生产运作与管理8 第8章 作业计划与控制
生产与运作管理 第8讲 生产作业计划制定
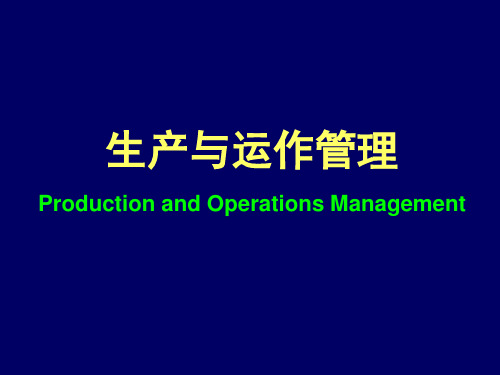
—— 零件工序生产周期
第8讲
Top —— 工序生产周期(小时/分) 该制品该工序的实际加工时间与工序准备时间之和,通常 t 用该工序工时定额来表示。 —— 单件工序时间(小时/分) Q —— 一批零件的数量(件)
一批制品的工序生产周期 S —— 同时完成该工序的设备数; 该批零件在一道工序上的实际加工时间、工序准备时间之 Fe —— 有效工作时间总额(小时/分) 和: Kt —— 工时定额完成系数;
生产与运作管理
Production and Operations Management
第八讲 生产作业计划制定
生产作业计划工作的任务与内容 期量标准 厂级生产作业计划的编制 车间作业计划的编制
第8讲
2
企业经营战略
生 产 与 运 作 管 理 的 知 识 体 系
生产运作战略
时间、质量、成本 、服务、柔性
外购件 10天 11
总装
5天 1 2
试车 1天 1 3
表面处理 6
冲压
3天83天1 022件 号
批 量
工 5 2 4 8 4 2 毛 毛 毛 3 9 坯 坯 坯 3 6 机 机 机 机 3 3 3 0 加 加 加 加
作 2 7 保 险 期
日 2 4 2 1 1 8 1 5 1 2 9 6 3
01-1
Qt Top Tse SFe K t
Tse —— 准备结束时间。
16
期量标准 —— 生产周期
—— 零件工序生产周期
第8讲
大量大批生产的工序生产周期
流水生产线:由于流水生产线的特定要求,零件的工序生 产周期即为流水生产线的节拍; 成批生产方式:其工序生产周期可按一批零件的工序生产 周期计算公式进行计算。
生产运作管理(各章节学习)

主题:导论——重点知识点讲解(生产管理、运营管理、生产运作管理的概念,霍桑试验结论)1、生产管理:又称生产控制,是有计划、组织、指挥、监督调节的生产活动。
以最少的资源损耗,获得最大的成果。
是对企业生产系统的设置和运行的各项管理工作的总称。
2、运营管理:就是对运营过程的计划、组织、实施和控制,是与产品生产和服务创造密切相关的各项管理工作的总称。
从另一个角度来讲,运营管理也可以指为对生产和提供公司主要的产品和服务的系统进行设计、运行、评价和改进。
3、生产运作管理:是指为了实现企业经营目标.提高企业经济效益,对生产运作活动进行计划、组织和控制等一系列管理工作的总称。
生产运作管理有狭义和广义之分:狭义的生产运作管理仅局限于生产运作系统的运行管理,实际上是以生产运作系统中的生产运作过程为中心对象。
广义的生产运作管理不仅包括生产运作系统的运行管理,而且包括生产运作系统的定位与设计管理,可以认为是选择、设计、运行、控制和更新生产运作系统的管理活动的总和。
4、霍桑试验:实验结论:1、改变工作条件和劳动效率没有直接关系;2、提高生产效率的决定因素是员工情绪,而不是工作条件;3、关心员工的情感和员工的不满情绪,有助于提高劳动生产率。
说明起初,一九二四年西方电子公司在伊利诺州的霍桑工厂做了一个实验(Hawthorne Studies,1927~1932),这个实验在于找出是否有「疲劳」之外但会降低生产力的因素。
工人坡分成两组:一组为控制组,所有工人都往环境不变的情况下持续工作,一组为实验组;实验本身是为了观察工作环境经过各种改变时工人的反应情形,并比较两组之生产力。
霍桑实验的工作环境改变是透过改变照明亮度来观察,结果是,亮度增加,生产力增加,但亮度逐渐下障生产力仍然继续升高。
更奇异的是,控制组的照明其实一点都没改变,但生产力仍会上升。
甚至,实验人员延长工时或减少休息时间,生产力也会上升。
许多工人都比实验前更满意自己的工作。
生产与运作管理8章生产运作总计划与控制

(3)技术组织条件:产品、工艺设备、劳动组织等方面。 (4)企业生产能力是企业内部各个生产环节的综合生 产能力。
2019/2/6
授人以鱼不如授人以渔
23
影响生产能力的因素
人员能力 人员数量 工作时间 出勤率 技术水平 设备能力 设备数量 技术水平 开动率 完好率 管理能力 管理水平
工作态度
2019/2/6
授人以鱼不如授人以渔
10
2019/2/6
短期生产计划
短期生产计划,又称为生产作业计划,它的计 划期在半年以下,一般为月或跨月计划。 包括:物料需求计划、生产能力需求计划等。 任务:是直接根据顾客的定单,合理地安排生 产活动的每一个细节,使它们紧密衔接,以确 保按顾客要求的质量、数量和交货期交货。
第七章 生产能力计划
主讲:朱明
高级技师、经济师、工程师 高级技能专业教师 汽车维修工高级考评员
2019/2/6
授人以鱼不如授人以渔
1
第八章 总体计划
第一节 总体计划概述 第二节 总体计划的编制方法 第三节 关于总体计划的讨论
2019/2/6
授人以鱼不如授人以渔
2
第一节 生产运作总体计划概述
80
50
275
55
300
按假定产品得出的产品年产量为:27+82+136+55=300 与具体产品得出的年产量之和相等。 ◆编制计划时可以先用假定产品优化,然后再将优化
结果转换成具体产品。
2019/2/6
授人以鱼不如授人以渔
30
5、生产能力与生产任务的平衡
(1)内容
※ 生产能力与生产任务进行比较; ※ 按比较的结果采取措施; ※ 计算能力利用指标。
第八章 生产运作计划与控制
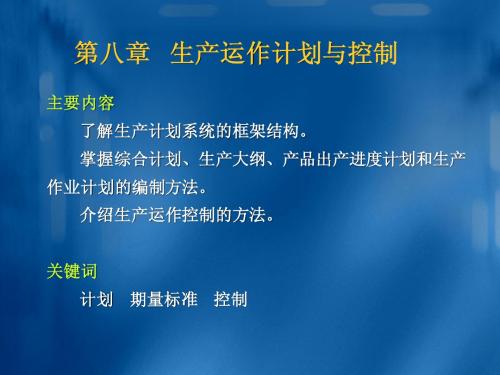
5元/单位/月 单位/ 10元/单位 10元 5元/小时(40元/日) 小时(40元 7元/小时(8小时以上) 小时( 小时以上) 1.6小时/单位 1.6小时 小时/
提高生产率的成本(培训和新聘) 10元/单位 提高生产率的成本(培训和新聘) 10元 降低生产率的成本(解聘) 降低生产率的成本(解聘) 15元/单位 15元
1.5
综合计划的方法
MTS (备货生产) 备货生产) MTO (按单生产) 按单生产)
综合计划的成本
员工雇佣和解雇成本 兼职员工的工资 设备引进技术改造的成本 外包成本
加班工资 库存费用 缺货损失 质量损失
综合计划评价标准
成本最低
1.5.1
综合计划的方法- 综合计划的方法-图表法
案例: 屋顶材料生产的综合计 案例: 划
分配计划
物料需求计划(MRP) 物料需求计划(MRP) 需求管理 生产运作作业计划 订货合同 生产运作控制
能力控制
1 综合计划 1.1综合计划体系 综合计划体系
市场和需求 产品决策 研究和技术
生产能力决策
劳动力 可获得的原材料
需求预测, 需求预测,定单
综合计划 现有库存 主生产计划 MRP系统 和MRP系统 详细的工作排程 外部生产能力(转包) 外部生产能力(转包)
1.5.3
综合计划的方法- 综合计划的方法-收入盈亏顺序法
确定产品品种的一种方法以销售收入顺序为横坐标,盈 确定产品品种的一种方法以销售收入顺序为横坐标,
利顺序为纵坐标,将各品种对应地列入坐标图中 利顺序为纵坐标,
盈利 顺序 M .A C . .B N . G . D O . F . H . J
N‘
期初库存:45 生产批量:80 生产批量: 期初库存: 4月 周 次 1 2 3 20 20 20 需求预计 23 15 8 顾客订货 现有库存量 MPS量 MPS量 ATP量 ATP量 22 0 7 2 0 62 80 68
蔡建华-生产与运作管理-08 生产作业计划与控制
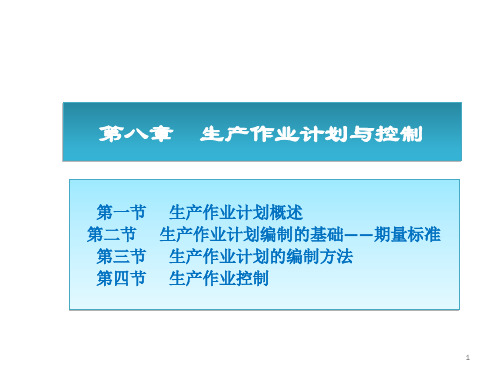
图8.1 成批生产时在制品占用的各种情况
(2) 车间之间周转在制品定额 它是处于车间之间的中间仓库,它们的储备量经常处于
变动之中,假如是前车间是成批入库,后车间每日领用,其 变化如图8.2所示。
图8.2 中间仓库库存量的变化情况
假设用Q为前车间的批量,Zi 库存周转在制品平均储备量。 则: Zi=(1/2)×Q,最大库存量为Q。在制品定额应为(Q /2+保险
Q (2NA / C)1/2
上式计算出的批量还应当进行适当调整,其调整原则是: ① 应使一批产品在主要工序的加工时问不少于半个轮班的产量,
或在数量上与月产量成倍数关系。 ② 批量的大小应与工艺装备的使用寿命相适应。并与夹具、工
位器具的要求相适应。 ③ 应遵循大件小批量,小件大批量的原则。 ④ 一般情况下应当是:毛坯批量>加工批量>装配批量,相互
tad——准备结束时间; Qmin——最小批量; t——单件工时。 损失系数由经验确定,可参考下表8-1(设备的调整时间损失系数),一般应在 0.02—0.1之间
表8-1 设备的调整时间损失系数
生产类型
零件体积
大批
中批
小批
大件
0.03
中件
0.04
小件
0.05
0.04
0.05
0.05
0.08
0.08
0.1
合理的期量标准,有助于建立正常的生产秩序和 工作秩序,组织均衡生产,充分利用生产能力,缩 短产品生产周期,加速流动资金周转,提高企业经 济效益。
注意点:期量标准是编制生产作业计划的依据。
8
8.2.2期量标准的类型 流水生产的期量标准有:节拍、标准计划、在制品定额等; 成批生产的期量标准有:批量、生产间隔期、生产周期、投入
生产运作管理重点
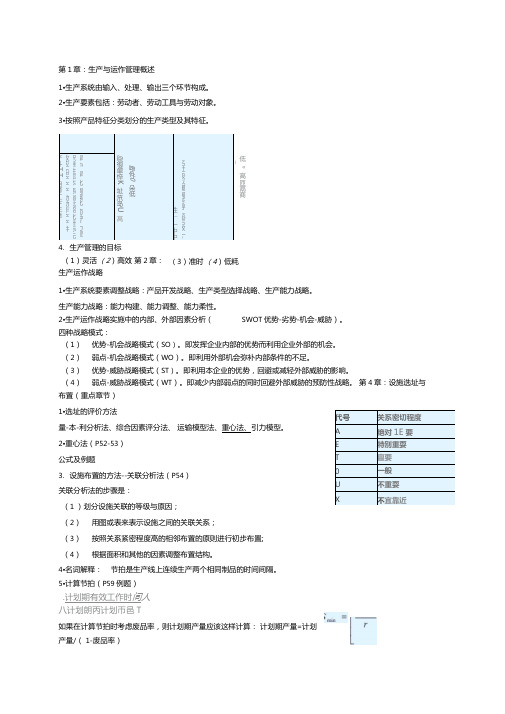
第1章:生产与运作管理概述1•生产系统由输入、处理、输出三个环节构成。
2•生产要素包括:劳动者、劳动工具与劳动对象。
3•按照产品特征分类划分的生产类型及其特征。
4. 生产管理的目标(1)灵活 (2)高效 第2章:生产运作战略1•生产系统要素调整战略:产品开发战略、生产类型选择战略、生产能力战略。
生产能力战略:能力构建、能力调整、能力柔性。
2•生产运作战略实施中的内部、外部因素分析(SWOT 优势-劣势-机会-威胁)。
四种战略模式: (1) 优势-机会战略模式(SO )。
即发挥企业内部的优势而利用企业外部的机会。
(2) 弱点-机会战略模式(WO )。
即利用外部机会弥补内部条件的不足。
(3) 优势-威胁战略模式(ST )。
即利用本企业的优势,回避或减轻外部威胁的影响。
(4)弱点-威胁战略模式(WT )。
即减少内部弱点的同时回避外部威胁的预防性战略。
第4章:设施选址与布置(重点章节)1•选址的评价方法量-本-利分析法、综合因素评分法、 运输模型法、重心法、引力模型。
2•重心法(P52-53)公式及例题3. 设施布置的方法--关联分析法(P54)关联分析法的步骤是:(1 )划分设施关联的等级与原因; (2) 用图或表来表示设施之间的关联关系;(3) 按照关系紧密程度高的相邻布置的原则进行初步布置; (4)根据面积和其他的因素调整布置结构。
4•名词解释: 节拍是生产线上连续生产两个相同制品的时间间隔。
5•计算节拍(P59例题).计划期有效工作时间人 八计划朗丙计划帀邑T如果在计算节拍时考虑废品率,则计划期产量应该这样计算: 计划期产量=计划产量/( 1-废品率)稈 护 稈 化 调虞化 菊种«力程駅准性率本孫崩批能化卅标无牧应 船产产产动动作产产件 产斗T.T.自育工卞生举啰件0 朵低屁很单悴K 址笊岛U髙名牡股以履阀芳寻甌宅救一-牲一一中中低«髙匝鬲商m 少丸圉很简很低咆低代号 关系密切程度 A 绝对1E 要 E 特別重耍 T 亶要 0 一般 U 不重耍 X 不宜靠近(3)准时 (4)低耗6•计算最小工作地数目Ti----为第i个工序的单件工作时间。
生产与运作管理第二版 第8章 生产计划
已知:
产品 A B
可供资源
单价 4 5
单位耗材 单位耗人工 1 4 3 3 12 24
设生产A产品X1台,生产B产品X2台,则 Max Z = 4X1 + 5X2 S.t. X1 + 3X2 ≦ 12
168 176 176 168 184 168 168 160 160 160 152 176
190 159 136 119 163 238 298 313 375 375 329 227
37 31 23 17 44 75 60 15 62
46 102
7400 6200 4600 3400 13200 22500 18000 4500 18600 0 9200 20400 128000
1、 改变需求的办法
通过改变价格转移需求 推迟交货 改变劳动力数量 忙时加班加点,闲时培训 利用半时工人 利用库存调节 转包 改变自制和外购的决策
2、 调整能力的办法
利用库存调节
改变库存水平,维持生产速率不变
需求/产量 需求速率变化
生产速率恒定
库存上升
库存下降
时间
8.2.2 反复试验法
大量生产,品种单一,可用具体产品数表 示生产能力; 大批生产,品种数少,可用代表产品数表 示生产能力; 代表产品——结构与工艺有代表性,且产 量与劳动量乘积最大的产品。 多品种、中小批量生产,以假定产品的产 量来表示生产能力; 假定产品——按各种具体产品工作量比重 构成的一种实际上不存在的产品。
代表产品法
采用的优化方 法举例
生产与运作管理-第8章---制造业作业计划
明J
的
i
实
际完工
时间超过了完工期限,
Li 0,说明Ji提前完工,Li 0,说明按期完工。Lmax max{Li}为最长延迟时间。
4、排序问题分类和表示法
排序问题的分类
(1)按机器的种类和数量:单台/多台。
■多台机器排序问题:按工件加工路线特征(相同与否),分 为单件(JOB-SHOP)作业排序和流水作业(FLOW-SHOP)排序 问题。
2、约翰森算法:
(1)从加工时间矩阵中找出最短加工时间; (2)若最短加工时间出现在机器 M1上,则对应工件应该 尽可能往前排;若最短加工时间出现在机器M2 上,则对应 工件应该尽可能往后排。然后从加工时间矩阵中划去已排序 工件的加工时间。若最短加工时间有多个,则任挑一个。
2021/4/9
17
8.2.2 两台机器排序问题的最优算法(续)
T 零件平行移动的加工周期 平 为: m T平 ti (n1)tL i1 tL : 为最长的单件工序时间
例题:已知n=4, t1 10分钟 t2 5分钟
t3 15分钟t4 10分钟
“工件”代表“服务对象”。工件可以是单个零件, 也可以是一批相同的零件。
“加工路线”是工件加工的工艺过程决定的,它是 工件加工在技术上的约束。
“加工顺序”则表示每台机器加工n个零件的先后 顺序,是排序和编制作业计划要解决的问题。
2021/4/9
6
3、假设条件与符号说明
假设条件(6个):
(1)一个工件不能同时在几台不同的的机器上加工; (2)工件在加工过程中采取平行移动方式,即当上一道
Work Center #2 Output
11
8.2.1 最长流程时间Fmax的计算
生产与运作管理第八章制造业作业计划与控制
02
综合作业计划和专项作业计划。
按制定方式
03
指令性作业计划和指导性作业计划。
02
制造业作业计划方法
甘特图法
总结词
甘特图法是一种直观的图形表示方法,用于表示项目的进度计划和时间安排。
详细描述
甘特图法通过绘制条形图来代表各个任务或活动,并使用箭头表示任务之间的逻辑关系和时间顺序。 甘特图法可以清晰地展示项目的整体进度和各个任务的依赖关系,有助于项目团队更好地协同工作。
成本分析与优化
通过对作业成本的深入分析,找出成本节约的空间,优化作业过程,降低生产 成本。
04
制造业作业计划与控制案例 分析
案例一:某汽车制造企业的作业计划与控制
总结词
高效协同、精细化控制
详细描述
该汽车制造企业采用先进的生产计划和控制 方法,各部门之间高效协同,实现了精细化 的生产流程控制。通过实时监控生产数据, 及时调整生产计划,确保按时交付高质量产 品。
案例二
总结词
快速响应、灵活性
详细描述
该电子产品制造企业注重快速响应市场需求 ,采用灵活的生产计划和控制方式。通过建 立敏捷的生产调度系统,及时调整生产计划 ,快速适应市场变化,提高生产效率和产品
质量。
案例三:某机械制造企业的作业计划与控制
要点一
总结词
要点二
详细描述
标准化、模块化生产
该机械制造企业采用标准化的生产计划和控制流程,通过 模块化生产方式提高生产效率。通过制定标准作业指导书 ,规范生产操作,确保产品质量稳定可靠。同时,采用自 动化设备减轻工人劳动强度,提高生产效率。
质量检验
对作业过程进行质量检验,及时发现并处理质量问题, 防止不合格品流入下一环节。
生产与运作管理第8讲生产作业计划制定
生产与运作管理第8讲生产作业计划制定生产作业计划制定是生产与运作管理中的重要环节,它涉及到资源的有效配置,生产计划的合理安排以及生产效率的提高。
本文将从生产作业计划制定的定义、目的和关键要素、制定流程和应注意事项等方面进行详细介绍。
一、生产作业计划制定的定义和目的生产作业计划制定是指根据市场需求、原材料供应、生产能力等因素,通过合理安排生产活动的时间、顺序和数量,制定出一份可行的计划,以达到提高生产效率、降低成本、提高客户满意度的目标。
生产作业计划制定的目的主要有以下几个方面:1.实现生产与市场需求的有效衔接:通过制定合理的生产作业计划,能够根据市场需求来安排生产活动,以达到及时交付产品的目标,避免因产能过剩或不足而导致的损失。
2.合理配置资源:通过精确的生产作业计划制定,能够科学、有效地配置各类资源,如人力、设备、原材料等,减少资源的浪费,提高资源利用率。
3.降低生产成本:通过优化生产作业计划,能够减少生产过程中的浪费,降低生产成本。
4.提高生产效率:通过合理安排生产活动的时间和顺序,可以减少生产过程中的闲置时间,提高生产效率。
5.提高客户满意度:根据客户需求制定合理的生产作业计划,能够及时交付产品,提高客户满意度,增强客户忠诚度。
二、生产作业计划制定的关键要素生产作业计划制定的关键要素主要包括市场需求、资源配置、时间安排和生产数量。
1.市场需求:生产作业计划制定的首要依据是市场需求。
只有根据市场需求来安排生产活动,才能满足客户的需求,实现生产与市场的有效衔接。
2.资源配置:资源配置是生产作业计划制定中的重要环节。
合理配置资源可以降低成本,提高生产效率。
资源包括人力、设备、原材料等,根据生产需求来合理配置资源是制定生产作业计划的重要要素。
3.时间安排:时间安排是生产作业计划制定中的关键要素之一、合理安排生产活动的时间可以避免闲置时间,提高生产效率。
时间安排应充分考虑生产环节的流程及其所需时间,并与市场需求相协调。
- 1、下载文档前请自行甄别文档内容的完整性,平台不提供额外的编辑、内容补充、找答案等附加服务。
- 2、"仅部分预览"的文档,不可在线预览部分如存在完整性等问题,可反馈申请退款(可完整预览的文档不适用该条件!)。
- 3、如文档侵犯您的权益,请联系客服反馈,我们会尽快为您处理(人工客服工作时间:9:00-18:30)。
设备2 8 2 4 6 3
作业时间最短的作业,出 现在设备1的排在开头,出 现在设备2的排在最尾。
剩余的作业时间最短的作业, 出现在设备1的从前往后排,出 现在设备2的从后往前排。
C
A
D
E
B
3、n项作业的n机调度
假设一个计划人员有5项作业,可以在5台机器上完成, (n=5)。下表中显示的是完成每个机器--作业组合所需要 的成本。计划人员想要设计一种成本最小化的指派。( 一共存在5!,也就是120种可能的指派方法。)
首先,计算各车间10月份的出产、投入累计号数,并进 行修正。
M装入=M装出+T装入N装=(160+10×2)号=180号 M机出=M装出+T机出N装=(160+20×2)号=200号 M机入=M装出+T机入N装=(160+50×2)号=260号 修正:M机=260/50]×50号=250号(与M机入比较) 其次,计算装配车间10月份的任务量。 出产任务量=(160-100)件=60件=2批 投入任务量=(180-120)件=60件=2批
法,也不能采用累计编号法。 各种产品的生产任新完全取决于货的数量,不需要再进行
计算,解决的问题是产品在各生产单位出产和投人时间能 够相互衔接起来,保证成品的交货期。
应用生产周期法编制生产作业计划的步是
首先,编制各项订货产品的投入出产综合进度计划表。 其次,在综合进度计划中摘录出属于每个生产单位的当
批量和间隔期 生产周期 生产提前期
在制品定额
一、批量和间隔期
• 批量是指一次投入(或出产)生产同种制品(产 品或零部件)的数量。
• 生产间隔期又叫生产重复期,是前后两批同种制 品投入或产出的间隔时间。
批量=生产间隔期×平均日产量
批量与生产间隔期有着密切的关系。在产品生产任务 确定以后,平均日产量不变时,批量大,生产间隔期 就会相应延长;反之,批量小,生产间隔期相应缩短。
入量,按照与批量相等或成整数倍的关系,对投入量与 出产量进行修正。
例8-1 某企业成批生产一种产品,在10月初已累计投入 120号,累计出产100号。根据生产计划的要求,10月份 装配车间累计出产达到160号,平均日产量2台,装配生 产周期为10天,装配车间的批量是30件。装配车间的前 一车间是机加工车间,机加工车间出产提前期为20天, 投入提前期为50天,机加工车间的批量是50套。试计算 机加工车间的投入、出产累计号及装配车间10月份的计 划投入、出产任务量。
1、标准计划法
标准计划法适用于大量生产。 通过把所有的各种制品的投入及出产顺序、期限和数量,
以及各个工作地上加工的不同制品的次序、期限和数量 全部制成标准,并固定下来,就是标准计划法,也就是 标准化了的生产作业计划。 若下达的作业计划采用的计划单位是零件,则对其略加 修改就可以作为生产单位内部的作业计划,不必再作计 算;若采用的计划单位是产品或部件,则首先要分解, 然后再以零件为单位将任务分配到小组。
8.2 生产作业计划
一、生产作业计划编制方法
• 在制品定额法:适用于流水生产或大量生产的作 业计划编制方法。
• 提前期法:适用于成批轮番生产的企业。 • 生产周期法:适用于根据订单组织生产的单件小
批生产企业。
1、在制品定额法
• 基本原则:按反工艺顺序,从后面向前环环相扣进行计 算。
具体计算公式: Q出=Q后投+M销+(Z末库-Z初库) Q投=Q后出+M废+(Z末定-Z初定)
《生产运作与管理》课件(8)
(张 群)
第8章 作业计划与控制
【2018-2019学年第2学期】
第8章 作业计划与控制
8.1 期量标准 8.2 生产作业计划 8.3 作业排序与服务排队 8.4 生产控制
8.1 期量标准
期量标准,又称作业计划标准,是指为加工对象 (零件、部件、产品等)在生产期限和生产数量 上所规定的标准数据。
2、定期排序法
在成批生产中,每一个工作地和每一个工人要轮番生产 多种零部件,轮番执行多种工序。为了使各道工序能够 相互衔接地进行,使机器设备能够有充分的负荷,就必 须安排零部件工序进度和机床负荷进度计划。因此,工 件加工的排序问题就成为成批生产作业计划的难点,定 期排序法就应运而生。
关于作业排序,下一节将详细介绍。
8.3 作业排序
一、作业排序
排序(Sequencing)是决定在某些机器或者某些工作中心 上先开始哪个作业的过程。
排序不等于作业计划( Scheduling),排序确定各个工件在 设备上加工的先后顺序,而作业计划不仅包括确定工件的 加工顺序,还包括确定机器加工每个工件的开始时间和完 成时间。在排序的基础上再给定每一个工件的加工开始和 结束时间,这样就构成一个完整的作业计划。
排序结果 作业加工时间ti 交货期di 完工时间Ci 拖期量Di 最大拖期量 平均流程时间
按SOT规则的排序
J3
J1
J4
J5
J2
1
2
3
6
7
8
25
9
10
23
1
3
6
12 19
0
0
0
2
0
Dmax=2
F 1(1 3 6 12 19) 8.2
5
按EDD规则的排序
J3
J4
J5
J2
J1
1
3
6
7
2
8
对其作业加工优先级进行排序。
作业编号 作业加工时间ti
交货期di
J1 J2 J3 J4 J5 2 713 6 25 23 8 9 10
解析: 按照上述的SOT规则,作业加工顺序为J3-- J1--J4-J5-- J2,平均流程时间为最小,但J5将延期交货,
排序结果 作业加工时间ti 交货期di 完工时间Ci 拖期量Di 最大拖期量 平均流程时间
大量生产中在制品定额
流水线内在制品占用量
流水线间在制品占用量
工艺占用量
周转占用量
运输占用量
运输占用量
周转占用量
保险占用量
保险占用量
成批生产中在制品
车间内在制品
批量
生产周期 生产间隔
库存在制品
流动在制品
保险在制吕
第8章 作业计划与控制
8.1 期量标准 8.2 生产作业计划 8.3 作业排序与服务排队 8.4 生产控制
二、生产周期
产品的生产周期是从原材料投入生产起,一直到 成品出产为止的全部日历时间。
产品的生产周期由各零部件生产周期组成,包括 零件的毛坯生产周期,机加工生产周期和装配生产 周期,以及各工艺阶段之间的保险期时间之和
毛坯生产 周期
保 险 期
机加工生 保 产周期 险
期
部装生产 周期
保 险 期
总装生产 周期
,是指作业在整个流程中的时间; (3)在制品库存量(WP)最小; (4)机器或者人员空闲时间最短。
(三)作业排序方法 n个作业的单机排序(n/1); n个作业的双机排序(n/2); n个作业的(n/m)多机排序。
1、n个作业的单机排序 有5个作业在单台设备上加工,请按下表所给条件
3、日常分配法
该法适用于单件小批量生产。 在一些生产不太稳定的单件小批量生产单位,由于变化
因素较多,难以预先作好长时间的安排,计划员就要根 据生产任务的要求和各种设备的实际负荷情况,每天给 工作地安排生产任务。
第8章 作业计划与控制
8.1 期量标准 8.2 生产作业计划 8.3 作业排序与服务排队 8.4 生产控制
3)由于同一台产品的所有零件都属于同一个累计编号, 所以,只要每个生产环节都能出产到计划规定的累计号数, 就能有效地保证零件的成套性。
3、生产周期法
生产法是依据各项货的变货目期和每类产品的生产周期 标准,来规定各生产单位入由产任的方法。
这种方法适用于根据订单组织生产的单件小批生产企业。 持点是产量少:重复性生产少,既不能采用在制品定额
作业排序和作业计划的实质是要解决如何按照时间的先后 ,是将有限的人力、物力资源分配给不同的任务,使预定 的目标最优化。
(一)作业排序的优先原则
作业排序优先级规则:FCFS、SPT、EDD、STR、STR/OP、 CR、QR、LCFS
最短作业时间( Shortest Processing Time,SPT)规则。 这一规则是指首先加工所需时间最短的作业,然后是第二 短的,依次类推。此规则也称为SOT( Shortest Operating Time)。
车间出产提前期=后车间投入提前期+保险期
各工艺阶段的批量不同
车间投入提前期=本车间出产提前期+本车间生产 周期
车间出产提前期=后车间投入提前期+(本车间生 产间隔-后车间生产间隔)+保险期
四、在制品定额
在制品定额是指在一定的技术组织条件下,各生 产环节上为了保证生产衔接所必须的、最低限度 的在制品储备量。
(1)计算产品在各车间计划期末应达到的累计出产和投入 的号数。
M出= M后出+T出 N后 M投=M后出 + T投N后 (2)计算各生产单位计划期内应完成的出产量和投入量。 出产任务量=期末出产累计号数-期初已出产累计号数 投入任务量=期末投入累计号数-期初已投入累计号数 (3)如果严格按照批量进行生产,则计算出的出产量和投
最早交货期( Earliest Due Date,EDD)规则。这一规则 是指将交货期最早的作业优先安排,而交货期要求晚一些 作业则排到后面加工。交货期是指整个作业的交货期。
(二)作业排序方案的评价标准
(1)满足顾客交货日期或者下游工序的交货日期。 (2)流程时间最短。流程时间也称为产出周期或产出时间