人造石的生产流程及生产工艺
人造石的生产流程
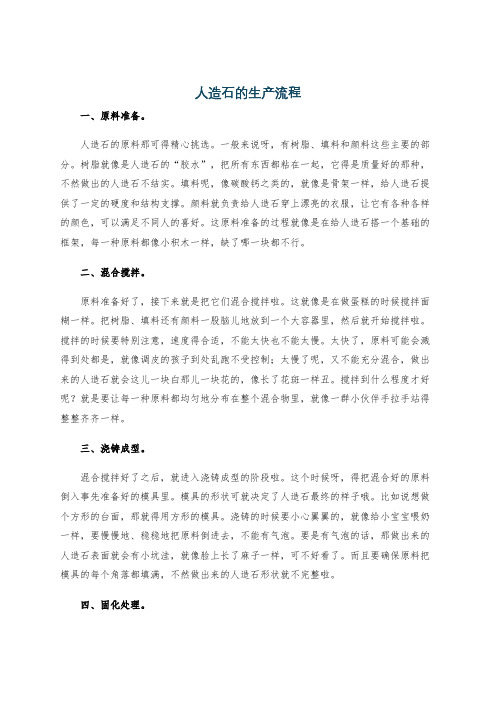
人造石的生产流程一、原料准备。
人造石的原料那可得精心挑选。
一般来说呀,有树脂、填料和颜料这些主要的部分。
树脂就像是人造石的“胶水”,把所有东西都粘在一起,它得是质量好的那种,不然做出的人造石不结实。
填料呢,像碳酸钙之类的,就像是骨架一样,给人造石提供了一定的硬度和结构支撑。
颜料就负责给人造石穿上漂亮的衣服,让它有各种各样的颜色,可以满足不同人的喜好。
这原料准备的过程就像是在给人造石搭一个基础的框架,每一种原料都像小积木一样,缺了哪一块都不行。
二、混合搅拌。
原料准备好了,接下来就是把它们混合搅拌啦。
这就像是在做蛋糕的时候搅拌面糊一样。
把树脂、填料还有颜料一股脑儿地放到一个大容器里,然后就开始搅拌啦。
搅拌的时候要特别注意,速度得合适,不能太快也不能太慢。
太快了,原料可能会溅得到处都是,就像调皮的孩子到处乱跑不受控制;太慢了呢,又不能充分混合,做出来的人造石就会这儿一块白那儿一块花的,像长了花斑一样丑。
搅拌到什么程度才好呢?就是要让每一种原料都均匀地分布在整个混合物里,就像一群小伙伴手拉手站得整整齐齐一样。
三、浇铸成型。
混合搅拌好了之后,就进入浇铸成型的阶段啦。
这个时候呀,得把混合好的原料倒入事先准备好的模具里。
模具的形状可就决定了人造石最终的样子哦。
比如说想做个方形的台面,那就得用方形的模具。
浇铸的时候要小心翼翼的,就像给小宝宝喂奶一样,要慢慢地、稳稳地把原料倒进去,不能有气泡。
要是有气泡的话,那做出来的人造石表面就会有小坑洼,就像脸上长了麻子一样,可不好看了。
而且要确保原料把模具的每个角落都填满,不然做出来的人造石形状就不完整啦。
四、固化处理。
浇铸完了之后,就到了固化处理这一步。
这个过程就像是让人造石从一个软软的小团子变成一个硬邦邦的大石头。
固化的时候需要一定的温度和时间呢。
就像孵小鸡一样,得在合适的温度下等待合适的时间。
温度太高了,可能会把人造石烤焦了,变得脆脆的,容易坏掉;温度太低了呢,固化的时间就会变得很长很长,就像乌龟爬一样慢。
人造石的生产流程及生产工艺

人造石的生产流程及生产工艺人造石是用非天然的混合物制成的,如树脂、水泥加碎石黏合剂。
人造石(又称"人造大理石")是一种新型的复合材料,是用不饱和聚脂树脂与填料、颜料混合,加入少量引发剂,经一定的加工程序制成的。
在制造过程中配以不同的色料可制成具有色彩艳丽、光泽如玉酷似天然大理石的制品。
人造石的生产流程及图片介绍说明下配方—碎色板—制颗粒—配颗粒料—混料—调色浆—成型配料—搅拌浆料—倒刮浆—抽真空—排气泡—模具打蜡—起模和堆放—烤箱烘烤—砂板—补板—配胶水—检验—入库人造石生产工艺说明书:人造石所用材料大致为:1,不饱和树脂;2,粉料(钙粉或铝粉);3,不饱和树脂用固化剂(甲乙酮)和促进剂(钴水).主要流程:配料--搅拌--真空--凝胶--固化成型--脱模--砂光--检验--入库工艺流程:把树脂放进搅拌罐里在放促进剂先均匀搅拌2分就可以然后放相应的添加剂色浆在搅拌5分钟后放入粉料与固化剂真空均匀搅拌20分左右,把搅拌好的浆料到如入准备好的玻璃板上(事先在玻璃上吐沫三星腊或普通地板腊都可以也叫脱模剂)后在过20分产品固化成型,这个时候板材自然形成的硬度是70%如果不进行后固化(也就是放进恒温50到80度之间空间内3小时到6小时)需要7天完全达到100%硬度,异型无须后固化,标板需要事先生产很多板材放在库房里等待销售所以要后固化以防变形.产品的色泽外观主要靠把握色浆的准确添加.色浆的称取之前,最好是用苯乙烯稀释成1%浓度的稀色浆密封,待用。
这样能够比直接称取色浆来正确度提高百倍。
最合理的搅拌顺序顺次是:树脂+促进剂搅拌+色浆搅拌+填料搅拌+固化剂搅拌。
成型过程中、砂光好的板材要避免阳光(紫外线)映照。
同样颜色的板子,固化剂和促进剂的投入量要不异,加固化剂后的搅拌时间也要不异,抽真空时间也要不异。
大搅拌罐里一次性搅拌几十张的料,每次出料之前,要适当地搅拌几转再出料。
原因是在一小时左右的时间里,大搅拌罐里会出现上下料之间轻微的比重失衡现象(沉淀)。
人造石制造流程

人造石制造流程人造石是一种人工合成的材料,常用于建筑、装饰和家具制造等领域。
它具有天然石材的美观外观和质感,同时具备更好的均匀性和可塑性。
人造石制造流程包括原料准备、混合、成型、固化和加工等多个步骤。
下面将详细介绍每个步骤的具体流程。
1. 原料准备人造石的主要原料包括树脂、颜料、填料和助剂等。
树脂通常采用聚酯树脂、环氧树脂或丙烯酸树脂等。
颜料用于调配出所需的颜色和纹理效果。
填料可以是石粉、石英砂、玻璃纤维等,用于增加人造石的硬度和强度。
助剂包括固化剂、增塑剂和防火剂等,用于调节人造石的性能和特性。
在原料准备阶段,首先需要将树脂和颜料按照一定比例混合,确保颜色的均匀性。
然后将填料加入到混合物中,搅拌均匀,使填料与树脂充分结合。
最后,根据需要添加助剂,如固化剂用于固化树脂,增塑剂用于调节人造石的柔韧性,防火剂用于提高人造石的阻燃性能。
2. 混合混合是将原料充分搅拌均匀的过程。
通常采用搅拌机进行混合,搅拌机的类型根据生产规模和工艺要求而定。
混合的时间和速度需要根据原料的性质和配方进行调整,以确保混合物均匀分散。
在混合过程中,需要注意搅拌机的温度控制,避免过高的温度导致树脂固化或填料热分解。
同时,还需要定期检查混合物的质量,确保颜色和纹理的一致性。
3. 成型成型是将混合物转化为所需形状的过程。
常见的成型方法包括挤出法、压制法和喷涂法等。
挤出法挤出法是将混合物通过挤压机挤出成型的方法。
首先,将混合物注入到挤压机的进料口,并通过螺杆将混合物推入模具中。
模具的形状决定了最终成型产品的形状。
在挤出过程中,需要控制挤出机的温度和压力,确保混合物充分填充模具,并保持一定的成型速度。
压制法压制法是将混合物放置在模具中,然后通过压力将其压制成型的方法。
模具可以是单个模具或多个模具组合而成的模具板。
在压制过程中,需要控制压力和温度,使混合物在模具中充分流动,并保持一定的成型时间。
喷涂法喷涂法是将混合物通过喷涂枪喷涂到模具表面的方法。
树脂人造石的工艺流程
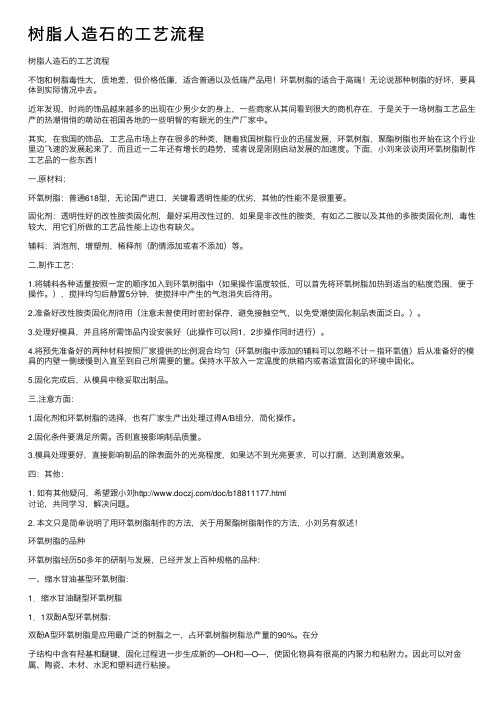
树脂⼈造⽯的⼯艺流程树脂⼈造⽯的⼯艺流程不饱和树脂毒性⼤,质地差,但价格低廉,适合普通以及低端产品⽤!环氧树脂的适合于⾼端!⽆论说那种树脂的好坏,要具体到实际情况中去。
近年发现,时尚的饰品越来越多的出现在少男少⼥的⾝上,⼀些商家从其间看到很⼤的商机存在,于是关于⼀场树脂⼯艺品⽣产的热潮悄悄的萌动在祖国各地的⼀些明智的有眼光的⽣产⼚家中。
其实,在我国的饰品,⼯艺品市场上存在很多的种类,随着我国树脂⾏业的迅猛发展,环氧树脂,聚酯树脂也开始在这个⾏业⾥边飞速的发展起来了,⽽且近⼀⼆年还有增长的趋势,或者说是刚刚启动发展的加速度。
下⾯,⼩刘来谈谈⽤环氧树脂制作⼯艺品的⼀些东西!⼀.原材料:环氧树脂:普通618型,⽆论国产进⼝,关键看透明性能的优劣,其他的性能不是很重要。
固化剂:透明性好的改性胺类固化剂,最好采⽤改性过的,如果是⾮改性的胺类,有如⼄⼆胺以及其他的多胺类固化剂,毒性较⼤,⽤它们所做的⼯艺品性能上边也有缺⽋。
辅料:消泡剂,增塑剂,稀释剂(酌情添加或者不添加)等。
⼆.制作⼯艺:1.将辅料各种适量按照⼀定的顺序加⼊到环氧树脂中(如果操作温度较低,可以⾸先将环氧树脂加热到适当的粘度范围,便于操作。
),搅拌均匀后静置5分钟,使搅拌中产⽣的⽓泡消失后待⽤。
2.准备好改性胺类固化剂待⽤(注意未曾使⽤时密封保存,避免接触空⽓,以免受潮使固化制品表⾯泛⽩。
)。
3.处理好模具,并且将所需饰品内设安装好(此操作可以同1,2步操作同时进⾏)。
4.将预先准备好的两种材料按照⼚家提供的⽐例混合均匀(环氧树脂中添加的辅料可以忽略不计-指环氧值)后从准备好的模具的内壁⼀侧缓慢到⼊直⾄到⾃⼰所需要的量。
保持⽔平放⼊⼀定温度的烘箱内或者适宜固化的环境中固化。
5.固化完成后,从模具中稳妥取出制品。
三.注意⽅⾯:1.固化剂和环氧树脂的选择,也有⼚家⽣产出处理过得A/B组分,简化操作。
2.固化条件要满⾜所需。
否则直接影响制品质量。
3.模具处理要好,直接影响制品的除表⾯外的光亮程度,如果达不到光亮要求,可以打磨,达到满意效果。
人造大理石配方和工艺(转)

生产石质人造大理石是以不饱和聚酯树脂为粘合剂,以石粉为主要填料,配以玻璃粉、矿渣石等为辅料加工制成。
石质人造大理石的生产工序包括原料选配、模具及其处理、混料、花纹制作、震捣成型、脱模修整等。
1.原料选配用于制作人造大理石的不饱和聚酯树型号很多,目前较为广泛使用的有197号、196号、195号等。
对于石质人造大理石面层的树脂,最好选用透明度高、防老化、阻燃性能优越、表面硬度高的品种。
对于石粉要求并不十分严格,除少数影响树脂固化者外,大多数石粉都可用作填料,但粒度和色泽有一定的要求。
原则上,石粉细,产品表面光泽度就高,但树脂用量多;反之,石粉粗糙,产品致密度差,光泽度低,但可节省树脂。
我们将石粉和碎玻璃粉进行筛分,各类筛分的百分比如:石粉和玻璃的筛分粒度(目) 占总重量的百分比(%)石粉玻璃粉粒度(目)占总重量的百分比(%) 石粉玻璃粉20~40 3.2 44.00 120~140 1.68 2.7040~60 3.7 21.75 140~160 9.8 1.5460~80 2.52 8.25 140~160 2.45 0.5880~100 12.40 9.0 160~180 19.16 2.53100~120 7.40 2.7 180~200 38.25 9.95带色石粉用于制作颜色相同的产品比较理想。
带色石粉不能用于制作白色人造大理石,而用白色石粉则可制作各种色彩的人造大理石。
因此尽可能选用白色纯净的汉白玉石粉、方解石石粉、白石石粉等。
这样不但能保证产品的色调美,而且制品的石质感强。
其他辅助填料,同样对粒度和色泽有不同的要求。
同时还必须考虑辅料与石粉之间的合理配比。
2、模具及其处理生产人造大理石所用的模具分为模板和边框部分。
模板的表面光泽度关系到制品的表面性能。
要求模板必须高度平整、光亮,并且具有一定的硬度。
模板先用清水洗净,若有油污需用洗衣粉或其他去油剂沾水擦洗。
用专用胶漆滚(一般用油印机滚)在模板上涂上脱模剂,晾晒干透以后再用胶滚涂上一层树脂作为面层。
人造大理石配方和生产法

人造大理石配方和生产法
人造大理石配方和生产法
人造大理石
人造大理石实际上是一种“塑料混凝土”,是一种新型的建筑材料,用于高档建筑及家具装饰等。
人造大理石的原料易得,制作简便,既可机械化大规模生产,也可用手土法制作。
一、配方
1、配方一:
(1)胶料:
(2)填料:石粉,胶料重量的3倍。
(3)脱模剂:聚乙烯醇水溶液适量。
2、配方二:
(1)胶料:
(2)
(3)脱模剂:甘油(或液体石腊)适量。
二、制法:
1、按配方计量后,将胶料的各种原料混合调匀。
2、将填料与配好的胶料立即混匀,倒入涂了脱模剂的模型内,振动,使其均匀紧实,无孔隙,并行调花,平整后让其静置固化。
3、脱模后进行修边、磨光、抛光即成。
三、说明
1、固化剂乙二胺可改苯二甲胺,后者毒性小,但用量需15份左右。
2、模型最好选用抛光不锈钢模。
3、调花料一般用轻质碳酸钙粉末。
4、可用500#水泥和细砂与水调匀作人造大理石的填料,或作人造大理石的底层(板)和里层等。
水泥与河砂的重量比为1:2。
人造石生产工艺
人造石生产工艺
人造石是一种人工合成的石材,采用天然矿物颗粒、沙子、水泥和树脂等材料混合而成。
其生产工艺通常包括原料准备、混合和加压、固化和后处理等步骤。
首先,原料准备。
人造石的基本原料主要有石英砂、石英粉、树脂、颜料和填充料等。
其中,石英砂和石英粉是人造石的主要矿物颗粒,树脂可提供强度和耐磨性,颜料和填充料则用于增加石材的色彩和纹理。
接着是混合和加压阶段。
将原料按照一定比例混合,并加入适量的水泥和树脂粘合剂,制成石材浆料。
浆料将被倒入模具中,并用振动平台震动,以除去气泡和均匀分布颗粒。
随后,将浆料放入压机中进行加压,以消除水分,使石材更紧密、坚硬。
固化是人造石生产中不可缺少的一步。
将加压后的人造石板用烤箱等设备进行固化,其目的是使树脂发生化学反应,形成牢固的结合,并提高人造石的强度和耐久性。
最后是后处理。
固化后的人造石板需要进行研磨和抛光,以获得光滑、平整的表面。
在研磨过程中,使用研磨机械对石材表面进行打磨,以去除任何杂质和瑕疵。
然后,使用抛光机械对石材表面进行抛光,以增加石材的光泽和质感。
除了以上基本的生产工艺,人造石的生产还涉及到色彩调配和纹理设计等环节。
通过调整颜料和填充料的比例,可以制造出各种色彩的人造石。
此外,还可以在石材表面通过特殊的处理
方式来模拟天然石材的纹理,如大理石纹、花岗岩纹等等。
总的来说,人造石的生产工艺包括原料准备、混合和加压、固化和后处理等环节。
通过这些步骤,人造石得以制造出各种颜色和纹理的石材,具备与天然石材相似甚至更好的性能,广泛应用于建筑、装饰和家具等领域。
人造石工艺流程
人造石工艺流程
人造石是一种人工合成的石材,通常用于建筑装饰和家居装饰。
人造石工艺流程是一个复杂的过程,需要经过多道工序才能完成。
下面就让我们来了解一下人造石的工艺流程。
首先,人造石的原材料主要包括天然石粉、树脂、颜料等。
这些原材料需要经过精确的配比,确保混合物的质地和颜色都符合要求。
接下来,将混合物倒入模具中,进行压实和振动,以确保混合物充分填满模具并排除气泡。
然后,将模具放入特定温度和湿度的环境中,进行固化和养护,使混合物逐渐硬化成为坚实的石材。
在固化和养护的过程中,人造石可能需要进行一些特殊的处理,比如切割、打磨、上釉等。
这些工序的目的是为了使人造石的表面更加光滑、均匀,并且增加一些特殊的装饰效果。
最后,经过质量检查和包装,人造石就可以正式出厂了。
整个人造石工艺流程看似简单,实际上却需要经过精密的操作和严格的监控。
只有严格按照工艺流程进行操作,才能保证人造石的质
量和稳定性。
此外,人造石的工艺流程也需要不断的改进和创新,以适应市场需求和技术发展的变化。
总的来说,人造石工艺流程是一个综合性的工程,需要各个环节的精密配合和严格控制。
通过不懈的努力和创新,在不断改进工艺流程的同时,人造石的品质和应用范围也将得到进一步提升。
人造石台面生产工艺
人造石台面生产工艺
人造石台面生产工艺是指将多种原材料经过混合、搅拌、填充、硬化和调色等加工步骤,制成具有美观、耐用和环保等特点的石材台面。
以下是人造石台面生产工艺的一些内容示例:
1.材料准备:首先需要选择优质的原材料,包括无机材料、有机胶粘剂、天
然矿石粉、填料和各种颜料等。
根据生产需要,将这些原材料进行适当的混合和搅拌。
2.搅拌与混合:将各种原材料按照规定的比例混合在一起,并进行充分的搅
拌,以保证材料均匀分布。
搅拌过程中需要控制温度和湿度,以避免出现结块或不均匀的现象。
3.填充与硬化:将混合好的材料填充到台面模具中,并经过一定的硬化处理。
硬化的时间、温度和压力等因素都会影响人造石台面的质量和性能。
4.调色与打磨:在硬化后的人造石台面上进行调色处理,以调整外观颜色和
纹理效果。
同时需要进行打磨和抛光,以提高台面的光洁度和美观度。
5.质量检测与包装:在人造石台面生产完成后,需要进行质量检测,确保产
品符合相关标准和要求。
合格的产品进行包装处理,以便运输和储存。
总之,人造石台面生产工艺是一种较为复杂的过程,需要经过多个加工步骤和控制环节,以确保生产出高质量的人造石台面。
人造大理石生产工艺流程
人造大理石生产工艺流程人造大理石,又称合成石英石,是一种由人工合成的人造石材,具有类似大理石的外观和质感。
它由天然石英石粉、树脂、颜料等材料经过一系列工艺加工而成。
以下是人造大理石的生产工艺流程。
一、原材料准备1.1 石英石粉准备:选用高质量的天然石英石矿石,经过破碎、研磨等工艺处理,得到细腻的石英石粉。
1.2 树脂准备:选择适合制作人造大理石的树脂,如聚酯树脂、环氧树脂等,确保树脂的质量稳定。
二、配料混合2.1 石英石粉与树脂的配比:按照一定比例将石英石粉与树脂混合,以确保石英石粉能被树脂充分包裹。
2.2 添加颜料:根据需要,将适量的颜料添加到混合物中,以赋予人造大理石丰富的色彩。
三、搅拌和充填3.1 搅拌:将配料混合物放入搅拌设备中,进行充分的搅拌,以确保各种成分均匀混合。
3.2 充填:将混合物倒入模具中,用振动台或压力机进行充填,以排除气泡并使混合物密实。
四、固化和烘干4.1 固化:将充填好的模具放入固化室中,通过控制温度和湿度等参数,使混合物充分固化。
4.2 烘干:在固化后,将固化好的人造大理石块放入烘干室中,以去除余留的水分,并提高其硬度和强度。
五、打磨和抛光5.1 打磨:使用砂轮或磨头对固化后的人造大理石块进行粗磨,以去除表面的不平整和凹凸。
5.2 抛光:通过机械抛光或手工抛光,对打磨后的人造大理石块进行细磨,使其表面光洁如镜。
六、切割和加工6.1 切割:根据需要,将抛光好的人造大理石块进行切割,以得到所需的板材、砖块等形状。
6.2 加工:对切割好的人造大理石进行边角修整、孔洞开凿等加工,以满足不同的使用需求。
七、质检和包装7.1 质检:对生产好的人造大理石进行质量检验,包括外观、尺寸、硬度等指标的检测,以确保产品符合标准要求。
7.2 包装:将合格的人造大理石产品进行包装,通常采用木箱、纸箱等包装材料,以保护产品不受损坏。
人造大理石的生产工艺流程是一个复杂而精细的过程,需要严格控制每个环节的参数和质量。
- 1、下载文档前请自行甄别文档内容的完整性,平台不提供额外的编辑、内容补充、找答案等附加服务。
- 2、"仅部分预览"的文档,不可在线预览部分如存在完整性等问题,可反馈申请退款(可完整预览的文档不适用该条件!)。
- 3、如文档侵犯您的权益,请联系客服反馈,我们会尽快为您处理(人工客服工作时间:9:00-18:30)。
人造石的生产流程及生产工艺人造石是用非天然的混合物制成的,如树脂、水泥加碎石黏合剂。
人造石(又称"人造大理石")是一种新型的复合材料,是用不饱和聚脂树脂与填料、颜料混合,加入少量引发剂,经一定的加工程序制成的。
在制造过程中配以不人造石是用非天然的混合物制成的,如树脂、水泥加碎石黏合剂。
人造石(又称"人造大理石")是一种新型的复合材料,是用不饱和聚脂树脂与填料、颜料混合,加入少量引发剂,经一定的加工程序制成的。
在制造过程中配以不同的色料可制成具有色彩艳丽、光泽如玉酷似天然大理石的制品。
人造石的生产流程及图片介绍说明下配方—碎色板—制颗粒—配颗粒料—混料—调色浆—成型配料—搅拌浆料—倒刮浆—抽真空—排气泡—模具打蜡—起模和堆放—烤箱烘烤—砂板—补板—配胶水—检验—入库人造石生产工艺说明书:人造石所用材料大致为:1,不饱和树脂;2,粉料(钙粉或铝粉);3,不饱和树脂用固化剂(甲乙酮)和促进剂(钴水).主要流程:配料--搅拌--真空--凝胶--固化成型--脱模--砂光--检验--入库工艺流程:把树脂放进搅拌罐里在放促进剂先均匀搅拌2分就可以然后放相应的添加剂色浆在搅拌5分钟后放入粉料与固化剂真空均匀搅拌20分左右,把搅拌好的浆料到如入准备好的玻璃板上(事先在玻璃上吐沫三星腊或普通地板腊都可以也叫脱模剂)后在过20分产品固化成型,这个时候板材自然形成的硬度是70%如果不进行后固化(也就是放进恒温50到80度之间空间内3小时到6小时)需要7天完全达到100%硬度,异型无须后固化,标板需要事先生产很多板材放在库房里等待销售所以要后固化以防变形.产品的色泽外观主要靠把握色浆的准确添加.色浆的称取之前,最好是用苯乙烯稀释成1%浓度的稀色浆密封,待用。
这样可以比直接称取色浆来精确度提高百倍。
最合理的搅拌顺序依次是:树脂+促进剂搅拌+色浆搅拌+填料搅拌+固化剂搅拌。
成型过程中、砂光好的板材要避免阳光(紫外线)照射。
同样颜色的板子,固化剂和促进剂的投入量要相同,加固化剂后的搅拌时间也要相同,抽真空时间也要相同。
大搅拌罐里一次性搅拌几十张的料,每次出料之前,要适当地搅拌几转再出料。
原因是在一小时左右的时间里,大搅拌罐里会出现上下料之间轻微的比重失衡现象(沉淀)。
因为,有可能大搅拌罐下部位的混合料里粉料和颗粒多一些,上部位的混合料里色浆和树脂多一些。
人造石的优点人造大理石具有优良品质:它兼备了大理石的天然质感和坚固质地、陶瓷的光洁细腻和木材的易加工性,可加工成任何可设想的形状,能做到真正的无缝拼接;色彩丰富绚丽,其色彩采用天然色素,用天然色素做的台面色彩其稳定性好,光泽持久,不会褪色,既使是在长时间在烈日爆晒下其色彩也不会褪色;人造石没有任何毛细孔,霉菌、细菌及其它微生物无法生存,而且也不会被任何液体所渗透,很顽固的污渍可用清洁剂轻易去除。
相比天然石人造石具备的优点有:1.人造石更耐磨、耐酸、耐高温,抗冲、抗压、抗折、抗渗透等功能也很强。
其变形、黏合、转弯等部位的处理有独到之处;花色丰富,整体成型,并可反复打磨翻新。
因此抗污力强,因为表面没有孔隙,油污、水渍不易渗入其中,一般性的污渍可用湿布或清洁剂即可擦去;可任意长度无缝粘接,同材质的胶黏剂将两块粘接后打磨,浑然一体,接缝处毫无痕迹。
2.人造石的纹路和色彩丰富,完全可以和石材媲美。
石英石是一种全新的以天然石英结晶体矿为原料,由高达93%的石英结晶和7%的树脂聚合物、矿物材料、复合剂、填加剂在真空高温及机械压力下合成的,经过抛光工艺制成的装饰面材,是一种高硬度及环保的复合石英材料。
这种石英晶体本身具有晶莹剔透、清亮、色调美观、华贵、硬度高、不变形、不变色、韧性力强、无放射性、耐酸碱等自然特性,采用该原料制成的面材集天然石和人造石之优点于一身,比其他装修面材应用在厨房及浴室上更胜一筹,是最理想的装饰台面材料。
该产品具有以下特点:1、刮不花石英石的石英含量高达93%,而石英结晶是自然界中硬度仅次于钻石的天然矿产,其表面硬度高达摩氏7—8度,普遍高于一般的铁器的硬度,家庭使用的刀、铲、钢丝球等铁器都无法将其划伤、磨损,一般情况下,您可以在台面上随意放置各种家用物品(但要注意,避免用诸如钻石、砂纸、硬质合金等高硬度物品强力刮划台面)。
这是目前市面上任何一种橱柜台面材料都不具备的优点,可以说,石英石台面是没有售后服务的。
2、烫不坏金刚石台面的基材以天然的石英结晶为主,石英结晶是典型的耐火材料,而石英的熔点高达1300C,在添加了少量复合材料后,石英石表面仍然具有相当高的抗烫伤能力,它耐高温、不变形、表面不起翘,热锅或锅底脱落的热焦渣短时间不会使其表面熔化、变色或爆裂,也不会被从锅里溅出的热水或油渍等损坏,是目前除不锈钢以外抗温性最好的台面材料。
一般普通树脂板人造石台面经常会被烟头和锅底脱落的焦渣烫伤,而石英石台面完全具备抵抗这些烫伤的能力,并保持台面持久光洁。
3、污不染石英石中含有多种复合材料和超微石英粉,保证了材料具有很高水平的无微孔结构,板材表面和内部结构同样致密且均匀,吸水率低,平均只有0、03%,这就意味着该材料基本上没有渗透现象,一般厨房用的油、酱、醋、红酒、浓茶、果汁、咖啡、酸、碱等物质都不可能渗透,只要在每次使用之后能够用清水或中性洗涤剂将台面清洁干净,就不会有液体在台面上留下痕迹,顽固的滞留物仅需要使用清洁剂等即可祛除,不会渗透到材料内部,粘在台面上或者死角内的污垢还可以用铲或钢丝棉来清除,该产品的抗染污性是其他任何材料所无法比拟的。
4、用不旧虽然石英石的颜色相当多的成分是人工配制的,但其材料以矿物颜料为主,材料中含有高品质的复合剂以及昂贵的抗老化(UV)添加剂,使其具有很强的抗老化能力和抗褪色能力,在室内长期的日常生活使用过程中也不会因氧化、老化、腐蚀、热物接触等原因而致褪变色彩和光泽。
如果不在强日光下进行常年的局部对比照射,肉眼很难观察到色彩的变化,基本上可以认为是不褪色的材料。
5、无毒、无辐射石英石色彩主要由矿物颜料形成,它在人工合成之前的原料是颗粒状的,经过严格的选矿、洗矿和去杂提纯,不含重金属杂质,也就不存在放射性问题,是经国家建材认证为可以直接接触食品的无毒卫生材料。
人造石生产工艺流程图分析人造石实体面材的生产及发展前景人造石是以树脂为粘结剂,配以天然大理石或方解石、白云石、硅砂、玻璃粉等无机矿物粉料,以及适量的阻燃剂、稳定剂、颜料等,经配料混合、浇铸、真空成型、打磨抛光等成型固化及加工制成的一种人造石材。
实体面材人造石外观表面光洁,色彩美丽,具有一定的透明度;有足够的强度、刚度、硬度,耐冲击性、抗划痕性好;有耐气候老化,抗变形以及骤冷骤热性;由底至面实心一体,无毛细孔,不藏污纳垢,容易清理,历久常新;拼接无缝,表面光滑平顺;耐热、耐冷、耐腐蚀;可切割及加热弯曲,塑造各种不同形状。
人造石保留了天然石材的高贵、典雅气质,克服了天然石中常有的毛细孔、裂纹、色差、放射性等方面的缺陷,迅速成为国际流行的高档环保装饰材料。
实体面材按基体材料可分为丙烯酸类(pmma)和不饱和聚酯类(upr)两大类,国内企业普遍生产的为upr类。
upr类实体面材是由不饱和聚酯树脂与氢氧化铝或碳酸钙石粉复合而成,生产工艺为平板浇铸成型。
其生产主要工艺控制点:①树脂与填料的搭配和混合效果;②凝胶时间的控制;③真空排气泡效果;④固化温度与时间的控制;⑤后处理技术等。
人造石实体面材的生产及发展前景在石材的成型过程中,最重要也是基本的成型过程是树脂的固化,树脂从液态转变为固态的过程,这个过程可以在不通过加压和常温下完成,从化学原理上看,是从线型结构转变为体型结构的过程。
树脂经过固化反应后,液体树脂即变成固态的体型结构,不溶不熔的交联共聚物,并且有了一定的强度、硬度和韧性。
1、不饱和聚酯类实体面材的生产工艺生产聚酯石材的主要原料不饱和聚酯树脂是不饱和二元羧酸或它们与饱和二元羧酸组成的混合酸与多元醇缩聚而成的,具有酯键和不饱和双键的线型高分子化合物。
通常聚酯化缩聚反应是在190~220℃进行,直至达到预期的粘度。
在聚酯化缩聚反应结束后,趁热加入一定量的乙烯基单体,配成粘稠的液体,即人造石材的主要原料——面漆。
人造石是用面漆与色浆、颗粒、填料、颜料混合,经一定的加工程序制成的。
1.1实体面材浇注工艺流程图实体面材浇注工艺流程图点击此处查看全部新闻图片1.2工艺过程中的影响因素 1.2.1配料过程配料的过程中要注意各种原料的添加是否准确。
因为色浆加多加少会影响板材的底色,颗粒、填料、面漆都会影响到关键的工艺参数———粘度的高低,其中对色尤为重要,否则不能满足客户的要求,失去应用价值。
加入的填料通常为氢氧化铝,其与up树脂混合后制成的台板有玛瑙般的质感,调色后制品色泽鲜艳,受到消费者的青睐。
1.2.2脱泡过程由于在配料搅拌的过程中溶进了大量的气体,若不能排除产品内部的气泡,产品质量会受到影响,因此脱泡过程是非常重要的。
脱泡分为两步:一次脱泡和二次脱泡。
首先是一次脱泡,具体实施方法为在真空搅拌罐中,控制真空度为0.9~1mpa的条件下抽真空,在这种真空度下,微小气泡难以排净。
在此过程中,体系的粘度会因搅拌时间,反应时间的延长而增高,而粘度的高低会影响到板材的质量。
粘度太低会使颗粒沉淀,粘度太高会使气泡脱不干净使得原料聚合后产生大量的气孔。
倒料过程是将真空条件下脱泡完全的料注入模具的过程,在此过程中要注意控制倒料速度和拉模具的速度,避免出现色团和色分。
为了排除倒料过程中带入的空气,需要进行二次脱泡。
二次脱泡即振动架振动脱泡:该方法的使用应注意平台的振幅、频率及振动时间,振幅过大会使填料沉积到模板的表面,造成一面贫树脂,固化慢、收缩小,放热温度低;而另一面因富树脂,固化快,收缩慢,放热温度高,容易出现翘曲现象。
在这个工段振动的同时还要用刮板进行处理刚注入模具的料使其达到一定的水平度,便于后处理。
1.2.3固化过程固化过程是在烘箱中进行的,控制烘箱的温度是关键,而且环境温度的高低也是影响人造石板材制作的一个重要因素。
所以冬天和夏天的烘箱设定温度就有一定的差别,冬天环境温度较低聚合时间较长液体料增粘速度较慢,所以相应提高烘箱温度可以缩短聚合时间(大约40℃左右);夏天温度高粘度增得较快,要严格控制室内温度及烘箱温度防止板材出现质量上的问题。
从烘箱内出来的板材温度不可达到最高发热温度,否则板材就会出现弓翘、裂纹、龟纹等质量问题。
板材聚合的时间也要严格控制,过早会使板材有“水印”,当板材用压板玻璃压起来后由于板材并没有完全聚合,处在聚合后期,既要克服玻璃的压力又要克服自身的内应力就会出现细小的裂纹。
1.2.4脱模过程脱模过程是将板材从烘箱里取出并将其从模具中取出的过程。