曲轴减振皮带轮的设计汇总.
曲轴构造解析

B
36
B
37
3、V型八缸发动机:
空间曲拐,各平面曲拐成90°夹角,发火间隔角是 720/ 8=90 °。发火顺序是 18436572。
V型八缸发动机的曲拐布置
B
38
10、扭转减振器
• 扭转振动:当发动机工作时, 曲轴在周期性变化的转矩作 用下,各曲拐之间发生周期 性相对扭转的现象。
• 功用:吸收曲轴扭转振动的 能量、消除扭转振动,避免 发生共振极其引起的恶果。
B
6
(二)曲轴的工作条件和要求
1、工作条件:
承受周期性变化的气体压力、往复惯性力、离心力以 及由此产生的扭矩、弯矩的共同作用。...
2、要求:
(1)足够的刚度、疲劳强度和冲击韧性;... (2)各工作表面润滑良好、耐磨;...
(3)旋转惯性力系达到良好的平衡(离心力合力及 其合力矩为零时称为完全平衡,亦称动平衡)。...
轴向(推力)轴承用于限制曲轴的轴向窜动(发动机工作时,曲轴常受到离合器施加 于飞轮的轴向力作用而有轴向窜动的趋势),保证曲柄连杆机构各零件正确的相对位置。 但曲轴受热膨胀时,又应允许其自由伸长,故曲轴上的轴向定位装置必须有,但只能设 于一处,通常设在中间主轴承处。现代汽车发动机常将径向轴承和推力轴承合而为一, 制成翻边滑动轴承。
第四节 曲轴飞轮组
组成:曲轴、飞轮、扭转减振器、皮带轮、正时齿轮或链轮等
B
1
EQ6100Q-1型发动机曲轴飞轮分解圆柱销
图带 扭转减震器 轮 挡
起动爪锁 紧垫圈
油 片
起动爪
中
定时齿轮
一、六气缸 活塞处在上 止点时的记 号(钢球)
螺母 齿环
主间
止推片
轴轴
曲轴减震皮带轮粘附工艺的实验分析与实践

指 标 , 征 了 曲 轴 减 震 皮 带 轮 在 发 动 机 运 表 矩 , 征 曲 轴 减 震 皮 带 轮 在 发 动 机 运 行 过 表 程 中, 带轮抗曲轴角加速度冲击的能力。 皮
s m p e t uc u e a d o i l s r t r n l w c s . le d m p r c a ks f i m a e p f e r i a d h b. o t Pu l y a e r n ha t s d u o g a r ng n u And ub e i ma i g h d mp n e f c r b r s k n t e a i g f e t
1 图 2 、 。
_
2轮 毂和齿环 的连接 强度的实验验证 方案
对 于 曲 轴 减 震 皮 带 轮 而 言 , 估 轮 毂 评
图 1 压 入式 涂 胶工 艺 图 3 轴 向压 脱 实验 示意 图
l髓 _
图 2 硫 化 注入 式涂 胶 工 艺
图 4 滑 移扭 矩测 试 实验 示 意 图
科技资讯 S IN E & T C N L G N O MA I N CE C E H O O Y IF R TO
工 业 技 术
与 齿 环 连 接 强 度 , 要 从 轴 向 压 脱 和 滑 动 轮 的 轮 毂 和 齿 环 分 离 , 时 记 录 压 脱 力与 胶 , 毂 不 涂 胶 , 环 只 涂 底 胶 , 环 只 涂 需 同 轮 齿 齿 扭 矩 两 部 分 来 进 行 评 估 。 于 轴 向 压 脱 力 位 移 的 关 系 。 对 面 胶 和 齿 环 不 涂 胶 六 种 情 况 对 于 最 终 黏 合
工 业 技 术
SIC &T H0OY CNE E NLG E C
皮带轮的设计
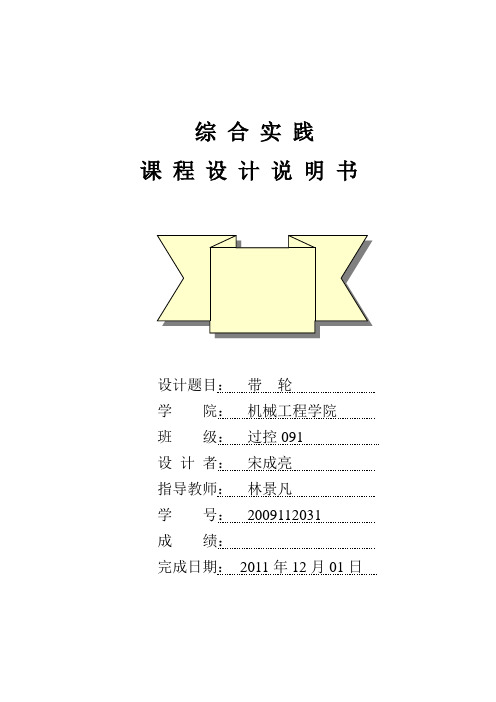
综合实践课程设计说明书设计题目:带轮学院:机械工程学院班级:过控091设计者:宋成亮指导教师:林景凡学号:2009112031成绩:完成日期:2011年12月01日目录一、关键字-------------------------------------------------------------------3二、摘要----------------------------------------------------------------------4三、铸造工艺方案制定-----------------------------------------------------51:材料分析------------------------------------------------------------5 2:铸造方法------------------------------------------------------------5 3:分型面的选择------------------------------------------------------5 4:铸件形状------------------------------------------------------------6 5:工艺参数------------------------------------------------------------6 6:质量及浇注系统的计算------------------------------------------7 7:冒口计算------------------------------------------------------------8 四、机械加工工艺---------------------------------------------------------81:工艺分析------------------------------------------------------------8 2:基准的选择---------------------------------------------------------8 3:刀具与机床夹具的选择------------------------------------------8 4:切削液的选择和使用--------------------------------------------------9 5:工艺过程------------------------------------------------------------9 6:机械加工工艺卡片----------------------------------------------------9五、参考文献--------------------------------------------------------------------14六、指导教师评语------------------------------------------------------------15 附件1:零件图附件2:毛坯图附件3:工艺图一、关键字:带轮、铸造工艺、机械加工一;摘要对于此课题为《皮带轮》的课程设计,通过对所给材料的性能分析,确定加工方法,此例为铸造,然后根据零件图确定铸件图,铸造工艺图,及铸造方案,通过查铸造手册确定加工余量,收缩率,浇注系统等,考虑是否留冒口,尽量使铸件无夹渣、气孔等缺陷,得到铸件后进行机械加工,根据零件图上所需零件形状及粗糙度选择刀具及加工方法,确定基准,确定背吃刀量,最后得到成品。
皮带轮规格优化设计原则与方法

皮带轮规格优化设计原则与方法皮带轮是一种常见的传动装置,广泛应用于各种机械设备中。
合理设计皮带轮的规格可以提高传动效率、延长使用寿命,并降低设备故障率。
本文将探讨皮带轮规格优化的设计原则与方法。
一、选取合适的材料皮带轮的材料选择直接影响到其使用寿命和传动效率。
一般情况下,选择淬火齿轮钢或铸铁作为皮带轮的材料,具有较高的强度和硬度,能够承受较大的负荷和使用压力。
此外,材料的热处理也十分重要,通过适当的温度和时间控制可以进一步提高材料的强度和硬度。
二、确定皮带轮的直径皮带轮的直径直接影响到传动效率和传动比。
在设计过程中,需要综合考虑驱动电机的转速、传动带的宽度和张力等因素。
一般来说,皮带轮的直径越大,其传动效率越高,但同时也会增加设备的尺寸和重量。
因此,在确定皮带轮的直径时,需要在满足传动要求的基础上,尽可能选择较小的直径,以便节约空间和材料成本。
三、考虑皮带轮的齿数皮带轮的齿数是指其齿轮的数量,也与传动比有关。
传统方法是根据所需的传动比和带速来计算。
然而,在实际设计中,还需要考虑到传动带的最小齿数和弯曲半径等因素。
通常情况下,应选择满足最小齿数和最小弯曲半径的齿数组合,以确保皮带轮的正常运转和使用寿命。
四、优化皮带轮的结构除了考虑皮带轮的材料、直径和齿数外,还可以通过优化其结构来提高传动效率和减少噪声。
例如,使用轻量化的结构设计可以减小惯性,降低能量损耗;采用凸弧齿轮设计可以改善齿轮的接触性能,减小传动噪声。
此外,还可以通过加工精度和装配质量的提高来进一步改善传动性能。
五、进行仿真和试验验证在最后的设计阶段,可以通过使用计算机仿真软件或进行实际试验来验证皮带轮的设计方案。
通过仿真和试验可以评估传动效率、噪声水平、振动情况等指标,以进一步优化设计,并在实际应用中进行性能验证。
综上所述,皮带轮规格的优化设计是一个综合考虑材料、直径、齿数和结构等因素的过程。
合理选择材料、确定直径和齿数,优化结构,并通过仿真和试验验证,可以提高皮带轮的传动效率和使用寿命,从而为机械设备的正常运行提供可靠的支持。
曲轴减振皮带轮的设计myself

?
J eJ d?
M e (kd ? ? 2 J d ) 4 ? ( J d kd ? J d ke ? J e kd )? 2 ? kekd
(3)
由上式可见,系统有两
个共振频率
?
n1和?
,一个反共振频率
n2
?
2 an
?
kd
/ Jd
?
?
2。
d
在? n1和? n2处, Ae的幅值为无穷大,在 ? an处, Ae的幅值为零。
1、调频 调整曲轴扭振固有频率的基本方法是调整系统的转动惯量、扭转刚度及 分布规律。由于系统各阶固有频率对转动惯量、扭转刚度变化的灵敏度 不同,不同频率振型下的调频方案也不同。具体说来,节点及其附近刚 度的变化和远离节点的转动惯量的变化对固有频率影响最大。根据这个 特点,理论上可以做到仅调整某阶固有频率和使其他阶固有频率基本不 变。
三、扭振减振器设计
扭振减振器的设计主要是正确合理的确定减振器的三个基本参数 ?减振器惯性元件的转动惯量J d ?弹性元件的刚度 Kd ?以及阻尼比?
我们将原系统简化为一单扭摆,加上减振器后形成双扭摆。这种模型可以
反映原系统的基本扭转特性,由它可以导出减振器设计的基本概念。
对自由度系统简化为单扭摆的原则是使简化前后的固有频率相同,振动时
?
J d ke
?
J e kd
)?
2
?
ke kd ) 2
??
2
C
2 d
[
ke
??
2 (Je
?
J d )]2
ΔA为幅值差,为了说明阻尼弹性减振器的减振特性,首先讨论两种特 殊情况下Ae的变化曲线。
1、当减振器阻尼为零时,即Cd=0或ξ=0,图2所示系统变为无阻尼双 扭摆系统,式(2)中的Ae式简化为:
皮带轮设计要点
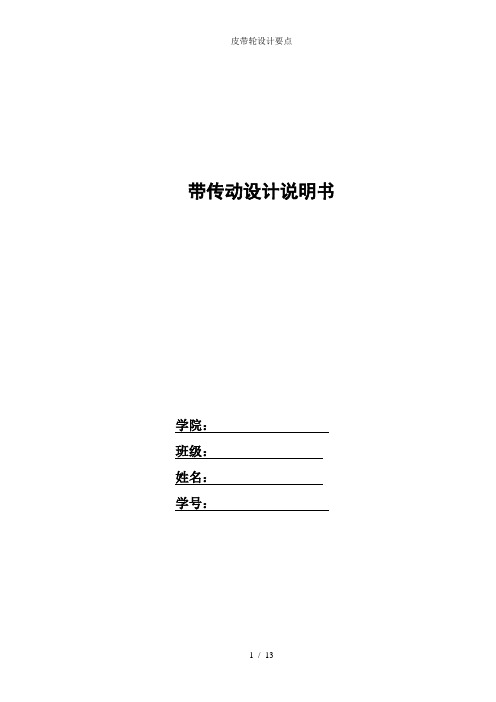
带传动设计说明书学院:班级:姓名:学号:原始数据如下:项目 参数电机功率 3.0KW电机转速 1430rpm减速器输入轴转速614rpm电机型号 Y100L2-4减速器中心高 125mm根据电机型号查得其参数如下:型号 Y100L2-4额定功率 3.0KW额定电流 6.8A转速 1430rpm轴伸端直径28mm1. 普通V 带传动的设计计算1.1 确定计算功率 计算功率ca P 是根据传递的功率P 和带的工作条件而确定的:P K P A ca =。
其中,已知KW P 0.3=。
(表8-8)根据表8-8得:1.1=A K 。
KW P K P A ca 3.331.1=⨯==KW P ca 3.3=1.2 V 带带型的选择已知计算功率KW P ca 3.3=,小带轮转速rpm n 14301=,然后根据表8-11得:V 带的带型为A 型带。
1.3 确定带轮的基准直径d d 并验算带速v 1.3.1 初选小带轮的基准直径1d d 由1.2得V 带为A 型带,然后根据表8-7和表8-9得: mm d d 1001=,同时满足mm d d d d 75min1=≥)(。
槽型 Y Z A B C D Ed 20 50 75 125 200 355 500 表8-71.3.2 验算带速v 因为带速不宜过低或过高,一般应使s m v /25~5=,最高不超过s m /30,所以应该进行带速v 的验算。
根据公式10006011⨯=n d v d π得:s m n d v d /49.7100060143010010006011=⨯⨯⨯=⨯=ππ,满足条件。
1.3.3 计算大带轮的基准直径根据公式12d d id d =可得2d d 。
V 带为A 型带mm d d 1001=s m v /49.7= 满足条件(腹板式)由图8-14的经验公式,可确定:m md L m mB C m mC m m f e z B m m h d d m md m m d d m md a d a d 5.50288.1)2~5.1(84861)41~71(1489215)13(2)1(5.10575.2210021002.53289.1)2~8.1(281=⨯===⨯=='==⨯+⨯-=+-==⨯+=+===⨯=== 小带轮和轴之间采用平键连接,根据轴的直径mm d 28=,查表GB/T1095-2003可得:mm h mm b 7,8==。
皮带轮设计
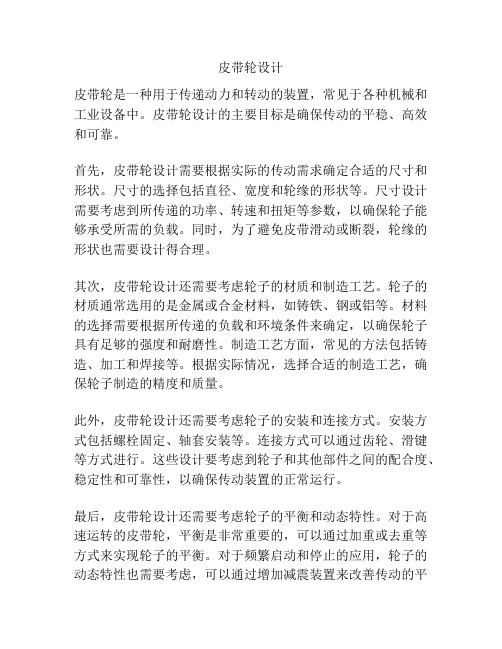
皮带轮设计
皮带轮是一种用于传递动力和转动的装置,常见于各种机械和工业设备中。
皮带轮设计的主要目标是确保传动的平稳、高效和可靠。
首先,皮带轮设计需要根据实际的传动需求确定合适的尺寸和形状。
尺寸的选择包括直径、宽度和轮缘的形状等。
尺寸设计需要考虑到所传递的功率、转速和扭矩等参数,以确保轮子能够承受所需的负载。
同时,为了避免皮带滑动或断裂,轮缘的形状也需要设计得合理。
其次,皮带轮设计还需要考虑轮子的材质和制造工艺。
轮子的材质通常选用的是金属或合金材料,如铸铁、钢或铝等。
材料的选择需要根据所传递的负载和环境条件来确定,以确保轮子具有足够的强度和耐磨性。
制造工艺方面,常见的方法包括铸造、加工和焊接等。
根据实际情况,选择合适的制造工艺,确保轮子制造的精度和质量。
此外,皮带轮设计还需要考虑轮子的安装和连接方式。
安装方式包括螺栓固定、轴套安装等。
连接方式可以通过齿轮、滑键等方式进行。
这些设计要考虑到轮子和其他部件之间的配合度、稳定性和可靠性,以确保传动装置的正常运行。
最后,皮带轮设计还需要考虑轮子的平衡和动态特性。
对于高速运转的皮带轮,平衡是非常重要的,可以通过加重或去重等方式来实现轮子的平衡。
对于频繁启动和停止的应用,轮子的动态特性也需要考虑,可以通过增加减震装置来改善传动的平
稳性。
总之,皮带轮设计需要综合考虑传动需求、材质选择、制造工艺、安装和连接方式以及平衡和动态特性等因素。
只有在全面考虑各种因素的基础上,才能设计出高效、稳定和可靠的皮带轮。
发动机曲轴皮带轮装配问题分析与解决
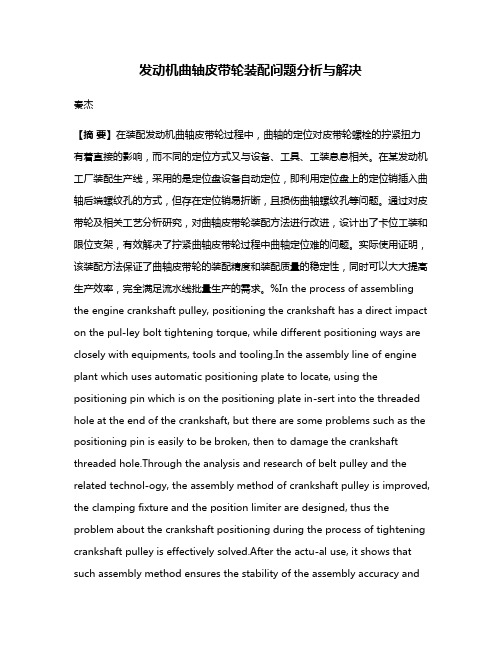
发动机曲轴皮带轮装配问题分析与解决秦杰【摘要】在装配发动机曲轴皮带轮过程中,曲轴的定位对皮带轮螺栓的拧紧扭力有着直接的影响,而不同的定位方式又与设备、工具、工装息息相关。
在某发动机工厂装配生产线,采用的是定位盘设备自动定位,即利用定位盘上的定位销插入曲轴后端螺纹孔的方式,但存在定位销易折断,且损伤曲轴螺纹孔等问题。
通过对皮带轮及相关工艺分析研究,对曲轴皮带轮装配方法进行改进,设计出了卡位工装和限位支架,有效解决了拧紧曲轴皮带轮过程中曲轴定位难的问题。
实际使用证明,该装配方法保证了曲轴皮带轮的装配精度和装配质量的稳定性,同时可以大大提高生产效率,完全满足流水线批量生产的需求。
%In the process of assembling the engine crankshaft pulley, positioning the crankshaft has a direct impact on the pul-ley bolt tightening torque, while different positioning ways are closely with equipments, tools and tooling.In the assembly line of engine plant which uses automatic positioning plate to locate, using the positioning pin which is on the positioning plate in-sert into the threaded hole at the end of the crankshaft, but there are some problems such as the positioning pin is easily to be broken, then to damage the crankshaft threaded hole.Through the analysis and research of belt pulley and the related technol-ogy, the assembly method of crankshaft pulley is improved, the clamping fixture and the position limiter are designed, thus the problem about the crankshaft positioning during the process of tightening crankshaft pulley is effectively solved.After the actu-al use, it shows that such assembly method ensures the stability of the assembly accuracy andthe assembly quality of the crankshaft pulley, at the same time, it can greatly improves the production efficiency, and entirely meet the needs of mass pro-duction of assembly line.【期刊名称】《机械研究与应用》【年(卷),期】2016(000)001【总页数】4页(P202-204,207)【关键词】曲轴皮带轮;装配;卡位工装;限位支架【作者】秦杰【作者单位】上汽通用五菱汽车股份有限公司,广西柳州 545007【正文语种】中文【中图分类】V472曲轴皮带轮是汽油机上的关键功能部件之一,安装在曲轴前端,随曲轴一起旋转。
- 1、下载文档前请自行甄别文档内容的完整性,平台不提供额外的编辑、内容补充、找答案等附加服务。
- 2、"仅部分预览"的文档,不可在线预览部分如存在完整性等问题,可反馈申请退款(可完整预览的文档不适用该条件!)。
- 3、如文档侵犯您的权益,请联系客服反馈,我们会尽快为您处理(人工客服工作时间:9:00-18:30)。
(3)
2 2 由上式可见,系统有两 个共振频率n1和n 2,一个反共振频率 an kd / J d d 。
2 2 kd 2Cd 2 ( J e J d 4 ( J d k d J d ke J e k d ) 2 k e k d ) 2 2Cd [ke 2 ( J e பைடு நூலகம் d )]2 2 ( k d 2 J d ) 2 2Cd (2) 4 2 2 2 2 2 2 ( J e J d ( J d k d J d ke J e k d ) k e k d ) Cd [k e ( J e J d )]
J e J i i2
i 1 2 K e n Je
n
式中,n 为原系统需避开的那个固有频率;Ji 为原系统第i个惯性刚形体 元件的转动惯量;i 为与 n 相对应的固有振型中,第i个惯性刚性体元件 的相对振幅。
3.1橡胶减振器的作用原理及模型化计算
当减振器主动件与惯性元件之间由橡胶弹性元件连接时,即构成橡胶阻尼 弹性减振器。图1所示为橡胶减振器的结构图;图2为原系统简化为扭摆, 装上减振器后便成为双扭摆模型。 1 2
3
图1 橡胶减振器结构图 1-带轮 2-橡胶环 3-轮毂
图2、双扭摆模型
根据达朗贝尔定理
S+Mc+U=0
即
I C k 0
其中:S表示惯性矩; Mc 表示与振动方向相反的抵抗力矩; U表示轴的弹性力矩。 得到其运动方程:
J d d Cd ( d e ) K d ( d e ) 0
三、扭振减振器设计
扭振减振器的设计主要是正确合理的确定减振器的三个基本参数 减振器惯性元件的转动惯量J d 弹性元件的刚度 K d 以及阻尼比 我们将原系统简化为一单扭摆,加上减振器后形成双扭摆。这种模型可以 反映原系统的基本扭转特性,由它可以导出减振器设计的基本概念。 对自由度系统简化为单扭摆的原则是使简化前后的固有频率相同,振动时 系统能量,由此可得单扭摆的当量转动惯量 J e 与刚度 K e 为
1、调频 调整曲轴扭振固有频率的基本方法是调整系统的转动惯量、扭转刚度及 分布规律。由于系统各阶固有频率对转动惯量、扭转刚度变化的灵敏度 不同,不同频率振型下的调频方案也不同。具体说来,节点及其附近刚 度的变化和远离节点的转动惯量的变化对固有频率影响最大。根据这个 特点,理论上可以做到仅调整某阶固有频率和使其他阶固有频率基本不 变。
2、配置减振器 配置减振器是减小振动、降低扭振应力的一个重要措施。 阻尼减振器能为系统提供很大的阻尼,以加大系统振动能量的耗散,其中 以橡胶和硅油减振器应用最为广泛。 动力减振器利用子系统共振时的动力效应来减小成抵消原系统共振时的激 励力矩,同时由于安装了减振器也改变了原系统的固有频率。 3、减少输入系统的扭转能量 降低发动机输入系统的扭振能量的基本点是靠减小相对振幅矢量和。影响 相对振幅矢量和大小的主要因素是系统振型和激振力矩矢量图。后者取决 于发动机的曲柄排列、发火顺序和简谐次数。
(1)
J e e Cd (e d ) K d (e d ) K e(e d ) M e e jwt
式中,Kd、Cd为减振器惯性元件与主动件间连接刚度与阻尼。
设方程的解为 d Ad e i (t ed ) , e Ae e i (t ee ),带入式( 1 )得 Ad M e Ae M e A
M e 2 J d
2 ( J e J d 4 ( J d k d J d ke J e k d ) 2 k e k d ) 2 2Cd [k e 2 ( J e J d )]2
ΔA为幅值差,为了说明阻尼弹性减振器的减振特性,首先讨论两种特 殊情况下Ae的变化曲线。 1、当减振器阻尼为零时,即Cd=0或ξ=0,图2所示系统变为无阻尼双 扭摆系统,式(2)中的Ae式简化为:
扭转减振器的种类
单级扭转减振器
二级扭转减振器
三级并联扭转减振器
硅油—橡胶复合式扭转减振器
两级串联式减振器
弯曲复合式减振器
二、扭转振动的消减方法
扭振振动的消减与回避大致包括调频、配置减振器、减少输入系统 的振动能量和简单回避等几方面的措施 调频就是调整系统的固有频率,使严重的共振转速远离工作转速或常用 工作转速范围。 减振器有两大类:增加系统阻尼以减小振幅、降低应力的阻尼减振器; 利用子系统共振时的动力效应产生的反向力矩以抵消共振力矩的动力减 振器。 减少输入系统的振动能量主要是靠减小发动机相对振幅矢量和。
曲轴减振皮带轮的设计
龚明成 2014.4.4
目录
一、减振器的功能和种类
二、扭转振动的消减方法 三、扭振减振器设计 3.1橡胶减振器的作用原理及模型化计算 3.2橡胶阻尼减振器的参数设定 四、总结
一、扭转减振器的功能和种类
当发动机工作时,曲轴系统将会同时产生弯曲振动和扭转振动, 因为曲轴一般均采用全支撑结构,弯曲刚度较大,所以弯曲振动的自 然频率较高,一般不研究。 对扭转振动而言,由于曲轴较长,扭转刚度较小,而且曲轴轴系的转 动惯量又较大,故曲轴扭振的频率较低,在内燃机工作转速范围内容 易产生共振, 当发动机转矩的变化频率与曲轴扭转的自振频率相同或 成整数倍时,就会发生共振。共振时扭振振幅增大,并导致传动机构 磨损加剧,发动机功率下降,甚至曲轴断裂。因此,扭转振动时内燃 机设计过程中必须考虑的重要因素。 为了降低曲轴的振动,一般采用加装曲轴减振器,但其他方式再后面 也将简略提到。 扭转减振器的功能 1)消减曲轴扭转振动,提高曲轴的疲劳寿命,减少应力水平; 2)传递扭矩,衰减扭矩波动; 3)减少整车的振动、噪音。