催化裂化
催化裂化工艺介绍

1。
0催化裂化催化裂化是原料油在酸性催化剂存在下,在500℃左右、1×105~3×105Pa 下发生裂解,生成轻质油、气体和焦炭的过程.催化裂化是现代化炼油厂用来改质重质瓦斯油和渣油的核心技术,是炼厂获取经济效益的重要手段。
催化裂化的石油炼制工艺目的:1)提高原油加工深度,得到更多数量的轻质油产品;2)增加品种,提高产品质量。
催化裂化是炼油工业中最重要的一种二次加工工艺,是重油轻质化和改质的重要手段之一,已成为当今石油炼制的核心工艺之一。
1。
1催化裂化的发展概况催化裂化的发展经历了四个阶段:固定床、移动床、流化床和提升管。
见下图:固定床移动床流化床提升管(并列式)在全世界催化裂化装置的总加工能力中,提升管催化裂化已占绝大多数。
1。
2催化裂化的原料和产品1。
2。
0原料催化裂化的原料范围广泛,可分为馏分油和渣油两大类。
馏分油主要是直馏减压馏分油(VGO),馏程350—500℃,也包括少量的二次加工重馏分油如焦化蜡油等,以此种原料进行催化裂化称为馏分油催化裂化。
渣油主要是减压渣油、脱沥青的减压渣油、加氢处理重油等。
渣油都是以一定的比例掺入到减压馏分油中进行加工,其掺入的比例主要受制于原料的金属含量和残炭值.对于一些金属含量低的石蜡基原有也可以直接用常压重油为原料。
当减压馏分油中掺入渣油使通称为RFCC。
以此种原料进行催化裂化称为重油催化裂化。
1。
2.1产品催化裂化的产品包括气体、液体和焦炭。
1、气体在一般工业条件下,气体产率约为10%-20%,其中含干气和液化气。
2、液体产物1)汽油,汽油产率约为30%-60%;这类汽油安定性较好。
2)柴油,柴油产率约为0—40%;因含较多芳烃,所有十六烷值较低,由重油催化裂化得到的柴油的十六烷值更低,这类柴油需经加氢处理。
3)重柴油(回炼油),可以返回到反应器内,已提高轻质油收率,不回炼时就以重柴油产品出装置,也可作为商品燃料油的调和组分。
4)油浆,油浆产率约为5%—10%,从催化裂化分馏塔底得到的渣油,含少量催化剂细粉,可以送回反应器回炼以回收催化剂。
催化裂化原理
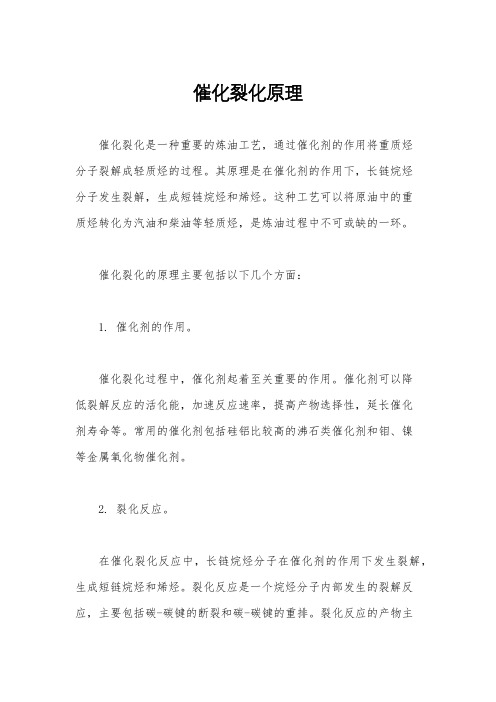
催化裂化原理催化裂化是一种重要的炼油工艺,通过催化剂的作用将重质烃分子裂解成轻质烃的过程。
其原理是在催化剂的作用下,长链烷烃分子发生裂解,生成短链烷烃和烯烃。
这种工艺可以将原油中的重质烃转化为汽油和柴油等轻质烃,是炼油过程中不可或缺的一环。
催化裂化的原理主要包括以下几个方面:1. 催化剂的作用。
催化裂化过程中,催化剂起着至关重要的作用。
催化剂可以降低裂解反应的活化能,加速反应速率,提高产物选择性,延长催化剂寿命等。
常用的催化剂包括硅铝比较高的沸石类催化剂和钼、镍等金属氧化物催化剂。
2. 裂化反应。
在催化裂化反应中,长链烷烃分子在催化剂的作用下发生裂解,生成短链烷烃和烯烃。
裂化反应是一个烷烃分子内部发生的裂解反应,主要包括碳-碳键的断裂和碳-碳键的重排。
裂化反应的产物主要是烷烃、烯烃和芳烃。
3. 反应条件。
催化裂化的反应条件包括温度、压力、催化剂种类和用量等。
通常情况下,催化裂化反应需要在较高的温度下进行,以提高反应速率和产物选择性。
此外,适当的压力和催化剂的选择也对裂化反应的效果有重要影响。
4. 产物分离。
催化裂化反应产生的混合气体需要进行分离和纯化,以得到所需的轻质烃产品。
通常采用的分离技术包括精馏、萃取、吸附等,以获得高纯度的汽油和柴油产品。
5. 催化剂再生。
在催化裂化过程中,催化剂会因受到焦炭和烃类物质的污染而失活,需要进行再生。
催化剂再生是通过热氧化或化学氧化等方法将焦炭烧除,恢复催化剂的活性和选择性,延长催化剂的使用寿命。
总的来说,催化裂化是一种重要的炼油工艺,通过催化剂的作用将重质烃分子裂解成轻质烃,可以提高原油的利用率,生产出更多的汽油和柴油产品。
催化裂化的原理涉及催化剂的作用、裂化反应、反应条件、产物分离和催化剂再生等多个方面,需要综合考虑和控制,以实现高效、稳定的生产过程。
催化裂化工艺流程ppt

催化剂对裂解过程的促进作用
提供活性中心
催化剂表面具有特殊的活性中 心,能够吸附和活化重质烃分 子,使其更容易发生裂解反应
。
降低反应活化能
催化剂可以降低裂解反应的活化 能,使反应更容易进行。
促进反应选择性
催化剂可以促进特定结构的烃分子 发生裂解反应,提高产品的选择性 。
产品的主要性质及用途
乙烯和丙烯
催化裂化工艺流程ppt
xx年xx月xx日
contents
目录
• 概述 • 工艺流程 • 催化裂化反应原理 • 工艺特点 • 应用和发展 • 安全和环保
01
概述
催化裂化是什么
1
催化裂化是一种将重质烃转化为轻质烯烃和芳 烃的石油化工过程。
2
催化裂化催化剂通常为酸性催化剂,如硅酸铝 、沸石等。
3
催化裂化工艺可分为固定床、流化床和移动床 三种类型,其中流化床工艺最为常用。
THANKS
谢谢您的观看
三废处理
对工艺流程中产生的废水、废气、废渣进行分类处理,实现资源化再利用。 例如,将废气中的二氧化碳进行捕获和封存,实现减排目标;将废水进行深 度处理后再次利用;将废渣进行资源化利用等。
绿色催化裂化工艺流程的探索
不断探索新的催化裂化工艺流程,采用绿色催化剂、提高反应转化率和能量 利用率等措施,实现工业生产与环境保护的有机结合。
产品收率和质量调整
通过调整催化剂种类和反应条件,可以改变产品的收率和质 量。这使得催化裂化工艺具有很强的适应性,能够根据市场 需求灵活调整产品结构。
05
应用和发展
在石油工业中的地位
01
石油工业作为国家经济发展的重要支柱,催化裂化工艺在其中扮演着至关重要 的角色。
催化裂化计算公式
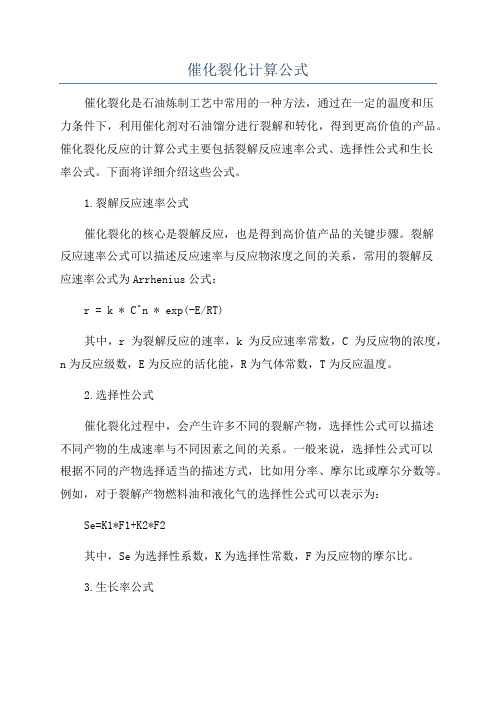
催化裂化计算公式催化裂化是石油炼制工艺中常用的一种方法,通过在一定的温度和压力条件下,利用催化剂对石油馏分进行裂解和转化,得到更高价值的产品。
催化裂化反应的计算公式主要包括裂解反应速率公式、选择性公式和生长率公式。
下面将详细介绍这些公式。
1.裂解反应速率公式催化裂化的核心是裂解反应,也是得到高价值产品的关键步骤。
裂解反应速率公式可以描述反应速率与反应物浓度之间的关系,常用的裂解反应速率公式为Arrhenius公式:r = k * C^n * exp(-E/RT)其中,r为裂解反应的速率,k为反应速率常数,C为反应物的浓度,n为反应级数,E为反应的活化能,R为气体常数,T为反应温度。
2.选择性公式催化裂化过程中,会产生许多不同的裂解产物,选择性公式可以描述不同产物的生成速率与不同因素之间的关系。
一般来说,选择性公式可以根据不同的产物选择适当的描述方式,比如用分率、摩尔比或摩尔分数等。
例如,对于裂解产物燃料油和液化气的选择性公式可以表示为:Se=K1*F1+K2*F2其中,Se为选择性系数,K为选择性常数,F为反应物的摩尔比。
3.生长率公式催化裂化反应中,一些分子会通过生长过程生成更大的分子,这些生长过程可以通过生长率公式描述。
一般来说,生长率公式可以基于碳原子的增长数量表示。
G=A*C^m其中,G为生长率,A为生长常数,C为反应物的浓度,m为生长度。
需要注意的是,上述公式只是催化裂化反应计算中的常用公式,实际应用中还需要结合具体的反应机理和实验数据进行修正和拟合。
此外,催化裂化反应过程中还涉及到反应器设计、催化剂选择、操作参数优化等多方面的问题,需要综合考虑才能得到准确的计算结果。
催化裂化工艺流程及主要设备

2023催化裂化工艺流程及主要设备pptcontents •概述•催化裂化工艺流程•催化裂化主要设备•工艺特点和操作规程•安全与环保•常见故障及排除方法•发展方向和新技术应用目录01概述催化裂化是一种将重质烃类转化为轻质烃类和液化气的过程,是石油化工中重要的二次加工手段之一。
催化裂化工艺主要采用流化床反应器,催化剂作为床层中的介质,在适宜的温度、压力和空速条件下进行反应。
催化裂化基本概念1催化裂化主要设备23流化床反应器是催化裂化的主要设备之一,分为单器、双器和多器系统。
反应器再生器是催化裂化中的重要设备,用于烧去催化剂表面的积炭,恢复催化剂活性。
再生器旋风分离器用于将反应和再生两个工艺流程分开,同时将催化剂从反应器物料中分离出来。
旋风分离器催化裂化工艺流程简介原料油进入反应器,在适宜的温度、压力和空速条件下进行反应。
分离出的催化剂进入再生器,烧去积炭恢复活性。
反应后的物料进入旋风分离器,将催化剂从物料中分离出来。
再生后的催化剂回到反应器物料中,继续参与反应。
02催化裂化工艺流程原料油缓冲在催化裂化工艺中,原料油首先需要进入缓冲罐,进行初步的脱水和脱盐处理。
原料油加热原料油通过加热炉加热到一定温度,以便能够进行催化裂化反应。
原料预处理催化裂化主要流程加热后的原料油被送到催化裂化反应器中,同时加入催化剂。
进料在催化裂化反应器中,原料油在催化剂的作用下发生裂化反应,生成轻质油品和小分子烃类。
裂化反应裂化反应后的油气和催化剂分离,油气进入分馏塔进行分离。
催化剂分离分离后的催化剂进入再生器烧焦再生,循环使用。
催化剂循环油气在分馏塔中根据沸点不同,分离成不同沸点的油品,如汽油、柴油和重油。
油品分馏分离出的油品通过一系列精制过程,如脱硫、脱氮、脱氧等处理,提高油品质量。
油品精制催化裂化过程中产生的气体,通过压缩、冷却和分离等步骤,得到液态烃和干气。
气体分离经过处理的油品和气体分别进入相应的储罐或装置进行储存或进一步加工。
催化裂化机理及特点

催化裂化机理及特点催化裂化是一种通过加热和催化剂的作用将长链烃分子裂解为短链烃分子的重要工艺。
催化裂化机理及特点主要包括以下几个方面:一、催化裂化机理1.构造反应:长链烃分子在裂化过程中首先发生构造反应,通过裂解碳-碳键,形成相对较短的碳链碳烃和烯烃。
2.重排反应:长链烃分子中的骨架碳骨架会经历一系列重排反应,使得产物中更多的是相对稳定的异构体和环状化合物。
3.脱氢反应:重排反应过程中,长链分子中的烃基可能失去氢原子,从而形成烯烃,增加了催化裂化的产物中烯烃的含量。
4.脱氢裂解反应:在高温高压下,部分碳链碳烃可以发生脱氢裂解反应,形成更短的链长烃烃烃烃、烯烃和芳香烃。
二、催化裂化特点1.催化裂化具有高选择性:在催化剂的影响下,催化裂化反应主要发生在长链烃分子中的弱键和缺陷位置,使得产物中的碳链长度相对较短,同时产生更多的异构体和环状化合物。
2.催化裂化反应速度快:催化剂的存在提高了反应活性,使得裂化反应可以在相对低的温度和压力下进行,加快了反应速度。
3.催化裂化可以产生高附加值的产品:催化裂化使得重质燃料油转化为轻质烃类产品,其中包括汽油、炼厂气、润滑油基础油等,这些产品有较高的附加值。
4.催化裂化可以降低能源消耗:通过催化裂化将重质原油转化为较轻质产品,如汽油和炼厂气,不仅提供了更多的高附加值产品,还减少了对原油的需求,降低了能源消耗。
5.催化裂化可以调节产品分布:通过不同的催化剂组合和反应条件,可以调节催化裂化产物的碳链长度分布,以满足市场需求,提高产品经济效益。
总之,催化裂化是一种高效、高选择性的炼油工艺,通过加热和催化剂的作用,将长链烃分子裂解为短链烃分子,产生高附加值产品,并降低能源消耗。
催化裂化机理和特点的深入研究对于提高炼油工艺的效率和降低能源消耗具有重要意义。
催化裂化工艺流程
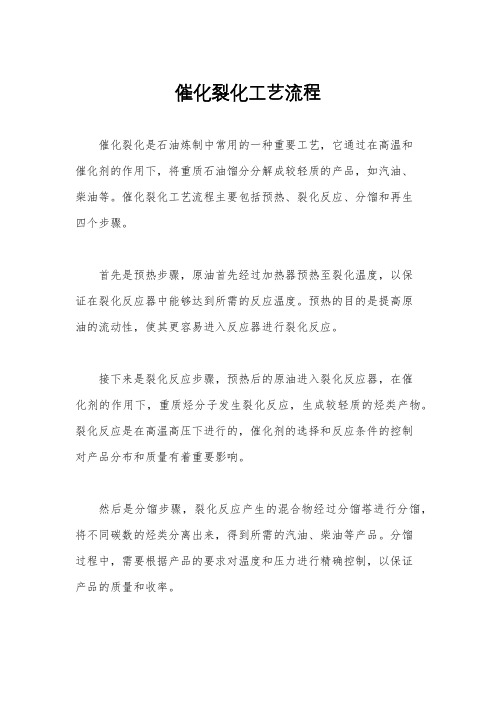
催化裂化工艺流程
催化裂化是石油炼制中常用的一种重要工艺,它通过在高温和
催化剂的作用下,将重质石油馏分分解成较轻质的产品,如汽油、
柴油等。
催化裂化工艺流程主要包括预热、裂化反应、分馏和再生
四个步骤。
首先是预热步骤,原油首先经过加热器预热至裂化温度,以保
证在裂化反应器中能够达到所需的反应温度。
预热的目的是提高原
油的流动性,使其更容易进入反应器进行裂化反应。
接下来是裂化反应步骤,预热后的原油进入裂化反应器,在催
化剂的作用下,重质烃分子发生裂化反应,生成较轻质的烃类产物。
裂化反应是在高温高压下进行的,催化剂的选择和反应条件的控制
对产品分布和质量有着重要影响。
然后是分馏步骤,裂化反应产生的混合物经过分馏塔进行分馏,将不同碳数的烃类分离出来,得到所需的汽油、柴油等产品。
分馏
过程中,需要根据产品的要求对温度和压力进行精确控制,以保证
产品的质量和收率。
最后是再生步骤,裂化反应产生的催化剂在经过一段时间的使
用后会失活,需要进行再生。
再生过程包括焙烧和再生氢化两个步骤,通过高温气体的通入和催化剂的洗涤,使催化剂重新获得活性,可以继续用于裂化反应。
总的来说,催化裂化工艺流程是一个复杂的过程,需要对原油
的性质、催化剂的选择、反应条件的控制等方面进行精确的把握。
只有在各个步骤都能够得到合理的设计和操作,才能够得到高质量
的裂化产品。
同时,随着石油资源的日益枯竭和环保要求的提高,
对催化裂化工艺的研究和改进也变得日益重要,希望在未来能够有
更多的突破和创新,为炼油行业的发展做出更大的贡献。
催化裂化原理
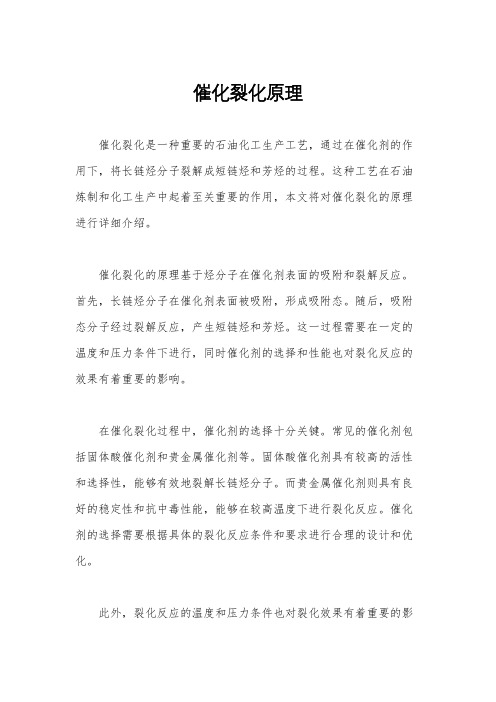
催化裂化原理催化裂化是一种重要的石油化工生产工艺,通过在催化剂的作用下,将长链烃分子裂解成短链烃和芳烃的过程。
这种工艺在石油炼制和化工生产中起着至关重要的作用,本文将对催化裂化的原理进行详细介绍。
催化裂化的原理基于烃分子在催化剂表面的吸附和裂解反应。
首先,长链烃分子在催化剂表面被吸附,形成吸附态。
随后,吸附态分子经过裂解反应,产生短链烃和芳烃。
这一过程需要在一定的温度和压力条件下进行,同时催化剂的选择和性能也对裂化反应的效果有着重要的影响。
在催化裂化过程中,催化剂的选择十分关键。
常见的催化剂包括固体酸催化剂和贵金属催化剂等。
固体酸催化剂具有较高的活性和选择性,能够有效地裂解长链烃分子。
而贵金属催化剂则具有良好的稳定性和抗中毒性能,能够在较高温度下进行裂化反应。
催化剂的选择需要根据具体的裂化反应条件和要求进行合理的设计和优化。
此外,裂化反应的温度和压力条件也对裂化效果有着重要的影响。
一般来说,较高的温度和适当的压力有利于裂化反应的进行。
在一定的温度范围内,裂化反应速率随温度的升高而增加,但过高的温度会导致产物的选择性下降。
因此,裂化反应的温度需要在活性和选择性之间进行平衡。
另外,裂化反应的产物选择性也是一个重要的问题。
在裂化反应中,短链烃和芳烃的选择性对于产品的质量和产率有着重要的影响。
通过调整催化剂的性质和反应条件,可以实现对产物选择性的调控,从而获得理想的产品。
总的来说,催化裂化是一种重要的石油化工生产工艺,通过催化剂的作用,将长链烃分子裂解成短链烃和芳烃。
催化裂化的原理涉及到催化剂的选择、反应条件的控制以及产物选择性的调控等方面。
通过对催化裂化原理的深入理解,可以为工程实践提供理论指导和技术支持,推动石油化工生产的发展和进步。
- 1、下载文档前请自行甄别文档内容的完整性,平台不提供额外的编辑、内容补充、找答案等附加服务。
- 2、"仅部分预览"的文档,不可在线预览部分如存在完整性等问题,可反馈申请退款(可完整预览的文档不适用该条件!)。
- 3、如文档侵犯您的权益,请联系客服反馈,我们会尽快为您处理(人工客服工作时间:9:00-18:30)。
催化裂化技术的发展概况及前景展望张坚强1引言催化裂化(FCC)工艺是将重质油轻质化,目的产品是汽油、柴油和液化气。
由于转化率高,产品质量好,近半个世纪以来, FCC工艺技术和生产规模都有了很大的发展。
从催化裂化减压蜡油到掺混渣油,并逐步提高掺混比例,大大提高了原油的加工深度,获得了更大的经济效益。
目前,催化裂化装置已成为炼油工业深度加工和汽油生产的主体装置[1]。
由于催化裂化投资和操作费用低,原料适应性强,转化率高,自1942年第一套工业化流化催化裂化装置运转以来,它已发展成为炼油厂中的核心加工工艺,是重油轻质化的主要手段之一,而我国石油资源中,原油大部分偏重,轻质油品含量低,这就更加决定了炼油工业必须走深加工的路线[2]。
面对日益严格的环保法规的要求,通过装置改造和与其它上下游工艺结合(如进料加氢,产品后处理等),催化裂化能以合适的费用生产合适的产品。
近十几年来,我国催化裂化掺炼渣油量在不断上升,已居世界领先地位。
催化剂的制备技术已取得了长足的进步,国产催化剂在渣油裂化能力和抗金属污染等方面均已达到或超过国外的水平。
在减少焦炭、取出多余热量、催化剂再生、能量回收等方面的技术有了较大发展[3]。
从当前炼油工艺发展和炼油厂改造与建设情况看来,催化裂化仍居重要地位,并未因生产清洁燃料的苛刻要求而止步不前,即使从更长远的目标看,催化裂化装置所产汽油经加氢饱和后也应能成为燃料电池的一种燃料组分。
本文主要综述国内催化裂化技术现状及其发展前景。
2 国内外催化裂化技术发展动力及其概况2.1 催化裂化技术进步的推动力近年来,催化裂化原料的品质越来越差,但对提高目的产物收率、汽柴油质量、柴汽比,以及多产丙烯和改善烟气排放等提出了更高的要求。
围绕这些问题,催化剂、设备和工艺技术方面的新技术不断涌现,推动着催化技术不断向前发展。
由于催化裂化过程的庞大加工规模,目的产品产率提高零点五个百分点即可产生巨大的经济效益,因此提高目的产品产率始终是催化裂化技术进步的主旋律。
由于馏分油和重质油性质的显著差别,至今所取得的大多数技术进步主要都是针对重油催化裂化。
此外,近年来对催化裂化产品质量的要求越来越高,对产品需求结构的变化,以及环保法规的逐渐完善,都促进了催化裂化技术的发展。
除原料变差以外,市场对产品结构和产品品质的要求也在不断变化。
在产品结构方面,要求提高柴汽比和增产丙烯;在产品的品质方面,要求生产低烯烃含量和低硫含量的高辛烷值汽油和低硫含量的高十六烷值柴油。
由于我国许多炼化企业生产的汽油除催化裂化汽油外,其他的调合组分很少甚至没有,因而,汽油标准对烯烃和硫含量的限制给许多企业带来了不小的压力。
催化裂化过程的环保问题主要涉及SOx 和NOx的排放,国外采取的主要措施是在催化裂化反应再生过程中添加SOx 和NOx转移剂或转化剂。
SOx转移剂是在催化剂再生过程中与SOx 反应生成硫酸盐,在反应过程中硫酸盐被还原,硫以H2S的形式进入到干气中,被后续过程回收利用。
NOx 转化剂主要是将部分NOx还原成N2,从而减少对环境的污染。
我国目前用得较多的是SOx转移剂,已有多家研究单位或公司在研究和生产这类产品[4]。
2.2 国内外催化裂化工艺发展状况2.2.1渣油催化裂化技术进展目前,世界上渣油催化裂化(RFCC)工艺主要有Kellogg公司的HOC、S&W公司的RFCC、IFP/Total公司的R2R、UOP公司的RFCC、Shell公司的RFCC和Exxon 公司的Flexi cracking工艺。
这几种工艺已在世界各地运行多年。
目前,RFCC 加工原油残炭可达3% ~ 10%,镍和钒含量可达10 ~ 40μg/ g,平衡剂上金属沉积量最高可达10 000μg/g[5]。
然而,催化裂化反应过程的核心受提升管反应器技术一直未有突破。
其弊端表现为:提升管反应器过长,造成反应时间过长;由于积碳,因此使催化剂活性和选择性迅速下降;催化剂在上行过程中受重力作用产生滑落与返混;提升管下游部位的热裂化与非理想二次反应等。
针对提升管存在的缺陷,世界各大石油公司致力于新型RFCC工艺的开发。
开发重点放在反应技术方面:提高反应温度、缩短反应时间至15以内、消除反应器中催化剂和油气的返混、改善催化剂性能、改变反应器型式等。
有些工艺已经工业化,取得了较好的经济效益,有些还处于实验室研究或中试阶段的研究。
表1列出了RFCC新工艺、新技术的进展。
2.2.2多产柴油催化裂化技术进展2.2.2.1多产柴油和液化气的MGD技术MGD技术是中国石油化工股份有限公司石油化工科学研究院(RIPP)开发的以重质油为原料,利用常规催化裂化装置同时多产液化气和柴油,并可显著降低汽油烯烃含量的工艺技术。
该技术与常规催化裂化技术相比,具有以下特点:(1)采用粗汽油控制裂化技术,增加液化气产率,降低汽油烯烃含量,调节裂化原料的反应环境以增加柴油馏分的生成和保留。
(2)重质原料油在高苛刻度下、轻质原料油在低苛刻度下进行选择性反应,以增加重质原料油一次裂化和柴油馏分的生成。
(3)液化气和柴油产率明显大于常规的FCC技术,高价值产品(液化气、汽油和柴油)与常规FCC技术相当;(4)汽油中烯烃含量能够大幅度降低,且汽油辛烷值有一定提高。
2.2.2.2多产柴油的MDP技术RIPP在传统增产柴油工艺技术的基础上开发了催化裂化增产柴油的新工艺MDP。
该工艺具有以下特点:(1)可以加工重质、劣质的催化裂化原料。
(2)采用配套研制的增产柴油催化剂,且维持平衡剂的活性适中。
(3)应用原料组分选择性裂化技术,将催化裂化原料按馏分的轻重及其可裂化性能区别处理,在提升管反应器不同位置注入不同原料组分,使性质不同的原料在不同环境和适宜的裂化苛刻度下进行专利商/研究机构工艺名称工业化动态UOP 毫秒催化裂化技术 1套位于美国新泽西Cosatal公司Eagle Point炼油(MSCC)厂,为改造装置(2.8Mt/a),1994年开工;1套建于美国路易斯安那Trans American 炼油公司(5.0Mt/a),1999年开工;另一套装置将在今后在土库曼斯坦建成投产[7]下行床反应器停留时间S&W 快速段接触反应(QC) 中试 < 200msMobil 超短接触FCC工艺中试 < 500msWest Ontario大学渣油超短裂解工艺小型中试 <50ms清华大学下行管式FCC工艺专利技术 <500ms国内新工艺、新技术进展RIPP/北京设计院/燕山石化 VRFCC 第一套VRFCC工业装置是由北京燕山石化公司炼油厂的合作开发催化裂化装置改造而成,处理能力为800kt/a洛阳石化工程公司 ROCC—V 第一套ROCC—V型装置(100kt/a)1996年5月在洛阳石化工程公司炼油实验厂投产,1999年9月在青岛石化工厂投产1.0Mt/a工业化装置石油大学两段提升管FCC工艺中试反应。
(4)采用较为苛刻的裂化条件和适宜的回炼比,装置的加工量和汽油的辛烷值不会受到影响。
2.2.3低碳烯烃催化裂化技术进展目前,国外有多家公司推出了多产烯烃的FCC工艺技术,如UOP公司的Petro FCC工艺、公司的perlex工艺、Lummus公司的选择性裂化(SCC)工艺、Neste Oy 公司的NEXCC工艺。
20世纪80年代末,我国开始了低碳烯烃技术的研究,成功开发了以多产低碳烯烃和高辛烷值汽油为目的的FCC工艺家族技术。
目前,已工业化的技术有DCC、MGG、MIO、ARGG。
表2列出了几种典型多产烯烃的工艺。
2.2.4 生产清洁燃料催化裂化技术进展我国催化裂化汽油中烯烃含量高达40%-65%,远远高于我国车用汽油烯烃不大于35%的指标。
为此,RI即通过对催化裂化反应机理和烃类在不同类型反应器上得到的结果进行了综合分析,提出了生产清洁汽油的催化裂化新工艺(MIP)。
该工艺突破了现有催化裂化工艺对二次反应的限制,实现了可控性和选择性地进行裂化反应、氢转移反应和异构化反应。
可明显降低汽油烯烃含量并增加异丁烷产率,提出了一种生产清洁汽油组分的新概念。
另外,现有FCC装置可较容易地改造为MIP装置。
MIP工艺还可以和其他工艺藕合,为其他装置提供原料。
专利商/研究机构工艺名称工业化动态国外技术进展UOP Petro FCC 印度一套新建装置采用该工艺LOCC 还未见工业化报道Kellogg/Moblil Maxofin 中试:以Minas蜡油为原料,丙烯产率为18%Arco Chemical SuperflexLummus SCC 还未见工业化报道Neste Oy NEXCC 中试丙烯收率为15%。
一套120 ~160kt/a的半工业化装置于1999年建于芬兰Fortum的Porvoo炼厂,2002年实现工业化。
国内技术进展RIPP DCC—Ⅰ国内建有多套装置;另有一套建于泰国TPI(750kt/t) DCC—Ⅱ 1997年投产MGG 国内建有多套装置MIO 1995年在中国石油工业部兰州石化公司实现工业化ARGG 国内建有多套装置2.3 催化裂化催化剂技术进展2.3.1 渣油催化裂化催化剂由于对RFCC催化剂需求的增加,因此,近年来国外催化剂主要生产商(如Graee-Davision、Akzo-Nobel、Engelhard公司等)在渣油裂化催化剂研究方面开展了很多工作。
Grace-Davision公司生产的催化剂主要有Ramcat系列(我国镇海炼油化工股份有限公司炼油厂等几套装置正在使用)、Orion系列、XP系列(已用于30多套装置)、Astra系列(中国石油化工股份有限公司北京燕山分公司炼油厂和抚顺石化公司石油二厂使用过该系列催化剂,效果良好)、GKZ系列、Spectra系列。
Engelhard公司催化剂牌号主要有Ma,asiv系列、Vision系列、Advance系列、Dimension系列。
Akzo Nobel公司催化剂牌号主要有Centurion(已在9套装置上使用,我国洛阳石化总厂在使用国产催化剂CHV-l前也曾用过Centurion-43 L抗钒催化剂 )、Oetavision527、MC/MZ系列及以后开发的KMP/KOB系列。
CCIC公司催化剂主要有STW、DCT、ACZ,STW和DCT,已在日本国内多家FCC装置上使用。
小试结果表明,使用ACZ催化剂后,重循环油以上收率降低。
基于多年对渣油裂化催化剂的研究开发,RIPP认为渣油裂化催化剂应有梯度孔分布和梯度酸性中心分布,以对付具有不同分子大小和裂化性能的复杂原料;渣油裂化过程中基质的作用十分重要,其孔结构、酸中心性质和活性必须与沸石的活性匹配;沸石的裂化活性与氢转移活性也应有适当的平衡。