基于矩阵循环的智能RGV的动态调度策略
智能RGV的动态调度策略
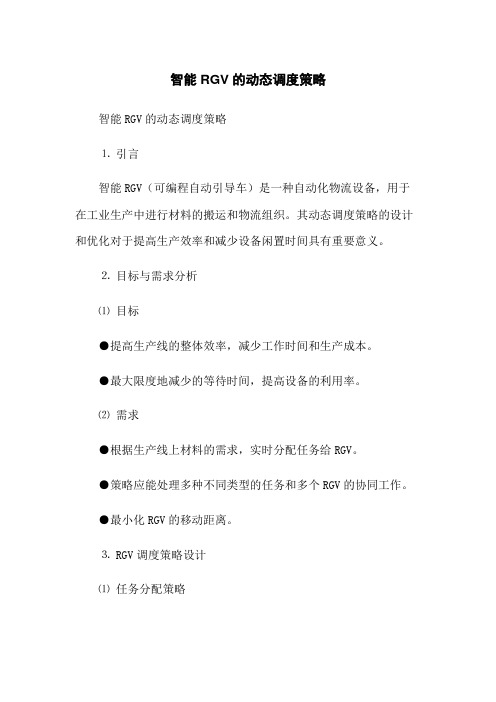
智能RGV的动态调度策略智能RGV的动态调度策略⒈引言智能RGV(可编程自动引导车)是一种自动化物流设备,用于在工业生产中进行材料的搬运和物流组织。
其动态调度策略的设计和优化对于提高生产效率和减少设备闲置时间具有重要意义。
⒉目标与需求分析⑴目标●提高生产线的整体效率,减少工作时间和生产成本。
●最大限度地减少的等待时间,提高设备的利用率。
⑵需求●根据生产线上材料的需求,实时分配任务给RGV。
●策略应能处理多种不同类型的任务和多个RGV的协同工作。
●最小化RGV的移动距离。
⒊ RGV调度策略设计⑴任务分配策略根据生产线上各个工作站的生产节拍和产量需求,将任务按优先级排序,并合理分配给可用的RGV。
任务分配的依据可以是任务的紧急程度、材料的重要性,或者其他相关的因素。
⑵移动选择策略在任务分配过程中,需要考虑RGV的移动选择策略。
可以采用最近可达算法,即选择最近的可达工作站或材料存放位置。
同时,还需要考虑RGV的载重能力,确保能够搬运材料的重量或容量。
⑶等待时间优化策略为了减少RGV的等待时间,可以采用预测算法预测未来一段时间内各个工作站的任务需求,提前调度RGV到相应的位置,以便及时处理任务。
同时,还可以采用优先级调度算法,优先处理紧急任务或关键任务,避免任务堆积和延误。
⒋系统实现与优化⑴系统架构设计根据需求分析和策略设计,设计智能RGV的系统架构,包括任务调度模块、移动控制模块、数据传输模块等。
确保系统的可靠性和稳定性。
⑵算法实现与优化根据调度策略设计,实现相关的算法,并进行优化,以提高系统的响应速度和处理效率。
可以采用动态规划、遗传算法、模拟退火等方法来寻找最优解。
⒌系统测试与验证对智能RGV系统进行全面的测试和验证,包括功能测试、性能测试、稳定性测试等,确保系统的准确性和可靠性。
通过测试数据的分析和验证结果的对比,评估系统的性能,并对系统进行进一步的优化。
⒍结论智能RGV的动态调度策略设计对提高生产线效率和减少成本具有重要意义。
智能RGV的动态调度策略
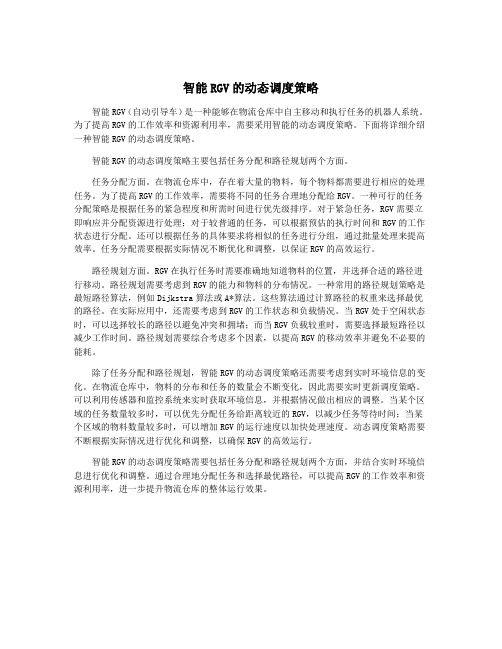
智能RGV的动态调度策略智能RGV(自动引导车)是一种能够在物流仓库中自主移动和执行任务的机器人系统。
为了提高RGV的工作效率和资源利用率,需要采用智能的动态调度策略。
下面将详细介绍一种智能RGV的动态调度策略。
智能RGV的动态调度策略主要包括任务分配和路径规划两个方面。
任务分配方面。
在物流仓库中,存在着大量的物料,每个物料都需要进行相应的处理任务。
为了提高RGV的工作效率,需要将不同的任务合理地分配给RGV。
一种可行的任务分配策略是根据任务的紧急程度和所需时间进行优先级排序。
对于紧急任务,RGV需要立即响应并分配资源进行处理;对于较普通的任务,可以根据预估的执行时间和RGV的工作状态进行分配。
还可以根据任务的具体要求将相似的任务进行分组,通过批量处理来提高效率。
任务分配需要根据实际情况不断优化和调整,以保证RGV的高效运行。
路径规划方面。
RGV在执行任务时需要准确地知道物料的位置,并选择合适的路径进行移动。
路径规划需要考虑到RGV的能力和物料的分布情况。
一种常用的路径规划策略是最短路径算法,例如Dijkstra算法或A*算法。
这些算法通过计算路径的权重来选择最优的路径。
在实际应用中,还需要考虑到RGV的工作状态和负载情况。
当RGV处于空闲状态时,可以选择较长的路径以避免冲突和拥堵;而当RGV负载较重时,需要选择最短路径以减少工作时间。
路径规划需要综合考虑多个因素,以提高RGV的移动效率并避免不必要的能耗。
除了任务分配和路径规划,智能RGV的动态调度策略还需要考虑到实时环境信息的变化。
在物流仓库中,物料的分布和任务的数量会不断变化,因此需要实时更新调度策略。
可以利用传感器和监控系统来实时获取环境信息,并根据情况做出相应的调整。
当某个区域的任务数量较多时,可以优先分配任务给距离较近的RGV,以减少任务等待时间;当某个区域的物料数量较多时,可以增加RGV的运行速度以加快处理速度。
动态调度策略需要不断根据实际情况进行优化和调整,以确保RGV的高效运行。
智能RGV的动态调度策略

智能 RGV 的动态调度策略摘要:针对智能 RGV 系统一道工序的物料加工作业情况,首先,RGV根据距离就近原则选择下一操作的CNC。
在 RGV 对所有 CNC 完成一次上料操作后,不断进行上下料、清洗作业的循环操作。
考虑到物料加工时间,我们选择离 RGV 最近的 CNC 作为下一个上料对象。
模型反复按顺序进行操作,直到时间达到 8 小时。
代入各组数据计算,得到相应的RGV动态调度模型和相应的求解算法。
关键词:RGV动态调度全局搜索工作时间均衡度一、背景介绍一个智能加工系统的示意,由 8 台计算机数控机床、1 辆轨道式自动引导车、1 条 RGV 直线轨道、1 条上料传送带、1 条下料传送带等附属设备组成。
RGV 是一种无人驾驶、能在固定轨道上自由运行的智能车。
它根据指令能自动控制移动方向和距离,并自带一个机械手臂、两只机械手爪和物料清洗槽,能够完成上下料及清洗物料等作业任务。
1.任务复述与情况分析任务复述:对一般问题进行研究,给出 RGV 动态调度模型和相应的求解算法。
情况分析:要求对只加工一道工序的情况进行一般性研究。
以 8 小时内加工出最多物料为目标,我们给出了以下一道工序 RGV 动态调度模型。
考虑到RGV 移动的时间远小于物料加工时间,我们选择离 RGV 最近的 CNC 作为下一个上料对象。
模型中反复按顺序进行以下操作,直到时间达到 8 小时:1.等待直到 RGV 空闲且至少一个 CNC 空闲2.使 RGV 移动到距 RGV 当前位置最近的空闲 CNC 处3.对该 CNC 进行上下料操作,若有熟料则还需进行清洗作业三、问题求解针对于智能加工系统来说每班次工作共存在两种状态:启动阶段和稳定阶段。
启动阶段:即开始有 CNC 处于空闲状态的阶段,当所有 CNC 都有处于加工过程时,这一阶段结束,在这一阶段,RGV 不存在等待和清洗操作,CNC 只有空闲和正在加工中两个状态。
稳定阶段:即所有 CNC 都开始工作后的情况,在这一阶段 CNC 有正在加工中,成熟等待,正在上下料三个状态;RGV 有等待、移动、上下料、清洗作业四种状态。
智能RGV的动态调度策略
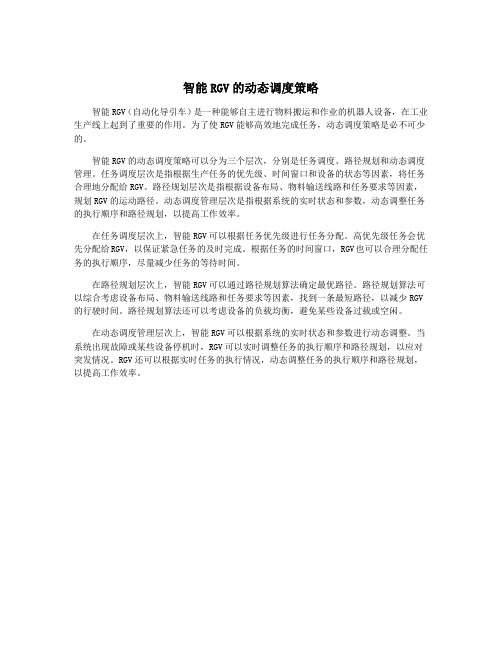
智能RGV的动态调度策略
智能RGV(自动化导引车)是一种能够自主进行物料搬运和作业的机器人设备,在工业生产线上起到了重要的作用。
为了使RGV能够高效地完成任务,动态调度策略是必不可少的。
智能RGV的动态调度策略可以分为三个层次,分别是任务调度、路径规划和动态调度管理。
任务调度层次是指根据生产任务的优先级、时间窗口和设备的状态等因素,将任务合理地分配给RGV。
路径规划层次是指根据设备布局、物料输送线路和任务要求等因素,规划RGV的运动路径。
动态调度管理层次是指根据系统的实时状态和参数,动态调整任务的执行顺序和路径规划,以提高工作效率。
在任务调度层次上,智能RGV可以根据任务优先级进行任务分配。
高优先级任务会优先分配给RGV,以保证紧急任务的及时完成。
根据任务的时间窗口,RGV也可以合理分配任务的执行顺序,尽量减少任务的等待时间。
在路径规划层次上,智能RGV可以通过路径规划算法确定最优路径。
路径规划算法可以综合考虑设备布局、物料输送线路和任务要求等因素,找到一条最短路径,以减少RGV 的行驶时间。
路径规划算法还可以考虑设备的负载均衡,避免某些设备过载或空闲。
在动态调度管理层次上,智能RGV可以根据系统的实时状态和参数进行动态调整。
当系统出现故障或某些设备停机时,RGV可以实时调整任务的执行顺序和路径规划,以应对突发情况。
RGV还可以根据实时任务的执行情况,动态调整任务的执行顺序和路径规划,以提高工作效率。
智能RGV的动态调度策略
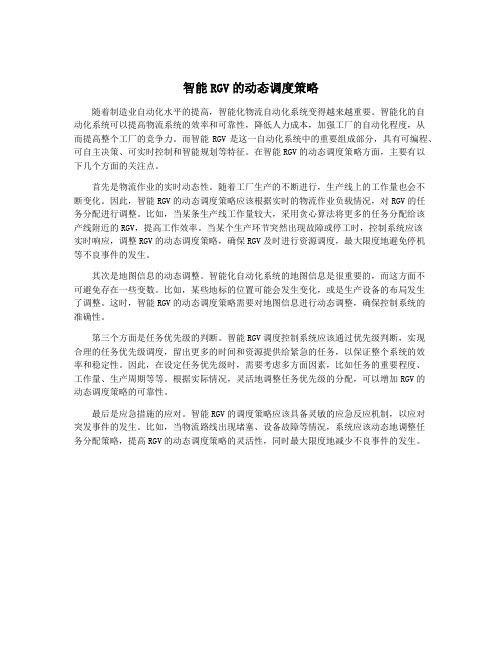
智能RGV的动态调度策略随着制造业自动化水平的提高,智能化物流自动化系统变得越来越重要。
智能化的自动化系统可以提高物流系统的效率和可靠性,降低人力成本,加强工厂的自动化程度,从而提高整个工厂的竞争力。
而智能RGV是这一自动化系统中的重要组成部分,具有可编程、可自主决策、可实时控制和智能规划等特征。
在智能RGV的动态调度策略方面,主要有以下几个方面的关注点。
首先是物流作业的实时动态性。
随着工厂生产的不断进行,生产线上的工作量也会不断变化。
因此,智能RGV的动态调度策略应该根据实时的物流作业负载情况,对RGV的任务分配进行调整。
比如,当某条生产线工作量较大,采用贪心算法将更多的任务分配给该产线附近的RGV,提高工作效率。
当某个生产环节突然出现故障或停工时,控制系统应该实时响应,调整RGV的动态调度策略,确保RGV及时进行资源调度,最大限度地避免停机等不良事件的发生。
其次是地图信息的动态调整。
智能化自动化系统的地图信息是很重要的,而这方面不可避免存在一些变数。
比如,某些地标的位置可能会发生变化,或是生产设备的布局发生了调整。
这时,智能RGV的动态调度策略需要对地图信息进行动态调整,确保控制系统的准确性。
第三个方面是任务优先级的判断。
智能RGV调度控制系统应该通过优先级判断,实现合理的任务优先级调度,留出更多的时间和资源提供给紧急的任务,以保证整个系统的效率和稳定性。
因此,在设定任务优先级时,需要考虑多方面因素,比如任务的重要程度、工作量、生产周期等等。
根据实际情况,灵活地调整任务优先级的分配,可以增加RGV的动态调度策略的可靠性。
最后是应急措施的应对。
智能RGV的调度策略应该具备灵敏的应急反应机制,以应对突发事件的发生。
比如,当物流路线出现堵塞、设备故障等情况,系统应该动态地调整任务分配策略,提高RGV的动态调度策略的灵活性,同时最大限度地减少不良事件的发生。
智能RGV的动态调度策略

智能RGV的动态调度策略
智能RGV动态调度策略的核心是在不同的时间段,根据当前的生产环境和生产需要调整RGV的工作任务及路径,以最大化利用RGV的运输能力、降低RGV的等待时间以及确保RGV的运输安全。
一、基于实时数据的任务调度策略
在这种策略中,RGV的调度任务是基于实时数据的变化来决定的,主要通过监测生产环境中的物料状态、生产设备状态以及产品生产计划等多种参数,制定RGV的调度任务和路径。
例如,当RGV在某个位置停留时,可以通过检测发现目标生产设备发生了故障或者负载状况发生了改变,则根据这些变化信息实时制定下一步的调度任务,以保证RGV的运输效率。
例如,根据历史生产数据,可以预测未来某个时间段的生产设备工作量、产品需求量及物料需求量等变化情况,进而调度RGV的运输任务和路径,以最大化利用RGV的运输功效。
在这种策略中,RGV的调度任务既参考实时数据,又运用预测模型,将两者相结合,以更准确地判断生产环境和生产需求,制定更为合理的调度任务和路径。
例如,借助实时数据确定RGV的工作量和任务,同时结合预测模型实现对未来生产环境的预测,以确保RGV能够快速响应生产需求,最大限度地发挥其运输能力和效率。
综上所述,智能RGV的动态调度策略是制定RGV的运输任务和路径的关键,不同的策略适用于不同的生产环境和生产需求,因此在实践中应根据具体情况选择合适的策略。
通过优化RGV的调度策略,可以提高物料运输效率,并为企业生产和经济效益的提升提供有力支持。
工业RGV的动态调度策略

工业RGV的动态调度策略工业RGV(工业用移动机器人)是一种能够在工业现场中移动、搬运和处理各种物品的机器人。
在工厂生产中,RGV能够将工件从一个工序转移到另一个工序,缩短工艺流程,提高生产效率。
为了更好地利用RGV,需要对其进行动态调度,使其能够高效地完成各项任务。
动态调度策略可以分为基于规则的策略和基于优化的策略。
基于规则的策略是根据事先设定的规则来指导RGV的运动轨迹。
例如,当需要将工件从A工序移动到B工序时,RGV会按照事先设定的路径行进,将工件顺利地运到B工序。
这种策略简单易实现,但是不能很好地适应工厂的实际情况。
基于优化的策略是通过优化RGV的行动路线,提高RGV的工作效率。
优化的策略可以分为两种类型:静态优化和动态优化。
静态优化是根据生产数据和生产时间计算出最优的路径,然后将这个路径固定在RGV上。
这种策略可以提高RGV的运维效率,但是不能适应生产现场的变化。
相对于静态优化,动态优化可以根据实时的生产数据和生产状态来调整RGV的行动路径,以达到最优的效果。
但是,动态调度需要收集实时数据,分析数据并更改RGV的运动路线,这需要较高的技术水平和信息处理能力。
在选择动态调度策略时,还需要考虑以下因素:工厂的规模、生产流程、设备状态和挑战等级。
对于小型工厂,可以采用基于规则的策略,因为工作量较小,规则相对简单。
对于大型工厂,需要采用基于优化的策略,以提高RGV的运营效率。
综上所述,RGV的动态调度策略是一项复杂的任务。
需要在工厂的实际情况下选择最合适的策略,并合理调配资源,以达到最优的生产效果。
随着技术的发展和硬件的进步,RGV的动态调度策略也将逐渐趋于完善。
智能RGV的动态调度策略
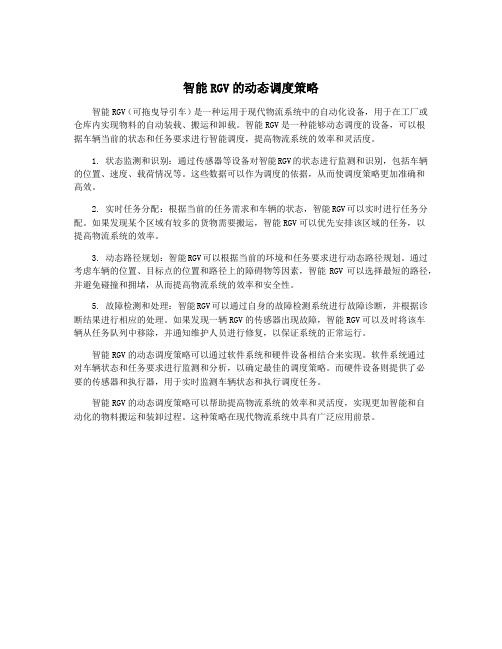
智能RGV的动态调度策略智能RGV(可拖曳导引车)是一种运用于现代物流系统中的自动化设备,用于在工厂或仓库内实现物料的自动装载、搬运和卸载。
智能RGV是一种能够动态调度的设备,可以根据车辆当前的状态和任务要求进行智能调度,提高物流系统的效率和灵活度。
1. 状态监测和识别:通过传感器等设备对智能RGV的状态进行监测和识别,包括车辆的位置、速度、载荷情况等。
这些数据可以作为调度的依据,从而使调度策略更加准确和高效。
2. 实时任务分配:根据当前的任务需求和车辆的状态,智能RGV可以实时进行任务分配。
如果发现某个区域有较多的货物需要搬运,智能RGV可以优先安排该区域的任务,以提高物流系统的效率。
3. 动态路径规划:智能RGV可以根据当前的环境和任务要求进行动态路径规划。
通过考虑车辆的位置、目标点的位置和路径上的障碍物等因素,智能RGV可以选择最短的路径,并避免碰撞和拥堵,从而提高物流系统的效率和安全性。
5. 故障检测和处理:智能RGV可以通过自身的故障检测系统进行故障诊断,并根据诊断结果进行相应的处理。
如果发现一辆RGV的传感器出现故障,智能RGV可以及时将该车辆从任务队列中移除,并通知维护人员进行修复,以保证系统的正常运行。
智能RGV的动态调度策略可以通过软件系统和硬件设备相结合来实现。
软件系统通过对车辆状态和任务要求进行监测和分析,以确定最佳的调度策略。
而硬件设备则提供了必要的传感器和执行器,用于实时监测车辆状态和执行调度任务。
智能RGV的动态调度策略可以帮助提高物流系统的效率和灵活度,实现更加智能和自动化的物料搬运和装卸过程。
这种策略在现代物流系统中具有广泛应用前景。
- 1、下载文档前请自行甄别文档内容的完整性,平台不提供额外的编辑、内容补充、找答案等附加服务。
- 2、"仅部分预览"的文档,不可在线预览部分如存在完整性等问题,可反馈申请退款(可完整预览的文档不适用该条件!)。
- 3、如文档侵犯您的权益,请联系客服反馈,我们会尽快为您处理(人工客服工作时间:9:00-18:30)。
Table 1. Three sets of data sheets for smart processing system operating parameters (Time unit: second) 表 1. 智能加工系统作业参数的 3 组数据表(时间单位:秒)
系统作业参数 RGV 移动 1 个单位所需时间 RGV 移动 2 个单位所需时间 RGV 移动 3 个单位所需时间 CNC 加工完成一个一道工序的物料所需时间 CNC 加工完成一个两道工序物料的第一道工序所需时间 CNC 加工完成一个两道工序物料的第二道工序所需时间 RGV 为 CNC1#,3#,5#,7#一次上下料所需时间 RGV 为 CNC2#,4#,6#,8#一次上下料所需时间 RGV 完成一个物料的清洗作业所需时间 注:每班次连续作业 8 小时。
Keywords
Matrix Cycle, Traveling Salesman Problem, Time Determinant, Fault Reduction Dimension, Optimal Scheduling
基于矩阵循环的智能RGV的动态调度策略
顾 扬*#,张洲镕†,姜 锦†
*第一作者。 #通讯作者。 †共同第二作者。
第1组 20 33 46 560 400 378 28 31 25
第2组 23 41 59 580 280 500 30 35 30
第3组 18 32 46 545 455 182 27 32 25
2. 问题分析
该问题是对智能加工系统中 RGV 的动态调度问题,理想的调度策略可以保证系统的作业效率,以高 效地满足生产需求。
2.1. 任务一的问题分析
2.1.1. 情况(1)的分析 在分析了智能加工系统的工作流程之后,进行程序模拟只有一道工序的调度过程,发现 RGV 的调度
是周期循环调度,在验证了周期性的合理性后,可判断循环调度即为最优调度。同时,所有 CNC 完成上
DOI: 10.12677/aam.2019.83054
按照要求在智能系统实际的运作规则下,考虑三种一般问题: 1) 一道工序的物料加工作业; 2) 两道工序的物料加工作业; 3) CNC 发生故障情况下一道工序和两道工序的物料加工作业。 建立出 RGV 动态调度模型,给出相应的求解算法,并利用给出的 3 组数据系统作业参数分别检验模 型的实用性和算法的有效性,给出 RGV 的调度策略和系统的作业效率。
Dynamic Scheduling Strategy of Smart RGV Based on Matrix Cycle
Yang Gu*#, Zhourong Zhang†, Jin Jiang†
College of Science, Nanjing University of Aeronautics and Astronautics, Nanjing Jiangsu
483
应用数学进展
顾扬 等
下料作业与相应的清洗作业所用总时间都是固定值,因此可将该部分时间消耗看作一个整体,将优化策 略体现在 RGV 的移动顺序上,整个过程就可以简化为单纯的路径规划问题,从寻找最优路径着手,逐步 建立调度模型。为此,引入邻接矩阵 A 和位置矩阵 B,可以认为邻接矩阵在每个周期内均为同一状态, 于是可以将模型简化,把规划目标转化为 RGV 调度周期最短,从而基于矩阵循环建立 RGV 最优调度模 型,该模型的求解从根本上可归结为旅行商问题[1],利用 Lingo [2]软件可解出其最优路径,用 MATLAB 软件[3]模拟仿真可得三组参数条件下工件生产总数和系统的作业效率。
摘要
本文主要研究一种智能RGV的动态调度问题。针对一道工序的加工作业,通过模拟分析判断出周期循环 调度是最优调度。因此建立基于矩阵循环的最优调度模型,将路径规划转化为旅行商问题,利用Lingo、 MATLAB求得三组参数条件下工件生产总数分别为384、347、395,系统作业效率均高达98%。针对两 道工序,引入时间决定因子y表示两道工序所需时间的比值,分三种情况分析:y近似于1,y大于1和y 小于1,分别建立基于时间决定因子的最优调度模型,求解可得三组参数条件下工件生产总数分别为243、 226、295,系统作业效率分别达88%、82%、89%。针对故障情况,按照故障点把时间分割成若干片 段,建立基于时间分段的故障降维最优调度模型,求解可得一道工序下工件生产总数分别为370、322、 378,系统作业效率高达94%、91%、94%;两道工序下工件生产总数分别为212、198、250,系统 的作业效率分别达77%、72%、75%。
Open Access
1. 引言
智能加工系统如图 1 所示,由 8 台计算机数控机床(Computer Number Controller, CNC)、1 辆轨道式 自动引导车(Rail Guide Vehicle, RGV)、1 条 RGV 直线轨道、1 条上料传送带、1 条下料传送带等附属设 备组成。RGV 是一种无人驾驶、能在固定轨道上自由运行的智能车。它根据指令能自动控制移动方向和 距离,并自带一个机械手臂、两只机械手爪和物料清洗槽,能够完成上下料及清洗物料等作业任务。
Advances in Applied Mathematics 应用数学进展, 2019, 8(3), 481-495 Published Online March 2019 in Hans. /journal/aam https:///10.12677/aam.2019.83054
Received: Feb. 28th, 2019; accepted: Mar. 12th, 2019; published: Mar. 19th, 2019
Abstract
This paper mainly studies the dynamic scheduling problem of a smart RGV. For the processing operation of one process, it is judged by simulation analysis that the cyclic cycle scheduling is the optimal scheduling. Therefore, we establish an optimal scheduling model based on matrix cycle, and transform the path planning into a traveling salesman problem (TSP). Then we use Lingo and MATLAB to solve three sets of parameters, the total number of workpiece production is 384, 347, and 395, respectively, and the system operation efficiency is as high as 98%. For the two processes, the time determinant y is introduced to represent the ratio of the time required for the two processes. We analyze in three cases: y is approximately 1, y is greater than 1 and y is less than 1, and respectively establish optimal scheduling model based on time determinant. The total number of workpieces produced under the three parameters of the solution is 243, 226, 295, and the system operating efficiency is 88%, 82%, and 89%, respectively. For the fault situation, the time is divided into several segments according to the fault point, and we establish the optimal scheduling model for fault reduction dimension based on time segmentation. The total number of workpieces produced in one process is 370, 322, and 378, and the system operation efficiency is as high as 94%, 91%, and 94%. The total number of workpieces produced in two processes is 212, 198, and 250, respectively, and the system operation efficiency is 77%, 72%, and 75%, respectively.
文章引用: 顾扬, 张洲镕, 姜锦. 基于矩阵循环的智能 RGV 的动态调度策略[J]. 应用数学进展, 2019, 8(3): 481-495. DOI: 10.12677/aam.2019.83054
顾扬 等
南京பைடு நூலகம்空航天大学理学院,江苏 南京
收稿日期:2019年2月28日;录用日期:2019年3月12日;发布日期:2019年3月19日
Figure 1. Schematic diagram of smart processing system 图 1. 智能加工系统示意图
DOI: 10.12677/aam.2019.83054