压力容器制造工艺流程
压力容器制作通用工艺

4. 机械加工表面和非机械加工表面的线性尺寸的极限偏差,分别按
GB/T1804-2000 中的 m 级和 c 级的规定。
5. 容器法兰按 JB4700~ JB4707-2000 进行加工,管法兰按 HG20592-97
及其它相应标准要求加工。
6. 平盖和筒体端部的加工按以下规定:
a) 螺柱孔或通孔的中心圆直径以及相邻两孔弦长允差为±0.6mm;任
8. 低碳钢及低合金钢封头宜采用热冲压的方法成形,采用冷成形的封头
应进行热处理。奥氏体不锈钢封头宜采用冷成形。
9. 成型后的封头,应用弦长不小于 3/4Di 的样板检查内(或外)表面的 形状偏差,其最大间隙不得大于 1.25%Di,其中 Di 大于 4000mm 的最 大间隙不得大于 1%Di,封头直边部分纵向皱折深度应不大于 1.5 mm, 直边高度允差 h2+5-3。对于碟形及折边锥形封头,其过渡区转角内半径 不得小于图样规定值。偏差的检查应使用样板垂直于表面进行测量,
理、耐压试验等均按我厂压力容器管理制度规定列为关键控制点(停 止点 H)。关键控制点要求工序完工操作者记录并签字,检验员及监理 签证认可后方可转入下道工序。 b. 制作过程中的下料、零件加工、组装、焊前准备、焊后处理等工序均 列为主要控制点。主要控制点的相关尺寸精度、坡口处理、外观质量、
-2-
形位公差等项目必须按 GB150-98 及 GB151-99 的相关要求控制。要求 工序完工自检,检验员复检,双方记录并签字。凡无法事后确认的工 序检验必须经监理认可后方可转入下道工序。 c. 产品工艺过程对工序的要求列为一般控制点。可根据工厂制造条件、 工艺工装情况及产品特殊的工艺要求等进行确定。主要是保证下道工 序能满足制造标准规定或制造环节必须的工艺工序见证。例如原材料 的处理,下料后的板边清理,涂装前的清理等。控制方法可参照主要 控制点的方法。 二、材料: 1. 压力容器用材料应附合 GB713-2008 和其它相应的国家标准、行业标准 的规定。我公司压力容器用材料应取得材料生产单位质量证明书原件或 复印件(加盖材料专用红章并签字),且材料上应有清晰、牢固的钢印 标志或其它标志在明显部位,至少包括材料制造标准代号、材料牌号及 规格、炉(批)号、国家安全监察机构认可标志、材料生产单位及检验 印鉴标志。材料质量证明书的内容必须齐全、清晰,并加盖材料生产单 位质量检验章(红章)。
压力容器制造工艺(3篇)
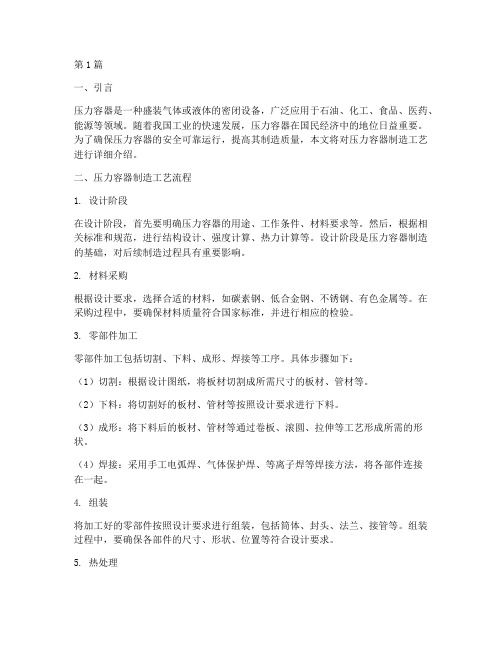
第1篇一、引言压力容器是一种盛装气体或液体的密闭设备,广泛应用于石油、化工、食品、医药、能源等领域。
随着我国工业的快速发展,压力容器在国民经济中的地位日益重要。
为了确保压力容器的安全可靠运行,提高其制造质量,本文将对压力容器制造工艺进行详细介绍。
二、压力容器制造工艺流程1. 设计阶段在设计阶段,首先要明确压力容器的用途、工作条件、材料要求等。
然后,根据相关标准和规范,进行结构设计、强度计算、热力计算等。
设计阶段是压力容器制造的基础,对后续制造过程具有重要影响。
2. 材料采购根据设计要求,选择合适的材料,如碳素钢、低合金钢、不锈钢、有色金属等。
在采购过程中,要确保材料质量符合国家标准,并进行相应的检验。
3. 零部件加工零部件加工包括切割、下料、成形、焊接等工序。
具体步骤如下:(1)切割:根据设计图纸,将板材切割成所需尺寸的板材、管材等。
(2)下料:将切割好的板材、管材等按照设计要求进行下料。
(3)成形:将下料后的板材、管材等通过卷板、滚圆、拉伸等工艺形成所需的形状。
(4)焊接:采用手工电弧焊、气体保护焊、等离子焊等焊接方法,将各部件连接在一起。
4. 组装将加工好的零部件按照设计要求进行组装,包括筒体、封头、法兰、接管等。
组装过程中,要确保各部件的尺寸、形状、位置等符合设计要求。
5. 热处理对压力容器进行热处理,以改善其力学性能、消除残余应力等。
热处理方法包括退火、正火、调质、固溶处理等。
6. 检验检验是压力容器制造过程中的重要环节,包括外观检查、尺寸检查、无损检测、力学性能检测等。
检验结果应满足相关标准和规范的要求。
7. 表面处理为了提高压力容器的耐腐蚀性能、美观度等,可对其进行表面处理,如喷漆、镀锌、阳极氧化等。
8. 标识在压力容器上标注相关信息,如制造单位、产品编号、材料牌号、工作压力、温度等。
9. 出厂经过检验合格的压力容器,办理出厂手续,交付用户使用。
三、压力容器制造工艺特点1. 材料要求严格压力容器制造对材料的质量要求较高,需选用符合国家标准、具有良好力学性能和耐腐蚀性能的材料。
压力容器制造工艺流程

压力容器制造工艺流程压力容器是一种用于储存或运输气体或液体的设备,通常用于工业生产中。
由于其特殊的使用环境和功能要求,压力容器的制造工艺流程需要严格遵循相关的标准和规范,确保其安全可靠。
下面将详细介绍压力容器的制造工艺流程。
1. 设计阶段压力容器的制造工艺流程首先需要进行设计阶段,这一阶段的主要任务是确定压力容器的结构、材料、尺寸和工作参数等。
设计人员需要根据客户的需求和相关标准规范进行设计,确保压力容器在使用过程中能够满足安全和功能要求。
2. 材料准备在确定了压力容器的设计方案后,需要准备相应的材料。
压力容器的材料通常包括钢板、合金钢、不锈钢等。
在材料准备阶段,需要对材料进行检验和验收,确保其质量符合要求。
3. 材料加工一般情况下,压力容器的制造工艺流程包括下列工序:切割、弯曲、焊接、成型、表面处理等。
首先,需要根据设计图纸对材料进行切割和弯曲加工,以满足压力容器的结构要求。
随后,进行焊接工艺,将各个部件进行组装,形成压力容器的整体结构。
在加工过程中,需要严格控制各个工序的质量,确保压力容器的结构牢固、密封性好。
4. 检测与检验在压力容器制造的过程中,需要进行多次的检测与检验,以确保其质量和安全性。
常见的检测手段包括X射线检测、超声波检测、磁粉探伤等。
通过这些检测手段,可以对压力容器的焊缝、材料和结构进行全面检测,确保其符合相关标准和规范的要求。
5. 表面处理在压力容器制造完成后,需要进行表面处理,以提高其耐腐蚀性能和美观度。
常见的表面处理方法包括喷砂、喷漆、镀锌等。
通过表面处理,可以有效延长压力容器的使用寿命,提高其外观质量。
6. 总装与调试最后一道工序是压力容器的总装与调试。
在总装过程中,需要将各个部件进行组装,确保其结构完整、功能正常。
随后进行压力测试和泄漏测试,以验证压力容器的安全性和密封性。
只有通过了严格的测试,压力容器才能出厂并投入使用。
综上所述,压力容器的制造工艺流程包括设计、材料准备、材料加工、检测与检验、表面处理、总装与调试等多个环节。
压力容器制造工艺流程

压力容器制造工艺流程图工艺流程:采购原材料——>检验——>下料——>制作成型——>组对、焊接——>耐压试验——>喷漆——>检验——>入库一、选材及下料(一)容器设备的选材原理1.具有足够的强度,塑性,韧性和稳定性。
2.具有良好的冷热加工性和焊接性能。
3.在有腐蚀性介质的设备必须有良好的耐蚀性和抗氢性。
4.在高温状态使用的设备要有良好的热稳定性。
5.在低温状态下使用的设备要考虑有良好的韧性。
(二)设备容器材料的种类1.碳钢,低合金钢2.不锈钢3.特殊材料:①复合材料(16MnR+316L)②刚镍合金③超级双向不锈钢④哈氏合金(NiMo:78% 20%合金)(三)常用材料常用复合材料:16MnR+0Gr18Ni9A:按形状分:钢板、棒料、管状、铸件、锻件B:按成分分:碳素钢:20号钢20R Q235低合金钢:16MnR、16MnDR、09MnNiDR、15CrMoR、16Mn锻件、20MnMo锻件高合金钢:0Cr13、0Cr18Ni9、0Cr18Ni10Ti尿素级材料:X2CrNiMo18.143mol(尿素合成塔中使用,有较高耐腐蚀性)二、下料工具与下料要求(一)下料工具及试用范围:1、气割:碳钢2、等离子切割:合金钢、不锈钢3、剪扳机:&≤8㎜L≤2500㎜切边为直边4、锯管机:接管5、滚板机:三辊(二)椭圆度要求:内压容器:椭圆度≤1%D;且≤25㎜换热器:DN≤1200㎜椭圆度≤0.5%DN且≤5㎜DN﹥1200㎜椭圆度≤0.5%DN且≤7㎜塔器:DN(500,1000)(1000,2000)(2000,4000)(4000,+∞)椭圆度±5㎜±10㎜±15㎜±20㎜多层包扎内筒:椭圆度≤0.5%D,且≤6㎜(三)错边量要求:见下表(四)直线度要求:一般容器:L≤30000 ㎜直线度≤L/1000㎜L﹥30000㎜直线度按塔器塔器:L≤15000 ㎜直线度≤L/1000㎜L﹥15000㎜直线度≤0.5L/1000 +8㎜换热器:L≤6000㎜直线度≤L/1000且≤4.5㎜L﹥6000㎜直线度≤L/1000且≤8㎜三、焊接(一)焊前准备与焊接环境1、焊条、焊剂及其他焊接材料的贮存库应保持干燥,相对湿度不得大于60%。
压力容器制造工艺流程

压力容器制造工艺流程
压力容器制造工艺流程是指将原材料经过一系列工艺加工和组装而制成压力容器的过程。
下面是一个常见的压力容器制造工艺流程的简要描述。
1.材料准备:选择合适的材料,如碳钢、不锈钢等,根据容器的用途和工作条件进行材料选型。
2.设计和制图:根据容器的工作压力、体积和形状要求,进行容器的设计和制图。
3.材料切割和成型:根据制图要求,使用自动切割机或者剪切机对材料进行切割,然后使用折弯机或者模具将切割好的材料进行成型。
4.焊接:将成型后的材料进行焊接,常见的焊接方法包括电弧焊、气体保护焊等。
焊接过程中需要控制好焊接温度和焊接速度,确保焊缝的质量和强度。
5.热处理:对已焊接好的容器进行热处理,以消除焊接过程中产生的应力和改善材料的性能。
6.表面处理:对容器的内外表面进行处理,如除锈、喷漆等,以保护容器的表面免受腐蚀和磨损。
7.安装和组装:根据容器的用途,安装和组装附件,如法兰、阀门、测量仪表等。
8.压力试验:将容器充满压力介质,进行压力试验,以确认容器的密封性和耐压性能。
9.检验和验收:对制造完成的容器进行非破坏性检测和物理性能测试,以确保容器的质量符合相关的国家标准和规定。
10.交付和使用:经过检验合格的容器交付给用户使用,并按照规定进行维护和保养。
以上是一个典型的压力容器制造工艺流程,具体的工艺步骤和流程可能因不同的容器类型和要求而有所不同。
在整个制造过程中,需要严格遵守安全操作规程和相关的国家法规,确保制造出的压力容器的质量和安全性。
压力容器制造工艺流程

压力容器制造工艺流程压力容器是一种专门用于存储和传递气体或液体的容器,常用于石油化工、医药、食品加工等工业领域。
压力容器制造工艺流程包括以下几个主要步骤:1.设计和规划:在制造压力容器之前,首先需要进行设计和规划。
这包括确定容器的尺寸、材料、工作压力、工作温度等技术参数,并绘制出相应的制造图纸。
2.材料采购和准备:根据设计要求,选择适合的材料。
常用的压力容器材料包括碳钢、不锈钢、合金钢等。
材料采购完成后,需要对其进行加工和处理,如裁剪、焊接和热处理等。
3.加工和制造:根据设计图纸和工艺要求,对准备好的材料进行加工和制造。
一般包括以下几个环节:(1)坯料制备:首先将材料坯料切割成相应的形状和尺寸。
这一步骤通常通过剪切、切割机械或CNC加工中心等设备完成。
(2)成形:将切割好的材料进行成形。
常用的成形方法有冷冲压、热冲压、锻造、旋压等。
(3)焊接:将成形好的零件进行焊接。
焊接工艺通常包括手工焊接、自动焊接和机器人焊接等。
焊接后需要进行无损检测,以确保焊接质量。
(4)热处理:对焊接好的压力容器进行热处理,以提高材料的力学性能和防腐蚀性能。
常见的热处理方法包括退火、正火、淬火、回火等。
(5)表面处理:将处理好的压力容器进行表面处理,如去除焊接痕迹、喷涂防腐涂料等,以提高容器的美观性和耐腐蚀性。
4.检测和测试:在压力容器制造完成后,需要对其进行检测和测试,以确保其质量符合设计和规范要求。
常用的检测方法包括气密性测试、压力测试、超声波检测、射线检测等。
5.验收和出厂:通过检测和测试后,对合格的压力容器进行验收,并进行相应的标识和记录。
验收合格后,进行出厂,用于实际应用。
除了上述主要步骤外,压力容器制造还需要遵守相关的法律法规和标准,如《压力容器安全法》、《压力容器制造和安全技术监察规程》、GB150《钢制压力容器》等,并严格遵循相关的质量管理体系,如ISO9001等。
此外,压力容器制造还需要注意工人的劳保和安全防护,确保生产过程的安全性。
典型压力容器(贮罐)全套制造工艺
空气贮罐容器简图空气贮罐容器制造工艺流程图零件制造工艺筒体制造工艺工艺路线:材料检验——展开尺寸——划线——下料——坡口制备——卷板——装配——探伤、校圆——筒节组焊一.材料检验1.材料:Q235-B2.规格:6000x1500x8mm3. 理化性能应符合HG20592-97《压力容器用钢》标准4.钢板要平直,表面不得有麻点、裂纹、夹层及厚度不均匀等缺陷。
二.展开尺寸1.1500x3166mm 如图12.650x3166mm 如图2三.划线1.划线尺寸见下图.2.对角线误差≤2mm3.在划线的钢板上用油漆注明零件图号、钢号。
四.下料1.采用半自动火焰切割机2.按划线切割3.割口波浪纹≤0.2mm4.清理钢板表面,去毛刺边。
5. 余料用油漆注明钢号、规格。
五.坡口制备1.坡口尺寸见下图2.采用半自动火焰切割机3.割口波浪≤0.2mm六.卷板1.采用三辊卷板机卷弯,2.预弯,用模板(R=500mm δ≥16mm)预弯钢板两端,长度100mm~150mm.3.对中,保持素线与轴辊轴线平行,4.辊弯,用样板(R=500 mmδ=0.8~1.5mm)进行边辊边校正,使样板紧贴筒体内壁。
5.对边错边量≤2mm.七.装配1.清理坡口内壁至出现金属光泽。
2.固定点焊(见焊接工艺卡)3.在纵缝两端点焊两块试板。
4.焊接参数(见焊接工艺卡)八.检验、校圆1.切割去除试板,清理焊缝表面。
2.X射线探伤:(见检验工艺)。
3.测量:用卷尺测量筒节的直径。
4.校圆:在卷板机上校圆。
标准椭圆形封头制造工艺工艺路线:材料检验——化纤——下料——冲压成形——修边——边缘加工一.材料检验1.材料:Q235-B2.规格:1500x6000x83. 理化性能应符合HG20592-97《压力容器用钢》标准4.钢板要平直,表面不得有麻点、裂纹、夹层及厚度不均匀等缺陷。
二.划线1.封头划线尺寸见下图。
2.件数:2件,3.误差≤2mm4.在划线的钢板上用油漆注明零件图号、钢号。
压力容器制造工艺流程及主要工艺参数
压力容器制造工艺流程及主要工艺参数一、压力容器制造工艺流程:1.原材料准备:选择合适的材料,如低合金钢、不锈钢等,并按照图纸要求进行材料切割。
2.加工制造:将原材料进行加工,包括焊接、锻造、铸造等工艺,形成容器的基本形状。
3.进行检测:对制造好的容器进行尺寸检测、无损检测等,确保质量合格。
4.表面处理:对容器进行除锈、喷漆等表面处理,提高容器的耐腐蚀性和美观度。
5.安装配件:根据图纸要求,安装容器上的配件,如阀门、仪表等。
6.再次检测:对已安装好配件的容器进行再次检测,确保安装质量。
7.压力测试:将容器充满压力,进行压力测试,看是否能承受设计压力。
8.整容器检测:对整个容器进行综合检测,确认质量合格。
9.包装出厂:对制造好的容器进行包装,准备出厂。
二、主要工艺参数:1.温度和压力参数:根据容器的设计要求,确定运行的温度和压力参数,包括最大温度、最大压力、设计压力等。
2.材料选择:根据容器的使用环境和介质特性,选择合适的材料,如低合金钢、不锈钢等。
3.容器尺寸:根据容器的设计要求,确定容器的尺寸,包括直径、高度、壁厚等。
4.焊接工艺参数:根据容器的材料和设计要求,确定焊接工艺参数,包括焊接电流、焊接电压、焊接速度等。
5.表面处理要求:根据容器的使用环境和要求,确定表面处理要求,包括除锈等。
6.配件安装要求:根据图纸要求,确定配件安装的位置、尺寸和固定方式等。
7.检测标准:确定容器的检测标准,包括尺寸检测标准、无损检测标准等。
以上是压力容器制造的工艺流程及主要工艺参数的简要介绍。
在实际制造过程中,还需要根据具体的项目和要求进行详细设计和操作,以确保压力容器的质量和安全性。
压力容器制造工艺流程图[1]
焊筒节纵缝、抛光
试板检验探伤
试板检验
产品焊接试板 B 类项目 确认通知书
焊缝射线探伤报告 焊缝探伤合格通知
检验探伤 组焊环缝、容器法兰、抛光
审核
检验探伤
开孔划线
检验
责任部门
电焊工、冷作工 检验员 电焊工 检验员员 压力试验责任人
最终检验责任人
压力容器制造工艺流程图
责任部门
材料责任人 生产管理部
冷作工检验员
压力容器制造工艺流程图
流程图
材料确认、生产指令
相关说明
标记确认、放样划线
使用表单
材料入库验收 通知书
制造工艺过程卡
检验员
冷作工 冷作工、电焊工、检验员
下料前检查 下料
刨边、坡口设备
电焊工 抛光工
探伤工
冷作工 电焊工 探伤工
冷作工 检验员
筒节成型
焊第一筒节、试板、抛光
流程图
相关说明
使用表单
接管、法兰、补强板焊接 补强致密检验 内件组装焊接 焊接检验
总装焊接、抛光 总装检验
耐压前审查 耐压试验 检查确认
抛光、包装、铭牌 检验 入成品库 出厂检验 软件归档
耐压试验 A 类项目 确认通知书
耐压试验检验记录卡 铭牌、拓印件 总检记录卡
成品入库清单
压力容器制造工艺流程
压力容器制造工艺流程1.设计准备阶段:-根据使用要求和相关标准,确定压力容器的基本参数,包括容器材质、容器尺寸等。
-绘制压力容器的设计图纸,包括容器的整体结构和配件安装位置等。
-进行强度计算和有限元分析,确定容器壁厚、焊缝长度等设计参数。
2.材料准备阶段:-根据设计要求,选购符合标准的压力容器材料,包括金属材料和非金属材料。
-对所选购的材料进行验收,包括化学成分分析、机械性能测试等。
-对材料进行切割、修整、清理等预处理工艺,确保材料表面光洁、无裂纹等。
3.成型工艺阶段:-根据设计要求,采用冲压、拉伸、锻造等工艺,对材料进行成型,制造出容器的主体部分。
-对于大型压力容器,可能需要分段成型后进行组装,然后进行焊接。
4.焊接工艺阶段:-根据设计要求,选择合适的焊接方法,包括手工焊接、自动焊接等。
-进行材料的预热处理,确保焊接连接的质量和强度。
-进行焊接操作,包括对主体部分的焊接、焊缝的填充等,确保焊接质量。
5.分部组装阶段:-将焊接完成的部分与其他配件进行组装,如法兰、管道、阀门等。
-对组装后的部件进行调整和校正,保证容器的整体结构和尺寸的准确性。
6.表面处理阶段:-对压力容器的表面进行清理,包括除锈、除油等处理工艺。
-进行喷涂、镀锌等表面防护处理,提高容器的耐腐蚀性。
7.检测验收阶段:-对制造完成的压力容器进行各种检测,确保其安全可靠。
-包括压力试验、磁粉探伤、超声波检测、射线检测等。
-根据相关标准的要求,对检测结果进行评估和判定。
8.成品出厂阶段:-对通过检测的压力容器进行整理和包装,确保其运输安全。
-出具相应的质量证明书和合格证明。
综上所述,压力容器制造工艺流程主要包括设计准备、材料准备、成型工艺、焊接工艺、分部组装、表面处理、检测验收以及成品出厂等环节,在每个环节中都需要符合相关标准和要求,以确保最终制造出的压力容器具备安全可靠的性能。
为了保证压力容器的质量,厂家还需严格执行工艺标准和质量控制要求,确保产品合格、出厂安全。
- 1、下载文档前请自行甄别文档内容的完整性,平台不提供额外的编辑、内容补充、找答案等附加服务。
- 2、"仅部分预览"的文档,不可在线预览部分如存在完整性等问题,可反馈申请退款(可完整预览的文档不适用该条件!)。
- 3、如文档侵犯您的权益,请联系客服反馈,我们会尽快为您处理(人工客服工作时间:9:00-18:30)。
28mm
5E
坡口 用铣床加工吊耳坡口坡口型式 K 型,坡口角度 加工 55±5°,钝边 0~2mm,,
坡口型式 坡口角度 坡口钝边
K型 505 0~2mm
6E
准备 转入总装工序
检验结论:
检查员:
年月日
自检(操作者)
结论
签名
专检(检查员)
结论
签名 日期
产品名称
产品编号 产品图号
制造工艺流程卡
零件名称
06Cr19Ni10 规格 89*6
工艺过程工艺要求
7/6 材检编号 材检编号
件号
a
FL2014-01-01
G2014-03 检验项目及数据
工艺要求
项目
数据
领出接管法兰及制备好的接管短节
确认材质规格及检号
按照图纸接管直径 89mm,接管长度尺寸 163mm 进 行划线。并做好标记移植
规格 尺寸 标记移植
确认材质规格及检 号 下料尺寸
标记移植
角度
钝边
/ 3787×1320 B2014-04
30°
0~2mm
卷筒 按左、中、右三点确认预弯弧度,卷制成型,并在 错边量 b
4
E
成型 卷板机上点焊,对口间隙 0~1mm,错边量 b≤2mm。 组对间隙
≤2mm 0~1mm
结 构 示 意 图
自检(操作者)
结论
签名
A1 B2014-04
件号
\
零件加工数量 共 1 件 第 1 件
检验项目及数据
工艺要求
项目
数据
所用材料应具有质量证明书,标记齐全。
划线长度允差±1mm,宽度允差±1mm,两对角线 之差≤2mm。下料人员作好材料标记移植,检验员 确认后,按线下料。 每侧坡口角度 30°,钝边 0~2mm,加工后清除坡 口两侧 20mm 范围内的氧化物等有害杂质,露出金 属光泽。
零件加工数量 共 6 件
序 控制 工 号点 序
名 称 备 1R料
划 2 E线
下 3 E料
打 4 E磨 5 准备
工艺过程工艺要求
检验项目及数据
工艺要求
项目
数据
所用材料应具有质量证明书,标记齐全。
按照图纸筋板规格寸 l=180mm;b=120mm;h=420mm,进行划线。并做好 标记移植
确认材质规 格及检号
按照划线尺寸 400×200×14mm 的规格,用空 气等离子切割进行切割下料
规格 尺寸
14mm 400×200
4 E 坡口
坡口角度 50°±5°,钝边 4mm,加工后清除 坡口两侧 20mm 范围内的氧化物等有害杂质, 露出金属光泽。
坡口角度 钝边
50 度 4mm
5 E 压弧
压制顶部吊耳垫板弧度,垫板应与封头曲面紧 密贴合,其间隙不得大于 1mm,
序 号
控 制 点
工序名称
工艺过程工艺要求 工艺要求
检验项目及数据
项目
数据
1R
备料 所用材料应具有质量证明书,标记齐全。
确认材质规格及检号 /
2 E 划线
按照图纸标准垫板规格尺寸 400×200×14mm, 进行划线。并做好标记移植
规格 尺寸
标记移植
14mm 400×200
B2014-05
3 E 下料
按照划线尺寸 163mm,用锯床进行切割下料
规格 尺寸
/ 89*6 163mm
G2014-03 89*6 163mm
四点定位点固,接管与法兰密封面的垂直度偏差不 4 E 组对 超过 1%Di。
垂直度 管口布置
≤1%Di 跨中
5 E 焊接 焊缝焊接按焊接工艺卡施焊,焊角应凹型圆滑过渡
焊缝质量焊脚 焊脚尺寸
产品编号:
备注
图纸会审记录
产品名称
产品编号
产品图号
一、 设计单位
1.压力容器设计资格:□无 □有
2.总图上的资格印章:□无 □有
3.资格印章编号
二、设计所依据的技术标准、技术规范等是否具有有效版本:□无 □有
三、 图样:1.几何尺寸是否正确:□是 □否
2.图面是否整洁、清晰:□是 □否
3. 技术要求叙述是否正确、完整、简明:□是 □否
焊脚尺寸
无缺陷 ≥6mm
6
准备
转入总装工序
检验结论:
检查员:
年月日
接管法兰与接管短节组对
说 明
自检(操作者)
结论
签名
专检(检查员)
结论
签名 日期
产品名称 产品编号 产品图号 零件名称 部件图号
吊耳垫板 12
制造工艺流程卡
说
吊耳垫板编号
12
件号
\
明
材质 022Cr19Ni10 规 格 14mm 材检编号 B2014-05 零件加工数量 共 2 件
支座垫板
部件图号
2
支座垫板编号
2
件号
\
材质 022Cr19Ni10
序 号
控 制 点
工序名称
规 格 10mm 材检编号 工艺过程工艺要求 工艺要求
B2014-07
零件加工数量 共 3 件 检验项目及数据
项目
数据
1R
备料 所用材料应具有质量证明书,标记齐全。
确认材质规格及检号 /
2 E 划线
按照图纸标准垫板规格尺寸 280×240×10mm, 进行划线。并做好标记移植
确认材质规格及检 号 下料尺寸
标记移植
角度
钝边
/ 200×1322 B2014-06
30°
0~2mm
卷筒 按左、中、右三点确认预弯弧度,卷制成型,并在 错边量 b
4
E
成型 卷板机上点焊,对口间隙 0~1mm,错边量 b≤2mm。 组对间隙
≤2mm 0~1mm
结 构 示 意 图
自检(操作者)
结论
签名
5 E 焊接 按焊接工艺卡施焊。
弧度 吻合间隙
与封头吻合 ≤1mm
6 E 钻孔
在垫板所规定的位置钻孔,用规格8.5mm 钻头 进行钻孔
钻孔直径
8.5mm
7 E 攻丝
在垫板8.5 孔上进行攻螺纹 M10 孔
螺纹规格
M10
8 准备
转入总装工序
检验结论:
检查员:
年月日
自检(操作者)
结论
签名
专检(检查员)
结论
签名 日期
产品名称 产品编号 产品图号 零件名称 部件图号
规格 尺寸 标记移植
10mm 280×240 B2014-07
3 E 下料
按照划线尺寸 280×240×10mm 的规格,用空 气等离子切割进行切割下料
规格 尺寸
10mm 280×240
4 E 压弧 5 E 钻孔
压制支座垫板弧度,垫板应与封头曲面紧密贴 合,其间隙不得大于 1mm,
在垫板所规定的位置钻孔,用规格8mm 钻头进 行钻孔
无缺陷
≥6mm
6
准 备 转入总装工序
检验结论:
检查员:
年月日
接管法兰与接管短节组对
说 明
自检(操作者)
结论
签名
专检(检查员)
结论
签名 日期
产品名称
产品编号 产品图号
制造工艺流程卡
零件名称 法兰接管
部件图号
法兰
接管
序 号
控 制 点
1R
2E
3E
材质 材质
工序名 称
备料
划线
下料
11
法兰接管编号
S30408
规格 尺寸
标记移植
按照划线尺寸 450mm,用锯床进行切割下料
规格 尺寸
/ 89*6 450mm
G2014-03 89*6 450mm
4 E 组对
四点定位点固,接管与法兰密封面的垂直度偏差不 垂直度
超过 1%Di。
管口布置
≤1%Di 跨中
5 E 焊接
焊缝质量 焊缝焊接按焊接工艺卡施焊、焊脚应凹型圆滑过渡
规格
尺寸
标记移植
/
10mm 见图 B2014-08
按照划线尺寸,用空气等离子切割进行切割下料
规格 尺寸
10mm 见图
加工后用角向磨光机清除打磨坡口两侧 20mm 范 围内以及等离子切割时残留的的氧化物、等有害 打磨质量 杂质,露出金属光泽。
件号
e
零件加工数量 共 1 件 第 1 件
检验项目及数据
工艺要求
项目
数据
所用材料应具有质量证明书,标记齐全。
划线长度允差±1mm,宽度允差±1mm,两对角线 之差≤2mm。下料人员作好材料标记移植,检验员 确认后,按线下料。 每侧坡口角度 30°,钝边 0~2mm,加工后清除坡 口两侧 20mm 范围内的氧化物等有害杂质,露出金 属光泽。
4.管口表是否正确统一:□是 □否
5.技术特性表是否正确统一:□是 □否
6.明细表内容是否齐全、正确:□是 □否
四、图样中存在问
题及更改情况:
五、结论意见:
设计责任师
材料零部件责任师
作业(工艺)责任师
检验与试验责任师
焊接责任师
无损检测责任师
图纸会审日期:
年 月日
产品名称
储气罐部件布置方位排版图
产品编号
吊耳 12
制造工艺流程卡
说
吊耳垫板编号
12
件号
\
明
材 Q235B
质
规 格 30mm 材检编号 B2014-09 零件加工数量 共 2 件
序 控制 号 点 工序名
称
工艺过程工艺要求 工艺要求