压力容器制造工艺流程
压力容器制造流程

压力容器制造流程1.原材料采购和准备首先,根据客户的要求,采购合格的原材料,通常使用的材料有碳钢、不锈钢、合金钢等。
原材料应经过材质鉴定和化学成分分析,确保质量和可靠性。
2.板料切割将原材料的板材进行切割,通常使用切割设备如剪板机、等离子切割机等,根据容器的形状和尺寸,将板材切割成适当的尺寸和形状。
3.弯曲和成形利用弯曲机将切割好的板材进行弯曲和成形,得到器件的圆筒形状。
这个过程需要根据设计图纸和布局要求精确控制弯曲半径和角度。
4.焊接将成形的板材进行焊接,通常使用的方法有手工电弧焊、气体保护焊、埋弧焊等。
焊接需要严格遵守焊接程序和参数,以保证焊接质量和可靠性。
5.检测进行焊接后,需要对焊缝进行检测,以确保焊接质量和无缺陷。
常用的检测方法有射线检测、超声波检测、磁粉检测等。
根据相关标准和规范进行检测,并根据检测结果对焊缝进行修补和处理。
6.试验完成焊接和检测后,需要对压力容器进行试验。
常见的试验包括水压试验、气压试验、材料拉伸试验等。
通过试验检测容器的强度和密封性,并确保容器满足设计和使用要求。
7.表面处理完成试验后,对容器进行表面处理,以提高容器的防腐性和美观度。
常见的表面处理方法有喷漆、镀锌、酸洗等。
根据客户要求或相关标准进行表面处理。
8.组装和安装经过表面处理后,将容器的各个部件进行组装和安装,包括法兰、法兰垫片、法兰螺栓等。
保证各个部件的连接紧固度和密封性。
9.验收和出厂根据相关标准和规范,对制造完成的压力容器进行验收。
验收包括物理性能测试、尺寸检查、检测报告和相关证明文件的编制等。
通过验收后,压力容器可以出厂交付给客户。
以上是压力容器制造的典型流程,具体的流程和工序可能会因厂家和产品类型的不同而有所差异。
无论是哪种压力容器,制造过程中都必须严格按照相关标准和规范操作,以确保容器的质量和安全性。
压力容器制造工艺(3篇)
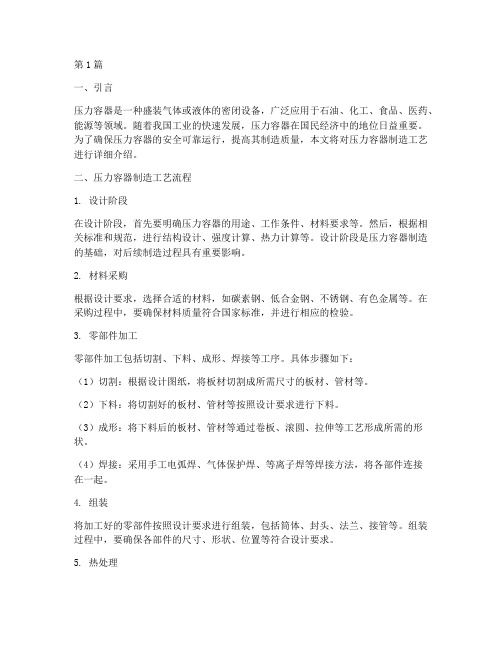
第1篇一、引言压力容器是一种盛装气体或液体的密闭设备,广泛应用于石油、化工、食品、医药、能源等领域。
随着我国工业的快速发展,压力容器在国民经济中的地位日益重要。
为了确保压力容器的安全可靠运行,提高其制造质量,本文将对压力容器制造工艺进行详细介绍。
二、压力容器制造工艺流程1. 设计阶段在设计阶段,首先要明确压力容器的用途、工作条件、材料要求等。
然后,根据相关标准和规范,进行结构设计、强度计算、热力计算等。
设计阶段是压力容器制造的基础,对后续制造过程具有重要影响。
2. 材料采购根据设计要求,选择合适的材料,如碳素钢、低合金钢、不锈钢、有色金属等。
在采购过程中,要确保材料质量符合国家标准,并进行相应的检验。
3. 零部件加工零部件加工包括切割、下料、成形、焊接等工序。
具体步骤如下:(1)切割:根据设计图纸,将板材切割成所需尺寸的板材、管材等。
(2)下料:将切割好的板材、管材等按照设计要求进行下料。
(3)成形:将下料后的板材、管材等通过卷板、滚圆、拉伸等工艺形成所需的形状。
(4)焊接:采用手工电弧焊、气体保护焊、等离子焊等焊接方法,将各部件连接在一起。
4. 组装将加工好的零部件按照设计要求进行组装,包括筒体、封头、法兰、接管等。
组装过程中,要确保各部件的尺寸、形状、位置等符合设计要求。
5. 热处理对压力容器进行热处理,以改善其力学性能、消除残余应力等。
热处理方法包括退火、正火、调质、固溶处理等。
6. 检验检验是压力容器制造过程中的重要环节,包括外观检查、尺寸检查、无损检测、力学性能检测等。
检验结果应满足相关标准和规范的要求。
7. 表面处理为了提高压力容器的耐腐蚀性能、美观度等,可对其进行表面处理,如喷漆、镀锌、阳极氧化等。
8. 标识在压力容器上标注相关信息,如制造单位、产品编号、材料牌号、工作压力、温度等。
9. 出厂经过检验合格的压力容器,办理出厂手续,交付用户使用。
三、压力容器制造工艺特点1. 材料要求严格压力容器制造对材料的质量要求较高,需选用符合国家标准、具有良好力学性能和耐腐蚀性能的材料。
压力容器制造工艺流程

压力容器制造工艺流程压力容器是一种用于储存或运输气体或液体的设备,通常用于工业生产中。
由于其特殊的使用环境和功能要求,压力容器的制造工艺流程需要严格遵循相关的标准和规范,确保其安全可靠。
下面将详细介绍压力容器的制造工艺流程。
1. 设计阶段压力容器的制造工艺流程首先需要进行设计阶段,这一阶段的主要任务是确定压力容器的结构、材料、尺寸和工作参数等。
设计人员需要根据客户的需求和相关标准规范进行设计,确保压力容器在使用过程中能够满足安全和功能要求。
2. 材料准备在确定了压力容器的设计方案后,需要准备相应的材料。
压力容器的材料通常包括钢板、合金钢、不锈钢等。
在材料准备阶段,需要对材料进行检验和验收,确保其质量符合要求。
3. 材料加工一般情况下,压力容器的制造工艺流程包括下列工序:切割、弯曲、焊接、成型、表面处理等。
首先,需要根据设计图纸对材料进行切割和弯曲加工,以满足压力容器的结构要求。
随后,进行焊接工艺,将各个部件进行组装,形成压力容器的整体结构。
在加工过程中,需要严格控制各个工序的质量,确保压力容器的结构牢固、密封性好。
4. 检测与检验在压力容器制造的过程中,需要进行多次的检测与检验,以确保其质量和安全性。
常见的检测手段包括X射线检测、超声波检测、磁粉探伤等。
通过这些检测手段,可以对压力容器的焊缝、材料和结构进行全面检测,确保其符合相关标准和规范的要求。
5. 表面处理在压力容器制造完成后,需要进行表面处理,以提高其耐腐蚀性能和美观度。
常见的表面处理方法包括喷砂、喷漆、镀锌等。
通过表面处理,可以有效延长压力容器的使用寿命,提高其外观质量。
6. 总装与调试最后一道工序是压力容器的总装与调试。
在总装过程中,需要将各个部件进行组装,确保其结构完整、功能正常。
随后进行压力测试和泄漏测试,以验证压力容器的安全性和密封性。
只有通过了严格的测试,压力容器才能出厂并投入使用。
综上所述,压力容器的制造工艺流程包括设计、材料准备、材料加工、检测与检验、表面处理、总装与调试等多个环节。
压力容器生产工艺流程

压力容器制作工艺流程生产指令→审图→材料计划→封头、法兰外委→铆工工艺焊接工艺编制→材料检验→封头验收→计算封头实际中性层→按中性层、管口方位、支座板布置情况排版→下料前标记移植→下料→刨边→试板制作→筒节卷圆→纵缝焊接→试板机械性能试验→人孔制作→法兰验收→法兰与管焊接→对大于φ250的管着色检查→下锥体制作→整体组装→焊接→超声波检查和拍片→对缺陷进行返修→人孔及各管孔划线→停点检查→割制各管孔→管与筒体组装→焊接→超声波探伤及拍片→水压试验→停点检查→需热处理的进行热处理→→工程质量记录由技术监督科保管,交工后由档案室保管, 保存期为7年生产指令→审图(压力容器章、材料表尺寸与图纸是否相符,图中尺寸是否全是否正确、管口方位是否全、材料工程师看采用的材料是否能买到相应的材料)→材料计划(材料按排版情况选择宽度和长度,主要考虑管口方位和接缝情况)→封头外委(比图纸尺寸厚2mm,坡口方向)、法兰(按国家标准画图,清楚要做的是哪个面,注意画水线)外委→铆工工艺(有编制好的工艺,每一受压元件一份工艺卡,上、下封头各份,每一筒节各一份,工人在制作过程中要按工艺流程按时进行填写)、→焊缝布置图(根据焊缝分类和排版图将每一条焊缝在图中进行编号,以便拍片,焊接记录,焊接工艺使用)→焊接工艺编制(一种焊接形式一份工艺,根据焊缝布置图,每一条焊缝都对应有焊接工艺,并对应有焊接工艺评定)→材料检验(核对化学含量、机械性能、炉号、批号、钢号、出厂日期,厚度公差,外观,容器板为正公差)→封头验收(资质、合格证、探伤、拍片报告、直径公差;封头总深度;表面形状公差)→计算封头实际中性层(封头厚度比筒体厚度厚2mm,对接处以内壁对齐,计算中性层时以筒体的中性层为准)→按中性层、管口方位、支座板布置、相邻节焊缝情况排版(筒体的最短筒节长度≥300m,不锈钢>200mm相邻筒节的纵焊缝距离或封头焊缝的端点与相邻筒节纵焊缝的距离应>δn(δn为名义厚度)且>100mm。
压力容器制造工艺流程

压力容器制造工艺流程
压力容器制造工艺流程是指将原材料经过一系列工艺加工和组装而制成压力容器的过程。
下面是一个常见的压力容器制造工艺流程的简要描述。
1.材料准备:选择合适的材料,如碳钢、不锈钢等,根据容器的用途和工作条件进行材料选型。
2.设计和制图:根据容器的工作压力、体积和形状要求,进行容器的设计和制图。
3.材料切割和成型:根据制图要求,使用自动切割机或者剪切机对材料进行切割,然后使用折弯机或者模具将切割好的材料进行成型。
4.焊接:将成型后的材料进行焊接,常见的焊接方法包括电弧焊、气体保护焊等。
焊接过程中需要控制好焊接温度和焊接速度,确保焊缝的质量和强度。
5.热处理:对已焊接好的容器进行热处理,以消除焊接过程中产生的应力和改善材料的性能。
6.表面处理:对容器的内外表面进行处理,如除锈、喷漆等,以保护容器的表面免受腐蚀和磨损。
7.安装和组装:根据容器的用途,安装和组装附件,如法兰、阀门、测量仪表等。
8.压力试验:将容器充满压力介质,进行压力试验,以确认容器的密封性和耐压性能。
9.检验和验收:对制造完成的容器进行非破坏性检测和物理性能测试,以确保容器的质量符合相关的国家标准和规定。
10.交付和使用:经过检验合格的容器交付给用户使用,并按照规定进行维护和保养。
以上是一个典型的压力容器制造工艺流程,具体的工艺步骤和流程可能因不同的容器类型和要求而有所不同。
在整个制造过程中,需要严格遵守安全操作规程和相关的国家法规,确保制造出的压力容器的质量和安全性。
压力容器制造工艺流程

压力容器制造工艺流程压力容器是一种专门用于存储和传递气体或液体的容器,常用于石油化工、医药、食品加工等工业领域。
压力容器制造工艺流程包括以下几个主要步骤:1.设计和规划:在制造压力容器之前,首先需要进行设计和规划。
这包括确定容器的尺寸、材料、工作压力、工作温度等技术参数,并绘制出相应的制造图纸。
2.材料采购和准备:根据设计要求,选择适合的材料。
常用的压力容器材料包括碳钢、不锈钢、合金钢等。
材料采购完成后,需要对其进行加工和处理,如裁剪、焊接和热处理等。
3.加工和制造:根据设计图纸和工艺要求,对准备好的材料进行加工和制造。
一般包括以下几个环节:(1)坯料制备:首先将材料坯料切割成相应的形状和尺寸。
这一步骤通常通过剪切、切割机械或CNC加工中心等设备完成。
(2)成形:将切割好的材料进行成形。
常用的成形方法有冷冲压、热冲压、锻造、旋压等。
(3)焊接:将成形好的零件进行焊接。
焊接工艺通常包括手工焊接、自动焊接和机器人焊接等。
焊接后需要进行无损检测,以确保焊接质量。
(4)热处理:对焊接好的压力容器进行热处理,以提高材料的力学性能和防腐蚀性能。
常见的热处理方法包括退火、正火、淬火、回火等。
(5)表面处理:将处理好的压力容器进行表面处理,如去除焊接痕迹、喷涂防腐涂料等,以提高容器的美观性和耐腐蚀性。
4.检测和测试:在压力容器制造完成后,需要对其进行检测和测试,以确保其质量符合设计和规范要求。
常用的检测方法包括气密性测试、压力测试、超声波检测、射线检测等。
5.验收和出厂:通过检测和测试后,对合格的压力容器进行验收,并进行相应的标识和记录。
验收合格后,进行出厂,用于实际应用。
除了上述主要步骤外,压力容器制造还需要遵守相关的法律法规和标准,如《压力容器安全法》、《压力容器制造和安全技术监察规程》、GB150《钢制压力容器》等,并严格遵循相关的质量管理体系,如ISO9001等。
此外,压力容器制造还需要注意工人的劳保和安全防护,确保生产过程的安全性。
压力容器制造工艺流程及主要工艺参数
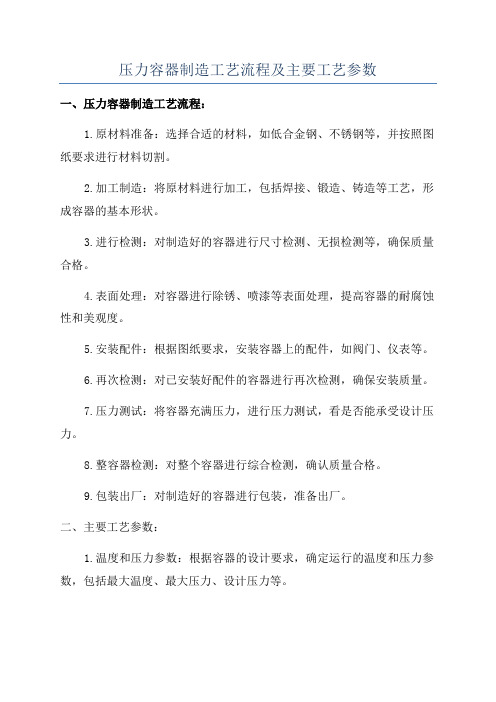
压力容器制造工艺流程及主要工艺参数一、压力容器制造工艺流程:1.原材料准备:选择合适的材料,如低合金钢、不锈钢等,并按照图纸要求进行材料切割。
2.加工制造:将原材料进行加工,包括焊接、锻造、铸造等工艺,形成容器的基本形状。
3.进行检测:对制造好的容器进行尺寸检测、无损检测等,确保质量合格。
4.表面处理:对容器进行除锈、喷漆等表面处理,提高容器的耐腐蚀性和美观度。
5.安装配件:根据图纸要求,安装容器上的配件,如阀门、仪表等。
6.再次检测:对已安装好配件的容器进行再次检测,确保安装质量。
7.压力测试:将容器充满压力,进行压力测试,看是否能承受设计压力。
8.整容器检测:对整个容器进行综合检测,确认质量合格。
9.包装出厂:对制造好的容器进行包装,准备出厂。
二、主要工艺参数:1.温度和压力参数:根据容器的设计要求,确定运行的温度和压力参数,包括最大温度、最大压力、设计压力等。
2.材料选择:根据容器的使用环境和介质特性,选择合适的材料,如低合金钢、不锈钢等。
3.容器尺寸:根据容器的设计要求,确定容器的尺寸,包括直径、高度、壁厚等。
4.焊接工艺参数:根据容器的材料和设计要求,确定焊接工艺参数,包括焊接电流、焊接电压、焊接速度等。
5.表面处理要求:根据容器的使用环境和要求,确定表面处理要求,包括除锈等。
6.配件安装要求:根据图纸要求,确定配件安装的位置、尺寸和固定方式等。
7.检测标准:确定容器的检测标准,包括尺寸检测标准、无损检测标准等。
以上是压力容器制造的工艺流程及主要工艺参数的简要介绍。
在实际制造过程中,还需要根据具体的项目和要求进行详细设计和操作,以确保压力容器的质量和安全性。
压力容器制造工艺流程

压力容器制造工艺流程1.设计准备阶段:-根据使用要求和相关标准,确定压力容器的基本参数,包括容器材质、容器尺寸等。
-绘制压力容器的设计图纸,包括容器的整体结构和配件安装位置等。
-进行强度计算和有限元分析,确定容器壁厚、焊缝长度等设计参数。
2.材料准备阶段:-根据设计要求,选购符合标准的压力容器材料,包括金属材料和非金属材料。
-对所选购的材料进行验收,包括化学成分分析、机械性能测试等。
-对材料进行切割、修整、清理等预处理工艺,确保材料表面光洁、无裂纹等。
3.成型工艺阶段:-根据设计要求,采用冲压、拉伸、锻造等工艺,对材料进行成型,制造出容器的主体部分。
-对于大型压力容器,可能需要分段成型后进行组装,然后进行焊接。
4.焊接工艺阶段:-根据设计要求,选择合适的焊接方法,包括手工焊接、自动焊接等。
-进行材料的预热处理,确保焊接连接的质量和强度。
-进行焊接操作,包括对主体部分的焊接、焊缝的填充等,确保焊接质量。
5.分部组装阶段:-将焊接完成的部分与其他配件进行组装,如法兰、管道、阀门等。
-对组装后的部件进行调整和校正,保证容器的整体结构和尺寸的准确性。
6.表面处理阶段:-对压力容器的表面进行清理,包括除锈、除油等处理工艺。
-进行喷涂、镀锌等表面防护处理,提高容器的耐腐蚀性。
7.检测验收阶段:-对制造完成的压力容器进行各种检测,确保其安全可靠。
-包括压力试验、磁粉探伤、超声波检测、射线检测等。
-根据相关标准的要求,对检测结果进行评估和判定。
8.成品出厂阶段:-对通过检测的压力容器进行整理和包装,确保其运输安全。
-出具相应的质量证明书和合格证明。
综上所述,压力容器制造工艺流程主要包括设计准备、材料准备、成型工艺、焊接工艺、分部组装、表面处理、检测验收以及成品出厂等环节,在每个环节中都需要符合相关标准和要求,以确保最终制造出的压力容器具备安全可靠的性能。
为了保证压力容器的质量,厂家还需严格执行工艺标准和质量控制要求,确保产品合格、出厂安全。
- 1、下载文档前请自行甄别文档内容的完整性,平台不提供额外的编辑、内容补充、找答案等附加服务。
- 2、"仅部分预览"的文档,不可在线预览部分如存在完整性等问题,可反馈申请退款(可完整预览的文档不适用该条件!)。
- 3、如文档侵犯您的权益,请联系客服反馈,我们会尽快为您处理(人工客服工作时间:9:00-18:30)。
2
E
划线
按照图纸接管直径89mm,接管长度尺寸163mm进行划线。并做好标记移植
规格
89*6
尺寸
163mm
标记移植
G2014-03
3
E
下料
按照划线尺寸163mm,用锯床进行切割下料
规格
89*6
尺寸
163mm
4
E
组对
四点定位点固,接管与法兰密封面的垂直度偏差不超过1%Di。
垂直度
≤1%Di
管口布置
跨中
6
准备
转入总装工序
检验结论:检查员:年月日
产品名称
制造工艺流程卡
说明
产品编号
ห้องสมุดไป่ตู้产品图号
零件名称
吊耳垫板
部件图号
12
吊耳垫板编号
12
件号
\
材质
022Cr19Ni10
规格
14mm
材检编号
B2014-05
零件加工数量
共2件
序号
控制点
工艺过程工艺要求
检验项目及数据
自检(操作者)
专检(检查员)
工序名称
工艺要求
项目
坡口型式
K型
坡口角度
505
坡口钝边
0~2mm
6
E
准备
转入总装工序
检验结论:检查员:年月日
产品名称
制造工艺流程卡
说明
产品编号
产品图号
零件名称
支座垫板
部件图号
2
支座垫板编号
2
件号
\
材质
022Cr19Ni10
规格
10mm
材检编号
B2014-07
零件加工数量
共3件
序号
控制点
工艺过程工艺要求
检验项目及数据
自检(操作者)
规格
14mm
尺寸
400×200
4
E
坡口
坡口角度50°±5°,钝边4mm,加工后清除坡口两侧20mm范围内的氧化物等有害杂质,露出金属光泽。
坡口角度
50度
钝边
4mm
5
E
压弧
压制顶部吊耳垫板弧度,垫板应与封头曲面紧密贴合,其间隙不得大于1mm,
弧度
与封头吻合
吻合间隙
≤1mm
6
E
钻孔
在垫板所规定的位置钻孔,用规格8.5mm钻头进行钻孔
规格
89*6
尺寸
450mm
标记移植
G2014-03
3
E
下料
按照划线尺寸450mm,用锯床进行切割下料
规格
89*6
尺寸
450mm
4
E
组对
四点定位点固,接管与法兰密封面的垂直度偏差不超过1%Di。
垂直度
≤1%Di
管口布置
跨中
5
E
焊接
焊缝焊接按焊接工艺卡施焊、焊脚应凹型圆滑过渡
焊缝质量
无缺陷
焊脚尺寸
≥6mm
说明
产品编号
产品图号
零件名称
支座底板
部件图号
2
支座底板编号
2
件号
\
材质
Q235B
规格
10mm
本厂材编
B2014-08
零件加工数量
共3件
序号
控制点
工艺过程工艺要求
检验项目及数据
自检(操作者)
专检(检查员)
工序名称
工艺要求
项目
数据
结论
签名
结论
签名
日期
1
R
备料
所用材料应具有质量证明书,标记齐全。
确认材质规格及检号
压力容器制造工艺流程卡
产品编号:产品名称:
产品图号:工艺编号:
编制:
校核:
审批:
工艺文件目录
产品名称:产品编号:
序号
文件名称
备注
1
图纸会审记录
2
筒体部件布置方位排版图
3
筒体制造工艺过程卡
4
人孔筒节制造工艺卡
5
人孔法兰与筒节组装工艺卡
6
法兰接管(a)制造工艺卡
7
法兰接管(d)制造工艺卡
8
吊耳、垫板制造工艺卡
打磨质量
表面光滑,无缺陷
5
E
钻孔
在底板中心的位置钻地脚螺栓孔,用规格24mm钻头进行钻孔
钻孔直径
24mm
6
E
准备
转入总装工序
检验结论:检查员:年月日
产品名称
制造工艺流程卡
说明
按JB/T4712.4-2007支座A2图纸进行制作
专检(检查员)
工序名称
工艺要求
项目
数据
结论
签名
结论
签名
日期
1
R
备料
所用材料应具有质量证明书,标记齐全。
确认材质规格及检号
/
2
E
划线
按照图纸标准垫板规格尺寸280×240×10mm,进行划线。并做好标记移植
规格
10mm
尺寸
280×240
标记移植
B2014-07
3
E
下料
按照划线尺寸280×240×10mm的规格,用空气等离子切割进行切割下料
≤1%Di
管口布置
跨中
3
E
焊接
焊接角焊缝,按焊接工艺卡施焊、焊脚尺寸应≥10mm,焊脚应凹形圆滑过渡。
焊缝质量
无缺陷
焊脚尺寸
≥10mm
4
5
6
7
8
准备
转入总装工序
检验结论:检查员:年月日
产品名称
制造工艺流程卡
说明
接管法兰与接管短节组对
产品编号
产品图号
零件名称
法兰接管
部件图号
7/6
法兰接管编号
7/6
件号
a
法兰
材质
S30408
规格
PL80-10RF
材检编号
FL2014-01-01
接管
材质
06Cr19Ni10
规格
89*6
材检编号
G2014-03
序号
控制点
工艺过程工艺要求
检验项目及数据
自检(操作者)
专检(检查员)
工序
名称
工艺要求
项目
数据
结论
签名
结论
签名
日期
1
R
备料
领出接管法兰及制备好的接管短节
确认材质规格及检号
/
8
准备
转入壳程组装工序。
检验结论:检查员:年月日
产品名称
制造工艺流程卡
结构示意图
产品编号
产品图号
零件名称
人孔筒节
筒体图号
4
筒体编号
A2
件号
e
材质
06Cr19Ni10
规格
δ=5
本厂材编
B2014-06
零件加工数量
共1件第1件
序号
控制点
工艺过程工艺要求
检验项目及数据
自检(操作者)
专检(检查员)
工序名称
棱角度
≤2.5mm
7
R
无损检测
对焊缝进行100% RT检测,按JB/T4730.2-2005标准Ⅲ级合格。
见无损检测报告单
/
8
E
准备
转入人孔法兰与人孔筒节组对工序
检验结论:检查员:年月日
产品名称
制造工艺流程卡
人孔法兰
产品编号
产品图号
零件名称
人孔法兰
筒体图号
4
部件编号
RK2014-01
件号
e
材质
06Cr19Ni10
下料尺寸
3787×1320
标记移植
B2014-04
3
E
坡口加工
每侧坡口角度30°,钝边0~2mm,加工后清除坡口两侧20mm范围内的氧化物等有害杂质,露出金属光泽。
角度
30°
钝边
0~2mm
4
E
卷筒成型
按左、中、右三点确认预弯弧度,卷制成型,并在卷板机上点焊,对口间隙0~1mm,错边量b≤2mm。
错边量b
钻孔直径
8.5mm
7
E
攻丝
在垫板8.5孔上进行攻螺纹M10孔
螺纹规格
M10
8
准备
转入总装工序
检验结论:检查员:年月日
产品名称
制造工艺流程卡
说明
产品编号
产品图号
零件名称
吊耳
部件图号
12
吊耳垫板编号
12
件号
\
材质
Q235B
规格
30mm
材检编号
B2014-09
零件加工数量
共2件
序号
控制点
工艺过程工艺要求
检验项目及数据
图纸会审日期:年月日
储气罐部件布置方位排版图
产品名称
产品编号
部件名称
筒体
规格
DN1200
部件方位排版图注:b管件在上封头,f管件在下封头;部件尺寸详见图纸
产品名称
制造工艺流程卡
结构示意图
产品编号
产品图号
零件名称
壳程筒节
筒体图号
5
筒体编号
A1
件号
\
材质
022Cr19Ni10
规格
δ=6
材检编号
B2014-04
9
支座、垫板制造工艺卡
10