延迟焦化装置工艺条件及影响因素研究
延迟焦化工艺详解及其安全注意事项
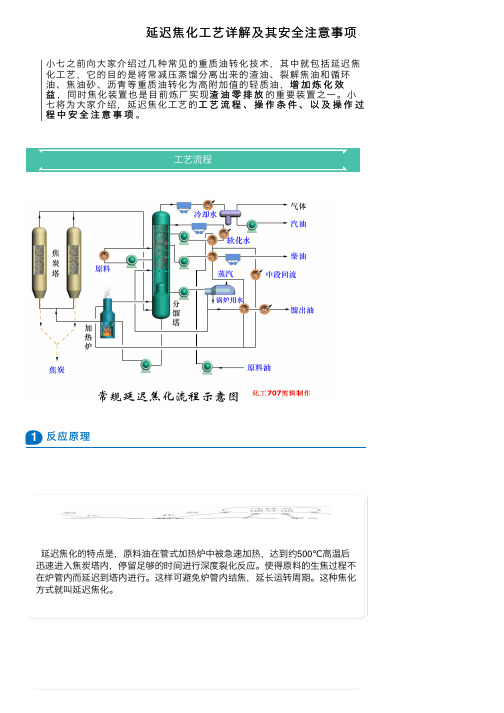
1延迟焦化⼯艺详解及其安全注意事项⼩七之前向⼤家介绍过⼏种常见的重质油转化技术,其中就包括延迟焦化⼯艺,它的⽬的是将常减压蒸馏分离出来的渣油、裂解焦油和循环油、焦油砂、沥青等重质油转化为⾼附加值的轻质油,增增加炼化效益,同时焦化装置也是⽬前炼⼚实现渣渣油零排放的重要装置之⼀。
⼩七将为⼤家介绍,延迟焦化⼯艺的⼯⼯艺流程、操作条件、以及操作过程中安全注意事项。
⼯艺流程反应原理延迟焦化的特点是,原料油在管式加热炉中被急速加热,达到约500℃⾼温后迅速进⼊焦炭塔内,停留⾜够的时间进⾏深度裂化反应。
使得原料的⽣焦过程不在炉管内⽽延迟到塔内进⾏。
这样可避免炉管内结焦,延长运转周期。
这种焦化⽅式就叫延迟焦化。
延迟焦化装置的⽣产⼯艺分焦化和除焦两部分,焦化为连续操作,除焦为间歇操作。
2由于⼯业装置⼀般设有两个或四个焦炭塔,所以整个⽣产过程仍为连续操作。
⼯艺描述原料经加热炉对流室预热管预热⾄350℃进⼊焦化分馏塔下部与来⾃焦炭塔顶的⾼温油⽓换热,可同时将轻质油蒸出。
换热后原料油温度约390~395℃,再与循环油⼀起泵⼊加热炉炉管,迅速加热到500℃再进⼊焦炭塔底。
为了防⽌炉管结焦,需向炉管内注⽔以加⼤流速。
渣油在焦炭塔内停留⾜够长时间以完成裂化、缩合反应,⽣成的焦炭留在焦炭塔内。
⾼温油⽓从塔顶通⼊分馏塔下部;经换热后分馏得到产品⽓、汽油、柴油等。
焦炭塔轮流使⽤。
操作条件影响焦化的主要因素有:原料性质、加热炉出⼝温度、反应压⼒。
加热炉出⼝温度:500℃左右;加热炉出⼝温度的变化直接影响到炉管内和焦炭塔内的反应深度,加热炉出⼝温度太⾼,反应速度和反应深度增⼤,⽓体、汽油和柴油的产率增⼤,蜡油的产率减⼩,焦炭产率也会由于所含挥发性组分的减⼩⽽降低 ,同时由于温度太⾼,会造成汽油、柴油继续裂解,结焦增多。
加热炉出⼝温度太低,则会造成反应不完全。
分馏塔底温度:375 ~395℃,过⾼易结焦。
分馏塔顶温度:100 ~110℃柴油输出线温度:275 ~285℃系统压⼒直接影响到焦炭塔的操作压⼒,⼀般来说,压⼒降低会使蜡油产率增⼤⽽使柴油产率降低。
影响延迟焦化开工周期的因素及对策

影响延迟焦化开工周期的因素及对策在原油逐渐重质化劣质化,轻质油品需求量不断上升,重油深度加工任务日益繁重的今天,延迟焦化装置在炼油生产中的地位显得日益重要,装置是否能长周期安全平稳运行,决定着炼油厂重油平衡任务和原油加工量的顺利完成。
在实际生产过程中,影响延迟焦化装置开工周期的主要因素关键部位的结焦、关键部位渗漏、关键设备发生故障、关键岗位发生事故,这些都会导致装置出现非计划停工,因而影响长周期运行。
全面分析影响因素,针对关键部位、制定专业措施,实施重点防护,将风险降低到最低,是实现装置长期运行的重要方面。
一、防止关键部位结焦1.防止加热炉炉管结焦影响加热炉炉管结焦的因素主要有原料性质、炉管壁温度、渣油在炉管内的流动状态等,减缓炉管结焦就要从这几方面考虑。
1.1适当调整循环比在渣油密度较大的情况下,增加循环比不仅可以降低辐射进料的沥青质含量,提高辐射进料的芳烃与沥青质比,改善原料性质,而且还可以提高辐射进料的临界分解温度,抑制沥青质和甲苯不溶物的生成,缩短辐射进料分解后在低温高压炉管范围内的流动距离和停留时间,有利于进一步减轻焦化炉管的结焦。
1.2保持合理的炉膛温度在装置正常生产过程中,要严格监控,保持合理的炉膛温度,出现紧急情况时要及时提高注水量,保证炉管温度不超标,同时还要严格控制火焰高度,保持火焰高度在炉膛高度的1/3左右,严禁火焰直接燃烧炉管,防止炉管壁温度太高。
2.减缓大油气线结焦焦炭塔大油气管线结焦是延迟焦化装置普遍存在的一个问题,解决大油气管线结焦是延长焦化装置开工周期,确保高负荷加工渣油的关键之一。
大油气管线结焦会导致管线压降过大,焦炭塔顶操作压力增大,甚至接近安全阀的定压值,严重影响了装置的正常运行,有时还会被迫停工清焦。
因此,解决大油气管线结焦是延长延迟焦化装置生产周期的一个关键问题。
大油气线结焦的影响因素主要有急冷油注入点位置、加热炉出口温度、冷焦吹汽量、泡沫层高度、生焦高度、焦炭塔塔顶温度、切塔时的平稳操作等。
研究延迟焦化装置长周期运行的制约因素与措施

研究延迟焦化装置长周期运行的制约因素与措施延迟焦化装置是炼油厂中重要的装置之一,其主要功能是将重质原油或渣油中的高分子化合物转化为较轻的馏分。
由于装置内部的高温高压环境以及原料的多变性,延迟焦化装置在长时间运行中可能会面临一些制约因素。
本文将探讨延迟焦化装置长周期运行的制约因素以及相应的解决措施。
一个重要的制约因素是装置内部催化剂的失活。
由于高温高压条件下的催化反应,催化剂会逐渐失去活性。
原料质量的波动以及催化剂中的有害物质也会加速催化剂的失活。
为了解决这个问题,可以采用定期的催化剂再生工艺,通过高温氢气处理或烧结来恢复催化剂的活性。
定期的催化剂更换也是一种有效的措施。
装置内部的管道和设备可能会因为高温高压环境以及原料中的硫化物等有害物质而受到腐蚀和磨损。
这种腐蚀和磨损会导致管道泄露和设备故障,进而影响装置的正常运行。
为了解决这个问题,可以采用不锈钢、镍基合金等耐腐蚀材料来替换容易受到腐蚀的部件。
定期的设备检修和维护也是非常重要的。
延迟焦化装置在长时间运行中可能会面临原料中的杂质含量增加、混合物比例变化等问题。
这些问题可能会导致催化剂失活、设备堵塞以及产品质量下降等。
为了解决这个问题,可以采用精细过滤和脱盐工艺来去除原料中的杂质。
建立定期的原料采样与分析系统,可以帮助及时发现原料质量的变化。
装置内部的操作和控制参数的调整也是保证延迟焦化装置长周期运行的重要因素。
合理的操作和控制可以提高装置的效率和稳定性,减少失效的风险。
设立完善的操作规程和自动化控制系统非常重要。
延迟焦化装置长周期运行的制约因素与措施包括催化剂的失活与再生、管道和设备的腐蚀和磨损、原料的杂质变化以及操作和控制的调整等。
通过采取相应的措施,可以提高装置的稳定性和运行效率,延长装置的使用寿命。
延迟焦化影响因素.pptx
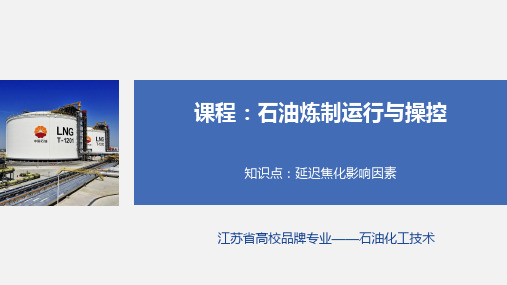
出
炉 管 结
口 控 制
焦
500 ℃
延迟焦化影响因素
三、反应压力的影响
延迟焦化的目的是希望多产馏分油而少产焦炭。压力较高时对热 裂解反应是不利的,而有利于缩合反应。
较低的压力下焦炭 产率较低。 一般焦炭塔的操作 压力为 0.15~0.17MPa。
延迟焦化影响因素
四、循环比的影响
循环比:焦化分馏塔内一部分比焦化馏出油重的循环油量与原 料油量的比值。
课程:石油炼制运行与操控
知识点:延迟焦化影响因素 江苏省高校品牌专业——石油化工技术
延迟焦化影响因素
原料
分馏塔
产品
分馏塔
加热炉 焦炭塔
延迟焦化影响因素
一、原料对延迟焦化的影响
1、原料的性质 延迟焦化的产物分布与原料的性质有密切的关系。
(1)与原料残炭值关系:
焦炭产率与原料残炭值直接相 关,一般情况下约为原料残炭 值的1.5~2.0倍。
焦化蜡油与焦炭的产率降低,焦炭的挥发分降低。
加 热 炉 出 口 温 度
焦 炭 塔 温 度
反
反
应
应
速
深
度
度
焦
炭
轻
产
组
率
分
与
产
挥
率
发
分
延迟焦化影响因素
二、反应温度的影响 (2)加热炉出口温度控制是延迟焦化生产重要操作因素。
加热炉出口温度受到加热炉加热负荷的限制,同时过高的温度使炉管易于
结焦,影响开工周期; 实际生产中加热炉出口温度一般控制在480~515℃内,根据不同的原料确 定加热炉出口温度,残炭值较高的原料,加热炉出口温度应较低。
%
50 45
研究延迟焦化装置长周期运行的制约因素与措施

研究延迟焦化装置长周期运行的制约因素与措施延迟焦化装置长周期运行的制约因素及其措施石油化工行业中,延迟焦化工艺被广泛采用,因其具有较高的经济效益和良好的资源利用率。
然而,长周期的稳定运行一直是工业界面临的难题。
在长时间的操作中,设备容易受到磨损和腐蚀,这些因素将影响延迟焦化装置的生产量和质量。
因此,本文分析了延迟焦化装置长周期运行的制约因素,并提出了相应的措施。
1. 热裂解管系的损坏热裂解管系是延迟焦化装置的重要组成部分,其工作环境无论是在高温还是高压下都具有较大的冲击力。
长期运行后,热裂解管系容易发生磨损和裂纹,影响其稳定运行。
对此,应增加热裂解管系的检查周期,定期进行管道壁厚测量、超声波探伤等工作,及时发现问题并进行维护和修复。
2. 催化剂的堆塞催化剂是延迟焦化过程中不可或缺的催化剂。
虽然催化剂的使用寿命较长,但是在长周期运行后,催化剂的表面会发生撕裂和变形等现象,导致催化剂的性能逐渐下降。
堆塞严重时,会影响反应速率和延迟焦化产品质量。
因此,应定期对催化剂进行评估,并选择合适的时间,及时更换。
3. 烟气排放系统烟气排放系统是延迟焦化装置中重要的组成部分,排放效果不仅关乎设备的环保性能,还直接影响设备的性能和寿命。
长周期的运行中,烟气排放系统会遭受高温和浓度较高的有机气体的侵蚀,造成管道堵塞,减少排放效果,严重时会导致系统爆炸等安全隐患。
加强烟气排放系统的维护,增加检查频率,及时发现和处理系统中的隐患,确保系统安全。
总之,延迟焦化装置的长周期运行需要全面系统地考虑各因素,针对性地制定合理的措施,不断优化工艺和技术,从而确保设备的稳定运行。
研究延迟焦化装置长周期运行的制约因素与措施

研究延迟焦化装置长周期运行的制约因素与措施通过对我国某化工产业当中,延迟焦化设备长期运行工作当中的制约因素进行分析和探索,根据延迟焦化设备的实际工作特性,分析炼油厂当中延迟焦化设备长期运行工作当中产生的制约性因素,有效总结和优化了整个生产工艺流程,减缓了内部一些关键性部位的结焦、结盐等问题,制定出了有效的预防措施来进行保障,以此来达到延迟焦化设备长期稳定工作的目标。
标签:延迟焦化设备;长期运行;结焦;结盐当前世界上有85%以上的焦化处理设备基本上都采用的是延迟焦化生产工艺,并且取得了良好的工作效果。
本文针对延迟焦化设备,在长期工作运行过程当中产生的不良影响因素进行了分析和探索,同时提出了有效的解决措施。
1 延迟焦化装置长周期运行的制约因素1.1 原油性质变化大在延迟焦化设备的设计原理上,主要使用的是鲁宁管减压渣油,而在实际的生产过程当中,通过使用鲁宁管减压渣油和进口渣油之间进行混合提炼,有的时候通过进口渣油单独提炼,其中产生了进口原油和渣油之间的相互变换非常频繁,进而造成了原油的性质变化比较明显。
在整个工作过程当中的操作难度较大,对整个延迟焦化设备的安全稳定运行形成了不良的影响。
1.2 加热炉管结焦问题加热炉是延迟焦化设备当中非常重要的构成环节,渣油在炉管内部进行有效的加热,超过一定的温度界限之后会产生裂解缩合反应。
该反应完成之后原油当中会产生大量的游离碳元素,这些碳元素会在设备的内壁上进行聚集成焦,结焦之后的管道内壁温度会不断上升,压力上也会不断上涨,严重的情况下甚至会造成整个设备的工作停止,直接影响到了加热炉的长期稳定工作和运行。
1.3 挥发线内结焦问题在高温的工作环境下,原油当中的成分会产生一定的挥发现象,在挥发出来的气体和内壁管道上进行结焦。
当原油当中含有大量的硫元素,那么焦炭塔的顶层上直接会直接形成结焦问题,此时会发现结焦会形成焦炭,塔内部的压力不断上涨,最高压力可以达到0.25MPa以上,直接威胁到了焦炭塔的安全稳定生产。
延迟焦化影响因素.
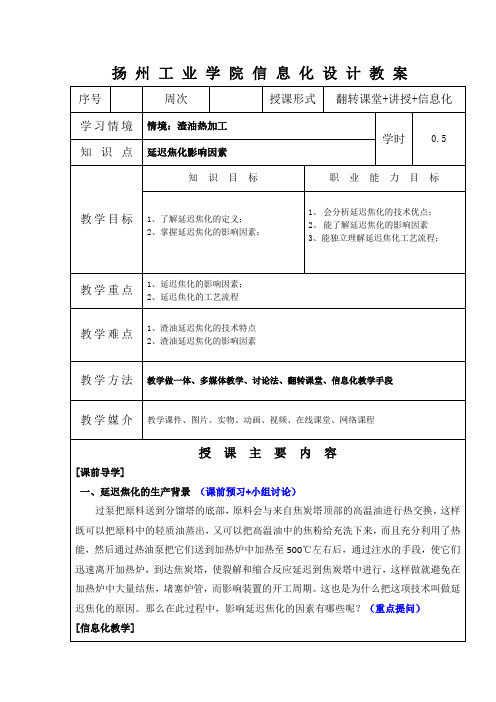
序号
周次
授课形式
翻转课堂+讲授+信息化
学习情境
情境:渣油热加工
学时
0.5
知识点
延迟焦化影响因素
教学目标
知识目标
职业能力目标
1、了解延迟焦化的定义;
2、掌握延迟焦化的影响因素;
1、会分析延迟焦化的技术优点;
2、能了解延迟焦化的影响因素
3、能独立理解延迟焦化工艺流程;
教学重点
1、延迟焦化的影响因素;
2、延迟焦化的工艺流程
教学难点
1、渣油延迟焦化的技术特点
2、渣油延迟焦化的影响因素
教学方法
教学做一体、多媒体教学、讨论法、翻转课堂、信息化教学手段
教学媒介
教学课件、图片、实物、动画、视频、在线课堂、网ቤተ መጻሕፍቲ ባይዱ课程
授课主要内容
[课前导学]
一、延迟焦化的生产背景(课前预习+小组讨论)
过泵把原料送到分馏塔的底部,原料会与来自焦炭塔顶部的高温油进行热交换,这样既可以把原料中的轻质油蒸出,又可以把高温油中的焦粉给充洗下来,而且充分利用了热能,然后通过热油泵把它们送到加热炉中加热至500℃左右后,通过注水的手段,使它们迅速离开加热炉,到达焦炭塔,使裂解和缩合反应延迟到焦炭塔中进行,这样做就避免在加热炉中大量结焦,堵塞炉管,而影响装置的开工周期。这也是为什么把这项技术叫做延迟焦化的原因。那么在此过程中,影响延迟焦化的因素有哪些呢?(重点提问)
3、系统压力的影响,延迟焦化的目的是希望多产馏分油而少产焦炭。压力较高时对热裂解反应是不利的,反应压力对焦化的产品分布有一定的影响,压力高,反应深度加大,气体和焦炭收率增加,液体收率下降,焦炭的挥发分也会有所增加;压力太低,不能克服分馏塔及后路系统的阻力。原则上是在克服系统阻力的条件下,尽可能采用低的反应压力,通常为0.15~0.17MPa(表)。
研究延迟焦化装置长周期运行的制约因素与措施

研究延迟焦化装置长周期运行的制约因素与措施延迟焦化装置是炼油厂中一种重要的装置,它通过高温条件下将石油原料进行热分解,产生大量的石油焦和其他重质油品。
延迟焦化装置在长周期运行过程中会面临一些制约因素,如设备老化、操作不当、原料质量变化等问题。
本文将探讨延迟焦化装置长周期运行的制约因素,并提出相应的解决措施。
设备老化是导致延迟焦化装置长周期运行问题的主要因素之一。
随着设备使用时间的延长,设备件的磨损、腐蚀等问题逐渐显现。
这些问题会导致设备性能下降,影响焦化反应效果。
为解决这一问题,可以采取以下措施:1. 定期检修和维护设备。
对设备进行定期的检查、维护和维修,修复或更换受损的设备件,确保设备的正常运行。
2. 加强设备保护。
在设备的易损部位设置保护措施,如喷涂耐磨材料、加装补偿装置等,延长设备使用寿命。
操作不当也是延迟焦化装置长周期运行的一个重要因素。
操作人员对于设备的操作技术和工艺要求不熟悉,容易导致操作不当。
为解决这一问题,可以采取以下措施:1. 建立完善的操作规程和操作培训制度。
制定明确的操作规程,并对操作人员进行培训,提高其操作技术水平。
2. 引入先进的自动化控制系统。
通过引入先进的自动化控制系统,减少对操作人员的依赖,提高设备操作的准确性和稳定性。
原料质量变化也会对延迟焦化装置的长周期运行造成一定的影响。
原料的硫含量、金属含量、凝点等参数会影响焦化反应的进行。
为解决这一问题,可以采取以下措施:1. 优化原料调配。
根据原料质量的变化情况,合理调配不同原料,调整生产工艺,使其适应原料质量变化。
2. 设置预处理装置。
在延迟焦化装置前设置预处理装置,对原料进行预处理,如脱硫、脱氮等,降低原料对焦化装置的影响。
延迟焦化装置长周期运行受到设备老化、操作不当和原料质量变化等因素的制约。
通过定期检修维护设备、加强设备保护、建立完善的操作规程和操作培训制度、引入先进的自动化控制系统、优化原料调配和设置预处理装置等措施,可以有效地解决这些问题,确保延迟焦化装置的长周期运行效果。
- 1、下载文档前请自行甄别文档内容的完整性,平台不提供额外的编辑、内容补充、找答案等附加服务。
- 2、"仅部分预览"的文档,不可在线预览部分如存在完整性等问题,可反馈申请退款(可完整预览的文档不适用该条件!)。
- 3、如文档侵犯您的权益,请联系客服反馈,我们会尽快为您处理(人工客服工作时间:9:00-18:30)。
第三章延迟焦化装置的工艺条件及影响因素分析
3.1延迟焦化装置的主要工艺操作指标
工艺指标是由安全生产和生产目的决定的,是生产方案的产物,是进行生产调节的依据,同是也是安全生产的要求。
实际生产中,工艺操作指标确定后,操作就按照它来控制。
通常,不允许随意更改工艺指标。
3.1.1产品质量指标
产品质量指标是控制出装置产品质量的依据,它是根据产品的用途确定下来的。
如果用途改变了,指标应随之调整。
操作过程中要求严格控制产品质量的意义,也在于一方面保证质量,另一方面同时考虑经济效益;既保证质量,又保证数量。
尽管焦化装置出产的汽油、柴油、液化气、干气、蜡油、石油焦都是半成品,都要经过后续装置精制才能成为产品,但为了后续装置加工方便,对汽油、柴油等还是作出相关规定,见第一章表1-5-3。
3.1.2主要工艺操作指标
操作指标是保证装置正常生产的先决条件,某些指标超过了就要造成生产波动或事故。
生产中要加强操作调节,保证生产的正常进行,而操作指标是根据实际生产经验和生产目的制订的,要求生产中严格执行。
3.1.2.1原料进装置及公共系统要求
以某石化延迟焦化装置为例,原料进装置及公共系统要求见表3-1-1。
3.1.2.1焦炭塔
焦炭塔工艺操作指标见表3-1-2。
表3-1-1原料进装置及公共系统要求
表3-1-2焦炭塔工艺操作指标
3.1.2.3分馏塔
分馏塔工艺操作指标见表3-1-3。
表3-1-3分馏塔工艺操作指标
3.1.2.4加热炉
加热炉工艺操作指标见表3-1-4。
表3-1-4加热炉工艺操作指标
3.1.2.5放空塔
放空塔工艺操作指标见表3-1-5。
3.1.2.6吸收稳定系统
吸收稳定系统控制参数见表3-1-6。
3.1.2.7气压机组
气压机主要控制参数见表3-1-7。
表3-1-7气压机主要控制参数
3.2延迟焦化的影响因素分析
延迟焦化的影响因素主要有原料性质、工艺操作条件。
3.2.1延迟焦化的原料性质
常规延迟焦化原料是减压渣油。
由于延迟焦化是一种热加工过程,因此原料的多样性是其重要的特点和优点之一,对于延迟焦化而言,加工各种高硫含量、高酸值的减压渣油都不应该成为问题。
此外,从各种炼油工艺和工艺产出的重质料也都可以成为焦化的原料,例如各种三废处理得到的废油、废渣,催化裂化油浆、润滑油精制抽出油、丙烷脱沥青得到的硬沥青,乙烯裂解得到的乙烯焦油等均可能成为其加工对象。
焦化原料性质极大地影响到焦化产品收率的分布。
焦化原料性质见第一章表1-5-
1。
图3-2-1是原料油密度和焦化产品分布之间的关系。
3.2.2延迟焦化主要工艺条件
延迟焦化主要操作参数包括焦炭塔顶压力、加热炉出口温度和联合循环比等,生产普通焦的延迟焦化主要条件见表3-2.1。
表3-2-1延延焦化生产普通焦的主要操作条件
<1)反应压力
一般用焦炭塔顶压力来代表。
压力对焦化产品分布是有一定影响的。
压力增高,反应深度加大,气体和焦炭收率增加,液体收率下降,焦炭中挥发分含量也增加。
现代延迟焦化在保证能克服下游系统阻力的前提下,尽可能采用较低的反应压力。
20世纪80年代设计
的焦炭塔压力为0.172~0.206Mpa,目前则为0.103~0.137Mpa。
表3-2-2列出了操作压力对产品产率分布的影响。
图3-2-2是压力对焦化馏出油收率的影响。
在压力0.103Mpa、循环比1.15时,焦化蜡油<CGO)收率可以达到35.2﹪,比常规高出10﹪左右。
表3-2-2延迟焦化装置的操作压力对产品收率的影响
<2)反应温度
一般是指焦化加热炉出口温度或焦炭塔温度,是延迟焦化装置的重要操作指标,它的变化直接影响到炉管内和焦炭塔内的反应深度,从而影响到焦化产物的产率和性质。
当操作压力和循环比固定后,提高焦炭塔温度将使气体和石脑油收率增加,瓦斯油收率降低。
焦炭产率将下降,并使焦炭中挥发分下降。
但是,焦炭塔温度过高,容易造成泡沫夹带并使焦炭硬度增大,造成除焦困难。
温度过高还会使加热炉炉管和转油线的结焦倾向增大,影响操作周期。
如焦炭塔温度过低,则焦化反应不完全并生成软焦或沥青。
挥发分含量是焦炭的重要质量指标,生产中一般控制焦炭的挥发分为 6.0﹪~8.0﹪。
在操作中用焦炭塔温度来控制焦炭的挥发分含量。
但是,焦化装置操作温度的可调节范围很窄。
我国的延迟焦化装置加热炉出口温度一般均控制在495~505℃范围之内。
加热炉出口温度对焦化产品产率的影响见表3-2-3。
<3)循环比
循环比=循环油/新鲜原料油。
联合循环比=<新鲜原料油量+循环量)/新鲜原料油量=1+循环比。
在生产过程中,循环油并不单独存在。
在分馏塔下部脱过热段,因反应油气气的降低,重组分油从汽相转入液相,冷凝后进入塔底,这部分油就称循环油,它与原料油在塔底混合后一起送入加热炉的辐射管,而新鲜原料油则进入对流管中预热。
因此,在实际生产中,循环油流量可由辐射管进料量与对流管进料量之差来求得。
对于较重的、易结焦的原料,由于单程裂化深度受到限制,就要采用较大的循环比,有时达1.0左右;对于一般原料,循环比为0.1~0.5。
,循比增大,可使焦化汽油、柴油收率拉加,焦化蜡油收率减少,焦炭和焦化气体的收率拉加。
3-2-3为联合循环比对大庆减压渣油焦化产品收率的影响。
中国石油化工研究院开发了单程操作延迟焦化,进行了循环比为0的实验。
表3-2-
4比较了有循环比和单程操作对延迟焦化收率的影响。
、
由表中数据可看出,与高循环比的操作相比较,单程操作的液体收率可提高5﹪~6﹪,气体和焦炭收率均可下降2﹪~4﹪。
降低循环比也是延迟焦化工艺发展趋向之一,其目的是通过增产焦化蜡油来扩大催化裂化、加氢裂化的原料油量。
然后,通过加大裂化装置处理来提高成品汽、柴油的产量。
另外,在加热炉能力确定的情况下,低循环比还可以增加装置的处理能力。
降低循比的办法是是减少分馏塔下部重瓦斯油回流量,提高蒸发希和塔底温度。
这将引起塔底和炉管结焦,开工周期缩短。
因此塔底温度不宜超过400℃。
循环比降低后,可以降低焦炭产率和提高液体产品收率。
但焦化蜡油的质量也相应下降。
表3-2-5为在低压、超低循环比的条件下,焦化蜡油产率和质量的对比。
表3-2-5不同操作条件下的焦化蜡油产率和质量
在讨论焦化循比时应指出,新设计的焦化不仅可以采用低反应压力,超低循环比等工艺条件,而且可采用馏分油循环技术。
这一技术是由Conoco/Bechtel Alliance联合开发的,可延长加热炉运行周期,降低焦炭收率和增加液体收率。
装置由此可以增加的经济效益大致如下;
液体收率增加2.0﹪~2.5﹪;
焦炭产率下降2.5﹪~3.5﹪;
经济效益800*104美元/年<按2.0Mt/a装置能力计算),详细比较见表3-2-6
表3-2-6延迟焦化馏分油循环情况对比。