浅析蒸汽轮机蒸汽(间隙)激振、油膜涡动及油膜振荡
汽轮发电机机组油膜振荡综合诊断与处理建议

汽轮发电机机组油膜振荡综合诊断与处理建议一、机组油膜振荡的主要原因1.机组结构与工作环境汽轮发电机机组具有复杂的结构和特殊的工作环境,机组内部存在着各种摩擦和振动,这些因素都会对机组油膜振荡产生影响。
2.润滑油机组润滑油的粘度、温度和油料质量等因素,都会对油膜振荡产生直接的影响。
如果润滑油的粘度过高或过低,都会导致机组油膜不稳定,从而引起振荡。
3.轴承磨损轴承在长时间工作过程中,难免会出现磨损和松动现象。
如果轴承运行时有松动,就会引起机组的振动,从而引起油膜振荡。
机组油膜振荡的检测方法很多,包括现场检测和实验室检测两种。
具体方法如下:1.现场检测现场检测是指利用现场技术手段,对机组进行振动、噪声等参数的测量和分析。
2.实验室检测实验室检测是指将机组的润滑油送到实验室进行检测。
实验室检测可以检测润滑油的粘度、杂质、酸值等物理和化学指标,进一步分析机组油膜振荡的原因和性质。
机组油膜振荡的处理方法应该根据具体情况进行综合分析和处理。
如果机组油膜振荡是由于润滑油的质量不好或者是油料粘度过低或过高引起的,就需要更换润滑油。
换一种合适的润滑油,可以很好地解决油膜振荡问题。
2.多次加油为了保证机组正常运行,可以进行多次加油。
多次加油可以确保机组内部的润滑油充足,避免机组因为润滑不良而引起的油膜振荡问题。
如果机组油膜振荡是由于轴承松动引起的,就需要更换轴承。
更换完好的轴承可以确保机组稳定运行,避免机组因为松动而导致的振荡问题。
1.定期检查机组油膜振荡问题的预防,最关键的是要做到定期检查。
定期检查可以发现机组问题的早期迹象,及时进行处理,避免问题不断扩大。
2.保养维护保养维护是预防机组油膜振荡问题的另一个重要方法。
机组的保养维护工作必须要做好,可以重点关注润滑油的保养、轴承的保养以及机组的清理和维护等。
综上所述,汽轮发电机机组油膜振荡对机组的运行稳定性和生产效益都会产生极大的影响。
因此,我们必须要注重机组油膜振荡的综合诊断和处理,并且加强管理,采取有效的预防措施,确保机组的正常运行和生产效益。
汽轮机振动大的原因分析及其解决方法(3)

汽轮机振动大的原因分析及其解决方法(3)二、火电厂汽轮机常见异常振动的分析及解决措施1、油膜震荡(1)产生的原因分析油膜自激震荡是由于汽轮发电机转子在轴承油膜上高速旋转时,丧失稳定性的结果。
稳定时,转轴是围绕轴线旋转的。
当失稳后。
一方面转轴围绕其轴线旋转,另一方面该轴线本身还围绕平衡点涡动。
轴线的涡动频率总保持大约等于转子转速的一半,故又称半速涡动。
当半速涡动的涡动速度同转子的临界转速相重合时,半速涡动被共振放大,就表现为激烈的振动。
油膜振动具有下列特征:① 油膜震荡一经发生,振幅便很快的增加,使机组产生激烈振动。
这种振动随着转速的升高,振幅并不减小。
失稳而半速涡动可能较早。
而油膜震荡则总是在2倍于第一临界转速之后出现。
② 油膜震荡时,振动的主频率约等于发电机的一阶临界转速,且不随转速升高而改变。
③ 发生油膜震荡时,振幅将不只是于转速一致的工频振动,而且还有低频分量。
④ 发生油膜震荡的轴承,顶轴油压也发生剧烈摆动,轴承内有明显的金属撞击声。
⑤ 油膜震荡严重时,仔细观察可以看到主轴的外露部分在颤动。
(2)故障解决措施在机组出现油膜震荡时,可采用以下解决措施:① 增加轴瓦比压。
② 减小轴瓦顶部间隙或增大上轴瓦轴承合金的宽度。
③ 减小轴颈与轴瓦的接触角,一般可减小至300~400。
④ 降低润滑油动力粘度。
例如提高油温或选用粘度较小的润滑油等。
⑤ 用平衡的方法将转子原有不平衡分量降得很少。
2、汽流激振(1)产生的原因分析汽流激振类振动有以下特点:a、汽轮发电机组的负荷超过某一负荷点,轴振动立即急剧增加;如果降负荷低于负荷点,振动立即迅速减小。
b、强烈振动的频率约等于或低于高压转子一阶临界转速。
c、汽流激振一般为正向涡动。
d、发生汽流激振的部位在高压转子或再热中压转子段。
其原因主要是由于叶片受不均衡的气体来流冲击就会发生汽流激振;对于大型机组,由于末级较长,气体在叶片末端膨胀产生流道紊乱也可能发生汽流激振现象;轴封也可能发生汽流激振现象。
汽轮发电机机组油膜振荡综合诊断与处理建议

汽轮发电机机组油膜振荡综合诊断与处理建议汽轮发电机机组是利用汽轮机驱动发电机产生电能的装置,其正常运转对于电力生产至关重要。
由于机组长期运行以及其他因素的影响,机组中的润滑油系统可能出现油膜振荡问题,严重影响机组的正常运行和寿命。
对于汽轮发电机机组油膜振荡问题的综合诊断和处理非常重要。
本文将从机组油膜振荡的原因、诊断方法和处理建议三个方面进行综合分析。
一、机组油膜振荡的原因1. 油膜振荡是由于机组运行时润滑油的振动引起的。
润滑油在机械部件表面形成一层薄膜,减少机械部件之间的摩擦和磨损,从而保证机组的正常运行。
但当润滑油的振动频率与机械部件的共振频率相近时,就会产生油膜振荡。
2. 机组设计不合理是油膜振荡的重要原因之一。
机组结构刚度不足、支座刚度不均匀、轴承刚度过大或过小等问题都可能导致油膜振荡的发生。
3. 机组运行过程中的机械故障也是油膜振荡的重要原因。
机械部件的磨损、轴承的损坏、齿轮间隙过大等问题都可能导致机组的振动频率发生变化,从而引发油膜振荡。
二、机组油膜振荡的诊断方法1. 观察机组的振动情况:通过安装振动传感器等设备,观察和记录机组的振动情况,特别是在运行过程中的振动频率和振幅的变化。
如果发现振动频率接近共振频率,说明存在油膜振荡的可能性。
2. 检测润滑油的振动:将机组的润滑油样品取出,使用振动传感器等设备检测润滑油的振动情况。
如果发现润滑油的振动频率与机组振动频率相近,说明存在油膜振荡问题。
3. 利用计算机模拟或仿真软件进行分析:将机组的结构和运行参数输入计算机模拟或仿真软件,通过计算和分析机组的共振频率和振动模态,判断是否存在油膜振荡。
三、机组油膜振荡的处理建议1. 对机组进行结构改造:根据机组的实际情况,对结构刚度不足、支座刚度不均匀等问题进行改造。
增加机组的刚度可以降低共振频率,从而减少油膜振荡的发生。
2. 更换合适的润滑油:选择合适的润滑油可以改善油膜振荡问题。
润滑油的黏度、粘度指数、摩擦系数等参数对油膜的形成和振动频率有一定的影响。
汽轮发电机机组油膜振荡综合诊断与处理建议
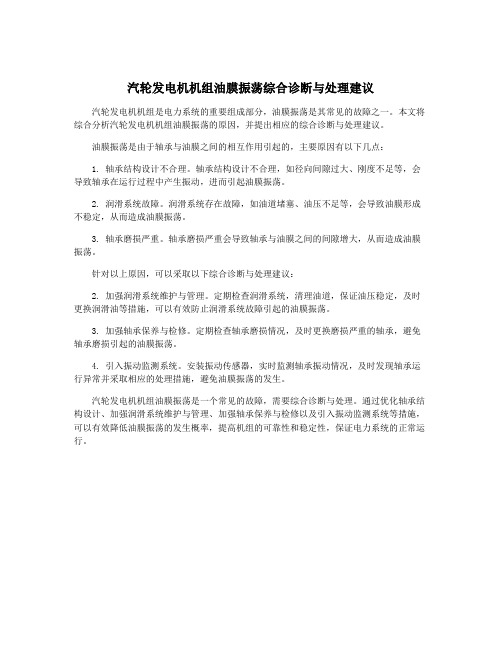
汽轮发电机机组油膜振荡综合诊断与处理建议
汽轮发电机机组是电力系统的重要组成部分,油膜振荡是其常见的故障之一。
本文将综合分析汽轮发电机机组油膜振荡的原因,并提出相应的综合诊断与处理建议。
油膜振荡是由于轴承与油膜之间的相互作用引起的,主要原因有以下几点:
1. 轴承结构设计不合理。
轴承结构设计不合理,如径向间隙过大、刚度不足等,会导致轴承在运行过程中产生振动,进而引起油膜振荡。
2. 润滑系统故障。
润滑系统存在故障,如油道堵塞、油压不足等,会导致油膜形成不稳定,从而造成油膜振荡。
3. 轴承磨损严重。
轴承磨损严重会导致轴承与油膜之间的间隙增大,从而造成油膜振荡。
针对以上原因,可以采取以下综合诊断与处理建议:
2. 加强润滑系统维护与管理。
定期检查润滑系统,清理油道,保证油压稳定,及时更换润滑油等措施,可以有效防止润滑系统故障引起的油膜振荡。
3. 加强轴承保养与检修。
定期检查轴承磨损情况,及时更换磨损严重的轴承,避免轴承磨损引起的油膜振荡。
4. 引入振动监测系统。
安装振动传感器,实时监测轴承振动情况,及时发现轴承运行异常并采取相应的处理措施,避免油膜振荡的发生。
汽轮发电机机组油膜振荡是一个常见的故障,需要综合诊断与处理。
通过优化轴承结构设计、加强润滑系统维护与管理、加强轴承保养与检修以及引入振动监测系统等措施,可以有效降低油膜振荡的发生概率,提高机组的可靠性和稳定性,保证电力系统的正常运行。
汽轮机振动的原因及处理分析

汽轮机振动的原因及处理分析摘要:电力能源是推动国家发展的重要基础,为了确保全国经济发展以及国民用电的需求,加强热电厂汽轮机组维修、养护工作,保证城市能够正常供电,是电厂最重要的工作。
汽轮机组在工作的过程中,无法避免会存在一定的振动,当振动超出一定范围时,振动会对设备产生极大的损害,因此,针对汽轮机振动原因及处理措施展开分析。
关键词:汽轮机组;振动机理;处理分析中图分类号:TM621文献标识码:A引言随着现代技术发展,机械设备内部的精密程度越来越高,内部零件耦合状态的要求也更加明显。
一旦某个零部件发生故障,将会影响整个生产链。
对于汽轮机来说,可以通过观察其振动情况来判断内部零件是否出现松动和发生故障。
若汽轮机出现振动过大,则表明该汽轮机出现故障,必须立即诊断维修。
影响汽轮机振动的因素有很多,因此,准确排查故障原因,给出解决措施,对企业有着重要意义。
1汽轮机振动故障分析1.1动静部位碰摩一般来说,动静部位碰摩分为局部碰摩和整周碰摩。
(1)动静局部碰摩特征。
轻微碰摩,振幅不变,严重碰摩,振幅减小。
碰摩增加,谐波分量也出现增加现象。
碰摩造成不平衡质量点位置不断发生改变,使得相位也发生变化。
(2)动静整周碰摩特征。
转子横向振动频率变高;轴颈中心向轴承内部间隙圆中心偏移;1×频最大振幅为摩擦点截面间隙圆。
造成动静部位碰摩的原因主要有3个:首先是在设计或安装过程中动静间隙过小;其次是转子振幅过大;还有可能是因为轴系不对中,引起转子偏斜,发生碰摩。
1.2转子质量不平衡(1)热弯曲。
当转子发生热弯曲后,其转速会下降。
当下降到临界值时再启动,就会产生更大振幅,从而出现汽轮机振动。
转子在不同状态下的波特图能够帮助判断是否发生热弯曲。
此外,转子材料的热应力、气缸进水等原因都会使转子发生热弯曲。
(2)原始性不平衡。
该类不平衡在转子转动前就存在,在加工或者检修过程中遗留下来的,其特征是振幅和相位受其他参数影响不大,振动特征较稳定。
蒸汽轮机异常振动原因的分析和处理措施

蒸汽轮机异常振动原因的分析和处理措施
蒸汽轮机在运行中出现异常振动,可能会导致设备损伤或停机,严重影响生产。
因此必须及时分析产生原因,并采取相应的技术措
施进行处理。
本文将从以下几个方面进行分析。
一、原因分析
1.设备松动或失衡:蒸汽轮机在运转过程中,由于受各种因素
的影响,设备可能会发生松动或失衡现象,从而导致异常振动。
2.轴承故障:轴承是蒸汽轮机中比较易损坏的部件,如果轴承
损坏,就会导致蒸汽轮机出现异常振动。
轴承故障的原因可能是轴
承过载、磨损、润滑不良等因素。
3.传动链路不同步:传动链路不同步是指蒸汽轮机中的传动部位,在运转中出现转速不同步的现象,导致蒸汽轮机出现异常振动。
4.物料固定不到位:蒸汽轮机在运行中,物料未能固定到位,
从而导致设备受到冲击,产生振动。
二、处理措施
1.定期检查设备:定期检查蒸汽轮机各设备是否松动或失衡,
并及时加以调整和修复,保证设备运行平稳。
2.加强轴承维护:加强轴承维护,及时更换磨损的轴承,在轴
承润滑方面加强管理,确保轴承正常工作。
3.增强传动链路同步性:加强传动链路同步性,保证传动链路
运转的同步性,减少机械设备振动。
4.加强物料固定:加强物料的固定,保证物料在设备中的平稳运行,避免设备振动。
在蒸汽轮机的运行过程中,应该加强设备管理,建立全面的设备检查机制,及时修复设备问题,减少设备故障,确保生产的正常进行。
【精品】超临界汽轮机组蒸汽激振的分析
超临界汽轮机组蒸汽激振的分析摘要:蒸汽激振是关系汽轮发电机组经济性、安全性的重大问题.机组容量不断增大、蒸汽参数不断提高使蒸汽激振问题成为目前大机组,尤其是超临界机组,设计、运行、检修中必须考虑的重要问题之一。
本文分析了蒸汽激振的原理、特征以及蒸汽激振对汽轮机组的危害,给出了当前常用的汽流激振治理方法。
关键词:蒸汽激振,超临界,激振力,汽轮机.Abstract:Thesteam—inducedself-excitedvibrationisaprimaryproblemfortur bo—generators.Ithasbecomeoneofthemostimportantissuesfortheultr a—supercriticalsteamturbineandmustbetakenintoaccount。
Thispaperanalyzestheprinciplesandfeaturesexcitingsteama ndsteamturbinevibrationoftheharm,giventhecurrentcommonlyusedtreatmentmethodforsteamflowexcit ation.Keywords:steamexcitation,supercritical,excitingforce,turbin e.前言采用超临界压力甚至超超临界压力是提高汽轮机热效率的重要途径之一.一般而言,超临界机组的热效率比亚临界机组的高2%-3%左右,而超超临界机组的热效率比常规超临界机组的高4%左右。
随着我国电力工业的结构调整,研制、生产和发展超临界压力机组是火力发电节约能源、改善环保、提高发电效率、降低发电成本的必然趋势。
但汽轮机蒸汽参数的提高,会导致高压缸进汽密度增大、流速提高,蒸汽作用在转子上的切向力对动静间隙、密封结构及转子与汽缸对中度的灵敏度提高,增大了作用在转子上的激振力,这使超临界汽轮机发生蒸汽激振的可能性远大于亚临界汽轮机。
汽轮机运行中的振动分析及对策
汽轮机运行中的振动分析及对策摘要:汽轮机的振动原因是多种多样的,而振动又是汽轮机的主要故障原因,解决这一问题将对我国的电力生产产生极大的推动作用。
目前,我国的电厂一线工人和专家学者也对这一问题进行了研究,并且取得了相当程度的进展。
火力发电作为我国的主要发电方式,必须保证其安全稳定地运行。
关键词:汽轮机运行;振动;对策振动是指物体偏离原有的平衡位置,发生了动能和位能的连续相互转换作用,因此产生振动。
在机械运转过程中,微小的振动是不可能预防的,只要振动的幅度不超过一定的范围都是可以接受的,汽轮机的运行过程中,振动也是不可避免的,在一般规定水平下振动是没有危害的,但是往往因为各种原因,汽轮机在运行工作中振动就会超过一定的范围,对汽轮机造成了损害。
一、汽轮机振动的原因分析1.1油膜失稳汽轮机发生油膜失稳主要有两种形式,半速涡动和油膜振荡。
半速涡动一般发生在转子的转速小于两倍第一临界转速的时候,在提高转速的过程中,从某一个较低的转速开始出现,通常情况下,这种振动会一直持续到最高转速,也可能在转子的转速达到某一个数值时就会消失。
当转子转速发生变化的时候,涡动的频率也会随之发生变化,但是转度的半频关系始终不变。
半速涡动最有效的识别办法是级联图,在级联图上,半频振峰的频率点连线表现为一条斜率为2的直线。
除此之外,在波形图上或者是轴心轨迹途中也能看到以低频为主的特征。
1.2气流振动气流振荡发生的形式也是多种多样的,原因也是各有不同:首先是顶隙激振,由于对汽轮机效率和性能的追求,热机设计人员采用了提高工作转速和增加级数的方法,级数的变化使转子的跨距变长,临界转速降低,而转速的提高又造成工作转速与临界转速比变大,这就造成了轴系统的稳定性下降。
由于转子的弯曲是通流部分的径向间隙被改变了,一侧的间隙变小,另一侧的间隙扩大,变小一端的热效率增加,变大一方的热效率减小,就会造成切向力作用在轴颈上,使轴颈沿转动方向做正向的涡动。
汽轮发电机组滑动轴承油膜振荡故障的分析与治理
3 振 动 突 变原 因分 析
综 合 以上 振 动 特 征 , 为 突发 振 动 是 真 实 信 认 号 , 稳定 振动 与发 电机转 子 本 身 没 有关 系 , 不 而是 由支 承转 子 的 轴 承 故 障 所 致 。通 过 对 振 动 突 发
性 、 动 与转 速 之 间 的关 系 及 发 电机 转 子 一 阶 临 振
摘要 : 台 3 0MW 汽轮发 电机组 检修后开机过程 出现异 常振 动, 现为发 电机轴 承振动 突变 。分析 表明 , 某 5 表 振 动突变 的原 因是发 电机轴 承发生了油膜振荡故 障。通过对 安装数 据 的分 析 , 为发 电机轴 承单边侧 隙偏小 是 认 诱发油膜振荡 的主要原 因 , 通过修改轴承侧 隙和标 高消除 了机组的油膜振荡故障 。
机。 上述异常振动影响了机组的安全稳定运行。
构 , 轴 系有 6套 轴 承 , 中汽 轮 机 1 2 轴 承 为 全 其 , 可倾 瓦轴 承 , , 承 为 椭 圆 瓦轴 承 , 电机 5 , 3 4轴 发 6轴承 为球 面瓦 轴 承 。机 组 结 构振 动 发 散 伯 德 图
( ) 4给 出了 3个 典型 转 速下 的频 谱 图 , 3图 分 别 代 表 1 0 m n之前 、 8 0~ 0 m n和振 0r i 8 / 1 0 29 0r i /
图 4 3个典 型 转 速 下 5轴 承 测 点 的 频谱 图
而且 幅值 较大 , 远超 过工频 分量 幅值 。 图 5给 出了某 次振 动 突 变后 的振动 波 形 。 图 上 黑点 与汽轮 机旋 转 周期 相 对应 。该 波 形 图所 对
宣
i 璺 罂
应 的转速 为 29 15rrn 由该 图反 推 出故 障信 2 . / i。 a
浅述汽轮机振动原因与处理
面相关 , 而且 与汽缸膨胀 、 蒸汽流动等热方面以及发电机电气参 数等诸 多 因素相关 。因此 , 正确分 析出振动故障原 因后 , 就需要对具体 的振动 故 障原 因此采用合适可行的方法 进行处理。 尽管汽轮发电机有关结 构振
题。
的振动特性区别在于其不 同的相位关系 。 弯轴 引起 的两轴承轴 向振动相 位相反。 而外伸端质量不平衡引起 的两轴 承轴 向振动相位 同相 。 处理汽 轮机转子 弯轴 引起的振动 主要方法 是更换转子或对原转 子进行局部刨 平 、直轴 ,然后进行动平衡实验 以消 除振动 。 三 、不对 中:联轴器不对中有联轴 器端面瓢偏和不 同心两种情况 , 联轴器端面飘偏表现为产生较大的轴 向振动 , 且沿联轴器两端测 量的振 动相位反相 。 联轴器不 同心产生 的振动现象和端面飘 偏时的相类似 , 但 其表现为较大 的径 向振动 , 且沿联轴器两端测量振动相位反 相。 当联轴 器端面飘偏或不 同心较严重时 , 会对振动频谱的特征产生重要影响 , 处
汽轮发 电机组的振动 问题往往涉及许多复杂 因素 , 它不仅与机 械方
理不对 中这种故 障的方法是将联轴器 进行热态及冷态对 中或改变联轴 器型式以降低对 中灵敏度 。 四、 共振 :当强迫力频率和系统 自然频率相同时产生共振 , 共振 时 出现剧烈振动可 能弓 I 起部 件损坏 , 当系统处于共振状态时 , 由于相位 发
现 出来的振动故障往往不同 , 下面列 出有关振动故障的种类及其 处理方
法:
一
的轴承设计 , 润滑油参数的改变 等因素 引起 的。 通常其处 理方法 为改变
、
质量不平衡 。质量不平衡往往 反映出很大 的 l x振动 ,由跨 内
- 1、下载文档前请自行甄别文档内容的完整性,平台不提供额外的编辑、内容补充、找答案等附加服务。
- 2、"仅部分预览"的文档,不可在线预览部分如存在完整性等问题,可反馈申请退款(可完整预览的文档不适用该条件!)。
- 3、如文档侵犯您的权益,请联系客服反馈,我们会尽快为您处理(人工客服工作时间:9:00-18:30)。
浅析蒸汽轮机蒸汽(间隙)激振、油膜涡动及油膜振荡东方汽轮机厂黄永东梁小兵摘要定性地阐述蒸汽(间隙)激振、油膜涡动及油膜振荡的机理,认为由流体产生的切向力是引起机组自激失稳的主要原因,并提出解决措施。
关键词自激振动;极限环;蒸汽(间隙)激振;油膜涡动;油膜振荡;失稳;措施1 前言随着汽轮机技术迅猛发展,蒸汽轮机机组容量和蒸汽参数也在不断提高,作为自激振动特例的蒸汽(间隙)激振、油膜涡动及油膜振荡引起转子失稳的问题也日愈突出。
要求了解自激激振的机理和成因,提出相应的解决措施,更好地提高机组的安全可靠性。
2 自激振动与自激振荡自激振动是汽轮机较为常见的故障现象之一,对它的研究是随着柔性转子发展而发展起来的。
事实上在机械振动理论中将自激振动定义为当系统在一个周期内损失的能量和吸入的能量相等时所形成的周期性振动,并将在相平面上形成封闭的运动相迹,称之为极限环。
极限环的振动幅值决定于振动系统的参数,也就是说系统本身控制振动能量的补充,并通过运动不断向自身反馈能量,一旦振动系统有初始运动(扰动)振动的能量就随之补充,使得极限环运动得以保持;而当振动系统处于静止或振动系统的参数发生改变,极限环的振动幅值就变为零或者振动幅值就会发生改变,因此可以说自激振动同外界激励是无关的。
而强迫振动则是另一种类型的振动,它由外界激振力对系统做功,振动系统的振动频率与外界激振力的频率是完全一致的,一旦振动系统的参数一定,振动系统的振动幅值就主要受外界激振能量的控制和维持。
在蒸汽轮机中的极限环运动称之为涡动,它也是失稳运动的临界状态。
可从两个方面进行解释。
其一从能量的角度来分析,系统振动能量的耗散主要是系统阻尼作用的结果,而能量的输入是由于系统存在与正阻尼相反方向的力作用的结果,也就是通常说的“负阻尼”作功,一旦系统的阻尼不能平衡振动系统的输入能量,其结果必然会引起系统振动发散而导致系统失稳。
对于机组而言该力位于轴心轨迹平面而与轴心径向垂直且与转子的线速度方向同向,它削弱了机组转子系统阻尼的作用,在转子设计阶段就是采用能量法来计算转子失稳转速的。
其二从频率的角度来解释,极限环运动是一个周期性振动,它必然存在一个振动频率,对于蒸汽轮机而言该频率是转速的分频,如果极限环振动频率同系统固有频率相重合,系统就会发生自激共振,此时系统振动将围绕不稳定结点运动。
此时极限环运动称之为自激振荡。
总之,不论涡动或者自激振荡都是系统运动所不允许的,机组应避免出现自激振动故障。
3 蒸汽(间隙)激振、油膜涡动及油膜振荡的原因及处理措施3.1 蒸汽(间隙)激振3.1.1 蒸汽(间隙)激振的机理发生在汽轮机上的蒸汽(间隙)激振是随着高参数大容量机组的出现而出现的。
经过国内外专家从理论和试验上分析研究,得出蒸汽对转子系统形成一个作用在转子偏心垂直方向上并与转子线速度方向同向的切向力是引起转子系统蒸汽自激振动的根本原因。
通常可以将蒸汽(间隙)激振切向力分为3大类。
3.1.1.1 第1种蒸汽激振力主要由沿叶轮周向不均匀分布汽流而产生,它同机组的负荷有关。
其产生的原因如下:(1)由于汽流在蒸汽轮机中是轴向流动的,当汽流碰到叶片时,将对叶片产生切向力并推动转子旋转而作功。
如果机组运行转态下转子通流中心没有偏心,则汽流作用于级叶片的切向力将是均匀分布的,这样叶片上的切向力的合力应为零;如果转子通流中心有偏心,则会造成级叶轮径向间隙沿周向分布不均匀,其中间隙大的地方蒸汽漏汽较大,进入叶片的工质就少些,反之则反。
因此,沿周向方向汽流对叶片产生的切向力是不均匀的,这样在叶轮上,将产生一个与转子线速度方向相同的切向力合力(如图1),该切向力将给转子运动输入能量,而形成涡动,习惯称为Alford力。
其激振力大小的公式为:式中W——级功率y——偏心率H——叶片高度β——级效率D——汽轮机叶轮平均半径ω——转子旋转角速度(2)由于制造误差、机组运行阶段静子部分变形和动叶片表面结垢,同样会造成汽流在级通道间流动不均匀,也会形成一个与转子线速度方向相同的切向力合力。
该类蒸汽激振力极易造成高、中压转子失稳,其切向力随着机组负荷和蒸汽参数增加而增加。
3.1.1.2 第2类蒸汽激振力主要由螺旋形汽流效应而形成。
在高、中转子的密封间隙处(主要指围带密封处,因为该处汽流的流速较高),汽流的惯性效应远远大于汽流的摩擦效应,单位蒸汽从汽封齿某点进入,由于惯性的作用,它不是从同一子午平面上的下一个汽封齿流出,而是旋转了一个角度2Δ,如图2。
假设转子的偏心为y,则点1和点2处的间隙应分别为:假定在两齿内蒸汽介质密度ρ为常数,则可以求得汽封齿间腔室内各点压力值可见,F x同Δ、ε、D参数有关并随围带汽封齿的个数增加而增大,它垂直于OO′轴,同样也是一个与转子线速度相同的切向力。
该类激振力较易造成高、中压转子失稳。
3.1.1.3 第3种蒸汽激振力主要产生于转子端部的轴封处和隔板汽封,是由于气体弹性效应(习惯上称之为Alford 效应)和二次流效应而形成的。
当转子在偏心和转子存在倾角时,在汽轮机端部将产生汽体弹性效应和二次流效应,其中汽体弹性效应只有在汽封齿进口间隙大于汽封齿出口间隙时,才会导致“负阻尼”作功,转子失稳;但是当汽封齿进口间隙小于汽封齿出口间隙时,所产生的效果有助于提高转子的稳定性,如图3。
据有关资料报道该蒸汽激振力往往较小,通常多在小型蒸汽轮机组上才会导致转子失稳。
另外由于轴封处的供汽压力是恒定的,该类蒸汽激振力在机组空负荷时就会导致转子自激振动。
3.1.2 蒸汽(间隙)激振的处理措施一旦机组产生蒸汽(间隙)激振,其振动低频分量将占主要成分。
从蒸汽(间隙)激振的机理可知,汽流形成与转子线速度方向同向的切向力是导致蒸汽(间隙)激振失稳的根本原因,因此,如何减少该切向力就是解决蒸汽激振失稳的根本方法。
首先,该切向力同转子偏心是密切相关的。
由于通流找中时是机组在冷态下进行的,而汽轮机在运行时,转子在轴封、隔板等洼窝内的位置和冷态下有所不同,其影响因素较多,故在转子静态找中时应充分估计转子中心(水平和垂直)的变化趋势,以便在通流找中预先将这些影响量考虑进去。
(1)油膜厚度的影响,特别是对于椭圆轴承和可倾瓦轴承混用的机组,由于可倾瓦轴承只会将转子抬高而不会使转子产生水平位移,而椭圆轴承不但会使转子抬高还使转子产生水平位移,因此,应协调好椭圆轴承和可倾瓦轴承对转子中心变化的量值关系。
(2)中、低靠背轮预留的标高差,不但应考虑两相邻轴承、轴承箱温度差,还应考虑实际运行阶段轴封送汽温度和漏汽量的影响。
(3)汽缸及转子的热变形。
特别应充分考虑温度对转子弹性模量的影响,因为它直接影响了转子运行状况的饶度。
(4)静子重量和支承变形的影响。
(5)阀门配汽和喷嘴调节时,应计算汽流对前几级叶轮切向力大小及方向,避免出现与转子旋转方向同向的蒸汽切向力。
(6)采用可倾瓦轴承减少油膜切向力与蒸汽切向力之间的相互影响。
其次,该切向力同转子各级通道的不均匀性也是密切相关的。
因此,在制造、机组安装时应充分保证级各通道均匀性,机组在运行时,一旦发生静止变形和漏汽应及时解决,避免造成附加切向蒸汽激振力。
3.2 油膜涡动及油膜振荡3.2.1 油膜涡动及油膜振荡的机理由于润滑油的一定的粘性和转子的旋转作用,流体将会被转子带动并随之一起旋转,且最靠近转子的流体将以转子旋转速度旋转;而靠近轴承壁的流体由于轴承壁是静止不动的,所以其速度最低(为零),此时轴承中流体速度分布如图4(其中λ为流体周向平均速度比);正因为流体周向流动的存在,它将对转子形成一个与转子旋转方向相同的切向力并向转子输入振动能量。
该切向力削弱了系统阻尼作用并形成极限环运动,一旦该切向力达到一定值就将导致转子失稳。
为了描述转子/轴承系统中流体激励失稳(涡动/振荡)所产生的影响,给出图5的简单系统来分析影响转子失稳的因素。
该系统包含转子的质量m,轴的刚度K s、轴承的径向刚度K B和阻尼D B。
其中λ为油膜轴承中流体周向平均速度比,是流体平均角速度同转子旋转角速度的比值。
描述系统的运动方程为:再将该式分解为正交项和直接项并且它们应分别等于零:ω得到不同的值将会导致两种截然不同的失稳现象。
当公式(3)被满足时转子系统将发生油膜涡动失稳。
通常把公式(3)称为失稳转速的门槛值,失稳主要受轴承刚度的影响。
而当公式(4)被满足时,就会导致油膜振荡发生,这种情况只会在K B→∞时才会发生。
但实际上不可能有一种无限大刚度的轴承,因此通常在K B≥K s时就会产生油膜振荡失稳。
综上所述,产生油膜涡动和油膜振荡失稳的最终原因也是流体对转子产生了与转子线速度方向相同的切向力(jD BλΩ项),并且可以得出油膜失稳主要决定于下面两个因素:(1)流体的平均角速度率λ。
流体的平均角速度应介于零和转子旋转角速度之间,通常将流体平均角速度和转子旋转角速度的比值用λ表示,当轴承的形式和端泄一定时,该λ值同转子偏心位置是密切相关的。
图6给出了λ随转子偏心变化的曲线。
公式(3)反映出λ同转子的失稳转速是成反比的,也就是说λ值在一定程度上控制了转子的失稳转态。
(2)油膜径向刚度。
转子在轴承中位置决定它的大小,图7给出了油膜径向刚度随转子偏心变化的曲线。
同样从公式(3)可以看出油膜径向刚度增大可以提高转子的油膜失稳转速。
因此,在转子工作时,应尽量提高轴承的径向刚度和减少流体的平均角速度比,保证转子工作在轴承中最佳位置,从而提高转子失稳门槛值。
3.2.2 油膜涡动及油膜振荡的处理措施油膜涡动和油膜振荡在高、中压和低压转子上均可能发生,并且由于转子标高受热负荷的影响,油膜失稳不但可能在升速过程而且也可能在带负荷期间发生,一旦产生上述失稳运动,其振动频谱同样是低频分量占主要成分。
在数学上如果忽略流体的惯性影响,可以得到转子/轴承的动刚度为:K Ds=(K-mω2)+j(Dω-DλΩ)式中K为转子/轴承径向刚度、m为转子的模态质量、Ω为转子旋转角速度、D为系统阻尼、ω为油膜涡动角速度。
据上式可以得出转子的稳定区域,如图8。
为此,减少油膜失稳的措施就应从增大转子稳定区域入手:(1)减少油粘度以减少λ值。
(2)提高转子运行时的临界转速,增加转子的稳定性。
(3)采用静压和动压混合式运行方式提高轴承/油膜的径向刚度,如采用顶轴油泵并联运行,其运行原理式如同航空发动机的挤压油膜轴承。
(4)采用“友好”不对中增大轴承载荷,提高转子在轴承中的偏心率即增加轴承/油膜径向刚度和减少λ值。
(5)采用高稳定性的可倾瓦块式轴承。
因为流体在可倾瓦块式轴承的流动是不连续的,有利于减少流体对转子的切向力,并且可倾瓦块式轴承的油膜是靠瓦块自身摆动而形成油膜的,减少了转子的水平位移,有利于转子工作在最佳位置。