冲裁变形过程分析2
22冲裁变形过程分析
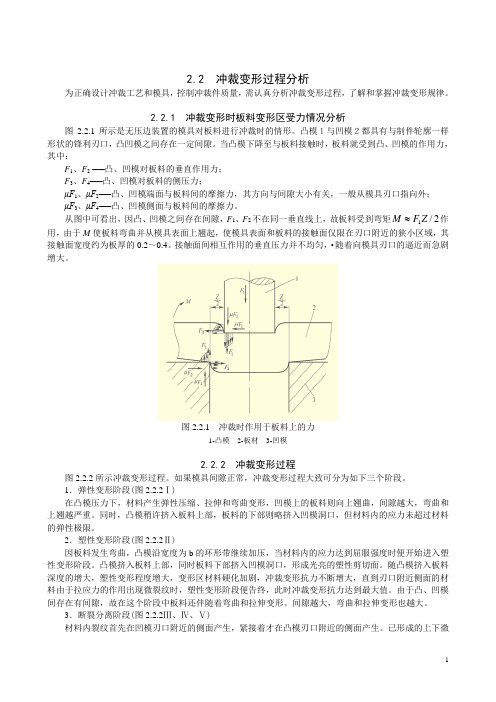
2.2 冲裁变形过程分析为正确设计冲裁工艺和模具,控制冲裁件质量,需认真分析冲裁变形过程,了解和掌握冲裁变形规律。
2.2.1 冲裁变形时板料变形区受力情况分析图2.2.1所示是无压边装置的模具对板料进行冲裁时的情形。
凸模1与凹模2都具有与制件轮廓一样形状的锋利刃口,凸凹模之间存在一定间隙。
当凸模下降至与板料接触时,板料就受到凸、凹模的作用力,其中:F 1、F 2 ──凸、凹模对板料的垂直作用力;F 3、F 4──凸、凹模对板料的侧压力;μF 1、μF 2──凸、凹模端面与板料间的摩擦力,其方向与间隙大小有关,一般从模具刃口指向外; μF 3、μF 4──凸、凹模侧面与板料间的摩擦力。
从图中可看出,因凸、凹模之间存在间隙,F 1、F 2不在同一垂直线上,故板料受到弯矩2/1Z F M 作用,由于M 使板料弯曲并从模具表面上翘起,使模具表面和板料的接触面仅限在刃口附近的狭小区域,其接触面宽度约为板厚的0.2~0.4。
接触面间相互作用的垂直压力并不均匀,•随着向模具刃口的逼近而急剧增大。
图2.2.1 冲裁时作用于板料上的力1-凸模 2-板材 3-凹模2.2.2 冲裁变形过程图2.2.2所示冲裁变形过程。
如果模具间隙正常,冲裁变形过程大致可分为如下三个阶段。
1.弹性变形阶段(图2.2.2Ⅰ)在凸模压力下,材料产生弹性压缩、拉伸和弯曲变形,凹模上的板料则向上翘曲,间隙越大,弯曲和上翘越严重。
同时,凸模稍许挤入板料上部,板料的下部则略挤入凹模洞口,但材料内的应力未超过材料的弹性极限。
2.塑性变形阶段(图2.2.2Ⅱ)因板料发生弯曲,凸模沿宽度为b 的环形带继续加压,当材料内的应力达到屈服强度时便开始进入塑性变形阶段。
凸模挤入板料上部,同时板料下部挤入凹模洞口,形成光亮的塑性剪切面。
随凸模挤入板料深度的增大,塑性变形程度增大,变形区材料硬化加剧,冲裁变形抗力不断增大,直到刃口附近侧面的材料由于拉应力的作用出现微裂纹时,塑性变形阶段便告终,此时冲裁变形抗力达到最大值。
锻压工艺学-冲裁.ppt

图.2.7 间隙对冲裁件尺寸精度的影响 16
2.2.2间隙对冲裁力的影响
图2.7.1 间隙大小对冲裁力的影响
图2.8.1 间隙大小对卸料力的影响
17
2.2.3间隙对模具寿命的影响 模具寿命:以冲出合格制品的冲裁次数来衡量,分 两次刃磨间的寿命与全部磨损后总的寿命。 凸模刃口磨钝 : 凹模刃口磨钝: 凸、凹模磨钝 : 刃口磨钝还将使制件尺寸精度、断面光洁度降低, 冲裁能量增大。
37
阶梯凸模减力时应注意: (1)阶梯高度差H稍大于断面光亮带b。 (2)各阶梯凸模的分布要注意对称(原因)。 (3)先工作的凸模应是端部带有导正销的凸模。一般 先冲大孔,后冲小孔(原因)。
38
2.4.2卸料力、推件力与顶件力 卸料力: 推件力: 顶件力:
图2.10 卸料力、推件力与顶件力
39
经验公式计算:
厚度小于3 mm的外形简单的工件,只需一次整
修。厚度大于3 mm或工件有尖角时,需进行多次
整修。
49
整修前落料凸、凹模的尺寸应为 凸模: Dp (Dy)0p 凹模: Dd (Dy)0d 式中 D-工件公称尺寸,mm;
z-双面间隙值,mm y-整修余量,mm。
50
整修时所需的力可按下式近似计算:
P cL(S0.1tn )0
21
表2.1 b/t与值(厚度t,毫米)
b/t*100%
材料
t<1 t=12 t=24 t>4
软钢 7570 7065 6555 5540 56
中硬 钢
硬钢
6560 6055 5548 4535 5047 4745 4438 3525
45 4
22
(2)经验确定法
c=mt
冲压工艺及模具

②当Z过大:
拉伸作用强,挤压作用弱,光亮带窄,相对滑动距
离短,冲件弹性恢复与上相反 。凸凹模磨损大为减轻。
③同一间隙Z:凸模端面比凹模端面磨损小。
凸模侧面比凹模侧面磨损大。 为提高模具寿命,一般采用较大间隙。若采用小间隙 应提高模具硬度,模具制造精度高,表面粗糙度低,并改 善润滑条件,以减小磨损。
冲压件尺寸减小,因此,尺寸误差是两者的综合结果。
② 模具制造精度低,工件的尺寸精度无法保证。
冲裁件内外形能达到的经济精度IT11—14,尺寸越大,精度越高,不
同的冲压件尺寸精度所对应的模具制造精度不同。
(3)间隙对弯曲度的影响(图2-11)
Z增大,h增大,为提高制件的平整度,可加压料板或反向压板,要求 太高可以加整形工序。
二、模具间隙
模具间隙——指凸、凹模刃口间的间缝隙,单边用C表
示,双边用Z表示。 间隙是冲裁模设计的关键尺寸。间隙大小对冲裁件质量和 模具使用寿命都有很大影响。
1、间隙对冲裁件质量的影响(断面、尺寸、形状即
弯曲度)
(1)间隙对断面质量的影响(图2-10)
a——Z过小,断面平直,双光亮带,挤长毛刺薄,易去除。 b——Z合理,有一定的斜度,比较平直,光洁,光亮带1/2-1/3。 c——Z过大,斜度大,粗糙,光亮带小,拉长毛刺厚,难去除。
4. 合理间隙的确定
生产中选用一个适当的范围作为合理间隙,只要间隙在这个范围内, 就可冲出良好产品,这个范围的最小值称为最小合理间隙,最大值称为 最大合理间隙。 新设计模具应采用最小值。
⑴ 理论确定法:
根据两裂纹重合,获得良好断面依据。
单边 c=t(1—ho/t)tgβ ho/t——相对压入深度
β ——裂纹与垂线间夹角
第三章 冲裁冲裁变形过程分析

第三章 冲裁
垫圈的落料与冲孔 a)落料 b)冲孔
第三章 冲裁
落 料 冲 孔 复 合 模
1-下模板 2-卸料螺钉 3-导柱 4-固定板 5-橡胶 6-导料销
7-落料凹模
8-推件块 9-固定板 10-导套 11-垫板 12、20-销钉 13-上模板 14-模柄 15-打杆 16、21-螺钉 17 冲孔凸模 18 凸凹模 19 卸料板 22-挡料销
不可避免。此外,间隙不正常、刃口
不锋利,还会加大毛刺。
第三章 冲裁
第二节 冲裁变形过程分析
二、冲裁件质量及其影响因素(续)
1.冲裁件断面质量影响因素 (1)材料性能的影响 a、b、d大,c小 (2)模具间隙的影响
间隙小,出现二次剪裂,产生第二光亮带
间隙大,出现二次拉裂,产生二个斜度 (3)模具刃口状态的影响
第二章 冲裁工艺与冲裁模设计
第三章 冲裁
冲裁变形过程
第三章 冲裁
冲裁区应力、变形和冲裁件正常的断面状况
a)冲孔件
b)落料件
第三章 冲裁
间隙对剪切裂纹与断面质量的影响 a )间隙过小 b)间隙合理 c)间隙过大
第三章 冲裁
凸、凹模刃口磨钝时毛刺的形成情况 a) 凹模磨钝 b) 凸模磨钝 c) 凸、凹模均磨钝
当凸模刃口磨钝时,则会在落料件上端产生毛刺; 当凹模刃口磨钝时,则会在冲孔件的孔口下端产 生毛刺; 当凸、凹模刃口同时磨钝时,则冲程分析
二、冲裁件质量及其影响因素(续)
2.冲裁件尺寸精度及其影响因素 冲裁件的尺寸精度:
指冲裁件的实际尺寸与图纸上基本尺寸之差。 该差值包括两方面的偏差:
扭曲:冲裁件呈扭歪现象。它是由于材料的不平、 间隙不均匀、凹模后角对材料摩擦不均匀等 造成的。
冲裁过程板料的变形过程 -回复

冲裁过程板料的变形过程-回复板料的冲裁过程涉及到材料的变形,使得板料在冲裁后可以具备所需的形状和尺寸。
在这个过程中,板料将会经历多个阶段,包括切割、塑性变形和回弹等。
接下来,我将详细解释板料的冲裁过程及其变形过程。
首先,在板料冲裁过程中,切割是第一个步骤。
切割是指通过在板料上施加足够大的应力,使其出现切割缺口。
这通常是通过冲裁模具完成的,冲裁模具的结构可以根据需要设计成各种形状和尺寸。
在切割过程中,板料经受了高速冲击应力,形成一个切割缺口,而缺口周围的板料则会遭受较小的冲击应力。
这就导致了板料的变形。
接下来是板料的塑性变形阶段。
在切割后,冲裁模具将施加力量来改变板料的形状和尺寸。
在这个过程中,板料内的晶粒发生了变形,产生了滑移和重新排列。
此时,板料的塑性变形成为主导因素,而弹性变形相对较小。
塑性变形可以通过塑性流动和沉积等方式来实现,以使板料达到所需形状和尺寸。
然而,板料的变形过程并不是完全可逆的。
尽管塑性变形可以使板料在冲裁过程中达到所需的形状和尺寸,但一旦冲裁模具撤离,板料将发生回弹。
回弹是指板料在冲裁后恢复到部分或全部原始形状和尺寸的现象。
回弹是由于板料的弹性回复和切割缺口的释放应力引起的。
回弹的大小取决于材料的性质、板料的厚度和切割缺口的尺寸。
为了减小回弹的影响,通常需要对板料进行后续的调整和修整。
在整个冲裁过程中,变形过程是由切割、塑性变形和回弹三个阶段组成的。
切割阶段通过冲击应力在板料上形成切割缺口,引发了板料的变形。
塑性变形阶段通过塑性流动和沉积等方式,使板料达到所需的形状和尺寸。
然而,由于板料的弹性回复和切割缺口的应力释放,板料在冲裁后会发生回弹。
因此,为了实现板料冲裁的精确度和一致性,需对其进行后续调整和修整。
总结一下,板料冲裁过程中的变形过程可以分为切割、塑性变形和回弹阶段。
这个过程中,板料经历了切割缺口的形成、塑性变形以及回弹等变形行为。
理解这些变形过程对于控制冲裁过程的质量和精确度至关重要。
1.冲裁变形过程
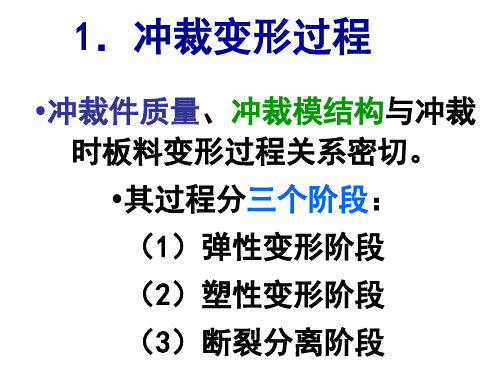
1)间隙过小
• 增大了冲裁力、卸料力和推件力; • 加剧了凸、凹模的磨损; • 降低了模具寿命(冲硬材突出)。 • 外表尺寸略有增大,内腔尺寸略有 缩小(弹性回复)。 • 光面宽度增加,塌角、毛刺、斜度 等都有所减小,工件质量较高。
2)间隙过大
• 断面光面减小,塌角与斜度增大, 形成厚而大的拉长毛刺,且难以去 除; • 冲裁的翘曲现象严重;
1.冲裁变形过程
•冲裁件质量、冲裁模结构与冲裁 时板料变形过程关系密切。 •其过程分三个阶段: (1)弹性变形阶段
(2)塑性变形阶段
(3)断裂分离阶段
•冲裁变形区的应力与变形情况和 冲裁件的切断面的状况:
2.凸、凹模间隙
•不仅严重影响冲裁件的断面
质量,而且影响模具寿命、卸
料力、推件力、冲裁力和冲裁 Biblioteka 的尺寸精度。冲裁模合理间隙值
• 外形尺寸缩小,内腔尺寸增大;
• 模具寿命较高。
• 对于批量较大而公差又无特殊
要求的冲裁件,采用“大间隙”
冲裁,提高模具寿命。
3)间隙合适
•冲裁力、卸料力和推件力适中; •模具有足够的寿命; •光面约占板厚的1/2~1/3左右,切 断面的塌角、毛刺和斜度均很小; •零件的尺寸几乎与模具一致,完全 可以满足使用要求。 •合理的间隙值可查表选取。
第二章-冲裁工艺与冲裁模具设计PPT课件

都有搭边。材料利用率低,但能保证冲裁件质量,
模具寿命较高。
少废料排样
模具只沿工件部分外形轮廓冲裁,只有局部有
搭边。废料较少,工件质量不高,模具摩损快。
无废料排样
工件间、工件与条料间均没有搭边的存在。模具刃口
沿板料依次切下获取工件。材料利用率高,工件质量差,
模具易损坏。
裁板
纵裁
联合裁
横裁
21
冲压工艺力和压力中心的计算
概 念:
~是冲裁时压力机应具有的最小压力,是完成分离
所必需的力和其它附加力(卸料力、推料力、顶料力)的
总和。它是设计模具、选择压力机的重要依据。
冲裁力的计算
使板料发生分离的力称为冲裁力。一般平刃冲裁模的冲裁
力P可用下式计算:
= KLt
(K-系数,取1.3)
合理冲裁间隙值的确定:
❖ 工件断面质量无严格要求时,应取大间隙值;
❖ 工件的断面质量和制造精度较高时,应取较小间隙值;
❖ 在设计冲模刃口尺寸时,应考虑模具摩损因素,冲裁
间隙应取最小值。
6
方法1:理论确定法
如右图所示,可得冲裁间隙为:
= 2( − ℎ0 )tan = 2(1 − ℎ0 Τ)tan
能与其冲压时定位 基准重合 ,
并选择在冲裁过程中基本上下
不变动的面或线上。
9
凸、凹模刃口尺寸的计算
重要性:
冲模刃口处的尺寸及制造公差直接影响工件的尺寸
精度,合理的冲裁间隙也靠其保证。
前提:
尺寸
计算
的原
则:
因冲裁间隙的存在,落下的料和冲出的孔都带有锥
度,且落料件的大端尺寸与凹模刃口尺寸相近,冲出
第二章 冲裁
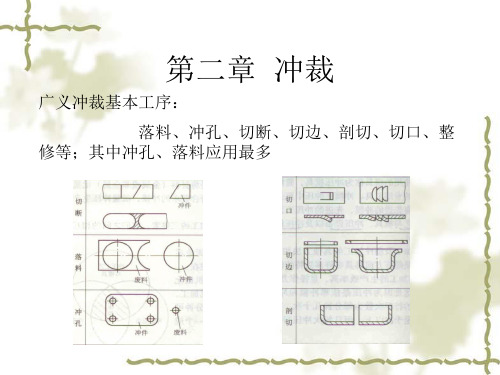
尺寸精度影响因素 一般冲裁件能达到的尺寸精度比模具的精度
1. 模具制造精度 低一到三级。
2. 材料性质及模具结构 冲裁件会发生回弹现象,从而影响 其精度,较软的材料弹性变形小,冲裁后回弹小,精度较高, 在模具上增加压板料和顶件器会减小回弹值,提高冲件精度。
3. 冲裁间隙 间隙适当时,材料在较纯的剪应力下分离,间隙 较大时,材料除受到剪切外,还产生较大的拉伸应力与弯曲变 形,冲孔件会大于凸模尺寸,落料件会小于凹模尺寸;间隙较 小时,材料会受到较大的挤压作用,冲孔件会小于凸模尺寸, 落料件会大于凹模尺寸。
3 使凸、凹模沿封闭轮廓线冲裁,提高零件质量和模具寿命。
搭边值的确定: 根据经验定,搭边值不可过小也不可过大,过大浪费材料,过 小起不到搭边作用,还可能被拉入凸凹模间隙中,使模具刃口损坏。
搭边值确定取决于材料种类、厚度、冲裁件大小、轮廓形状等,材 料越厚、硬度越低、冲裁件尺寸越大、形状越复杂,合理搭边值越大。 一般搭边值由经验确定,可以查表。 送料步距: 条料在模具上每次被送进的距离,步距计算公式为: A = D + a1
图2.9 模具间隙
Z 2t (1
h0 t
)tg
(2—4)
上式中: h0——产生裂纹时凸模的压入深度(mm); t ——材料厚度(mm); β —— 最大切应力方向与垂线之间的夹角(裂纹方向角)。
β、 h0与材料性质有关,可以查表得到。
2 查表法
3 经验记忆法
Z = mt
Z:合理冲裁间隙 t: 板料厚度
图2.2 冲裁件塑性变形
三 断裂分离阶段 当板料应力达到抗剪切强度后,凸模继续下压,凸、凹模口 部产生裂纹并不断扩展,当上下裂纹重合时,板料发生分离。当 凸模继续下行时,已分离的板料被推出,完成整个冲裁过程。
- 1、下载文档前请自行甄别文档内容的完整性,平台不提供额外的编辑、内容补充、找答案等附加服务。
- 2、"仅部分预览"的文档,不可在线预览部分如存在完整性等问题,可反馈申请退款(可完整预览的文档不适用该条件!)。
- 3、如文档侵犯您的权益,请联系客服反馈,我们会尽快为您处理(人工客服工作时间:9:00-18:30)。
3.断裂分离阶段
变形区内部材料应力大于强度极限。
裂纹首先产生在凹模刃口附近的侧面 凸模刃口附近的侧面 上、下裂纹扩展相遇
材料分离
三、冲裁断面分析
▪
由于冲裁变形的特点,冲裁件的断面具有明
显的区域性特征,可以分成圆角带、光亮带、断
裂带和毛刺四个部分。
▪ 圆角带a:由于凸模和凹模之间存在 间隙,当凸模刃口压入材料时,刃口 附近的材料产生弯曲和伸长变形,材 料被拉入间隙形成圆角带
光亮带b:该区域放生在塑性变形阶段, 当刃口切入材料后,材料与凸凹模切刃 的侧表面挤压而形成光亮垂直的断面
断裂带c:该区域是在断裂阶段形成, 是由刃口附近的微裂纹在拉应力下不 断扩展而形成的撕裂面,此处冲裁件 断面粗糙不光滑。
2020/5/1
12
毛刺区d:毛刺的形成是由于在塑性变 形阶段后期,由于微裂纹产生的位置不 是正对刃口,而是在刃口附近的侧面上, 在拉应力的作用下,裂纹加长,材料断 裂产生毛刺。
出现裂纹
裂纹贯通
板料完全断裂分离
冲裁变形过程
二、冲裁变形过程
冲裁变形过程可分为三个阶段:
1.弹性变形阶段 在凸模和凹模压力的作用下,板料产生弹性压缩、 拉伸、和弯曲变形,凸模下部略微挤入板料上部, 板料的下部则略微挤入凹模孔内,凹模上的板料则 向上翘曲,间隙越大,弯曲和上翘越严重。
2.塑性变形阶段
2020/5/1
15
2020/5/1
16
2020/5/1
17
3.模具刃口状态影响 模具刃口状态对冲裁过程中的应力
状态及制件的断面质量有较大影响。当 刃口磨损成圆角时,挤压作用增大,因 此制件圆角带和光亮带增大。
2020/5/1
18
2020/5/1
13
冲裁件断面质量影响因素
▪ 1.材料的性能: ▪ 塑性好的材料,冲裁时裂纹出现较迟,材料
被剪切的深度较大,所得断面光亮带所占比例就 大。
2.模具间隙的影响 模具间隙适中时,冲裁凸、凹模附 近沿最大 面与材料表面不垂直,但还是比较 平直、光滑、毛刺较小。
2.1 冲裁变形过程分析
冲裁是利用模具使板料沿一定轮廓形状产生分离的 冲压工序。 它包括落料、冲孔、切口、切边、剖切等多种工序。
(冲裁过程视频)
冲裁过程变形分析
▪ 一、剪切区应力状态分析。 ▪ 冲裁模工作部分特征:模具有锋利刃口;凸凹模
间有一定间隙C。
凸、凹模间隙存在,产生
弯矩。
弹性变形
塑性变形