注塑成型周期的最优化设置(成型技术)
注塑成型周期的最优化设置(成型技术)
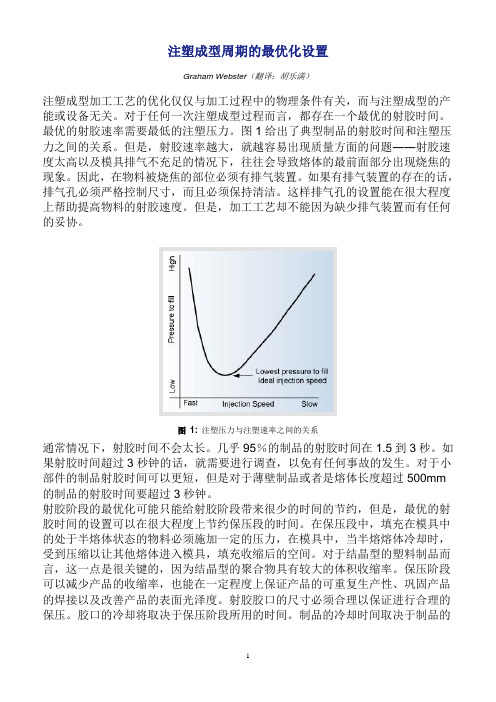
注塑成型周期的最优化设置Graham Webster(翻译:胡乐满)注塑成型加工工艺的优化仅仅与加工过程中的物理条件有关,而与注塑成型的产能或设备无关。
对于任何一次注塑成型过程而言,都存在一个最优的射胶时间。
最优的射胶速率需要最低的注塑压力。
图1给出了典型制品的射胶时间和注塑压力之间的关系。
但是,射胶速率越大,就越容易出现质量方面的问题――射胶速度太高以及模具排气不充足的情况下,往往会导致熔体的最前面部分出现烧焦的现象。
因此,在物料被烧焦的部位必须有排气装置。
如果有排气装置的存在的话,排气孔必须严格控制尺寸,而且必须保持清洁。
这样排气孔的设置能在很大程度上帮助提高物料的射胶速度。
但是,加工工艺却不能因为缺少排气装置而有任何的妥协。
图1:注塑压力与注塑速率之间的关系通常情况下,射胶时间不会太长。
几乎95%的制品的射胶时间在1.5到3秒。
如果射胶时间超过3秒钟的话,就需要进行调查,以免有任何事故的发生。
对于小部件的制品射胶时间可以更短,但是对于薄壁制品或者是熔体长度超过500mm的制品的射胶时间要超过3秒钟。
射胶阶段的最优化可能只能给射胶阶段带来很少的时间的节约,但是,最优的射胶时间的设置可以在很大程度上节约保压段的时间。
在保压段中,填充在模具中的处于半熔体状态的物料必须施加一定的压力,在模具中,当半熔熔体冷却时,受到压缩以让其他熔体进入模具,填充收缩后的空间。
对于结晶型的塑料制品而言,这一点是很关键的,因为结晶型的聚合物具有较大的体积收缩率。
保压阶段可以减少产品的收缩率,也能在一定程度上保证产品的可重复生产性、巩固产品的焊接以及改善产品的表面光泽度。
射胶胶口的尺寸必须合理以保证进行合理的保压。
胶口的冷却将取决于保压阶段所用的时间。
制品的冷却时间取决于制品的壁厚以及聚合物的类型。
这一点是很容易确定的,可以直接从数据表格中查到效应的数据或者可以通过利用CAE软件来做精确的确定。
在通常情况下,保压时间大概是冷却时间的80%,一般情况下,冷却时间要比设定的时间短。
塑料工程中的注塑成型工艺优化方法

塑料工程中的注塑成型工艺优化方法注塑成型是塑料工程中一种常用的加工方法,其优化方法对于提高产品质量、降低成本和提升生产效率至关重要。
本文将介绍塑料工程中的注塑成型工艺优化方法,帮助读者更好地理解和应用这些方法。
首先,优化注塑成型工艺的关键是选用合适的原料。
不同的塑料材料具有不同的熔化温度、流动性和收缩性等特性,因此在注塑成型之前需要根据产品要求选择合适的原料。
合适的原料能够保证产品的功能性能和外观质量,并且能够降低生产过程中的能耗和废料率。
其次,注塑成型的工艺参数调整对产品质量和生产效率都有着重要的影响。
例如,注塑温度的调整可以影响产品的缩水率和表面质量,过高或过低的温度都会导致产品瑕疵;注塑压力的调整可以控制产品的密实度和尺寸精度,过高的压力可能导致产品开裂,而过低的压力可能导致产品无法填充模腔。
因此,通过对注塑温度、注塑压力和冷却时间等参数的优化调整,可以达到最佳的成型效果。
此外,在注塑成型工艺中,模具的设计和制造也是很重要的一环。
合理的模具设计能够提高产品的质量和生产效率。
例如,增加模具的冷却系统可以加快产品的冷却速度,缩短成型周期;优化模腔和模芯的结构设计,可以减少产品的缩水率和变形。
因此,在进行注塑成型工艺优化时,需要注重模具的设计和制造,选择合适的模具材料和加工方式,以提高模具的寿命和使用效果。
此外,注塑成型过程中还应注意产品的后处理。
例如,对于高要求的产品,可以通过表面处理(如喷漆、打磨等)来提高产品的外观质量;对于某些产品,可以通过热处理或淬火等方法来改善产品的力学性能。
因此,了解并应用合适的后处理方法,可以满足不同产品的特定要求。
最后,注塑成型工艺优化还需要注重工艺参数的监控和调整。
通过对注塑机的监测和数据分析,可以实时了解工艺参数的变化和异常,及时调整以保证产品的质量和生产效率。
例如,通过定期维护注塑机,并进行设备清洁和润滑,可以减少设备故障和停机时间,提高生产效率。
总之,注塑成型工艺的优化是塑料工程中非常重要的一环。
精密注塑成型系统中注塑参数的优化设计
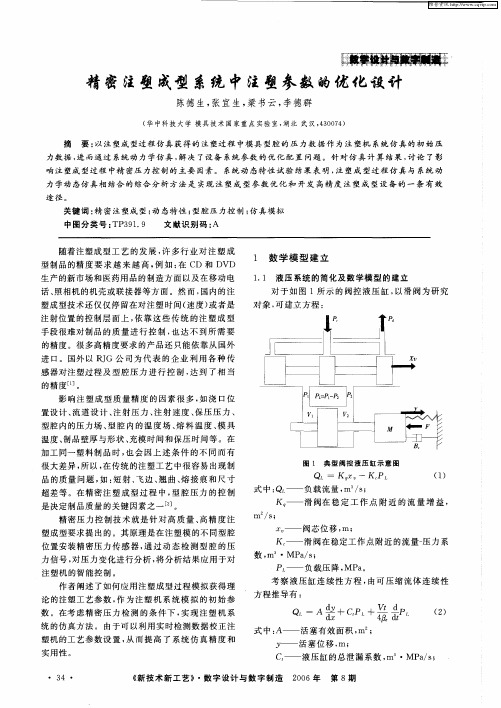
加工 同一塑 料制 品 时 , 也会 因上 述 条件 的不 同而 有 很大 差异 , 以 , 所 在传 统 的注 塑工艺 中很容 易出 现制 品 的质量 问 题 , : 射 、 如 短 飞边 、 曲 、 接 痕和 尺 寸 翘 熔 超差 等 。在 精密 注 塑 成型 过 程 中 , 腔 压力 的控 制 型
— —
精密 压 力控 制技 术 就 是针 对 高 质 量 、 高精 度 注
塑成 型要求 提 出的 。其原理 是在 注塑 模 的不 同型腔
阀芯位 移 , ; r n
位 置安装精 密压 力 传 感 器 , 过 动 态 检 测 型腔 的压 通
力 信号 , 压力 变化 进行分 析 , 分析 结果 应用 于对 对 将 注 塑机 的智 能控 制 。
厂 ]
1
r—————_ 1
影 响 注 塑成 型质 量 精 度 的 因素 很 多 , 浇 口位 如
置设 计 、 流道 设计 、 注射 压 力 、 射 速度 、 压 压 力 、 注 保
型腔 内的压 力场 、 腔 内的温 度 场 、 料 温 度 、 具 型 熔 模 温度 、 制品 壁厚 与形状 、 充模 时间 和保 压时 间等 。在
的精度 。很 多高精 度要 求 的产 品还 只 能依靠从 国外 进 口 。国外 以 R G公 司为 代 表 的企 业 利 用 各 种 传 J
感 器对 注塑过 程及 型 腔 压力 进 行 控 制 , 到 了相 当 达
的精度u 。 j
【 r● 厂 ]_ — -
I
厂 — ]
广—————]
是决 定制 品质量 的关 键 因素 之一 [ 。 2 ]
图 1 典 型 阀控 液 压 缸 示 意 图
QL— K。 一 K z PL
第43:注塑成型条件设定方法

第43问注塑成型条件设定方法一、开合模参数的设定方向:连续生产中,必须考虑工艺在今后生产中的稳定性,所以,开关模的参数设定必须保证开合模动作平稳设备不晃荡。
在产品取出方便的条件下,开关模位置越短越好。
低压保护设定,保证产品在模腔里合模起不到高压而报警,确保模具不会被压坏;高压锁模力最好设定低些,保证PL面不出披锋为止;设定太高,相反会有一定的坏处。
锁模力太高,易损坏模具;PL面排气不良,产品易困气烧焦;产品内应力大,出模后才可弃放;影响产品尺寸等。
具体的设定技巧:1.合模参数设定:以高压、慢速起步,短行程;中压、快速运行,导柱惯性到导套前;低压、匀速靠近腔面前;微压、低速惯性接触母模;高压、中速起高压合模。
有行位的模具,开模速度不可太快;2.开模参数设定:以高压、慢速离开母模;中压、快速运行惯性至终点前;高压、低速到开模终点。
3.低压保护位置与低压压力值的设定:接触模具的低压、低速设定必须能推动模具(特别是有弹簧或有行位的模具),但力量不能大于压坏产品的力(产品厚度被压至到原来的4/5所需要的力量);低压保护要调好,因为新模成品的形状与脱模情况不太了解;有抽蕊以及绞芽的模具,要先行手动试验,功能正常后方可用自动;4.高压锁模位置与高压锁模力的设定:高压位置设定方法。
(先不设定高压锁模力值,用前面设定的所有参数合模,模具会停在一个位置上,显示位置值将是实际的高压位置,在这位置上加上0.5㎜~1㎜就行)。
确认合模力是否充足:合模力(g)≥成形面投影面积(cm²)×模具内的平均压力(通常为400kg/cm²)。
合模力的大小计算可按《合模力设定方法》进行。
直压式机台需注意锁模力是否足够,肘节式机台注意十字头是否伸直,以防射出时模具后退,而出现大毛边涨坏模具;锁模力设定依据:最小锁模力=最高射出压力×(产品的投影面积+流道的投影面积);实际锁模力=最小锁模力×(1+5%~20%),再慢慢加到不出现毛边为止,闭模到30~50mm时,速度要转为慢速。
注射成型条件设定的最优化

模温的测量:冷却剂进口温度的测量 冷却剂出口温度的测量 模具金属温度的测量
31
加工问题(潮气)
潮气:潮气会在模腔或模芯表面产生,由于外
部的湿气温度比模腔表面温度高,遇冷 凝结成潮气。 影响:使塑料制件表面产生麻点,斜孔,或者 金属被腐蚀。
32
加工问题(锁模力)
锁模力:是由于机器上的气杆绷紧,产生锁
控制面板的监控 重点:关于控制面板的监控内容中,主要的参数
设定有温度,时间,位置与压力等,其中最为重要 的就是温度(温度读数)。
温度读数主要有起始设定温度与实际温度。 在控制面板中一般会将起始设定温度与实际温 度显示在一起,供模具工参照比较以及调整, 在实际操作中起始设定温度与实际温度存在一 定的差别。
1、安全步骤 设备:
安全套 安全手套及安全鞋 栓上长的头发 不要穿戴宽松的衣物
机械检查: 机械检查(检查安全是否在正确
位置以及功能是否正常)
6
一、最佳化射出成形操作的方法
2、注塑机的注塑循环
塑件
冷却固 化
冲模
加热 熔融
注塑 机料 筒
颗粒 、粉 状塑 料
7
一、最佳化射出成形操作的方法
3、预先准备的步骤
11
控制内容
填充速度曲线 转压点 补压及保压 开模及关模时间
12
四、维持最佳效率 解决程序中的问题
13
两大问题
两大问题 控制面板的监控 加工问题
14
控制面板的监控 控制面板的监控:控制面板主要用于操作参
数
的设定以及结果的数据的
显 示。
监 控 内 容
喷嘴区的温度
注入的时间
循环时间 软垫的尺寸
注塑成型技术篇――如何有效缩短成型周期提高生产效率?
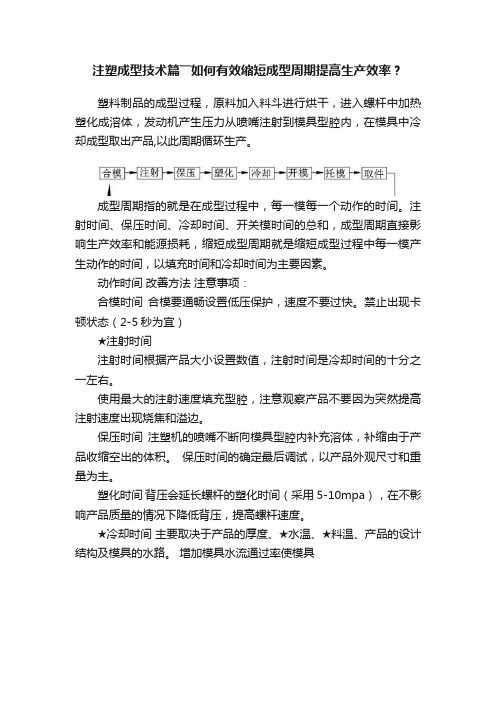
注塑成型技术篇――如何有效缩短成型周期提高生产效率?塑料制品的成型过程,原料加入料斗进行烘干,进入螺杆中加热塑化成溶体,发动机产生压力从喷嘴注射到模具型腔内,在模具中冷却成型取出产品,以此周期循环生产。
成型周期指的就是在成型过程中,每一模每一个动作的时间。
注射时间、保压时间、冷却时间、开关模时间的总和,成型周期直接影响生产效率和能源损耗,缩短成型周期就是缩短成型过程中每一模产生动作的时间,以填充时间和冷却时间为主要因素。
动作时间改善方法注意事项:合模时间合模要通畅设置低压保护,速度不要过快。
禁止出现卡顿状态(2-5秒为宜)★注射时间注射时间根据产品大小设置数值,注射时间是冷却时间的十分之一左右。
使用最大的注射速度填充型腔,注意观察产品不要因为突然提高注射速度出现烧焦和溢边。
保压时间注塑机的喷嘴不断向模具型腔内补充溶体,补缩由于产品收缩空出的体积。
保压时间的确定最后调试,以产品外观尺寸和重量为主。
塑化时间背压会延长螺杆的塑化时间(采用5-10mpa),在不影响产品质量的情况下降低背压,提高螺杆速度。
★冷却时间主要取决于产品的厚度、★水温、★料温、产品的设计结构及模具的水路。
增加模具水流通过率使模具大众新朗逸后灯总成降温和降低塑料的塑化温度(塑化温度过低会导致填充时流动性变差和不能完全熔融)。
开模时间开模速度不要太快,原则:慢—快—慢,开模不能卡顿,保持通畅(2-5秒为宜)脱膜时间包含公模吹气和托膜延迟,提高托膜压力和速度和托模进延时,托膜退延时。
不能因为过快导致产品龟裂和顶白。
大型四色成型饰圈取件时间缩短机械手的引拔时间,吸取时间,抱取时间,翻平时间,橫出时间所产生的动作。
不宜过快加剧机械手使用寿命和人身安全造成隐患。
注塑成型工艺介绍与参数设定

注塑成型工艺介绍与参数设定注塑成型工艺介绍与参数设定立式注塑成型机外观图卧式注塑成型机外观图常见塑料的成型材料方法介绍(透明料的注塑、PC、PC+ABS料的注塑、TPU的注塑、PP料的注塑)透明料的注塑成型1、常用透明原料的特性透明塑料由于透光率要高,必然要求塑料制品表面质量要求严格,不能有任何斑纹、气孔、泛白、雾晕、黑点、变色、光泽不佳等缺陷,因而在整个注塑过程对原料、设备、模具、甚至产品的设计,都要十分注意和提出严格甚至特殊的要求。
其次由于透明塑料多为熔点高、流动性差,因此为保证产品的表面质量,往往要在较高温度、注射压力、注射速度等工艺参数作细微调整,使注塑料时既能充满模,又不会产生内应力而引起产品变形和开裂。
由于透明塑料多为熔点高、流动性差,因此为保证产品的表面质量,往往要在较高温度、注射压力、注射速度等工艺参数作细微调整,使注塑料时既能充满模,又不会产生内应力而引起产品变形和开裂。
2、工艺方面应注意的问题为了减少内应力和表面质量缺陷,在注塑工艺方面应注意以下几方面的问题。
1)注射温度在塑料树脂不分解的前提下,宜用较高注射湿度;2)注射压力:一般较高,以克服熔料粘度大的缺陷,但压力太高会产生内应力造成脱模因难和变形;3)注射速度:在满足充模的情况下,一般宜低,最好能采用慢-快-慢多级注射;?4)保压时间和成型周期:在满足产品充模,不产生凹陷、气泡的情况下;宜尽量短,以尽量减低熔料在机筒停留时间;5)螺杆转速和背压:在满足塑化质量的前提下,应尽量低,防止产生解降的可能;?6)模具温度:制品的冷却好坏,对质量影响极大,所以模温一定要能精确控制其过程,有可能的话,模温宜高一些好。
7)由于为要防上表面质量恶化,一般注塑时尽量少用脱模剂;当用回用料时不得大于20%3、常用透明原料的注塑工艺注塑除了以上的共同问题,透明塑料亦各有一些工艺特性,现分述如下:1、PMMA粘度大,流动性稍差,因此必须高料温、高注射压力注塑才行,其中注射温度的影响大于注射压力,但注射压力提高,有利于改善产品的收缩率。
注塑成型工艺参数的设置及其调整方法

注塑成型工艺参数的设置及其调整方法注塑成型工艺参数的设置及其调整方法一、注塑注塑成型工艺流程成型工艺流程成型工艺流程可以简单的表示如下可以简单的表示如下可以简单的表示如下::上一周期——闭模——填充——保压——回胶——冷却——开模——脱模——下一周期在填充保压降段,模腔压力随时间推移而上升,填充满型腔之后压力将保持在一个相对静态的状态,以补充由于收缩而产生的胶量不足,另外此压力可以防止由于注射的降低而产生的胶体倒流现象,这就是保压阶段,保压完了之后模腔压力逐渐下降,并随时间推移理论上可以降到零,但实际并不为零,所以脱模之后制品内部内存内应力,因而有的产品需经过后处理,清除残存应力。
所谓应力,就是来傅高子链或者链段自由运动的力,即弯曲变形,应力开裂、缩孔等。
二、注塑注塑成型成型成型的主要参数的主要参数1、料筒温度注塑胶料温度,熔体温度对熔体的流动性能起主要作用,由于塑胶没有具体的熔点,所谓熔点是一个熔融状态下的温度段,塑胶分子链的结构与组成不同,因而对其流动性的影响也不同,刚性分子链受温度影响较明显,如PC 、PPS 等,而柔性分子链如:PA 、PP 、PE 等流动性通过改变温度并不明显,所以应根据不同的材料来调校合理的注塑温度。
2、注射速度注射速度是熔体在炮筒内(亦为螺杆的推进速度)的速度(MM/S )注射速度决定产品外观、尺寸、收缩性,流动状况分布等,一般为先慢——快——后慢,即先用一个较的速度是熔体更过主流道,分流道,进浇口,以达到平衡射胶的目的,然后快速充模方式填充满整个模腔,再以较慢速度补充收缩和逆流引起的胶料不足现象,直到浇口冻结,这样可以克服烧焦,气纹,缩水等品质不良产生。
3、注射压力注射压力是熔体克服前进所需的阻力,直接影响产品的尺寸,重量和变形等,不同的塑胶产品所需注塑压力不同,对于象PA 、PP 等材料,增加压力会使其流动性显著改善,注射压力大小决定产品的密度,即外观光泽性。
4、模具温度模具温度,有些塑胶料由于结晶化温度高,结晶速度慢,需要较高模温,有些由于控制尺寸和变形,或者脱模的需要,要较高的温度或较低温度,如PC 一般要求60度以上,而PPS 为了达到较好的外观和改善流动性,模温有时需要160度以上,因而模具温度对改善产品的外观、变形、尺寸,胶模方面有不可抵估的作用。
- 1、下载文档前请自行甄别文档内容的完整性,平台不提供额外的编辑、内容补充、找答案等附加服务。
- 2、"仅部分预览"的文档,不可在线预览部分如存在完整性等问题,可反馈申请退款(可完整预览的文档不适用该条件!)。
- 3、如文档侵犯您的权益,请联系客服反馈,我们会尽快为您处理(人工客服工作时间:9:00-18:30)。
注塑成型周期的最优化设置
Graham Webster(翻译:胡乐满)
注塑成型加工工艺的优化仅仅与加工过程中的物理条件有关,而与注塑成型的产能或设备无关。
对于任何一次注塑成型过程而言,都存在一个最优的射胶时间。
最优的射胶速率需要最低的注塑压力。
图1给出了典型制品的射胶时间和注塑压力之间的关系。
但是,射胶速率越大,就越容易出现质量方面的问题――射胶速度太高以及模具排气不充足的情况下,往往会导致熔体的最前面部分出现烧焦的现象。
因此,在物料被烧焦的部位必须有排气装置。
如果有排气装置的存在的话,排气孔必须严格控制尺寸,而且必须保持清洁。
这样排气孔的设置能在很大程度上帮助提高物料的射胶速度。
但是,加工工艺却不能因为缺少排气装置而有任何的妥协。
图1:注塑压力与注塑速率之间的关系
通常情况下,射胶时间不会太长。
几乎95%的制品的射胶时间在1.5到3秒。
如果射胶时间超过3秒钟的话,就需要进行调查,以免有任何事故的发生。
对于小部件的制品射胶时间可以更短,但是对于薄壁制品或者是熔体长度超过500mm
的制品的射胶时间要超过3秒钟。
射胶阶段的最优化可能只能给射胶阶段带来很少的时间的节约,但是,最优的射胶时间的设置可以在很大程度上节约保压段的时间。
在保压段中,填充在模具中的处于半熔体状态的物料必须施加一定的压力,在模具中,当半熔熔体冷却时,受到压缩以让其他熔体进入模具,填充收缩后的空间。
对于结晶型的塑料制品而言,这一点是很关键的,因为结晶型的聚合物具有较大的体积收缩率。
保压阶段可以减少产品的收缩率,也能在一定程度上保证产品的可重复生产性、巩固产品的焊接以及改善产品的表面光泽度。
射胶胶口的尺寸必须合理以保证进行合理的保压。
胶口的冷却将取决于保压阶段所用的时间。
制品的冷却时间取决于制品的
壁厚以及聚合物的类型。
这一点是很容易确定的,可以直接从数据表格中查到效应的数据或者可以通过利用CAE软件来做精确的确定。
在通常情况下,保压时间大概是冷却时间的80%,一般情况下,冷却时间要比设定的时间短。
冷却的速率与温度和时间之间存在这一个指数关系。
比率是不断下降的。
提高成型时的温度能减少冷却时需要的时间(见图2)。
研究表明:注塑设备中冷却时间的设定往往时通过试验来确定的。
当然,这个过程中的循环时间还包括固定设备上的时间,如果各个参数都是很固定的话,也可以在一定的程度上减少加工周期。
图2:冷却时间与注塑温度成指数关系
通常情况下,影响循环周期最坏的因素是模具的冷却,原因不是温度的问题,往往是缺少冷冻剂的问题。
关于模具冷却方面的问题存在着很多的误解。
事实上,所有的金属的传导率比一般塑料制品的要高200倍。
塑料将很容易地将热传递给金属,但是,往往要以同样的速度从模具中得到热量,而且将冷冻剂输入到每个冷却管道里是一件很困难的事情。
了解冷冻剂是否已经流入到没给冷却通道里是一件很重要的事情。
通常情况下,冷却管道是平行的,在很多的情况下,有的冷却管道很难获得冷却剂。
因此,将所有的冷却管道做成一个整体的系统可能是一种最好的解决办法。
冷冻剂温度的提高将会推动冷冻剂在整个冷却管道中的流动。
从模具中取出制品也是很费时的一个过程。
在一般的情况下,不考虑制品尺寸,整体型的制品一般要花5秒钟的时间将制品从模具中取出,对于分开注塑的部件,得花8秒钟的时间取出,然后再装成整体的制品。
如果不能保证这些时间的话,就证明设备各个参数设计的不合理。
所有的制品从模具中取出来的这个过程应该时可以控制的,速度可以增加,也可以减小,以获得最优化的循环时间。
一般的,机械手能很好地控制这一点。
注塑过程中生产周期的最优话会再很大程度上降低生产成本和提高生产效率。
大多数的产品离最优化的生产具有很大的距离,实际上,很多产品的注塑成型周期能缩短10%-30%。