压力容器制造工艺卡
压力容器工艺过程流转卡

件号
第
3
页
1
共 13
页
控制 标记
序 号
工序
工艺内容及技术要求
R
1
核查
看 清
有裂纹、凹凸、分层、表面无锈蚀。检验员签字确认后划线下料
2
划线
毛 坯 标
W
3 4 5
检验 定位
记 检 验 对
焊 焊接
拼 对 拼 笔
标
φ
划
2
线
1±1㎜ 错边量
W
6 7
检验
检 验 委
托
H
8
检验
1 )
内表面形状偏差:外凸≤1.25% Di 即≤ 25.00 mm
坡口表面不得有裂纹、分层、夹渣等缺陷,清理坡口两侧不小于20㎜范围内污物,打磨见金属光
泽。
6 滚圆 按要求对钢板进行卷筒制作,要求筒节内径Φ444mm。
7
定位 焊
对卷筒完毕后的件进行定位焊,焊道长度10~20mm,间隔50mm,要求错边量b≤3mm,对接间隙
1±1㎜;
W
8
焊接
对筒节的纵焊缝分别进行焊接,清除焊接熔渣及飞溅物,焊接参数见对应的焊接工艺卡,焊接完 成后,
进行标识移植。
W 4 检验 按图纸及工艺检查下料几何尺寸。
W 5 坡口 进行坡口加工,要求按图加工单边V型坡口,坡口角度35°±2°,钝边高度:1±1mm。 坡口表面不得有裂纹、分层、夹渣等缺陷,清理坡口两侧不小于20㎜范围内污物,打磨见金属光 泽。
6 卷制 按要求对钢板进行卷筒制作,要求卷制零件内径Φ2036mm。
文件编号:ZB2005
产品编号 R20-01
管口位置 共
压力容器通用制造工艺过程卡

压力容器通用制造工艺过程卡封头工艺过程卡辽B2—6.1编号共 2 页第 1 页审核:年月日编制:年月日封头工艺过程卡(续页)辽B2—6.2共 2 页第 2 页筒体工艺过程卡辽B2—6.1编号共 2 页第 1 页审核:年月日编制:年月日筒体工艺过程卡(续页)辽B2—6.2 共 2 页第 2 页法兰工艺过程卡辽B2—6.1编号共 1 页第 1 页审核:年月日编制:年月日接管工艺过程卡辽B2—6.1编号共 1 页第 1 页审核:年月日编制:年月日弯管工艺过程卡辽B2—6.1编号共 1 页第 1 页审核:年月日编制:年月日补强圈工艺过程卡辽B2—6.1编号共 1 页第 1 页审核:年月日编制:年月日鞍座(支腿)垫板工艺过程卡辽B2—6.1编号共 1 页第 1 页审核:年月日编制:年月日鞍座(支腿)底板工艺过程卡辽B2—6.1编号共 1 页第 1 页审核:年月日编制:年月日鞍座(支腿)筋板工艺过程卡辽B2—6.1编号共 1 页第 1 页审核:年月日编制:年月日鞍座(支腿)腹板工艺过程卡辽B2—6.1编号共 1 页第 1 页审核:年月日编制:年月日铭牌座工艺过程卡辽B2—6.1编号共 1 页第 1 页审核:年月日编制:年月日人孔法兰工艺过程卡辽B2—6.1编号共 1 页第 1 页审核:年月日编制:年月日人孔筒体工艺过程卡辽B2—6.1编号共 2 页第 1 页审核:年月日编制:年月日人孔筒体工艺过程卡(续页)辽B2—6.2共 2 页第 2 页人孔法兰盖工艺过程卡辽B2—6.1编号共 1 页第 1 页审核:年月日编制:年月日人孔筒体与工艺过程卡辽B2—6.1编号共 1 页第 1 页审核:年月日编制:年月日人孔筒体与工艺过程卡(续页)辽B2—6.2 共 2 页第 2 页。
压力容器制造工艺检验流转卡

铆 工
划线尺寸Φ=
坡口角度α°
坡口钝边P
标记移植
划线尺寸Φ=
坡口角度α°
坡口钝边P
标记移植
E
3
对 接
点 焊
(1)按标号组对。
(2)对坡清理坡口及其两侧各20mm范围内溶渣飞边、除锈 、去污
(3)拼板的对口错边量b不应大于材料厚度δs的10%,且不大于1.5mm。
(4)点固封头拼板。
焊缝代号
A -----筒体及接管等纵缝
B -----筒体及接管等环缝
C-----法兰、平板与筒体及接管等焊缝
D -----接管、凸缘、补强圈等与壳体的焊缝
E -----非受压元件与受压元件的焊缝
BDJL6-03
BDJL6-04
某某
有限公司
容器排版图
名称
压缩空气罐
型号
DN2200
材质
Q345R
编号
R15-0xx
批准手续
返修次数
增探比例
返修结论
批准手续
返修次数
增探比例
返修结论
焊接责任人
签字
E
质控符号:E----检查点H----停止点
筒体制造工艺检验流转卡
BDJL6-06
产品编号
XXXX
材料
Q345R
材料移植号
代用材料
质
控
符号
零部件名称
筒体
规格
DN2200X12
件号
12-2
件数
1
状态
序号
工序
名称
工序内容及工艺要求
质控符号:E----检查点 H----停止点
筒体制造工艺检验流转卡
压力容器出厂检验报告及组装件工艺记录卡
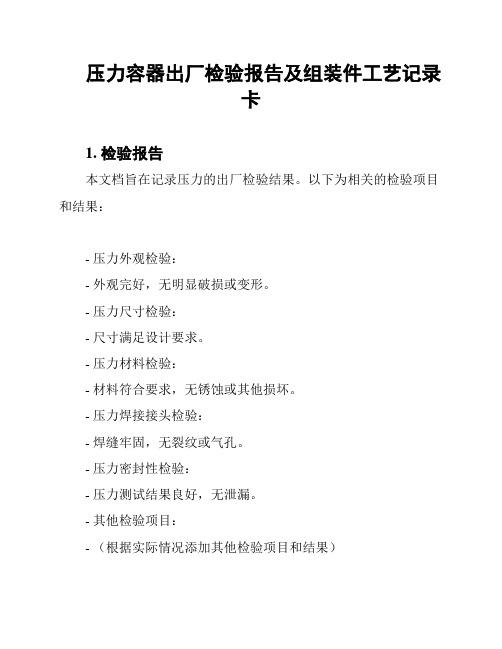
压力容器出厂检验报告及组装件工艺记录
卡
1. 检验报告
本文档旨在记录压力的出厂检验结果。
以下为相关的检验项目和结果:
- 压力外观检验:
- 外观完好,无明显破损或变形。
- 压力尺寸检验:
- 尺寸满足设计要求。
- 压力材料检验:
- 材料符合要求,无锈蚀或其他损坏。
- 压力焊接接头检验:
- 焊缝牢固,无裂纹或气孔。
- 压力密封性检验:
- 压力测试结果良好,无泄漏。
- 其他检验项目:
- (根据实际情况添加其他检验项目和结果)
根据以上检验结果,本压力合格出厂,并可投入使用。
2. 组装件工艺记录卡
本文档旨在记录压力组装过程中的工艺细节。
以下为相关的组装步骤和记录:
1. 准备工作:
- 确保所需组装件齐全。
- 清洁工作区域,确保卫生和安全。
2. 组装步骤:
1. (详细描述组装步骤)
2. (详细描述组装步骤)
3. (详细描述组装步骤)
- (根据实际情况添加更多组装步骤)
3. 检查和测试:
- 对组装完成的压力进行外观检查。
- 进行密封性测试,确保无泄漏。
- (根据实际情况添加其他检查和测试步骤)
4. 验收和记录:
- 完成组装后,对压力进行验收。
- 记录组装日期、验收人员和相关检查结果。
以上为组装件工艺记录卡的简要内容。
具体的组装步骤和记录应根据实际情况进行详细记录。
压力容器工艺工序过程卡

产品名称:Ф1200×5104反应釜
产品编号:06WY1—601
编制:王鹉2005年12月14日
校审:2005年12月15日
批准:张中伟2005年12月16日
中国长城铝业公司建设公司
NO.2
产品名称
Ф1200反应釜
压力容器主要零部件制造工艺(工序)过程卡
容器类别
Ⅱ类
件号
1
产品编号
材质、标记
3.实测钢板厚度,用超声波逐张进行检验,Ⅲ级合格。
厚度
二
筒节排料划线
1.按(封头内径+55)×3.14159展开长度划下料线、检查线、加工线,划线公差≯1.5mm,宽误差≯1.5mm,对角线误差≯2mm,长=3943mm,宽=2100mm,对角线=4467mm。
划线尺寸(长)
划线尺寸(宽)
06WY1--601
主材牌号
16MnR
规格
φ1200×55
图号
06WY1--0
部件名称
首节筒体
序号
工序
工艺内容与技术要求
工装
设备
检验项目
自检值
操作者
专检值
检验员
时间
备注
一
领料
检验
1.检查材料表面状况,不允许有裂纹、结疤、折叠、夹渣、分层、麻坑等缺陷。
表面质量
2.核对出厂标记与质量证明书是否一致,打材料标记,填写记录。
2.移植材料标记,打产品编号钢印。
标记移植
3.检查员复验划线尺寸、打确认钢印。
尺寸
4.确认
检验责任工程师确认:
三
下料
按下料线切割下料,清除毛刺、熔渣。
半自动切割机
压力容器焊接工艺过程卡

卷筒
将板材卷成圆筒
卷弯至筒体要求的尺寸
CDW11-8 2500B上调式三辊卷板机
7
装配
将卷制的筒体进行装配,并固定好
无错边,定位精确,坡口间距符合标准约2mm
螺旋拉紧器,夹具
8
纵缝焊接
将装配好的筒节进行焊接
无弧坑、咬边、裂纹等缺陷,焊缝平整、均匀,余高约为1.5mm缝宽约8mm
MAG半自动焊机
9
矫圆
将筒节进行形状矫正处理
筒节横截面符合设计尺寸要求
三辊卷板机
10
检验
对焊缝进行无损检验
符合焊缝质量国家标准Ⅱ级
X射线探伤装置
X射线
压力容器主要受压元件工艺过程卡
产品编号
产品名称
图号
容器类别
零件名称
件号
零件图号或标准号
数量
规格
材质
材料标记
责任师确认
压力容器
筒节
2
序号
工序名称
工作内容
质量要求
加工设备
主要检验工具
检查结果
操作者
检查员
接受人
交检日期
备注
1
材料复检
检验材料是否符合质量要求,选出拟定规格板材
确保材料符合所用的要求1800 6400 12料两块
材料质证书
化学成分实验设备
2
表面预处理
对板材进行机械除锈、喷丸处理等
要求表面无锈迹,且材料达到所要求的强度
GYX-nM预处理装置和喷丸机
3
下料
按排版图尺寸下料
等离子切割机
4
边缘加工
对板材边缘进行刨边,加工出符合要求的V型坡口
坡口表面平整,无裂纹、划痕
压力容器制造工艺流程图[1]
![压力容器制造工艺流程图[1]](https://img.taocdn.com/s3/m/73836dcda1c7aa00b52acbfb.png)
焊筒节纵缝、抛光
试板检验探伤
试板检验
产品焊接试板 B 类项目 确认通知书
焊缝射线探伤报告 焊缝探伤合格通知
检验探伤 组焊环缝、容器法兰、抛光
审核
检验探伤
开孔划线
检验
责任部门
电焊工、冷作工 检验员 电焊工 检验员员 压力试验责任人
最终检验责任人
压力容器制造工艺流程图
责任部门
材料责任人 生产管理部
冷作工检验员
压力容器制造工艺流程图
流程图
材料确认、生产指令
相关说明
标记确认、放样划线
使用表单
材料入库验收 通知书
制造工艺过程卡
检验员
冷作工 冷作工、电焊工、检验员
下料前检查 下料
刨边、坡口设备
电焊工 抛光工
探伤工
冷作工 电焊工 探伤工
冷作工 检验员
筒节成型
焊第一筒节、试板、抛光
流程图
相关说明
使用表单
接管、法兰、补强板焊接 补强致密检验 内件组装焊接 焊接检验
总装焊接、抛光 总装检验
耐压前审查 耐压试验 检查确认
抛光、包装、铭牌 检验 入成品库 出厂检验 软件归档
耐压试验 A 类项目 确认通知书
耐压试验检验记录卡 铭牌、拓印件 总检记录卡
成品入库清单
压力容器制造工序过程卡
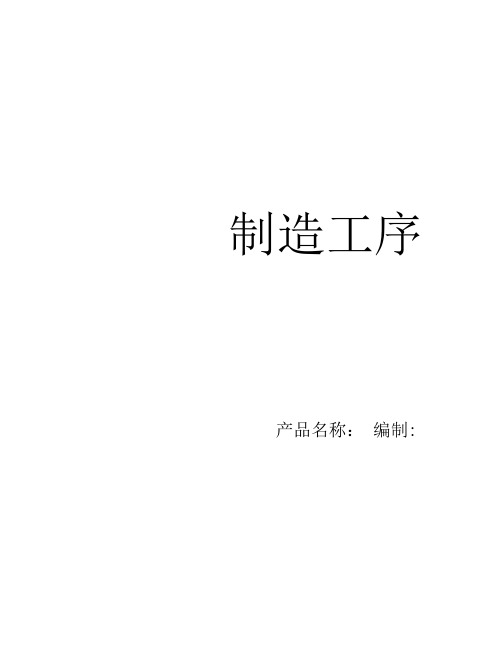
制造工序产品名称:编制:
过程卡制造编号:审核:
制造工序过程卡
注:不锈钢可用等离子体切割编制:年月曰审核:年月日
制造工序过程卡
产品名称:序号:共页第2页
注:不锈钢可用等离子体切割编制:年月曰审核:年月日
序号:共页第4页
产品名称:
编制:年月曰审核:年月日
编制:年月曰审核:年月日
产品名称:序号:共页第7页
编制:年月曰审核:年月日
制造工序过程卡
产品名称:序号:共页第8页
注:不锈钢可用等离子体切割编制:年月曰审核:年月日
序号: 共页第9页
制造工序过程卡
产品名称:
产品名称:序号:共页第10页
编制:年月曰审核:年月日
产品名称:序号:共页第11页
编制:年月曰审核:年月日
产品名称:序号:共页第12页
编制:年月曰审核:年月日
平焊管法兰一览表
编制:年月曰审核:年月日
组装工序过程卡
编制:年月曰审核:年月日
接管安装焊接工序过程卡产品名称:
编制:年月曰审核:年月日
产品名称:序号:共页第页
编制:年月曰审核:年月日
产品名称:序号:共页第页
编制:年月曰审核:年月日
压力容器外观及几何尺寸检验报告产品编号:共页第18页
产品编号: 胀管操作记录: 胀管机型号:
不锈钢产品酸洗钝化处理工艺卡。
- 1、下载文档前请自行甄别文档内容的完整性,平台不提供额外的编辑、内容补充、找答案等附加服务。
- 2、"仅部分预览"的文档,不可在线预览部分如存在完整性等问题,可反馈申请退款(可完整预览的文档不适用该条件!)。
- 3、如文档侵犯您的权益,请联系客服反馈,我们会尽快为您处理(人工客服工作时间:9:00-18:30)。
6 检测 探伤室 按探伤工艺对拼接焊缝进行 100%超声检测,按 JB4730 标准 Ⅰ 级合格。
超声仪
7 热处理 生产科 拼接焊缝按热处理工艺作焊后热处理。
8 校平 铆焊 校正法兰上下平面,要求平面度≤ ± 3.0 mm,棱角度 E≤
mm。
9 车 金工 按零件图车成,要求密封面粗造度
,厚度
mm;作材料标记移植。
Байду номын сангаас
按图纸尺寸及排板要求划线,内外径预留
mm 机加余量;分瓣拼焊时 氧炔
按分 瓣划线。库管员作好材料标记移植,检验员检查确认后,按线下料。
按焊接工艺加工坡口,清理坡口两侧 30mm 范围内污物;拼接焊缝组对错边量
b≤
mm,棱角度 E≤
mm。
按焊接工艺施焊;清除熔渣及焊接飞溅,补焊凹坑、咬边、弧坑等缺陷并修磨; 打焊工钢印;填写施焊记录;检验员检查外观质量。
2 下料
铆焊
按图纸尺寸及排板要求划线,库管员作好材料标记移植,检验员检查确认后,按 氧炔
线下料。
3 煨形 铆焊 按要求滚卷钢板,圆弧部分应与所补强的壳体紧密贴合。
卷板机
钻孔 4 攻丝
金工 在补强板下部、距边缘 15mm 处划线,钻底孔φ8.4mm,丝锥攻丝 M10—7H。 钻床
5 组焊 铆焊 补强板与壳体紧密贴合后点固,按要求施焊。
单台数量
材料状态
检验数据
操作者
检验员
日期
日期
编制
年月日
审核
年月日
3 / 20
艺表—04
产品编号
产品名称
产品图号
序 工序
号
承制 单位
1 备料 库房
压力容器制造工艺卡
补强圈制造卡
件号
材料
工序内容及技术要求
设备 工装
库房备有材质证明书、检验合格的δ= mm,
钢板,要求
材料表面不得有裂纹、结疤、夹渣、分层等缺陷;核对材料标记,实测钢板厚度。
件,冲击
件。 试验机
8 组对
铆焊 按筒体布板图要求组对各筒节,定位焊要求同 4;筒体 B 类环缝组对错边量
b≤ mm,棱角度 E≤
mm;筒体直线度≤H/1000 即≤
mm。
9 焊接 铆焊 要求同 4 条。
10 检测 探伤室 按探伤工艺对 B 类环焊缝进行 %RT 检测,按
标准 级合格。 射线机
共页
第页
年月日
5 / 20
审核
年月日
艺表—05
产品编号
产品名称
产品图号
序 工序
号
承制 单位
1 备料 库房
2 下料 铆焊
3 组对 铆焊
4 焊接 铆焊
压力容器制造工艺卡
法兰制造卡
件号
材料
工序内容及技术要求
设备 工装
库房备有材质证明书、检验合格的δ= mm,
钢板,要求
材料表面无可见缺陷;经超声波检测无分层缺陷;核对材料标记,实测钢板厚度。
材料状态
检验数据
操作者 日期
检验员 日期
4
外协
供应科 库管员在封头坯料上作原材料钢印标记;工艺员填写封头外协委托单;供应科持 委托单联系外协冲压。
⑴检查封头合格证内容是否完整;检查封头原材料标记。
⑵检查封头几何尺寸和表面形状:
内表面形状偏差:外凸≤1.25%Di 即≤
mm,内凹≤0.625%Di 即
入厂 5 检验 检验科
≤
mm;总深度公差为(-0.2~0.6)%Di 即
mm;最小厚度 测厚仪
不得小于
mm;直边倾斜度向外≤1.5mm,向内≤1.0mm;直边高度公
差为(-5~10)%h 即
mm;直径公差为
mm;外周长
公差为
mm;直边部分不得有纵向皱折;封头表面光滑无突变。
⑶作封头入厂检验标记、材料标记移植。
艺表—01
产品编号 产艺品表编—号01
产品名称 产品图号
压力容器制造工艺卡
椭圆封头制造卡 椭圆封头制造卡
件号
材料
共2页 共2页 单台数量
材料状态
第1页 第1页
编制
年月日
1 / 20
审核
年月日
压力容器制造工艺卡
产品名称
单台数量
产品图号
序 工序
号
承制 单位
1 备料 库房
2 下料 铆焊 3 焊接 铆焊
件号
6 检测 探伤室 按探伤工艺对封头拼接焊缝进行 100%RT 检测,按
7 坡口
铆焊/ 按零件图要求加工封头端面坡口。 金工
8 酸洗 生产科 不锈钢封头作酸洗钝化处理。
标准 级合格。 射线机
编制
年月日
审核
年月日
2 / 20
艺表—02
产品编号
产品名称
产品图号
序 工序
号
承制 单位
1 备料 库房
2 下料 铆焊
共2页
第2页
单台数量
材料状态
检验数据
操作者
检验员
日期
日期
6 试验 生产科 补强圈与壳体焊接后,以 0.5 MPa 压缩空气作试漏检查。
空压机
编制
年月日
4 / 20
审核
年月日
艺表—04
产品编号
产品名称 产品图号
压力容器制造工艺卡
补强圈制造卡
件号
材料
共2页 单台数量
材料状态
第1页
件
号
D
D1
δ
材料
数量
编制
焊;清除熔渣及焊接飞溅,补焊凹坑、咬边、弧坑等缺陷并修磨;打焊工钢印;
填写施焊记录;检验员检查外观质量。
筒体校圆,要求最大最小直径差 e≤
mm,棱角度 E≤
mm。 卷板机
6 检测 探伤室 按探伤工艺对纵焊缝进行
%RT 检测,按
标准
级合格。 射线机
7 理化 理化室 焊接试板进行机械性能试验,拉伸
件,弯曲
材料
工序内容及技术要求
设备 工装
库房备有材质证明书、检验合格的δ= mm,
钢板,要求材
料表面不得有裂纹、结疤、夹渣、分层等缺陷;核对材料标记,实测钢板厚度。
按封头理论展开尺寸及排板要求划线,库管员作好材料标记移植,检验员检查确 氧炔 认后,按线下料。
按焊接工艺施焊;将封头起弧段焊缝余高修磨平,但不得低于母材。
检验员检查确认后,按线下料;同时下试板、引弧板、灭弧板。
氧炔
筒体理论下料尺寸为:
。
按工艺规程要求滚卷钢板,筒体 A 类焊缝组对错边量 b≤
mm,棱角度
E≤
mm。筒体纵缝延长部位点固试板、引熄弧板,定位焊长度 20~50mm, 卷板机
间距 150~200mm。
按焊接工艺要求加工坡口,坡口两侧 30mm 范围内清理污物,然后按焊接工艺施
3 卷筒 铆焊
4 焊接 铆焊 5 校圆 铆焊
压力容器制造工艺卡
筒体制造卡
件号
材料
工序内容及技术要求
设备 工装
库房备有材质证明书、检验合格的δ= mm,
钢板,要求材
料表面不得有裂纹、结疤、夹渣、分层等缺陷;核对材料标记,实测钢板厚度。
按实测封头外圆周长计算展开尺寸,按排板要求划线,库管员作好材料标记移植,
10 钻孔
金工
按螺栓孔中心圆直径φ
mm 划线,钻孔 φ
。要求螺栓孔
中心圆直径偏差 ± 1.0 mm, 相邻二螺栓孔弦长允差≤ ± 0.5 mm,任意二
螺栓孔弦长允差≤ ± 1.0 mm。
共页
第页
单台数量
材料状态
检验数据
操作者
检验员
日期
日期
编制
年月日
6 / 20
审核
年月日