冶金过程动力学
冶金过程动力学导论

冶金过程动力学导论
冶金过程动力学是一门研究冶金过程中反应动力学规律与机理的学科,它涉及多种领域,包括物理化学、材料科学、热力学等。
冶金过程动力学主要关注的是控制金属在冶炼过程中的变化过程,从而实现冶炼过程的优化和控制。
在冶金过程中,反应动力学起着至关重要的作用。
反应动力学研究的是反应速率和反应机理,以及反应条件对反应速率和反应机理的影响。
反应速率是指单位时间内反应物浓度变化的速率,其大小决定了反应的快慢。
而反应机理则是指反应过程中各个步骤和反应产物的形成路径,了解反应机理和速率对于冶金工艺优化和炉料控制极为重要。
常见的冶金过程动力学反应包括金属与非金属元素的化学反应、金属之间的化学反应、固态反应以及气相反应等。
在冶金过程中,重要的反应有铁矿石还原、碳酸钙分解、焦炭氧化等。
掌握这些反应的动力学规律,对于调节炉料组分、掌握反应动力学规律都有着极为重要的意义。
综上所述,冶金过程动力学的研究可以为冶金工艺提供基础支撑和科学指导。
冶金过程的优化和控制,离不开对反应动力学规律和机理的深入研究。
钢铁冶金过程中的反应动力学研究
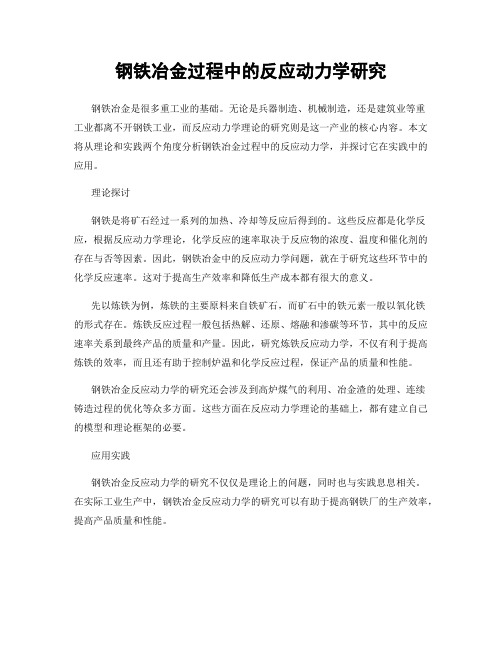
钢铁冶金过程中的反应动力学研究钢铁冶金是很多重工业的基础。
无论是兵器制造、机械制造,还是建筑业等重工业都离不开钢铁工业,而反应动力学理论的研究则是这一产业的核心内容。
本文将从理论和实践两个角度分析钢铁冶金过程中的反应动力学,并探讨它在实践中的应用。
理论探讨钢铁是将矿石经过一系列的加热、冷却等反应后得到的。
这些反应都是化学反应,根据反应动力学理论,化学反应的速率取决于反应物的浓度、温度和催化剂的存在与否等因素。
因此,钢铁冶金中的反应动力学问题,就在于研究这些环节中的化学反应速率。
这对于提高生产效率和降低生产成本都有很大的意义。
先以炼铁为例,炼铁的主要原料来自铁矿石,而矿石中的铁元素一般以氧化铁的形式存在。
炼铁反应过程一般包括热解、还原、熔融和渗碳等环节,其中的反应速率关系到最终产品的质量和产量。
因此,研究炼铁反应动力学,不仅有利于提高炼铁的效率,而且还有助于控制炉温和化学反应过程,保证产品的质量和性能。
钢铁冶金反应动力学的研究还会涉及到高炉煤气的利用、冶金渣的处理、连续铸造过程的优化等众多方面。
这些方面在反应动力学理论的基础上,都有建立自己的模型和理论框架的必要。
应用实践钢铁冶金反应动力学的研究不仅仅是理论上的问题,同时也与实践息息相关。
在实际工业生产中,钢铁冶金反应动力学的研究可以有助于提高钢铁厂的生产效率,提高产品质量和性能。
例如,在钢铁冶金过程中,大量煤气会产生,这些煤气中含有很多高能物质,包括一氧化碳、甲烷等。
通过对反应动力学的研究,我们可以了解这些高能物质对其它反应过程的影响,进而优化工艺,从而实现超高炉煤气的高效利用,节约资源。
另外,钢铁铸造过程也是反应动力学的实践应用之一。
具体来说,连铸是钢铁厂最重要的生产环节之一。
研究熔体的凝固过程,对于提高钢铁的成品率、规格精度,以及钢铁结晶器的设计优化等,都有着至关重要的作用。
钢铁冶金反应动力学的研究,对于提高钢铁质量、提高生产效率,以及降低成本都有着重要的作用。
冶金原理 课后题答案
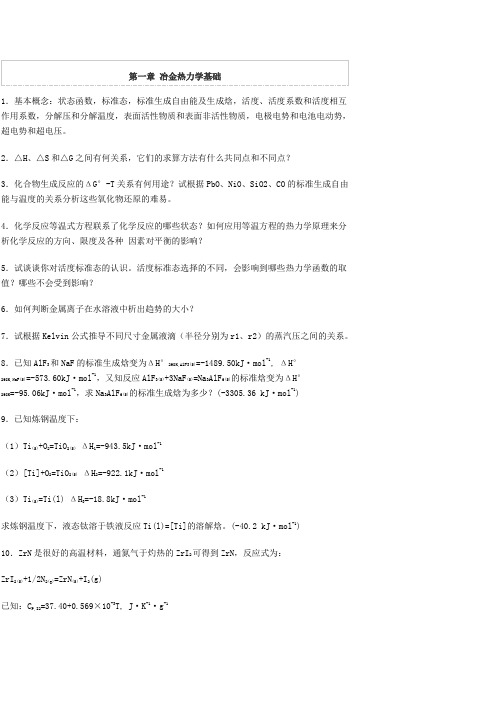
第一章 冶金热力学基础1.基本概念:状态函数,标准态,标准生成自由能及生成焓,活度、活度系数和活度相互作用系数,分解压和分解温度,表面活性物质和表面非活性物质,电极电势和电池电动势,超电势和超电压。
2.△H 、△S 和△G 之间有何关系,它们的求算方法有什么共同点和不同点?3.化合物生成反应的ΔG °-T 关系有何用途?试根据PbO 、NiO 、SiO2、CO 的标准生成自由能与温度的关系分析这些氧化物还原的难易。
4.化学反应等温式方程联系了化学反应的哪些状态?如何应用等温方程的热力学原理来分析化学反应的方向、限度及各种 因素对平衡的影响?5.试谈谈你对活度标准态的认识。
活度标准态选择的不同,会影响到哪些热力学函数的取值?哪些不会受到影响?6.如何判断金属离子在水溶液中析出趋势的大小?7.试根据Kelvin 公式推导不同尺寸金属液滴(半径分别为r1、r2)的蒸汽压之间的关系。
8.已知AlF 3和NaF 的标准生成焓变为ΔH °298K,AlF3(S)=-1489.50kJ ·mol -1, ΔH °298K,NaF(S)=-573.60kJ ·mol -1,又知反应AlF 3(S)+3NaF (S)=Na 3AlF 6(S)的标准焓变为ΔH °298K=-95.06kJ ·mol -1,求Na 3AlF 6(S)的标准生成焓为多少?(-3305.36 kJ ·mol -1)9.已知炼钢温度下:(1)Ti (S)+O 2=TiO 2(S) ΔH 1=-943.5kJ ·mol -1(2)[Ti]+O 2=TiO 2(S) ΔH 2=-922.1kJ ·mol -1 (3)Ti (S)=Ti(l) ΔH 3=-18.8kJ ·mol -1求炼钢温度下,液态钛溶于铁液反应Ti(l)=[Ti]的溶解焓。
《冶金热力学与动力学实验》

《冶金热力学与动力学实验》指导书实验一 、 碳的气化反应一.实验目的1.测定恒压下不同温度时反应的平衡常数。
2.了解在恒温恒压下反应达平衡时测定平衡常数的方法。
3.了解影响反应平衡的因素。
二.实验原理在高炉炼铁、鼓风炉炼铜、铅、锌以及煤气发生炉等生产实践中,固体碳的气化反应具有十分重要的意义。
其反应为:C +CO 2=2CO该反应的自由度为F =2-2+2=2,即反应平衡时,气相成分取决于温度和系统的压力。
在一大气压时,该反应的平衡常数为:%)(%)(2222CO CO P P K CO CO P ==(1—1)由等压式知B RT H K P +∆-=303.2lg (1—2)式中ΔH 为反应热,R 为气体常数,T 为绝对温度,B 为常数。
三.实验装置如图2-3所示,由二氧化碳气瓶、气体净化系统、管式高温炉及控温仪表、气体分析仪器组成。
图1-3碳的汽化反应实验装置1.CO2气瓶2 流量计3.管式电阻炉4.铂铑热电偶5.温度控制器6. CO2传感器;7.计算机8实验台四.实验步骤1.按图装好仪器设备,将碳粒装入电炉内瓷管的高温带,塞上胶塞,用融化的石蜡密封好。
2.分段检查系统是否漏气,重新密封,直至不漏气为止。
3.通电升温接通电源,打开控温器电流为5A,逐步升到10~12 A。
在升温的同时;打开气瓶,以较大的气流(40ml/分)排出系统内的空气,排气5分钟后调流量为20ml/分,并保持此流量不变。
4.炉温在600℃恒温5分钟后,接通CO2气体传感器,计算机读数,记录CO2%含量。
5. 再按上述操作连续4点,700℃,800℃,900℃,1000℃。
分析反应平衡气体中CO2含量同上操作,再取该温度下反应平衡气体,记录CO2%含量。
7.实验完毕,恢复仪器原状,切断电源,关闭气体。
五.实验报告要求1.计算各温度下平衡气相成分,以体积百分数表示,取10次结果的平均值。
2.计算各温度下的平衡常数K p。
3.绘制平衡气相中一氧化碳与温反t的关系曲线。
钢铁冶金原理教学 反应过程动力学方程的建立

如用物质的量浓度对时间的导数来表示总反应的速率,则 因
于是前式可改写为
令
为容量速率常数,则有
该式为双膜理论的液-液反应过程动力学速率微分式
前式中,令 —为总反应的速率常数;则速率微分式为
式中
是反应的驱动力,而各环节容量速率常数
的倒数,则是各环节呈现的阻力。三个阻力之和即是反
为c0,反应界面上的浓度为c,反应气体的 平衡浓度为c平。组成环节的速率式如下:
界面化学反应速率: 产物层内扩散速率: 对上式(Ⅱ)分离变量积分并由二联立式解出界面浓度c并 代入一式,得出
上式即在忽略外扩散的条件下,反应过程由界面化学反应及 内扩散混合控速的反应速率式。
讨论:内扩散和化学反应限速的情况
2)在两相的界面上,处于动态平衡状态; 3)在每相的范围内组元的扩散通量,对于液体来说与该组元在溶液体 内和界面处的浓度差成正比即
4)虽然在液相内有紊流,但边界层中的流体是静止不动的,不受流体 体内流动状态的影响,在各相中的传质被看作是独立进行的,互不影响。
速率式的推导
各环节及速率如下: 反应物向相界面扩散: 界面化学反应: 产物离开相界面扩散: 当反应处于稳定态时, 联立以上三式可得 出总反应的速率式:
第三节 反应过程动力学方程的建立
Forming the Kinetics Equation of Reaction Process
本节主要内容: 3.1 稳态原理; 3.2 动力学方程的建立过程; 3.3 液-液相反应模型—双膜理论; 3.4 气-固相反应模型—未反应核模型。
3.1 稳定态原理的内容
原理内容:
对串联的反应过程:稳态原理就是串联反应进行了一段时间后,各 反应的速率经过互相调整,从而达到相等。反应的中间产物被下一串联 反应消耗,不出现物质的积累,过程处于稳态中。
冶金过程动力学
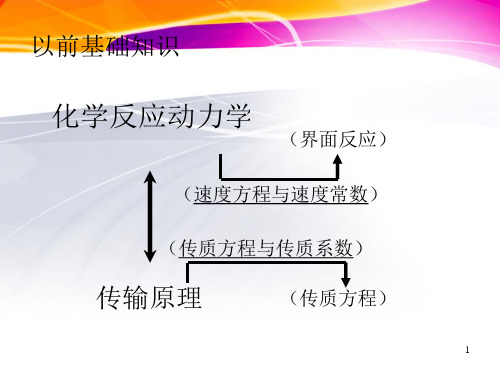
p静=lgh
2 cos rmax gh
l
14
气液相部分主体思路
2[N] N2 2[H] H2 2[O] O2 [C]+[O] CO
N2 H2 O2 CO 钢液
气泡
[N] [O] [C] [H]
钢液边界层内扩 散是控制环节
(1)氧、碳等穿过钢液边界层扩 散到气泡表面,即
[O][O]s, [C][C]s, [H][H]s, [N][N]s等
以前基础知识
化学反应动力学
(界面反应)
(速度方程与速度常数)
(传质方程与传质系数)
传输原理
(传质方程)
1
基本概念
化学反应: AA BB YY ZZ
反应物 i 0 ;生成物 i 0 。
反应进度:
ni nio i
反应速率:
•
d
dt
1
i
dni dt
or
v 1 • dci
i dt
• (1)[A] 由金属液内穿过金属液一侧边界层 向金属液-熔渣界面迁移;
• (2)(Bz+)由渣相内穿过渣相一侧边界层向熔 渣-金属液界面的迁移;
• (3)在界面上发生化学反应 ; • (4)(Az+)*由熔渣-金属液界面穿过渣相边界
层向渣相内迁移;
• (5)[B]* 由金属液/熔渣界面穿过金属液边界 层向金属液内部迁移。
C+O2=CO2
氧化物还原 反应
CO CO2
反 气层 生 应 体成界 边物面 界 层
MO+CO=M+CO2
10
抽象化--未反应核模型
(1)反应物致密的 ,产物层 多孔; (2) 扩散速度 << 化学反应速度。
第8章 冶金过程动力学 ★★★★
(1). 外扩散限制,kG<<De(k), (2). 内扩散限制, De<<k(kG),
t
t
O r0
R 0 e (C A CA ) 3kG
O r02
(Fe2O3︱Fe 或Fe3O4 ︱Fe 或FexO︱Fe)的一界面模型和有3
个界面(Fe2O3︱Fe3O4 ︱FexO︱Fe)的三界面模型,其中一 界面未反应核模型应用比较广泛。
依此未反应核模型,铁矿石还原反应步骤为:
(1) 还原气体A通过气相边界层向矿球表面扩散,即外扩散;
(2) 气体A通过多孔的产物层向反应界面扩散,同时铁离子也 通过产物层向内部扩散,称为内扩散; (3) 在反应界面上气体A与铁氧化物发生还原反应,其中包括 还原剂的吸附和气体产物的脱附; (4) 气体产物通过固体产物层向矿球表面扩散; (5) 气体产物离开矿球表面向气相内部扩散;
氧流与熔池作用,将动量
传递给金属液; 金属熔池产生循环运动。
8.2.1 元素氧化反应的动力学 氧流穿入熔池某一深度并构成火焰状作用区(火点区)
8.2.1 元素Байду номын сангаас化反应的动力学
氧气炼钢中还存在乳化和泡沫现象 在氧流强冲击和熔池沸腾 作用下,部分金属微小液 滴弥散在熔渣中;
乳化的程度与熔渣粘度、 表面张力等性质有关;
ri r0 (1 R)1/ 3
0 e 4r02 (C A CA ) dn JA dt r0 r0 ri r02 1 K k G De ro k (1 K ) ri2
锗冶炼中的冶金反应动力学
通过实验测定还原反应的动力学数据,验证动力学模 型的准确性。
锗的挥发反应动力学分析
挥发反应
在特定条件下,锗以气态形式从熔融态或溶液 中挥发出来。
挥发机制
研究锗的挥发机制,包括挥发温度、挥发速率 等,有助于提高锗的提取效率。
实验方法
通过实验测定锗的挥发温度和挥发速率,分析挥发反应的动力学特性。
循环利用冶炼渣
通过反应动力学分析,可以探索 从冶炼渣中进一步提取锗的方法 ,从而实现锗的高效回收和循环 利用。
控制锗冶炼过程中的环境污染
减少有害气体排放
基于反应动力学原理,优化锗冶炼过程中的气体排放控制,降低 有害气体的产生和排放。
降低废水排放
通过反应动力学分析,可以优化废水处理工艺,降低废水中有害 物质的含量,减轻对环境的污染。
05反应动力学在锗Fra bibliotek炼过程 中的应用
优化锗冶炼工艺参数
1 2 3
确定适宜的反应温度
通过研究反应动力学,可以确定在一定条件下, 锗冶炼反应的最佳温度范围,从而提高锗的提取 率和纯度。
控制反应时间
根据反应动力学模型,可以确定达到最佳锗提取 效果所需的反应时间,避免过长的反应时间导致 能耗增加和设备腐蚀。
锗冶炼中的冶金反应动力学是研究锗在高温、高压条件下与 不同介质发生的化学反应速率和反应机制的重要学科,对于 提高锗的冶炼效率和产品质量具有重要意义。
国内外研究现状
国外对锗冶炼中的冶金反应动力学研究起步较早,已经取 得了一定的研究成果。国内在这方面的研究相对较少,但 随着锗需求的增加和冶炼技术的进步,国内的研究也在逐 步加强。
感谢您的观看
THANKS
减少固体废弃物产生
基于反应动力学原理,优化锗冶炼工艺,减少固体废弃物的产生 ,提高资源利用率。
冶金宏观动力学基础
冶金宏观动力学基础冶金宏观动力学基础是研究冶金材料宏观性能变化的学科。
它研究材料在外界条件变化下的宏观响应,以及材料内部微观结构与性能之间的关系。
冶金宏观动力学基础是冶金学的重要分支,对于材料的制备、加工和应用具有重要意义。
在冶金宏观动力学基础中,常常涉及到材料的力学性能、热力学性能和变形行为。
力学性能是指材料在受力作用下的应力和应变关系,是冶金宏观动力学研究的基础。
热力学性能是指材料在温度变化下的热膨胀、热导率等性质。
而变形行为则是指材料在外力作用下的塑性变形、断裂行为等。
冶金宏观动力学基础研究的对象可以是金属材料、非金属材料以及复合材料等。
不同材料具有不同的宏观动力学性能,这取决于其组织结构和化学成分。
例如,金属材料的宏观性能受到晶体结构、晶界、位错和孪晶等微观结构的影响。
非金属材料如陶瓷和聚合物材料的宏观性能则与其分子结构和键合方式有关。
在冶金宏观动力学基础研究中,常常采用实验和数值模拟相结合的方法。
实验可以通过应力-应变曲线、热膨胀曲线等测试手段来获取材料的宏观性能数据。
数值模拟则可以通过建立数学模型和使用计算机软件来模拟材料的宏观响应。
这种方法可以更好地理解材料的宏观性能变化机制。
冶金宏观动力学基础的研究成果在冶金工程中具有广泛的应用。
例如,在材料制备过程中,可以通过控制材料的加热和冷却过程来调控材料的相变行为,从而获得具有特定性能的材料。
在材料加工中,可以根据材料的宏观性能变化来选择合适的加工工艺,以提高材料的力学性能和耐磨性。
在材料应用中,可以根据材料的宏观性能来设计合理的结构和使用条件,以保证材料的安全可靠性。
冶金宏观动力学基础是研究材料宏观性能变化的学科,它对于材料的制备、加工和应用具有重要意义。
通过研究材料的力学性能、热力学性能和变形行为,可以更好地理解材料的宏观响应机制,为冶金工程提供科学依据。
冶金原理气固反应动力学讲解
对反应 aA(s) bB(g,l) eE(s) dD(g,l) 而言,由于内扩散控制
故:单位时间A的反应量 dm 单位时间B的扩散量 J
dt
dm dt
4r12
dr1 dt
根据菲克第一定律求出在Cs = C0时
J
4 D2
r0r1 r0 r1
C0
两式相等,解方程得
(式13-12b)
2.问题分析
(1)方程式 1 (1 R)1的/3 适用k'范t 围
任何真理都有其一定的适用范围 从推导过程的“假设”知其适用范围为:
反应固相为单一、致密球体,其各方向上的化学性质一致; 反应剂浓度C0保持不变。 对非球体:
1 (1 R)1/Fp k't
三维尺寸不等时Fp 的取值介于 2和3之间
1-(1-R)1/3 1-(1-R)1/3
0
t
t
(3)应用
a. 指明提高反应率的途径
1 (1 R)1/3 kC0n t
r0
式中 kC0n t 项↑则(1- R)1/3↓ R↑
r0
故 时间t↑、C0↑、r0↓、提高温度使k↑,都有利于提高R
b. 利用不同温度下k值求反应的表观活化能
根据Arrhenius公式: lnk E B RT
形的致密颗粒,反应剂浓度不变、反应前后颗粒直径不变的情况下,
当属内扩散控制,则 直线通过原点。
1 2 R (1 R)与2/3反应时间t成直线关系, 3
表观活化能小,8~30kJ·mol-1
1-2/3R-(1-R)2/3
0
t
实例:黄铜矿的硫酸高铁浸出过程:
反应 2Fe2(SO4)3(aq) + CuFeS2(s) = CuSO4(aq) +5FeSO4(aq) + 2S(s)
- 1、下载文档前请自行甄别文档内容的完整性,平台不提供额外的编辑、内容补充、找答案等附加服务。
- 2、"仅部分预览"的文档,不可在线预览部分如存在完整性等问题,可反馈申请退款(可完整预览的文档不适用该条件!)。
- 3、如文档侵犯您的权益,请联系客服反馈,我们会尽快为您处理(人工客服工作时间:9:00-18:30)。
反应:A(g) + bB(s) = gG(g) + sS(s)
• 外扩散: rg= 4r02kg(cAbcAs)
•
内扩散:
rD=
4ri2Deff
dcA dri
• 界面反应:rc= 4ri2krea (cAi-cGi/K )
dnA dt
稳态过程:rg = rD = rc
cij
控速环节:rg
or
N I N II Nr
1/ kI 1/ mk II 1/ k
1/ kI 1/ mk II 1/ k
1/ kI 1/ mk II 1/ kI 1/ mk II
8
控速环节的浓度特征及其应用
界面化学 反应控速
反
气 体
应 界
浓
面
度
气体边界层 内传质控速
Cb C0
反
应
界
面
r = k+A(ci-ci’/K) r = kdA(cb-c0)
r
p静=lgh
2 cos rmax gh
l
15
气液相部分主体思路
2[N] N2 2[H] H2 2[O] O2 [C]+[O] CO
N2 H2 O2 CO 钢液
气泡
[N] [O] [C] [H]
钢液边界层内扩 散是控制环节
(1)氧、碳等穿过钢液边界层扩 散到气泡表面,即
[O][O]s, [C][C]s, [H][H]s, [N][N]s等
(c[Mn]
1 Kθ
c(Mn2 c) [Fe] ) c(Fe2 )
24
其它步骤为控速环节
• 第2步骤:
.
N (Fe2 )
A D(Fe2 )
(Fe2 )
c(Fe2 ) (1
Q Kθ )
• 第4步骤: • 第5步骤:
N (Mn2 )
A D(Mn2 )
(Mn2 )
Kθ c ( (Mn2 ) Q
1)
冶金过程动力学
总结
1
以前基础知识
化学反应动力学
(界面反应)
(速度方程与速度常数)
(传质方程与传质系数)
传输原理
(传质方程)
2
基本概念
化学反应: AA BB YY ZZ
反应物 i 0 ;生成物 i 0 。
反应进度:
ni nio i
反应速率:
•
d
dt
1
i
dni dt
or
v 1 • dci
23
第1步骤为控速环节
N[Mn]
kd
A(c[Mn]
c* [Mn]
)
A
DMn
[Mn]
(c[Mn]
c* [Mn]
)
Kθ
c c *
*
(Mn2 ) [Fe]
c c (Mn2 ) [Fe]
c c * [Mn]
* (Fe 2+ )
c c * [Mn]
(Fe 2+ )
N[Mn]
A D[Mn]
[Mn]
dt M [C]
dnC kd A (w[O] w[O]s )
dt M [O]
dnC VAr dpCO dt RT dt
p / pθ
w[O]s
CO
104 KCO w[C]
17
例:低碳钢脱碳
B kd ART
VM[C]
VAr dpCO kd A (w[C]
p / pθ CO
)
RT dt M[C]
i dt
3
基本关系(1)
• 速率方程:
v kcAA cBB
(质量作用定律)
一级反应: 二级反应:
dc kc dt
dx dt
k1 (cA0 - x) – k-1(cB0+x)
dcA adt
kcAcB
4
基本关系(2)
• 菲克第一、第二定律:
J Ax
D
A
(
dcA dx
)
C D 2C
恒等式,即动力学方程。 • (7)通过实验结果验证方程的适用性。
27
N[ Fe]
A D[Fe]
[Fe]
c[Fe]
Kθ (
Q
1)
N [Mn]
Vst
dc[Mn] dt
Q c(Mn2 ) c[Fe] c c [Mn] (Fe2 ) 25
w[Mn]* w[Mn]eq
N[Mn]
A D[Mn]
[Mn]
(c[Mn]
c* [Mn]
)
N[Mn]
A D[Mn]
[Mn]
(c[Mn]
c[Mn],eq )
N [Mn]
Vst
dc[Mn] dt
c[i]
w[i]
st
M [i]
dw[Mn] dt
AD[Meq
)
ln
w[Mn]0 w[Mn]eq w[Mn] w[Mn]eq
VAstD[[MMnn]2]6t
多相反应动力学一般研究思路
p' CO
peq CO
KCO pθ[C][O]104
19
吹氩脱氢-脱氢与脱碳关系
p' H2
KH2 w[H]2 pθ 104
• 脱氢吹氩量:
p
'
H2
dVAr
103Wd[H ]
RT
2M[H ]
VAr,0
273VAr T
1.12W 1
(
K H2 [H ]t
1
)
[H ]0
/ m3
• 脱碳与脱氢关系:
t
x 2
• 传质方程:
N J A kd A(Cs Cb )
(稳态)
(非稳态)
• Sh = kdL/D (Sherwood) • Re = uL/ν(Reynolds) • Sc =ν/D (Schmidt)
5
双膜理论---引出两者间联系
Nr
A(k CIi
k
'
C
i II
)
NI
kI A(CI
d[C] 6KCO[C][O] d[H ]
dt
KH[H ]2
dt
20
真空脱气
dnA V dcA
dt
dt
dnA dt
Akd (c
cs)
dcA dt
A
V
kd
(cA
cAs )
ln cA cAo
cAs cAs
A V
kdt
21
液-液相反应步骤
[A] + (B z+ ) = (Az+ ) + [B]
104 KCO w[O]
C w[C]0 3 (w[O]0 w[O]) 4
dpCO dt
B(C DpCO )
D
104
K
1 CO w[O]
p
ln
C
C
Dp
' CO
BDt
C
1
ln
C
Dp
' CO
ln
1
ln 1
1
10
4
kd ART
K V CO ArM [C
]
p
t w[O]
18
吹氩脱碳-氩气需要量
VAr,0
22
反应: [Mn]+(FeO)=(MnO)+[Fe]
• (1) 钢中锰原子向钢渣界面迁移; • (2) 渣中Fe2+向渣钢界面迁移; • (3) 钢渣界面上发生化学反应:
[Mn]+(Fe2+)=(Mn2+)+[Fe] • (4) 生成的Mn2+从界面向渣中扩散; • (5) 生成的Fe原子从界面向钢液内扩散。
1
k f 4r02 Deff 4r0ri krea 4ri2 (1 1/ K )
dri
(C
b A
C
eq A
)bM
B
/
B
dt (ri / r0 )2 ri (r0 ri )
1
kf
Deff r0 k (1 1/ K )
14
活性孔隙半径的上限
p附
2
R
2
cos(180 )
r
2 cos
(2)气泡表面上发生化学反应: [O]s+[C]sCO, 2[H]s H2, 2[N]s N2 等
(3)生成气体从表面扩散到气泡 内部,并随气泡上浮排出。
16
吹氩脱碳-气泡内压力变化
p / pθ
w[C]s
CO
104 KCO w[O]
• 低碳钢脱碳: • 高碳钢脱碳:
dnC kd A (w[C] w[C]s )
C+O2=CO2
氧化物还原 反应
CO CO2
反 气 生应 体 成界 边 物面 界层 层
MO+CO=M+CO2
11
抽象化--未反应核模型
(1)反应物致密的 ,产物层 多孔; (2) 扩散速度 << 化学反应速度。
• 两点假设: (1)反应在同一界面上进
行; (2)反应过程外径不变,
未反应核与生成层结构均 一。
273V Ar T
0.14W ln [O]0 KCO[C] [O]
• 高碳钢脱碳:
pC' O dVAr 103W d[O]
RT dt
M[O] dt
• 低碳钢脱碳:
pC' O dVAr 103W d[C]
RT dt
M [C] dt
VAr,0
273V Ar T
0.187W ln [C]0 KCO[O] [C]