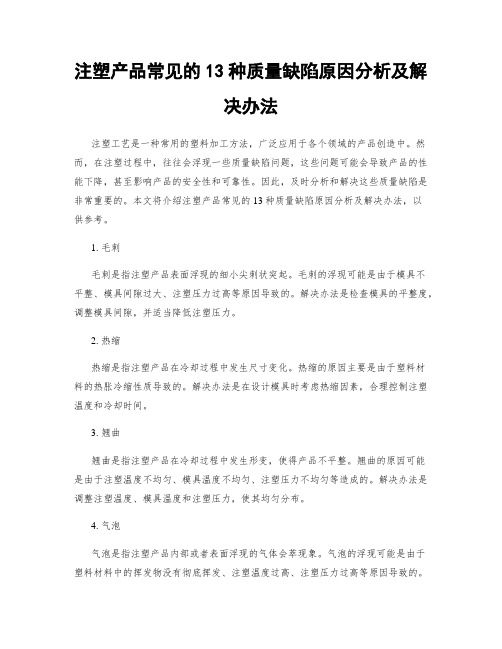
注塑产品常见的13种质量缺陷原因分析及解决办法注塑工艺是一种常用的塑料加工方法,广泛应用于各个领域的产品创造中。
然而,在注塑过程中,往往会浮现一些质量缺陷问题,这些问题可能会导致产品的性能下降,甚至影响产品的安全性和可靠性。
因此,及时分析和解决这些质量缺陷是非常重要的。
本文将介绍注塑产品常见的13种质量缺陷原因分析及解决办法,以供参考。
1. 毛刺毛刺是指注塑产品表面浮现的细小尖刺状突起。
毛刺的浮现可能是由于模具不平整、模具间隙过大、注塑压力过高等原因导致的。
解决办法是检查模具的平整度,调整模具间隙,并适当降低注塑压力。
2. 热缩热缩是指注塑产品在冷却过程中发生尺寸变化。
热缩的原因主要是由于塑料材料的热胀冷缩性质导致的。
解决办法是在设计模具时考虑热缩因素,合理控制注塑温度和冷却时间。
3. 翘曲翘曲是指注塑产品在冷却过程中发生形变,使得产品不平整。
翘曲的原因可能是由于注塑温度不均匀、模具温度不均匀、注塑压力不均匀等造成的。
解决办法是调整注塑温度、模具温度和注塑压力,使其均匀分布。
4. 气泡气泡是指注塑产品内部或者表面浮现的气体会萃现象。
气泡的浮现可能是由于塑料材料中的挥发物没有彻底挥发、注塑温度过高、注塑压力过高等原因导致的。
解决办法是控制注塑温度和压力,选择合适的塑料材料,并进行充分的挤出和干燥处理。
5. 缩孔缩孔是指注塑产品内部浮现的空洞状缺陷。
缩孔的原因可能是由于注塑温度过低、注塑压力不足、模具设计不合理等导致的。
解决办法是提高注塑温度、增加注塑压力,并优化模具设计。
6. 裂纹裂纹是指注塑产品表面或者内部浮现的裂纹状缺陷。
裂纹的浮现可能是由于注塑温度过高、注塑压力过大、冷却时间过短等原因导致的。
解决办法是降低注塑温度、减小注塑压力,并延长冷却时间。
7. 毛边毛边是指注塑产品边缘浮现的不平整现象。
毛边的原因可能是由于模具设计不合理、注塑压力过高、注塑速度过快等导致的。
解决办法是优化模具设计,降低注塑压力,并适当调整注塑速度。
- 1、下载文档前请自行甄别文档内容的完整性,平台不提供额外的编辑、内容补充、找答案等附加服务。
- 2、"仅部分预览"的文档,不可在线预览部分如存在完整性等问题,可反馈申请退款(可完整预览的文档不适用该条件!)。
- 3、如文档侵犯您的权益,请联系客服反馈,我们会尽快为您处理(人工客服工作时间:9:00-18:30)。
注塑成型常见不良现象及处理措施精编Document number:WTT-LKK-GBB-08921-EIGG-22986射出成型中常见不良现象产生原因分析及对策以下所列举的成型中产生的不良原因及对策是指在一般情况下可能出现的﹐也仅以本人在工作中的一些心得﹐体验为例﹐如有不妥或不周之处﹐还请各位行家指正﹗(一)短射(不饱模)(1)短射(不饱模)﹕即是溶融塑料未能完全填充填满成型空间(模穴)各个角落的现象。
(2)原因及改善对策(见下表)(二)毛边(1)毛边﹕即是在分模面﹑流道周围及模仁镶块间隙内出现的膜状或毛刺状的多余胶料。
(2)原因及改善对策(见下表)*注﹕成型时间过长﹐模温过低而采用高压﹐高速射出也是产生毛边的常见原因(三)银线(1)银条(银线)即是在成型产品表面或表面附近﹐沿塑料流动方向﹐呈放射状的银白色条纹。
(2)原因及改善对策(见下表)(四)成品光泽度低(1)成品光泽度低是指成品表面光泽达不到质量要求﹐表面无折光度。
(2)原因及改善对策(见下表)(五)变形(1)变形可分为对角线的扭曲及平行边沿的曲翘两种﹐是成品成型中发生的不规则弯曲现象。
(2)原因及发善对策(见下表)(六)顶白(1)顶白(也叫白化)是指成品在脱模之际﹐在顶针或其它脱模部位出现白色痕迹。
(2)原因及改善对策(见下表)(七)结合线(1)结合线是指在成型中﹐二道或多道熔融材料融合时出现的细线状。
(2)原因及改善对策(见下表)(八)冲料痕(1)冲料痕是指熔融材料在进料点附近﹐以浇口为中心而呈现的条纹状。
(2)原因及改善对策(九)异色(黑纹)(1)异色(黑纹)是指在成型过程中﹐在成品表面出现的黑色或其它深色条纹。
(2)原因及改善对策(见下表)(十)气泡(1)气泡是熔融塑料中的水份﹐挥发气体于成型过成中被封入内部而残留的空动现象。
(2)原因及改善对策(见下表)在射出成型作业中﹑换料﹑换色的问题﹐值得吾入深入探讨﹒如何以最快速的方法完成换料﹑换色﹐除可节省时间外﹐并可降低一笔相当可观的生产成本。
一﹑同一材料之换色1﹒1同一材料的换色时﹐原则上从淡色材料换为深浓色材料﹐较从不透明材料换为透明材料容易。
一般换色作业程序如下﹕(1)关斗漏料斗下部的进料挡门﹔(2)空射数次﹐将加热料管内的材料全部射出﹔(3)新材料加入漏斗﹔(4)打开进料挡门﹐螺杆前进后退十数次直到换色完成﹒从不透明材料换为透明材料时﹐尤需拆除喷嘴头部份﹐清除残留的材料﹐必要时杆亦需抽出撤底清理﹐不可有残余料积存死角处。
二﹑不同材料之换色不同材料的更换作业﹐是利用前后各材料的熔融黏度差﹐与加热管的温度控制来施行换料手续。
热可塑性塑料材料的温度高时﹐会黏着于金属面﹐温度低时不黏着。
换料作业即利用此性质﹐使欲更换的加热缸内原黏着于加热缸壁﹐以让供经冷螺杆的高黏度清除用材料削取之。
此时﹐螺杆温度宜低﹐欲使更换之原料不掷附于螺杆而得以削除之﹐因而清除用材料宜用熔融黏度高的材料﹐如高密度PE或PS等。
不同材料换料作业须注意下列事项﹕(1)在焕料终了前﹐加热缸温度应低于实际的成型温度﹔如成型温度低的材料A更换成高的材料B的场合﹐清除料B的温度应低于B的温度应低于B材料成型温度10℃~~20℃为宜。
又成型温度高的材料B更换成低的材料A 的场合﹐清除材料A的温度应低于A的成型温度10℃~20℃为宜。
(2)螺杆转速宜低﹐减低螺杆背压﹐防止摩擦热导致材料温度上升。
(3)欲更换的原材料﹐熔融状态下昼量勿卷附螺杆上。
(4)以短行程使螺杆前进﹐冲出材料数次﹐换料效果极佳。
(5)加热缸内壁或螺杆头部或外径﹑螺杆沟槽部份﹐若有伤痕或缺口﹐则熔融材料会滞留该处而使换料作业困难。
二﹑换料作业实例在塑料射出成型作业中﹐换料换色之场合经常发生﹐所以如果对于换料之基本知识缺乏﹐易造成工厂内原物料之浪费﹐又耽误时间。
为了解决换色换料之难题﹐市面上推础一种西德制料管清洗剂---CORATEX﹐可清除螺杆﹑喷嘴﹑模具(?尤以热浇道模具之清除理想)之残留料﹐对缩短换色之时间相当有帮助。
射出成型塑料的特性射出成型技术中四大主要因素之一----塑料,在成型技术中起着非常重要的作用,因此,要很好地掌握成型技术,必需要了解塑料的特性,以下是塑料的一些常见特性:一,化学特性1,绝缘性;2,抗电阻性;3,耐药品性;4,吸水(吸湿性)性;5,耐水性;6,气体透过率;7,毒性;二,物理特性1,比重;2,收缩率;3,流动性;4,色调;5,着色性;三,机械特性1,抗拉,压缩,弯曲; 2,冲击强度,剪断; 3,耐塺耗性,硬度; 4,负荷变形;5,疲劳特性;6,潜变性;四,光学特性1,透明度;2,光透过率;3,耐侯性;4,放射线特性;五,热特性1,成型温度范围;2,热膨胀率;3,热变型温度;4,熔融温度;5,分解温度;6,燃烧性,脆化;7,温度低温特性;五大工程塑料射出成型特性一,尼龙(PA---聚胺树脂)1,比重:2,熔点:PA 220℃PA66 255℃3,成型温度:PA 225---280℃PA66 260---280℃4,压缩比: 5,喷嘴温度: 260---300℃6,螺杆进料后退时间为塑料滞留时间的90%则可以获一致的高韧性。
7,干燥温度:79℃超过93℃3小时会变色。
二,PC(LEXAN---聚碳酸酯树脂)1,比重:2,熔点:221℃3,成型温度: 250---290℃4,容易起水分解屋温度不宜超过300℃以上。
5,螺杆附着的分解物以二氯甲烷溶剂除去。
6,再生料加收24%以下并以筛纲去粉末。
7,L/D:20以上(螺杆须20牙以上)。
8,压缩比:2—39,除湿至%以下以防气泡产生。
三,POM聚缩醛(塑料钢)1,比重: 2,熔点:175℃3,成型温度: 200---210℃4,成弄时易变形,曲翘,凹陷;在高温下有热分解气体产生有爆裂现像发生应特别注意。
四,变性PPO(NORYLR)1,比重: 2,熔点:强化(GF)275---315℃3,成型温度;一般260---300℃4,模温:80---100℃5,易发生龟裂,易吸湿,须彻底干燥。
6,背压:5---15kg/cm27,I/D:18---208,料管以PC或PMMA清洗。
五,PBT聚酯树酯(VALOX)1,比重:2,熔点:225℃3,成型温度:240---260℃4,分解温度:280℃5,模温:60---70℃可防止变形。
6,快速射出可使表面光泽度佳,但要注意排气,以防烧焦。
7,以PS或HIPS清洗料管,再生料使用25%以下。
射出成型不良常见重案分析例案一,生产过程中料管升温异常引起升温异常原因大致如下:1,射速太快;2,感温线接触不良或感温点设计不当;3,喷嘴孔径小;4,背压太高;5,螺杆转速太快;6,螺杆与料管偏心而磨擦生热;7,料管入料处冷却不够;8,喷嘴处堵塞或温度过低。
例案二,较大之成品中央部份变形(ABS)1,改善前射出模式:第一段快速第二段减速,第三段快速,这种模式易造成填充过饱而引起脱模困境难,顶出时发生变形。
对策:采且一快,二,三段减射出模式。
2,模具使用过冻冷冻水,造成成品表面冷却快,内部冷却慢而产生后收缩现像引起收缩差异使成品发生曲翘变形。
对策:升高冷冻水温,并以适当延长冷却时间。
3,模温及料温偏低而使用较高压力成型而引起残留应力造成曲翘且成品密度不均。
对策:适当提高模温及料温以利低压成型。
4,有脱模倒勾,成品取拿困难造成变形。
对策:抛光脱模倒勾,注意平横取拿成品。
例案三,料头拉丝1,射喷温度过高或加热过频繁对策:降低射嘴温度及喷嘴加热频率。
2开模位置及变速设定不佳对策:调整变速开模位置,适当加快快速开模及增加开模行程。
3,适当调点松退(1mm~5mm)对策:调整松退时特别注意位置不可太大,以免成品出现缩水,银线,气泡等。
4,调整背压轴(0KG/CM2 ---10 KG/CM2 )注意:喷嘴流涕的处理方法与上叙处理拉丝大致一样。
另:流涕有可能是背压及保压压力过大,因此要考虑调整背压及保压。
例案四:成品表面出现黑点一,成品表面固定点出现黑点1,模面某定点太脏或排气孔淤塞。
2,锁模时模具导销或滑块掉落污泽于模母模模穴。
3,顶针油污,锈斑。
4,顶针及顶针孔磨损或顶针有倒勾拉料屑。
二,成品表面不固定出现黑点]1,原料本身有黑点。
2,烘料桶不洁,进风口太脏。
3,料管未清洗干净。
4,火箭头模损或射嘴未上到位。
5,工作环境内灰尘太多。
例案五,成品短料,缩水的同时又出现毛边1,模具未闭紧或模具公,母模面不吻合。
2,机具销模力不够。
3.模具排气不良。
4,料管温度过高。
5,射速太快,射压太高。
6,一次射出压力,位置位调好。
7,模具温度太低或太高。
8,成品太薄,表面积太大而灌点又太远。
9,保压压力太大。
10,保压切换太早。
11,四支哥林柱不平衡或有哥林柱断。
例案六,螺杆储料时断时续或未干燥料卡住螺杆加料不顺1,把螺杆射到底时停止马达不操作,料管继续正常加温。
2,把料管冷却水关掉。
3,把离冷却水最近一段度加高20---30度,前端温度不变。
4,在加升最后一段温度时,温控自然跳动达二次以上后,方把新料加上,清洗因加高温后而变质的料,然后使度恢复正常料管冷却水开,即可正常生产,理由是:要把卡在杆上的料熔化掉,使新料易通过,因此,凡对于吸水率强的料(如尼龙料,二次料,拌色粉料等)温度未达到时,千万不要先放入料管以防止卡住螺杆。
例案七,含玻璃纤维的成型要点1,FRTR的流动性低于非强化料,所以常须增加料管温度,模温,及射压力等,同理模具的浇口,横浇道,浇口等的尺寸也须大于非强化料。
2,成型收缩率甚小于非强化料,呈方向性流动,所以浇口方向设计尽量减少配向所致的不良影响。
3,成品的接合线部份强度,低于其它部份,因此,模具接合线部位一定要开排气,不致于包风现像。
4,注意模具,螺杆组件,料管,螺杆的材质及表面硬度。
塑料原料的分类以及特性说明价格比较低,材料特性较脆,强度差,外观比较不光亮,不适合做外观材料。
价格比HIPS贵,韧性较好,外观很光亮,可以电镀。
价格比ABS贵,韧性强度佳,外观光滑。
PC料与ABS料混合在一起的工程塑料。
耐磨,比如可以适合用作齿轮。
<玻璃钎维> 是一种添加剂,可以增加强度,但缩收率减低,其减低的比率为加10%的GF要减低%的缩收率,表面粗糙,不适合做外观件。