提高冷冲压零件的几种办法
复合处理提高冷冲冲裁模具寿命

复合处理提高冷冲冲裁模具寿命作者:陈鸿桂许颖来源:《中外企业家·下半月》 2014年第4期陈鸿桂1 许颖2(1. 武汉工程职业技术学院,湖北武汉430080;2. 武钢矿业公司大冶铁矿,湖北黄石435006)摘要:随着社会经济的快速发展,机械制造业为了确保机械产品的加工质量,提高产品加工效率,冷冲压模具在零部件的批量化生产中已经应用越来越广泛。
然而冷冲模具由于其应用的特殊情况,使其寿命并不长,多出现裂纹、磨损、断裂等现象,大大的降低了产品的出产率。
于是,如何提高冷冲模具的使用寿命成为了模具制造中的一项重要的研究课题。
因此,笔者对于冷冲模型寿命的提高提出了一些解决方案。
关键词:冷冲压模具;失效;热处理;表面处理中图分类号:TG385.2 文献标志码:A 文章编号:1000-8772(2014)12-0109-02随着我国工业生产的飞速发展,对于工业产品的品种、形状精度、数量、质量等的相关要求也越来越高,厂家为了能够快速获得质量上乘、尺寸精准、工艺稳定的产品对对模具的要求越来越高,需要量也相应增加。
模具性能好坏,寿命高低,直接影响了产品的质量和厂家的经济效益。
经过多年的研究和发展,我国冷冲压模具行业已经有了长足的发展,但目前仍存在一些问题亟需解决。
一、冷冲压模具失效(一)过载失效此类失效主要由于材料本身承载能力不足以满足工作载荷(包括随机波动载荷)引起模具失效,如材料韧度不足、开裂失效、强度不足易变形、镦粗失效,特别是脆断开裂失效是生产中最为常见的失效方式。
1. 材料韧性不足的失效冲头模具的折断、开裂等,甚至能够造成模具不可修复永久失效。
此种失效的主要原因是因为材料的韧性不能够满足模具工作时所需要满足的条件。
2. 强度不足失效在冷镦、冷挤冲头中由于模具材料不能够满足工作需要承担的压力,易出现镦头、下凹、弯曲变形等情况的失效。
此种模具失效主要是由于工作载荷过大,模具硬度偏低。
此类失效表明模具所使用材料强度不足,塑性、韧度有余。
提高冷冲压模具寿命的措施

国内 冲模 寿命 普 遍 较低 是 长 期 困扰 企 业 的 问 题 。 随着 高 效 、 速 、 精 度 的新 型 塑 性 加 工 工 艺 的 高 高
一
。
出现 及 发 展 , 模 具 寿 命 提 出 了 越 来 越 高 的 要 求 。 对
2 提 高 冷 冲 模 寿 命 的措 施
批 模 具 不 可 能 均 以 同 一 种形 式 失 效 , 研 究 在
提 高模 具 寿 命 的 技 术 措 施 方 案 时 , 先 应 分 析 确 定 首 这一 批 模 具 的 主要 失 效 形 式 , 分析 其 原 因 、 响 因 并 影 素 , 而 提 出 解 决 问题 的 方 案 。 从 可按如下步骤 分析模具失效原 因 :
伤失效 。
断 口。
检 查 表 面 到 心 部 的 金 相 组 织 、 量 从 表 面 到 心 测 部的硬度 。
12 模 具 失 效 原 因 的 分 析 .
一
( ) 析 判 断 汇 集 上 述 分 析 结 果 后 进 行 综 合 3分 分 析 , 断 引 起损 伤 和 失 效 的 原 因 , 此 基 础 上 制 订 判 在 提 高模 具 寿 命 的各 项 技 术 措 施 。
【 要 】 本 文分 析 了冷 冲压 模具 失效 的基本 形 式 及原 因 , 多方 面探 讨 了提 高 冷冲模 寿命 的 措施 。 摘 从 【 题 词 】 冷 冲模 主 【u na 】 S m -- ay 寿命 措 施 s ae aa s dt r n a r fnadtn bu t l qnh g ol s s dt l.r o rs g pr nl i e o adl . l vlao ot e o uci u d c s ela e fa i p ys h fm c  ̄s i i i a c d oo h n m d i u e h l s : in e ̄
如何提高冷冲压模具使用寿命
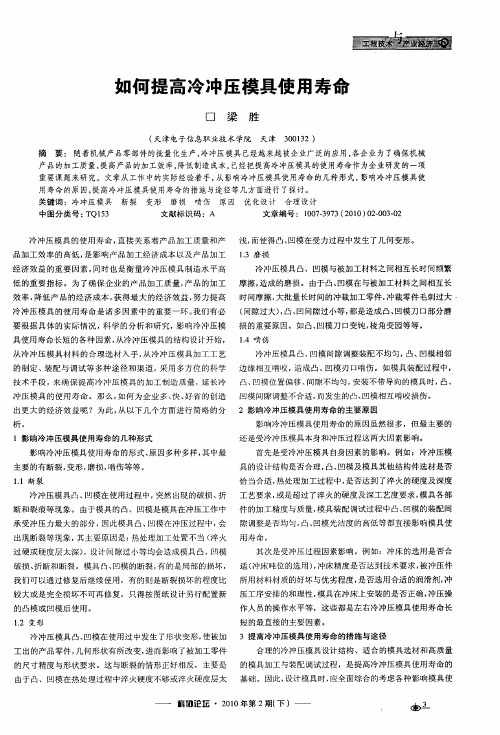
冷冲压模具 凸、凹模与被加工材料之 间相互长时 间频繁
低 的重 要 指 标 。 为 了确 保 企 业 的产 品 加 工 质 量 , 品 的 加 工 摩 擦 , 成 的 磨 损 。 由 于 凸 、 模在 与被 加工 材 料 之 间相 互 长 产 造 凹
效率 , 降低产 品的经济成本 , 获得最 大的经济效益 , 努力提高 时间摩擦, 大批量长时间的冲裁加工零件 , 冲裁零件毛刺过大 冷冲压 模具的使用寿命 是诸多因素 中的重要一环 。 我们有必 ( 间隙过大) 凸、 , 凹间隙过小等, 都是造成凸、 凹模刀 口部分磨
我们可以通过修复后继续使用 ,有 的则是断裂损坏的程度比 所 用 材 料 材 质 的 好 坏 与优 劣程 度 , 否选 用合 适 的润 滑 剂 , 是 冲
模 冲 较 大 或 是 完 全 损 坏 不 可 再 修 复 ,只 得 按 图纸 设 计 另 行 配 置 新 压工 序 安 排 的 和 理 性 , 具 在 冲 床 上 安 装 的 是 否 正确 , 压 操
如何 提高冷冲压模具使 用寿命
口 梁 胜
天津 303 ) 0 12 ( 津 电子 信 息职 业 技 术 学 院 天
摘
要 : 随着机械产 品零部件 的批量化生产 , 冷冲压模具 已经越来越被企业广泛 的应用, 各企业为 了确保机械
产 品的加工质量 , 提高产 品的加工效率, 降低 制造 成本 , 已经把提高冷冲压模具 的使用寿命作 为企业研发的一项 重 要课题来研 究。文章从工作 中的实际经验着手, 从影响冷冲压模具使用寿命的几种 形式, 影响冷冲压模具使 用 寿命 的原 因, 提高冷冲压模具使用寿命 的措施与途径等凹模间隙调整装配不均匀 , 凸、 凹模相邻
的制 定 、装 配 与 调 试 等 多 种 途 径 和 渠 道 , 用 多 方 位 的 科 学 边 缘 相 互 啃 咬 , 成 凸、凹模 刃 口啃 伤 。如 模 具 装 配 过 程 中 , 采 造
冲压磨具制造精要提升冲压件质量的秘诀
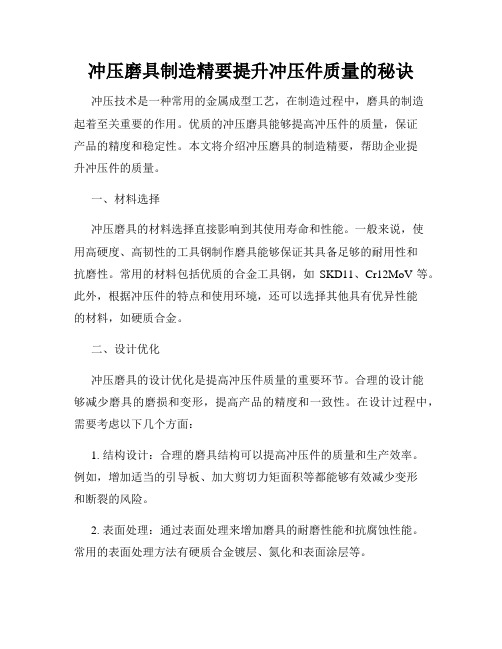
冲压磨具制造精要提升冲压件质量的秘诀冲压技术是一种常用的金属成型工艺,在制造过程中,磨具的制造起着至关重要的作用。
优质的冲压磨具能够提高冲压件的质量,保证产品的精度和稳定性。
本文将介绍冲压磨具的制造精要,帮助企业提升冲压件的质量。
一、材料选择冲压磨具的材料选择直接影响到其使用寿命和性能。
一般来说,使用高硬度、高韧性的工具钢制作磨具能够保证其具备足够的耐用性和抗磨性。
常用的材料包括优质的合金工具钢,如SKD11、Cr12MoV等。
此外,根据冲压件的特点和使用环境,还可以选择其他具有优异性能的材料,如硬质合金。
二、设计优化冲压磨具的设计优化是提高冲压件质量的重要环节。
合理的设计能够减少磨具的磨损和变形,提高产品的精度和一致性。
在设计过程中,需要考虑以下几个方面:1. 结构设计:合理的磨具结构可以提高冲压件的质量和生产效率。
例如,增加适当的引导板、加大剪切力矩面积等都能够有效减少变形和断裂的风险。
2. 表面处理:通过表面处理来增加磨具的耐磨性能和抗腐蚀性能。
常用的表面处理方法有硬质合金镀层、氮化和表面涂层等。
3. 排料设计:合理的排料设计能够降低冲压件的变形风险。
在排料方面,需要考虑工件的材料、形状、尺寸等因素,避免材料过多或者过少的堆积情况。
三、制造工艺冲压磨具的制造工艺对其质量有着直接的影响。
在制造过程中,应该注重以下几点:1. 数控加工:采用数控加工设备能够提高磨具的加工精度和一致性,减少人为误差。
尤其是对于复杂形状的磨具来说,数控加工技术不仅能够提高制造效率,还能够减少废品率。
2. 热处理:热处理可以改变磨具的组织和性能,提高其硬度和强度。
常用的热处理方法有淬火、回火、渗碳等。
根据磨具的具体要求和工作条件,选择合适的热处理工艺能够提高其使用寿命和性能。
3. 组装和调试:在磨具的组装和调试过程中,需要严格遵循工艺要求,确保磨具的各个部件能够正常配合。
同时,还需要进行灵敏性及精度的调试,以确保磨具能够稳定工作并提供高质量的冲压件。
冲压磨具结构设计中的优化方法提高冲压效果的有效途径

冲压磨具结构设计中的优化方法提高冲压效果的有效途径在冲压磨具结构设计中,优化方法可以有效提高冲压效果的效率。
通过设计和改进冲压磨具的结构,可以降低冲压过程中的摩擦力和应力集中,提高产品质量和生产效率。
本文将介绍几种优化冲压磨具结构的方法。
1. 合理选择磨具材料磨具的材料选择关系到冲压加工的效果和寿命。
常用的磨具材料有高速钢、硬质合金等。
根据不同的冲压工件要求,选择合适的材料可以提高冲压磨具的硬度和耐磨性,减少磨具损耗和加工成本。
2. 设计合理的结构形式磨具的设计结构形式应根据冲压工件的形状和加工要求进行合理选择。
合理的结构设计可以减少冲击载荷和振动,降低冲压过程中的噪音和能量消耗。
例如,在冲压过程中,为了减少应力集中,可以采用圆角设计,增加局部强度,提高磨具的抗变形能力等。
3. 优化磨具的表面处理磨具的表面处理可以提高冲压效果和寿命。
通过表面处理可以增加磨具的硬度、抗磨性和降低摩擦系数。
常用的表面处理方法有热处理、镀膜和涂层等。
合适的表面处理方法可以延长磨具的使用寿命,提高冲压效果。
4. 运用CAD/CAE技术进行优化设计利用计算机辅助设计软件(CAD)和计算机辅助工程分析软件(CAE)对磨具结构进行仿真和优化分析,可以快速获取磨具结构的各种参数和性能指标。
通过CAD/CAE技术的应用,可以避免设计方案中的缺陷和问题,提高设计效率和精度。
5. 加强磨具的检测和维护对于已经使用的冲压磨具,定期进行检测和维护是保持冲压效果的有效途径。
通过检查和维护可以及时发现和解决磨具的磨损、变形和缺陷等问题,保持磨具的准确性和稳定性,延长使用寿命。
通过优化冲压磨具的结构设计,可以有效提高冲压效果的效率,降低加工成本和改善产品质量。
合理选择磨具材料、设计合理的结构形式、优化磨具的表面处理、运用CAD/CAE技术进行优化设计和加强磨具的检测和维护都是提高冲压效果的有效途径。
冲压磨具的结构优化与改进技巧分享提高冲压磨具的精度和稳定性
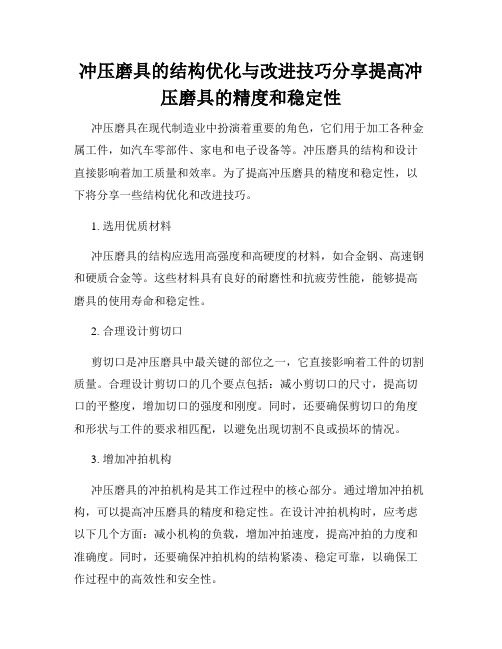
冲压磨具的结构优化与改进技巧分享提高冲压磨具的精度和稳定性冲压磨具在现代制造业中扮演着重要的角色,它们用于加工各种金属工件,如汽车零部件、家电和电子设备等。
冲压磨具的结构和设计直接影响着加工质量和效率。
为了提高冲压磨具的精度和稳定性,以下将分享一些结构优化和改进技巧。
1. 选用优质材料冲压磨具的结构应选用高强度和高硬度的材料,如合金钢、高速钢和硬质合金等。
这些材料具有良好的耐磨性和抗疲劳性能,能够提高磨具的使用寿命和稳定性。
2. 合理设计剪切口剪切口是冲压磨具中最关键的部位之一,它直接影响着工件的切割质量。
合理设计剪切口的几个要点包括:减小剪切口的尺寸,提高切口的平整度,增加切口的强度和刚度。
同时,还要确保剪切口的角度和形状与工件的要求相匹配,以避免出现切割不良或损坏的情况。
3. 增加冲拍机构冲压磨具的冲拍机构是其工作过程中的核心部分。
通过增加冲拍机构,可以提高冲压磨具的精度和稳定性。
在设计冲拍机构时,应考虑以下几个方面:减小机构的负载,增加冲拍速度,提高冲拍的力度和准确度。
同时,还要确保冲拍机构的结构紧凑、稳定可靠,以确保工作过程中的高效性和安全性。
4. 优化刃口结构刃口是冲压磨具中起到切削和成形作用的部分,其结构优化对于提高冲压磨具的精度和稳定性至关重要。
在优化刃口结构时,应考虑以下几个因素:减小刃口的边缘半径,提高刃口的抗疲劳性能,改善刃口的切削角度和刃口曲线,以提高切割质量和加工效率。
5. 引入润滑和冷却系统在冲压磨具的设计中,引入润滑和冷却系统可以有效地降低摩擦和热量的产生,减少磨具磨损和变形的风险,从而提高冲压磨具的精度和稳定性。
润滑和冷却系统可以采用液体或气体形式,具体的选择取决于工件的材料和加工要求。
6. 考虑磨具的维护和保养冲压磨具在使用过程中需要进行定期的维护和保养,以确保其良好的工作状态和长期的使用寿命。
维护和保养包括切削刃口的修磨、刃口的更换、磨具的清洁和润滑等。
只有通过良好的维护和保养,才能保证冲压磨具的精度和稳定性。
冷冲压实训操作能力培养探究

冷冲压实训操作能力培养探究冷冲压是一种常见的金属加工工艺,广泛应用于汽车、家电、电子产品等行业中。
冷冲压实训操作能力培养对于金属加工专业学生和从业人员来说至关重要。
本文将探究冷冲压实训操作能力培养的重要性,并介绍一些有效的培养方法和技巧。
1. 提高学生的操作技能冷冲压实训操作能力培养可以帮助学生掌握冷冲压机床的操作技能,包括模具安装、调整、操作等方面的技能。
通过实际操作,学生可以了解冷冲压机床的结构和工作原理,提高自己的实际操作能力。
2. 培养学生的安全意识冷冲压机床是一种高速运转的机械设备,操作不慎可能导致严重的伤害。
通过实训操作能力培养,可以让学生养成严谨的操作习惯和安全意识,提高他们在实际工作中的安全风险意识。
3. 加强学生的团队合作能力冷冲压机床通常需要多人合作进行操作,包括模具更换、产品收集、机床调整等等。
实训操作能力培养可以帮助学生培养团队合作的能力,学会与他人配合,提高工作效率。
二、冷冲压实训操作能力培养的方法和技巧1. 实地实训对于冷冲压专业的学生来说,实地实训是最重要的一环。
通过实地操作冷冲压机床,学生可以更加直观地领会机床的工作原理和操作技巧。
学校可以与相关企业合作,提供实地实训的机会,让学生亲身体验真实的工作环境。
2. 模拟实训在实际的冷冲压机床操作过程中,风险较大,因此学校可以设置模拟实训环节。
通过模拟实训,学生可以在较为安全的环境下进行操作练习,尝试不同的操作方法和技巧,提高自己的实际操作能力。
3. 知识点讲解除了实际操作,学校还可以通过知识点讲解的方式,向学生介绍冷冲压机床的结构、工作原理、操作规范等知识,让学生对冷冲压加工有一个系统的认识。
这样可以帮助学生更好地理解实际操作中的一些技巧和注意事项。
4. 案例分析通过案例分析的方式,让学生了解一些冷冲压加工中的典型问题和解决方法,帮助他们在实际操作中能够更加从容地应对各种突发情况。
5. 实训考核为了检验学生的实际操作能力,学校可以设置相关的实训考核环节,对学生进行综合考核,包括操作技能、安全意识、团队合作等方面的评价。
冲压磨具结构改进方案提升冲压质量的有效途径
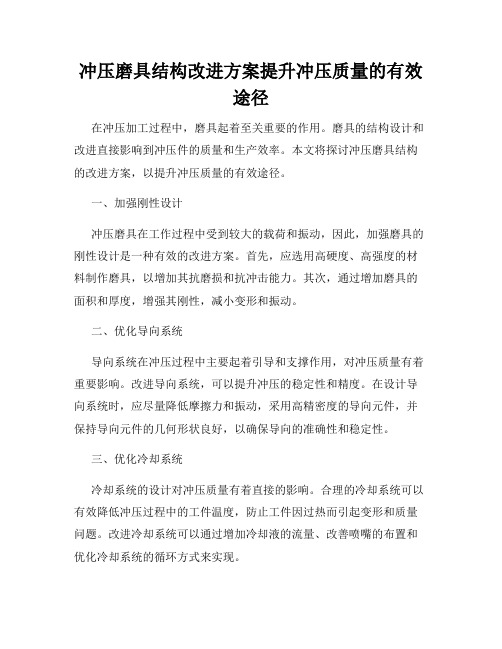
冲压磨具结构改进方案提升冲压质量的有效途径在冲压加工过程中,磨具起着至关重要的作用。
磨具的结构设计和改进直接影响到冲压件的质量和生产效率。
本文将探讨冲压磨具结构的改进方案,以提升冲压质量的有效途径。
一、加强刚性设计冲压磨具在工作过程中受到较大的载荷和振动,因此,加强磨具的刚性设计是一种有效的改进方案。
首先,应选用高硬度、高强度的材料制作磨具,以增加其抗磨损和抗冲击能力。
其次,通过增加磨具的面积和厚度,增强其刚性,减小变形和振动。
二、优化导向系统导向系统在冲压过程中主要起着引导和支撑作用,对冲压质量有着重要影响。
改进导向系统,可以提升冲压的稳定性和精度。
在设计导向系统时,应尽量降低摩擦力和振动,采用高精密度的导向元件,并保持导向元件的几何形状良好,以确保导向的准确性和稳定性。
三、优化冷却系统冷却系统的设计对冲压质量有着直接的影响。
合理的冷却系统可以有效降低冲压过程中的工件温度,防止工件因过热而引起变形和质量问题。
改进冷却系统可以通过增加冷却液的流量、改善喷嘴的布置和优化冷却系统的循环方式来实现。
四、采用先进的润滑技术润滑剂在冲压过程中扮演着润滑、降低摩擦和冷却的重要角色。
选择合适的润滑剂和先进的润滑技术可以显著提高冲压质量。
例如,使用高效液体润滑剂(Minimum Quantity Lubrication)可以有效降低润滑剂的用量,提高冷却效果,并减少润滑剂残留对环境的污染。
五、应用数值模拟技术数值模拟技术能够模拟和分析冲压过程中的各种物理现象和机理,可以帮助冲压磨具结构的优化设计。
通过数值模拟,可以预测和优化冲压过程中的应力分布、变形情况和变动轨迹,从而提升冲压质量。
数值模拟技术可以节省时间和成本,优化设计方案,并大幅减少试验。
应用数值模拟技术是提升冲压质量的一种有效途径。
六、持续改进和优化冲压磨具结构的改进和优化是一个持续不断的过程。
要不断关注新的技术和材料的发展,吸取经验教训,及时总结和反思,不断进行改进和优化。
- 1、下载文档前请自行甄别文档内容的完整性,平台不提供额外的编辑、内容补充、找答案等附加服务。
- 2、"仅部分预览"的文档,不可在线预览部分如存在完整性等问题,可反馈申请退款(可完整预览的文档不适用该条件!)。
- 3、如文档侵犯您的权益,请联系客服反馈,我们会尽快为您处理(人工客服工作时间:9:00-18:30)。
论提高冷冲压钣件表面质量的几种办法
众所周知,随着中国汽车和农机行业的发展,产品质量的提升越来越受到关注,尤其作为车身“脸面”的冷冲压覆盖件,其表面质量就就显得尤为重要。
大部分冷冲压车身覆盖件采用钢板如DC04、SPCC、BLC、B280VK 等,由于钢板本身硬度较低,模具表面一旦产生碎屑,就会像尖刀一样在钢板表面划出一道道痕迹,严重影响制件外表质量。
如何提升冷冲压件表面质量,本文将从以下三个方面进行介绍。
一.提升模具表面光洁度。
钢板在成型过程中要受到模具的挤压并产生摩擦力,一套模具的设计寿命约为10万到几十万件,在这么多的冲压频次中,模具表面因与钢板挤压摩擦难免要产生一些碎屑,这些碎屑不仅会将钢板表面划伤,产生一道道划痕,也会将模具表面划伤,在模具表面形成一道道划痕,用手触摸就感觉摸在砂纸上一样。
这种划痕一旦在模具上产生,就会在以后的零件成型中留下划痕,严重影响了零件表面质量。
如何将这些划痕去掉,对于没有电镀处理的模具,可首先采用砂轮机将拉磨处粗略打磨,然后用砂纸或用磨石打磨模具表面,经过反复打磨后确保零件表面光滑平顺。
二.适当使用润滑油辅助生产。
冷板冲压件在拉延序生产时,由于部分模具制造质量低,模具表面硬度不高,拉延过程中很容易造成制件和模具拉伤,并经常导致制件出现隐裂、开裂等现象,影响外表质量的同时也增加了不良品率。
冲压拉伸油在冲压拉延序的应用,增加了模具钢板之间的润滑性,为节省冲压油的使用量,根据模具不同的质量和零件形状,可在被模具挤压并与模具产生相对流动的地方涂抹拉伸油,如钢板与模具压边圈接触的地方。
根据制件的状况,可间隔性的在制件上刷油,比如每3-5件在零件表面刷一次油,为保证钢板双面都受到润换,在质量允许的情况下可没隔几件翻一次钢板,在钢板另一侧涂抹拉延油,若钢板不允许则隔一段时间在模具上下模表面涂抹拉伸油。
拉延油涂抹应该采取不过的原则,及尽量少的涂抹拉延油,一是降低加工成本,二是过多的涂抹拉延油将降低焊接质量,焊枪点焊后将发生“井喷”现象。
目前拉伸油一般分为油基拉延油和水基拉延油两种,油基拉延油的的拉延性能较好,一般其抗压性能、润滑性能要高于水性拉延油。
油基拉延油的PB值可达到100KG以上。
可用于一些型面复杂,拉延深度较深的零件,如油箱、顶盖、地板等。
而水基拉伸油抗挤压性能较差,其PB值一般在100Kg以下,可用于型面简单的零件的辅助生产,如加强筋、横梁等。
另外油基拉伸油防锈期较水基拉延油好,正常天气情况下,北方地区室内保存其防锈期一般可达30天左右,而水基拉伸油相对较少,其只能起到工序间防锈的作用,正常天气北方地区室内保存防锈期可达7-12天。
超过一定期限后,拉延油中化学成分开始变质,将加快钢板的腐蚀,对焊接质量和去脂清洗造成一定的影响。
拉延模经过几万件工作后,其表面硬化处理部分已经受严重磨损,
这是零件表面将出现拉延痕,模具也会加速拉伤。
这就需要提高模具表面硬度,目前提高模具表面硬度的方法一般有两种,一种是TD处理,一种是镀鉻。
一、设计和材料选用
并非所有的汽车结构件模具都需要TD处理,只有产量大、产品质量要求高、易磨损的汽车结构件、底板件模具才最需要TD。
我们认为汽车结构件模具在采用TD处理时需要注意的主要事项有:
1、设计:选择合适的长径比,单块模具的长度最好小于380mm, 厚度大于70mm,孔距、孔边距大于5mm,尽量避免尖角,R需大于0.5mm。
这样才能确保TD过程中的变形控制、热应力和组织应力的消除,从而有效规避和减少工件在TD过程中开裂和变形量过大的风险;
2、基体材料的选用:最好选择Cr12MoV、SKD11、KD11S、DC5
3、D2 、D6、 A2等。
我们通过六年的材料选用跟踪,我们认为如果不采用TD技术,进口材料的使用效果明显优于国产材料。
如果采用TD处理,相同含碳量的国产材料的使用效果与进口材料差别不大。
因为影响TD层形成,及其质量优劣的主要因素是金属材料的含碳量的高低和分布的均匀性;
3、初始热处理工艺;
4、制造过程的控制;
5、特殊情况下的焊补;
6、装配、调整和使用,人、机、料、法、环的匹配。
二、正确认识TD后工件的变形量
从理论上讲,并没有不变形的热处理,TD也一样,这也是TD今后攻关的主要课题。
只不过TD在如此高温度下相对其他热处理其变形量应该算最小的。
尽管TD处理也会有变形,但是可以通过工艺试验,最有效的方法是用预留尺寸法来弥补。
事实上TD处理的变形量针对每一种金属材料并没有一个通用的、精确的计算公式。
目前针对国产的金属材料我们摸索出的平均的变形量约为≤0.05‰,如果只针对于同一炉次的材料我们通过工艺试验的方法可以精确地控制在能够满足
用户使用的范围之内。
我们认为,只要通过事先的沟通和工艺试验,模具经过TD处理后可以不影响装配和使用。
影响模具TD过程中影响工件变形的因素很多,主要有:
1.设计:长径比、型腔结构;
2.材料:化学成分、轧制质量、纤维方向(棒材、板材、锻件)等;
3.热处理:TD前的热处理工艺和质量,特别是组织应力和热应力的消除情
况;
4.TD:工件的装夹及TD工艺控制。
三、工件在TD前的焊补
即便是发达的工业国家,模具的焊补也在所难免,也完全可行。
我们通过前期的技术沟通,焊补的模具也不会明显影响其使用性能。
模具焊补后容易出现的缺陷主要表现在:
1、焊点开裂;
2、模具变形超差
3、焊接部分不能做上TD覆层,整个工件的TD层不均匀。
我们建议对模具的焊补采取下列方法后,可以减少或规避缺陷模具焊补的缺陷:
1.焊接设备选用:依序选择直流焊、交流焊、氩弧焊;
2.焊接材料选用:Cr12MoV\SDK11\KD11S\DC53\D2\A2模具材料请选择日本东海
熔业TM-10B焊材和Trader公司的SKD11(这个牌号极有可能是针对中国市场特取名的)焊材;
3.焊接工艺:
1)对焊接部位打坡口,并确保其洁净;
2)工件用80 -120℃预热透保温2小时,直流焊、交流焊的焊条用 200℃保
温2小时。
如果现场不具备保温条件可用其他加热设备代替(氧气、乙炔等);
3)对焊接量较大的工件实行堆焊,堆焊时要确保焊渣清除干净,同时还
需用角磨机反复打毛焊接面后再焊。
一个焊接面尽量使用一支焊条,焊接过程中尽可能规避焊条接续;
4)对焊接好的工件用80 -120℃热透保温2小时后随炉冷却。
四、TD前仍然要对工件进行热处理的理由
TD其实就是一个完整的热处理过程。
不管TD前的工件的基体硬度有多高,在TD过程中都会有一个重新淬火的过程。
尽管如此,我们仍然建议客户在TD前应该给工件淬火或调质,其理由是:
1.消除组织应力和热应力,可以降低TD处理过程中的变形量;
2.可以保证工件磨削加工的光洁度;
3.有基体硬度可以支撑试模;
4.材料的锻造缺陷可及时发现;
5.降低物流中工件撞伤的几率。
五、工件在TD前可选择的热处理工艺
1.真空淬火;
2.中性盐浴炉;
3.普通井式电炉;
4.普通厢式电炉;
5.表面感应淬火;
6.表面激光淬火;
六、模具采用TD处理的刚性条件的建议
1.工作温度低于500℃的以磨损失效的冲压、挤压、拉拔、滚压模具;
2.被加工材料板厚超过1.4mm;
3.被加工材料屈服强度超过400Mpa;
4.产品的外观要求严格;
5.单一产量大于10万件。
另外一种是模具镀鉻,
板料厚度1.2mm以上的不适宜电镀。
一般以1.0mm及其以下的为宜。
电镀前模具处理:模具本体所用材质种类较多,但是,材质为Cr12MoV、
Cr12、SKD11、KD11S 的模具易出现电镀后开裂问题,须特别注意。
⏹主要修理项目:砂眼、开裂、压伤、板料表层在模具上的残留、拉毛/拉伤
焊条的选用:推荐使用:含Ni、Cr成分的焊条不适宜电镀
TM2000B
11CB
SUPER45
O172(深/浅)
UTP665
D517
韩国制62
锦州锦泰A103
⏹打磨修理工具的选用:油石,金刚锉、磨石
⏹模具附带部品的拆卸:导板
⏹定位销、定位块
⏹配管、配线
⏹氮气缸等
模具镀铬后的保养
⏹调试前的涂油保养
⏹生产过程中及结束后的表面清洁
A 异物、杂质的清理
B 板料表层残留的清理
⏹生产1个批次后的表面抛光
⏹电镀层的定期点检及再电镀
⏹调试前的微量涂油保养
电镀完成至上机调试前如果能够涂油并使其渗透24小时,模具表面润滑效果更佳。
但是,油脂不宜过多。
⏹生产过程中的表面清洁
第1次生产200~300件后,停机清洁模具表面
⏹生产结束后的表面清洁
A 异物、杂质的清理
⏹电镀层不可磕碰、压伤
⏹电镀层表面不可涂抹含腐蚀性的物质
⏹冲压车间的粉尘治理很重要
⏹电镀后板件褶皱会缩短镀层寿命,需要
重点关注并及时调整。
⏹电镀层的定期点检及再电镀
◇生产1万次以后,开始定期检查电镀
层并做好相应清洁工作。
◇生产3万次后,定期检查电镀层的磨
损情况,保证模具始终处于镀层的
保护之下。