从“福特制”到“丰田制”的演变
【一周一案】全球生产方式演变:福特制、丰田制与温特制
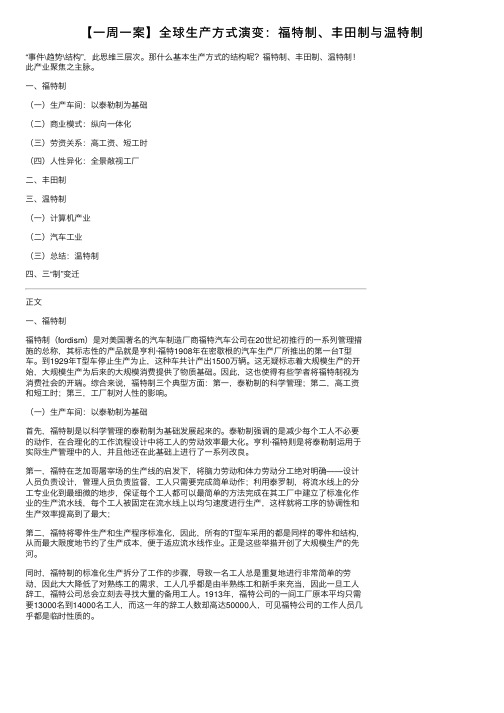
【⼀周⼀案】全球⽣产⽅式演变:福特制、丰⽥制与温特制“事件\趋势\结构”,此思维三层次。
那什么基本⽣产⽅式的结构呢?福特制、丰⽥制、温特制!此产业聚焦之主脉。
⼀、福特制(⼀)⽣产车间:以泰勒制为基础(⼆)商业模式:纵向⼀体化(三)劳资关系:⾼⼯资、短⼯时(四)⼈性异化:全景敞视⼯⼚⼆、丰⽥制三、温特制(⼀)计算机产业(⼆)汽车⼯业(三)总结:温特制四、三“制”变迁正⽂⼀、福特制福特制(fordism)是对美国著名的汽车制造⼚商福特汽车公司在20世纪初推⾏的⼀系列管理措施的总称,其标志性的产品就是亨利·福特1908年在密歇根的汽车⽣产⼚所推出的第⼀台T型车。
到1929年T型车停⽌⽣产为⽌,这种车共计产出1500万辆。
这⽆疑标志着⼤规模⽣产的开始,⼤规模⽣产为后来的⼤规模消费提供了物质基础。
因此,这也使得有些学者将福特制视为消费社会的开端。
综合来说,福特制三个典型⽅⾯:第⼀,泰勒制的科学管理;第⼆,⾼⼯资和短⼯时;第三,⼯⼚制对⼈性的影响。
(⼀)⽣产车间:以泰勒制为基础⾸先,福特制是以科学管理的泰勒制为基础发展起来的。
泰勒制强调的是减少每个⼯⼈不必要的动作,在合理化的⼯作流程设计中将⼯⼈的劳动效率最⼤化。
亨利·福特则是将泰勒制运⽤于实际⽣产管理中的⼈,并且他还在此基础上进⾏了⼀系列改良。
第⼀,福特在芝加哥屠宰场的⽣产线的启发下,将脑⼒劳动和体⼒劳动分⼯绝对明确——设计⼈员负责设计,管理⼈员负责监督,⼯⼈只需要完成简单动作;利⽤泰罗制,将流⽔线上的分⼯专业化到最细微的地步,保证每个⼯⼈都可以最简单的⽅法完成在其⼯⼚中建⽴了标准化作业的⽣产流⽔线,每个⼯⼈被固定在流⽔线上以均匀速度进⾏⽣产,这样就将⼯序的协调性和⽣产效率提⾼到了最⼤;第⼆,福特将零件⽣产和⽣产程序标准化,因此,所有的T型车采⽤的都是同样的零件和结构,从⽽最⼤限度地节约了⽣产成本,便于适应流⽔线作业。
正是这些举措开创了⼤规模⽣产的先河。
{企业管理流程图}精益价值流价值流程图
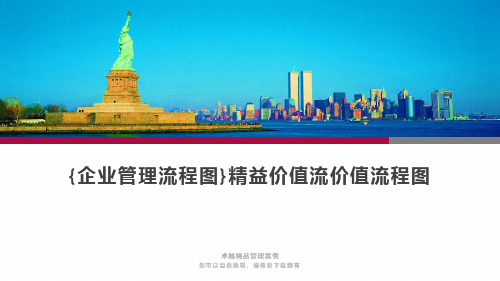
1 选定产品组
挑选出典型的产品作为深入调查分析的对象。
销售金额大、生产数量多、生产周期长。
2 价值流图常用符号
3 绘制当前状态图
1、收集相关信息 一般从最下游的作业(即发货)开始,收集实际的过程数据,例 如发货频率、订货量、工艺流程图、各工序作业时间、换模时间、 操作工人数、班次、周期时间等。
价值流程图的组成
• VSM的基本构成有四大部分(无 先后): 顾客部分。顾客发出 信息,可能是订单,新产品, 等等; 公司系统部分。可能是 ERP, SAP任何系统,顾客信息进 入公司系统; 供应商部分。
• 内部物料流。主要指产线部分, 至少需要人机料(Man, Machine,
价值流程图的组成
流程的系统性诊断工具。从整个流程而非某个工艺过程分析问题。
实施精益的战略性工具。实施计划的基础。
Kaizen
价值流程图的作用
应用价值流分析能够做到: • 缩短整个流程时间,提高增值时间比 • 降低库存,增加流动资金 • 加强流动弹性 • 简化信息流 • 消除浪费,减少间劳动时间
价值流图析步骤
应用价值流程图改善的案例
发现问题点
1、信息通过香港分公司周转后周期长、成本高。 2、原材料订购时间需要60天,延缓了周转速度。 3、在产品生产过程中,生产周期长,中间的在库量太大,
重复的搬运和停顿非常多。 4、成品的在库量太大,时间长达14.6天。
绘制未来状态图
精益生产管理的着眼点
着眼点一:创造价值,把不产生价值、却占用企业资源的业务流程 环节、实物流程环节全部删除。 通过解决重复、停顿现象去发 现问题,使得管理流程的价值最大化。因此,推行JIT 要以价值 为关注焦点开展革新活动。
VSM价值流程图基本概
生产方式演变及发展趋势

八种生产方式形态
作坊生产 工场式生产
批量生产 流水生产
&1820年奥斯特发现电流磁效应 &安培提出电流相互作用定律 &1831年法拉第提出电磁感应定律 &1864年麦克斯韦尔电磁场理论的建立 &电气化改变了机器结构 &机器在动力学、运动学上的无可比拟 优越性 &产品的批量也得到了提高 &企业也从批量生产中获得了“规模效益 &“造得多”取代“能制造”开始成为最重 要策略。
八种生产方式形态
大量生产 高质量生产
快速生产 大规模定制
& 微电子、计算机技术的发展,为设计、制造和 营销过程的信息管理与计算机辅助设计制造创造 了前所未有的条件 & 近代制造技术及其自动化的发展,为先进制造 技术积累了现代工艺和管理文明 & 运筹学、专家系统、仿真技术和人工智能等发 展,为制造技术走向智能化创造了技术前提 & 先进的工艺如精密成型,超精密加工、精细焊 接、表面技术和在线检测技术的发展为制造技术 提供了新的工艺基础。 & 通过企业严格的内部分工和高度专业化操作、 塔形多层次的垂直领导以及严格的生产节拍控制 &“有人要”已成为新的生产策略
精益生产模式的发展和特征
在以福特公司为代表的福特制生产组织市场份额下 降、利润率减少时, 日本汽车公司的生产率、市场占 率和利润水平却在不断上升, 并在1980年突破1000万 大关, 成为世界汽车第一制造大国。
1985年美国麻省理工学院的Danie l Ross教授等 资500万美元, 用了近5年的时间对90多家汽车厂进行 考察, 将福特制与丰田生产方式进行了对比分析, 提 精益生产的生产组织概念 。
精益生产与日本制造业的兴盛
丰田家族与丰田生产制度的故事

丰田家族与丰田生产制度的故事在丰田公司追求卓越的路上,最引人注目的产物是其制造理念,一般称之为「丰田生产制度」。
「丰田生产制度」是继亨利.福特发明的大量生产制度后,第二次事业流程效率的重大变革,它被详细记载、分析、并输出至全世界各产业公司。
在丰田公司以外,「丰田生产制度」经常被称为「精实」或「精实生产」,因为以下两本畅销书使用这两个名词而使其变得家喻户晓:《改变世界的企业经营体制:精实生产的故事》(The Machine That Changed the World: The Story of Lean Production)、《精实思维》(Lean Thinking)。
不过,这两本书的作者非常明确地强调,他们对于「精实生产」的研究,系以「丰田生产制度」及丰田公司对此制度的发展为基础。
尽管丰田公司现在全球各地总计有超过二十四万名员工,但就许多方面而言,它依旧是一个大型的家族企业,创办该公司的丰田家族仍然对该公司有相当大的影响力。
为了解「丰田生产制度」与「丰田模式」,以及该公司如何发展成全世界最优秀的制造业者,我们首先应该了解该公司创办家族成员的历史与个性,因为丰田家族对丰田公司文化留下持久的影响。
最重要的不是一家族的掌控(福特汽车公司在这方面也是类似情况),而是丰田在其整部历史中展现非常一致的领导与理念,「丰田模式」中所有原则的根源皆可追溯至该公司创始之初,丰田的每一位领导者,不论是不是丰田家族成员,都融入了「丰田模式」的DNA。
丰田家族:代代都展现一致的领导丰田家族的故事始于丰田佐吉(Sakichi Toyoda),他擅长修修补补,也是个发明家,其出身背景和亨利.福特相仿,成长于十九世纪末期日本名古屋郊外一个偏僻的农村。
在当时的日本,织布是主要产业,日本政府为了促进小型企业的发展,鼓励全日本各地创立家庭工业,雇用少数员工的小型工作坊与工厂相当遍及,家庭主妇普遍到附近的工作坊或在家里工作,以赚取微薄工资贴补家用。
丰田学习福特剖析

四、丰田创新:精益生产之JIT
多级供应链变成 单级库存管理
工序间在制 品为“零”
供应商库存管理
一个流生产
JIT
拉动生产
按订单协调 生产周期
看板管理
均衡生产
四、丰田创新:精益生产之看板管理
看板传递:信息流 看板传递:物流信息,如原材料和在制品转移
考察对象:美国汽车厂商 丰 田 学 习 福 特
130家工厂、7个研究所和5所大学 丰 田 模 仿 建 厂
二战致使学习 搁浅
产量提升, 质量问题突显
学习内容
福特的汽车和零部件技术
一、丰田与福特发展背景:丰田第二次学习
丰田英二主要事迹:(丰田创始人丰田佐吉的侄子)
1、学习福特流水线-提出精益生产 2、1974年,设立了“丰田财团”-无偿性 3、1981年创办了“丰田工业大学” 4、1982年创立了“国际经济研究所”
节省取零件时间
输送带 汽 车 组 装 个人生产效率提升
价格与成本降低
质量与产量的提升
一、丰田与福特发展背景:福特流水线生产
对比内容 流水线生产前 流水线生产后
T型车组装时间 12小时28分钟
生产效率提升 生产工序
10秒钟
提升4488倍 3000多道 84道
销售价格
850美元
低于300美元
注意:组装时间是指生产上一辆与生产下一 辆汽车的间隔时间。
更新设备 整顿生产线 丰 田 生 产 设 备 现 代 化 提高热效率和集中动力源 硬 件 改 造 引进自动检查设备 进口高性能、高精度机械 完善通信设备 引进办公设备
提高生产能力 提高生产效率 节约能耗 提高检查精确度 改善作业环境 促进生产管理合理化 促进办公合理化
美国、日本汽车产业发展阶段
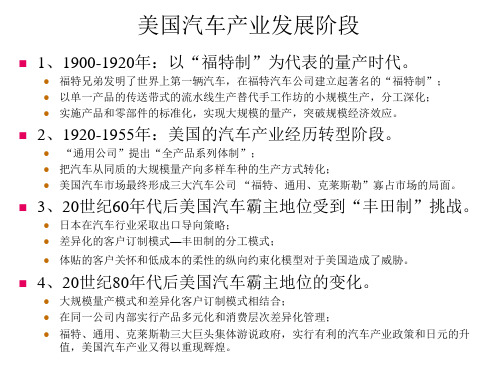
4、进入20世纪90年代日本汽车产业的转型。
大量引入了先进技术和知识,也意味着面临更多知识产权保护和贸易摩擦的风险; 日本从来都是一个资源和原材料匮乏、产业结构非常依赖进出口的国家,在这种国际 背景下日本不得不改变“贸易立国”产业政策,开始大量转移国际产业并在海外设立 分公司。
美国汽车产业分工转变:从纵向一体化到全球分包
4、20世纪80年代后美国汽车霸主地位的变化。
大规模量产模式和差异化客户订制模式相结合; 在同一公司内部实行产品多元化和消费层次差异化管理; 福特、通用、克莱斯勒三大巨头集体游说政府,实行有利的汽车产业政策和日元的升 值,美国汽车产业又得以重现辉煌。
日本的汽车产业发展阶段
1、战后日本汽车产业的起步阶段。
“通用公司”提出“全产品系列体制”; 把汽车从同质的大规模量产向多样车种的生产方式转化; 美国汽车市场最终形成三大汽车公司 “福特、通用、克莱斯勒”寡占市场的局面。
3、20世纪60年代后美国汽车霸主地位受到“丰田制”挑战。
日本在汽车行业采取出口导向策略; 差异化的客户订制模式—丰田制的分工模式; 体贴的客户关怀和低成本的柔性的纵向约束化模型对于美国造成了威胁。
“动态的国际分工论”和“静态的国际分工论”两种理论之争,对立点在于“发展汽车 产业与否”以及深层次的“优先开发国内资源还是发展贸易战略” ; 最终,日本优先发展的是对外贸易,汽车产业就此起步。
2、“丰田制”时代。
银行要求丰田汽车公司的经销部门独立出来,成为“丰田汽车经销公司”,汽车公司 只能按经销公司的订单数量进行生产,目的是限制它的发展; 丰田为了生存,创造出“及时生产(JIT)”制度,以后不断完善,把公司供应的原料 与零件直接送到生产线,立即投产,生产线上的每一个员工都将手中的存货、原料、 半产品和产品降至零,产生了超低成本和高质量的产品,节省中间成本; 丰田制代表更先进、适应客户个性化需求和多元化的分工模式。
jit生产历史
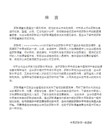
战后的日本经济萧条,缺少资金和外汇。怎样建立日本的汽车工业?照搬美国的大量生产方式,还是按照日本的国情,另谋出路,丰田选择了后者。日本的社会文化背景与美国是大不相同的,日本的家族观念、服从纪律和团队精神是美国人所没有的,日本没有美国那么多的外籍工人,也没有美国的生活方式所形成的自由散漫和个人主义的泛滥。日本的经济和技术基础也与美国相距甚远。日本当时没有可能全面引进美国成套设备来生产汽车,而且日本当时所期望的生产量仅为美国的几十分之一。“规模经济”法则在这里面临着考验。
日本企业在国际市场上的成功,引起西方企业界的浓厚兴趣,西方企业家认为,日本在生产中所采用的方式是其在世界市场上竞争的基础。80年代以来,西方一些国家很重视对丰田生产方式的研究,并将其应用于生产管理。首先推广应用的是美国的通用汽车,接着其他的汽车公司和其他产业的公司也开始实施精益生产。
随着各国对精益生产的理解和应用,加之由于市场的快速变化,迫使企业生产需要做出快速响应,这样,在精益生产的基础上,发展了敏捷制造(AM)思想,敏捷制造系统是以精益生产的设备,全面生产维护(TPM)以及设备各组合部之模块化为基础建立起来的高柔性生产系统。敏捷制造能对顾客的多样化和个性化的需求做出快速的反应,以满足顾客需求。
丰田英二和他的伙伴大野耐一进行了一系列的探索和实验,根据日本的国情,提出了解决问题的方法。经过30多年的努力,终于形成了完整的丰田生产方式,使日本的汽车工业超过了美国,产量达到了1300万辆,占世界汽车总量的中。丰田生产方式是日本工业竞争战略的重要组成部分,它反映了日本在重复性生产过程中的管理思想。丰田生产方式的指导思想是,通过生产过程整体优化,改进技术,理顺物流,杜绝超量生产,消除无效劳动与浪费,有效利用资源,降低成本,改善质量,达到用最少的投入实现最大产出的目的。
精益价值流—价值

价值流改进重点在于物流和信息流。精益生产中,信息流被视为与物流一样重要。考虑怎样流 动信息才能使一个工序仅仅生产出为下一道工序所需要的物料,而且是在需要的时候进行生产。
价值流程图概念
价值流程图(Value Stream Mapping):通过用特 定的图标将整个价值流的过程绘制出来,使价值 流目视化的工具,包括物流、信息流和过程流。
C、绘制发货与收货信息。在客户图标下画出卡车图标, 填上发货的频率,箭线指向客户。在供应商图标的下 方画一个卡车图标,填上送货的频率,箭线指向价值 流最上游。
C、绘制发货与收货信息。在客户图标下画出卡 车图标,填上发货的频率,箭线指向客户。在 供应商图标的下方画一个卡车图标,填上送货 的频率,箭线指向价值流最上游。
是一种系统改善信息流程、实物流程的方法。
供应商
工序C
信息控制
工序B
客户
工序A
理解流程…看到价值…憧憬未来状态
价值流程图的发展
起源于1980s的TOYOTA, “物与情报流程图”
大野耐一(Taiichi Ohno )
新乡重夫(Shigeo Shingo)
随着1998年美国Mike Rother & John Shook的著作《学习如何看:价值流程 图创造价值和消除浪费》而风靡全球。
“Whenever there is a product for a customer, there is a value stream. The challenge lies in seeing it.”
价值流程图的作用
识别浪费的工具,发现浪费的根源。
改善沟通的工具。用价值流图可反映各项作业怎样与生产控制中 心沟通信息;各项作业之间怎样沟通信息。
- 1、下载文档前请自行甄别文档内容的完整性,平台不提供额外的编辑、内容补充、找答案等附加服务。
- 2、"仅部分预览"的文档,不可在线预览部分如存在完整性等问题,可反馈申请退款(可完整预览的文档不适用该条件!)。
- 3、如文档侵犯您的权益,请联系客服反馈,我们会尽快为您处理(人工客服工作时间:9:00-18:30)。
福特生产模式,单品大批量生产方式
丰田生产模式,多品种小批量生产方式
沃尔沃,人性化生产方式
以上三种生产方式,探讨生产方式的演变。
一、福特制与丰田制的比较
在全球化、市场化和信息化三大时代背景下,企业的生产组织形式正在形成由“福特制”时代的刚性生产方式向“丰田制”时代的柔性生产方式转变的趋势。
前者以大批量、标准化和垂直一体化为特征,后者以柔性技术和组织及复杂的生产网络为特点。
“福特制”正逐渐被“丰田制”所取代,其原因可以从内外两个方面进行分析:
一是来自竞争者的外在压力。
在“福特制”时代,大多数企业均进行大批量、少品种的集中化生产,企业之间的竞争主要来自产品成本和销量上的竞争。
然而随着消费者时代的到来,顾客对于产品的要求越来越高,不再满足单一的产品品种,而是更加注重产品的个性化需求。
消费者的需求就是企业的生命线,因此很多企业单单依靠批量销售标准型产品难以维系生存,于是便以市场为导向,按照顾客的需求对产品进行改革创新,进行小批量、多品种的生产。
毫无疑问,这种生产方式能够抢占更多的市场份额,而那些“福特制”的固守者也不得不转变其生产方式,以增强自身的竞争力。
二是源于对利润追求的内在动力。
“福特制”的利润空间主要是通过高效率批量生产而对成本空间进行压缩,然而这种利润方式的取得具有一定的局限性。
由生产资料和劳动力等所构成的生产成本都有一个最低限度,不可能无限制地压缩。
要想更进一步提升利润,企业必须另辟蹊径,“丰田制”生产方式则是企业解决这一问题的最佳选择。
“丰田制”的始创者丰田喜一郎在创办公司时,致力于降低成本、减少浪费、降低库存,将零部件生产外包给周边的小企业。
围绕丰田汽车公司约有300家制造汽车零件、铸模和工具的承包商,在这300家承包商周围又有上千家的小工厂承包制造更小的零件,形成一个汽车生产辐射网,也形成了丰田汽车城。
在丰田市和几个邻县的境内,几乎每家企业都直接或间接地成为这个辐射网中的一分子,汽车生产和供应集中在以丰田集团为中心、半径为10公里的范围内。
即时生产、零库存、敏捷制造等现代生产和物流方法也被丰田创造,并向世界推广。
丰田的这种模式减少了运输环节,被世界汽车制造业视为较理想的生产方式。
“丰田制”的核心思想是以整体优化的观点合理配置和利用现有生产要素,消除生产过程中一切不产生附加价值的劳动和资源,获得更高的生产效率和更大的经济效益。
“福特制”与“丰田制”属于两种完全不同的生产方式,“丰田制”完全打破了“福特制”的经营理念、生产方式和管理策略,具有很强的创新性、适应性。
二者的区别见表1。
产业集群特别适用于具有规模经济效益、关联产业多、配套环节多的汽车产业。
二:沃尔沃,人性化生产方式
沃尔沃人性化的安全和健康设计
VOLVO生产方式五原则:
1.利用整体概念来衡量价值,即产品的价值是由顾客决定的,而不是由企业决定。
2.投放的每项产品都必须确定整体的价值链。
3.联接沿价值链的所有流程的每个环节使价值流程是连续的,并对组织进行重新调整,而时间是该流程的重要衡量基准。
4.生产流程必须是根据顾客的需要来拉动。
5.工作必须追求完美,持续改进永无止境。
上世纪80年代后期,该生产方式在乌迪伐拉工厂实践成功,以集中管理方式,配送给各组装车套件,扁平化的组织结构和培养、自律的员工队伍,应用人机工程学原理进行作业研究和改进,提高机械利用率和其与人的最佳匹配。