智能RGV的动态调度策略
智能RGV的动态调度策略
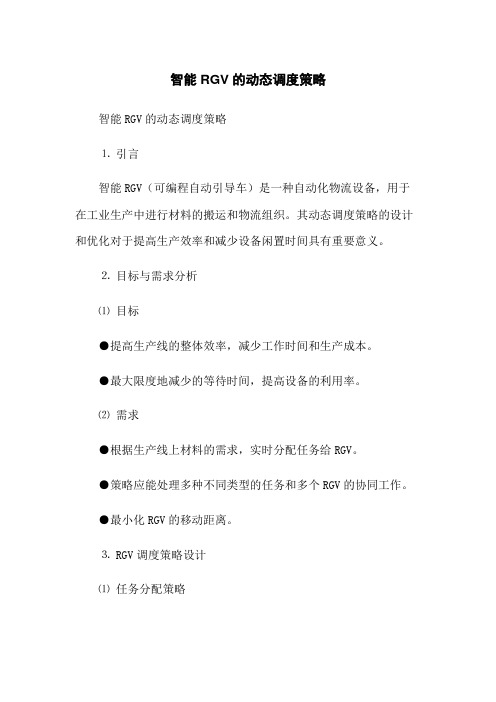
智能RGV的动态调度策略智能RGV的动态调度策略⒈引言智能RGV(可编程自动引导车)是一种自动化物流设备,用于在工业生产中进行材料的搬运和物流组织。
其动态调度策略的设计和优化对于提高生产效率和减少设备闲置时间具有重要意义。
⒉目标与需求分析⑴目标●提高生产线的整体效率,减少工作时间和生产成本。
●最大限度地减少的等待时间,提高设备的利用率。
⑵需求●根据生产线上材料的需求,实时分配任务给RGV。
●策略应能处理多种不同类型的任务和多个RGV的协同工作。
●最小化RGV的移动距离。
⒊ RGV调度策略设计⑴任务分配策略根据生产线上各个工作站的生产节拍和产量需求,将任务按优先级排序,并合理分配给可用的RGV。
任务分配的依据可以是任务的紧急程度、材料的重要性,或者其他相关的因素。
⑵移动选择策略在任务分配过程中,需要考虑RGV的移动选择策略。
可以采用最近可达算法,即选择最近的可达工作站或材料存放位置。
同时,还需要考虑RGV的载重能力,确保能够搬运材料的重量或容量。
⑶等待时间优化策略为了减少RGV的等待时间,可以采用预测算法预测未来一段时间内各个工作站的任务需求,提前调度RGV到相应的位置,以便及时处理任务。
同时,还可以采用优先级调度算法,优先处理紧急任务或关键任务,避免任务堆积和延误。
⒋系统实现与优化⑴系统架构设计根据需求分析和策略设计,设计智能RGV的系统架构,包括任务调度模块、移动控制模块、数据传输模块等。
确保系统的可靠性和稳定性。
⑵算法实现与优化根据调度策略设计,实现相关的算法,并进行优化,以提高系统的响应速度和处理效率。
可以采用动态规划、遗传算法、模拟退火等方法来寻找最优解。
⒌系统测试与验证对智能RGV系统进行全面的测试和验证,包括功能测试、性能测试、稳定性测试等,确保系统的准确性和可靠性。
通过测试数据的分析和验证结果的对比,评估系统的性能,并对系统进行进一步的优化。
⒍结论智能RGV的动态调度策略设计对提高生产线效率和减少成本具有重要意义。
智能RGV的动态调度策略
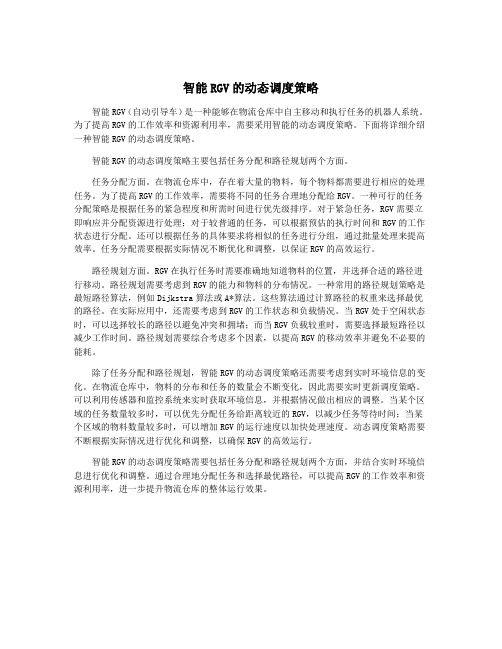
智能RGV的动态调度策略智能RGV(自动引导车)是一种能够在物流仓库中自主移动和执行任务的机器人系统。
为了提高RGV的工作效率和资源利用率,需要采用智能的动态调度策略。
下面将详细介绍一种智能RGV的动态调度策略。
智能RGV的动态调度策略主要包括任务分配和路径规划两个方面。
任务分配方面。
在物流仓库中,存在着大量的物料,每个物料都需要进行相应的处理任务。
为了提高RGV的工作效率,需要将不同的任务合理地分配给RGV。
一种可行的任务分配策略是根据任务的紧急程度和所需时间进行优先级排序。
对于紧急任务,RGV需要立即响应并分配资源进行处理;对于较普通的任务,可以根据预估的执行时间和RGV的工作状态进行分配。
还可以根据任务的具体要求将相似的任务进行分组,通过批量处理来提高效率。
任务分配需要根据实际情况不断优化和调整,以保证RGV的高效运行。
路径规划方面。
RGV在执行任务时需要准确地知道物料的位置,并选择合适的路径进行移动。
路径规划需要考虑到RGV的能力和物料的分布情况。
一种常用的路径规划策略是最短路径算法,例如Dijkstra算法或A*算法。
这些算法通过计算路径的权重来选择最优的路径。
在实际应用中,还需要考虑到RGV的工作状态和负载情况。
当RGV处于空闲状态时,可以选择较长的路径以避免冲突和拥堵;而当RGV负载较重时,需要选择最短路径以减少工作时间。
路径规划需要综合考虑多个因素,以提高RGV的移动效率并避免不必要的能耗。
除了任务分配和路径规划,智能RGV的动态调度策略还需要考虑到实时环境信息的变化。
在物流仓库中,物料的分布和任务的数量会不断变化,因此需要实时更新调度策略。
可以利用传感器和监控系统来实时获取环境信息,并根据情况做出相应的调整。
当某个区域的任务数量较多时,可以优先分配任务给距离较近的RGV,以减少任务等待时间;当某个区域的物料数量较多时,可以增加RGV的运行速度以加快处理速度。
动态调度策略需要不断根据实际情况进行优化和调整,以确保RGV的高效运行。
智能RGV的动态调度策略

智能 RGV 的动态调度策略摘要:针对智能 RGV 系统一道工序的物料加工作业情况,首先,RGV根据距离就近原则选择下一操作的CNC。
在 RGV 对所有 CNC 完成一次上料操作后,不断进行上下料、清洗作业的循环操作。
考虑到物料加工时间,我们选择离 RGV 最近的 CNC 作为下一个上料对象。
模型反复按顺序进行操作,直到时间达到 8 小时。
代入各组数据计算,得到相应的RGV动态调度模型和相应的求解算法。
关键词:RGV动态调度全局搜索工作时间均衡度一、背景介绍一个智能加工系统的示意,由 8 台计算机数控机床、1 辆轨道式自动引导车、1 条 RGV 直线轨道、1 条上料传送带、1 条下料传送带等附属设备组成。
RGV 是一种无人驾驶、能在固定轨道上自由运行的智能车。
它根据指令能自动控制移动方向和距离,并自带一个机械手臂、两只机械手爪和物料清洗槽,能够完成上下料及清洗物料等作业任务。
1.任务复述与情况分析任务复述:对一般问题进行研究,给出 RGV 动态调度模型和相应的求解算法。
情况分析:要求对只加工一道工序的情况进行一般性研究。
以 8 小时内加工出最多物料为目标,我们给出了以下一道工序 RGV 动态调度模型。
考虑到RGV 移动的时间远小于物料加工时间,我们选择离 RGV 最近的 CNC 作为下一个上料对象。
模型中反复按顺序进行以下操作,直到时间达到 8 小时:1.等待直到 RGV 空闲且至少一个 CNC 空闲2.使 RGV 移动到距 RGV 当前位置最近的空闲 CNC 处3.对该 CNC 进行上下料操作,若有熟料则还需进行清洗作业三、问题求解针对于智能加工系统来说每班次工作共存在两种状态:启动阶段和稳定阶段。
启动阶段:即开始有 CNC 处于空闲状态的阶段,当所有 CNC 都有处于加工过程时,这一阶段结束,在这一阶段,RGV 不存在等待和清洗操作,CNC 只有空闲和正在加工中两个状态。
稳定阶段:即所有 CNC 都开始工作后的情况,在这一阶段 CNC 有正在加工中,成熟等待,正在上下料三个状态;RGV 有等待、移动、上下料、清洗作业四种状态。
智能RGV的动态调度策略
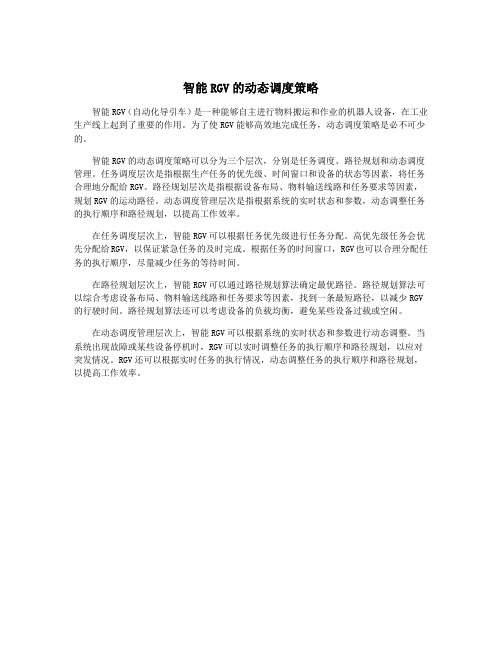
智能RGV的动态调度策略
智能RGV(自动化导引车)是一种能够自主进行物料搬运和作业的机器人设备,在工业生产线上起到了重要的作用。
为了使RGV能够高效地完成任务,动态调度策略是必不可少的。
智能RGV的动态调度策略可以分为三个层次,分别是任务调度、路径规划和动态调度管理。
任务调度层次是指根据生产任务的优先级、时间窗口和设备的状态等因素,将任务合理地分配给RGV。
路径规划层次是指根据设备布局、物料输送线路和任务要求等因素,规划RGV的运动路径。
动态调度管理层次是指根据系统的实时状态和参数,动态调整任务的执行顺序和路径规划,以提高工作效率。
在任务调度层次上,智能RGV可以根据任务优先级进行任务分配。
高优先级任务会优先分配给RGV,以保证紧急任务的及时完成。
根据任务的时间窗口,RGV也可以合理分配任务的执行顺序,尽量减少任务的等待时间。
在路径规划层次上,智能RGV可以通过路径规划算法确定最优路径。
路径规划算法可以综合考虑设备布局、物料输送线路和任务要求等因素,找到一条最短路径,以减少RGV 的行驶时间。
路径规划算法还可以考虑设备的负载均衡,避免某些设备过载或空闲。
在动态调度管理层次上,智能RGV可以根据系统的实时状态和参数进行动态调整。
当系统出现故障或某些设备停机时,RGV可以实时调整任务的执行顺序和路径规划,以应对突发情况。
RGV还可以根据实时任务的执行情况,动态调整任务的执行顺序和路径规划,以提高工作效率。
智能RGV的动态调度策略
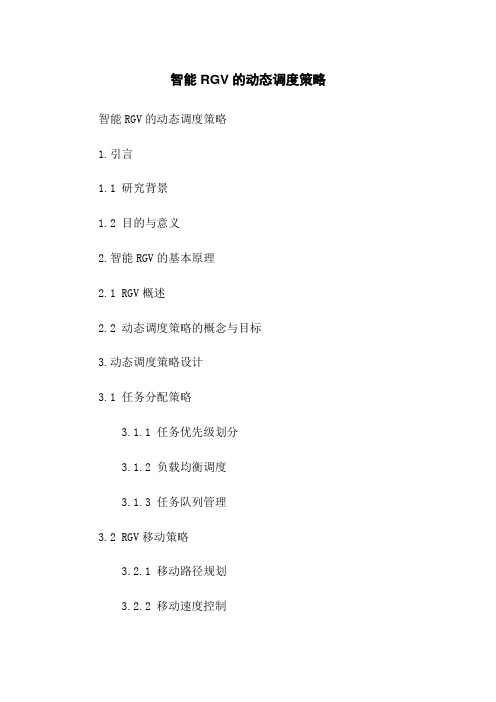
智能RGV的动态调度策略智能RGV的动态调度策略1.引言1.1 研究背景1.2 目的与意义2.智能RGV的基本原理2.1 RGV概述2.2 动态调度策略的概念与目标3.动态调度策略设计3.1 任务分配策略3.1.1 任务优先级划分3.1.2 负载均衡调度3.1.3 任务队列管理3.2 RGV移动策略3.2.1 移动路径规划3.2.2 移动速度控制3.3 状态监测与调整策略3.3.1 传感器监测与数据采集3.3.2 状态调整算法4.仿真实验及分析结果4.1 仿真环境与参数设置4.2 实验设计与分析5.结果分析与讨论5.1 仿真结果分析5.2 实际应用中的可行性讨论6.总结与展望附件:________1.实验数据分析表格2.仿真模型代码法律名词及注释:________1.RGV:________指代自动化物流系统中的轨道式供应车,即Rl Guided Vehicle的缩写。
2.动态调度策略:________指根据系统实时情况动态分配任务和调整设备状态的策略。
3.任务优先级划分:________指对不同任务进行优先级划分,以便更高效地完成任务。
4.负载均衡调度:________指通过合理调配任务以实现系统负载尽量均衡的调度方法。
5.移动路径规划:________指根据设备位置和任务需求进行路径规划,以确保设备能够高效地达到目标位置。
6.移动速度控制:________指根据系统的需求和设备状态动态调整移动速度,以提高系统吞吐量和减少能耗。
7.传感器监测与数据采集:________指使用传感器对设备状态和环境数据进行监测,并采集数据用于系统调度和性能分析。
8.状态调整算法:________指根据采集到的数据和系统需求,对设备状态进行调整的算法或方法。
智能RGV的动态调度策略
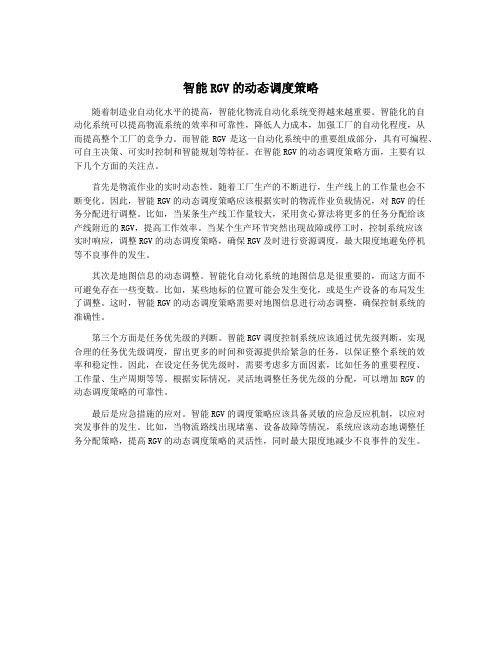
智能RGV的动态调度策略随着制造业自动化水平的提高,智能化物流自动化系统变得越来越重要。
智能化的自动化系统可以提高物流系统的效率和可靠性,降低人力成本,加强工厂的自动化程度,从而提高整个工厂的竞争力。
而智能RGV是这一自动化系统中的重要组成部分,具有可编程、可自主决策、可实时控制和智能规划等特征。
在智能RGV的动态调度策略方面,主要有以下几个方面的关注点。
首先是物流作业的实时动态性。
随着工厂生产的不断进行,生产线上的工作量也会不断变化。
因此,智能RGV的动态调度策略应该根据实时的物流作业负载情况,对RGV的任务分配进行调整。
比如,当某条生产线工作量较大,采用贪心算法将更多的任务分配给该产线附近的RGV,提高工作效率。
当某个生产环节突然出现故障或停工时,控制系统应该实时响应,调整RGV的动态调度策略,确保RGV及时进行资源调度,最大限度地避免停机等不良事件的发生。
其次是地图信息的动态调整。
智能化自动化系统的地图信息是很重要的,而这方面不可避免存在一些变数。
比如,某些地标的位置可能会发生变化,或是生产设备的布局发生了调整。
这时,智能RGV的动态调度策略需要对地图信息进行动态调整,确保控制系统的准确性。
第三个方面是任务优先级的判断。
智能RGV调度控制系统应该通过优先级判断,实现合理的任务优先级调度,留出更多的时间和资源提供给紧急的任务,以保证整个系统的效率和稳定性。
因此,在设定任务优先级时,需要考虑多方面因素,比如任务的重要程度、工作量、生产周期等等。
根据实际情况,灵活地调整任务优先级的分配,可以增加RGV的动态调度策略的可靠性。
最后是应急措施的应对。
智能RGV的调度策略应该具备灵敏的应急反应机制,以应对突发事件的发生。
比如,当物流路线出现堵塞、设备故障等情况,系统应该动态地调整任务分配策略,提高RGV的动态调度策略的灵活性,同时最大限度地减少不良事件的发生。
智能RGV的动态调度策略
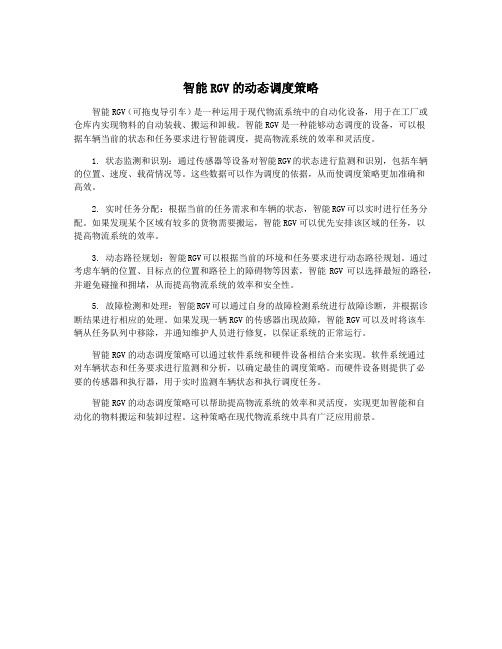
智能RGV的动态调度策略智能RGV(可拖曳导引车)是一种运用于现代物流系统中的自动化设备,用于在工厂或仓库内实现物料的自动装载、搬运和卸载。
智能RGV是一种能够动态调度的设备,可以根据车辆当前的状态和任务要求进行智能调度,提高物流系统的效率和灵活度。
1. 状态监测和识别:通过传感器等设备对智能RGV的状态进行监测和识别,包括车辆的位置、速度、载荷情况等。
这些数据可以作为调度的依据,从而使调度策略更加准确和高效。
2. 实时任务分配:根据当前的任务需求和车辆的状态,智能RGV可以实时进行任务分配。
如果发现某个区域有较多的货物需要搬运,智能RGV可以优先安排该区域的任务,以提高物流系统的效率。
3. 动态路径规划:智能RGV可以根据当前的环境和任务要求进行动态路径规划。
通过考虑车辆的位置、目标点的位置和路径上的障碍物等因素,智能RGV可以选择最短的路径,并避免碰撞和拥堵,从而提高物流系统的效率和安全性。
5. 故障检测和处理:智能RGV可以通过自身的故障检测系统进行故障诊断,并根据诊断结果进行相应的处理。
如果发现一辆RGV的传感器出现故障,智能RGV可以及时将该车辆从任务队列中移除,并通知维护人员进行修复,以保证系统的正常运行。
智能RGV的动态调度策略可以通过软件系统和硬件设备相结合来实现。
软件系统通过对车辆状态和任务要求进行监测和分析,以确定最佳的调度策略。
而硬件设备则提供了必要的传感器和执行器,用于实时监测车辆状态和执行调度任务。
智能RGV的动态调度策略可以帮助提高物流系统的效率和灵活度,实现更加智能和自动化的物料搬运和装卸过程。
这种策略在现代物流系统中具有广泛应用前景。
智能RGV的动态调度策略
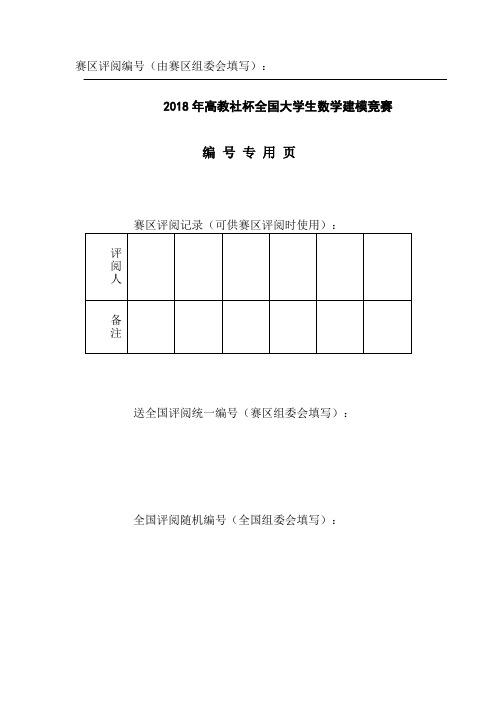
赛区评阅编号(由赛区组委会填写):2018年高教社杯全国大学生数学建模竞赛编号专用页赛区评阅记录(可供赛区评阅时使用):评阅人备注送全国评阅统一编号(赛区组委会填写):全国评阅随机编号(全国组委会填写):智能RGV的动态调度策略一、问题重述本课题是智能RGV的动态调度问题。
问题是由8台计算机数控机床(Computer Number Controller,CNC)、1辆轨道式自动引导车(Rail Guide Vehicle,RGV)、1条RGV直线轨道、1条上料传送带、1条下料传送带等附属设备组成。
RGV是一种无人驾驶、能在固定轨道上自由运行的智能车。
它根据指令能自动控制移动方向和距离,并自带一个机械手臂、两只机械手爪和物料清洗槽,能够完成上下料及清洗物料等作业任务。
1.1系统的构成及说明智能加工系统由8台CNC、1台带机械手和清洗槽的RGV、1条RGV直线轨道、1条上料传送带和1条下料传送带等附属设备构成。
(1)CNC:在上料传送带和下料传送带的两侧各安装4台CNC,等距排列,每台CNC同一时间只能安装1种刀具加工1个物料。
如果物料的加工过程需要两道工序,则需要有不同的CNC安装不同的刀具分别加工完成,在加工过程中不能更换刀具。
第一和第二道工序需要在不同的CNC上依次加工完成,完成时间也不同,每台CNC只能完成其中的一道工序。
(2)RGV:RGV带有智能控制功能,能够接收和发送指令信号。
根据指令能在直线轨道上移动和停止等待,可连续移动1个单位(两台相邻CNC间的距离)、2个单位(三台相邻CNC间的距离)和3个单位(四台相邻CNC间的距离)。
RGV同一时间只能执行移动、停止等待、上下料和清洗作业中的一项。
(3)上料传送带:上料传送带由4段组成,在奇数编号CNC1#、3#、5#、7#前各有1段。
由系统传感器控制,只能向一个方向传动,既能连动,也能独立运动。
(4)下料传送带:下料传送带由4段组成,在偶数编号CNC2#、4#、6#、8#前各有1段。
- 1、下载文档前请自行甄别文档内容的完整性,平台不提供额外的编辑、内容补充、找答案等附加服务。
- 2、"仅部分预览"的文档,不可在线预览部分如存在完整性等问题,可反馈申请退款(可完整预览的文档不适用该条件!)。
- 3、如文档侵犯您的权益,请联系客服反馈,我们会尽快为您处理(人工客服工作时间:9:00-18:30)。
同时,定义 RGV 当前所在的列数 j0 ∈ (1, 2,3, 4 ) 。以此,我们可以计算 RGV 到任意 CNC 的单位距离
∆d , ∆d 即是 RGV 将要移动的距离(相邻两列的距离为一个单位),计算公式如下:
DOI: 10.12677/csa.2019.91011 91 计算机科学与应用
钟卓辉 等
收稿日期:2019年1月1日;录用日期:2019年1月11日;发布日期:2019年1月18日
摘
要
本文分别针对直线轨道RGV智能加工系统的一道工序和两道工序的物料加工作业情况,以工作时长内实 际成料数、RGV作业效率、CNC作业效率多目标作为目标函数,给出RGV动态调度模型和算法。前者在
*
通讯作者。
文章引用: 钟卓辉, 高雨彤, 周嘉欣, 李纯. 智能 RGV 的动态调度策略[J]. 计算机科学与应用, 2019, 9(1): 89-95. DOI: 10.12677/csa.2019.91011
T = T∆d + Tα + Td
8
(4)
最后,我们还确定了一个对 RGV 移动的指令如下,在 ∑ i=1 xi = 0 的时候,RGV 前往最快使生料成为 熟料的 CNC 去。 综合上述分析可知, 智能 RGV 的动态调度策略是为了让智能加工系统在某班次时间内达到成料数最 大化,因此以成料数最大化为目标,得到智能 RGV 动态调度模型目标函数:
Computer Science and Application 计算机科学与应用, 2019, 9(1), 89-95 Published Online January 2019 in Hans. /journal/csa https:///10.12677/csa.2019.91011
st th th
Received: Jan. 1 , 2019; accepted: Jan. 11 , 2019; published: Jan. 18 , 2019
Abstract
In this paper, aiming at the material processing operations of one and two processes of the linear track RGV intelligent processing system, the dynamic scheduling model and algorithm of RGV are given by taking the actual number of finished products, RGV operating efficiency and CNC operating efficiency as the objective functions. In the former, the overall efficiency of the intelligent processing system is higher and the moving mode of the trolley is basically similar under the experimental data with little time difference between different operations. The latter obtained that the operation time of different processes would affect the number of CNC allocated in different processes and the operation mode of moving trolley. The data simulation results showed that the established model and algorithm were feasible.
working 0, = xi = , i 1, 2, ,8 waiting 1,
4 列,定义第 i 个 CNC 所处的列数 ji ∈ (1, 2,3, 4 ) ,具体计算公式如下:
ji = ( i + 1) ÷ 2 , i = 1, 2, ,8
(1)
其中,0 表示 CNC 正在加工,1 表示 CNC 处于等待加工状态, i 表示第 i 台 CNC。将智能加工系统分为 (2)
Figure 1. Schematic diagram of intelligent machining system 图 1. 智能加工系统示意图 DOI: 10.12677/csa.2019.91011 90 计算机科学与应用
钟卓辉 等
图 1 中的工作分为执行移动、停止等待、上下料和清洗作业四个部分且这四个部分只能独立作业并 且需要耗费一定时间,CNC 同一时间只能安装 1 种刀具加工 1 个物料,本文针对不同情况解决动态调度 的最优模型问题并求出相应的算法。 同时也提供一些数值计算实例, 检验模型的实用性和算法的有效性, 并且给出具体的调度策略以及系统工作效率。
Open Access
1. 问题背景
2003 年 Malmborg 教授及其课题组首先提出自动小车存取系统,它主要包括轨道导引小车系统,通 过 RGVS 小车进行货物存取。RGVS 控制系统通常与 AGVS 比较,RGVS 智能加工系统优化调度一直是 研究的热点。目前众多国内学者对此做出了许多研究,罗键[1]等初步概述了智能加工系统调度的一般方 法。刘丰瑞[2]等用动态规划法建立最优路径的逆序递归数学模型,求解复合作业的最佳配对组合,使复 合作业的路径优化方法更加简单。张甜宗[3],陈粱[4]等通过遗传算法时利用多重编码技术,结合计算机 模型仿真求解进行研究。刘二辉[5]等提出一种用于求解复杂环境下自动导引小车路径规划问题的改进灰 狼优化算法,引入路径微调算子和邻域变异算子来提高灰狼优化算法的局部开发能力,采用改进的路径 片段与障碍物相交判断算法来提高算法的运行效率。江唯[6]等以任务最短完成时间为目标,此基础上提 出路径最短和堵塞次数最少两个优化目标,提出了改进的自适应权重的求解方案,进一步提高了算法性 能。智能算法的缺点在于收敛速度较慢以及求解时容易陷入局部最优,因此解决算法获得最终较优解的 时间效率问题成为未来研究的重点[7] [8],这也是智能算法在实际生产过程中的瓶颈问题。 图 1 是一个 RGV 有轨制导车辆系统,是集各高新技术于一体的系统,配合 CNC 计算机数控机床在 物料加工方面有一定的实际应用。它有一个机械手臂、两只机械手爪和物料清洗槽,能够完成上下料及 清洗物料等作业任务。本文讨论的是在结合 8 台 CNC、1 条 RGV 直线轨道、1 条上料传送带、1 条下料 传送带等附属设备条件下,如何实现物料加工的效率最高化问题。
Keywords
Intelligent Processing System, Dynamic Scheduling Strategy, Monte Carlo Algorithm
智能RGV的动态调度策略
钟卓大学,理学院,湖南 长沙 湖南农业大学,经济学院,湖南 长沙
4) 当物料加工需要两道工序时,在一道工序的基础上,物料需要经过不同的 CNC 进行二次加工, 这时 CNC 不同刀具的分配将会影响 RGV 的调度模型。
3. 模型建立与数值计算
3.1. 一道工序动态调度仿真模型
由于一台 RGV 在同一时间只能为一台 CNC 上下物料,并且 RGV 运动需要花费一定时间,因此为 了在特定时间内可以加工最多的物料,本文让 RGV 尽量节省移动耗费的时间,让 RGV 以就近原则为基 础,模拟仿真整个智能加工系统作业过程。一般情况下,每一台 CNC 的工作状态可采用 0~1 变量表示, 以 CNC 是否向 RGV 发送信号为决策变量进行 0~1 规划, X ∈ { x1 , x2 , , x8 } ,具体如下:
2) RGV 的上下料时间偏短为好。 8 台 CNC 平均分布在 RGV 两侧, 设 RGV 编号为奇数的一边(1, 3, 5,
7)为 A 组,编号为偶数(2, 4, 6, 8)的一边为 B 组。B 组所花费的上下料时间要大于 A 组所花费的上下料时 间。所以在 RGV 两侧都有 CNC 时,应先给 A 组上下物料。 CNC 出进行等待。 3) RGV 的停止等待时间越短越好,当所有 CNC 都在工作时,RGV自行进行移动至最快完成工作的
∆di = ji − j0 , ∆di ∈ (1, 2,3) , i = 1, 2, ,8
(3)
RGV 为偶数编号 CNC 一次上下料所需时间要大于为奇数编号 CNC 一次上下料所需时间, 并且为了 尽快地开始进行上下料工作,因此,RGV 选取下一次上下料所在的 CNC 的规则如下:CNC 的当前状态 处在等待加工即 xi = 1 。此 CNC 与 RGV 的距离为最短距离 min ( ∆di ) 。在 min ( ∆di ) 相等的情况下优先选 择奇数编号的 CNC。在智能加工系统中,作业时间 T 中包括 RGV 移动的时间 T∆d ,RGV 停止等待的时 间 Td ,RGV 为 CNC 一次上下料的时间 Tα ,CNC 加工完成一个一道工序的物料所需时间 Tm ,RGV 完成 一个物料的清洗作业所需时间 Tω 。以 RGV 为观察对象,另外,引进变量 T0 ∈ R1×8 为包含各 CNC 加工完 成的时刻。定义一般班次的时间 Tb 在系统工作时间 T ≤ Tb 内,得到作业时间 T 计算公式如下:
Intelligent RGV Dynamic Scheduling Strategy
Zhuohui Zhong1, Yutong Gao1, Jiaxin Zhou2, Chun Li1*
1 2
School of Science, Hunan Agricultural University, Changsha Hunan School of Economics, Hunan Agricultural University, Changsha Hunan