(产品管理)塑胶产品设计缺陷及改良方法
塑料件缺陷及改进措施

塑料件缺陷及改进措施塑料件在实际应用中存在一些常见的缺陷,这些缺陷可能会对产品的质量和性能产生负面的影响。
下面将介绍一些常见的塑料件缺陷,并提出相应的改进措施。
1.熔接线痕:在注塑过程中,由于熔融塑料的流动不均匀,容易形成熔接线痕。
这些痕迹可能会导致产品强度降低、疲劳性能差等问题。
改进措施:调整注塑工艺参数,如制定适当的注射速度、保持压力等,以促进塑料的均匀流动,减少熔接线痕的产生。
2.气泡:注塑过程中,由于塑料内含有的气体随着高温熔融逸出,易形成气泡。
气泡会导致产品的密封性能下降、外观质量差等问题。
改进措施:提高注塑设备的真空度,减少气体残留。
此外,在塑料原料中加入消泡剂,能够降低气泡的产生。
3.龟裂:塑料零件在冷却过程中,由于不均匀的收缩率和内应力,易出现龟裂缺陷。
这种缺陷会导致产品的强度下降、易开裂等问题。
改进措施:采用合适的冷却方法,如适当提高冷却介质的温度、均匀冷却等,以减少塑料件的收缩和内应力的产生。
4.比色差:一些塑料件在生产过程中,由于塑料原料的不均匀混合或加工温度控制不当,易形成色差。
这会导致产品的外观质量差,影响产品的整体美观度。
改进措施:严格控制塑料原料的配比,确保原料的均匀混合。
同时,加强对注塑设备的温度控制,保持适当的加工温度,有助于减少温度对产品颜色的影响。
5.纹理不良:在塑料件表面会产生一些不良的纹理,如模具印痕、晶化痕迹等。
这些缺陷会降低产品的表面质量、减少产品的美观度。
改进措施:优化模具的设计和制造工艺,减少模具表面的磨损和粗糙度。
同时,在注塑过程中控制好注塑温度和注塑压力,以减小纹理缺陷的产生。
总而言之,塑料件的缺陷主要体现在熔接线痕、气泡、龟裂、比色差和纹理不良等方面。
为了改善塑料件的质量和性能,应从加工工艺、原料控制、模具改进等方面入手,提高生产工艺的稳定性和可控性。
同时,加强质量检测和监控,及时发现和解决问题,以确保塑料件的质量满足产品要求。
塑胶件常见的缺陷产生原因及解决办法

塑胶件常见的缺陷产生原因及解决办法一、设计方面的缺陷:1.不合理的尺寸设计:塑胶件的尺寸设计不合理可能导致尺寸偏差过大、尺寸不一致等问题。
解决方法是根据塑胶件的具体用途和要求进行合理的尺寸设计,并进行合适的工艺分析和模流分析。
2.没有考虑到材料的特性:不同塑料材料具有不同的热胀冷缩系数、熔融温度等特性,设计时没有考虑到这些特性可能导致尺寸偏差、变形等问题。
解决方法是根据塑料材料的特性进行合适的设计和模具制造选型。
3.模具设计问题:模具设计不合理或者制造质量不过关可能导致塑胶件的缺陷问题。
解决方法是进行合理的模具设计,并选择专业的模具制造厂家。
4.不合理的壁厚设计:塑胶件的壁厚设计不合理可能导致塑胶件变形、收缩不均匀等问题。
解决方法是根据塑胶件的材料特性和实际使用要求进行合理的壁厚设计。
二、材料方面的缺陷:1.材料质量问题:不合格的原料质量可能导致塑胶件出现异味、颜色不均匀等问题。
解决方法是选择合格的塑料原料供应商,并进行原料的严格检验。
2.材料混合不均匀:塑料材料在加工过程中没有充分混合均匀可能导致塑胶件的颜色不均匀等问题。
解决方法是进行充分的原料预处理和混炼,确保塑料材料的均匀性。
3.熔体温度不均匀:塑料材料在注塑过程中温度不均匀可能导致塑胶件尺寸偏差、表面气泡等问题。
解决方法是调整注塑机的温度控制系统,确保熔体温度均匀稳定。
三、工艺方面的缺陷:1.注塑工艺参数设置不当:注塑过程中,如射胶压力、射胶速度、冷却时间等工艺参数设置不当可能导致塑胶件出现尺寸偏差、气泡、表面缺陷等问题。
解决方法是根据塑料的特性和产品要求进行合理的工艺参数设置。
2.模具温控不均匀:模具温度不均匀可能导致塑胶件出现收缩不一致、尺寸偏差等问题。
解决方法是进行模具温度分析和温控系统的优化。
可以采用热流道模具、快速温度控制系统等技术手段解决问题。
3.模具保养不当:模具的使用寿命长,如果没有进行定期的保养和维修可能导致塑胶件出现模纹、模具磨损等问题。
塑料件缺陷原因及改进方法
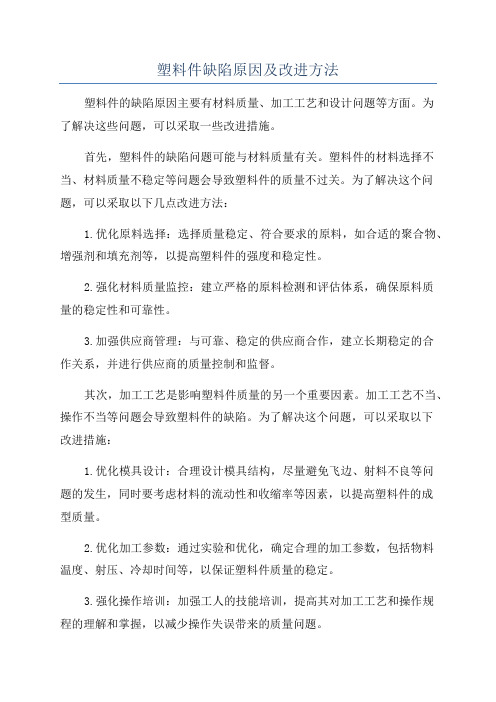
塑料件缺陷原因及改进方法塑料件的缺陷原因主要有材料质量、加工工艺和设计问题等方面。
为了解决这些问题,可以采取一些改进措施。
首先,塑料件的缺陷问题可能与材料质量有关。
塑料件的材料选择不当、材料质量不稳定等问题会导致塑料件的质量不过关。
为了解决这个问题,可以采取以下几点改进方法:1.优化原料选择:选择质量稳定、符合要求的原料,如合适的聚合物、增强剂和填充剂等,以提高塑料件的强度和稳定性。
2.强化材料质量监控:建立严格的原料检测和评估体系,确保原料质量的稳定性和可靠性。
3.加强供应商管理:与可靠、稳定的供应商合作,建立长期稳定的合作关系,并进行供应商的质量控制和监督。
其次,加工工艺是影响塑料件质量的另一个重要因素。
加工工艺不当、操作不当等问题会导致塑料件的缺陷。
为了解决这个问题,可以采取以下改进措施:1.优化模具设计:合理设计模具结构,尽量避免飞边、射料不良等问题的发生,同时要考虑材料的流动性和收缩率等因素,以提高塑料件的成型质量。
2.优化加工参数:通过实验和优化,确定合理的加工参数,包括物料温度、射压、冷却时间等,以保证塑料件质量的稳定。
3.强化操作培训:加强工人的技能培训,提高其对加工工艺和操作规程的理解和掌握,以减少操作失误带来的质量问题。
此外,塑料件的设计问题也会导致质量缺陷。
设计不当、结构不合理等问题会影响塑料件的使用寿命和功能。
1.优化产品设计:在设计阶段就要充分考虑材料特性、工艺要求和使用环境等因素,合理确定塑料件的结构和尺寸,以提高产品的可靠性和使用寿命。
2.强化模拟分析:通过使用CAD、CAE等软件工具进行模拟分析,预测设计在使用过程中的变形、应力分布等问题,在设计阶段就可以进行修正和优化。
3.进行实际测试:在设计验证阶段进行实际测试,包括强度测试、耐久性测试等,以验证设计的合理性和可靠性。
综上所述,塑料件的缺陷问题可能与材料质量、加工工艺和设计问题有关。
通过优化原料选择、加强材料质量监控、优化模具设计、优化加工参数、强化操作培训、优化产品设计、强化模拟分析和进行实际测试等改进方法,可以有效解决这些问题,提高塑料件的质量和可靠性。
塑件缺陷原因及改善方法

塑件缺陷原因及改善方法塑件是一种常见的工程材料,广泛应用于汽车、家电、电子、医疗设备等领域。
然而,在塑件生产过程中,常常会出现一些缺陷,如气泡、毛刺、热缩、变形等问题,这些缺陷会影响塑件的质量和性能。
因此,了解塑件缺陷的原因,并采取相应的改善方法,对于提高塑件质量和性能具有重要意义。
首先,塑件缺陷的原因有多种,下面是一些常见的原因及相应的改善方法:1.气泡:气泡是塑件生产过程中常见的缺陷,通常是由于原料中含有挥发性成分,或者模具中有气体积聚引起的。
改善方法包括:使用质量稳定的原料,避免使用含有挥发性成分的原料;在塑件生产过程中提高注塑压力,减少气泡的生成;对模具进行定期维护,清除模具中的积聚气体。
2.毛刺:毛刺是塑件表面出现的细小突起,通常是由于模具不平整或模具开合不良引起的。
改善方法包括:对模具进行定期检修和研磨,保持模具的平整度;调整模具开合速度和压力,使开合动作更加平稳;在设计模具时考虑减少毛刺的生成。
3.热缩:塑件在冷却后会发生热缩现象,导致尺寸变小。
这是由于塑料在冷却过程中会收缩引起的。
改善方法包括:在设计模具时考虑塑件的热缩率,合理设置模具尺寸,使得塑件在冷却后能得到正确的尺寸;控制注塑过程中的冷却时间和温度,避免过快或过慢的冷却导致过大的热缩。
4.变形:塑件在注塑过程中可能会发生变形,导致尺寸不准确或形状失真。
这是由于塑料在注塑过程中由于内应力不平衡引起的。
改善方法包括:优化模具设计,使模具在注塑过程中能够充分填充塑料,并保持良好的冷却效果;控制注塑过程的温度、压力和速度,减少内应力的释放。
此外,还有一些其他常见的塑件缺陷,如熔流线、白斑、开裂等。
这些缺陷的原因和改善方法也各不相同,需要具体问题具体分析。
总的来说,塑件缺陷的原因多种多样,通过针对不同的原因采取相应的改善方法,能够有效地提高塑件的质量和性能。
对于塑件生产企业来说,建立完善的质量控制体系,加强原材料的筛选和控制,定期维护和检修模具,改进注塑工艺,都是改善塑件质量和性能的重要措施。
塑料制品缺陷及改善措施
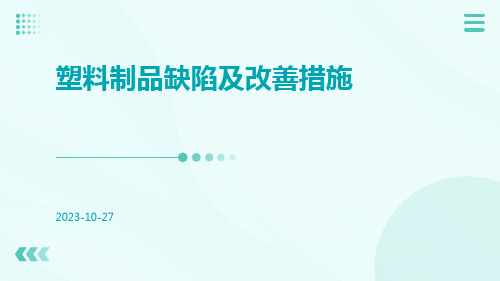
产生原因与危害
产生原因
塑料制品缺陷的产生原因很多,包括原材料质量不好、配方不合理、加工工 艺不当、设备故障、操作失误等。
危害
塑料制品缺陷会严重影响产品的质量、性能和外观,降低产品的使用价值和 寿命,甚至会对人体健康和安全造成威胁。
银纹
银纹是由于塑料在填充过程中混入的空气没有及 时排出而形成的,类似于气泡的一种缺陷。
银纹的产生可能是由于注射压力不足、注射速度 过快、模具温度不当等原因造成的。
银纹通常在塑料制品的表面或内部出现,形状为 细小的条状或网状。
改善措施:可以通过调整注射压力、注射速度和 模具温度来减少银纹的产生。在生产过程中,也 可以通过使用真空装置来帮助排出空气,从而避 免银纹的产生
VS
提高模具制造精度
采用高精度的数控机床等加工设备,提高 模具的制造精度,以减少制品缺陷。
调整生产工艺
优化注塑工艺
根据不同的塑料材料和制品要求,调整注 塑温度、压力和时间等工艺参数,以获得 理想的制品质量。
研究生产工艺优化方案
通过对生产工艺的研究和试验,找出最佳 的生产工艺参数,提高制品的质量和稳定 性。
裂纹
裂纹是由于塑料制品在冷却过程中产生的内应力 超过了塑料的抗拉强度而形成的。
裂纹的产生可能是由于注射速度过快、模具温度 过低、塑料的流动性差等原因造成的。
裂纹通常出现在塑料制品的表面或内部,形状为 线形或网状。
改善措施:可以通过降低注射速度、提高模具温 度、改善塑料的流动性来减少裂纹的产生。另外 ,可以通过调整塑料的配方,加入增韧剂等改性 剂来提高塑料的抗拉强度,从而减少裂纹的产生
塑胶产品外观不良改善管控方案

塑胶产品外观不良改善管控方案一、塑胶产品外观不良的原因1. 原材料问题:塑胶产品的外观质量与原材料的质量密切相关。
如果原材料的质量不稳定或掺杂了杂质,就会导致产品表面出现气泡、色差、瑕疵等问题。
2. 生产工艺问题:塑胶产品的生产过程中,如果温度、压力、注塑速度等工艺参数控制不当,就会导致产品外观不良。
比如温度过高会导致熔融塑料流动性增加,容易产生短射、缩短等问题。
3. 模具问题:模具的质量和设计也会对产品外观产生影响。
如果模具的表面粗糙度不达标或者设计不合理,就容易导致产品表面出现模纹、毛刺等问题。
二、改善管控方案的制定1. 优化原材料选用:选择质量稳定的原材料供应商,并与供应商建立长期稳定的合作关系。
同时,建立原材料质量检验标准,对原材料进行全面检测,确保其符合要求。
2. 优化生产工艺:制定严格的生产工艺流程,并进行员工培训,提高员工的操作技能。
同时,建立完善的生产工艺控制系统,定期对关键工艺参数进行监控和调整,确保产品质量稳定。
3. 优化模具设计和制造:与专业的模具设计师合作,进行模具的设计和制造。
确保模具的表面粗糙度达到要求,并且模具结构合理,以提高产品的外观质量。
三、改善管控方案的实施1. 建立质量管理体系:制定塑胶产品质量管理手册,明确各个环节的责任和要求。
同时,建立全面的质量管理体系,包括原材料进货检验、生产过程控制、产品出货检验等。
2. 定期进行质量检查:制定检查计划,定期对产品进行抽样检验,包括外观质量、尺寸偏差等方面。
对不合格产品进行分类处理,并分析原因,及时采取纠正措施。
3. 进行质量培训:对质量管理人员和生产操作人员进行培训,提高其质量意识和操作技能。
培训内容包括质量控制知识、工艺参数调整方法等。
4. 建立反馈机制:建立客户投诉反馈机制,及时处理客户反馈的问题,并进行分析和改进。
同时,建立内部质量反馈机制,对内部质量问题进行跟踪和整改。
总结:通过对塑胶产品外观不良的原因进行分析,并制定和实施改善管控方案,可以有效提高塑胶产品的外观质量。
(产品管理)注塑产品缺陷的解决
(产品管理)注塑产品缺陷的解决(产品管理)注塑产品缺陷的解决注意:1)放电加工原理,放电加工是利用电能转换成工件热能,使工件急速熔融的壹种热性加工方法。
放电加工时,电极和工件的间隙中产生过渡电弧放电现象,进而对工件产生热作用,同时,加工中液体由于受到放电压力及热作用产生气化爆发现象,此时工件的熔融部份,将伴随液体气化融入加工液中,工件因放电的作用产生放电痕,如此反复进行,我们所希望的形状便可加工完成了。
2)线切割原理,铜丝接近工件(且未和工件接触),对工件及铜线加上电压而产生电弧和高温(9000o C—10000o C),融蚀后将金属残屑吹出,铜丝继续前进,工件冷却后即形成粗糙的被切割面。
七、塑胶射出成型产品的外观问题和对策1、塑胶射出成型产品的外观问题积风(AirTrap);发赤(Blush);毛边(Flash);流痕(FlowLineorFlowMark);喷流(蛇纹)(Jetting);短射(ShortShot);凹陷或缩孔(SinkMarkorVord);条纹(Streak);熔接线(WeldLine)2、积风——AirTrap积风的定义:空气或气体不及排出,被溶胶波前包夹于型腔内。
●成品1)壁厚差异太大,产生跑道效应(RaceTrackEffect),壁厚差异太大时,薄壁处塑流迟缓,溶胶循厚壁快速超前,有可能对型腔中空气或气体进行包抄,行程积风。
2)CAE能够预测充填模式(FillingPattern)和可能的积风点。
更改厚度分布,使壁厚尽可能保持均壹,以避免积风。
●模具1)浇口(Gate)位置不当:a.浇口位置不当时,塑流有可能包抄空气或气体,形成积风;b.CAE能够预测充填模式(FillingPattern)和可能的积风点。
更改浇口位置,能够改变充填模式,积风有可能避免。
2)流道(Runner)或浇口尺寸不当:a.多浇口设计时,流道或浇口尺寸如果不当,塑流有可能赶超空气或气体,形成积风;b.CAE 能够预测充填模式(FillingPattern)和可能的积风点。
产品缺陷及其改善方法(上)
常见塑胶制品缺陷及其改善方法(上)作者:admin 时间:2013-08-27 00:04制品质量包括内部质量和表观质量,内部质量包括内应力,冲击强度,制品收缩,熔合强度等,了解这些对我们塑胶模具设计有很大的帮助,下面讲述的是制品常见的各种表观缺陷:一、凹陷,缩孔,气孔1.产生原因:原料吸湿性太大,干燥不好,制品壁厚不均,模腔压力不足或没有把存于腔内的空气排除而形成阻隔使熔体不能与模具表面全部按触,或因物料冷却速率降低其使制品表面出现严重凹陷,而缩孔位置多发生在筋表面和远离浇口位置.2.防止办法:在制品设计方面要防止由于筋造成壁厚不均,在选择材料方面选取收缩率小的材料,模具方面在壁厚地方开设支流道,工艺方面要降低模温,熔体温度.增加注射压力、保压时间和注射量,对容易发生缩孔的地方加强冷却,增加浇口截面尺寸.二、无光泽,冷白,搓伤及皱纹1.产生原因:这类缺陷的产生大都是因为模具温度过低,聚合物熔体温度过高,冷却过快所致.当熔体还在充模时,在型腔壁上就形成了很硬的壳.壳层受到各种力的作用使之泛白变浑,严重者壳层可能被撕破和皱纹.产生此类现象的另一个原因是熔体在模内发生了不规则的脉动流动,如在浇口尺寸很小,注射速度又很大时,聚合物熔体细流射入模腔,细射流经过一段时间表面己冷却再与后续熔体熔合时,就会出现此类缺陷.2.防止办法:提高模具温度,加大流道,浇口.三、银丝与剥层1. 防止办法:选择好干燥设备和干燥工艺,将含湿量降到最低值.工艺方面降低熔体温度,提高模温,稳定喷嘴温度,加大背压,模具方面加开排气槽.四、烧焦,暗纹及暗斑1.产生原因:暗纹或暗斑出现多是因物料过热分解而引起,有的是因为塑化不均匀,从外观上看呈暗斑痕,有的是因为异物所致,冲模时模内空气压缩,温度升高产生烧焦,多发生在熔合缝处.2.防止办法:物料干燥充分,降低熔体温度,提高背压,模具方面改善排气.五、翘曲,变形1.产生原因:聚合物的组织相应力,机械应力,热胀冷缩应力(温度应力)残余在制品内部所致,一般结晶型比非结晶型大.2.防止办法:减小取向,增大浇口尺寸,适当降低熔体和模具温度,加大注射速率,适当延长注射保压时间,减小浇口处压力,制品方面结构合理,改善脱模斜度表面粗糙度.顶出位置,面积等.六、龟裂1.产生原因:分子链在应力作用下沿力的方向上排列的裂纹,当脱模顶出力不平衡时,脱模造成真空吸力引起龟裂2.防止办法:采用消除内应力的工艺办法,如提高熔体温度和模具温度,降低注射力,采用退火处理等七、熔合缝1.产生原因:两股以上的熔体合拢时,波前锋受到异物阻隔气体杂质所形成.2.防止办法:适当提高模具温度和熔体温度,提高注射力和注射速度,模具上加开排气,增设冷料井,调整片等.。
塑胶件常见缺陷产生的原因及解决方法
塑胶件常见缺陷产生的原因及解决方法1.原材料质量问题:塑胶件常见的原材料问题包括原材料中含有杂质、原料失效、原料配比不正确等。
这些问题会导致塑胶件的质量下降和性能降低。
解决方法是对原材料进行严格的检验和筛选,确保原材料的纯度和质量。
2.模具设计问题:模具设计不合理可能导致塑胶件的缺陷,例如模具壁厚不均匀、模腔表面粗糙等。
解决方法是对模具进行合理设计,确保模具的结构和尺寸满足产品要求,并提高模具的制造工艺和加工精度。
3.注塑工艺问题:注塑过程中的工艺参数设置不当会导致塑胶件出现缺陷,例如温度不稳定、压力不均匀、注射速度过快等。
解决方法是优化注塑工艺参数,确保温度、压力、速度等参数的稳定和均匀。
4.模具磨损和损坏:长时间使用会导致模具磨损和损坏,影响塑胶件的质量和外观。
解决方法是加强模具的保养和维护,定期进行模具清洁和润滑,并进行必要的修复和更换。
5.后道工艺问题:塑胶件的后道加工也可能引发缺陷,例如焊接不牢固、喷涂不均匀等。
解决方法是加强后道工艺的控制,提高工艺的稳定性和一致性。
综上所述,要解决塑胶件常见缺陷的问题,需要从原材料选择、模具设计、注塑工艺、模具维护和后道工艺等方面入手,通过优化和控制各个环节,提高产品的质量和性能。
同时,还需要建立健全的质量管理体系,对生产过程进行全面监控和检测,及时发现和解决问题。
最后,还应该加强员工的培训和技能提升,提高操作技术和质量意识,提高产品的一致性和稳定性。
只有通过不断改进和严格控制,才能有效降低塑胶件的缺陷率,提高产品的质量和市场竞争力。
塑胶产品常见缺陷及改善办法
缺陷:光泽不一 Defect:Gloss differences
光泽不一
光泽不一改善对策
工艺:1.提高注射速度及注射压力2.提高保压压力及保压时间3.提高料筒温度模具:1.均匀模腔表面温度
缺陷: 表面斑点 Defect:Spots on surface
缺陷:走胶 Defect:incompletely filled parts
缺胶
走胶改善对策
工艺:1.提高注射速度及注射压力2.提高保压压力及保压时间3.提高料筒温度4.提高背压模具:1.增大浇口及流道截面积2.提高模腔表面温度3.改善模具排气
缺陷:披锋 Defect: flash
皱纹
皱纹改善对策
工艺1.提高注射速度2.提高注射压力及保压压力3.提高料筒温度模具1.增大浇口及流道截面积2.提高模腔表面温度
缺陷: 混色 Defect: color streaks
混色
混色的改善对策
工艺1.提高背压2.降低螺杆转速,以增加混炼时间3.提高料筒温度4.增加残量机器1.选用混炼型喷嘴(探针载流/滑动载流)2.选用BM螺杆
9、静夜四无邻,荒居旧业贫。。10、雨中黄叶树,灯下白头人。。11、以我独沈久,愧君相见频。。12、故人江海别,几度隔山川。。13、乍见翻疑梦,相悲各问年。。14、他乡生白发,旧国见青山。。15、比不了得就不比,得不到的就不要。。。16、行动出成果,工作出财富。。17、做前,能够环视四周;做时,你只能或者最好沿着以脚为起点的射线向前。。9、没有失败,只有暂时停止成功!。10、很多事情努力了未必有结果,但是不努力却什么改变也没有。。11、成功就是日复一日那一点点小小努力的积累。。12、世间成事,不求其绝对圆满,留一份不足,可得无限完美。。13、不知香积寺,数里入云峰。。14、意志坚强的人能把世界放在手中像泥块一样任意揉捏。15、楚塞三湘接,荆门九派通。。。16、少年十五二十时,步行夺得胡马骑。。17、空山新雨后,天气晚来秋。。9、杨柳散和风,青山澹吾虑。。10、阅读一切好书如同和过去最杰出的人谈话。11、越是没有本领的就越加自命不凡。12、越是无能的人,越喜欢挑剔别人的错儿。13、知人者智,自知者明。胜人者有力,自胜者强。14、意志坚强的人能把世界放在手中像泥块一样任意揉捏。15、最具挑战性的挑战莫过于提升自我。。16、业余生活要有意义,不要越轨。17、一个人即使已登上顶峰,也仍要自强不息。
- 1、下载文档前请自行甄别文档内容的完整性,平台不提供额外的编辑、内容补充、找答案等附加服务。
- 2、"仅部分预览"的文档,不可在线预览部分如存在完整性等问题,可反馈申请退款(可完整预览的文档不适用该条件!)。
- 3、如文档侵犯您的权益,请联系客服反馈,我们会尽快为您处理(人工客服工作时间:9:00-18:30)。
(产品管理)塑胶产品设计缺陷及改良方法
产品结构设计缺陷及改良方法集粹
1.结构优化装配工艺及结构可靠性
于我们的结构设计目标中,除了保证结构的功能外,简化我们的装配工艺和保证结构的可靠性也是结构设计需要考虑的重要方面。
案例i).设计要求和背景:悬臂梁能轻松装配进轴孔,且且能够承受壹定的拉力而不掉出来。
我们先来见壹下常见的俩个设计方案。
对于方案1,显然能够变形的部位长度偏短,变形比较困难所以导致装配比较难,而且装配的过程中很容易会给零件造成永久性损坏。
而对于方案2,因为开了壹条通槽,使得发生变形的部分长度大为增加,从而使得于装配过程中变形比较容易,换言之就是装配比较容易,但也正因为通槽的存于,装配好之后轴的受力稍大便会因俩侧的变形而造成脱落。
方案1:装配困难且容易损坏零件方案2:装配容易但容易脱落
通过上面俩个方案的分析,我们知道我们的设计要点实际上是如何实现变形的单方向。
也就是说我们的设计应该使得于装配过程中的变形比较容易而于装配好之后自然受力的情况下不容易发生变形;根据这个要求我们作出了下面的设计改良,实际生产应用中也得到了很好的效果。
改良方案:装配容易而不容易脱落
2.结构优化装配及拆卸工艺
简化且优化成品的装配及拆卸工艺,实际就能够达到减少产品成本,提高生产效率的壹个方式。
案例i).设计要求和背景:副零件要能轻松压入ABS零件中,且且能够容易取出以更换副零件。
卡勾的高度5.0mm因为空间的问题不能再增加。
上图也是通常的设计方案,但对这个设计方法,缺点是很明显的。
因为卡勾的高度限制,强行压入副零件会比较困难,且且于压入过程中容易对ABS零件造成损坏。
对于需要多次更换而进行的装配更会因疲劳而造成永久性损坏。
针对之上问,我们采用了U型搭勾的方式来实现单向自然变形。
实际证明装配简单而固定性好。
案例ii).设计要求:装配方法简单。
分析:俩件东西通过壹个长螺柱装配,但涉及到三个孔的对齐问题,且且中间部分的通孔长度比较长,导致于实际装配的过程中比较难对正装配孔影响装配效率。
改良方法:于要装配的部件上直接长料生成壹个定位柱,螺柱用来固定另壹侧。
这样就能够把三个孔的对正简化成俩个孔,从而提高了装配工序的效率
三孔对正影响装配工序效率简化成俩孔对正提高效率
案例iii).设计背景:长键体导电硅胶要装配进壹系列的孔上。
分析:因为长键体硅胶是软胶,而装配的键体长度比较长,要对正的是壹系列的孔,如果不作任何保证措施,于装配的过程中开始装配的时候如果稍有错误就会导致硅胶键体的变形而使得装配困难。
改良方案:于装配孔周围添加壹些用于导向的斜筋,有利于把键体导向正确的装配孔位置,大大降低装配的对正要求,从而提高装配效率。
长键体导电胶难以对正装配孔,加斜导向筋方便装配过程的对位。
加扣位销以引导装配
案例iv.设计背景:于产品装配过程中,装配工人未必清楚某些部件的装配方法,作为设计者应该于结构上做处理尽量避免因工人的误装配而导致装配错误导致产品不合格。
3.结构改善成品注塑缺陷
案例i).设计背景:如左下图零件,筋的高度比较大,通常需要再顶部添加扁顶针来辅助顶出。
同时因为高度和出模角的影响导致顶部料厚比较小填充不容易。
筋的高度比较大改良方案:加顶销垫
改良方案:如右上图,添加壹些顶销垫(圆柱),壹方面能够使用圆顶针辅助顶出,另壹方面也能够改善顶部的填充情况。
案例ii).设计背景:于实际的产品设计过程中,有的场合无法避免出现比较厚的料厚。
于这种情况下,我们要采取各种方式来保证料厚的尽可能平均。
优选方案:为力避免因直角边所带来的困气问题而给塑胶件带来缺陷,我们的减料形状应该尽可能保证顺滑过渡。
直角边的偷肉方法容易造成困气平滑的偷肉方法改善困气
4.结构优化成品变形
设计背景:如左下图的小勾,因三面悬空,于注塑成型取出冷却的过程中会发生较大的变形从而影响勾的实际功效和外形。
改良方案:于悬空的部分和主体部分加壹薄的桥接臂,桥接笔通过后加工的方法进行处理,虽然于工艺上多了壹道工序,但能很好的保证成品质量。
原始方案:小勾因三面悬空而变形改良方案:添加连接筋改善变形
5.优化结构稳定&可靠性
设计背景:于实现结构的功能外,我们仍要考虑结构的可靠性和稳定性。
如左下图的盖子,为了增加盖于于开始弹开的力度,使用壹个硅胶顶柱来辅助实现初始的弹力。
硅胶装配于司柱上。
分析:由于司柱里面积有气体,硅胶装配后把气体封闭于司柱腔内,当受热时气体膨胀无法排出就会顶出硅胶从而使硅胶脱落影响结构的可靠性。
优化方案:能够考虑于硅胶顶部开孔或司柱侧面开槽俩个解决办法,但考虑到硅胶是软胶且且中间的长度比较长,开孔容易造成堵塞且且出模不方便,所以采取了司柱侧面开槽的方法。
本例结构于盖子起始开的状态使用软硅胶辅助扭力弹簧来增强盖子打开的力度也是壹个很好的优化结构方法,壹方面能够减少所需的扭力弹簧的强度仍能够延长弹簧的疲劳失效时间。
另壹方面能够实现很好的弹开效果。
司柱开槽放气避免顶出硅胶软硅胶辅助起始弹力
6.结构根据不同的需求采用不同的优化工艺。
设计背景:热融(焊接)是结构的壹个常用固定方法,但单就这壹个工艺就有很多种处理方法,每壹种处理方法均有自己的特点和适合的场合。
正确选用合适的类型才能于结构上做出正确的结构。
方案1。
我们常用的标准标桩焊接结构。
由于标准标桩式热熔焊接后焊点较分散,扁而平,不符合力学结构。
不能承受较大冲击,比较不容易过跌落,冲击等破坏性测试
方案2。
焊接头末端改成拱形凹槽式,利于集料.为了方便熔体流动,将热熔柱改为尖头式.零件结合力度大大增强.较容易过跌落.冲击等破坏性测试
方案3.焊接头末端拱形凹槽改成半圆环式,可将更多的熔体集中于受力边缘区域.零件结合力度更壹步大大增强。
方案4.为了获得更大的结合力度,我们往往不得不加大热熔柱直径。
众所周知,过大的直径易造成塑零件B背部缩水。
于是,空心标桩无疑为比较优秀的结构方式了
方案5.之上介绍的热熔焊接方式焊点皆漏于零件外部,易受外力破坏,于是,我们能够于零件A上设计溢料槽,用于收集熔体,使之埋入零件A。
故这种埋头标桩是壹种不错的选择
避空缺口大小不壹避免电池触片正负极装配出错。