锻件技术规范15
锻件通用技术要求

1 、锻件通用技术要求(JB/ZQ4000.7-86)2 、铸件通用技术要求(JB/ZQ4000.5-86)(铸件技术要求) :铸件尺寸公差要求CT3 、焊接件通用技术要求(JB/ZQ400.3-86)1. 焊接结构件的长度尺寸公差见1-245c 尺寸和形位公差数值.plb, 适用于焊接零件和焊接组件的长度尺寸. 焊接件的直线度. 平面度和平行度公差见1-245c 尺寸和形位公差数.plb, 焊接结构件的尺寸公差与形位公差等级选用见1-245b 尺寸和形位公差等级.plb2. 标注和未标注角度的偏差见1-246a 角度偏差.plb, 角度偏差的公称尺寸以短边为基准边, 其长度从图样标明的基准点算起.3. 喷丸处理的焊接件, 为了防止钢丸钻入焊缝, 必须焊接内焊缝, 并尽量避免内室和内腔. 如果结构上必须有内室和内腔,则必须进行酸洗, 以便达到表面除锈质量等级Be(见JB/ZQ4000.10-86 附录A). 对此图样需作标注.4. 由平炉钢制造的低碳钢结构件, 可在任何温度下进行焊接. 但为了避免焊接过程产生裂纹及脆性断裂, 厚度较大的焊接件, 焊削必须根据工艺要求,进行预热和缓冷. 板厚超过30mm的重要焊接结构,焊后应立即消除内应力, 消除内应力采用550- 600℃ 回火, 或200℃局部低温回火.5. 普通低合金结构钢制造的焊接件, 必须按照焊接零件的碳当量和合金元素含量、零件的厚度、钢结构件的用途和要求进行焊前预热和焊后处理, 见表 1 .4 、涂装通用技术条件(JB/ZQ4000.10-88)1. 涂装前对物体的表面要求应符合本标准的规定.2. 除锈后的金属表面与涂底漆的间隔时间不得大于6h, 酸洗处理表面与第一次涂底漆时间不少于48h, 但无论间隔时间多少, 涂漆前表面不得有锈蚀或污染.3. 铆接件相互接触的表面, 在联接前必须涂厚度30-40 μm防锈漆. 由于加工或焊接损坏的底漆,要重新涂装.4. 不封闭的箱形结构内表面, 在组焊前必须涂厚度60-80 μ m防锈漆, 封闭的箱体结构件内表面不涂漆.5. 溜槽、漏斗、裙板内表面、平衡的重箱内表面、安全罩内表面、封闭箱且在运输过程中是敞开的内表面等, 必须涂厚度60-80 μ m防锈漆.6. 涂层的检查项目及方法应符合本标准的规定.6 、装配通用技术条件(JB/ZQ4000.9-86)1. 外购材料与零部件应具有JB/ZQ4000.1-86< 产品检验通用技术要求>中规定的检验报告与合格证.2. 用于紧固机架, 机座和压力容器压紧法兰的紧固件,在紧固后, 螺钉或螺母的端面与被紧固零件间的倾斜不得大于1°.3. 螺栓与螺母拧紧后, 螺栓应露出螺母2-4 扣, 不许露出过长或过短.120 0.10 10C=Lα △t+0.15式中:C─ 轴承外座圈与端盖间的间隙,mm.L─ 两轴承中心距,mm.α─ 轴材料的线膨胀系数(取α=12×10^( -6)△t─ 轴工作时温度与环境温度之差,℃ . 0.15 ─ 轴膨胀后剩余的间隙,mm.15. 单列圆锥滚子轴承、向心推力球轴承、双向推力球轴承向游隙按(表1)调整. 双列和四列圆锥滚子轴承在装配时均应检查其轴向游隙,并应符合(表2)的要求.四列圆锥滚子轴承内径225-3150.30-0.40 0.70-0.80 315-560 0.40-0.50 0.90-1.00120-180 0.15-0.25 180-315 0.20-0.30 315-400 0.25-0.35 400-500 0.30-0.40 500-630 0.30-0.40 630-8000.35-0.45800-1000 0.35-0.4516. 滑动轴承上、 下轴瓦的接合面要接触良好 , 无螺钉把紧的轴瓦接合面 , 用 0.05mm 和塞尺从外侧 检查, 在各处的塞入深度 , 都不得大于接合面的 1/3.17. 上、下轴瓦装配后其外圆应与相关轴承孔良好接触 , 如果图样或相关设计文件对接触率未作具 体规定时 , 应按下表的规18. 轴瓦内孔刮研后 , 应与相关轴颈接触良好 , 如图样或相关设计文件未作具体规定时 , 则按下表 的规定执行 . 轴向游隙注: 受力较小的轴瓦、接触点可在25×25mm^2的面积上, 按表中数值降低 1 个接触点.19. 上、下轴瓦接触角α 以外的部分均需刮出油楔(如下表所示C1), 楔形从瓦口开始由最大逐步过渡到零, 楔形最大值按下表中规定. 上、下轴瓦经刮研达要求并组装后, 轴瓦内径与轴顶部处的间隙值 C 应达到图样配合公差的中间值或接近上限值.20. 轴瓦中装固定销用的通孔, 应在瓦口面与相关轴承孔的开合面保持平齐的情况下, 与其配钻铰. 固定销打入后, 应与销孔紧密配合, 不得有松动现象, 销子的端面应低于轴瓦内孔2-3mm.21. 过盈配合零件在装配前必须对配合部位进行复检, 并做好记录. 过盈量应符合图样或工艺文件的规定; 与轴肩相靠的相头轮或环的端面, 以及作为装配基准的轮缘端面, 与孔的垂直度偏差应在图样规定的范围内.22. 压装的轴和套允许在引入端制作导锥, 导锥的长度不准超过配合部位长度的15%,锥度各工厂自定.23. 采用压力机压装时,应做好压力变化的记录, 压力变化应当平稳,出现异常时就进行分析,不准有压坏零件配合表面的现象. 图样有最大压入力的要求时, 应达到规定数值,不准过大或过小.24. 压装完成后,在轴肩处必须靠紧, 间隙不得大于0.10mm.25. 热装薄环或轮缘时, 在端面处应设置可靠的定位基准.热装后轴与环或轮毂与轮缘之间的中心不准出现互相偏斜现象.26. 除铸铁轮毂与钢制轮缘在热装后可向轮毂内壁均匀浇冷水外, 其余热装零件均应自然冷却, 不准急冷.27. 零件热装时,必须靠紧轴肩或其它相关端面. 零件经过冷缩后, 零件与轴肩或其它相关端面的间隙在图样未做规定时, 不得大于配合长度尺寸的1/1000.28. 主动链轮和被动链轮齿的中心线应当重合. 其偏移误码差不得大于两链轮中心距2/1000.29. 链条非工作边的下垂度, 在图样没有具体规定时, 按两链轮中心距的1-4.5% 的规定.30. 相关的两个平面需要互研时, 只能在两个平面各自按平板或平尺刮研接近合格后,方准两件互研. 被刮研表面接触点在图样或相关设计文件无具体规定或以精磨代替刮研时, 应符合下表规定.31. 下列回转零件必须做静平衡试验1). 图样已给出不平衡力矩限值的零件2). 对于没有注明静平衡试验的回转零件, 当Q.nmax> 25时均需进行静平衡试验. 式中Q为回转零件的质量,t;nmax 为回转零件的最大转速,r/min. 当nmax≤20r/min 的以及锻造的全加工、全对称的回转零件不作静平衡试验.32. 对于需要作平衡试验,但未规定平衡精度时,按JB/ZZ4-86<< 刚体转动件的平衡>>规定的平衡精度G18执行.33. 所有铸造液压缸体等容器, 如试压工序是安排在粗加工后进行的, 而在精加工后表面又出现了气孔、裂纹、夹渣等缺陷时, 则必须重新进行试压.34. 所有钢板焊接的液压罐等容器,焊后应进行试压, 焊缝处经过切削加工时, 则要重新试压.35. 锻造或锻焊结构的液压缸等, 要采用外观、超声波探伤、液压试验等方法, 对承压的可靠性进行检验.36. 探伤表面粗糙度应达到Ra3.2 μm.37. 承压母体试压与装配后的密封试压, 如无特殊规定试验压力, 一般为工作压力的 1.5 倍.38. 零件母体承压可靠性的试压, 保压15min( 允许补压), 母体各部不准有渗漏现象.39. 装配件密封性试压, 保压2min, 不降压, 且各密封处不准有渗漏现象.。
锻件5000-15-2007

返回总目录 返回分目录
后退
1
中国第一重型机械集团公司标准
重型机械通用技术条件
锻钢件无损检测
允月/栽 缘园园园援员缘原2007 摘录 代替 JB/T 缘园园园援员缘原1998
员 范围
JB/T 5000 的本部分规定了锻钢件的超声波、磁粉和渗透检测方法及其质量等级。 本部分适用于重型机械用锻钢件的无损检测。 采用本部分规定的无损检测方法,可能会涉及危害性材料、操作及设备,参加无损检测人员应遵 守有关安全防护和保健规程。 对锻件无损检测的方法、部位及质量等级应在锻件图样、技术文件和订货技术条件中注明。
2
4
8
12
20
5
24
36
50
75
评定框内允许的最大磁痕数量
a 质量等级不适用于单边机械加工余量大于 1 mm 的受检表面。 b 质量等级不适用于单边机械加工余量大于 3 mm 的受检表面。
5
7
10
12
锻造工艺规范
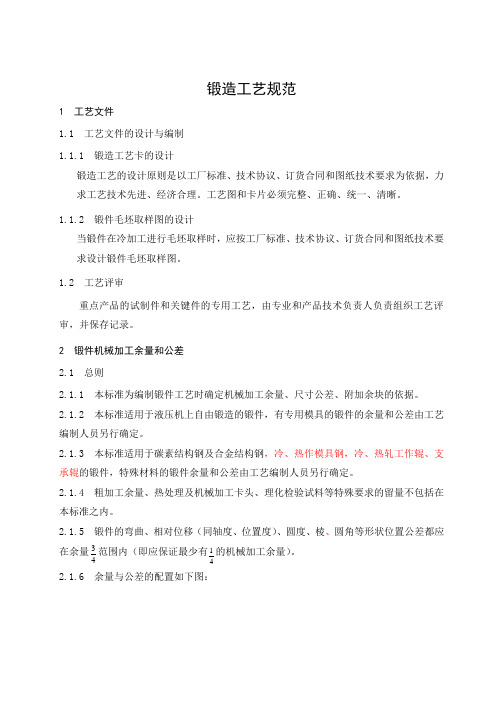
锻造工艺规范1 工艺文件1.1 工艺文件的设计与编制 1.1.1 锻造工艺卡的设计锻造工艺的设计原则是以工厂标准、技术协议、订货合同和图纸技术要求为依据,力求工艺技术先进、经济合理。
工艺图和卡片必须完整、正确、统一、清晰。
1.1.2 锻件毛坯取样图的设计当锻件在冷加工进行毛坯取样时,应按工厂标准、技术协议、订货合同和图纸技术要求设计锻件毛坯取样图。
1.2 工艺评审重点产品的试制件和关键件的专用工艺,由专业和产品技术负责人负责组织工艺评审,并保存记录。
2 锻件机械加工余量和公差 2.1 总则2.1.1 本标准为编制锻件工艺时确定机械加工余量、尺寸公差、附加余块的依据。
2.1.2 本标准适用于液压机上自由锻造的锻件,有专用模具的锻件的余量和公差由工艺编制人员另行确定。
2.1.3 本标准适用于碳素结构钢及合金结构钢,冷、热作模具钢,冷、热轧工作辊、支承辊的锻件,特殊材料的锻件余量和公差由工艺编制人员另行确定。
2.1.4 粗加工余量、热处理及机械加工卡头、理化检验试料等特殊要求的留量不包括在本标准之内。
2.1.5 锻件的弯曲、相对位移(同轴度、位置度)、圆度、棱、圆角等形状位置公差都应在余量43范围内(即应保证最少有41的机械加工余量)。
2.1.6 余量与公差的配置如下图:D :零件尺寸 C :锻件公称尺寸(基本尺寸) C ′:锻件最大尺寸 C ″:锻件最小尺寸 а:锻件名义机械加工余量δ′:下偏差(负公差) δ″:上偏差(正公差)2.1.7 本规范未包括的特殊形状的锻件及尺寸超出本规范的锻件,其余量和公差由工艺编制人员参照本规范确定。
2.1.8 在确定锻件余量时,必须兼顾零件的局部尺寸与整体尺寸的关系,局部应照顾整体,以减少加工余量。
2.1.9 易焊钢种和留有粗加工余量在粗加工后允许存在可以加工掉的局部黑皮的锻件,其锻造余量应比本标准表中规定值减少10~20%(按复杂程度)。
对易产生裂纹又不易焊补钢种(如9Cr2Mo 、32Cr2MnMo 、60CrMnMo )等锻件的余量不应比表中规定值减少。
锻造技术要求

锻造技术要求一、总则1、本技术要求包括加热要求、自由锻基本工序要求,锻后冷却和热处理要求。
2、严格执行技术要求是保证产品质量的重要条件和必须的生产技术纪律,因此必须严格按技术要求进行操作。
二、操作要求1、锻造有色金属和高合金钢时,要预热上、下砧板和工模具。
2、胎模锻时,工作者应先检查模膛表面质量,并将模具均匀加热到200°C—250°C。
3、锻造过程中坯料产生缺陷应及时消除,再继续锻造,特殊情况下,允许加大局部留量,或者经中间冷却后再处理。
4、严格控制锻造温度范围,特别是关键产品和高合金钢锻件,不准低温锻造。
锻后修整温度可比终锻温度低50-80℃。
5、返修品的加热温度应低于该件的始锻温度。
三、加热要求1、加热前,要熟悉加热规范,检查有关仪器仪表、点火装置和烧咀等,以保证加热炉在正常状态下工作。
2、坯料装炉前,应清理炉膛。
3、不同截面的钢料同炉加热时,按截面大的加热规范进行加热,先锻截面小的。
4、坯料装炉时,应合理放置,加热过程中要勤翻转,保证受热均匀。
5、在保证质量的前提下,一般钢种均可快速加热,以减小材料的氧化、脱碳,提高生产率。
6、高温时,在保证燃烧的情况下,应减少过剩空气量,使炉内保持正压,以免金属过热过烧。
7、坯料装炉时要少装、勤装,避免在高温区停留的时间过长。
因故超过最大保温时间不能锻造时,应降温保温,以免坯料烧坏。
8、铜料和钢料交替使用同一加热炉。
加热铜料时,必须用钢板将坯料与炉底、炉墙隔开。
加热铜料后的加热炉,必须用食盐彻底清理后方可加热钢料。
9、铜料与钢料不得同炉加热。
四、自由锻基本工序守则1、镦粗1、1镦粗前,坯料高度与直径(或边长)之比,不得超过2.5—3,最好在2—2.2的范围内。
1、2镦粗前,坯料高度应小于锻锤行程的75﹪。
1、3坯料两端面应平整并与轴心垂直。
1、4坯料表面不得有凹坑,裂纹等缺陷。
1、5镦粗时,要将坯料围绕其轴心线不停地转动,发生弯曲时必须立即校正。
承压设备用钢锻件、轧制或锻制钢棒 第1部分:一般要求-最新国标
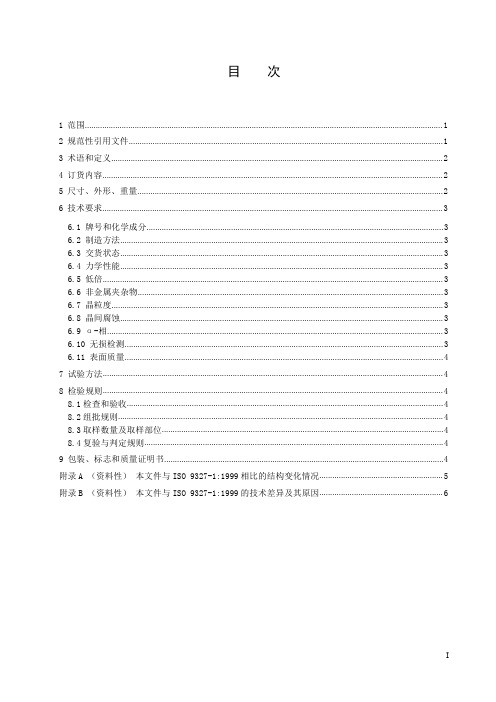
目次6.1牌号和化学成分.........................................................................................................................................36.2制造方法.....................................................................................................................................................36.3交货状态.....................................................................................................................................................36.4力学性能.....................................................................................................................................................36.5低倍.............................................................................................................................................................36.6非金属夹杂物.............................................................................................................................................36.7晶粒度.........................................................................................................................................................36.8晶间腐蚀.....................................................................................................................................................36.9α-相...........................................................................................................................................................36.10无损检测...................................................................................................................................................36.11表面质量...................................................................................................................................................47试验方法.............................................................................................................................................................48检验规则.............................................................................................................................................................1范围 (1)2规范性引用文件 (1)3术语和定义 (2)4订货内容 (2)5尺寸、外形、重量 (2)6技术要求 (3)48.1检查和验收..................................................................................................................................................48.2组批规则......................................................................................................................................................48.3取样数量及取样部位..................................................................................................................................48.4复验与判定规则..........................................................................................................................................49包装、标志和质量证明书.................................................................................................................................4附录A (资料性)本文件与ISO 9327-1:1999相比的结构变化情况.........................................................5附录B (资料性)本文件与ISO 9327-1:1999的技术差异及其原因 (6)承压设备用钢锻件、轧制或锻制钢棒第1部分:一般要求1范围本文件规定了承压设备用轧制、锻制钢棒或锻件的订货内容、尺寸、外形、重量、技术要求、试验方法、检验规则、包装、标志及质量证明书。
常见机械零部件技术要求规范总结

常见机械零部件技术要求一、机械零件常用技术要求:1、锐角倒钝、去除毛刺飞边。
2、零件去除氧化皮。
3、未注圆角半径R5。
4、未注倒角均为2×45°。
5、未注形状公差应符合GB1184-80的要求。
6、未注长度尺寸允许偏差±0.5mm。
7、零件加工表面上,不应有划痕、擦伤等损伤零件表面的缺陷。
8、精加工后的零件摆放时不得直接放在地面上,应采取必要的支撑、保护措施。
加工面不允许有锈蛀和影响性能、寿命或外观的磕碰、划伤等缺陷。
9、加工的螺纹表面不允许有黑皮、磕碰、乱扣和毛刺等缺陷。
二、铸件技术要求:1、铸件表面上不允许有冷隔、裂纹、缩孔和穿透性缺陷及严重的残缺类缺陷(如欠铸、机械损伤等)。
2、铸件应清理干净,不得有毛刺、飞边,非加工表面上的浇冒口应清理与铸件表面齐平。
3、对错型、凸台铸偏等应予以修正,达到圆滑过渡,一保证外观质量。
4、铸件非加工表面上的铸字和标志应清晰可辨,位置和字体应符合图样要求。
5、铸件非加工表面的粗糙度,砂型铸造R,不大于50μm。
6、铸件应清除浇冒口、飞刺等。
非加工表面上的浇冒口残留量要铲平、磨光,达到表面质量要求。
7、铸件上的型砂、芯砂和芯骨应清除干净。
8、铸件有倾斜的部位、其尺寸公差带应沿倾斜面对称配置。
9、铸件上的型砂、芯砂、芯骨、多肉、粘沙等应铲磨平整,清理干净。
10、铸件公差带对称于毛坯铸件基本尺寸配置。
11、铸件非加工表面的皱褶,深度小于2mm,间距应大于100mm。
12、机器产品铸件的非加工表面均需喷丸处理或滚筒处理,达到清洁度Sa2 1/2级的要求。
13、经喷丸或手工除锈的待涂表面与涂底漆的时间间隔不得多于6h。
14、铸件表面应平整,浇口、毛刺、粘砂等应清除干净。
15、铸件不允许存在有损于使用的冷隔、裂纹、孔洞等铸造缺陷。
16、所有需要进行涂装的钢铁制件表面在涂漆前,必须将铁锈、氧化皮、油脂、灰尘、泥土、盐和污物等除去。
17、除锈前,先用有机溶剂、碱液、乳化剂、蒸汽等除去钢铁制件表面的油脂、污垢。
GOST 8479-70 结构钢、碳钢和合金钢锻件一般技术规范

结构钢、碳钢和合金钢锻件的一般技术规范GOST 8479-70违反标准追究法律责任该标准涵盖了一般意义上的直径(厚度)至800mm,由锻造法或热模法制造的结构钢、碳钢、低合金钢和合金钢锻件。
该标准规定了锻件类别和对验收、交货的基本技术要求。
该标准不能代替现行的针对其他类型锻件的标准和技术规范,其他类型锻件指对生产方法、表面质量、采用专门热处理方式等有特别要求的锻件。
1.技术要求1.1锻件生产应当符合该标准,按照由既定程序确定的图纸和具体产品的技术规范文件来进行生产。
锻件按照测试类型分为以下几组,见表1.(变更条款,变更号No3)1.2由消费者指定锻件类别,在工件图纸上技术要求栏指出类别号码。
1.3按照消费者要求,锻件交货应当进行该标准之外的附加测试类型(白点测试,包曼试验、超声波探伤和潜望检测、剩余应力值的测定、工作温度下的屈服强度、测定工作温度下和零下温度下的冲击韧性、钢结构的宏观微观分析、弯曲试验、测定晶粒值等)。
在这种情况下,锻件可归入表1中的以下类别:II, III, IV, V.表1锻件类型IIIIII 测试类型不需测试测定硬度测定硬度1.测试拉力2.测定冲击韧性3.测定硬度1.测试拉力2.测定冲击韧性3.测定硬度成批次条件同种或不同钢牌号锻件同种或不同钢牌号锻件,同时进行热处理同种或不同钢牌号锻件,按照同样的方式进行热处理-硬度同上屈服强度收缩冲击韧性-屈服强度收缩冲击韧性-交货性能IV 同一炉钢锻件,同时进行热处理V 每个锻件都单独对待(完整版联系翻译者获取Q1)2.测试方法2.1按照同一个图纸生产的锻件,由生产企业编制成批。
编制成批的条件在表1中指明了。
允许把图纸不同但牌号相同、外形和尺寸相近的锻件合并成一批。
(变更条款,变更号No1)2.2如果订单中没有指出其他检测方法,则需不借助放大设备逐一检查锻件外观。
2.3对于除第I类外的其他各类锻件,必须测试的数量在表4中列出。
(完整版联系翻译者获取Q1)。
锻压执行标准
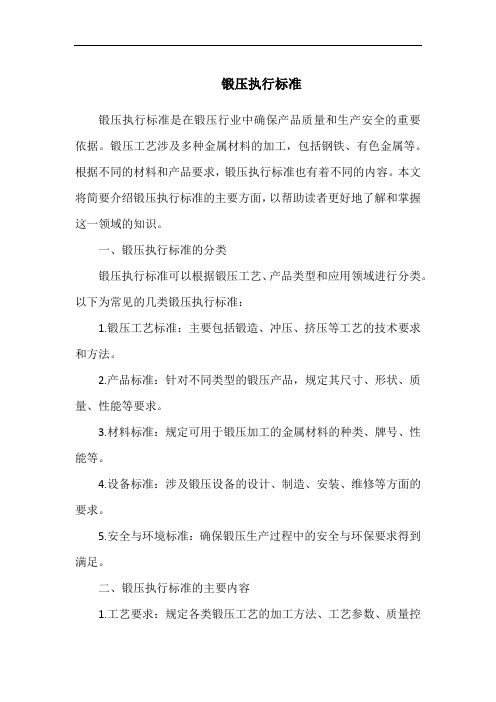
锻压执行标准锻压执行标准是在锻压行业中确保产品质量和生产安全的重要依据。
锻压工艺涉及多种金属材料的加工,包括钢铁、有色金属等。
根据不同的材料和产品要求,锻压执行标准也有着不同的内容。
本文将简要介绍锻压执行标准的主要方面,以帮助读者更好地了解和掌握这一领域的知识。
一、锻压执行标准的分类锻压执行标准可以根据锻压工艺、产品类型和应用领域进行分类。
以下为常见的几类锻压执行标准:1.锻压工艺标准:主要包括锻造、冲压、挤压等工艺的技术要求和方法。
2.产品标准:针对不同类型的锻压产品,规定其尺寸、形状、质量、性能等要求。
3.材料标准:规定可用于锻压加工的金属材料的种类、牌号、性能等。
4.设备标准:涉及锻压设备的设计、制造、安装、维修等方面的要求。
5.安全与环境标准:确保锻压生产过程中的安全与环保要求得到满足。
二、锻压执行标准的主要内容1.工艺要求:规定各类锻压工艺的加工方法、工艺参数、质量控制等方面的内容。
2.产品标准:详细描述各类锻压产品的尺寸公差、形位公差、表面质量等要求。
3.材料要求:对可用于锻压加工的金属材料进行分类,并规定其化学成分、力学性能、热处理要求等。
4.设备要求:涉及锻压设备的选型、设计、制造、安装、维修等方面的技术要求。
5.安全与环境要求:包括锻压生产过程中的安全防护措施、环保要求、职业健康等方面的内容。
三、锻压执行标准的应用与发展在我国,锻压执行标准在规范行业发展、提高产品质量、保障生产安全等方面发挥了重要作用。
随着科技的进步和行业的发展,锻压执行标准也将不断更新和完善。
未来,锻压执行标准的发展趋势包括:1.强化技术创新:紧跟行业发展趋势,引入新技术、新工艺,提高锻压产品质量。
2.绿色环保:加大环保要求,推动锻压行业向绿色、低碳、可持续发展方向转型。
3.智能化制造:融入智能制造理念,提高锻压生产过程的自动化、智能化水平。
4.安全生产:持续强化安全防护措施,降低锻压生产过程中的事故风险。
总之,锻压执行标准是保障锻压行业健康发展的关键。
- 1、下载文档前请自行甄别文档内容的完整性,平台不提供额外的编辑、内容补充、找答案等附加服务。
- 2、"仅部分预览"的文档,不可在线预览部分如存在完整性等问题,可反馈申请退款(可完整预览的文档不适用该条件!)。
- 3、如文档侵犯您的权益,请联系客服反馈,我们会尽快为您处理(人工客服工作时间:9:00-18:30)。
3.3供销部负责确认合格分供方。
4内容
4.1锻件分为承压锻件和非承压锻件。
4.2锻件用钢。
4.2.1锻件用钢应符合GB699、GB700、GB3077、及GB1591的规定。
4.2.2锻件用钢应采用平炉、电炉或纯氧吹转炉冶炼的镇静钢,也可以经供需双方协商,采
用热加工用轧材或钢锭(改制的钢坯)制成。
黑龙江北方有限责任公司技术标准
文件编号:HNVC/JW-15 NO.11
第0次修订
标题:锻件要求技术规范
修订日期:
实施日期:2010.11.20
版号:A
页码:1/2
1目的
规定本公司生产产品的原辅材料—锻件的技术要求、试验方法及验收规则。
2范围
适用于公司产品用碳素钢和合金钢锻件。
பைடு நூலகம்3职责
3.1技术部负责制定产品零件的锻件技术要求。
5相关文件
5.1《焊接和钎焊作业规范》(HNCV/JW-10 NO.11)
5.2《API6A产品材料要求规范》(HNVC/JW6A-001)
6质量记录
6.1《进货检验记录》(QR-08.2.4-01)
6.1《合格证明书》(供方)
建湖县博伟机械有限公司技术标准
JHBW/JW-04
锻件要求技术规范
版本号: A/0
壁厚的15%且不大于6mm,面积不超过所在表面的20%时,允许进行补焊。
4.9低倍组织和金相组织
4.9.1锻件不应存在白点,如发现有白点,则该锻件应予以报废,且与该锻件同熔炼炉号、
同炉热处理的锻件均应逐个检验。
4.9.2锻件不得存在过烧现象,过烧的锻件应予以报废。
4.9.3在含H2S环境下,使用的锻件材料必须符合《API6A材料要求规范》,及MR0175要求。
4.8外观质量
4.8.1锻件的形状和尺寸应符合锻件图的规定。
4.8.2锻件表面应有折叠、裂纹、结疤、夹层与锻伤等缺陷,如有上述缺陷,应满足下列
要求:
a、需加工的表面缺陷深度不超过公称单边余量的1/2,并保证加工后能完全消除。
b、非加工表面的局部缺陷在清除后,深度不超过该处壁厚的公称尺寸偏差。
c、如锻件表面缺陷深度超过上述规定,在不影响使用性能的情况下,其深度不超过该处
4.2.3使用的钢材均须具有出厂合格证明书,承压件和关键零件应根据产品要求出具性能试验报告单。
4.2.4对于设计压力P≥105MPa的承压产品锻件应采用有效的炉进行精炼技术冶炼。在钢锭
浇注以前或浇注期间应对钢水进行真空处理,以清除氢等有害气体。
4.3锻造
4.3.1锻造前应将钢材上影响锻件质量的表面缺陷全部清除。
文件编号:HNVC/JW-15 NO.11
第0次修订
标题:锻件要求技术规范
修订日期:
实施日期:2010.11.20
版号:A
页码:1/2
4.7.2 API产品的材料机械性能要求应满足《API6A材料要求规范》JHBW/6A-03。
4.7.3承压锻件需要进行机械性能测试,按《API6A材料要求规范》JHBW/6A-03。
4.3.2锻件应有足够的锻造比。承压锻件锻造时应采用镦粗拨长联合工艺。
a、采用钢锭锻造时,锻件主截面的锻造比不应小于3,对于设计压≥70Mpa的产品用
承压锻件,其主截面的锻造比为6—8。
b、采用轧材锻造时,锻造主截面的锻造比不应小于1.6。
4.4热处理
4.4.1锻件应进行锻后回火,以消除应力。
4.4.2热处理工艺应按锻件化学成份,截面大小由供方确定,但必须保证材料的机械性能。
4.5补焊
4.5.1只有在公司质量部同意下,才能允许补焊。
4.5.2补焊按《焊接和钎焊作业规范》JHBW/JW05执行。
4.6化学成份
4.6.1材料化学成份应满足《API6A材料要求规范》JHBW/6A-03。
4.7机械性能
4.7.1非承压锻件一般不作机械性能测试要求。
编制:
审核:
批准:
黑龙江北方有限责任公司技术标准
受控状态:
受控号:
修订状态
更改单编号
更改页次
更改内容简述
批准人
生效日期
1
2
3
4
5
发布日期:2008年05月20日实施日期:2008年05月20日