板类零件优化排样及余料利用
板材余料的有效利用

板材余料的有效利用---IE工作室众所周知,家具企业特别是以板式和实木为主的木制家具企业,原材料成本往往占整个产品总成本的40%以上。
近年来由于原材料特别是木制材料的价格大幅上涨,企业生产成本越来越高,加之市场环境的恶化,竞争日益激列,一个没有成本优势的企业根本无法存活。
如何提高材料利用率,如何降低生产成本是每个企业都必须认真对待的问题,同时也是经营者最为头疼的难题。
某定制家具企业经过长时间的深入研究,开创了大规模定制生产中关于余料管理的先进模式,使出材率在一年半的时间内,就由原来的70%左右提高到92%以上,仅此一项,一年就增加了100多万利润。
产生余料的原因要管好余料,首先要分析清楚余料产生的原因。
经过对板式车间生产过程的分析,余料产生的原因大致有以下几个方面:(1)板式开料领料由用料部门控制。
板料的领用包括什么板材、规格、数量由用料部门提出,这样难免出现使用部门只图自己方便好生产,很少或没有考虑如何根据生产情况选择合适的板材尽可能地提高板材利用率,降低生产成本的角度去领用板材;加之在计算板材用量时没有准确细致的板材用量定额,不清楚库存板材状况,领用的板材都是完整板件(1220*2440),只按流转卡上的规格、数量开领料单领用大板,从一开始起就没有成本意识,没有从源头上解决余料的问题,结果势必产生大量的余料,这也是家具企业管理中最为普遍的现象。
(2)板材的利用率低,画裁板图难,余料无法控制。
生产计划变动大,没有及时提供准确的周生产计划,以致无法快速地根据生产计划,将多个制令、多种不同的产品进行全面统筹,无法对多个裁板方案进行对比分析,从而确定最优的方案。
这也家具企业长期以来最为头疼的而没有解决的问题。
谈到裁板,许多企业对10%以上的浪费非常无奈。
其实,由于家具企业工作人员文化程度不高,生产批量小,同时在线生产的产品多,作业人员在短时间内既要考虑现场生产的产品及部件,又要考虑库存材料,并且需要经过大量多次的计算才能得出较好的裁板方案,这对现场来说很难做到。
板材下料优化方案

板材下料优化方案在木材加工行业中,如何最大程度地提高板材利用率和降低浪费是一个非常重要的问题。
传统的板材下料方式往往存在很大的浪费,而采用优化的板材下料方案可以有效地减少浪费,并提高生产效率。
本文将介绍一种常用的板材下料优化方案,通过优化下料方案来实现降低浪费,提高板材利用率。
一、了解板材规格和尺寸在制定下料优化方案之前,我们首先需要详细了解所使用的板材的规格和尺寸。
包括板材种类、厚度、长度、宽度等。
只有了解了板材的规格和尺寸,才能更好地制定下料方案,减少浪费。
二、利用计算软件进行优化可以借助计算机软件来进行板材下料的优化计算。
通过输入板材规格和需要裁剪的零件尺寸,计算软件可以自动生成最优的下料方案。
这些软件使用了高效的算法,可以快速且精准地进行优化计算。
例如,常用的下料软件有OptiCut、CutList Plus等。
三、合理设计零件尺寸在进行板材下料时,合理设计零件的尺寸也是非常重要的。
尽量避免设计过大或过小的零件,这样既可以减少浪费,又可以提高板材利用率。
同时,还可以考虑设计一些通用型的零件,以减少特定尺寸零件的数量,进一步降低浪费。
四、考虑边缘利用率和余料利用在进行板材下料时,除了面积利用率外,还要考虑板材的边缘利用率和余料利用。
通过合理规划下料方案,将板材边缘利用到最大化,并且合理利用余料,可以有效地减少浪费,提高板材利用率。
五、避免过多的切割在进行板材下料时,可以尽量避免过多的切割。
过多的切割不仅会增加加工的难度,还会增加浪费的可能性。
因此,在制定下料方案时,要避免过多的切割,尽量保持零件的形状和数量的简单性。
六、考虑批量生产的需求在制定板材下料方案时,还要考虑到批量生产的需求。
如果需要批量生产同样的零件,可以通过合理的下料方案来提高生产效率和板材利用率。
例如,可以将相同尺寸的零件集中进行下料切割,避免浪费和重复工作,提高生产效率。
七、严格控制切割误差和损耗在进行板材下料过程中,切割误差和材料损耗是无法完全避免的。
优化下料流程提高下料效率和材料利用率
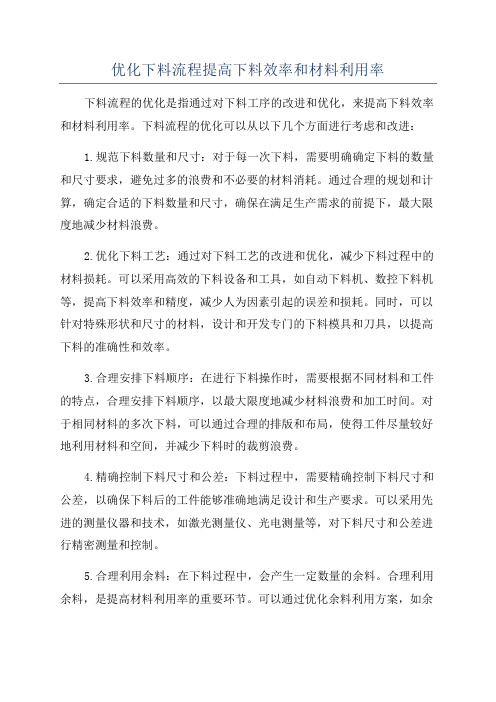
优化下料流程提高下料效率和材料利用率下料流程的优化是指通过对下料工序的改进和优化,来提高下料效率和材料利用率。
下料流程的优化可以从以下几个方面进行考虑和改进:1.规范下料数量和尺寸:对于每一次下料,需要明确确定下料的数量和尺寸要求,避免过多的浪费和不必要的材料消耗。
通过合理的规划和计算,确定合适的下料数量和尺寸,确保在满足生产需求的前提下,最大限度地减少材料浪费。
2.优化下料工艺:通过对下料工艺的改进和优化,减少下料过程中的材料损耗。
可以采用高效的下料设备和工具,如自动下料机、数控下料机等,提高下料效率和精度,减少人为因素引起的误差和损耗。
同时,可以针对特殊形状和尺寸的材料,设计和开发专门的下料模具和刀具,以提高下料的准确性和效率。
3.合理安排下料顺序:在进行下料操作时,需要根据不同材料和工件的特点,合理安排下料顺序,以最大限度地减少材料浪费和加工时间。
对于相同材料的多次下料,可以通过合理的排版和布局,使得工件尽量较好地利用材料和空间,并减少下料时的裁剪浪费。
4.精确控制下料尺寸和公差:下料过程中,需要精确控制下料尺寸和公差,以确保下料后的工件能够准确地满足设计和生产要求。
可以采用先进的测量仪器和技术,如激光测量仪、光电测量等,对下料尺寸和公差进行精密测量和控制。
5.合理利用余料:在下料过程中,会产生一定数量的余料。
合理利用余料,是提高材料利用率的重要环节。
可以通过优化余料利用方案,如余料利用方案的设计和规划,余料的再加工和利用等,有效地提高材料利用率,减少浪费。
6.加强质量管理:在下料生产过程中,加强质量管理是保证下料效率和材料利用率的关键。
通过建立和完善质量管理体系,加强对下料工艺和质量要求的控制和监督,及时发现和解决问题,以确保下料的质量和效率。
综上所述,通过规范下料数量和尺寸、优化下料工艺、合理安排下料顺序、精确控制下料尺寸和公差、合理利用余料和加强质量管理等措施,可以有效地提高下料效率和材料利用率,降低生产成本,提高企业竞争力。
排样的原则

排样的原则一、排样的概念先唠唠排样呢,就是在冲压生产中,对于冲压件在条料或者板料上的布置方法。
这就好比我们整理房间,要把东西合理地摆放,才能既节省空间,又方便取用一样。
在工业生产里,排样要是安排得好,那可就能节省好多原材料,提高生产效率,降低成本呢。
二、排样的原则大揭秘1. 提高材料利用率原则材料可是很宝贵的,就像我们口袋里的钱,能省一点是一点。
在排样的时候,要尽量让零件在板材上排列得紧密,减少废料的产生。
比如说,我们可以采用一些特殊的排样方法,像无搭边排样,这种排样方式就可以让材料的利用率大大提高。
不过这种排样方式对模具的精度要求比较高,就像做一件精细的手工艺品,得有精湛的手艺才行。
2. 操作方便原则这就像我们做饭,工具摆放得顺手,做菜才方便。
在排样的时候,要考虑到模具的结构和操作的便利性。
比如说,冲裁的方向要尽可能一致,这样在冲压的时候,就不需要频繁地调整模具的方向,操作工人也能轻松不少。
而且,零件在排样的时候,最好不要有太复杂的形状或者位置关系,不然在冲压的时候,模具可能就会出现故障,就像汽车发动机里的零件,如果安装得不合理,汽车就跑不动啦。
3. 保证冲裁件质量原则质量那可是产品的生命啊。
在排样的时候,要考虑到冲裁过程中零件的变形情况。
比如说,如果零件之间的距离太近,在冲裁的时候,就可能会因为材料的应力分布不均匀而导致零件变形。
这就好比我们盖房子,如果砖头之间的缝隙不均匀,房子就容易歪歪扭扭的。
所以,要合理地安排零件之间的距离和冲裁的顺序,保证冲裁出来的零件质量合格。
4. 模具结构简单原则简单的模具结构不仅制造起来容易,而且成本低,维修也方便。
在排样的时候,要尽量避免复杂的模具结构。
比如说,不要设计过多的冲孔和落料工序在同一个模具上,这样会让模具变得很复杂,就像一个机器上装了太多的零件,很容易出故障。
我们可以把一些工序分开,用多个简单的模具来完成,虽然工序多了一点,但是整体的效率和成本可能会更划算呢。
优化材料利用率的方法:提高效益

优化材料利用率的方法:提高效益提高材料利用率是降低定制成本、减少浪费和提升企业效益的重要手段。
以下是一些方法可以帮助提高材料利用率:1.优化设计方案:在产品设计阶段,应充分考虑材料利用率。
通过优化设计方案,减少材料消耗和浪费。
例如,采用更紧凑的布局、减少不必要的结构、合理利用材料的尺寸和厚度等。
2.标准化生产:标准化生产可以促进材料利用率的提高。
通过制定标准化的工艺流程、规范化的操作和统一的材料规格,实现材料的一致性和可互换性,降低材料损耗和浪费。
3.合理切割材料:在材料切割过程中,采取合理的切割方式和切割顺序,以提高材料的利用率。
利用计算机辅助设计软件进行精确排版和优化切割路径,减少废料和边角料,充分利用材料的尺寸和形状。
4.回收和再利用:对于生产过程中产生的废料和边角料,可以进行回收和再利用。
寻找合适的再利用途径,将废料用于其他产品或工艺中,减少浪费和环境污染。
5.提高工人技能:工人的技能水平对材料利用率有着直接的影响。
定期培训和技能提升计划可以帮助提高工人的技术水平,使其能够更熟练、准确地操作设备和进行加工,减少操作失误和浪费。
6.引入先进技术:采用先进的生产技术和设备可以提高材料利用率。
例如,引入智能化制造系统、数控机床等高精度设备,可以提高加工精度和材料利用率。
7.强化现场管理:加强现场管理,确保生产现场整洁有序,减少材料混放、错用和丢失的情况。
通过规范化的现场管理,可以提高材料的利用率并降低生产成本。
8.推行精益生产:精益生产是一种以消除浪费、提高效率为核心的生产方式。
通过推行精益生产,不断优化生产流程、减少浪费和提高效率,从而提升材料利用率。
通过以上方法,企业可以提高材料利用率,降低成本并减少浪费。
这不仅有助于提高企业的经济效益和市场竞争力,还有助于保护环境、实现可持续发展。
木板余料解决方案

025
400mm*555mm*15T
026
215mm*660mm*15T
027
135mm*660mm*15T
028
1220mm*290mm*18T
029
660mm*190mm*15T
030
310mm*310mm*15T
031
560mm*460mm*18T
032
1220mm*1060mm*15T
033
420mm*600mm*18T
103 pcs
014
540mm*400mm*18T
43 pcs
015
160mm*1220mm*18T
34 pcs
016
245mm*1220mm*18T
94 pcs
017
240mm*415mm*18T
36 pcs
截止日期:2005/8/1.来源于cutting 物料.
编号
尺寸规格 中纤板
001
110mm*610mm*15T
002
145mm*675mm*15T
003
1380mm*140mm*15T
004
1380mm*148mm*15T
005
1380mm*130mm*15T
006
120 mm*650mm*15T
数量
562 233 282 118 255 463 104 154 252 114 127
66 199
90 310 378
67 164
63 200 197
19 240 132
54 61 60 51 63 204 56 80 80 80 80 83 84 158 55 124
单位
pcs pcs pcs pcs pcs pcs pcs pcs pcs pcs pcs pcs pcs pcs pcs pcs pcs pcs pcs pcs pcs pcs pcs pcs pcs pcs pcs pcs pcs pcs pcs pcs pcs pcs pcs pcs pcs pcs pcs pcs
板料优化排样问题

板料优化排样问题摘要、在材料加工领域,板料优化排样是实现薄板和厚板材料充分利用的一个常见问题。
该问题是典型的NP完全问题,其求解过程复杂,求解耗时大,难以获得精确解。
这不利于该问题的工程应用,为此,目前学术界提出了多种用于解决该问题的近似算法,求取在工程应用中可接受且耗时合理的优化排样方案。
该文在对板料排样问题进行阐述的基础上,对近年来国内在板料优化排样问题方面所开展的研究进行了分析,对板料排样问题的发展前景进行了展望。
关键词、优化排样问题;板料优化;算法中图分类号、TP39文献标识码、A文章编号、1009-3044(2011)20-4983-03OnPlateNestingOptimizationProblemLIWei1,LIJian2(1.AcademicAdministrationofGuizhouNormalUniversity,Gu iyang550001,China;2.SchoolofMaterialsScienceandEngine eringofJiangsuUniversity,Zhenjiang212013,China)Abstract:PlatenestingoptimizationproblemisaCommonprob lemforsheetandplatematerialstoachievefulluseinthefiel dofmaterialprocessing.TheproblemisatypicalNP-completeproblem.Theproblemsolvingprocessiscomplex,tim e-consumingtosolvelarge,difficulttoobtainexactsolutions .Thisisnotconducivetotheproblemofengineeringapplicati ons,forwhich,forthecurrentacademicmadeavarietyofappro ximationalgorithmstosolvetheproblemofstrikeintheengin eeringapplicationsandtime-consumingreasonablyacceptableoptimalnestingprogram.Thispaperdescribesthesheetmetalnestingproblems,analysis oftherecentdomesticoptimalnestinginsheetissuesresearc hcarriedout,andlookedtotheproblemofsheetmetalnestingp rospects.Keywords:optimalnestingproblems;sheetoptimization;alg orithm在材料的加工制造中,原材料的规格和目标件规格之间具有复杂的组合关系。
板材优化下料方案研究
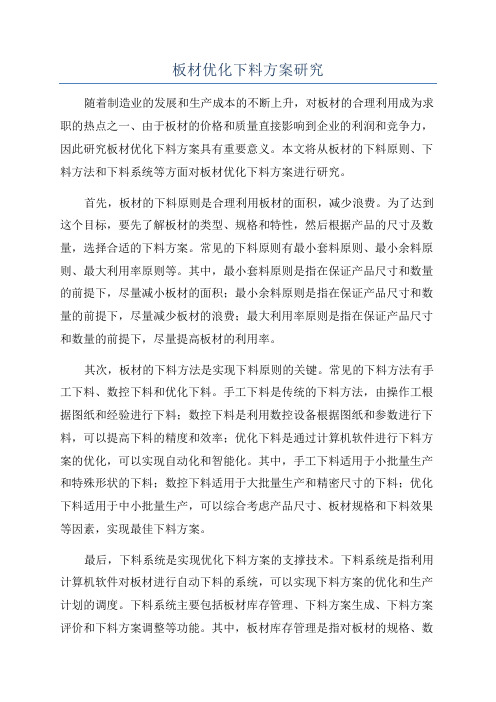
板材优化下料方案研究随着制造业的发展和生产成本的不断上升,对板材的合理利用成为求职的热点之一、由于板材的价格和质量直接影响到企业的利润和竞争力,因此研究板材优化下料方案具有重要意义。
本文将从板材的下料原则、下料方法和下料系统等方面对板材优化下料方案进行研究。
首先,板材的下料原则是合理利用板材的面积,减少浪费。
为了达到这个目标,要先了解板材的类型、规格和特性,然后根据产品的尺寸及数量,选择合适的下料方案。
常见的下料原则有最小套料原则、最小余料原则、最大利用率原则等。
其中,最小套料原则是指在保证产品尺寸和数量的前提下,尽量减小板材的面积;最小余料原则是指在保证产品尺寸和数量的前提下,尽量减少板材的浪费;最大利用率原则是指在保证产品尺寸和数量的前提下,尽量提高板材的利用率。
其次,板材的下料方法是实现下料原则的关键。
常见的下料方法有手工下料、数控下料和优化下料。
手工下料是传统的下料方法,由操作工根据图纸和经验进行下料;数控下料是利用数控设备根据图纸和参数进行下料,可以提高下料的精度和效率;优化下料是通过计算机软件进行下料方案的优化,可以实现自动化和智能化。
其中,手工下料适用于小批量生产和特殊形状的下料;数控下料适用于大批量生产和精密尺寸的下料;优化下料适用于中小批量生产,可以综合考虑产品尺寸、板材规格和下料效果等因素,实现最佳下料方案。
最后,下料系统是实现优化下料方案的支撑技术。
下料系统是指利用计算机软件对板材进行自动下料的系统,可以实现下料方案的优化和生产计划的调度。
下料系统主要包括板材库存管理、下料方案生成、下料方案评价和下料方案调整等功能。
其中,板材库存管理是指对板材的规格、数量和位置进行管理,通过对库存的分析和预测,实现下料方案的合理安排;下料方案生成是指根据产品的尺寸和数量,以及板材的规格和利用率等要求,生成符合要求的下料方案;下料方案评价是指对下料方案进行评价和分析,比较不同方案的优劣,提供合理的决策依据;下料方案调整是指根据实际生产情况,对下料方案进行调整和优化,及时地满足生产需求。
- 1、下载文档前请自行甄别文档内容的完整性,平台不提供额外的编辑、内容补充、找答案等附加服务。
- 2、"仅部分预览"的文档,不可在线预览部分如存在完整性等问题,可反馈申请退款(可完整预览的文档不适用该条件!)。
- 3、如文档侵犯您的权益,请联系客服反馈,我们会尽快为您处理(人工客服工作时间:9:00-18:30)。
— 152 —
生产。所以对回收的余料必须进行分割裁剪:板材按有用部分的最大
内接矩形裁剪。然后分规格、牌号、品种存放。为保证所存放的余料规
所示。
图 1 排样功能实现流程图 3.板材余料的利用及回收管理办法 板类零件制造企业使用的原材料主要是板材,占到原材料总量的 80%以上。在板材使用过程中,往往会产生许多余料,随着生产的进行 这样的余料越来越多。由于没有余料回收再利用的管理机制,造成的 余料浪费严重影响了企业的经济效益。板材余料的无管理状态阻碍了 企业的进一步发展。目前,企业基本上把余料板材作为废料处理,而作 为废料处理的价格仅为进货价的 1/6 左右,如果能把余料科学管理、合 理利用,可以显著提高企业的经济效益。 有时工人在加工时出现了差错,造成了材料浪费,害怕承担责任, 就自行找一块余料板材,重新加工零件,余料的这种自发式应用,给企 业的产品质量带来了安全隐患。 板材余料的随意堆积给企业的生产带来了不便和安全隐患。余料 由于没有清楚的标识,从而无法进行及时的清理,导致堆放在生产区 域,占据大量操作空间,给生产带来很大的不便和安全隐患。 余料管理方面的空白给企业全面实施信息化管理带来了极大的困 难。由于余料管理没有包含在企业信息化控制之内,成为企业信息化 的盲点。企业信息化是将企业的生产过程、物料移动、事务处理、现金 流动、客户交互等业务过程数字化,通过各种信息系统网络加工生成新 的信息资源,提供给各层次的人们洞悉、观察各类业务中的一切信息, 以作出有利于生产要素组合优化的决策,使企业资源合理配置,以使企 业能适应瞬息万变的市场经济竞争环境,求得最大利益。而余料板材 的管理是企业物流的重要组成部分。 提高材料的利用率,降低生产成本,已引起企业的高度重视,板材 余料的回收与再利用应规范管理,以省时省料,充分发挥余料的作用。[3] 由于搁置在车间的生产余料大多数为规格、牌号、品种混乱,长短、 大小、几何形状各异,若不进行一次切割裁剪、规范整理就难以再用于
0.引言 下料作为板类零件制造的第一道工序,工作虽然简单,但是影响很 大。板材下料方法主要有剪切下料、冲切下料、火焰切割和等离子切割 等。在进行下料之前需要给出零件在板材的排布方案,使所需材料最 少,也就是要进行优化排样。 排样方案直接影响材料利用率、零件的可制造性和加工效率。在 板类零件的制造中,金属板材是消耗的主要原材料之一,零件的原材料 费用在制造成本占有相当大比重,提高材料利用率和加工效率是降低 零件制造成本的重要措施。因此,高效、优良的排样技术是板类零件制 造中的关键技术之一。[1] 1.优化排样 1.1 板类零件的优化排样 板类零件的优化排样问题,是指在一组给定的原始板材上,尽可能 多的排放需要的二维零件产品,使得板材利用率最大,以减少废料。其 实质是一个二维布局的问题,属于排料优化问题中的二维情况。[2] 板类零件的排样手段经历了从手工排样到计算机辅助手工排样再 到自动化排样三个阶段,具体如下: 手工排样:对于形状简单的零件,由排样人员凭经验手工排样;对 复杂零件制作样板,利用样板手工排样,或在切割时现场手工排样。 计算机辅助手工排样:在绘图软件的支持下,操作者在计算机屏幕 上绘出板材以及需要排样的板类零件,模仿手工铺排样板,利用绘图软 件的图形平移、旋转等功能,使板材的空白部分尽量少,最终得到材料 利用率较高的排样方案,完成排样。同手工排样一样,这种排样方法也 要求操作者必须具备高度的排样技巧,而且当需要排样的零件种类和 数量增加时,排样处理需要很长的时间。 自动化排样:自动化排样是根据一定的排样算法,将排样过程加以 整理使之程序化,排样时只要把排样条件输入计算机,计算机就能按照 排样程序自动的配置样件,其所得排样结果主要取决于排样算法。排 样方案完全由计算机给出,在绝大多数情况下都能自动给出接近最优 的排样方案,无需人工干预。 1.2 板类零件制造中的排样类型 板类零件种类繁多,根据各自的特点有着不同的下料方式,需要先 进行排样再下料的下料加工形式有:冲切、剪切、火焰切割、等离子切割 等。由于不同种类的下料方式直接影响排样方式的选择,因此,需要根 据下料方式对排样问题进行分类。 (1)矩形件组合排样 矩形件组合排样是针对剪切下料的板类零件,在考虑剪切余量和 材料纤维方向等制造因素前提下,在给定的矩形板材上,确定一批给定 尺寸和数量的矩形毛料排布方案,并且使所用的板材最少。 (2)单种零件排样 单种零件排样是针对冲压落料的板类零件,需要确定冲裁件在条 料或板材上的布置方法,使材料利用率最高。选择排样方案时,除了材 料利用率之外,还应考虑到模具制造和使用是否方便、板材的纤维方向 是否满足后续工序要求等因素。 在综合考虑冲压模具设备的制造成本的前提下,针对冲压落料的 板类零件也可以采用套裁。 (3)曲线外形零件组合排样 曲线外形零件组合排样是针对火焰切割和等离子切割下料的板类 零件,需要综合考虑割矩等各项制造参数,对若干种材质和厚度相同, 数量一定,曲线外形的平板零件或毛料,在给定矩形板材内寻找一种全 局最优(或近似最优)方案,确定每块板料上的零件、零件的方位,使耗材 最少。 2.基于 AutoNest 的板类零件优化排样工具的开发 由以上分析可知板类零件的排样问题根据下料方式的不同分为矩 形件组合排样、单种零件排样、曲线外形零件组合排样,为实现系统的 排样功能,嵌入了 AutoNest 排样软件,并在此基础上进行了二次开发, 实现了面向不同排样类型的板类零件优料利用研究
南京农业大学工学院/江苏省智能化农业装备重点实验室 夏荣霞
[摘 要]本文介绍了板类零件制造中的排样问题,并开发了基于 AutoNest 的板类零件排样工具。分析了企业板料余料的利用现状, 研究了板材余料回收再利用的管理办法,并就排样零件数目较少、零件数目较多和几块余料板材的组合代替整板这三种情况进行了 余料再利用的分析。 [关键词]板类零件 排样 余料再利用