控制图的基本原理
质量管理05控制图

I—Rs图 计算移动极差Rsi
质量管理05控制图
控制图的绘制(续)
•4.(1)控制图样本参数的计算:
图名称 np图
步骤
计算平均不合格 品率
p 图 计算各组不合格 品率pi
c图 计算各样本的平 均缺陷数
u图 计算各样本的单 位缺陷数ui
计算公式
备注
(np)i——第i样本的 不合格品数(各样本 样本容量皆为n)
质量波动的来源主要有五个方面(简称 5M1E ):
• 操作人员(Man)——人 • 设备(Machine) —— 机 • 原材料(Material)——料 • 操作方法(Method)——法 • 环境(Environment)——环 • 测量(Measurement) ——测
质量管理05控制图
控制对象-质量波动(续)
质量管理05控制图
控制图的由来
•控制图的发展:
20世纪40年代,美国 贝尔电话公司应用统计质量 控制技术取得成效;美国军 方在军需物资供应商中推进 统计质量控制技术的应用; 美国军方制定了战时标准 Z1.1《质量控制指南》、 Z1.2《数据分析用的控制图 法》、 Z1.3《生产中质量管 理用的控制图法》。
质量管理05控制图
均值-极差控制图(续)
极差控制图随生产过程的特点不同 有其不同的作用: •在自动化水平比较高的生产过程中, 产品质量的一致性好。因此,当极差增 大,意味着机器设备出现故障.需要进 行修理或更换; •在非自动化生产过程中,极差反映出 操作者的技术水平,生产熟练程度,故 又称为操作者控制图。
–所谓满足规格要求,并不是指上、下控制线必须在规格上、下限内侧,
即UCL>TU;LCL< TL。而是要看受控工序的工序能力是否满足给定 的Cp值要求。
控制图
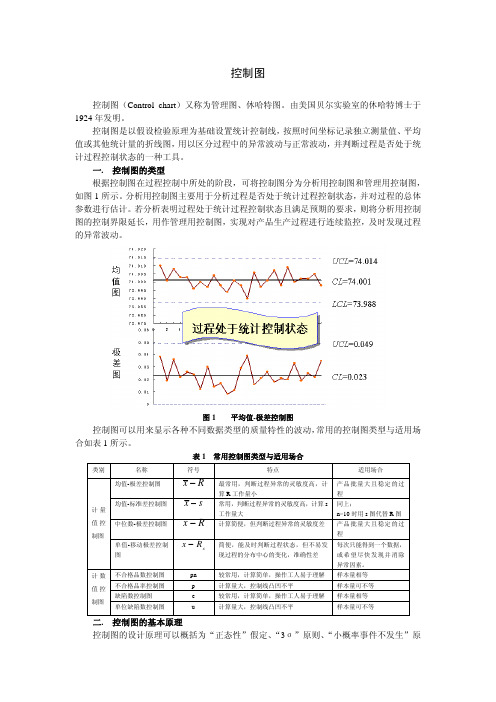
控制图控制图(Control chart)又称为管理图、休哈特图。
由美国贝尔实验室的休哈特博士于1924年发明。
控制图是以假设检验原理为基础设置统计控制线,按照时间坐标记录独立测量值、平均值或其他统计量的折线图,用以区分过程中的异常波动与正常波动,并判断过程是否处于统计过程控制状态的一种工具。
一. 控制图的类型根据控制图在过程控制中所处的阶段,可将控制图分为分析用控制图和管理用控制图,如图1所示。
分析用控制图主要用于分析过程是否处于统计过程控制状态,并对过程的总体参数进行估计。
若分析表明过程处于统计过程控制状态且满足预期的要求,则将分析用控制图的控制界限延长,用作管理用控制图,实现对产品生产过程进行连续监控,及时发现过程的异常波动。
图1 平均值-极差控制图控制图可以用来显示各种不同数据类型的质量特性的波动,常用的控制图类型与适用场合如表1所示。
表1 常用控制图类型与适用场合二. 控制图的基本原理控制图的设计原理可以概括为“正态性”假定、“3σ”原则、“小概率事件不发生”原理和“统计反证推断”思想。
具体说就是,假定所收集的质量特性数据服从正态分布,在此假定下,过程特性值落在分布中心上下各三倍标准差范围内的概率是99.73%,也就是说质量特性值落在上下三倍标准差之外的概率仅为0.27%,这是一个小概率事件,而“小概率事件不发生”原理认为小概率事件在一次观测中不发生,因此,一旦控制图出现“小概率事件发生”的现象,则表明过程发生了异常变化,这就是“统计反证推断”思想。
表2和表3分别表示计量值控制图和计数值控制图的中心线和控制界限的公式,以及样本量的确定。
表2 计量值控制图的中心线和控制界限表3 计量值控制图的中心线和控制界限三. 控制图的应用控制图显示随时间采集的数据和由这些数据计算出的波动;控制图与过程能力分析结合在一起称为统计过程控制(SPC)。
图2是一个典型的SPC的应用流程。
图2 典型的SPC的应用流程。
统计学中的控制图应用

统计学中的控制图应用统计学是一门研究数据收集、分析和解释的学科,它在各个领域都有广泛的应用。
其中,控制图是统计学中的一种重要工具,用于监控和控制过程的稳定性和质量。
本文将介绍控制图的基本原理和应用,并探讨其在实际问题中的重要性。
一、控制图的基本原理控制图是一种图形化的工具,用于显示过程的数据和统计信息。
它通过将过程数据与控制限相比较,帮助我们判断过程的稳定性和质量。
控制限是根据统计学原理计算得出的上下限值,当过程数据超出这些限制时,表明过程存在异常变化。
在控制图中,通常有中心线、上控制限和下控制限。
中心线代表过程的平均水平,上控制限和下控制限分别代表过程的变异范围。
当过程数据在这些限制之间波动时,我们可以认为过程是稳定的。
如果数据超出控制限,我们需要进一步分析问题的原因,并采取相应的措施进行改进。
二、控制图的应用控制图广泛应用于各个行业和领域,包括制造业、服务业、医疗保健等。
它可以帮助我们实时监控过程的稳定性,及时发现问题并采取措施进行纠正。
下面我们将以制造业为例,介绍控制图的应用。
在制造业中,产品质量是一个重要的关注点。
通过使用控制图,我们可以监控产品的关键特性,并及时发现任何异常变化。
例如,在汽车制造过程中,我们可以使用控制图来监控发动机的排放水平。
如果排放水平超出控制限,我们可以迅速发现问题,并检查是否存在零部件的故障或者生产过程中的变化。
这样可以帮助我们及时采取措施,确保产品质量符合标准。
除了产品质量,控制图还可以应用于监控生产过程的稳定性。
在制造业中,生产过程的稳定性对于产品的一致性和效率至关重要。
通过使用控制图,我们可以监控关键过程参数的变化,并及时发现任何异常情况。
例如,在电子芯片制造过程中,我们可以使用控制图来监控温度和湿度等参数。
如果这些参数超出了控制限,我们可以立即采取措施,避免不良产品的产生。
三、控制图的重要性控制图在实际问题中的应用非常重要。
它可以帮助我们实时监控过程的稳定性和质量,并及时采取措施进行改进。
控制图的原理
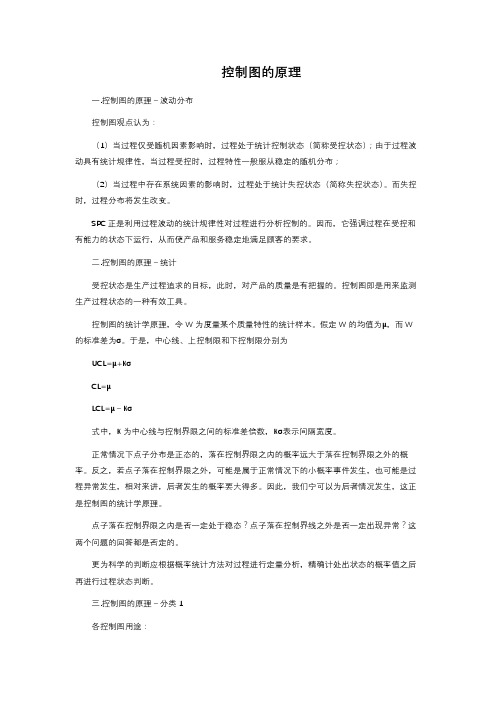
控制图的原理一.控制图的原理-波动分布控制图观点认为:(1)当过程仅受随机因素影响时,过程处于统计控制状态(简称受控状态);由于过程波动具有统计规律性,当过程受控时,过程特性一般服从稳定的随机分布;(2)当过程中存在系统因素的影响时,过程处于统计失控状态(简称失控状态)。
而失控时,过程分布将发生改变。
SPC正是利用过程波动的统计规律性对过程进行分析控制的。
因而,它强调过程在受控和有能力的状态下运行,从而使产品和服务稳定地满足顾客的要求。
二.控制图的原理-统计受控状态是生产过程追求的目标,此时,对产品的质量是有把握的。
控制图即是用来监测生产过程状态的一种有效工具。
控制图的统计学原理,令W为度量某个质量特性的统计样本。
假定W的均值为μ,而W 的标准差为σ。
于是,中心线、上控制限和下控制限分别为UCL=μ+KσCL=μLCL=μ-Kσ式中,K为中心线与控制界限之间的标准差倍数,Kσ表示间隔宽度。
正常情况下点子分布是正态的,落在控制界限之内的概率远大于落在控制界限之外的概率。
反之,若点子落在控制界限之外,可能是属于正常情况下的小概率事件发生,也可能是过程异常发生,相对来讲,后者发生的概率要大得多。
因此,我们宁可以为后者情况发生,这正是控制图的统计学原理。
点子落在控制界限之内是否一定处于稳态?点子落在控制界线之外是否一定出现异常?这两个问题的回答都是否定的。
更为科学的判断应根据概率统计方法对过程进行定量分析,精确计处出状态的概率值之后再进行过程状态判断。
三.控制图的原理-分类1各控制图用途:均值-极差控制图:是最常用、最基本的控制图,它用于控制对象为长度、重量、强度、纯度、时间和生产量等计量值的场合。
均值-标准差控制图:次图与上图类似,极差计算简便,故R图得到广泛应用,但当样本大小或0>10或12时,应用极差估计总体标准差的效率减低,最好应用S图代替R图。
中位数-极差控制图:由于中位数的计算比均值简单,所以多用于现场需要把测定数据直接记入控制图进行管理的场合。
控制图原理
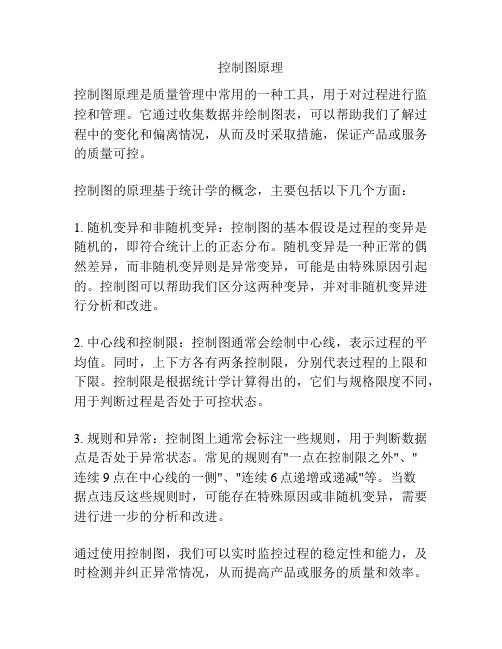
控制图原理
控制图原理是质量管理中常用的一种工具,用于对过程进行监控和管理。
它通过收集数据并绘制图表,可以帮助我们了解过程中的变化和偏离情况,从而及时采取措施,保证产品或服务的质量可控。
控制图的原理基于统计学的概念,主要包括以下几个方面:
1. 随机变异和非随机变异:控制图的基本假设是过程的变异是随机的,即符合统计上的正态分布。
随机变异是一种正常的偶然差异,而非随机变异则是异常变异,可能是由特殊原因引起的。
控制图可以帮助我们区分这两种变异,并对非随机变异进行分析和改进。
2. 中心线和控制限:控制图通常会绘制中心线,表示过程的平均值。
同时,上下方各有两条控制限,分别代表过程的上限和下限。
控制限是根据统计学计算得出的,它们与规格限度不同,用于判断过程是否处于可控状态。
3. 规则和异常:控制图上通常会标注一些规则,用于判断数据点是否处于异常状态。
常见的规则有"一点在控制限之外"、"
连续9点在中心线的一侧"、"连续6点递增或递减"等。
当数
据点违反这些规则时,可能存在特殊原因或非随机变异,需要进行进一步的分析和改进。
通过使用控制图,我们可以实时监控过程的稳定性和能力,及时检测并纠正异常情况,从而提高产品或服务的质量和效率。
它可以帮助我们识别潜在问题或改进机会,优化过程,并支持持续改进的目标。
控制图的原理及应用
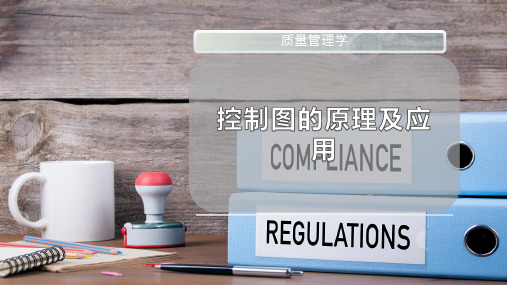
本:
,其平均值 x1, x有2,如…,下xn性质:
x
E(x)
(x)
n
和 则可通过k组大小为n的样本得到:
ˆ x
ˆ R
d2
其中, 是由n来d2确定的控制系数,可以通过查取计量控制图系数表(见表7-4)
得到。
12
二、计量值控制图
• 所以,由控制界限的一般公式即可得到图的控制界限为:
• 式中,
4
一、控制图基本原理
质 量 特 性 值
O
UCL CL
LCL 样本组号
5
一、控制图基本原理
(二)控制图的统计原理
1. 原理 3
当质量特性值服从正态分布时, 3即
X ~ N(, 2)
如果 生E(产X )过程中仅存在偶然因素,那么其产品质量特性值将会有
99.73%落在
的范围内。 3
6
一、控制图基本原理
c4
由此可以得到 图中x s 图的控x制界限为:
UCL
3 x 3s
n
c4 n
CL x
x
A3s
LCL
3
n
x
3s c4 n
x
A3s
• 式中
A3
3 c4
n
18
二、计量值控制图
• s图的控制界限为:
UCL c4 3
1 c42
3 s
1 c42 s c4
B4s
CL c4 s
LCL
• (三)控制图的分类——计量
分布 控制图类型 符号表示
适用范围及特点
平均值—极 差
控制图
xR 图
用于判断过程质量特性的均值以及极差(间接估算标 准差)是否处于所要求的水平,针对重量、长度、强 度等计量值控制对象,适用于产品批量较大且较为稳 定的工序,是最常用、最基本的控制图。判断工序异 常的灵敏度高,且极差计算工作量小
控制图原理介绍
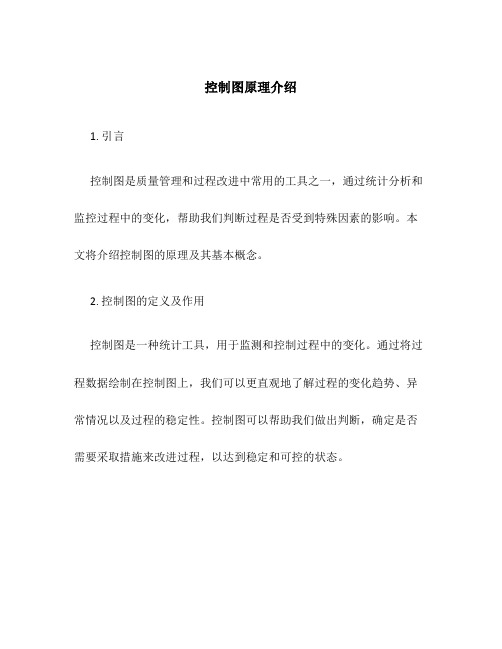
控制图原理介绍1. 引言控制图是质量管理和过程改进中常用的工具之一,通过统计分析和监控过程中的变化,帮助我们判断过程是否受到特殊因素的影响。
本文将介绍控制图的原理及其基本概念。
2. 控制图的定义及作用控制图是一种统计工具,用于监测和控制过程中的变化。
通过将过程数据绘制在控制图上,我们可以更直观地了解过程的变化趋势、异常情况以及过程的稳定性。
控制图可以帮助我们做出判断,确定是否需要采取措施来改进过程,以达到稳定和可控的状态。
3. 控制图的原理控制图基于统计学的基本原理,主要应用了过程能力分析和统计过程控制两个方面的方法。
3.1 过程能力分析过程能力分析是通过收集和分析数据来评估过程的稳定性和可控性。
它用一些指标来衡量过程的能力,如均值、方差等。
控制图中的中心线代表过程的平均值,而控制限代表过程的变异范围。
如果过程的数据点落在控制限之内,则说明过程是稳定的,否则可能存在特殊因素的影响。
3.2 统计过程控制统计过程控制是一种通过统计方法来监控过程的变化,并及时采取控制措施以避免过程产生不良品或错误结果的方法。
控制图中的控制限可以帮助我们判断过程是否处于可控状态。
如果数据点超出了控制限,就意味着过程发生了异常情况,需要进一步分析并采取相应的纠正措施。
4. 控制图的基本概念4.1 中心线控制图中的中心线代表过程的平均值。
它通常通过计算一组数据的平均值来确定。
4.2 控制限控制图中的控制限用于判断过程是否处于可控状态。
控制限分为上限和下限两个值。
上限代表过程的上界,下限代表过程的下界。
如果数据点超出了控制限,就意味着过程发生了异常情况。
4.3 标准差标准差是衡量数据的离散程度的指标。
在控制图中,标准差用于计算控制限。
较大的标准差意味着过程的变异性较大,而较小的标准差意味着过程的稳定性较高。
4.4 规格限规格限是工程师或客户规定的过程上下界限。
如果数据点超出了规格限,就意味着产品或过程不符合规格要求,需要进行调整或改进。
控制图与过程能力分析

控制图与过程能力分析控制图是一种用于监控过程稳定性和一致性的工具,它通过监控产品或过程的变异性来确保产品质量以及生产效率。
在工业生产中,控制图被广泛应用于监控制造过程中的变异性,以便及时发现和纠正问题,从而确保产品的稳定性和一致性。
与此同时,过程能力分析则是用于评估制造过程的稳定性和一致性的工具,它可以帮助企业确定其生产过程是否能够满足产品质量要求。
因此,控制图与过程能力分析在生产管理中扮演着至关重要的角色。
控制图的原理和类型控制图是一种通过统计方法来监控过程稳定性的工具,它可以帮助生产者及时发现和纠正生产过程中的问题。
控制图的原理是将生产过程中的数据进行分类,然后根据统计学方法对数据进行分析,以便确定过程是否处于稳定状态。
控制图的基本原理是将数据按照时间顺序绘制在图表上,并根据统计学规则来判断生产过程的稳定性。
常见的控制图类型包括X-bar图、R 图、P图和C图等,每种类型的控制图都有着不同的应用范围和适用条件。
X-bar图是一种用于监控过程平均值的控制图,它可以帮助生产者了解生产过程的变异情况。
R图则是用于监控过程变异性的控制图,它可以帮助生产者了解生产过程的一致性。
P图和C图则是用于监控不合格品率的控制图,它们可以帮助生产者了解生产过程的品质情况。
通过绘制这些不同类型的控制图,生产者可以全面了解生产过程的稳定性和一致性,从而及时发现和纠正生产过程中的问题。
过程能力分析的原理和方法过程能力分析是一种用于评估生产过程稳定性和一致性的工具,它可以帮助企业确定其生产过程是否能够满足产品质量要求。
过程能力分析的原理是通过统计方法对生产过程的数据进行分析,以便评估过程的稳定性和一致性。
常见的过程能力指标包括过程能力指数(Cp)、过程能力指数(Cpk)以及过程性能指数(Pp)和过程性能指数(Ppk)等,它们可以帮助企业全面了解生产过程的稳定性和一致性。
通过计算这些过程能力指标,企业可以全面了解生产过程的稳定性和一致性,从而确定生产过程是否能够满足产品质量要求。
- 1、下载文档前请自行甄别文档内容的完整性,平台不提供额外的编辑、内容补充、找答案等附加服务。
- 2、"仅部分预览"的文档,不可在线预览部分如存在完整性等问题,可反馈申请退款(可完整预览的文档不适用该条件!)。
- 3、如文档侵犯您的权益,请联系客服反馈,我们会尽快为您处理(人工客服工作时间:9:00-18:30)。
控制图的基本原理
则称的分布为正态分布,记为。
正态分布的概率密度函数如图5—1所示。
图5-l 正态分布概率密度曲线从图中我们叫以看出正态分布有如下
性质:
(1)曲线是对称的,对称轴是x=μ;
(2)曲线是单峰函数,当x=μ时取得最大值;
(3)当曲时,曲线以x轴为渐近线;
(4)在处,为正态分布曲线的拐点;
(5)曲线与x轴围成的面积为1。
另外,正态分布的数字特征值为:
平均值
标准偏差
数字特征值的意义:平均值μ规定了
图形所在的位置。
根据正态分布的性质,在x=μ处,曲线左右对称且为其峰值点。
标准偏差,规定了图形的形状。
图5-2给出了3个不同的值时正态分布密度曲线。
当小时,各数据较多地集中于μ值附近,曲线就较“高”和“瘦”;当大时,数据向μ值附近集中的程度就差,曲线
的形状就比较“矮”和“胖”。
这说明正态分布的形状由的大小来决定。
在质量管理中,反映了质量的好坏,越小,质量的一致性越好。
图5-2 大小不同时的正态分布
在正态分布概率密度函数曲线下,介于坐标,,,间的面积,分别占总面积的58.26%,95.45%,99.73%和99.99%。
它们相应的几何意义如图5-3听示。
图5-3 各种概率分布的几何意义二、控制图的轮廓线
控制图是画有控制界限的一种图表。
如图5-4所示。
通过它可以看出质量变动的情况及趋势,以便找出影响质量变动的原因,然后予以解决。
图5-4 控制图
我们已经知道:在正态分布的基本性质中,质量特性数据落在[μ±3]范围内的概率为99.73%,落在界外的概率只有
0.27%,超过一侧的概率只有0.135%,这是一个小概率事件。
这个结论非常重要,控制图正是基于这个结论而产生出来的。
现在把带有μ±3线的正态分布曲线旋转到一定的位置(即正态分布曲线向右旋转9,再翻转),即得到了控制图的基本形式,再去掉正态分布的概率密度曲线,就得到了控制图的轮廓线,其演变过程如图5-5所示。
图5—5 控制图轮廓线的演变过程通常,我们把上临界线(图中的μ+3线)称为控制上界,记为UCL(Upper Control Limit),平均数(图中的μ线)称为中心线,记为CL (Central Line),下临界线(图中μ-3线)称为控制下界,记为LCL(Lower Control Limit)。
控制上界与控制下界统称为控制界限。
按规定抽取的样本值用点子按时间或批号顺序标在控制图中,称为描点或打点。
各个点子之间用实线段连接起来,以便看出生产过程的变化趋势。
若点子超出控制界限,我们认为生产过程有变化,就要告警。
三、两种错误和3方式
从前面的论述中我们已知,如果产品质量波动服从正态分布,那么产品质量特性值落在μ土3控制界限外的可能性是
0.27%,而落在一侧界限外的概率仅为0.135%。
根据小概率事件在一次实验中不会发生的原理,若点子出界就可以判断生产有异常。
可是0.27%这个概率数值虽然很小,但这类事件总还不是绝对不可能发生的。
当生产过程正常时,在纯粹出于偶然原因使点子出界的场合,我们根据点子出界而判断生产过程异常,就犯了错发警报的错误,或称第一种错误。
这种错误将造成虚惊一场、停机检查劳而无功、延误生产等损失。
为了减少第一种错误,可以把控制图的界限扩大。
如果把控制界限扩大到μ±4,则第一种错误发生的概率为0.006%,这就可使由错发警报错误造成的损失减小。
可是,由于把控制界限扩大,会增大另一种错误发生的可能性,即生产过程已经有了异常,产品质量分布偏离了原有的典型分布,但是总还有一部分产品的质量特性值在上下控制界限之内,参见图5-6。
如果我们抽取到这样的产品进行检查,那么这时由于点子未出界而判断生产过
程正常,就犯了漏发警报的错误,或称第二种错误。
这种错误将造成不良品增加等损失。
图5-6控制图的两种错误要完全避免这两种错误是不可能的,一种错误减小,另一种错误就要增大,但是可以设法把两种错误造成的总损失降低
到最低限度。
也就是说,将两项损失之和是最小的地方,取为控制界限之所在。
以μ±3 为控制界限,在实际生产中广泛应用时,两种错误造成的总损失为最小。
如图5-7所示。
这就是大多数控制图的控制界限都采用μ±3方式的理由。
图5—7 两种错误总损失最小点。