线束基础知识与设计开发流程及工艺 V1
线束工艺流程
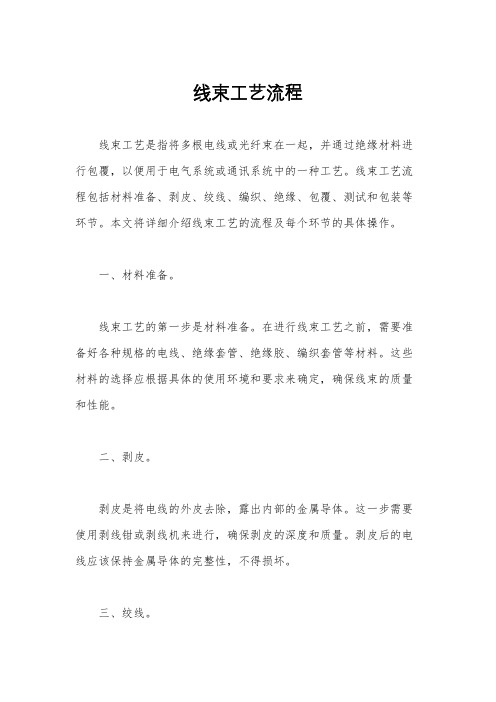
线束工艺流程线束工艺是指将多根电线或光纤束在一起,并通过绝缘材料进行包覆,以便用于电气系统或通讯系统中的一种工艺。
线束工艺流程包括材料准备、剥皮、绞线、编织、绝缘、包覆、测试和包装等环节。
本文将详细介绍线束工艺的流程及每个环节的具体操作。
一、材料准备。
线束工艺的第一步是材料准备。
在进行线束工艺之前,需要准备好各种规格的电线、绝缘套管、绝缘胶、编织套管等材料。
这些材料的选择应根据具体的使用环境和要求来确定,确保线束的质量和性能。
二、剥皮。
剥皮是将电线的外皮去除,露出内部的金属导体。
这一步需要使用剥线钳或剥线机来进行,确保剥皮的深度和质量。
剥皮后的电线应该保持金属导体的完整性,不得损坏。
三、绞线。
绞线是将多根电线按照一定的规则进行捆绑和绞合,使其成为一个整体。
这一步需要根据具体的线束设计要求进行操作,确保电线之间的布局合理、紧凑,并且不会相互干扰。
四、编织。
编织是将绞好的电线进行编织,以增强线束的抗拉强度和耐磨性。
编织材料可以是尼龙布、聚酯布等,根据具体的使用要求来选择。
编织后的线束应该外观整齐、紧密,不得有松散或交叉现象。
五、绝缘。
绝缘是为了保护线束中的电线不受外界环境的影响,使用绝缘套管或绝缘胶对电线进行包覆。
绝缘材料的选择应根据使用环境的温度、湿度等因素来确定,确保绝缘效果良好。
六、包覆。
包覆是将整个线束进行最终的包覆,通常使用PVC套管或热缩套管进行包覆。
包覆后的线束应该外观整洁、无气泡、无皱纹,确保线束的外观质量。
七、测试。
测试是对线束进行电学和机械性能的检测,确保线束的质量和性能达到要求。
电学测试包括导通测试、绝缘电阻测试等,机械性能测试包括拉力测试、耐磨测试等。
八、包装。
最后一步是将测试合格的线束进行包装,通常使用塑料袋或纸箱进行包装。
包装后的线束应该标明产品型号、规格、生产日期等信息,确保产品的追溯和售后服务。
以上就是线束工艺的流程及每个环节的具体操作。
通过严格的工艺流程和质量控制,可以生产出质量可靠的线束产品,满足不同领域的使用需求。
线束开发流程及作业内容
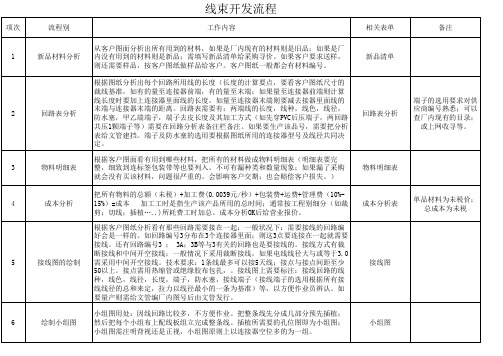
产品图
产品图的1:1尺寸需 要用尺实际测量;以 防有误差
8 9 10 11 12 13 14
作业标准书作成 端子压着模具的开发 检具的开发 设备的评估 设备制作 样线试做 新品送样
作业标准书 C表 C表 C表
15
APQP规划
有一些项目是需要其 他部门协助完成。见 程序书
16
PPAP
需要评估厂商协助采购生技纳入c表12设备制作协助生技配线板导通台的制作13样线试做将分析ok的资料交生技并协助生技样线试做14新品送样样品完成后送给品保做送样资料资料以客户需求为主如检查成绩书sgs报告及实验报告等
线束开发流程
项次 流程别 工作内容 从客户图面分析出所有用到的材料,如果是厂内现有的材料则是旧品;如果是厂 内没有用到的材料则是新品;需填写新品清单给采购寻价。如果客户要求送样, 则还需要样品,按客户图纸做样品给客户。客户图纸一般都会有材料编号。 根据图纸分析出每个回路所用线的长度(长度的计算要点,要看客户图纸尺寸的 裁线基准,如有的量至连接器前端,有的量至末端;如果量至连接器前端则计算 线长度时要加上连接器里面线的长度。如量至连接器末端则要减去接器里面线的 末端与连接器末端的距离。回路表需要有:两端线的长度,线种,线色,线径, 防水塞,甲乙端端子,端子去皮长度及其加工方式(如先穿PVC后压端子,两回路 共压1颗端子等)需要在回路分析表备注栏备注。如果要生产该品号,需要把分析 表给文管建挡。端子及防水塞的选用要根据图纸所用的连接器型号及线径共同决 定。 根据客户图面看有用到哪些材料,把所有的材料做成物料明细表(明细表要完 整,细致到连标签包装带等也要列入。不可有漏种类和数量现象;如果漏了采购 就会没有买该材料,问题很严重的。会影响客户交期;也会赔偿客户损失。) 把所有物料的总额(未税)+加工费(0.0039元/秒)+包装费+运费+管理费(10%15%)=成本 加工工时是指生产该产品所用的总时间;通常按工程别细分(如裁 剪;切线;插植…..)所耗费工时加总。成本分析OK后给营业报价。 根据客户图纸分析看有那些回路需要接在一起;一般状况下:需要接线的回路编 好会是一样的。如回路编号3分布在3个连接器里面;则这3点要连接在一起就需要 接线。还有回路编号3 ; 3A;3B等与3有关的回路也是要接线的。接线方式有裁 断接线和中间开空接线;一般情况下采用裁断接线,如果电线线径大与或等于3.0 需采用中间开空接线。技术要求:1条线最多可以接5天线;接点与接点间距至少 50以上。接点需用热缩管或绝缘胶布包扎,。接线图上需要标注:接线回路的线 种,线色,线径,长度,端子,防水塞,接线端子(接线端子的选用根据所有接 线线径的总和来定,拉力以线径最小的一条为基准)等,以方便作业员辨认。如 要量产则需给文管编厂内图号后由文管发行。 小组图用处:因线回路比较多,不方便作业。把整条线先分成几部分预先插植; 然后把每个小组布上配线板组立完成整条线。插植所需要的孔位图即为小组图; 小组图需注明背视还是正视,小组图原则上以连接器空位多的为一组。 相关表单 备注
线束制作的流程范文
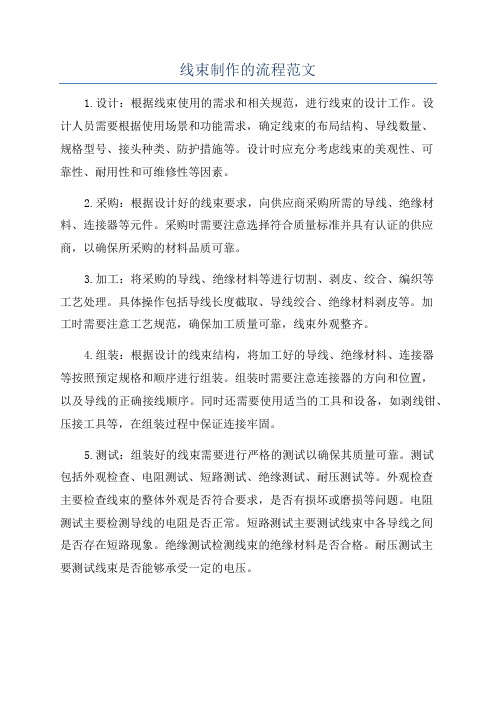
线束制作的流程范文1.设计:根据线束使用的需求和相关规范,进行线束的设计工作。
设计人员需要根据使用场景和功能需求,确定线束的布局结构、导线数量、规格型号、接头种类、防护措施等。
设计时应充分考虑线束的美观性、可靠性、耐用性和可维修性等因素。
2.采购:根据设计好的线束要求,向供应商采购所需的导线、绝缘材料、连接器等元件。
采购时需要注意选择符合质量标准并具有认证的供应商,以确保所采购的材料品质可靠。
3.加工:将采购的导线、绝缘材料等进行切割、剥皮、绞合、编织等工艺处理。
具体操作包括导线长度截取、导线绞合、绝缘材料剥皮等。
加工时需要注意工艺规范,确保加工质量可靠,线束外观整齐。
4.组装:根据设计的线束结构,将加工好的导线、绝缘材料、连接器等按照预定规格和顺序进行组装。
组装时需要注意连接器的方向和位置,以及导线的正确接线顺序。
同时还需要使用适当的工具和设备,如剥线钳、压接工具等,在组装过程中保证连接牢固。
5.测试:组装好的线束需要进行严格的测试以确保其质量可靠。
测试包括外观检查、电阻测试、短路测试、绝缘测试、耐压测试等。
外观检查主要检查线束的整体外观是否符合要求,是否有损坏或磨损等问题。
电阻测试主要检测导线的电阻是否正常。
短路测试主要测试线束中各导线之间是否存在短路现象。
绝缘测试检测线束的绝缘材料是否合格。
耐压测试主要测试线束是否能够承受一定的电压。
6.包装:经过测试合格的线束需要进行包装,以保护其不受外界环境的干扰和损坏。
包装时需要使用恰当的包装材料,如泡沫箱、缠绕胶带等,以确保线束运输过程中的安全性。
以上就是线束制作的大致流程,从设计到包装的每一步都需要精细操作以确保线束质量的可靠性和稳定性。
只有在每个环节都进行严格的把控,线束才能满足使用者的需求,并具有良好的性能和可靠性。
汽车线束设计基础知识
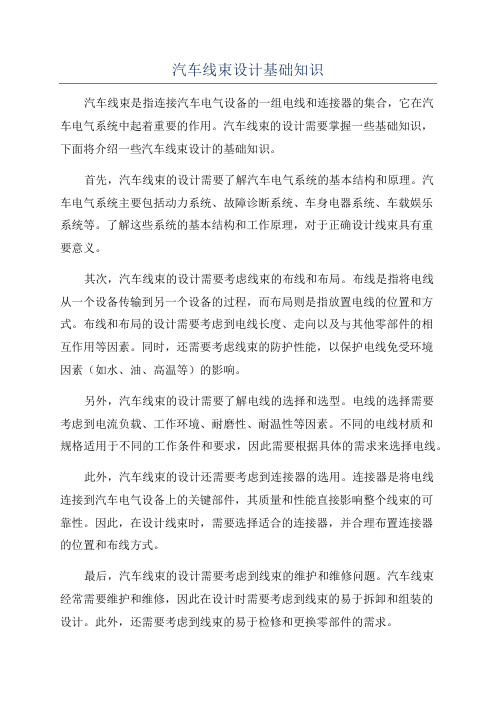
汽车线束设计基础知识汽车线束是指连接汽车电气设备的一组电线和连接器的集合,它在汽车电气系统中起着重要的作用。
汽车线束的设计需要掌握一些基础知识,下面将介绍一些汽车线束设计的基础知识。
首先,汽车线束的设计需要了解汽车电气系统的基本结构和原理。
汽车电气系统主要包括动力系统、故障诊断系统、车身电器系统、车载娱乐系统等。
了解这些系统的基本结构和工作原理,对于正确设计线束具有重要意义。
其次,汽车线束的设计需要考虑线束的布线和布局。
布线是指将电线从一个设备传输到另一个设备的过程,而布局则是指放置电线的位置和方式。
布线和布局的设计需要考虑到电线长度、走向以及与其他零部件的相互作用等因素。
同时,还需要考虑线束的防护性能,以保护电线免受环境因素(如水、油、高温等)的影响。
另外,汽车线束的设计需要了解电线的选择和选型。
电线的选择需要考虑到电流负载、工作环境、耐磨性、耐温性等因素。
不同的电线材质和规格适用于不同的工作条件和要求,因此需要根据具体的需求来选择电线。
此外,汽车线束的设计还需要考虑到连接器的选用。
连接器是将电线连接到汽车电气设备上的关键部件,其质量和性能直接影响整个线束的可靠性。
因此,在设计线束时,需要选择适合的连接器,并合理布置连接器的位置和布线方式。
最后,汽车线束的设计需要考虑到线束的维护和维修问题。
汽车线束经常需要维护和维修,因此在设计时需要考虑到线束的易于拆卸和组装的设计。
此外,还需要考虑到线束的易于检修和更换零部件的需求。
综上所述,汽车线束的设计需要掌握汽车电气系统的基本结构和原理,了解线束的布线和布局原则,选择适合的电线和连接器,并考虑到线束的维护和维修问题。
通过合理的设计,可以确保汽车线束具有良好的性能和可靠性,提高汽车电气系统的工作效率和安全性。
线束工艺流程
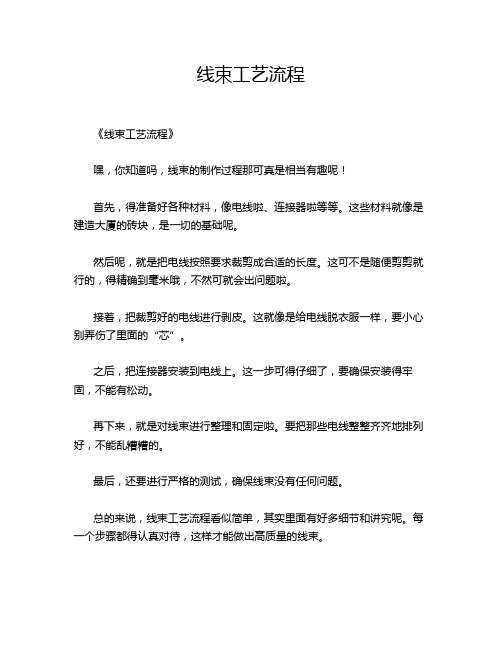
线束工艺流程
《线束工艺流程》
嘿,你知道吗,线束的制作过程那可真是相当有趣呢!
首先,得准备好各种材料,像电线啦、连接器啦等等。
这些材料就像是建造大厦的砖块,是一切的基础呢。
然后呢,就是把电线按照要求裁剪成合适的长度。
这可不是随便剪剪就行的,得精确到毫米哦,不然可就会出问题啦。
接着,把裁剪好的电线进行剥皮。
这就像是给电线脱衣服一样,要小心别弄伤了里面的“芯”。
之后,把连接器安装到电线上。
这一步可得仔细了,要确保安装得牢固,不能有松动。
再下来,就是对线束进行整理和固定啦。
要把那些电线整整齐齐地排列好,不能乱糟糟的。
最后,还要进行严格的测试,确保线束没有任何问题。
总的来说,线束工艺流程看似简单,其实里面有好多细节和讲究呢。
每一个步骤都得认真对待,这样才能做出高质量的线束。
整车线束设计开发流程

整车线束设计开发流程整车线束设计开发是指在整车设计中,针对整车电气系统的需求,进行线束的设计和开发。
线束是各个电气设备之间传递信号和电能的通道,它的设计和开发对整车的性能和可靠性有着重要的影响。
下面将介绍整车线束设计开发的流程。
1.需求分析在整车线束设计开发的初期,需要对整车的电气系统进行需求分析。
通过与传感器、执行器和控制器等相关部门的沟通,了解整车电气系统的功能需求、信号传输要求和功率传输要求等。
还需要考虑整车的可维护性和可靠性等因素,为线束设计提供指导。
2.线束布置设计线束的布置设计是指将各个电气设备之间的线缆进行布置的过程。
首先需要确定线束的总体布局,确定线束走向、穿越路径和固定方式等。
然后根据线束的长度和电流负载等参数,选择线束的截面积和材料。
最后,进行线束的具体布置设计,确定线束的分支点和连接方式。
3.线束分配设计线束分配设计是指将整车电气系统中的信号和电能分配到各个线束上的过程。
需要根据各个电气设备之间的连接关系和信号传输要求,进行线束的分配。
同时,需要考虑线束的排布和连接的便捷性,以提高制造和维修的效率。
4.线束选型和采购线束选型和采购是指根据线束的设计要求,选择合适的线束品牌和型号,并进行采购。
在选型时,需要考虑线束的额定电流、电压和工作环境等要求,以确保线束的安全性和可靠性。
在采购时,需要与线束供应商进行沟通,了解线束的交货时间和质量保证等信息。
5.线束制造线束制造是指将线束设计方案制造成实际的线束产品的过程。
首先需要对线束进行裁剪,根据线束的长度和分支点的位置,将线束切割成合适的长度和形状。
然后需要进行线束的剥皮和绝缘处理,以确保线束的安全性和导电性。
最后,将线束上的连接器进行压接和固定,完成线束的制造。
6.线束安装和调试线束安装和调试是指将线束安装到整车上,并进行电气连接和功能测试的过程。
首先需要根据线束设计方案,将线束穿过整车的壳体,并进行固定。
然后进行线束的电气连接,将线束连接到相应的电气设备上。
线束的工艺流程
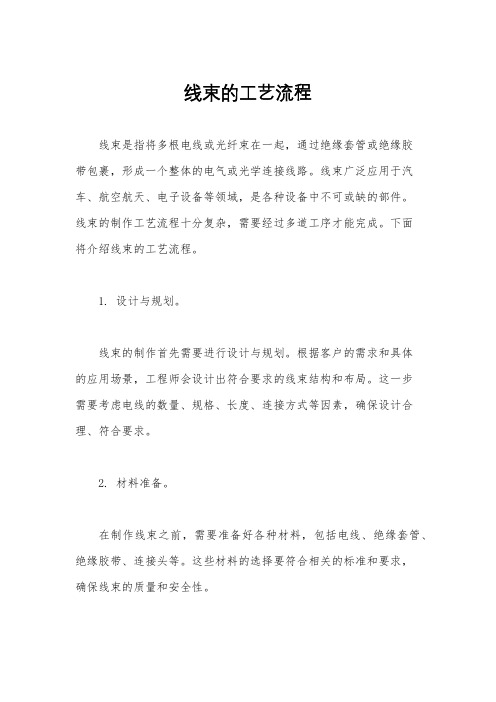
线束的工艺流程线束是指将多根电线或光纤束在一起,通过绝缘套管或绝缘胶带包裹,形成一个整体的电气或光学连接线路。
线束广泛应用于汽车、航空航天、电子设备等领域,是各种设备中不可或缺的部件。
线束的制作工艺流程十分复杂,需要经过多道工序才能完成。
下面将介绍线束的工艺流程。
1. 设计与规划。
线束的制作首先需要进行设计与规划。
根据客户的需求和具体的应用场景,工程师会设计出符合要求的线束结构和布局。
这一步需要考虑电线的数量、规格、长度、连接方式等因素,确保设计合理、符合要求。
2. 材料准备。
在制作线束之前,需要准备好各种材料,包括电线、绝缘套管、绝缘胶带、连接头等。
这些材料的选择要符合相关的标准和要求,确保线束的质量和安全性。
3. 剥线和组装。
接下来是剥线和组装的工序。
工人需要根据设计图纸和要求,将电线的外皮剥除,露出内部的金属导线。
然后根据设计要求,将各根电线按照一定的顺序和布局进行组装,通常会采用编织、捆扎或打包的方式进行组装。
4. 绝缘处理。
组装好的电线需要进行绝缘处理,以确保线束的安全性和耐用性。
这一步通常会采用绝缘套管或绝缘胶带进行包裹,同时需要进行压接或焊接等工艺处理,确保各根电线之间的连接牢固可靠。
5. 测试与检验。
制作完成的线束需要进行测试和检验,以确保质量合格。
通常会进行电气测试、耐压测试、绝缘测试等,确保线束符合相关的标准和要求。
6. 包装与出厂。
最后是线束的包装与出厂。
制作完成的线束会进行整理和包装,通常会采用盒装、托盘包装等方式进行包装,然后进行出厂检验,确保线束的质量符合要求后进行出厂。
通过以上工艺流程,线束的制作完成。
整个工艺流程需要严格按照标准和要求进行操作,确保线束的质量和安全性。
线束作为电气和光学连接的重要组成部分,在各种设备中发挥着重要的作用,其质量和稳定性直接关系到设备的性能和安全。
因此,制作线束的工艺流程非常重要,需要严格控制每一个环节,确保线束的质量和可靠性。
线束开发流程及作业内容

线束开发流程及作业内容线束开发是汽车电气系统中重要的一环,它涉及到汽车电器连接线的设计、开发和测试。
下面将介绍线束开发的流程及相关的作业内容。
一、线束开发流程1.需求分析阶段:在开始线束开发之前,首先需要进行需求分析。
这一阶段的目的是确定线束所要连接的电器设备以及线束的功能。
通过与汽车制造商、电器设备制造商以及其他相关团队的沟通,明确需求和要求,对线束进行初步的设计。
2.线束设计阶段:在线束设计阶段,根据需求分析的结果,进行线束的设计工作。
设计人员需要综合考虑线束的电气性能、机械性能以及可制造性等因素。
他们需要选取适当的线材、连接器、外壳等材料和部件,并进行线束布置、走向规划、连接关系设计等工作。
设计人员还需要制定相应的标准和规范,确保线束的可靠性和稳定性,满足汽车制造商的要求。
3.样品制作阶段:设计完成后,需要制作线束样品进行测试和验证。
样品的制作需要根据设计图纸进行,包括线束的剪切、剥皮、接插等工序。
在制作过程中,需要按照设计规范进行操作,确保线束的质量。
4.样品测试阶段:制作好的线束样品需要进行各项测试,包括电气性能测试、机械性能测试以及环境适应性测试等。
通过测试,验证线束的性能是否符合设计要求,是否满足汽车制造商的要求。
5.样品验证阶段:如果样品通过了测试,就可以进行样品的验证。
将样品应用到实际的汽车中,测试线束的可靠性和稳定性。
同时,还需要进行相关的安全性验证,确保线束的使用不会对汽车造成损坏或事故等意外情况。
6.量产阶段:线束通过了验证后,就可以进入量产阶段。
在量产阶段,需要根据实际需求进行大规模的线束生产。
这里涉及到材料采购、加工生产、质量控制等一系列工作。
7.售后服务阶段:线束投入市场后,需要进行售后服务。
这包括对线束进行监测和维修,确保线束的正常使用。
同时,还需要与汽车制造商和终端用户保持良好的沟通和合作,收集用户的反馈信息,以进一步改进线束的设计和性能。
二、线束开发的作业内容1.需求分析文档编写:根据与相关团队的沟通,编写线束需求分析文档,明确线束的功能和要求。
- 1、下载文档前请自行甄别文档内容的完整性,平台不提供额外的编辑、内容补充、找答案等附加服务。
- 2、"仅部分预览"的文档,不可在线预览部分如存在完整性等问题,可反馈申请退款(可完整预览的文档不适用该条件!)。
- 3、如文档侵犯您的权益,请联系客服反馈,我们会尽快为您处理(人工客服工作时间:9:00-18:30)。
3)环形端子/接线片 环形端子一般用于接地线,可适配的导线截面积可从0.35mm2到10mm2。 环形端子可以通过点锡或套热缩管来达到密封要求。 对于套筒式环形端子,压接后不需要点锡,可以套热缩管。 接线片一般用于起动机、发电机和稳压器的功率线以及蓄电池负极的接地,适配16、20和 25mm2的大截面导线。 不同的环形端子/接线片采用不同的拧紧力矩连接在车身螺柱或设备上。 接线片通常使用M8螺柱,环形端子使用M6螺柱进行电气连接。
P-C:母连接器,公连接器为P-L。 JPT:端子类型。 J :单线密封,通过密封塞+密封圈对尾部密封。 E:密封连接器。 9 :连接器孔位总数。 NR:连接器防插错颜色。 9636536080:连接器的PSA零件号。 INTERDIT… :辅助信息或固定卡零件号。
端子的镀层通常有镀锡、镀银和镀金,用于对振动、腐蚀有不同要求的场合。 大多数端子的镀层都为镀锡,此时在红框内的< >中为空或者为SN。 镀银的端子在DPCA还没有使用过,用< AG >表示。 镀金分为AU和AU40,AU表示可以承受25g的振动,AU40表示可以承受40g的高频振动。 线束连接器中的端子镀层与设备接口中的端子镀层应保持一致,否则会影响使用性能。
ห้องสมุดไป่ตู้
9)热缩管 热缩管的作用是进行绝缘和密封,并具有一定的机械保护作用。 热缩管分为带热熔胶和不带热熔胶两大类。 位于发动机舱内的接地环端/接线片压接后应增加热缩管,以进行密封保护。 位于座舱内的绞接点可以使用不带热熔胶的热缩管,以进行绝缘保护和机械保护。 位于发动机舱内的绞接点应使用带热熔胶的热缩管,以进行密封保护、绝缘保护和机械保护。
10)保险丝盒(保险丝/继电器) 集成在线束上的保险丝盒通常不带PCB板,如BSM MODULE 1(发动机舱8路保险丝盒), BFH5(座舱5路保险丝盒),BFH12(座舱12路保险丝盒),BFDB(蓄电池端起始保险丝 盒),MFRH(座舱保险丝和继电器模块),BFRM(发动机舱保险丝和继电器盒)等。 保险丝和继电器通常都带在保险丝盒和继电器盒上,也有部分集成在线束上,如TX3电动窗 升降系统、AAS系统、ALARME系统增加的继电器,B53、BX3警车、出租车线束上增加的保 险丝。 保险丝通常分为MINI、ATO、MAXI、MIDI这几种类型,容量有5A、7.5A、10A、15A、 20A、25A、30A、40A、50A、60A、70A、80A等。
1.2.2 接线片/环形端子
图纸表达方式同连接器。 G表示特软类绝缘层导线。 两根导线都在第1孔,表示双压。 接线片的PSA标准描述。 C:COSSE,环端或接线片 B:BATTERIE,蓄电池电 8:适配M8的螺柱 L:LAITON,原材料为黄铜 21:接触面的尺寸。 P3:接触面和压接面成90°角。
线束基础知识与设计开发流程及工艺
DMES/ELE/AEV Xia Mingchun 2015.11.27
目 录
一 线束基础知识
1.1 线束介绍 1.2 线束图纸介绍
1.3 线束2D设计步骤及案例分析 二 线束设计开发流程 2.1 线束设计流程 2.2 线束开发流程 三 线束制造工艺与常用文件 3.1 线束制造工艺
2)连接器/端子 连接器和端子需配合使用,每种连接器只能适配相应系列的端子类型。 同一类型的连接器根据防插错结构的差异可分为不同的颜色,防插错结构只是为 了装配考虑,不影响对接性能。 同一类型的端子有不同的压接翼,以适配不同导线截面。 端子在连接器孔位中的锁止一般分为2道,一次锁止由端子本身的结构决定,二 次锁止由连接器完成。 连接器的锁止可分为旋转杠杆式、抽拉卡箍式和搭扣式,部分要求更高的场合使 用的连接器还带有CPA锁止结构。 连接器的整体密封性需要连接器和设备接口的结构配合,连接器的尾部密封可分 为:通过连接器自带的密封垫/硅胶进行密封、在导线上增加密封圈进行密封、在 连接器上增加堵头对未使用的孔位进行密封。 连接器和端子可视为标准件,其主要的供应商有TYCO、MOLEX和DELPHI。 目前DPCA绝大部分都是使用PSA开发的产品,但是DPCA已经进行新的连接器 与端子开发工作,并在后续的自主品牌上进行使用。 并不是所有连接器都存在对接的连接器。
5)保护套管 线束上的保护套管主要作用是进行机械防护和降噪。 PVC管:一般机械防护。 对贴毛毡带:一般机械防护+降噪,主要用于座舱内。 袖套网管:中等机械防护+降噪,并保持线束分支的柔韧性,主要用于座舱内。 开缝波纹管:中等机械防护(高于袖套网管),主要用于发动机舱内。 降噪波纹管:中等机械防护+降噪,在开缝波纹管的表面覆盖有降噪材料,主要用于座舱内。 特殊波纹管:高等机械防护。有闭口波纹管、自闭合波纹管和双壳式波纹管等,以防止导线的 外露。 各种类型的保护套管都有不同的规格,以适配不同直径的线束分支,通常来说,线束分支的直 径不应超过套管内径的80%。 一般情况下,保护套管的一端或两端应用胶带缠绕固定在线束分支上,以防止套管的自由移动。
7)支架 支架用于固定线束或者保护线束(隔离潜在风险的零件,如发动机皮带和蓄电池等)。 支架主要分为金属支架和塑料支架两种。 金属支架:对于无油漆的各干燥区域,如果其边缘下垂并且无毛刺,进行镀锌就足够了。对于 各湿润区域(发动机舱、外部等),使用Z15 FNR (在不含氰化物的碱性槽里面完成纯锌镀层、 锌铁或锌钴合金镀层,镀层厚度最小为15um,无去氢处理,需要含3价铬的纯化,镀层厚度为黑 色,采用强化镀后处理)。 塑料支架:材料有PP(聚丙烯或者百折胶)、 PA6(聚酰胺6或者尼龙6)和PA66(聚酰胺66或 者尼龙66)等,质量要求塑料支架表面无飞边和无缩影等。 在进行支架平面布置设计时,支架与线束等环境件需要保证一个至少5至10mm的距离,以避免 CCP等风险。
3.2 线束工作中常用的文件
一、线束基础知识 1.1 线束介绍 1.1.1线束 线束是传输电信号和能量的媒介,是构建汽车电路的主体,是汽车的“神经网络”。线 束是由导线,连接器,端子,卡钉,保护覆盖物,支架,护套,保险丝盒(保险丝与继电器) 和热缩管等组成。它可以与电器设备进行快速连接与拆卸,以方便装配与返修。
2.2 线束开发流程 三 线束制造工艺与常用文件
3.1 线束制造工艺 3.2 线束工作中常用的文件
1.2 线束图纸介绍 1.2.1 连接器/端子
设备代码
设备名称
密封塞类型 节点编号 连接器描述 和零件号 分支尺寸(节点到 连接器末端的距离) 分支节点 1:连接器的孔位编号 7113:导线代码。与设备代码一样是唯一的,一个功能只有一个代码。 ND :导线颜色。一般只对地线定义颜色,ND表示未定义颜色。 B:导线绝缘层类型。B表示标准绝缘层厚度的PVC材料,C表示减薄绝缘层厚 度的PE材料。 00.50 :导线截面积 DDD02:Option code。不同的option code代表不同的功能。DDD02表示GEP 2:导线另一端所在连接器的孔位编号。 IC01:导线另一端所在连接器的设备代码。
8)护套 线束在穿过钣金孔时必须使用橡胶护套进行机械保护,同时还有防水密封的作用。 有些护套为纯橡胶件;而有些护套只是固定部分为塑料件,剩下部分为橡胶件。 护套固定在钣金孔或者金属/塑料支架上。 有些护套是用胶带缠绕或扎带固定在线束分支上,有些护套是直接和线束分支注塑在一起。 车门护套中的导线应该理顺,并且在长度上有一定余量,以避免车门运动过程中导线被扯断。 对于有防水要求的护套,穿过护套的线束分支上不能缠绕棉织胶带,以避免水顺着棉织胶带进 入干区。
11)集成零件 出于装配方面的考虑,某些零件会集成在线束上,然后通过线束总成装配到整车上,如: USB电缆、天线电缆、灯座和洗涤管等。 这些零件只是集成在线束上,由相关部门负责开发与认可。
目 录
一 线束基础知识
1.1 线束介绍 1.2 线束图纸介绍 1.3 线束2D设计步骤及案例分析 二 线束设计开发流程 2.1 线束设计流程
1
2
8 3 7 6 4
5
1:连接器 2:端子(接地) 3:卡钉 4:保护覆盖物 5:支架 6:护套 7:保险丝盒(保险丝与继电器) 8:热缩管
1.1.2线束类型 根据线束在整车上的安装位置的不同,线束可分为主线束,座舱线束,仪表板线束,门线 束,保险杠线束,发动机线束和正负极电缆等。
1.1.3线束组成 线束是由导线,连接器,端子,卡钉,保护覆盖物,支架,护套,热缩管,保 险丝盒等组成。 1)导线 DPCA使用的导线是PSA的原配供应商(ACOME、LEONI)在国内生产的产品,属 于法标导线。 通常所说的线径指的是导线的截面积,而导线截面积指的是导体部分(铜丝绞合 而成)的截面积,不包括绝缘层。 DPCA目前所使用的导线截面积有0.13、0.22、0.35、0.5、0.75、1.0、1.5、2.0、2.5、3.0、4.0、 5.0、6.0、7.0、10.0、16.0、20.0、25.0mm2,其中大于或等于16.0mm2以上的截面积一般用于蓄电 池电缆。PSA正在开发更小线径的导线。 导线绝缘层耐低温均为–40℃,根据耐高温的不同分为T1到T8,其温度分别为85,100,125,150 ,175,200,225,250 ℃。 导线可以承受一定时间的高一个等级的温度,例如对于标称温度等级为T2的导线,应该可以承受 3000小时的100 ℃以及240小时的125 ℃的耐高温试验。 PSA以及DPCA目前没有使用T1的导线。座舱内一般使用T2导线,发动机舱的主线束大部分使用 T2导线,局部使用T3导线。发动机线束大部分使用T3导线,局部使用T4或T6导线。 通过导线绝缘层表面上的符号来识别导线的供应商和耐温等级。比如导线上喷有3个连续的“* ”,则代表是ACOME生产的T3温度等级的导线(不同的导线供应商采用不同的符号)。 导线绝缘层表面上喷的数字/字母代表支路的编号,与线束图纸上定义的该支路的编号相同。 导线绝缘层的颜色在图纸上一般不做具体规定,但接地线强制为黄绿或绿黄色,预张紧器和安全 气囊为橙色或者黄色,美观件/外观件为黑色。