冲压模具开发流程
冲压模具设计全套步骤和流程

冲压模具设计全套步骤和流程1.零件设计:根据产品的功能要求和外观要求,进行零件的设计。
确定零件的几何形状、尺寸和所需的表面质量等。
2.材料选择:根据零件的要求和产品的使用环境,选择合适的材料。
考虑材料的强度、塑性和可加工性等因素。
3.模具结构设计:根据零件的几何形状和加工要求,设计模具的结构。
包括模具的底座、上模、下模、模具导向装置、顶针等部分。
4.模具零件设计:根据模具结构设计的要求,对模具的各个零部件进行设计。
包括模具的滑块、顶出装置、顶出销等。
5.模具总成设计:将各个模具零件组装成一个整体。
进行模具总成的设计,确定各个模具零件的安装位置、尺寸等。
6.模具加工工艺设计:根据模具结构和零件的加工要求,设计模具的加工工艺。
包括模具的加工工艺路线、加工顺序、机床设备等。
7.模具调试和试产:根据模具的设计和加工工艺,进行模具的组装和调试。
包括模具的调试、调整、测试以及初次试产。
根据试产结果,对模具进行优化和改进。
8.模具使用和维护:对模具进行使用和维护。
包括模具的防护、清洁、润滑和定期维护等。
9.模具性能评价:对模具进行性能评价。
包括模具的使用寿命、生产效率、加工精度等方面的评价。
10.模具改进和更新:根据使用中的问题和需求,对模具进行改进和更新。
包括模具的结构改进、材料选择和加工工艺的优化等。
以上是冲压模具设计的全套步骤和流程。
在进行设计的过程中,需要考虑零件的功能要求、材料的选择、模具的结构设计、加工工艺的确定等因素。
通过设计和优化,能够获得满足产品要求的冲压模具,提高生产效率和产品质量。
冲压模具加工流程

冲压模具加工流程冲压模具加工是一种常用的金属加工方法,用于制造各种形状的金属件。
冲压模具加工流程包括模具设计、模具制造、冲压工艺、模具调试和冲压生产等多个环节。
一、模具设计模具设计是冲压模具加工流程的第一步。
在模具设计中,需要根据产品的要求和规格,确定模具的结构、尺寸和工作原理。
模具设计要考虑到产品的形状、尺寸、材料和工艺要求,确保模具能够满足产品的加工需求。
二、模具制造模具制造是冲压模具加工流程的关键环节。
在模具制造中,需要根据模具设计图纸进行材料选择、零件加工和组装。
模具制造需要高精度的加工设备和技术,确保模具的尺寸和结构的精度要求。
三、冲压工艺冲压工艺是冲压模具加工流程的核心环节。
在冲压工艺中,需要确定冲头和模具的配合关系、冲头的冲程和冲次、冲压速度和压力等参数。
冲压工艺要考虑到产品的形状、材料和规格要求,确保产品能够满足使用要求。
四、模具调试模具调试是冲压模具加工流程的重要环节。
在模具调试中,需要对模具进行安装、调整和试模。
模具调试需要根据产品的加工要求,对冲压工艺进行优化和调整,确保产品的质量和生产效率。
五、冲压生产冲压生产是冲压模具加工流程的最后一步。
在冲压生产中,需要对模具进行定期的维护和保养,确保模具的使用寿命和加工质量。
冲压生产需要根据产品的需求,进行大批量的冲压加工,提高生产效率和产品质量。
冲压模具加工流程的每个环节都非常重要,任何一个环节的差错都可能导致产品质量的下降和生产效率的降低。
因此,冲压模具加工需要高度的技术和经验,以确保产品的质量和工艺要求的满足。
在冲压模具加工流程中,模具设计和制造是关键的环节,决定了产品的形状和尺寸的精度要求。
冲压工艺和模具调试是产品质量的保证,需要根据产品的加工要求进行调整和优化。
冲压生产是冲压模具加工流程的最终目标,需要高效的生产设备和工艺流程,确保产品的质量和生产效率。
冲压模具加工流程是一项复杂而精密的工艺,需要严格的控制和管理。
只有通过科学的设计、精密的制造、合理的工艺和高效的生产,才能确保冲压产品的质量和工艺要求的满足。
五金冲压模具模具设计开发控制程序

五金冲压模具模具设计开发控制程序首先,在模具设计开发过程中,要进行充分的前期准备工作。
这包括对产品的功能需求进行分析和确定,以及对模具的使用环境和条件进行了解。
通过这些准备工作,可以为后续的模具设计和开发提供指导和依据。
其次,在模具设计阶段,需要制定相应的设计准则和标准。
这些标准可以包括模具的使用寿命、制造成本、制造周期等要求。
在设计时要充分考虑到各种因素的影响,如模具的结构设计、材料选择、工艺要求等。
然后,在模具制造阶段,需要建立严格的制造管理程序。
这包括对材料采购、工艺过程、设备使用等方面的管理。
在制造过程中,需要进行严格的质量控制,确保模具的加工质量和尺寸精度符合设计要求。
在模具制造完成后,还需要进行模具试模和调试。
通过试模和调试,可以验证模具的设计和制造是否满足产品的要求,发现和解决可能存在的问题。
最后,在模具使用过程中,需要建立完善的维护和保养程序。
对于长期使用的模具,要定期进行维护,保证其正常使用。
在使用过程中,还要及时记录和反馈模具的使用情况,以便对模具进行优化和改进。
综上所述,五金冲压模具模具设计开发控制程序是一个较为复杂和繁琐的过程,需要从前期准备、设计、制造到使用的各个环节都进行严格的控制和管理。
只有这样,才能保证模具的质量和效率,提高生产效益。
冲压模具的开发步骤全过程

冲压模具的开发步骤全过程日期:2012-6-4 10:09:35 点击:次冲压模具的开发步骤全过程冲压模具-在冲床上,对金属或非金属板料进行分离或成型加工的模具:称为冲压模具。
冲压--是在室温下,利用压力机上的模具对材料施加压力,使其产生分离或塑性变形,从而获得所需零件的一种压力加工方法。
一套完整的冲压模具开发全过程,首先应该是客户把产品图发给冲压模具设计部门主管,然后将冲压模具产品图交给设计人员出图备料。
把模具需要的各个板子先买回来,粗加工让位、模板厚度研磨到一定的尺寸,一般是两面共留50条的余量,粗加工好了以后,送去热处理。
同时,设计部门人员开研讨会制定该产品每一步工序,排出料带图。
一个产品不可能只通过一个工序就能生产出来,还必须与其它工序配合,才能生产出合格的产品。
产品工序图确定完毕了以后,设计人员开始设计模具。
等设计把整个模具的所有零件画好出图了以后,模具就可以正式开始加工了,首先是模板研磨到正确的尺寸,然后放电、放穿线孔,再线切割、割入块孔、刀口、落料等,再送到铣床或CNC 加工沉头、让位等,最后由品保检测,不合格则退回责任部门再加工,合格了以后就可以送到仓库入库。
最后由钳工从仓库领走,开始组立前的准备工作,如倒角、去处毛刺、铁锈、确认尺寸、检查各个地方是否加工到位、是否缺孔少孔、螺丝牙是否有漏掉等,模具零件到了就可以暂时先开始组立模具了,到一点装一点,等模具零件到齐了以后,模具差不多就装好了,比零件全部都到齐了才开始装节省了许多时间。
模具组立完毕,开始试模、调试模具,直到模具可以生产出尺寸精度、外观质量复合要求的产品,然后送给客户签样品,客户确认好了,这一套模具的所有工作才算正式完成,就等上机台生产。
以后就是修模、保养模具了。
模具没事,钳工作业人员就没事。
做钳工这一行比较操心,还不知道模具什么时候坏,只要坏了马上就要去修,修的次数多了,就比较烦人。
当然,如果你模具装的好,该做的地方都做到位了,模具也没那么出问题。
冲压模具设计全套步骤和流程总算是弄明白了

冲压模具设计全套步骤和流程总算是弄明白了第一步:需求分析在冲压模具设计之前,首先需要对产品的需求进行分析。
包括确定产品的尺寸、形状、材料以及制造工艺要求等。
这是整个设计过程的基础,只有明确产品需求才能进行后续的设计工作。
第二步:模具结构设计在需求分析的基础上,开始进行冲压模具的结构设计。
包括模具的类型选择、结构设计、模板选择等。
设计师需要考虑到尽可能减少模具结构的复杂度,提高模具的稳定性和可靠性。
第三步:模具工艺设计在模具结构设计的基础上,进行模具的工艺设计。
包括冲床的选择、计算冲床的力量和速度等参数,并选择适当的冲床模型。
还需要考虑到在模具加工过程中可能出现的各种变形和误差,确定模具的装配方式和位置。
第四步:模具零部件设计在模具工艺设计的基础上,开始进行模具零部件的设计。
包括上、下模板、导向柱、导轨、顶针等零部件的设计。
设计师需要考虑到模具的可靠性和稳定性,选择合适的材料和标准件。
第五步:模具装配设计将设计好的模具零部件进行装配设计。
确定零部件之间的连接方式和位置,确保模具在使用过程中的精度和稳定性。
第六步:模具试制和调试完成模具的设计之后,进行模具的试制和调试。
对模具进行组装、调试和测试,发现并解决可能存在的问题和缺陷。
确保模具可以正常运转,并满足产品的要求。
第七步:模具使用和维护完成模具的试制和调试之后,模具将被交付给生产部门进行使用。
在使用过程中,定期对模具进行维护和保养,及时修复或更换损坏的零部件。
确保模具的使用寿命和稳定性。
总结:冲压模具设计的全套步骤和流程包括需求分析、模具结构设计、模具工艺设计、模具零部件设计、模具装配设计、模具试制和调试以及模具使用和维护。
通过严谨的设计和严格的质量控制,可以确保冲压模具设计的准确性和可靠性,提高产品的质量和生产效率。
冲压模具生产工艺流程
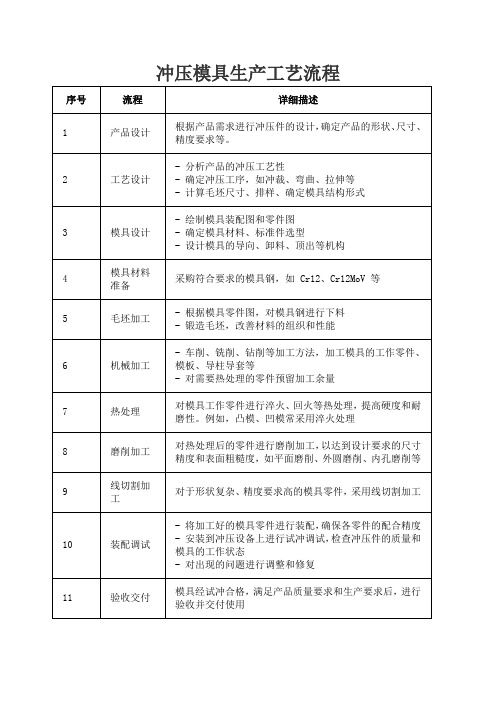
11
验收交付
模具经试冲合格,满足产品质量要求和生产要求后,进行验收并交付使用
4
模具材料准备
采购符合要求的模具钢,如 Cr12、Cr12MoV 等
5
毛坯加工
- 根据模具零件图,对模具钢进行下料
- 锻造毛坯,改善材料的组织和性能
6机械Leabharlann 工- 车削、铣削、钻削等加工方法,加工模具的工作零件、模板、导柱导套等
- 对需要热处理的零件预留加工余量
7
热处理
对模具工作零件进行淬火、回火等热处理,提高硬度和耐磨性。例如,凸模、凹模常采用淬火处理
冲压模具生产工艺流程
序号
流程
详细描述
1
产品设计
根据产品需求进行冲压件的设计,确定产品的形状、尺寸、精度要求等。
2
工艺设计
- 分析产品的冲压工艺性
- 确定冲压工序,如冲裁、弯曲、拉伸等
- 计算毛坯尺寸、排样、确定模具结构形式
3
模具设计
- 绘制模具装配图和零件图
- 确定模具材料、标准件选型
- 设计模具的导向、卸料、顶出等机构
8
磨削加工
对热处理后的零件进行磨削加工,以达到设计要求的尺寸精度和表面粗糙度,如平面磨削、外圆磨削、内孔磨削等
9
线切割加工
对于形状复杂、精度要求高的模具零件,采用线切割加工
10
装配调试
- 将加工好的模具零件进行装配,确保各零件的配合精度
- 安装到冲压设备上进行试冲调试,检查冲压件的质量和模具的工作状态
冲压模具设计的一般流程
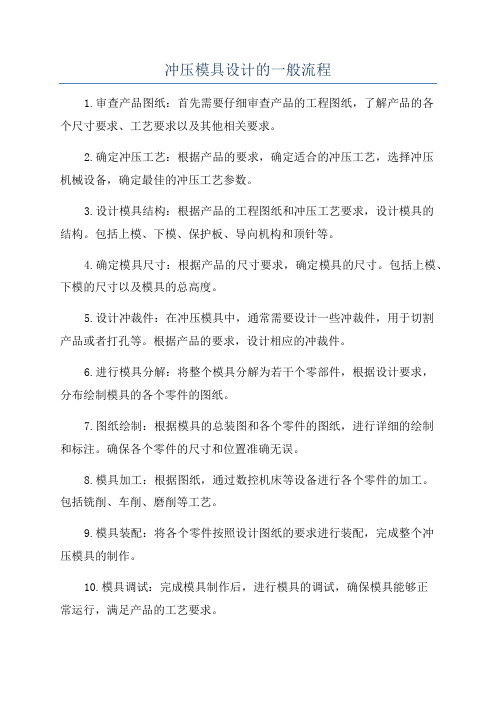
冲压模具设计的一般流程
1.审查产品图纸:首先需要仔细审查产品的工程图纸,了解产品的各
个尺寸要求、工艺要求以及其他相关要求。
2.确定冲压工艺:根据产品的要求,确定适合的冲压工艺,选择冲压
机械设备,确定最佳的冲压工艺参数。
3.设计模具结构:根据产品的工程图纸和冲压工艺要求,设计模具的
结构。
包括上模、下模、保护板、导向机构和顶针等。
4.确定模具尺寸:根据产品的尺寸要求,确定模具的尺寸。
包括上模、下模的尺寸以及模具的总高度。
5.设计冲裁件:在冲压模具中,通常需要设计一些冲裁件,用于切割
产品或者打孔等。
根据产品的要求,设计相应的冲裁件。
6.进行模具分解:将整个模具分解为若干个零部件,根据设计要求,
分布绘制模具的各个零件的图纸。
7.图纸绘制:根据模具的总装图和各个零件的图纸,进行详细的绘制
和标注。
确保各个零件的尺寸和位置准确无误。
8.模具加工:根据图纸,通过数控机床等设备进行各个零件的加工。
包括铣削、车削、磨削等工艺。
9.模具装配:将各个零件按照设计图纸的要求进行装配,完成整个冲
压模具的制作。
10.模具调试:完成模具制作后,进行模具的调试,确保模具能够正
常运行,满足产品的工艺要求。
11.产出产品:经过模具调试后,使用冲压机械设备进行批量生产,产出满足产品要求的冲压件。
12.模具维护和修理:冲压模具在使用过程中,需要进行定期的维护和修理,确保模具长时间稳定运行。
冲压模具设计全套步骤和流程总算是弄明白了

冲压模具设计全套步骤和流程总算是弄明白了第一步:了解产品需求第二步:确定冲压工艺在了解产品需求的基础上,确定适合的冲压工艺。
冲压工艺包括冲压方式、冲压压力、冲次、下模方式等,决定了模具的结构和材料的选择。
第三步:构思模具结构基于冲压工艺要求,开始构思模具的结构。
包括分模、上模、下模、导向、顶出、定位等,根据产品的形状和需求进行合理的布局。
第四步:选择材料根据模具的使用要求,选择合适的材料。
常见的模具材料有工具钢、硬质合金等,选择合适的材料有助于提高模具的寿命和稳定性。
第五步:设计模具零件根据模具的结构,开始设计模具的各个零件。
包括模座、模套、冲片、导柱、导套、顶出杆等,每个零件的设计都要考虑其相互之间的协调和可靠性。
第六步:组装模具完成各个零件的设计后,将其组装成完整的模具。
在组装时需要注意零件之间的配合尺寸和间隙,保证组装的准确性和稳定性。
第七步:试模调试完成模具的组装后,进行试模调试。
通过试模调试可以检验模具的设计是否准确,是否满足产品的要求,同时也可以发现并解决可能存在的问题。
第八步:验收模具经过试模调试后,进行对模具的验收。
验收包括模具寿命测试、产品检验、模具结构和配合尺寸的检查等,确保模具的性能和质量达到要求。
第九步:使用和维护通过验收后,模具可以投入使用。
在使用过程中,要定期进行维护和保养,及时处理模具的故障和损坏,延长模具的使用寿命。
以上就是冲压模具设计的全套步骤和流程。
冲压模具设计需要综合考虑产品的需求、冲压工艺和材料等因素,合理设计出高质量的模具,确保产品的质量和生产的效率。
- 1、下载文档前请自行甄别文档内容的完整性,平台不提供额外的编辑、内容补充、找答案等附加服务。
- 2、"仅部分预览"的文档,不可在线预览部分如存在完整性等问题,可反馈申请退款(可完整预览的文档不适用该条件!)。
- 3、如文档侵犯您的权益,请联系客服反馈,我们会尽快为您处理(人工客服工作时间:9:00-18:30)。
冲压模具开发流程
1.产品需求分析和设计:首先,对于需要冲压的零部件,需要进行需求分析并确定产品的设计要求。
根据产品的形状、尺寸以及数量要求,制定相应的设计方案。
2.模具设计:根据产品设计方案,进行模具的设计。
包括三维模型设计、结构设计、模具零部件设计等。
模具的设计要满足产品要求,并且考虑到材料的选择、加工工艺等因素。
3.模具制造:在完成模具设计后,需要进行模具的制造。
包括模具标准件的采购、非标准件的加工以及模具的组装等。
制造过程中需要进行严格的质量控制和检测,以确保模具的质量。
4.模具调试:在模具制造完成后,需要进行模具的调试。
包括模具零部件的配合检查、模具操作的检验、以及产品的抽样试模等。
通过调试,可以确保模具的正常运行,并达到产品设计要求。
5.试产和修正:在模具调试过程中,进行初步的试产。
通过试产可以发现模具存在的问题,并进行修正。
包括模具结构的改进、零部件的更换等。
通过多次试产和修正,最终达到满足产品质量要求的模具。
6.批量生产:在完成模具的调试和修正后,进行批量生产。
根据客户的需求,进行大批量的产品生产。
生产过程中需要进行质量控制和检测,以确保产品的质量稳定。
7.模具维护和改进:在模具的使用过程中,需要进行定期的维护和保养。
包括模具的清洁、零部件的更换等。
同时,根据客户反馈和产品要求的变化,进行模具的改进和升级。
总结起来,冲压模具开发流程包括产品需求分析和设计、模具设计、
模具制造、模具调试、试产和修正、批量生产以及模具维护和改进等环节。
在每个环节中,需要进行严格的质量控制和检测,以确保模具和产品的质量。
冲压模具开发流程的顺利进行,能够为企业提供优质的零部件,提高
生产效率和产品质量。