SOP-ZS-12试模作业指导书
试模具质检作业指导书

试模质检作业指导书1 目的为规范试模取样质检作业,确保产品符合技术图纸及客户要求,防止不良品模具入库,特制定此检验作业指导书。
2 适用范围适用于广东金兰集团新材料有限公司试模质检作业岗位。
3 职责与权限3.1职责3.1.1、对新模具试出的产品是否符合技术图纸要求、相关表面处理要求、相关标准要求负责;3.1.2、对违反检验规程,造成上机不合格,而产出批量质量事故负责;3.1.3、对试模产品检验、标识、保管、填写的检测记录的真实、完整、清晰负责;3.1.4、对检验区域内的样板和检测工具不被人为破坏负责;3.1.5、对尺寸问题反映不及时,造成模具重复上机影响生产负责;3.1.6、对工作交接不清,造成质量事故负责;3.1.7、对公司及部门领导下发的指令执行或跟进不完全,而造成质量事故负责。
3.2权限3.2.1、对试产产品取样的监督权;3.2.2、对新模合格与否和判定权;3.2.3、对不合格模重复上机的制止权;3.2.4、对检验区域内的样板和所使用的计量器具的防护权;3.2.5、对生产车间、模具维修车间工作完善的建议权。
4 工作内容4.1检验前4.1.1 检验前校对所用计量器具,确保检验量具符合相应精度;4.1.2按模具验收表对样品整理分类;4.1.3检验前对所有样品进行表面质量检查。
5 样品检验5.1样板料头检验5.1.1 按技术图纸要求对样品尺寸、角度、平面间隙、壁厚进行检验,检验过程将实测壁厚、不合格处尺寸标识在料头上,便于修模工根据标示修模;5.1.2检验判定时根据产品结构,对样板进行判定是否需修模后试模;5.1.2.1图纸模横截面尺寸、公差标注尺寸必须修模后重新试模合格方可签合格;5.1.2.2样品尺寸、角度、平面间隙、R角等必检项合格,壁厚按照开模具理论壁厚-mm判定验收,局部壁厚偏低下限差0.01~0.05mm可留样,并由修模工签名加厚可签合格,不用试模;5.1.3样品检验合格,对有装配关系、客户提供配件产品找实物进行装配,新产品试模有装配关系必须留取300mmx4支,时效后交岗位质检批量生产时装配检验。
试模流程作业指导书

Ph =
第八步: 记录并保存以上工艺参数.
第九步: 第二次及以上试模(尽量采用和上一次相同的工艺参数)
第十步:试模时应注意的小细节 1). 试模前必须确认: (1) 材料: 正确的材料; 清洁; 干燥彻底. (2) 设备: 机器料斗,附机及所有管道,接头清洁. (3) 模具: 清洁
作业指导书
试模作业流程
文件编号:QI/PED/017 版号/修改状态:06-A 第4页共6页
要求: 温差<5°C, 最好<2°C ;否则须检查模具冷却系统. 模具温度设定 °C
第三步: 在无保压和保压时间的前提下,作短射填充试验(一级速度), 找出压力切换点( 即产品打 满93% 的螺杆位置). 目的: • 把握熔体流动状态; 验证浇口是否平衡( 注意: 模温不均匀,对于尤其是热敏性材料及浇口很小 的情况下,些微的模温差异都会造成自然平衡流道的不平衡). • 查看熔体最后成型位置排气状况, 决定是否需要优化排气系统
3.2.2装模中的几项注意要点: 1) 装模的全过程注塑机必须是设定在低压手动状态.(直到模具完全调整OK后为止) 2) 装模时要确认是否需要强制复位,模具被紧固后,在第一次低压开模前的注意点: A、必须把顶针的长度设定为零或取消顶出动作设定。 B、设定开合模低压保护的速度及位置,速度压力取最小值。 C、模具在低压慢速打开时,观察模具在开模运动中的状态,若有异常立即停止。 3)当模具顺利打开后,顶针没有顶出前注意点: A、检查型芯,型腔是否有异常现象。 B、有滑块的模具检查滑块是否到位,斜导柱的长度是否合理,若顶针不完全退回时是否有滑 块压铲顶针的可能性,有铲顶针的话必须要装顶针后退确认开关,并确认顶针后退确认开关 的位置与灵敏度,顶针高出的位置必须小于产品最小的胶位,模具有要安装顶针后退开关的 必须上下安装顶针后退开关。 C、设定合理的顶针长度及速度,并确认顶针的活动状况,保证产品顺利取出。 D、设定合理的开合模位置及速度保证在规定时间内。 E、低压状态下多次运行,确认无异常后转手动状态试运行确认。
注塑模具试模作业指导书
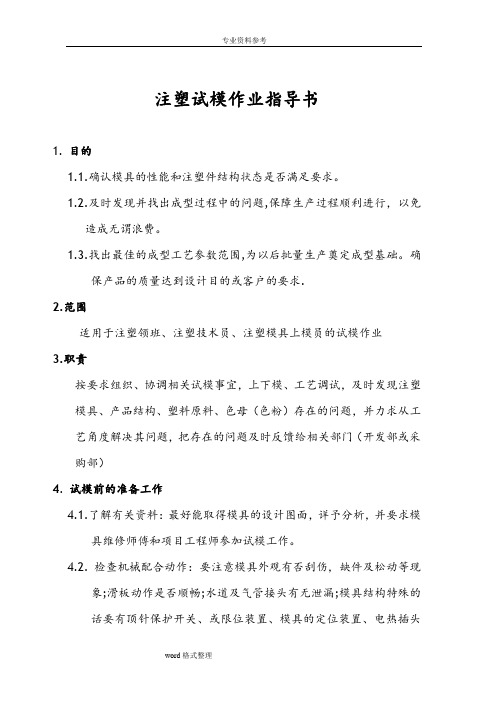
注塑试模作业指导书1. 目的1.1.确认模具的性能和注塑件结构状态是否满足要求。
1.2.及时发现并找出成型过程中的问题,保障生产过程顺利进行,以免造成无谓浪费。
1.3.找出最佳的成型工艺参数范围,为以后批量生产奠定成型基础。
确保产品的质量达到设计目的或客户的要求.2.范围适用于注塑领班、注塑技术员、注塑模具上模员的试模作业3.职责按要求组织、协调相关试模事宜,上下模、工艺调试,及时发现注塑模具、产品结构、塑料原料、色母(色粉)存在的问题,并力求从工艺角度解决其问题,把存在的问题及时反馈给相关部门(开发部或采购部)4. 试模前的准备工作4.1.了解有关资料:最好能取得模具的设计图面,详予分析,并要求模具维修师傅和项目工程师参加试模工作。
4.2. 检查机械配合动作:要注意模具外观有否刮伤,缺件及松动等现象;滑板动作是否顺畅;水道及气管接头有无泄漏;模具结构特殊的话要有顶针保护开关、或限位装置、模具的定位装置、电热插头等是否完整。
5. 选择适合的试模机器:5.1.锁模力:產品透影面的最低要求鎖模力,以機器鎖模力的70% 为基准。
长×宽(cm)×0.155(平方英寸in2)×各塑料锁模力系数(ton/in2)常用:ABS、PMMA、2.5-4.0 ton/in2;HIPS 、P S 1.0-2.0 ton/in2 P C、POM 、 3.0-5.0 ton/in2;GPPS(薄壁) 3.0-4.0 ton/in2TPU、PP、PE、1.5-2.5 ton/in2;POM 2.0-5.0 ton/in25.2.射胶量:产品重量的30%~75%最合适.5.3.导柱的宽度:装上模具并能安全的锁紧.5.4.最大的开模行程:能方便取出产品和水口。
6. 原料准备:6.1 依不同原料特性做正确的烘烤。
6.2 试模与将来量产尽可能采用同样的原料。
7.安装模具:7.1装模时注意在锁上所有夹模板及开模前吊钩不要取下,以免夹模板松动或断裂导致模具掉落。
试模作业指导书(注塑部)
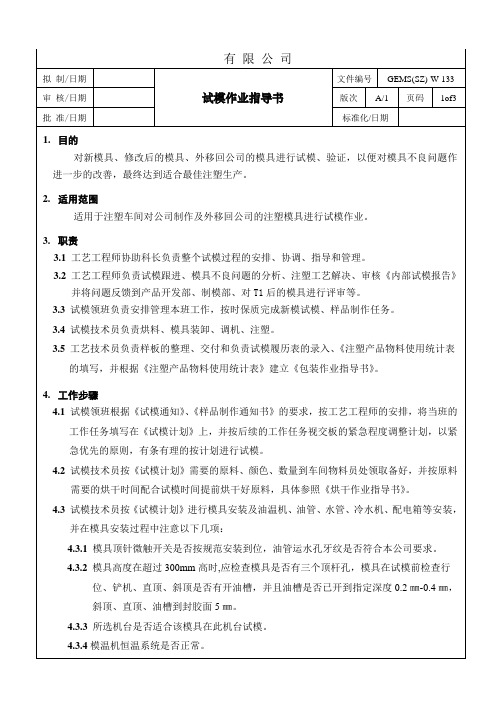
4.11试模技术员按产品不同规格填写新机型量产前《注塑产品物料使用统计表》,经工艺工程师审核后交产品开发部项目科签收,并根据《注塑产品物料使用统计表》建立《包装作业指作业导书》。
4.12试模技术员试完模后必须擦干净模腔表面、并在模腔表面上加喷防锈油后再卸模,新模具或未交付生产的模具交制模部模具管理员统一管理;特殊情况需马上修模或改模的模具,可直接交到制模车间由制模科长即时安排修模或改模。
4.4试模领班与试模技术员按产品开发部提供的尺寸、产品外观、结构配合要求进行调校注塑参数、注塑成型,若试模过程中发现模具有异常或产品达不到品质要求时,应及时通知本部门工艺工程师或科长现场确认解决,必要时通知产品开发部项目工程师、制模部制模主管等相关人员到现场监督试模,共同分析和解决问题,并视情况决定是否作落模处理。自检确认产品已符合要求或已是最好状态时,则通知质量保证部QC员或样板工程师到机位检测,若有异常再调校注塑参数,直至达到符合产品要求。
4.3.2模具高度在超过300mm高时,应检查模具是否有三个顶杆孔,模具在试模前检查行位、铲机、直顶、斜顶是否有开油槽,并且油槽是否已开到指定深度0.2㎜-0.4㎜,斜顶、直顶、油槽到封胶面5㎜。
4.3.3所选机台是否适合该模具在此机台试模。
4.3.4模温机恒温系统是否正常。
4.3.5模具安装过程必须按《模具安装作业指导书》操作。
6.2《试模通知》(编号:GEMS(SZ)-Q-0094)
6.3《样品制作通知书》(编号:GEMS(SZ)-Q-0082)
6.4《物料试用报告》(编号:GEMS(SZ)-Q-0214)
试模作业指导书
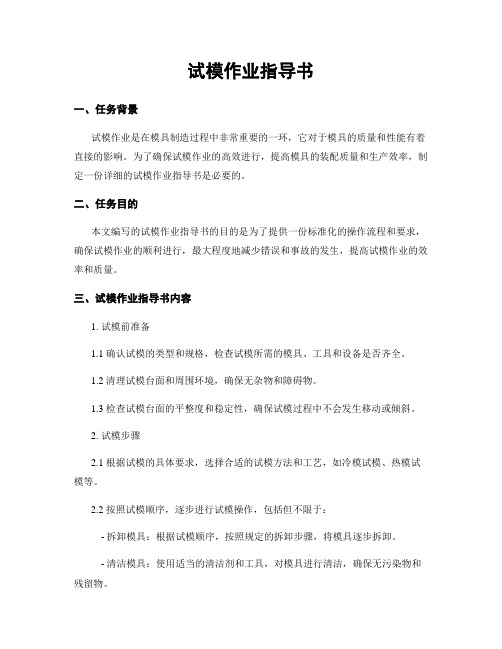
试模作业指导书一、任务背景试模作业是在模具制造过程中非常重要的一环,它对于模具的质量和性能有着直接的影响。
为了确保试模作业的高效进行,提高模具的装配质量和生产效率,制定一份详细的试模作业指导书是必要的。
二、任务目的本文编写的试模作业指导书的目的是为了提供一份标准化的操作流程和要求,确保试模作业的顺利进行,最大程度地减少错误和事故的发生,提高试模作业的效率和质量。
三、试模作业指导书内容1. 试模前准备1.1 确认试模的类型和规格,检查试模所需的模具、工具和设备是否齐全。
1.2 清理试模台面和周围环境,确保无杂物和障碍物。
1.3 检查试模台面的平整度和稳定性,确保试模过程中不会发生移动或倾斜。
2. 试模步骤2.1 根据试模的具体要求,选择合适的试模方法和工艺,如冷模试模、热模试模等。
2.2 按照试模顺序,逐步进行试模操作,包括但不限于:- 拆卸模具:根据试模顺序,按照规定的拆卸步骤,将模具逐步拆卸。
- 清洁模具:使用适当的清洁剂和工具,对模具进行清洁,确保无污染物和残留物。
- 检查模具:对拆卸下来的模具进行全面检查,包括模具的表面状况、零件的完整性等。
- 维修模具:如有需要,对模具进行必要的维修和更换,确保模具的完好性和正常使用。
- 组装模具:按照试模顺序,逐步组装模具,确保各零件的正确安装和紧固。
- 调试模具:对组装好的模具进行调试,确保模具的运行正常、无卡阻和其他问题。
- 试模测试:按照试模要求,进行试模测试,包括模具的开合、产品的成型等。
- 试模记录:记录试模过程中的关键信息和数据,如试模时间、试模结果等。
3. 试模安全措施3.1 确保试模过程中的安全性,如佩戴适当的防护用具,如手套、护目镜等。
3.2 严格遵守操作规程和安全操作流程,禁止操作人员擅自调整或更改试模设备和工具。
3.3 注意模具的重量和尺寸,避免因操作不当导致模具滑落或破损。
3.4 在试模过程中,及时清理模具周围的杂物和残留物,保持工作环境整洁。
注塑试模作业指导书

注塑试模作业指导书(ISO9001-2015)一、目的确认注塑模具、产品结构的状态、塑料原料、色母(色粉)是否符合开发设计的要求,保证量产的顺利进行。
二.范围:适用于注塑领班、注塑技术员、注塑架模员的试模作业。
三.职责:按要求组织、协调相关试模事宜,上下模、工艺调试,及时发现注塑模具、产品结构、塑料原料、色母(色粉)存在的问题,并力求从工艺角度解决其问题,把存在的问题及时反馈给相关部门(开发部或采购部)。
四.作业指导:(一)试模前的注意事项1、了解模具的有关资料:取得模具的设计图纸、模具使用说明书等相关资料,详细分析,并约定模具维修师参加试模工作。
2、先在工作台上检查其机械配合动作:要注意有否刮伤、缺件及松动等现象,模向滑板动作是否确实,水路及气管接头有无泄漏,模具的开模行程若有限制的话也应在模上标明。
以上动作若能在挂模前做到的话,就可避免在挂好模后发现了问题,再去拆卸模具所发生的工时浪费。
3、当确定模具各部动作适宜后,就要选择适合的注塑机试模,在选择时应注意①射出容量②导杆的宽度③最大的开程④配件是否齐全等。
一切都确认没有问题后则下一步骤就是吊挂模具,吊挂时应注意在锁上所有夹模板及开模之前吊钓不要取下,以免夹模板松动或断裂以致模具掉落。
模具装妥后应再仔细检查模具各部份的机械动作,如滑板、顶针、退牙结构及限制开关等动作是否确实。
并注意射料嘴与进料口是否对准。
下一步则是注意合模动作,此时应将关模压力调低,在手动及低速的合模动作中注意看及听是否有任可不顺畅动作及异声等现象。
4、试模时不可忽略模具温度,而在短时试模及将来量产时模具温度最不易掌握,而不正确的模温足以影响样品的尺寸、光度、缩水、流纹及欠料等现象,若不用模温机予以控制,将来量产时就可能出现困难。
5、适当提高模具温度:依据成品所用原料的性能及模具的大小选用适当的模温机将模具的温度提高至生产时所须的温度。
待模温提高之后须再次检视各部份的动作,因为钢材因热膨胀之后可能会引起卡模现象,因此须注意各部的滑动,以免有拉伤及颤动的产生。
试模作业指导书
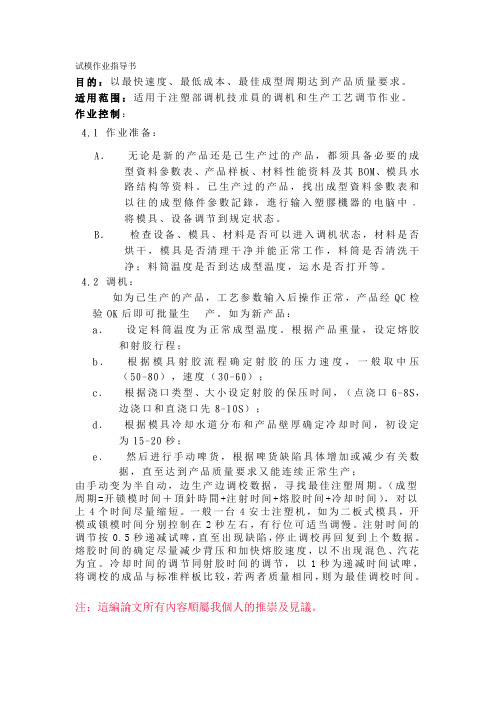
试模作业指导书目的:以最快速度、最低成本、最佳成型周期达到产品质量要求。
适用范围:适用于注塑部调机技朮員的调机和生产工艺调节作业。
作业控制:4.1 作业准备:A.无论是新的产品还是已生产过的产品,都须具备必要的成型資料參數表、产品样板、材料性能资料及其BOM、模具水路结构等资料。
已生产过的产品,找出成型資料參數表和以往的成型條件參數記錄,進行输入塑膠機器的电脑中﹐将模具、设备调节到规定状态。
B.检查设备、模具、材料是否可以进入调机状态,材料是否烘干,模具是否清理干净并能正常工作,料筒是否清洗干净;料筒温度是否到达成型温度,运水是否打开等。
4.2 调机:如为已生产的产品,工艺参数输入后操作正常,产品经QC检验OK后即可批量生产。
如为新产品:a.设定料筒温度为正常成型温度。
根据产品重量,设定熔胶和射胶行程;b.根据模具射胶流程确定射胶的压力速度,一般取中压(50-80),速度(30-60);c.根据浇口类型、大小设定射胶的保压时间,(点浇口6-8S,边浇口和直浇口先8-10S);d.根据模具冷却水道分布和产品壁厚确定冷却时间,初设定为15-20秒;e.然后进行手动啤货,根据啤货缺陷具体增加或减少有关数据,直至达到产品质量要求又能连续正常生产;由手动变为半自动,边生产边调校数据,寻找最佳注塑周期。
(成型周期=开锁模时间+頂針時間+注射时间+熔胶时间+冷却时间),对以上4个时间尽量缩短。
一般一台4安士注塑机,如为二板式模具,开模或锁模时间分别控制在2秒左右,有行位可适当调慢。
注射时间的调节按0.5秒递减试啤,直至出现缺陷,停止调校再回复到上个数据。
熔胶时间的确定尽量减少背压和加快熔胶速度,以不出现混色、汽花为宜。
冷却时间的调节同射胶时间的调节,以1秒为递减时间试啤,将调校的成品与标准样板比较,若两者质量相同,则为最佳调校时间。
注:這編論文所有內容順屬我個人的推崇及見議。
注塑模具试模作业指导书

注塑模具试模作业指导书注塑模具试模作业指导书1.介绍注塑模具试模作业指导书旨在指导操作人员正确使用注塑模具进行试模操作。
本指导书详细描述了试模前的准备工作、试模步骤、常见问题及解决方法等内容,以确保试模作业的安全、高效进行。
2.准备工作2.1 材料准备2.1.1 确保所需注塑材料已经准备好,并进行质量检测。
2.1.2 检查注塑材料的储存条件,确保其干燥、无杂质。
2.1.3 将注塑材料按照要求放置在指定区域。
2.2 模具检查2.2.1 检查注塑模具的外观,排除表面污垢,确保模具干净。
2.2.2 检查模具零部件,确保其完整、无损。
2.2.3 清洁模具的冷却系统,确保其畅通无堵塞。
2.2.4 涂抹模具专用防锈剂,保持模具的表面光洁。
2.3 设备准备2.3.1 开启注塑机设备并进行预热。
2.3.2 检查注塑机的工作性能,确保其正常运转。
2.3.3 准备好所需的模具安装工具。
3.试模步骤3.1 模具安装3.1.1 将模具安装在注塑机上,并确保模具与机器连接紧密。
3.1.2 安装模具的保护装置,确保操作人员的安全。
3.2 调整注塑参数3.2.1 根据注塑产品的要求,调整注塑机的温度、压力、速度等参数。
3.2.2 进行注塑材料的预热和预塑。
3.3 开始试模3.3.1 打开注塑机的开关,将注塑材料注入模具中。
3.3.2 关注注塑机的工作情况,确保注塑过程顺利进行。
3.3.3 观察试模产品的质量,确保其满足要求。
4.常见问题及解决方法4.1 模具堵塞问题:模具冷却系统堵塞,导致注塑过程中温度过高。
解决方法:清洁模具冷却系统,确保其畅通无堵塞。
4.2 产品质量不合格问题:产品存在短射、气孔等缺陷。
解决方法:调整注塑参数,改善注塑过程中的温度、压力控制。
5.附件本文档附带以下附件供参考:- 注塑模具试模检查表- 注塑参数调整记录表6.法律名词及注释6.1 注塑材料:用于注塑过程中的塑料原材料。
6.2 模具:用于塑料制品成型的工装,包括模具本体及相关零部件。
- 1、下载文档前请自行甄别文档内容的完整性,平台不提供额外的编辑、内容补充、找答案等附加服务。
- 2、"仅部分预览"的文档,不可在线预览部分如存在完整性等问题,可反馈申请退款(可完整预览的文档不适用该条件!)。
- 3、如文档侵犯您的权益,请联系客服反馈,我们会尽快为您处理(人工客服工作时间:9:00-18:30)。
文件修订履历1目的确保试模操作正确,防止不正当操作造成人身伤害和模具或机器的损坏提高试模效率及试模有效性2范围适用于试模流程3安全3.1 开机前安全要求3.1.1 进入工作岗位时需穿戴好工作服、工作鞋,特殊情况下:如拆卸注塑机射嘴.拆卸注塑机螺杆时要戴好防护眼镜;如上下模具要戴好安全帽。
3.1.2 节假日后第一班开机时,要检查设备有否漏电,检查冷却水系统是否堵塞和滴漏。
3.1.3 机筒加热升温时,要同时开机筒冷却水。
冬季寒冷时,车间温度较低,应先点动开启油泵,未发现异常现象时再开车空转10~15min后正常生产。
3.1.4 检查注塑机各滑轨部位,并给各润滑点加油。
3.2 生产过程的安全要求3.2.1 机筒温度达到工艺要求以后,要恒温15分钟才进行螺杆动作的操作。
3.2.2 操作必须使用安全门,如安全门行程开关失灵时不准开机,严禁不使用安全门(罩)操作。
3.2.3 安放模具、嵌件时要稳准可靠,合模过程中发现异常应立即停机排除故障。
3.2.4 机器修理或较长时间修理模具时,必须将注塑机的料筒温度设置为保温状态或者关闭。
3.2.5 清理模具中残料或制品时要用铜质等软金属材料。
3.2.6 运转设备的电器、液压及转动部份的各种盖板、防护罩等盖好、安好、固定螺栓旋紧。
3.2.7 身体进到模具开档内,一定要关闭设备马达或电源。
维修人员修机时,操作者不准脱岗。
3.2.8 避免在模具打开时,用注射座撞击定模,以免造成定模模具损伤。
3.2.9 对空注射有困难时,应停止操作,注意通知邻近人员避开危险区,检查温度是否正常。
3.2.10 发现设备、模具异常、及时通知维修人员检修。
3.2.11 试模中用于清洗螺杆的废料要严格处理,一定要等料完全冷却后才能放进废料袋。
用于擦模具的废布要单独处理。
3.3 停机后安全要求3.3.1 停机前要使用PP料或其它不易分解的材料清洗注塑机的螺杆。
3.3.2 停机后将机器手动合模至低压位置,及时关闭马达电源开关。
3.3.3 停机后将注塑机的哥林柱,导轨清洁干净,并喷上防锈水(WD40)或涂上液态黄油。
4. 职责试模组所有人员5.试模操作步骤5.1 原料干燥5.1.1 根据试模单的原料名称,原料等级,及项目开立的原料领料单至仓库进行领料。
5.1.2 加料前清洁原料干燥机或烤料盘,检查原料中有无杂质及异物。
5.1.3 将原料倒入烤料盘并做好标识或倒入原料干燥机内。
5.1.4 填写好试模原料使用记录并根据原料物性表设置好原料干燥机或烤箱的干燥温度。
5.2 上模5.2.1 确认模具尺寸、外观、是否有强制复位、抽芯油缸等信息并确定好试模机台吨位。
5.2.2 检查模具吊环孔或吊模杆是否完好;确认模具是否有锁模块;查看模具外观是否有重要标示;水路标示;模具是否受损等状况。
5.2.3 使用相匹配的吊环将模具吊上机台,调好模并锁紧码模夹。
5.2.4 松开锁模块并接好顶针回位确认开关(如有)。
5.3 模具检查确认5.3.1 模具动作检查(未接模温):模具慢速或点动开模,确认模具是否有开模异常。
5.3.2 检查模具顶出/回位是否正常:顶出前先确认模具滑块或模具抽芯是否完全退到位,与模具顶针是否有干涉。
根据产品需要及模具允许设置好模具顶出长度,进行手动顶出/回位动作五回合以上,确认顶出/回位动作是否有异音;顶针是否可以完全回位;模具顶针的回位速度是否符合注塑机顶杆的回位速度。
5.3.3 检查模具抽芯(如有)动作是否正常:先确认好模具抽芯与模具顶针是否有干涉;如有干涉必须在模具顶针完全回位后才可进行模具抽芯动作的操作(可使用顶针回位确认开关保证);且必须保证模具抽芯动作退到位后注塑机才可进行顶出动作(需使用电磁开关或行程开关与注塑机的顶针信号线串联才可保证)。
根据模具抽芯滑块的实际情况设置好油缸动作位置:进芯后合模还是合模后进芯;先退芯再开模还是开模后再退芯,油缸动作压力,速度及油缸适当的动作时间(压力越小比较好;动作速度需平稳)。
手动来回操作抽芯动作,确认模具的抽芯动作是否正常,动作方向是否正确。
5.3.4 检查模具滑块(如有)动作是否正常:合模前手工推合模具上的滑块确认动作是否顺畅,滑块定位是否正常,滑块弹簧是否正常。
5.3.5 检查模具开闭模动作是否正常:手动开闭模确认模具滑块的导柱长短是否适合;确认模具导柱导套的闭合时是否有撞击声或开模时导套内有积气的声音。
确认模具开闭动作时是否有磨擦的异常声音;确认模具拉料板的动作是否正常;弹簧推板是否可以正常开到位;模具闭模时的低压是否需调到很高才可正常合模。
5.3.6 模具水路确认检查模具水路是否做好标识;使用气枪确认每组水路是否通畅,清除水路内的杂质。
5.3.7 模具水路连接根据模具的水路进行水管连接。
要求:动定模的模芯与模架要单独接;如模具动定模的模芯与模架各只有一组,可相互连接为一组水路,但必须符合水路流量要求;如有滑块水路则只能与滑块水路相互连接。
应避免模具滑块水路串连模具的模芯或模架水路。
5.3.8 模具水路测试模具水管连接结束后要使用水流量计对每组连接水路的流量进行测试:一般情况下模具模芯及模架的水流量必须大于280L/H;模具滑块的水流量必须大于140L/H;如果不能达到此流量标准,则要检查模具水路连接是否太多组串连,进行拆组重测水流量;如单接一组水测量流量还是不足,则要检查模具水路是否堵塞或者模具水路设计本身太细所致。
还有就是使用的水温机的本身压力不足(建议采用增压式水温机,水温机本身压力4KG以上)。
同时确认模具是否有漏水现象。
5.3.9 根据试模使用的原料物性表设置水温机的温度,使模具在闭模状态下(未起高压)开始升温。
并记录好《模具水路连接示意图》与测试的各组水路的流量。
5.3.10 当水温机的实际温度恒温30-60分钟后。
按5.3.1的操作要求打开模具,并使用测温仪进行模具各部位的实际温度测量,并确认各点实际温度是否平衡。
5.3.11 当模具实际温度达到或接近原料物性要求后,再进行:5.3.2 的要求检查模具顶出/回位是否正常:5.3.3 的要求检查模具抽芯(如有)动作是否正常:5.3.4 的要求检查模具滑块(如有)动作是否正常:5.3.5 的要求检查模具开闭模动作是否正常:5.3.12 记录各检查项目的问题点与需要改进项目。
5.4 试模工艺输入(测试)5.4.1 原料干燥温度:参照原料物性表要求的干燥温度及时间取中间值进行原料预先干燥。
5.4.2 模具成型温度:参照原料物性表要求的模具温度取中间值设定,并测量实际模温达到要求。
5.4.3 成型加工温度:参照原料物性表要求的成型加工温度取中间值进行设置。
5.4.4 注射速度设置(塑料粘性测试),前是条件是:模具动作正常,产品可正常取样。
a复制并打开《塑料粘性测试报告》,填写将要测试的模具信息与测试条件和测试日期;b使用一段注射至产品的95%,进行位置切换;不使用保压;注射压力可设置注塑机最高压力;c注塑机全自动生产至模具温度稳定(可观查射出实际压力基本稳定);d在注塑机上依次设置注射速度:30mm/s-40mm/s-50mm…140mm/s;或35mm/s-45mm/s…145mm/s10进位为一测试阶段;每个阶段的射出模数不低于三模,依每个阶段记录注塑机所显示的实际注射压力、实际填充时间、射出残余位置及相对应的射出速度。
e根据下图显示的拆射图或表中右侧的粘度变化数值选择出最佳射出速度(粘度变化较少值相对应的上一个注射速度和此注射速度这间选择)。
5.4.5 进胶平衡测试(如为多穴)a打开《进胶平衡测试报告》,填写将要测试的模具信息与测试条件和测试日期;b根据5.4.4选择的最佳射出速度,并切换保压转换位置,取样50%、75%、95%三个阶段的样品各一模,将每个穴号的产品重量称好并记录于相对应的测试报告中。
表中将自动测算出模穴号的偏差率值。
偏差率的允许标准为:单个Cavity的重量在1.0g以下;允许偏差率值为低于10%;如单个Cavity的重量在1.0g以上;则允许偏差率值为低于2%;否则需对模具进行调整。
如果50%的进胶平衡值好于75%的值或75%的进胶平衡值好于95%的值,则可确为模具有排气不良现象。
5.4.6注射压力设置(稍大于《塑料粘性测试报告》中最佳射出速度所需的实际注射压力)。
5.4.7注射压力损耗测试:如模具短射时产品很难脱模则可不做注射压力损耗测试根据材料的特性,当实际射出压力超出一定的数值才要求做注射压力损耗测试。
a.如PP、ABS、PS/ABS、PA、PBT、POM、PVC等低料温流动性较好的塑胶材料合理射出压力数值为:1500kgf/c以内,注塑机总射出压力的53.5%.b.如PC、PPSU、PET、GF30%以上等高料温且流动性不佳的塑胶材料的合理射出压力数值为:2200kgf/c以内,注塑机总射出压力的80%。
打开《注射压力损耗测试报告》,填写将要测试的模具信息与测试条件和测试日期;调整注射的切换保压位置,进行:喷嘴空射、热流道嘴空射、流道到浇口位置、过浇口到产品位置、产品充填50%、产品充填95%。
记录各项所损耗的实际射出压力,如测试的注射压力损耗偏大,则要求检查模具并做模具调整。
5.4.8 注射保压压力设置(根据产品特性设置实际注射压力的40%-75%)。
5.4.9 注射保压时间设置(保压时间测试也叫封胶测试)。
a打开《保压时间测试报告》,填写将要测试的模具信息与测试条件和测试日期;b根据产品特性设置好保压压力,并依次设置保压时间:1s;2s;3s;4s;5s;6s…分别使用电子称称好每模产品重量记录于《保压时间测试报告》中;当产品重量2-3模无明显变化时,则可停止测试。
c选择产品重量无明显变化的第一模或第二模的保压时间作为该工艺的保压时间。
5.4.10产品冷却时间设置根据产品使用塑胶材料的热变形温度;产品设计的壁厚;模具温度等因素综合考虑来设置产品的冷却时间。
通常ABS、PC/ABS、PA系列、PP、PVC、PBT、PET、POM等材料的冷却时间设置为6-12s;通常PC、PPSU等高模温或高料温的材料以及壁厚较厚或结构较复杂的产品冷却时间一般设置为10-20s。
5.4.11特殊工艺设置如因产品外观需使用多段注射时,最高射出速度不可超出测试所得速度;如因产品结构特殊需使用多段保压时,保压最高压力不可超出注射压力的75%,保压总时间不可超出测试所得时间。
如因特殊材料(PPSU)、产品特殊结构产品壁厚薄相差大,工艺的设置可特殊性,但必须可适合于批量生产;使用国产(海天)注塑机试模均可不做相关测试,但模具冷却示意图、进胶平衡测试、保压时间测试不因设备限制必须要做。
5.5 试模取样5.5.1 根据输入的成型工艺及试模单要求的样品数量开始取样。