空心传动轴优化设计
基于机械动力学的传动轴系统优化设计
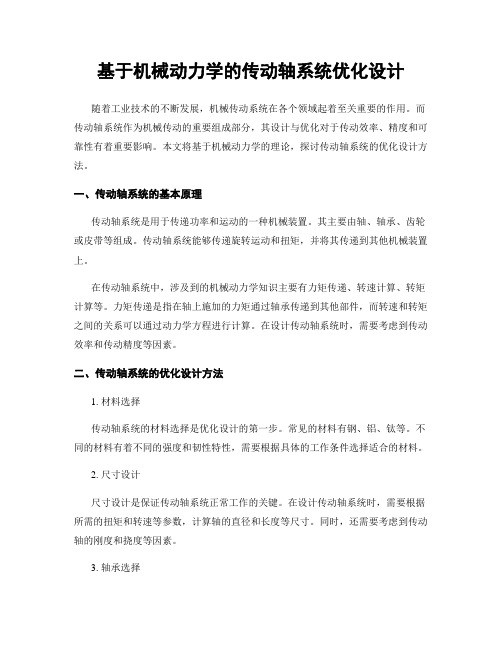
基于机械动力学的传动轴系统优化设计随着工业技术的不断发展,机械传动系统在各个领域起着至关重要的作用。
而传动轴系统作为机械传动的重要组成部分,其设计与优化对于传动效率、精度和可靠性有着重要影响。
本文将基于机械动力学的理论,探讨传动轴系统的优化设计方法。
一、传动轴系统的基本原理传动轴系统是用于传递功率和运动的一种机械装置。
其主要由轴、轴承、齿轮或皮带等组成。
传动轴系统能够传递旋转运动和扭矩,并将其传递到其他机械装置上。
在传动轴系统中,涉及到的机械动力学知识主要有力矩传递、转速计算、转矩计算等。
力矩传递是指在轴上施加的力矩通过轴承传递到其他部件,而转速和转矩之间的关系可以通过动力学方程进行计算。
在设计传动轴系统时,需要考虑到传动效率和传动精度等因素。
二、传动轴系统的优化设计方法1. 材料选择传动轴系统的材料选择是优化设计的第一步。
常见的材料有钢、铝、钛等。
不同的材料有着不同的强度和韧性特性,需要根据具体的工作条件选择适合的材料。
2. 尺寸设计尺寸设计是保证传动轴系统正常工作的关键。
在设计传动轴系统时,需要根据所需的扭矩和转速等参数,计算轴的直径和长度等尺寸。
同时,还需要考虑到传动轴的刚度和挠度等因素。
3. 轴承选择轴承在传动轴系统中起着支撑和导向作用。
在优化设计中,需要选择合适的轴承类型、尺寸和材料等。
同时,还需要进行轴承的润滑和密封等设计,以保证传动轴系统的正常工作。
4. 传动方式选择传动轴系统的传动方式有多种,如齿轮传动、皮带传动等。
在进行优化设计时,需要根据实际应用需求选择合适的传动方式。
不同的传动方式有着不同的传动效率和精度,需要根据具体情况进行选择。
5. 动力学要求在进行传动轴系统的优化设计时,需要根据具体应用要求考虑动力学要求。
比如,传动轴系统在高速运转时需要考虑离心力对轴的影响,同时还需要考虑传动带来的振动等。
三、案例分析为了更好地理解基于机械动力学的传动轴系统优化设计,我们以某机械设备的传动轴系统设计为例进行分析。
某型号空心传动轴的优化设计.doc
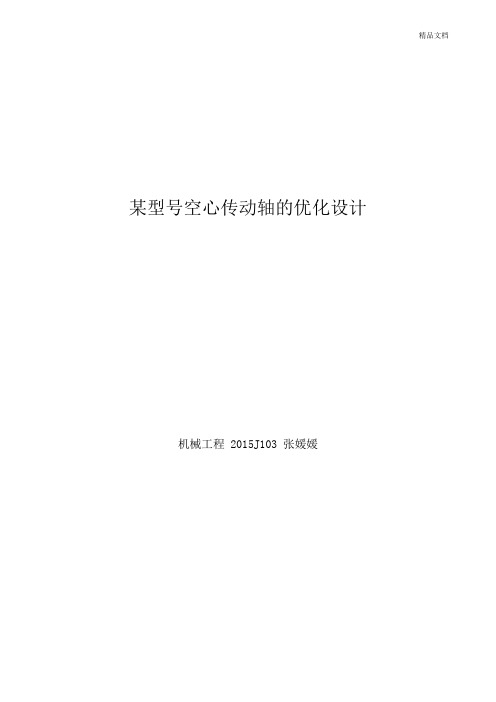
某型号空心传动轴的优化设计机械工程 2015J103 张媛媛欲设计如图1-1所示的某型号空心传动轴 ,其中D 和d 分别为空心轴的外径和内径 ,轴长L=4m 。
轴的材料密度ρ=7.8×10³kg/m ³ ,剪切弹性模量G=80GPa ,许用剪切成功[r]=40MPa ,单位长度许用扭转角[Ø]=1°/m ,轴索传递的功率P=5.5kW ,转速n=200r/min 。
在满足许用条件和结构尺寸限制条件的前提下对该空心轴进行优化 ,使该轴的质量最小。
一、确定工作变量图1-1所示传动轴的力学模型是一个受扭转的圆柱桶轴。
其外径D 和内径d 是决定圆轴的重要独立参数 ,故可作为设计变量 ,将其写成向量形式:X=[x 1 ,x 2 ]T =[D,d]T (1-1)二、简历目标函数若取质量最小为优化目标 ,则目标函数空心圆轴的质量可按下式计算: M=4πρL (D ²-d ²)(kg ) (1-2) L可见 ,这是一个合理选择D 和d 而使质量M 最小的优化问题。
注意:再设计时要确定目标变量的单位。
在确定目标函数和约束条件时 ,应保持它们单位的一致 ,即D 、L 的单位为毫米(mm ) ,质量M 的单位为千克(kg )。
三、上述设计应满足的使用条件和结构尺寸限制如下:(1)扭转强度、根据扭转强度 ,要求扭转剪应力需满足τmax =tW T ≤[τ] (1-3) 式中 ,T 为圆轴所受扭转 ,T=n 9549P (N •m );W t 为抗扭截面模量 ,W t=D D 16d -44)π((MPa)。
(2)扭转刚度 ,为了确保传动轴正常工作 ,除满足扭转强度条件外 ,还要限制轴的变形 ,限制即为刚度条件 ,通常要求单位长度的最大扭转度扭转角不超过规定的许用值 ,即Ø=pGI T ≤[Ø] (1-4) 式中 ,Ø为单位长度扭转角(rad );G 为剪切模量(MPa);I p 为极惯性矩(m 4)。
空心传动轴非概率可靠性优化设计
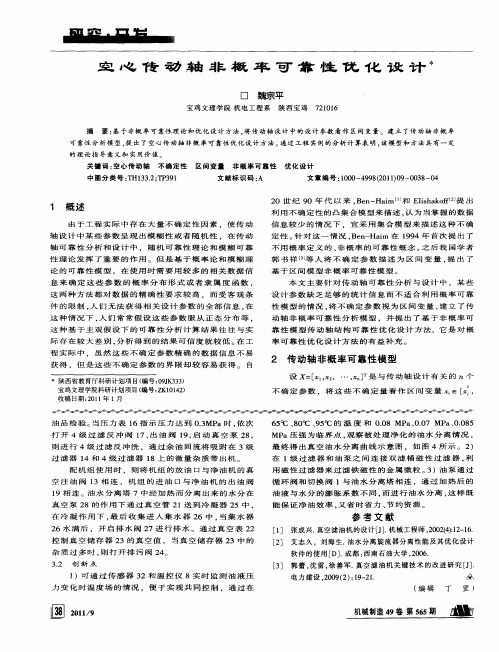
控 制 真 空 储 存 器 2 的 真 空 值 , 当 真 空 储 存 器 2 中 的 3 3
杂 质 过多 时 , 打 开排 污 阀 2 。 则 4
3. 2 创 新 点
1 )可 通 过 传 感 器 3 2和 温 控 仪 8实 时 监 测 油 液 压
可靠性分析模 型, 出了空心传动轴非概 率可靠性优化设计 方法。 提 通过工程 实例的分析计算表明 , 该模型和方法具有一定
的理 论 指 导意 义和 实 用价 值 。
关键词 : 心传动轴 空
不确 定 性
区 间变 量
非概率可靠性
优 化 设计
中 图分 类号 :H132T 3 1 T 3 .;P 9
力 变 化 时 温 度 场 的 情 况 ,便 于 实 现 共 同 控 制 。通 过 在
( 辑 丁 罡 ) 编
21 / 0 19
] 、 分别是区间变量的上界和下界) ( : 。令 :
对 传 动 轴 来 说 , 忽 略 弯 矩 的 影 响 , 动 轴 主 要 承 若 传
受 扭 矩 的 作 用 , 其 承 受 的 扭 矩 为 则 其 横 截 面 上 的 设 扭 转 剪 应 力 和 传 动 轴 的 扭 转 变 形 I分 别 为 : S ]
息 来 确 定 这 些 参数 的概 率 分 布 形 式或 者 隶 属 度 函数 , 这 两 种 方 法 都 对 数 据 的 精 确 性 要 求 较 高 ,而 受 客 观 条 件 的 限 制 , 们 无 法 获 得 相 关 设 计 参 数 的全 部 信 息 , 人 在
这 种 情况 下 , 们 常 常假 设 这些 参 数服 从正 态 分 布等 , 人 这 种 基 于 主 观 假 设 下 的 可 靠 性 分 析 计 算 结 果 往 往 与 实
基于matlab煤液钻空心传动轴的优化设计
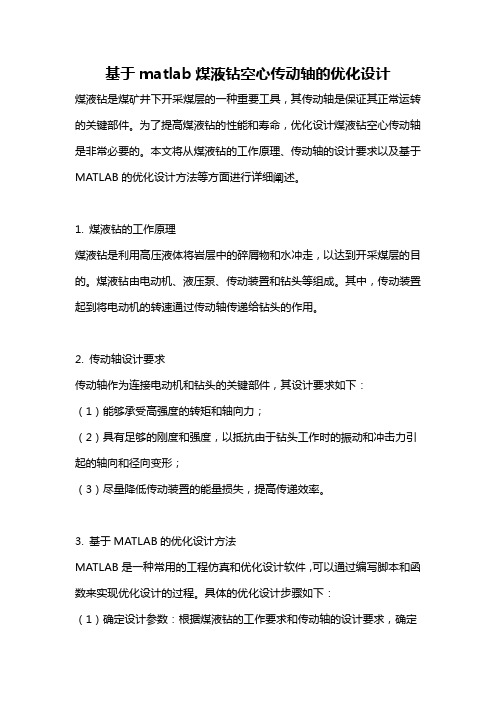
基于matlab煤液钻空心传动轴的优化设计煤液钻是煤矿井下开采煤层的一种重要工具,其传动轴是保证其正常运转的关键部件。
为了提高煤液钻的性能和寿命,优化设计煤液钻空心传动轴是非常必要的。
本文将从煤液钻的工作原理、传动轴的设计要求以及基于MATLAB的优化设计方法等方面进行详细阐述。
1. 煤液钻的工作原理煤液钻是利用高压液体将岩层中的碎屑物和水冲走,以达到开采煤层的目的。
煤液钻由电动机、液压泵、传动装置和钻头等组成。
其中,传动装置起到将电动机的转速通过传动轴传递给钻头的作用。
2. 传动轴设计要求传动轴作为连接电动机和钻头的关键部件,其设计要求如下:(1)能够承受高强度的转矩和轴向力;(2)具有足够的刚度和强度,以抵抗由于钻头工作时的振动和冲击力引起的轴向和径向变形;(3)尽量降低传动装置的能量损失,提高传递效率。
3. 基于MATLAB的优化设计方法MATLAB是一种常用的工程仿真和优化设计软件,可以通过编写脚本和函数来实现优化设计的过程。
具体的优化设计步骤如下:(1)确定设计参数:根据煤液钻的工作要求和传动轴的设计要求,确定设计参数,如轴的直径、材料、长度等。
(2)建立传动轴的有限元模型:根据设计参数和传动轴的几何形状,利用MATLAB中的有限元分析工具建立传动轴的有限元模型。
(3)应用约束条件和目标函数:根据传动轴的设计要求,将约束条件和目标函数转化为MATLAB中的数学表达式。
(4)选择优化算法:根据设计问题的特点和求解要求,选择合适的优化算法,如遗传算法、粒子群算法等。
(5)进行优化设计:利用MATLAB中的优化工具箱,结合选择的优化算法,对传动轴的设计参数进行优化求解,得到最优设计方案。
(6)评估设计方案:根据优化结果,对传动轴的性能和寿命进行评估,如果不满足要求,则返回第(3)步重新进行设计。
(7)制造和测试:根据最优设计方案,制造传动轴,并通过实验测试验证其性能和寿命。
通过以上步骤,我们可以利用MATLAB对煤液钻空心传动轴进行优化设计,提高煤液钻的工作效率和寿命。
空间万向传动当量夹角的计算和优化设计

空间万向传动当量夹角的计算和优化设计田中旭;祁平;高学峰【摘要】传动轴当量夹角是衡量含多万向节传动轴传动性能的重要指标,它的准确计算对传动轴的设计具有重要的意义.当传动轴空间布置时,当量夹角的准确计算变得困难.研究了空间当量夹角的精确计算方法,主要包括:给定了更加准确的万向节叉方位的描述模型、推导了精确的万向节叉初相位和传动轴夹角计算的数学模型;论文通过解析方法和算例,研究了当量夹角计算过程中产生误差的根本原因;还通过多体动力学软件ADAMS的运动学仿真对数学模型和算法进行了验证.基于当量夹角准确计算模型的基础上,对某商用车传动轴当量夹角进行了优化布置,使得当量夹角有了大幅度减小.【期刊名称】《机械设计与制造》【年(卷),期】2018(000)009【总页数】3页(P48-50)【关键词】传动轴当量夹角;万向节初相位;传动轴布置优化;传动轴运动学仿真【作者】田中旭;祁平;高学峰【作者单位】上海海洋大学工程学院,上海 201306;中国北方发动机研究所,山西大同 037036;蒂森克虏伯汽车系统计算有限公司,上海 201201【正文语种】中文【中图分类】TH161 引言十字轴万向节因其可靠性高,成本低廉,仍得到了广泛的应用。
当前,含万向节的传动轴在运动学[1]与强度[2]方面仍然存在很多值得研究的问题,这些问题的关键点在于万向节两侧的传动轴存在一定夹角。
在含多万向节的传动轴中,综合评价传动轴布置的参数就是当量夹角[3]。
在万向节传动当量夹角不为零时,传动轴的转速将产生波动[4-5],同时还在传动轴上产生波动附加弯矩作用[6]。
转速的波动会引起传动系统的齿轮啮合冲击和噪声,影响其可靠性;附加弯矩则会引起传动轴中间支撑的振动,会进一步引起设备或车辆的振动和噪声[7],同时也易引起传动轴本身的弯曲振动。
因此,传动轴当量夹角的设计和控制,是传动轴布置中最为重要的指标之一[8]。
而当量夹角的准确计算则是传动轴设计和优化的前提和基础。
空心轴的动态特性分析与优化设计

空心轴的动态特性分析与优化设计空心轴是一种轴类零件,具有较小的重量和惯性矩,广泛应用于机械和工程设计中。
它的独特结构使得其动态特性受到一系列因素的影响,包括材料选择、几何形状以及制造工艺等。
本文将从多个角度对空心轴的动态特性进行分析与优化设计。
首先,材料选择是影响空心轴动态特性的重要因素之一。
常见的轴材料包括碳素钢、合金钢和铝合金等。
碳素钢具有优良的机械性能和较高的抗腐蚀能力,适用于一般工程应用。
合金钢由于添加了合适的合金元素,具有更高的强度和硬度,适用于承受较大载荷的工作条件。
铝合金轴由于其较低的密度和耐腐蚀性能,适用于体积和质量要求较小的应用场景。
因此,在设计空心轴时,应根据具体的工作条件选择合适的材料,以达到最佳的动态特性。
其次,空心轴的几何形状也对其动态特性有重要影响。
一般而言,较大的直径和较小的长度可以提高空心轴的刚度和抗弯强度。
此外,几何形状的对称性对空心轴的动态特性也有一定影响。
如果轴的几何形状不对称,可能会导致轴在运动中产生不平衡力矩,从而影响工作效率和稳定性。
因此,在设计空心轴时,应尽量保持几何形状的对称性,以确保良好的动态特性。
除了材料选择和几何形状,制造工艺也是影响空心轴动态特性的重要因素之一。
例如,热处理可以通过改变材料的晶体结构和硬度来提高轴的强度和耐用性。
此外,精密加工和表面处理可以改善轴的表面光洁度和尺寸精度,从而减小摩擦阻力和振动噪声。
因此,在制造空心轴时,应选择适当的制造工艺,以提高其动态特性。
针对以上因素,空心轴的优化设计可以从多个方面入手。
首先,可以通过材料选择和几何形状的优化来改善轴的刚度和抗弯能力。
例如,可以选择高强度的合金钢材料,并根据实际工作条件调整轴的直径和长度。
其次,可以通过精密制造和表面处理来提高轴的表面质量和尺寸精度。
例如,可以采用CNC加工和研磨工艺,以确保轴的精度和光洁度。
最后,可以借助计算机辅助设计和模拟分析工具对轴的动态特性进行模拟和优化。
空心轴优化设计

l ≥ lmin d ≥0
轴的体积达到最小化,本文取空心轴长度 l 为设计变量。综
D−d ≥0
合上述分析可得优化数学模型为:
■■1.4 小节
X = (x1, x2, x3)T = (D, d ,l)T 综分析上述模型可知,该模型具有 3 个设计变量,5 个
主要分析和阐述了空心传动轴的设计要求、优化设计的 约束条件以及相关数学模型,整理可以得到以下优化设计数
最后得到的结果如下:
空心传动轴的设计既需要传统的设计理念同时需要新的
X = (x1, x2, x3)T = (D, d ,l)T = (178.0648,177.0523 3001.7751)T 最后圆整后的结果为: X = (x1, x2, x3)T = (D, d ,l)T = (179,177,3002)T
运行结果: * * * 空心传动轴实现函数优化设计最优解 * * *
通过优化设计算法计算之后得到的结果一般情况下并
空心传动轴外径 D=178.0648 mm
不是整数,即都是小数,但是该空心传动轴的设计参数一
空心传动轴内径 d=177.0523 mm
般规范为整数,即需要对优化设计到的参数进行圆整处
空心传动轴长度 l=3001.7751 mm
E=2*10^5; tao=60; g(1)=(x(2))^4-(x(1)); g(2)=(16*M*x(1))/(pi*((x(1))^4-(x(2))^4)*0.7*E)((x(1)-x(2))/x(1))^(3/2); ceq=[];
2 相关参数的处理
理。当然在进行数据圆整处理时需要注意顾及目标函数和
空心传动轴设计体积 v=0.0008 m^3
约束条件,有可能在进行圆整处理之后就不再满足约束条件
基于响应面法的转向驱动桥空心半轴轻量化优化设计

基于响应面法的转向驱动桥空心半轴轻量化优化设计汪朝晖;朱发渊;吕密;陈思【摘要】提出了一种基于数值优化与有限元模拟相结合的汽车转向驱动桥空心半轴轻量化设计方法.以半轴各段的壁厚、长度和过渡角为设计变量,半轴质量最小化为优化目标,2阶约束模态频率和半轴花键末端圆角过渡处等效应力为约束条件,建立了半轴轻量优化模型.利用正交试验设计得到10个设计变量和3个水平的数值模拟试验组合.采用最小二乘法建立了响应面近似模型,并利用序列二次规划算法对模型进行了迭代优化.结果表明:轻量化优化后的变径全空心半轴质量比初始设计减少约16.7g,半轴2阶约束模态频率增加约0.6Hz,且半轴花键末端圆角过渡处和最小轴径处的等效应力值均低于半轴材料的抗扭强度.【期刊名称】《汽车工程》【年(卷),期】2015(037)012【总页数】6页(P1477-1481,1476)【关键词】空心半轴;轻量化设计;正交试验设计;最小二乘法;响应面模型【作者】汪朝晖;朱发渊;吕密;陈思【作者单位】武汉科技大学机械自动化学院,武汉430081;武汉科技大学机械自动化学院,武汉430081;重庆建设工业(集团)有限责任公司,重庆400054;武汉科技大学机械自动化学院,武汉430081【正文语种】中文汽车轻量化设计是节约能源消耗的重要途径,研究表明:汽车运动部件质量每减轻1%,则可节油2%[1]。
转向驱动桥半轴是汽车最重要的运动零部件之一,它对汽车的驱动性能和运行稳定性有重要影响。
传统的转向驱动桥半轴结构轻量化优化设计主要是依据工程经验,其试验研究难度较大,设计周期冗长。
因此,采用新的轻量化优化方法设计转向驱动桥半轴势在必行。
国内外诸多学者在保证汽车传动轴工作可靠的基础上引入材料低载强化特性获取新型传动轴结构,取得了较好效果。
文献[2]中以材料40Cr的低载强化特性为依据,设计出空心传动轴,并对轻量化的传动轴进行强度校核及模态对比分析,验证了设计可行性;文献[3]中在传动轴结构优化过程中,以最佳累积强化效果为目标,根据设计应力分布区间与结构低载强化特性区间的对应关系获取了结构尺寸参数,验证了结构轻量化设计的有效性。