用热工艺 导热油
导热油介绍
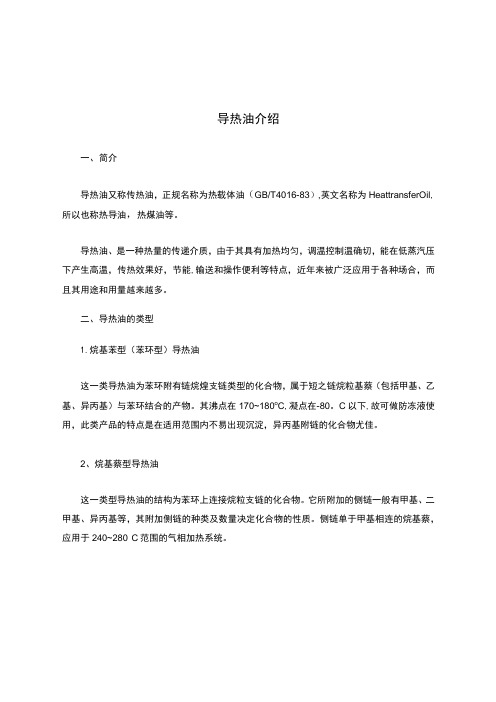
导热油介绍一、简介导热油又称传热油,正规名称为热载体油(GB/T4016-83),英文名称为HeattransferOil,所以也称热导油,热煤油等。
导热油、是一种热量的传递介质,由于其具有加热均匀,调温控制温确切,能在低蒸汽压下产生高温,传热效果好,节能,输送和操作便利等特点,近年来被广泛应用于各种场合,而且其用途和用量越来越多。
二、导热油的类型1.烷基苯型(苯环型)导热油这一类导热油为苯环附有链烷煌支链类型的化合物,属于短之链烷粒基蔡(包括甲基、乙基、异丙基)与苯环结合的产物。
其沸点在170~180o C,凝点在-80。
C以下,故可做防冻液使用,此类产品的特点是在适用范围内不易出现沉淀,异丙基附链的化合物尤佳。
2、烷基蔡型导热油这一类型导热油的结构为苯环上连接烷粒支链的化合物。
它所附加的侧链一般有甲基、二甲基、异丙基等,其附加侧链的种类及数量决定化合物的性质。
侧链单于甲基相连的烷基蔡,应用于240~280°C范围的气相加热系统。
3、烷基联苯型导热油这一类型的导热油为联苯基环上连接烷基支链一类的化合物。
它是由短链的烷基(乙基、异丙基)与联苯环相结合构成,烷基的种类和数量决定其性质。
烷麻基数量越多,其热稳定性越差。
在此类产品中,由异丙基的间位体、对位体(同分异构体)与联苯合成的导热油品质最好,其沸点>330°C,热稳定性亦好,是在300~340。
C范围内使用的理想产品。
4、联苯和联苯醛低熔混合物型导热油这一类型的导热油为联苯和联苯酸低熔混合物由26.5%的联苯和73.5%的联苯醛组成。
熔点为12。
(:,世界上最早使用的合成芳烧导热油是DoWtherm,其特点是热稳定性好,使用温度高(400℃)。
此类产品由于苯环上没有与烷峰基侧链连接,而在有机热载体中耐热性最正确。
这种凝点(12.3。
C)低熔混合物,在常温下,沸腾温度在256~258°C范围内使用比较经济。
这是由于两种物质的熔点均较高(联苯为<71。
导热油工艺流程

导热油工艺流程导热油工艺流程是指在工业生产中利用导热油传导热能的一项技术。
导热油是一种高温传热介质,具有较高的热传导率和热稳定性,能够满足工业生产过程中的高温传热需求。
以下是一份700字的导热油工艺流程介绍。
导热油工艺流程分为设备准备、导热油填充、循环运行和维护保养四个步骤。
首先,进行设备准备。
在进行导热油工艺之前,需要准备一系列的设备,包括导热油锅炉、导热油泵、加热器、膨胀罐、管道系统等。
确保设备的完好性和安全性,检查设备的压力和温度传感器是否正常工作,确保设备能够正常运行。
接下来,进行导热油填充。
将导热油加注到导热油锅炉中,并通过导热油泵将其泵入到系统中。
在填充过程中,需要保证导热油的温度和压力都处于设定范围内,以确保填充的导热油能够正常运行。
然后,进行循环运行。
将导热油从导热油锅炉通过管道输送到加热器或其他需要加热的设备中,使导热油在加热器中获得热能,并将其传递给被加热的物体或工艺流体。
导热油通过热对流的方式传输热量,在循环过程中将其传输到需要的地方,完成热能传递。
最后,进行维护保养。
导热油在运行一段时间后会出现老化和污染,需要定期进行维护保养。
维护包括导热油的定期更换,清洗导热油系统的管道和设备,检查导热油泵的工作状态等。
维护保养的目的是保证导热油系统的正常运行和安全性。
导热油工艺流程能够应用于许多工业领域,如化工、石油、塑料、橡胶等。
通过合理设计和运行导热油系统,可以实现高温传热的需求,提高生产效率,降低能源消耗。
同时,在导热油工艺流程中,需要加强运行的监控和安全措施,及时检测和排除可能出现的故障,确保生产过程的连续性和安全性。
总结起来,导热油工艺流程包括设备准备、导热油填充、循环运行和维护保养四个步骤。
通过合理操作和维护,可以确保导热油系统的正常运行,提高生产效率,降低能源消耗。
导热油工艺流程在工业生产中有着广泛的应用前景。
导热油工艺流程

导热油工艺流程
《导热油工艺流程》
导热油是一种高效的传热介质,在许多工业领域都有广泛的应用。
为了实现对导热油的生产和使用过程的高效管理,需要建立完善的工艺流程。
下面将介绍一种常用的导热油工艺流程:
1. 原料准备:首先需要准备好合适的原料,通常是通过精细提炼的石油产品。
原料的质量和纯度对最终产品的性能和稳定性有着重要的影响,因此这一步需要特别注意。
2. 加工操作:原料经过一系列的加工操作,包括脱气、脱硫、脱水等步骤,以保证导热油的纯净度和稳定性。
在加工操作过程中,需要控制好温度、压力和流速等参数,确保每一步都能够达到预期的效果。
3. 质量检测:对加工后的导热油进行质量检测,包括外观检测、化学成分分析、物理性能测试等。
只有通过了严格的质量检测的导热油才能够进入下一步的生产和使用环节。
4. 包装和储存:最后,经过质量检测合格的导热油会被进行包装,并储存在适当的条件下。
在包装和储存过程中,需要特别注意防止水分和杂质的侵入,以确保导热油的纯净度和稳定性。
总的来说,导热油的工艺流程是一个严格、复杂的过程,需要在每一个环节上都严格把关,确保最终产品的质量和性能能够
达到预期的标准。
只有这样,导热油才能在工业生产中发挥出其最大的效益和价值。
导热油使用注意事项

导热油使用注意事项
1.根据用热工艺的要求选择合适的导热油、油炉。
2.对于膨胀槽和低位槽,要正确、合理的进行设计,系统中尽量避免油不流
动的死角,确保导热油长期安全的运行。
3.导热油中严禁混入任何杂质。
4.在换新油时或第一次使用时管道必须要清洗干净,水、水锈等杂质要清洗
干净。
5.使用新导热油或导热油炉必须要严格脱水。
6.导热油炉使用时要先启动循环泵,运行正常后再点火,停炉时必须先停火,
循环泵继续运行到温度降到100℃左右才可以停泵。
7.对导热油油质进行定期检查,及时添加或更换新油。
8.时刻关注高位槽的油温。
9.严禁高温使用。
10.穿戴适当的个人防护装备,如耐高温手套、防护眼镜和防护服等。
导热油的生产工艺

导热油的生产工艺导热油的生产工艺1. 简介导热油是一种具有优异导热性能和稳定化学性质的热传导介质。
它广泛应用于工业生产中的高温传热领域,如化工、石油、制药等。
本文将介绍导热油的生产工艺。
2. 原料准备生产导热油所需的原料主要包括基础油和添加剂。
基础油通常选择具有良好热稳定性和氧化安定性的矿物油或合成油。
添加剂则根据导热油的使用环境和要求而定,常见的添加剂有抗氧化剂、抗腐蚀剂等。
3. 混合配方将基础油和添加剂按照一定比例混合,并加热至一定温度,使其充分混合均匀。
混合配方的关键在于保证添加剂的充分溶解和分散,以提高导热油的性能稳定性和寿命。
•比例控制:根据导热油的使用温度和要求,科学调配基础油和添加剂的比例,以确保导热油具备良好的导热性能和热稳定性。
•加热条件:加热基础油和添加剂的过程中,需要严格控制温度,避免过高温度导致添加剂变性或挥发。
常见的加热方式有电加热和蒸汽加热等。
4. 精炼处理混合配方后的导热油还需要进行精炼处理,以去除其中的杂质和不稳定成分。
•过滤:通过过滤器对导热油进行物理过滤,去除其中的悬浮固体颗粒和杂质。
•真空蒸馏:将导热油加热至一定温度,利用不同组分的沸点差异,通过真空蒸馏的方式分离出其中的挥发性成分和不稳定成分。
5. 包装与贮存经过精炼处理后的导热油需要进行包装和贮存,保证其品质和性能不受外界环境影响。
•包装方式:通常使用密封性好、耐腐蚀的容器进行包装,常见的包装方式有桶装、罐装等。
•贮存条件:导热油的贮存条件非常重要,应避免阳光直射、高温和潮湿环境。
同时,应定期检查导热油的质量,确保其在贮存期间的性能稳定。
结语导热油的生产工艺涉及原料准备、混合配方、精炼处理以及包装与贮存等环节。
每个环节的控制和操作都对最终产品的质量和性能产生影响。
只有严格遵守规程和要求,才能生产出优质的导热油产品,满足高温传热领域的需求。
6. 质量控制在导热油的生产工艺中,质量控制是至关重要的环节。
以下是常见的质量控制措施:•原料检验:在使用前,对基础油和添加剂进行严格的质量检验,确保其符合规定的标准和要求。
导热油使用手册
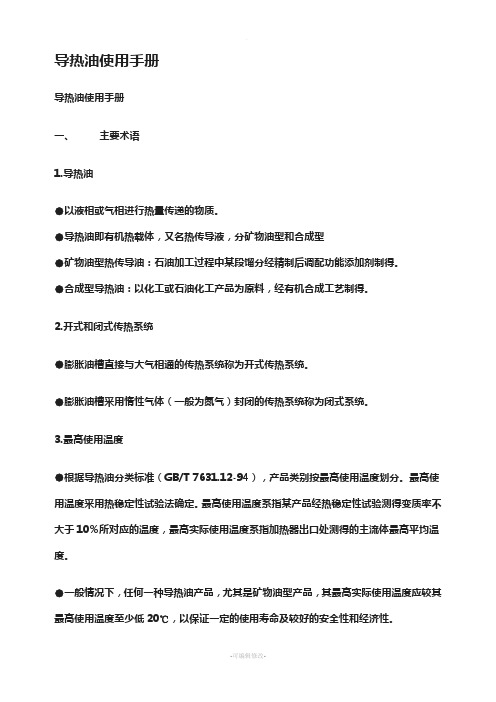
导热油使用手册导热油使用手册一、主要术语1.导热油●以液相或气相进行热量传递的物质。
●导热油即有机热载体,又名热传导液,分矿物油型和合成型●矿物油型热传导油:石油加工过程中某段馏分经精制后调配功能添加剂制得。
●合成型导热油:以化工或石油化工产品为原料,经有机合成工艺制得。
2.开式和闭式传热系统●膨胀油槽直接与大气相通的传热系统称为开式传热系统。
●膨胀油槽采用惰性气体(一般为氮气)封闭的传热系统称为闭式系统。
3.最高使用温度●根据导热油分类标准(GB/T 7631.12-94),产品类别按最高使用温度划分。
最高使用温度采用热稳定性试验法确定。
最高使用温度系指某产品经热稳定性试验测得变质率不大于10%所对应的温度,最高实际使用温度系指加热器出口处测得的主流体最高平均温度。
●一般情况下,任何一种导热油产品,尤其是矿物油型产品,其最高实际使用温度应较其最高使用温度至少低20℃,以保证一定的使用寿命及较好的安全性和经济性。
4.热稳定性●从试验角度讲,热稳定性是在规定的试验温度及时间条件下,导热油在隔绝空气状态下,因受热作用(热裂解和热聚合)而表现出的稳定性。
●对某一特定产品来说,其热稳定性由组成、纯度、精制深度、馏程范围等因素决定。
●热裂解反应,生成气体和低沸物。
●热聚合反应,生成高沸物和高分子粘稠状聚合物,最后形成沉渣。
●导热油在实际运行中,热裂解和热聚合反应会伴随始终,其组成无时无刻不在发生变化,是不可避免的,但其程度可以控制。
●热氧化反应,生成低分子或高分子的醇、醛、酮、酸等酸性组分,并进一步生成胶质、沥青质等粘稠物质,最后形成沉渣。
●热氧化是非正常情况引起的,一旦发生,会产生很坏的影响(加速热裂解和热聚合反应,酸性物质造成设备腐蚀和泄漏,粘度迅速增大,传热效率降低,造成过热和炉管结焦),但可以通过加入高温导热油复剂避免或延缓。
二、主要技术指标1. 热稳定性热稳定性是导热油区别于其他油品的重要使用性能,标准号为SH/T 0680-1999。
导热油加热系统工艺流程图
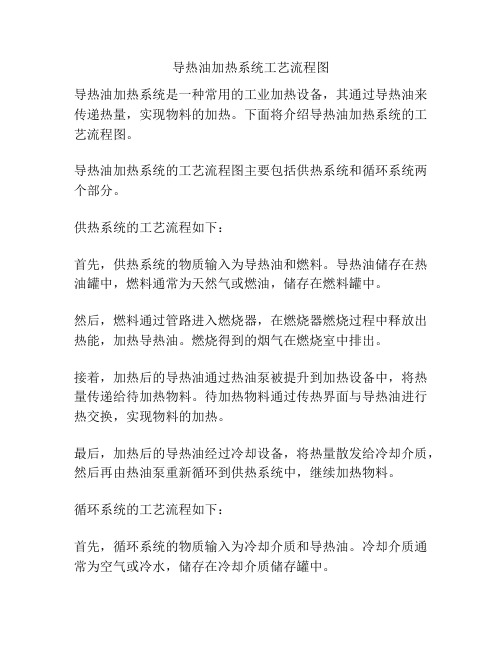
导热油加热系统工艺流程图
导热油加热系统是一种常用的工业加热设备,其通过导热油来传递热量,实现物料的加热。
下面将介绍导热油加热系统的工艺流程图。
导热油加热系统的工艺流程图主要包括供热系统和循环系统两个部分。
供热系统的工艺流程如下:
首先,供热系统的物质输入为导热油和燃料。
导热油储存在热油罐中,燃料通常为天然气或燃油,储存在燃料罐中。
然后,燃料通过管路进入燃烧器,在燃烧器燃烧过程中释放出热能,加热导热油。
燃烧得到的烟气在燃烧室中排出。
接着,加热后的导热油通过热油泵被提升到加热设备中,将热量传递给待加热物料。
待加热物料通过传热界面与导热油进行热交换,实现物料的加热。
最后,加热后的导热油经过冷却设备,将热量散发给冷却介质,然后再由热油泵重新循环到供热系统中,继续加热物料。
循环系统的工艺流程如下:
首先,循环系统的物质输入为冷却介质和导热油。
冷却介质通常为空气或冷水,储存在冷却介质储存罐中。
然后,冷却介质通过冷却介质泵被提升到冷却设备中,将热量传递给导热油。
导热油通过冷却界面与冷却介质进行热交换,散发热量,降低温度。
接着,冷却后的导热油经过过滤设备,去除其中的杂质和污染物,确保导热油的质量。
最后,冷却后的导热油经过热油泵重新循环到供热系统中,继续加热物料。
以上就是导热油加热系统的工艺流程图。
通过导热油和燃料的配合,实现对物料的加热。
循环系统中的冷却介质则起到了散热的作用,维持导热油的温度。
导热油加热系统能够快速、精确地实现物料的加热,广泛应用于化工、制药、食品等行业。
导热油使用规范.

导热油使用规范第一章热传导液的运行管理第一节热传导液的选择根据SH/T 0677-1999 热传导液标准及实际使用温度选择适宜牌号的产品,产品中需加入适宜经石油化工科学研究院评定的优质抗氧和抗垢复合添加剂。
(实际使用中,加热器出口处测得的主流体平均温度应比油品的最高使用温度至少低20℃)。
第二节开车调试一、开车前的准备1、检查各单位设备及工艺管道安装是否完善。
2、系统运转设备、传动机构按要求加入润滑油或润滑脂。
3、运转设备运行前必须盘车,确定无机械故障。
4、将各运转单元单机试运转,检查设备运转情况,声音是否正常。
5、炉排调速安全离合器的压力弹簧松紧调节适当。
6、调节好系统各个阀门,为注油试车做好准备。
7、油系统用干燥空气进行吹扫,彻底将水分吹除干净。
8、检查电器及控制仪表是否装妥。
9、准备好氮气5瓶。
(指闭式加热系统)二、冷态调试1、开启注油泵向高位槽注油,直至高位槽低液位不报警,关闭注油泵,启动热油循环泵开始冷油循环,打开高位槽放空阀,经常开启管道放空阀,不断排出空气,及时补充高位槽内热传导液,保持低液位。
2、冷油循环时间不少于4小时,观察油循环泵进出口压力及系统压力表、温度表等仪表显示是否正常,直至压差波动转向平稳,检查系统内无泄漏和阻塞现象,清理过滤器2-3次。
三、热态调试1、点火:用不带铁钉等金属的木柴,均匀铺在炉排上引燃,并控制燃烧量,使油循环泵保持不抽空,油升温速率控制在10℃/ h左右。
2、上煤:用手工向炉内均匀铺撒干煤,逐步过渡用煤斗上煤,从观火门观察炉内燃烧情况。
确保炉火燃烧平稳、均匀,无断火现象。
3、烘炉:按升温曲线要求进行,油温控制在100℃以下,注视循环油泵进出口压差波动情况,如出现循环油泵吸空,可停运2-3分钟,再重新启动,观察炉膛烘干情况。
以上三点指燃煤锅炉(新炉),燃油锅炉可参照第3点〈烘炉〉,要严格控制进油量与时渐进按升温曲线控制热油温度。
4、脱水排气:按升温曲线进行,油温控制在120℃—150℃,在此期间重点除去油中水分和低挥发成分,随着温度升高至200℃以上时,系统法兰连接处可进行热紧固,热油泵吸空可停运0.5-1分钟,再重新启动。
- 1、下载文档前请自行甄别文档内容的完整性,平台不提供额外的编辑、内容补充、找答案等附加服务。
- 2、"仅部分预览"的文档,不可在线预览部分如存在完整性等问题,可反馈申请退款(可完整预览的文档不适用该条件!)。
- 3、如文档侵犯您的权益,请联系客服反馈,我们会尽快为您处理(人工客服工作时间:9:00-18:30)。
一、合成革
图1-1湿法基布生产工艺流程图
图1-2干法移膜生产工艺流程图
用热情况:DMF溶剂回收、合成革干燥属于耗能较高的工段,有机溶剂DMF的回收采用蒸馏塔,采用负压蒸煮温度需要130-140℃,合成革湿法基布干燥温度高于160℃,基布贴膜后干燥温度130-140℃。
干法烘干温度为120-150℃。
二、染整
工艺流程:预定形→前处理→染色→皂洗、固色→后整理及成品定形。
预定形工艺条件:定形温度 180~185℃定形时间50~60 s
前处理工艺条件:精炼除油、精炼漂白,温度80℃。
染色:常规的活性染料染色以60~70℃中温,酸性染料最佳染色温
度98~100℃
固色:常规活性染料染纤维素纤维,其染色固色温度一般为中温即6 0℃,酸性染料染锦纶为100℃。
后整理及成品定形:温度160℃。
三、化工类产品
3.1合成树脂
合成树脂用热主要是反应用热,不同的树脂合成温度不同,现举如下两个树脂反应过程。
3.3.1醇酸树脂
图3-1 醇酸树脂生产工艺流程图
工艺温度:2h逐步升温至220℃,200-220℃保温2h,60到70℃过滤分装。
3.1.2丙烯酸树脂
图3-2 丙烯酸树脂生产工艺流程图
工艺温度:控制反应釜温度为138-142℃,过滤温度为60-70℃。
3.2油脂
主要用热过程为加热。
油脂精炼工艺流程:
脱胶碱炼:
毛油→毛油过滤器→计量流量计→板式加热器(75-80℃±)→刀式混和器→酸反应罐→输送泵→水冷却器(60-75℃±)→刀式混和器(变频调速)→中和反应罐(带搅拌)→输送泵→列管加热器→碟式离心机(85℃)
→板式加热器(90-92℃±)→离心混和器→碟式离心机(需95-100℃热水)→干燥器(-0.08Mpa)→至脱色工段
脱色:
碱炼油→输送泵→板式加热器(110-130℃)→白土混和罐(15-30min)→脱色塔(105-110℃、-0.092 Mpa、30-45 min)→脱色泵→叶片过滤机→脱色油罐→输送泵→袋式过滤器→棒式过滤器→至脱臭工段
脱酸脱臭:
脱色油→真空析气器(-0.092MPa±)→输送泵→列管换热器(140℃±)→列管换热器(-600Pa、190-220℃)→脱酸脱臭塔(-600Pa、240-280℃)→列管换热器(-600Pa、150℃±)→磁力泵→列管换热器→板式换热器(与毛油换热器)→板式水冷却器→袋式过滤器→棒式过滤器→成品油罐区
用热情况:在脱胶碱炼阶段采用蒸汽换热器换热,温度较低(75-80℃±)和90-92℃±两次换热,在脱色阶段需要换热器换热,温度为110-130℃,在脱色塔中利用饱和蒸汽蒸馏,温度为105-110℃。
在脱色阶段所需的蒸汽的温度较高,从140℃±升温到190-220℃再到脱酸脱臭塔240-280℃高温,再到换热管150℃,最后冷却至60℃以下。
3.3 染料
活性染料应用广泛,主要由母体染料和活性基组成。
活性染料分为两种制备工艺:
a.先缩合制备带活性基的偶合组分,再于重氮组分偶合得到染料
b.先重氮偶合得到染料再缩合制备活性组分
两者拥有相同的后处理操作过程:染料浆进喷雾干燥塔,去除水分,最终制得原染料。
用热情况:合成染料的反应过程所需温度降低,用热较大的是在后处理操作过程,在喷雾干燥塔中通常利用导热油或者蒸汽加热,浙江一染化活性厂的导热油温度为280℃。
四、食品
4.1饼干的生产
饼干的生产工艺:
原辅料配粉和面成型烘烤冷却包装成品用热温度:主要用热在烘烤步骤,设备为电烤炉,不同的饼干种类烘烤的温度不同,韧性饼干烘烤温度为200-240℃,时间3.5-5min,苏
打饼干200-280℃,分不同阶段,总时间 4.5-5.5min,酥性饼干210-250℃,时间6-7min。
五、导热油常用领域及过程装置
工业领域过程装置
橡塑工业热压、压延、挤压、硫化、人造皮革加工、薄膜加工精细化工医药、农药中间体、防老剂、表面活性剂、香料等合成油脂化工脂肪酸蒸馏、油脂分解、蒸馏、浓缩、硝化
化纤工业聚合反应、熔融纺纱、热固、纤维整理
造纸工业热熔融机、波纹板加工机、干燥机
木材加工复合板压制、干燥机
电器加工电线及电缆制造
能源工业废热回收、太阳能利用、反应堆取热
食品工业粮食干燥、食品烘烤
空调工业家庭暖房
化工及石油化工聚合、分解、蒸馏、浓缩、蒸发、熔融装置等
建筑及建材工业沥青融化、保温、石膏板烘干
纺织印染工业热熔染色、热定型、烘干装置。