轻烃回收工艺技术及其进展
轻烃回收工艺的发展趋势及新技术研讨

一、国内外轻烃回收当前的发展情况1.国外轻烃回收的相关工艺概述国外的轻质烃采收工艺最早出现于1904年。
第一座轻油采收工厂建于美国,已有100多年的历史。
国外的轻烃回收过程起步较早,因此比我国的过程要先进。
轻烃的产量以及油气资源的有效利用在国外加工中均取得了巨大成就。
行业在1970年代,其技术的研发目标开始不断提高公司自身的运营效率,以提高轻质烃的产量以及节能和减少能耗。
比较成熟的点主要是低温分离法。
该轻烃工艺具有深层分离,投资少,能耗低,效率高和撬装技术的技术优势,并且目前正在朝自动化方向发展。
2.我国轻烃回收工艺的相关概述我们国家的天然气轻烃分离技术开始在上个世纪的60年代产生,因为这一工艺当前的发展起步的相对来说会比较晚,只是发展只是停留在上个世纪的30到40年代国外的轻烃上的回收水平,这样的一种情况使得我国天然气企业受到了轻烃回收工艺的制约,产品的质量不能够满足预期的标准,并且轻烃自身的收率也并不高,企业完成生产得产品主要是被当成是民用以及工业燃料使用。
二、轻烃回收的相关技术概述1.轻烃回收技术的基础原理轻烃回收当前主要是运用气体混合物里很多不同的组成成分的一种液体溶解度之间出现的差别去完成所需要的吸收,从而使其能够达成气体混合物之间的物质分离。
整体进行吸收的过程主要是在固定的压力以及温度条件下去完成的,气液两相其在塔板上完成接触,通过多种液体烃类构成在吸收剂里溶解度产生的差异去完成阶段性分离吸收。
2.轻烃回收的相关工艺装置一般我国选择的轻烃回收工艺装置其本身属于一种使用煤液化的装置;其原料的分离尾气其主要是运用煤液化膜;塔顶气选择的主要是一种加氢的稳定装置;含硫气使用加氢改质装置,其他构成部分则属于间接的液化富气和净化中压气回收氢气后的尾气以与接液化富液等一系列的回收装置。
轻烃回收的核心目标主要是把液化气和石脑油等部分产品完成回收,并且为提供原料干气作为全厂使用的燃料气。
三、轻烃回收的核心工艺低温回收工艺其本身属于一种低温的分离方式,主要是按照原料中多种不同烃类气体其自身的冷凝温度差异完成不断分离的一种技术方法,实际的操作主要是先把原料气完成有效的冷却,然后不断的提高装置自身的反应温度,使用原料气中多种烃类在其沸点上的差异不断完成冷凝分离,再进行凝液精馏分离使其生成一种符合要求的产品。
轻烃回收工艺的发展方向及新技术

2018年08月轻烃回收工艺的发展方向及新技术王祥(中国石油集团公司吐哈油田分公司吐鲁番采油厂,新疆吐鲁番838000)摘要:随着我国节能减排保护环境政策的不断深入,越来越多的工业生产企业重视生产过程中的环保问题,并且引进新技术对产品进行高效回收处理,以降低污染物的排放。
目前,工业生产中除了对环保的需求量呈现出了大幅度增加的趋势外,对轻烃回收工艺的发展方向以及新技术的关注程度越来越高。
在轻烃回收工艺应用发展的过程中,虽然有许多工艺但是低温分离回收工艺是应用的最普遍的,但是轻烃回收工艺过程中能耗比较大,而收到的效益却并不理想,所以轻烃回收处理企业一直对轻烃回收工艺的发展和新技术进行研究和创新,以寻求更好的轻烃回收工艺来提高轻烃回收的经济效益和环保。
关键词:轻烃;回收工艺;发展方向;新技术目前我国化工企业在经济发展中也占据着非常重要的一部分,虽然在化工生产中会产生大量的污染物,但是在社会需求发展的状况下,已经加大对一些物质的回收再利用工艺的发展研究,既保障化工生产的需求也要保护环境并提高一些轻烃类物质的循环利用。
近几年,在天然气烃类回收中,使得天然气的经济效益有了明显的增长,而在轻烃回收工艺中,低温分离回收工艺应用的较为广泛和成熟,但是为了更好的提高轻烃的回收效率,加大轻烃回收工艺的发展和引进新技术是非常重要的。
1轻烃回收工艺发展方向分析1.1轻烃回收原理轻烃的回收处理主要是物理方法,即对轻烃低温分离,利用天然气中各组分在不同的温度和压力下挥发度不同的原理,来分离轻烃各组分。
首先,轻烃气体加压冷却,脱除杂质和水分,然后低温液化、进塔分离。
在分离过程中,气体和液体在塔板上接触,并且在温度和压力的作用下,各组分依据露点不同的原理达到分离的目的[1]。
1.2轻烃的低温回收工艺发展方向研究分析目前在轻烃回收处理中,低温回收工艺应用的最为广泛,而低温回收工艺中的核心环节就是制冷工艺环节,这个环节对于装置的要求很高,也正因为对回收装置的要求高,导致轻烃回收装置的投资成本较高,能耗也比较大,所以在未来轻烃回收工艺发展中,回收装置的节能降耗已经成了一个重点研究的方向。
轻烃回收工艺技术及其进展

轻烃回收工艺技术及其进展轻烃是指碳数在1至4之间的烃类化合物,包括甲烷、乙烷、丙烷和丁烷等,是石油和天然气中的重要组成部分。
随着全球能源需求的增长,轻烃的开采和利用越来越受到人们的关注。
由于轻烃的挥发性和易燃性,它在生产、储运和利用过程中容易造成能源的浪费和环境污染。
轻烃的回收工艺技术及其进展成为当前研究的热点之一。
轻烃的回收工艺技术涉及到轻烃的分离、提纯和再利用等方面。
目前,主要的轻烃回收工艺技术包括吸附分离、膜分离、压缩液工艺、结晶分离和化学吸收等。
这些工艺技术在轻烃回收中发挥着重要作用,不仅可以有效提高轻烃的回收率,减少能源浪费,还可以减少对环境的污染。
吸附分离是一种通过吸附材料选择性吸附轻烃分子的工艺技术。
常用的吸附剂包括活性炭、分子筛和硅胶等。
通过合理选择吸附剂和优化操作条件,可以实现对轻烃的高效分离和回收。
膜分离则是利用特定的膜材料,通过膜的选择性透过性,将轻烃与其他组分分离开来。
与传统的蒸馏分离相比,膜分离工艺具有能耗低、设备小、操作简便等优点,因此在轻烃回收中得到了广泛的应用。
压缩液工艺利用了轻烃在高压情况下溶解度的变化,通过变化温度和压力来实现轻烃的回收。
结晶分离则是通过控制温度和添加适当的添加剂,使轻烃在溶剂中结晶析出,实现轻烃的分离和回收。
化学吸收则是利用化学反应将轻烃与其他组分转化为更容易分离的化合物,然后再对其进行分离和回收。
随着科技的进步和工艺的不断改进,轻烃回收工艺技术也在不断地发展和完善。
膜分离技术是目前发展最为迅速的轻烃回收技术之一。
传统的多孔膜已经不能满足对轻烃的高效分离要求,因此近年来,研究者们将目光转向了纳米孔膜。
纳米孔膜具有孔径小、分离效果好、通量大等优点,可以实现对轻烃的高效分离和回收。
化学吸收技术也在不断地得到改进和应用。
传统的化学吸收工艺中使用的吸收剂对环境和人体健康都存在一定的污染和危害,因此研究者们将目光转向了新型环保型吸收剂。
这些新型吸收剂具有高效、低毒、易生物降解等特点,可以实现对轻烃的高效吸收和回收,同时减少对环境的污染。
轻烃回收工艺技术及其进展

轻烃回收工艺技术及其进展轻烃是一类石油化工产品,主要包括烷烃和烯烃两大类,是石油炼制和化工生产过程中的重要中间品和原料。
随着石油的日益枯竭和环境污染问题的日益严重,轻烃回收工艺技术成为了必然的发展趋势。
为了提高轻烃的回收率和降低对环境的影响,人们也在不断地研究和改进轻烃回收工艺技术。
本文将介绍轻烃回收工艺技术及其进展。
一、轻烃回收工艺技术概述轻烃回收工艺技术是指将石油炼制和化工生产中产生的尾气中的轻烃进行回收和再利用的工艺。
轻烃主要包括乙烯、丙烯、丁烯等,这些轻烃在正常情况下会随着尾气一起排放到大气中,不仅造成能源的浪费,还会对环境造成严重污染。
采用轻烃回收工艺技术对轻烃进行回收和再利用,是一种节能减排的重要手段。
目前,常见的轻烃回收工艺技术主要包括吸附法、压缩法、凝析法、膜分离法等。
吸附法是指通过吸附剂将轻烃从尾气中吸附出来,然后再进行脱附和回收。
压缩法是指通过采用压缩机将尾气中的轻烃压缩成液体,然后进行分离和回收。
凝析法是指通过降温将尾气中的轻烃凝析成液体,然后进行分离和回收。
膜分离法是指通过膜的选择性通透性,将尾气中的轻烃和其他组分进行分离和回收。
1. 吸附法吸附法是一种成熟的轻烃回收工艺技术,其主要优势是操作简单、成本低、回收效率高。
近年来,随着吸附剂的研究不断深入,吸附法在轻烃回收领域取得了显著的进展。
目前,国内外已经开发出了一系列高性能的吸附剂,其吸附速度和吸附容量均得到了显著提高。
结构优化和表面处理等技术的应用,使得吸附剂的选择性和循环利用率得到了显著提高。
吸附法在轻烃回收工艺技术中的应用前景十分广阔。
2. 压缩法压缩法是一种传统的轻烃回收工艺技术,其主要优势是操作稳定、回收效率高。
在近年来,人们在研究压缩机和分离设备的还不断地优化压缩法的操作参数和工艺流程,使得压缩法的回收效率和能耗得到了显著提高。
随着压缩机和分离设备的智能化和自动化程度的不断提高,压缩法在轻烃回收领域的应用前景也将更加广阔。
天然气轻烃回收工艺发展的探讨
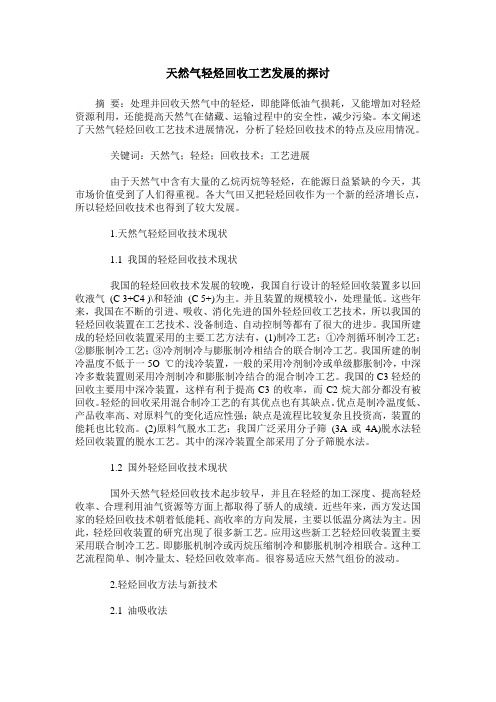
天然气轻烃回收工艺发展的探讨摘要:处理并回收天然气中的轻烃,即能降低油气损耗,又能增加对轻烃资源利用,还能提高天然气在储藏、运输过程中的安全性,减少污染。
本文阐述了天然气轻烃回收工艺技术进展情况,分析了轻烃回收技术的特点及应用情况。
关键词:天然气;轻烃;回收技术;工艺进展由于天然气中含有大量的乙烷丙烷等轻烃,在能源日益紧缺的今天,其市场价值受到了人们得重视。
各大气田又把轻烃回收作为一个新的经济增长点,所以轻烃回收技术也得到了较大发展。
1.天然气轻烃回收技术现状1.1 我国的轻烃回收技术现状我国的轻烃回收技术发展的较晚,我国自行设计的轻烃回收装置多以回收液气(C 3+C4 )\和轻油(C 5+)为主。
并且装置的规模较小,处理量低。
这些年来,我国在不断的引进、吸收、消化先进的国外轻烃回收工艺技术,所以我国的轻烃回收装置在工艺技术、没备制造、自动控制等都有了很大的进步。
我国所建成的轻烃回收装置采用的主要工艺方法有,(1)制冷工艺:①冷剂循环制冷工艺;②膨胀制冷工艺;③冷剂制冷与膨胀制冷相结合的联合制冷工艺。
我国所建的制冷温度不低于一5O ℃的浅冷装置,一般的采用冷剂制冷或单级膨胀制冷,中深冷多数装置则采用冷剂制冷和膨胀制冷结合的混合制冷工艺。
我国的C3轻烃的回收主要用中深冷装置,这样有利于提高C3的收率,而C2烷大部分都没有被回收。
轻烃的回收采用混合制冷工艺的有其优点也有其缺点。
优点是制冷温度低、产品收率高、对原料气的变化适应性强;缺点是流程比较复杂且投资高,装置的能耗也比较高。
(2)原料气脱水工艺:我国广泛采用分子筛(3A或4A)脱水法轻烃回收装置的脱水工艺。
其中的深冷装置全部采用了分子筛脱水法。
1.2 国外轻烃回收技术现状国外天然气轻烃回收技术起步较早,并且在轻烃的加工深度、提高轻烃收率、合理利用油气资源等方面上都取得了骄人的成绩。
近些年来,西方发达国家的轻烃回收技术朝着低能耗、高收率的方向发展,主要以低温分离法为主。
轻烃回收工艺技术及其进展

轻烃回收工艺技术及其进展1. 引言1.1 轻烃回收工艺技术的重要性轻烃是一种重要的化工原料,包括一系列碳数在1~4之间的烃类物质,如甲烷、乙烷、乙烯等。
轻烃在石油、天然气开采和化工生产中得到广泛应用,是许多化工产品的重要组成部分。
轻烃回收工艺技术的重要性主要体现在以下几个方面:轻烃是一种宝贵的资源,资源的再利用是推动可持续发展的重要途径。
随着我国经济的快速发展和化工产业的不断壮大,对轻烃的需求量逐渐增加。
有效回收和利用轻烃资源,不仅可以降低生产成本,提高资源利用效率,还可以减少对环境的污染,符合现代工业发展的可持续性原则。
轻烃作为化工原料,具有广泛的应用前景。
乙烯、丙烯等轻烃是合成许多重要化工产品的原料,如塑料、合成橡胶等。
轻烃回收工艺技术的发展和应用,对促进我国化工产业的创新与发展具有重要意义。
轻烃在石油、天然气加工中的回收利用,还可以提高能源利用效率,减少能源浪费,有利于能源资源的节约和清洁能源的发展。
研究和推广轻烃回收工艺技术,对于我国的能源战略和资源安全具有重要意义。
1.2 研究现状及意义当前,轻烃是石化工业中一类重要的原料,包括乙烯、丙烯、丁烷等,广泛应用于石油化工、合成橡胶、胶粘剂等行业。
轻烃在生产和运输过程中往往会发生泄露和挥发,不仅造成资源浪费,还对环境和人体健康造成危害。
研究和发展轻烃回收工艺技术具有重要意义。
目前,我国的轻烃回收工艺技术主要集中在传统的吸附、吸附-脱附、凝聚等方法上,这些方法在一定程度上可以实现轻烃的回收,但存在能耗高、设备大、操作复杂等缺点。
随着工业生产的不断发展和对环保要求的提高,对轻烃回收工艺技术的要求也日益增加,迫切需要研究新型的、高效节能的轻烃回收工艺技术。
通过研究和探索新型的轻烃回收工艺技术,可以提高轻烃回收率,降低能耗,减少对环境的污染,实现资源的可持续利用。
深入研究轻烃回收工艺技术,不仅有助于推动我国石化工业的发展,也有利于促进绿色环保产业的发展,具有重要的现实意义和深远的影响。
轻烃回收工艺的发展方向及新技术探讨

第21卷第2期2003年6月天 然 气 与 石 油Natural Gas And OilVol.21,No.2Jun.2003收稿日期:2002-09-04;修回日期:2002-09-12 作者简介:王 健(1964-),女,四川自贡市人,工程师,学士,1985年毕业于成都科技大学化学工程专业,从事油气加工设计及管理工作。
电话:(028)86014414。
文章编号:1006-5539(2003)02-0020-03轻烃回收工艺的发展方向及新技术探讨王 健(中国石油集团工程设计有限责任公司西南分公司,四川成都610017)摘 要:低温分离技术的发展,推动和促进了轻烃回收工艺的进步。
但总体来说能耗高、收率低仍然是制约轻烃回收工艺发展的重要因素。
近年来对轻烃回收工艺的研究也主要是围绕这两方面开展,同时开发利用了一些新技术和新工艺。
关键词:轻烃回收;能耗;收率;新工艺中图分类号:T E868 文献标识码:C1 引言为满足天然气长输管线的烃露点要求,回收天然气中很有价值的乙烷/丙烷,近年来气田轻烃回收作为各气田新的经济增长点,越来越受到人们重视,轻烃回收工艺也得到了较大发展。
在众多的轻烃回收方法中,低温回收工艺是当前主要采用的方法,深冷分离技术的发展,推动和促进了轻烃回收工艺的进步,并得到更为广泛的应用[1]。
2 低温回收工艺的研究发展方向低温回收工艺过程中最主要、最关键的步骤就是制冷工艺。
它直接影响装置的投资、能耗和回收率三大经济指标。
工业上采用的制冷方法大致有:节流制冷、膨胀机制冷、热分离机制冷、外冷源制冷和复合制冷。
目前对制冷工艺的研究紧紧围绕节能降耗和提高轻烃回收率两方面开展。
2 1 节能降耗现有轻烃回收装置大多能耗较高,制冷效率较低,因此节能降耗一直是轻烃回收技术中的一个重要研究课题。
节能的途径只有两种:一种是考虑单个设备如膨胀机或压缩机的能耗,合理选择设备型号;另一种就是从优化制冷方案着手,从可以采用的多种方法中筛选出最佳制冷方案,达到最佳的节能效果和经济效益。
轻烃回收工艺技术及其进展
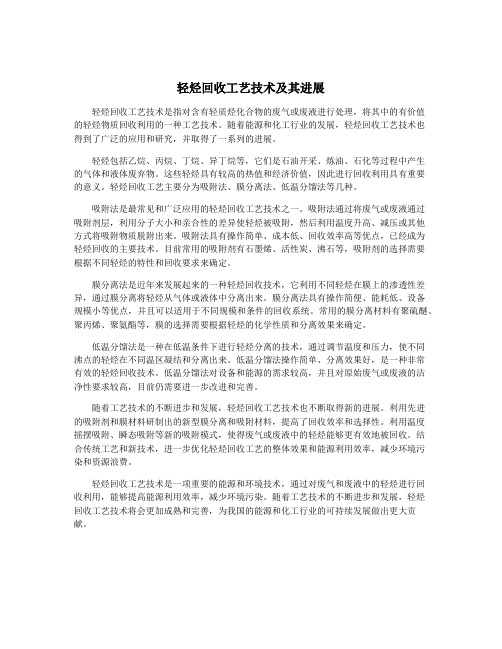
轻烃回收工艺技术及其进展轻烃回收工艺技术是指对含有轻质烃化合物的废气或废液进行处理,将其中的有价值的轻烃物质回收利用的一种工艺技术。
随着能源和化工行业的发展,轻烃回收工艺技术也得到了广泛的应用和研究,并取得了一系列的进展。
轻烃包括乙烷、丙烷、丁烷、异丁烷等,它们是石油开采、炼油、石化等过程中产生的气体和液体废弃物。
这些轻烃具有较高的热值和经济价值,因此进行回收利用具有重要的意义。
轻烃回收工艺主要分为吸附法、膜分离法、低温分馏法等几种。
吸附法是最常见和广泛应用的轻烃回收工艺技术之一。
吸附法通过将废气或废液通过吸附剂层,利用分子大小和亲合性的差异使轻烃被吸附,然后利用温度升高、减压或其他方式将吸附物质脱附出来。
吸附法具有操作简单、成本低、回收效率高等优点,已经成为轻烃回收的主要技术。
目前常用的吸附剂有石墨烯、活性炭、沸石等,吸附剂的选择需要根据不同轻烃的特性和回收要求来确定。
膜分离法是近年来发展起来的一种轻烃回收技术,它利用不同轻烃在膜上的渗透性差异,通过膜分离将轻烃从气体或液体中分离出来。
膜分离法具有操作简便、能耗低、设备规模小等优点,并且可以适用于不同规模和条件的回收系统。
常用的膜分离材料有聚硫醚、聚丙烯、聚氨酯等,膜的选择需要根据轻烃的化学性质和分离效果来确定。
低温分馏法是一种在低温条件下进行轻烃分离的技术,通过调节温度和压力,使不同沸点的轻烃在不同温区凝结和分离出来。
低温分馏法操作简单、分离效果好,是一种非常有效的轻烃回收技术。
低温分馏法对设备和能源的需求较高,并且对原始废气或废液的洁净性要求较高,目前仍需要进一步改进和完善。
随着工艺技术的不断进步和发展,轻烃回收工艺技术也不断取得新的进展。
利用先进的吸附剂和膜材料研制出的新型膜分离和吸附材料,提高了回收效率和选择性。
利用温度摇摆吸附、瞬态吸附等新的吸附模式,使得废气或废液中的轻烃能够更有效地被回收。
结合传统工艺和新技术,进一步优化轻烃回收工艺的整体效果和能源利用效率,减少环境污染和资源浪费。
- 1、下载文档前请自行甄别文档内容的完整性,平台不提供额外的编辑、内容补充、找答案等附加服务。
- 2、"仅部分预览"的文档,不可在线预览部分如存在完整性等问题,可反馈申请退款(可完整预览的文档不适用该条件!)。
- 3、如文档侵犯您的权益,请联系客服反馈,我们会尽快为您处理(人工客服工作时间:9:00-18:30)。
轻烃回收工艺技术及其进展
轻烃是指石油提炼或天然气加工过程中产生的低碳烷烃类化合物,包括乙烷、丙烷、
丁烷等。
由于轻烃具有高热值、易燃、易挥发以及广泛的应用价值,因此对于轻烃的回收
工艺技术的研究具有重要意义。
本文将介绍目前常用的轻烃回收工艺技术以及其进展。
轻烃回收工艺技术主要包括吸附分离、膜分离、蒸馏分离和冷凝分离等。
吸附分离是
一种通过固体吸附剂将轻烃从混合气中吸附出来的技术,常用的吸附剂包括活性炭、分子
筛等。
膜分离是利用半透膜的分离性能将轻烃分离出来的技术,常用的膜材料包括聚酯膜、聚丙烯膜等。
蒸馏分离是根据轻烃在不同温度下的沸点差异进行分离的技术,常用的蒸馏
设备包括塔式蒸馏塔、萃取塔等。
冷凝分离是通过降低轻烃的温度使其从气态转化为液态
从而实现分离的技术,常用的冷凝设备包括冷凝器、冷冻器等。
在膜分离技术中,聚酯膜是一种常用的膜材料,其具有良好的选择性和透过率,能够
实现对轻烃的高效分离。
为了提高聚酯膜的分离性能,研究人员通过改变共聚合物的比例、添加增渗剂等手段对膜材料进行改性。
聚丙烯膜也被广泛研究,其具有较高的烷烃选择性
和较低的分离性能损失,因此具有良好的应用潜力。
在蒸馏分离技术中,塔式蒸馏塔是最常用的分离设备之一,其通过控制不同温度层的
塔体来实现轻烃的分馏。
为了提高对轻烃的分离效果,研究人员通过改变塔体结构、优化
操作参数等手段对蒸馏设备进行改进。
萃取塔也是一种常用的蒸馏设备,其通过溶剂的加
入来实现对轻烃的选择性提取。
冷凝分离技术主要包括冷凝器和冷冻器两种方式。
冷凝器通过将轻烃的温度降低到其
饱和蒸汽压以下,使其从气态转化为液态从而实现分离。
冷冻器则通过降低轻烃的温度至
其凝点以下,使其凝结成冷凝液从而实现分离。
为了提高冷凝分离的效果,研究人员通过
改变冷却剂的流动方式、提高冷却剂的温度差等手段对冷凝设备进行改进。
轻烃回收工艺技术的研究不断取得进展,吸附分离、膜分离、蒸馏分离和冷凝分离等
技术不断被改进和创新,以满足不同场景和需求下的轻烃回收。
随着科学技术的不断发展,相信轻烃回收工艺技术将进一步提高其分离效率和经济性,并在能源和化工领域发挥更大
的作用。