机插印制板设计要求
机插印制板设计要求

③元器件插件密度限制(P :插入跨距
Y方向不可插入区域 X方向不可插入区域 单位:mm)
4
3
P
2.1 3
2.2
4
P+4.2
P+2
3
P+6
.
2.3mm
A
2.6mm A先插入
B 2.3mm
2.3mm
2.8mm
.
A B
2.3mm B先插入
3.4mm A先插入
2.3mm B先插入
2、轴向元件排版要求
①印制板传板方向上、下边距边缘5mm内不应有元件。 ②定位孔附近不可机插区域。(单位:mm)
机插印制板设计要求
1、印制板的外形尺寸。
厚度:1.60±0.10mm 长度:150~330mm 宽度:50~250mm
2、印制板翘曲度
插件方向
Max: 1.2mm
Max: 0.5mm
3、印制板定位孔的要求
机插板允许其中一个定位孔为长孔,但松下和环球插件机传板方
向不一致,如需贴片翻板后孔位置也将变化,建议两定位孔参数一
(3.6+d)/2
轴向与轴向元件 d为引脚直径,D为本体直径
(3.6+d1)/2 或 (D1+D2)/2
(3.6+d)/2
(3+D1)/2 或 (3.6+d1)/2
(3.6+d)/2 (2.0+d)/2
A B
(3.6+d1)/2
(2+D)/2 A先插入 (3.6+d1)/2 B先插入
(4+d)/2
A
60°
“V”型槽
0.4mm 0.3mm
PCB设计要求(手工插件)

贴片板的尺寸尽量掌握在长度 100-300mm 之间,插件板的尺寸必尽量掌握在长度 50-330mm 之 根本原则在进展印制板设计时,应考虑本标准所述的四个根本原则。
1.1 电气连接的准确性印制板设计时,应使用电原理图所规定的元器件,印制导线的连接关系应与电原理图导线连接关系相全都,印制板和电原理图上元件序号应一一对应。
注:如因构造、电气性能或其它物理性能要求不宜在印制板上布设的导线,应在相应文件〔如电原理图上〕上做相应修改。
1.2 牢靠性和安全性印制板电路设计应符合电磁兼容和电器安规的要求。
1.3 工艺性印制板电路设计时,应考虑印制板制造工艺和电控装配工艺的要求,尽可能有利于制造、装配和修理,降低焊接不良率。
1.4 经济性印制板电路设计在满足使用的安全性和牢靠性要求的前提下,应充分考虑其设计方法、选择的基材、制造工艺等,力求经济有用,本钱最低。
1 技术要求 1.1印制板的选用1.1.1 印制电路板的层的选择一般状况下,应中选择单面板。
在构造受到限制或其他特别状况下,可以选择用多层板设计。
1.1.2 印制电路板的材料和品牌的选择1.1.2.1 双面板应承受玻璃纤维板FR-4、CEM-3,CEM-22F ,单面板应承受半玻纤板CEM-11.1.2.2 印制板材料的厚度选用 1.6mm ,双面铜层厚度一般为 0.5 盎司,大电流则可选择两面都为 1 盎司, 单面铜层厚度一般为 1 盎司。
特别状况下,假设品质可以得到确保,可以选择其他厚度的印制板。
1.1.2.3 印制板材料的性能应符合企业标准的要求。
1.1.3 印制电路板的工艺要求双面板原则上应当是喷锡板〔除含有金手指的遥控器板和显示板外〕,单面板原则上假设有机插或贴片工艺原则上也必需是喷锡板〔或辘锡〕,以防止焊盘上的抗氧化膜被破坏且储存时间较长后引起焊接质量受到影响,在相关的技术文件的支持下,可承受抗氧化膜工艺的单面板。
1.2 自动插件和贴片方案的选择双面板尽可能承受贴片设计,单面板尽可能承受自动插件方案设计,应避开同一块板既承受贴片方案又同时承受自动插件方案设计,以免铺张设备资源。
印制电路板PCB行业标准概述

面 , 目前 主 要 生 产 商 都 是 直 接 采 用 英 国 IC或 -'R一 材 料 标 准 ) 美 J ̄ 4 h 。
■■一 [ 陋翰剐勘删 ‘ I = '" D lIIf COH . _ 二…I , - e
T 291 子 技 本 专 门 办 公 室 负 责 电 子 装 联 和 印 制 板 方 面 C5 / 电 标 准 的 制 定 、 修 订 工 作 , 目前 已 制 定 了 有 关 印 制 板 设 计 、 制 造 和 电 子 装 联 技 术 标 准 和 规 范 1 0余 项 。 涉 及 到 印 制 板 0 及 其 组 装 件 设 计 、 材 料 、 各 类 型 产 品 、 制 造 技 术 及 测 试 方 法 和 质量 保 证 等 方面 ,构 成 一个 相 互 配套 的体 系 。IC E 是 由 多 个 国 家 组 成 的 电 气 电 子 产 品 标 准 化 技 术 组 织 。 标 准 制 定 过 程 需 要 多 国 协 商 和 协 调 , 因 而 标 准 的 制 定 修 订 速 度 相 对 较 慢 、 配 套 性 尚 不 完 善 。 通 用 性 要 求 多 ,详 细 要 求 少 。
印 制 板 的 设 汁 是 涉 及 电 路 设 计 、元 器 件 应 用 、 印 制 板
材料 、制造 、安 装 和测 试等 不 同技 术范 畴 的 多种 材 料和 工 艺技 术 ,若要 将这 些技 术 有机地 结合 在一 起 形 成一 个 完整 的设 计产 品就 需要标 准 标准 是联 系不 同材 料 和技本 结合 的
lC 准 ,部 分 参 照 采 用 lC标 准 , 但 是 在 印 制 板 基 材 方 E 标 P
执 行起 来还 要 以本 国 或用 户的 标准作 为支撑 。 技 术 发达 国 家标 准 ,主 要有 美 国 、英 国 、 I本 等 国 , E I
印刷电路板(PCB)设计规范20(03518)
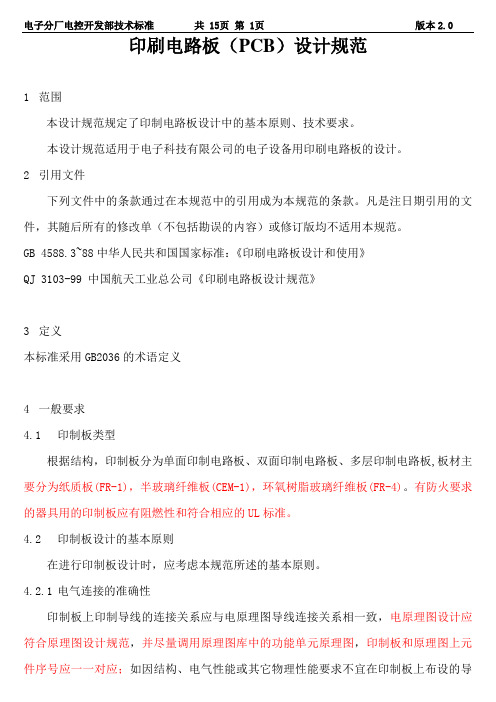
印刷电路板(PCB)设计规范1范围本设计规范规定了印制电路板设计中的基本原则、技术要求。
本设计规范适用于电子科技有限公司的电子设备用印刷电路板的设计。
2引用文件下列文件中的条款通过在本规范中的引用成为本规范的条款。
凡是注日期引用的文件,其随后所有的修改单(不包括勘误的内容)或修订版均不适用本规范。
GB 4588.3~88中华人民共和国国家标准:《印刷电路板设计和使用》QJ 3103-99 中国航天工业总公司《印刷电路板设计规范》3定义本标准采用GB2036的术语定义4一般要求4.1印制板类型根据结构,印制板分为单面印制电路板、双面印制电路板、多层印制电路板,板材主要分为纸质板(FR-1),半玻璃纤维板(CEM-1),环氧树脂玻璃纤维板(FR-4)。
有防火要求的器具用的印制板应有阻燃性和符合相应的UL标准。
4.2印制板设计的基本原则在进行印制板设计时,应考虑本规范所述的基本原则。
4.2.1电气连接的准确性印制板上印制导线的连接关系应与电原理图导线连接关系相一致,电原理图设计应符合原理图设计规范,并尽量调用原理图库中的功能单元原理图,印制板和原理图上元件序号应一一对应;如因结构、电气性能或其它物理性能要求不宜在印制板上布设的导线,应在相应文件(如电原理图上)上做相应修改。
4.2.2可靠性印制板应符合其产品要求的相应EMC规范和安规要求,并留有余量,以减小日益严重的电磁环境的影响。
影响印制板可靠性的因素很多,印制板的结构、基材的选用、印制板的制造和装配工艺以及印制板的布线、导线宽度和间距等都会影响到印制板的可靠性。
设计时必须综合考虑以上的因素,按照规范的要求,并尽可能的保留余量,以提高可靠性。
4.2.3工艺性设计电路板时应考虑印制板的制造工艺和装配工艺要求,尽可能有利于制造、装配和维修,各具体要求请严格遵守QG/MK03.04-2003V的工艺规范。
4.2.4经济性印制板设计应充分考虑其设计方法、选择的基材、制造工艺等成本最低的原则,满足使用的安全性和可靠性要求的前提下,力求经济实用。
GJB-QR-13-22 工艺总方案

修订记录目录1 概述 (1)2 工艺总方案依据、设计原则及执行标准 (1)2.1依据 (1)2.2工艺方案设计原则 (1)2.3引用标准 (1)3 产品的特点、组成及主要工艺技术 (2)3.1产品特点 (2)3.2组成 (2)3.3主要工艺部分 (2)4 产品工艺流程制造路线及分工 (3)4.1主要工艺流程 (3)4.2产品制造分工 (3)4.3产品工艺分析 (4)4.3.1 印制电路板的加工工艺 (4)4.3.2 结构件机加工艺及表面处理工艺 (4)4.3.3 组装、总装和调试工艺分析 (5)4.3.3.1 印制板组件特点 (5)4.3.3.2 模块、整机的装配工艺 (5)4.3.3.3 调试工艺 (5)4.3.4 包装工艺 (6)4.3.5 “三防”处理 (6)4.3.5.1 印制电路板组件的“三防” (6)4.3.5.2 结构件的“三防” (6)5 产品工艺质量保证措施及特殊安全、环保措施 (7)5.1静电防护 (7)5.2零部件防护控制 (7)5.3环境应力筛选 (7)5.3.1 模块筛选项目及程序 (7)5.3.2 筛选试验要求 (8)5.3.2.1 温度循环(缺陷剔除) (8)5.3.2.2 温度循环无故障检验试验 (8)6 外协加工的项目和要求 (9)6.1外协件的确定 (9)6.2外协件的检验方式和手段 (9)7 工艺关键项目及攻关措施、工艺试验项目 (10)7.1关键工序设置 (10)7.2质控点设置分析 (10)7.3工艺试验项目 (10)8 采用新技术、新材料、新工艺情况 (10)9 首件鉴定项目及实施要求 (10)10 工艺装备、试验和检测设备的选择 (11)10.1工艺装备要求 (11)10.2试验设备的要求如下: (11)11 制造过程中产品技术状态的控制要求 (11)12 工艺标准化要求 (11)13 工艺准备过程中形成的文件和具体要求 (12)14 工艺总方案的动态管理情况 (12)XXXX工艺总方案1概述88219.3XXXX是为XXXX所XXXX导航单元系统配套的产品。
电子装配对PCB设计要求

MAX 30 mm
图5
图6
3.
贴片对PCB设计要求
图1
自动插机对PCB要求
一、 印制板的插机定位孔 1.采用电插的印制板应在最长的一条边上设置主副两个电插定位孔。如图2 所示(元件面)。其中左下角为主定位孔,孔径为Ø4.0mm;右下角副 定位孔,其孔径尺寸应为Ø4.0mm的鹅蛋形定位孔
元件面
。L±Leabharlann .15.0±0.15.0±0.1 图2
Min 3.0
自动插机对PCB板要求
2. 两定位孔的中心轴连线平行于最长边,离最长边的距离为 5.0±0.1mm,主定位孔与左边的距离为5.0±0.1mm,副定位孔孔 边与右边的距离应不小于3.0mm,定位孔周围从孔边向外至少 2mm 范围内应覆铜箔以增加板的机械强度。
自动插机对PCB板要求
3.主副两定位孔的中心距L的优选系列为:290mm、235mm、350mm。 4.电插定位孔在元件面标记符号图中用方框标示。 二、印制板的非电插区 1.在非电插区内布置的元件(其插孔在此区内)不适用于电插机。 2.对于卧插元件,其非电插区(定位盲区和边缘盲区)为图3所示画有剖线 的区域。
贴片对PCB设计要求
1. 2. 要求PCB尺寸大于50X50mm。 PCB上对角处至少有2个MARK点(一角一个),MARK点直径 1mm。MARK点、焊盘边缘离走机器轨道的一边边缘距离大于 3.5mm,装配时优先使用长边走轨道(这样走板比较顺畅稳 定),要求焊盘、MARK点离长边边缘距离大于3.5mm,否则被 轨道夹住,不易装配,需加工艺边,工艺边宽度满足上述要求即 可,若板子较大,需短边走轨道,则MARK点、焊盘离短边边缘 距离大于3.5mm。走轨道的一边尽量规则,无或少缺口。 对于PCB尺寸大于50X50mm的,不做拼板可装配,但不是很大 的(比50X50mm稍大一点的)量较大,需做成拼板装配,可以 提高装配效率,走板也顺畅,易装配。
印制电路板的设计与制作培训课件
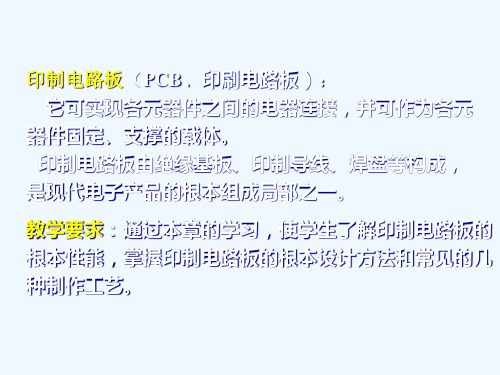
4.元器件排列方式 不规那么排列:指元器件轴线方向不一致,在板上的排 列顺序无规那么。其优点是印制导线短而少,减小了印 制电路板间的分布参数,抑制了干扰。尤其是对于高频 电路有利。但看起来杂乱无章,不太美观。
规那么排列:是指元器件轴线方向排列一致,并与印 制电路板的四周垂直或平行。其优点是元器件排列标 准,板面美观整齐,安装、调试、维修方便。但导线 布设较为复杂,印制导线相应增多。
一、设计印制电路板的准备工作
1.印制电路板的设计前提 ➢确定设计方案,完成电路设计; ➢元器件的选择; ➢仿真验证; ➢电路方案试验; ➢对电路试验结果的分析及对电路设计的改进; ➢考虑整机的机械结构和安装使用。
2. 印制电路板的设计目标 ➢ 准确性:元器件和印制导线的连接关系必须符合印制
板的电气原理图。 ➢ 可靠性:印制电路板的可靠性是影响电子设备可靠性
5. 元器件焊盘的定位 ➢焊盘的中心(即引线孔的中心)距离印制板的边缘不 能太近,一般距离应在2.5mm以上,至少应该大于板 的厚度。 ➢焊盘的位置一般要求落在正交网格的交点上,如图415所示。在国际IEC标准中,正交网格的标准格距为 2.54mm(0.1in);国内的标准是2.5mm。
§4.3 印制电路板上的焊盘及导线
四、印制导线的抗干扰和屏蔽
1. 地线布置引起的干扰
原因:
I1
I2
如印制导线AB长为10cm
要尽可能防止异形孔,以便降低加工本钱。
2. 焊盘的外径
密度的单面电路板: Dmin=d+1mm
双面电路板: Dmin≥2d
D
3. 焊盘的形状
岛形焊盘:
适用于元器件密集、不规那 么排列的电子产品。由于焊盘 面积大,抗剥离强度增大,可 以降低覆铜板的档次。
PCB生产工艺流程设计规范
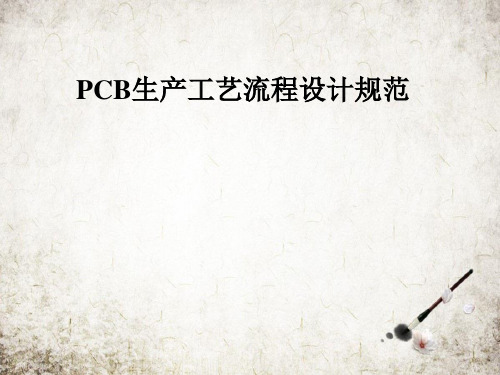
一次銅
D、外层干膜流程介绍
☺ 流程介绍:
前处理
压膜
曝光
显影
☺ 目的:
经过钻孔及通孔电镀后,内外层已经连通,本制程制作外 层干膜,为外层线路的制作提供图形。
外层干膜—前处理介绍
☺ 前处理:
目的:去除铜面上的污染物,增加铜面粗糙度,以利于压膜制程 重要原物料:磨刷
☺ 压膜(Lamination):
分类以及它的制造工艺。
A. 以材料分 a. 有机材料 酚醛树脂、玻璃纤维/环氧树脂、Polyimide、BT等皆属之。 b. 无机材料 铝基板、铜基板、陶瓷基板等皆属之,主要取其散熱功能。
B. 以成品软硬区分 a. 硬板 Rigid PCB b. 软板 Flexible PCB 见图1.3 c. 软硬结合板 Rigid-Flex PCB 见图1.4
晶圓
第0層次
第4層次 (Gate)
第3層次 (Board)
第1層次 (Module)
第2層次 (Card)
– 2、PCB的演变
1.早於1903年Mr. Albert Hanson(阿尔伯特.汉森)首创利用“线路 ”(Circuit)观念应用于电话交换系统上。它是用金属箔切割成线路导体,将 之粘于石蜡纸上,上面同样粘上一层石蜡纸,成了现今PCB的构造雏形。如 下图:
2L 3L 4L 5L
Layer 1 Layer 2 Layer 3 Layer 4 Layer 5 Layer 6
层压工艺—压合介绍
• 压合:
• 目的:通过热压方式将叠合板压成多层板 • 主要生产辅料: 牛皮纸、钢板
压力
可叠很多层
热板
钢板 牛皮纸 承载盘
层压工艺—后处理介绍
• 后处理: • 目的: • 对层压后的板经过磨边;打靶;铣边等工序进行初步的外形处理以便后
- 1、下载文档前请自行甄别文档内容的完整性,平台不提供额外的编辑、内容补充、找答案等附加服务。
- 2、"仅部分预览"的文档,不可在线预览部分如存在完整性等问题,可反馈申请退款(可完整预览的文档不适用该条件!)。
- 3、如文档侵犯您的权益,请联系客服反馈,我们会尽快为您处理(人工客服工作时间:9:00-18:30)。
-0
32.2
-0.5
-0.2
-0.05
项目 W2
T1
T2
B
参数 ≥5.5≤ 0.6 ≥0.6≤ ≤1.0
mm
18 ±0.3 1.5
插件机效率 ①标称速度: M:0.369
K: 0.16
Z: 0.32
J: 0.468
(4+d1)/2 (4+d1)/2 A先插入 (3.6+d1)/2 B先插入
2、径向元件排版要求
①印制板传板方向上、下边距边缘5mm内不应有元件。
②定位孔附近不可机插区域。(单位:mm)
Y
12
已插元件 X 14.2
③元件面的插件密度限制(单位:mm)
插入元件
插入元件引脚
45°
0.2
9.2
0.2
1.27
5.0
a
b
3.2
机插元器件要求
1. 铆钉
L1 R1
R2
L3
L2
H2 H1
尺寸
L1 L2 L3 H1 H2 R1 R2
大铆钉 小铆钉
2.5*3.5 1.6*2.8
4±0.05 3.1±0.05
2.5±0.05 2.1±0.05 3.5±0.15 0.5±0.05
1.6±0.02 1.34±0.05
2.8±0.1 0.4±0.1
D
已插元件高度+0.5mm
D
D>3.5或D>插入元件半径+0.2mm
D>5或D>插入元件半径+0.2mm
③铜泊面的插件密度限制(单位:mm)
a
b
3.8
a
b
4.0
a
b
3.7(a先插入) 3.9(b先插入) 5.0(b先插入,其一为三极管)
a b
3.4
5.0
b a
3.3(a先插入) 5.7(b先插入)
φ1.2+00。1 φ1.0+00。1
φ1.4+00。1 φ1.2+00。1
φ0.5±0.05
Φ0.9+00。1
φ1.1+00。1
φ0.4±0.05
Φ0.8+00。1
φ1.0+00。1
③一致性要求: 为保证插件机的正常运转,对同种印制板(含不
同模号)的一致性要求为任意两块印制板相同孔位的实际位置之
差为0.1mm之内。
Y方向不可插入区域 X方向不可插入区域
③元器件的插件密度限制(单位:mm)
P
P
L4
L1 L2
印制板
L4
L3
插件头部位导致死区
砧座剪切部位导致死区
2. 5 3. 6
P:插入跨距 L1:P+2.0 L2:P+7.5 L3:P+2.0 L4:P+4(基板 下方1mm)
6
3
轴向元件与已插跨线 (d为跨线直径)
0.25
0.2
0.15
0.1
2. 跨线 跨线要求为Ф0.6±0.02mm的镀锡铜线。
3. 轴向件
R
B S
T
R
Z P
S T
单位:mm W=52+00.2 P=5±0.3(连续20只元件的累 计误差不得超过±2) |L1-L2|≤0.2 T=6±1
Z≤1.0
B≥3.2
S≤0.8 R=0
3. 径向件
P
(3.6+d)/2 (3.6+d)/2 (3.6+d)/2 (2.0+d)/2
(4+d)/2
(4+d)/2
பைடு நூலகம்轴向与轴向元件 d为引脚直径,D为本体直径
(3.6+d1)/2 或 (D1+D2)/2
(3+D1)/2 或 (3.6+d1)/2
A B
A B
(3.6+d1)/2 (2+D)/2 A先插入 (3.6+d1)/2 B先插入
致,孔径均求为φ4+00.05mm的圆孔,距两边距均为5*5mm。
4、元件引线孔的要求。
①铆钉孔的要求 大铆钉(φ2.5mm)的孔径为:φ2.7+00.1mm。 小铆钉(φ1.6mm)的孔径为:φ1.8+00.1mm。
②元器件引脚的直径和公差要求如下表
引线直径
冲孔直径
钻孔直径
φ0.8±0.05 φ0.6±0.05
5、拼板及“V”型槽、邮票孔的要求 ①为提高机插效率,要求尽量将小块印制板拼接成大块印制板,拼
版要求拼成矩形。
不可接受的拼板方式
可接受的拼板方式
②印制板的四个角要求倒圆角,且R>3mm,以保证自动传板机 构的正常工作,避免卡板造成停机或损坏印制板.
③拼版加工后需分成小块印制板,故拼板之间开“V”型槽或邮票 孔.“V” 型槽或邮票孔开得过深容易造成机插时折断,开得过浅又 会分开时不易操作,故应按下图要求.
③元器件插件密度限制(P :插入跨距
Y方向不可插入区域 X方向不可插入区域 单位:mm)
4
3
P
2.1 3
2.2
4
P+4.2
P+2
3
P+6
2.3mm 2.3mm 2.3mm 2.8mm
2.6mm
A
A先插入
B A
B
2.3mm B先插入
3.4mm A先插入
2.3mm B先插入
2、轴向元件排版要求
①印制板传板方向上、下边距边缘5mm内不应有元件。 ②定位孔附近不可机插区域。(单位:mm)
P1 F
W1
ΔH
ΔH ΔP
ΔP
B
H1 L
H0
W
W2
T1
L1
P1
d
D
T2
项目 D L L1 P
P1 H1 H0 W W1 ΔH ΔP F
P1
d
参数 Ф4.0 ≤ ≤ 12.7 12.7 23 16.0 18.0 9.0 ≤ ≤ 5.0 3.85 Ф0.6+
mm ±0.2 11 1.0 +1.0 ±0.3 ~ ±0.5 +1 ±0.5 1.0 1.0 +0.8 ±0.3 0.06
②径向元件为‘N’型打弯,焊盘设计应为元件孔靠焊盘内侧。
B=1.2mm~1.8mm
7、机插元件的排版设计要求 所有插件机均只能实现X、Y两个方向的插件,故机
插元件排版不能斜排。
机插元器件排版计要求
1、跨线元件排版要求(跨线直径≤6,跨距5≤P≤26)
①印制板传板方向上、下边距边缘5mm内不应有元件。 ②定位孔附近不可机插区域。(单位:mm)
60°
“V”型槽
0.4mm 0.3mm
60°
1.0
2.5
1.0
n×2.5
铜箔面
邮票孔:圆孔直径为1.0mm, 间距为2.5mm;开槽孔宽为
1.0mm,长度为n×2.5mm。 两端的倒角R=0.5mm。
6、机插元件的焊盘设计要求 ①跨接线和轴向元件机插时引脚内弯方式,焊盘设计应为元件孔靠焊
盘外侧。
1.2~1.8mm
机插印制板设计要求
1、印制板的外形尺寸。
厚度:1.60±0.10mm 长度:150~330mm 宽度:50~250mm
2、印制板翘曲度
插件方向
Max: 1.2mm
Max: 0.5mm
3、印制板定位孔的要求
机插板允许其中一个定位孔为长孔,但松下和环球插件机传板方
向不一致,如需贴片翻板后孔位置也将变化,建议两定位孔参数一