价值流图析(下)
合集下载
价值流图析2

C/T=45S C/O=10min 使用率=80% 有效时间27600s 两班工作
C/T=62S C/O=0 使用率=100% 有效时间27600s 两班工作
C/T=40S C/O=0 使三、价值流图的绘制
第六步:绘制信息流,在图的上半部从右向左画
I
5天的 卷材
冲压 200T
I
4600左 2400右
点焊1#
1
I
1100左 600右
点焊2#
1
I
1600左 850右
装配1#
1
I
1200左 640右
装配2#
1
I
2700左 1440右
发运
平台
C/T=1S C/O=1h 使用率=85% 有效时间27600s 准备量2周
C/T=38S C/O=10min 使用率=100% 有效时间27600s 两班工作
6周 预测
生产控制部
MRP
90/60/30d 预测
每日订货
每周传真
每周计划
每日发 运计划
I
5天的 卷材
冲压
I
4600左 2400右
点焊1#
1
I
1100左 600右
点焊2# 1
I
1600左 850右
装配1# 1
I
1200左 640右
装配2#
1
I
2700左 1440右
发运 平台
200T
C/T=1S C/O=1h 使用率=85% 有效时间27600s 准备量2周
价值流图含有:
生产流(作业流程步骤
物 料
3
流
一、价值流图概念
3、价值流图作用
价值流图分析(PPT 59张)

价值流图分析
—查找和发现浪费的-mail:lgddyangwenku@
价值流图分析 VSM
目的
了解价值流分析的作用
掌握绘制价值流图的步骤 加深对精益思想的理解
价值流图分析 VSM
主要内容
第一部分 价值流分析基础知识 第二部分 价值流图的绘制步骤 第三部分 价值流分析的作用 作业
采用5W1H方法
1. Who——确定谁来做 需要一位了解产品价值流而且能推进其改进的人,这个人具有领导职责 (价值流经理),由他来领导一个小组进行价值流图析工作。 2. What——确定做哪些产品的价值流图析(正确选择确定物流) 通常我们首先按照80—20原则,对影响企业最大的产品进行图析。 3. When——确定何时做(正确选择确定物流) 应在实施改进之前对价值流进行分析,以确定应首先改进哪些过程。 4. Where——确定在哪里做(如何获取真实、正确的数据信息) 在现场!只有在现场收集的数据才能真正反映价值流的状况。 5.Why—为什么做价值流图析 明确价值,消除浪费 6、 How ——进行图析
价值流图分析 VSM
价值流图基本概述
价值流图分析 VSM
价值流图基本概述
价值流图与流程图区别
价值流图: • 让所有人看见整体 情况 • 根据真实数据 • 改善蓝图 • 持续改善 流程图: • 只能反映局部工艺 周期、流程 • 根据工程标准或旧 数据 • 一年一次的大计划
价值流图分析 VSM
价值流图析步骤
(以前的认识是我们创造了产品的价值,并且由此确定了其价值。)
总之,永远站在客户立场上看待我们的工作价 值。谁对我们的工作进行最终评判和衡量,谁就是 我们的客户。 客户—我们从事一切生产经营活动并进行改善的最根本的出发点和落脚点
—查找和发现浪费的-mail:lgddyangwenku@
价值流图分析 VSM
目的
了解价值流分析的作用
掌握绘制价值流图的步骤 加深对精益思想的理解
价值流图分析 VSM
主要内容
第一部分 价值流分析基础知识 第二部分 价值流图的绘制步骤 第三部分 价值流分析的作用 作业
采用5W1H方法
1. Who——确定谁来做 需要一位了解产品价值流而且能推进其改进的人,这个人具有领导职责 (价值流经理),由他来领导一个小组进行价值流图析工作。 2. What——确定做哪些产品的价值流图析(正确选择确定物流) 通常我们首先按照80—20原则,对影响企业最大的产品进行图析。 3. When——确定何时做(正确选择确定物流) 应在实施改进之前对价值流进行分析,以确定应首先改进哪些过程。 4. Where——确定在哪里做(如何获取真实、正确的数据信息) 在现场!只有在现场收集的数据才能真正反映价值流的状况。 5.Why—为什么做价值流图析 明确价值,消除浪费 6、 How ——进行图析
价值流图分析 VSM
价值流图基本概述
价值流图分析 VSM
价值流图基本概述
价值流图与流程图区别
价值流图: • 让所有人看见整体 情况 • 根据真实数据 • 改善蓝图 • 持续改善 流程图: • 只能反映局部工艺 周期、流程 • 根据工程标准或旧 数据 • 一年一次的大计划
价值流图分析 VSM
价值流图析步骤
(以前的认识是我们创造了产品的价值,并且由此确定了其价值。)
总之,永远站在客户立场上看待我们的工作价 值。谁对我们的工作进行最终评判和衡量,谁就是 我们的客户。 客户—我们从事一切生产经营活动并进行改善的最根本的出发点和落脚点
价值流图析
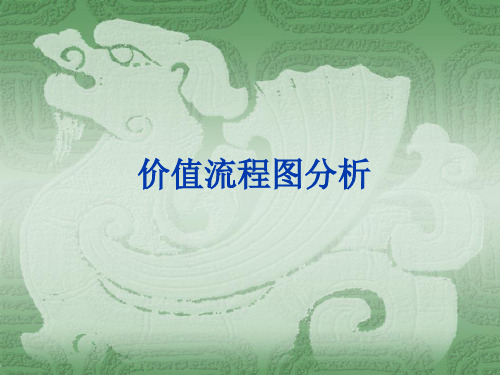
价值流图析
何谓价值流图析 例图
价值流图析
主要特点:
针对全局的流 而非 局部的流。 帮助你发现更多的浪费及其根源。 为改进提供共同的工具和平台。 帮助准确判断问题并得出严谨的结论。 将精益与技术结合起来。 为实现精益绘制蓝图。 显示材料流与信息流的联系。 可以很好的揭示目前所要做的事情。
价值流图析
价值流图析—怎样精益
重要的精益流的原则和准则。 准则3: 在连续流动无法向上游扩展处,使用看板或
超市控制生产。
价值流图析—怎样精益
重要的精益流的原则和准则。 准则3: 在连续流动无法向上游扩展处,使用看板或
超市控制生产。
由于以下原因而造成不能连续流动的点: 1. 过快或过慢的工序 2. 距离远运输不便;如供应商送货 3. 有些制造周期太长,以一个连续流动直接与其他
价值流图析—未来状态图
价值流图析—未来状态图
未来状态的关键问题1:需求
(1) 基于距离顾客最近的下游过程的有效时间节拍时间是什么? (2) 你是按照顾客的拉动还是直接按发送建立一个成品超市?
关键问题2:物流
(3) 在哪里可以使用连续流动过程? (4) 为了控制上游过程的生产你需要在哪里使用超市拉动系统?
通常定调增量介于5~60分钟之间。
价值流图析—怎样精益
重要的精益流的原则和准则。 准则6: 在定拍过程上游过程培养“每天制造各种零
件”的能力。
通过减少换型时间和在上游过程运用小批量,对下游 需求的变化反应会更快,因而他们超市中要求持 有的存货会更少。
价值流图析—未来状态图
绘制未来状态图 自己动手
价值流程图分析
目的及意义
本次培训将介绍价值流的概念,并以具体的 实例来说明价值流程图的绘制方法和流程图 分析的方法及实现价值流增值的基础原理与 方法!
《价值流图分析》PPT课件

编辑ppt
24
目 录
价值流简介 价值流与精益生产
价值流增值比
价值流改善提升方法
价值流增值比计算
VSM假设前提
VSM假设前提: 产品是先进先出, 连续生产。
VSM增值比
VSM增值比,就 是计算一个产品从 材料进公司开始, 到包装出货,在各 个制程所等待被加 工的时间和被加工 的时间的比值。
VSM增值比计算
准则1:按顾客节拍生产
准则2:尽可能地实现连续流动
准则3:在无法实现连续流动的地方采用广告 牌拉动管理
编辑ppt
33
设计并实施精益的未来价值流的准 则
• 准则4:努力使得顾客的订单只发到一个过程
• 准则5:在价值流启动过程按时间均匀分配多 品种产品的生产
• 准则6:在价值流启动过程通过启动一个单位 的工作来实现初始拉动
270
0.07天
周期时间 =8.99秒 制程=4.25分 转换时间 =20分钟 可利用时间 =1130分 正常运行时 间=98%
4.25分
成品仓
订货提前期=4.18天 价值增加时间=31.87分 价值增加比=1.3%
0天
汽车行业价值流
价值流未来状态图
编辑ppt
19
价值流简介 价值流与精益生产
价值流增值比 价值流改善提升方法
例:假设你排队参观某个风景点,该风景点固定的容纳人数是:60人。每个人 在该风景点停留的平均时间是:3分钟。假设在你的前面还排有20个人,问:你估 计你大概等多少时间才能进入该风景点。
答案:1小时(3×20=60)
编辑ppt
29
VSM计算举例
布
什 10人
挂号 挂号
3人
《价值流图析下》课件
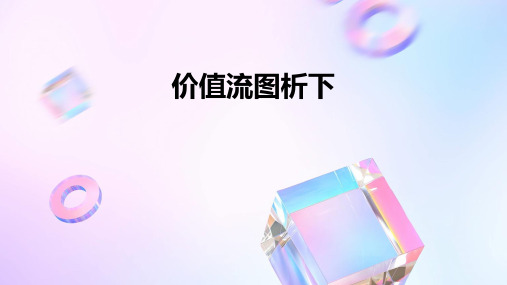
随着对可持续发展的关注度不断提高 ,价值流图析将更加注重环境、社会 和经济效益的综合优化。
如何不断提升价值流图析的能力与效果
持续学习与培训
通过参加培训课程、阅读专业文 献等方式,不断更新知识和技能 ,保持对最新理论和实践的掌握 。
实践经验积累
通过不断实践和总结,积累丰富 的价值流图析经验,提高实际操 作和分析能力。
04
价值流持续改进
持续改进的策略与方法
目标明确
数据驱动
明确持续改进的目标,确保改进活动始终 围绕核心问题展开。
利用数据和信息来指导改进,通过数据分 析和可视化工具来评估流程绩效。
跨部门协作
创新思维
鼓励不同部门之间的协作,打破组织壁垒 ,共同推动改进。
鼓励员工提出创新性的改进想法,不断探 索新的方法和解决方案。
现状图的分析与解读
识别瓶颈
分析流程图,找出可能制约产量的工艺步骤或资源瓶 颈。
对比标准
将现状图中的数据与行业标准或最佳实践进行对比, 找出差距。
解读问题
根据瓶颈和差距,解读出产品族在价值流中存在的问 题和不足。
现状图中发现的问题与改进点
问题1
部分工艺步骤过于复杂,导致时 间成本较高。
改进点
优化工艺步骤,简化操作过程, 提高效率。
跨部门合作与沟通
加强与其他部门的合作与沟通, 了解业务需求和流程,提高分析 结果的实际应用价值。
感谢您的观看
THANKS
3
服务业
价值流图析在服务业中用于识别和改进服务流程 中的低效环节,提升客户体验和忠诚度。
价值流图析的发展趋势与未来展望
数字化转型
随着数字化技术的不断发展,价值流 图析将更加依赖于数据分析和可视化 工具,以提供更准确和实时的分析结 果。
价值流图分析步骤课件

繪製現狀圖
最新版整理ppt
1
本單元目標
• 理解基本概念 • 繪製現狀圖
最新版整理ppt
2
簡介
價值溪流分析在著手進行改善活動時是一個有效 的工具。本工具提供了全盤鳥瞰現行生產運作 狀況的視野, 點出侷限和應予思考之處。它提 供了一個系統面的途徑, 有助於界定需要注意 和發展工作計畫的地方。
最新版整理ppt
FIFO
下一工序後拉物料
_ hour
制成品對顧客端的移動
庫存的墓碑
__pcs __day
卡車送貨
__/wk
最新版整理ppt
19
手工資訊流
電子資訊流 生管派工單
每週
連續派工單
所用的圖示 (續)
超市
A B C
生產指示卡
物料回撤卡
生產信號卡 生產流向 指出生產指示卡之途徑
指出物料回撤卡之途徑
最新版整理ppt
最新版整理ppt
5
現狀圖範例
生管
每週
每日生管派工
客戶
R.M W/H
Lamination
Airbag washing
Lead Time Quality R Down Time
Material Mixing
Lead Time Quality R Down Time
3.5 days
25 sec 4.5 days
PU Spray
Lead Time Quality R Down Time
Stockfit Assembly
Lead Time Quality R Down Time
F.G W/H
Material Mixing
Lead Time Quality R Down Time
最新版整理ppt
1
本單元目標
• 理解基本概念 • 繪製現狀圖
最新版整理ppt
2
簡介
價值溪流分析在著手進行改善活動時是一個有效 的工具。本工具提供了全盤鳥瞰現行生產運作 狀況的視野, 點出侷限和應予思考之處。它提 供了一個系統面的途徑, 有助於界定需要注意 和發展工作計畫的地方。
最新版整理ppt
FIFO
下一工序後拉物料
_ hour
制成品對顧客端的移動
庫存的墓碑
__pcs __day
卡車送貨
__/wk
最新版整理ppt
19
手工資訊流
電子資訊流 生管派工單
每週
連續派工單
所用的圖示 (續)
超市
A B C
生產指示卡
物料回撤卡
生產信號卡 生產流向 指出生產指示卡之途徑
指出物料回撤卡之途徑
最新版整理ppt
最新版整理ppt
5
現狀圖範例
生管
每週
每日生管派工
客戶
R.M W/H
Lamination
Airbag washing
Lead Time Quality R Down Time
Material Mixing
Lead Time Quality R Down Time
3.5 days
25 sec 4.5 days
PU Spray
Lead Time Quality R Down Time
Stockfit Assembly
Lead Time Quality R Down Time
F.G W/H
Material Mixing
Lead Time Quality R Down Time
价值流分析图课件

什么是价值流?
一个产品通过其基本生产过程所要求的全部活动(包括增加价值的活动和不增加价值的活动): 1)、 从原材料,到产品交到顾客手中的生产流程 2) 、从概念到正式投产的产品设计流程 3) 、从客户订单到工作指令的订单执行流程
什么是价值流图析?
从用户到供应商,跟踪产品的生产路径,在材料和信息流当中,用便于看清的图标,仔细画出每个过程,然后询问一组关键问题,描绘出价值流的“当前状态图”。然后要画出一个我们希望的价值流的“未来状态图”。价值流图析是使用铅笔和纸张,来帮助你看到、和理解生产过程在整个价值流中的材料、信息流动的情况。
研制实现“未来状态”的计划并且实施
价值流程图使用流程图
绘制当前VSM
划定价值流环
选定改善的价值流环
确定改善目标,制定改善内容和计划
绘制目标VSM
改善执行
绘制改善后VSM
价值流图基本结构
关键: 前后一致
绘图图标
物流图标
通用图标
信息图标
外部资源
XYZCorporation
绘制当前状态价值流图- (1)
节拍 TAKT
1
2
6
3
4
5
10
11
为适应客户的需求,而进行的连续性生产中完成两个产品之间的时间长度。如果能确切的知道某段时间里客户需求状况,则节拍时间就能够按下面的公式设定: __每天有效的工作时间__ 每天客户需求产品数节拍时间确定了每一工位必须完成工作的速率(操作周期时间)。
绘图图标
物流图标
通用图标
信息图标
外部资源
XYZCorporation
为什么要绘制价值流?
超越单个工艺过程层次而建立宏观整个生产流程的能力;帮助发现浪费,以及浪费源;展示了信息流与物流之间的联系;提供一个与各级沟通的工具;根据流动障碍确定改善的优先次序;使精益的概念与技术结合起来,帮助避免只挑容易的来改进;形成实施计划的基础;描绘为了影响这些定量的数据,实际应该做些什么;通过绘制价值流图,能学习以精益生产的角度来分析生产过程。
一个产品通过其基本生产过程所要求的全部活动(包括增加价值的活动和不增加价值的活动): 1)、 从原材料,到产品交到顾客手中的生产流程 2) 、从概念到正式投产的产品设计流程 3) 、从客户订单到工作指令的订单执行流程
什么是价值流图析?
从用户到供应商,跟踪产品的生产路径,在材料和信息流当中,用便于看清的图标,仔细画出每个过程,然后询问一组关键问题,描绘出价值流的“当前状态图”。然后要画出一个我们希望的价值流的“未来状态图”。价值流图析是使用铅笔和纸张,来帮助你看到、和理解生产过程在整个价值流中的材料、信息流动的情况。
研制实现“未来状态”的计划并且实施
价值流程图使用流程图
绘制当前VSM
划定价值流环
选定改善的价值流环
确定改善目标,制定改善内容和计划
绘制目标VSM
改善执行
绘制改善后VSM
价值流图基本结构
关键: 前后一致
绘图图标
物流图标
通用图标
信息图标
外部资源
XYZCorporation
绘制当前状态价值流图- (1)
节拍 TAKT
1
2
6
3
4
5
10
11
为适应客户的需求,而进行的连续性生产中完成两个产品之间的时间长度。如果能确切的知道某段时间里客户需求状况,则节拍时间就能够按下面的公式设定: __每天有效的工作时间__ 每天客户需求产品数节拍时间确定了每一工位必须完成工作的速率(操作周期时间)。
绘图图标
物流图标
通用图标
信息图标
外部资源
XYZCorporation
为什么要绘制价值流?
超越单个工艺过程层次而建立宏观整个生产流程的能力;帮助发现浪费,以及浪费源;展示了信息流与物流之间的联系;提供一个与各级沟通的工具;根据流动障碍确定改善的优先次序;使精益的概念与技术结合起来,帮助避免只挑容易的来改进;形成实施计划的基础;描绘为了影响这些定量的数据,实际应该做些什么;通过绘制价值流图,能学习以精益生产的角度来分析生产过程。
价值流图析
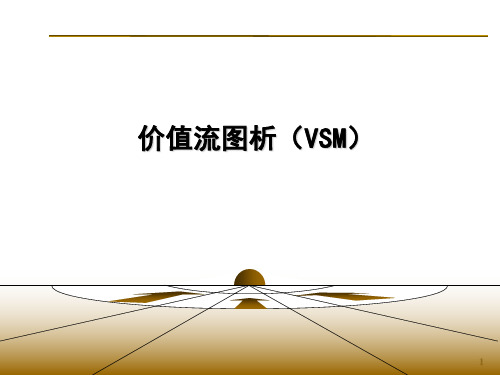
目的:勾勒物料的信息在整个生产和发货的增值过程中的流通。
1.价值流图的目的是突出浪费之源,并通过实行一个短期内可实现的未来状态的价值流来消除 它们。 2.目标是将单个过程与其顾客通过连续流动或拉动联系起来,建立一个生产链,并且每个过程 尽可能接近仅在顾客需要时按顾客要求的量生产。
15
四、价值流图的目的、特点和作用
在制品
WIP Store
I
P/N Q D/S 123 10 2.5 456 5 2.5
1
C/T = 14 sec C/O = 0 sec Uptime=100%
28,776 sec avail
1
1
冲压Press
I
P/N B C D E F Q 20 20 20 20 20
喷涂Paint
I
P/N B C D E F Q 13 13 9 5 5
C. 流动(Flow) 精益思想要求创造价值的各个活动 (步骤)流动起来,强调的是“动”。 传统观念是“分工和大量才能高效 率”,但是精益思想却认为成批、大
批量生产经常意味着等待和停滞。精 益将所有的停滞作为企业的浪费,消
灭一切的浪费。 精益思想强调分批、单件流、同步化、 均衡化生产等。
8
一、价值流图的产生背景
18
五、价值流图编制步骤——行动准备
价值流改进
材料流/信息 流是改进重 点
注意: 流程改进(价值流改善)和工序层次的改进都是公司所需要的,一方面 的改进同时也提高另一方面的改进。 价值流的改进重点在于物料流和信息流(需要从高的角度才能看到), 而流程改进则重点在于人和流程的流动。
19
五、价值流图编制步骤——行动准备
主要工作职责: 1 向现场最高管理者报告
- 1、下载文档前请自行甄别文档内容的完整性,平台不提供额外的编辑、内容补充、找答案等附加服务。
- 2、"仅部分预览"的文档,不可在线预览部分如存在完整性等问题,可反馈申请退款(可完整预览的文档不适用该条件!)。
- 3、如文档侵犯您的权益,请联系客服反馈,我们会尽快为您处理(人工客服工作时间:9:00-18:30)。
18
Date 2008/02/15
下面的情况下,精益流会怎么样
…如果一个设备停机了 …如果在好的产品里混有一个次品
装配厂
装配工序
2级供应商 1级供应商
焊接
冲压
Version I
19
Date 2008/02/15
定拍工序有节奏地生产和提取
• 计划在定拍工序生产和提取的数量 • 这个批量= “管理时间框架” • 传递一种明确的“节拍感”?
•
在定拍工序,准备如何混合生产不同的产品?
Pitch:单位提 取批量和时间
• 在定拍工序,生产计划和提取成品的单位量是多少?
• 哪些工序的改进是必须的?
(比如:开机率,切换时间,人员培训)
改善
Version I
22
Date 2008/02/15
未来状态的一些图标
Version I
23
Date 2008/02/15
Whiteboard 4-6
节拍时间=460分钟/460件=60秒 单位提取时间=60秒*20件=20分钟
2天
Version I
34
Date 2008/02/15
Whiteboard 4-7
Whiteboard 4-2
节拍时间=460分钟/460件=60秒 单位提取时间=60秒*20件=20分钟
Version I
27
Date 2008/02/15
Whiteboard 4-3
节拍时间=460分钟/460件=60秒 单位提取时间=60秒*20件=20分钟
Version I
28
Date 2008/02/15
工序(上游工序)的生产
Version I
14
Date 2008/02/15
尝试只在一点控制生产排程
计划排产
计划排产
Version I
15
Date 2008/02/15
超市拉动系统
1)顾客(下游工序)在需要的时候到超市提取需要的产品 2)供应(上游工序)生产以补充从超市中提取的产品
较长的换模时间、 停机时间和距离
4
3个操作员
(目标)
Version I
31
Date 2008/02/15
Flipchart4-5
Version I
32
Date 2008/02/15
Whiteboard 4-5
节拍时间=460分钟/460件=60秒 单位提取时间=60秒*20件=20分钟
Version I
33
Date 2008/02/15
=节拍时间×一个包装的数量
Version I
20
Date 2008/02/15
第3章 测验
未来状态的关键问题
• 节拍时间是什么?
• 准备成品库存超市,还是生产后直接交付运输?
• 什么地方可以采用连续流?
• 什么地方需要采用库存超市来控制上游生产?
• 在生产链中的哪一点是定拍工序,可以计划安排生产?
价值流图析
精益企业中国
未来状态图绘制
设计一个精益流 •价值流图析的长处就在于你总是需要一 个未来状态 •不要奢求一步就能达到完美的境界,只 要每次能改进一点就已经很好了 •用铅笔来画图 •物料流与信息流
•这是改进计划的基础,就像一张“蓝图” •从绘制现状图开始 •第一步使用现有的加工步骤和设备 •可以移动设备、花少量钱添置一些设备、 搬走传送带等。
Whiteboard 4-1
节拍时间=460分钟/460件=60秒 单位提取时间=60秒*20件=20分钟
Version I
24
Date 2008/02/15
Flipchart4-1
Version I
25
Date 2008/02/15
Flipchart4-2
Version I
26
Date 2008/02/15
流动
面对一段一段的流动,我们能如何控制生产? 依靠基于MRP的生产排程吗?
Version I
13
Date 2008/02/15
超市拉动系统
1)顾客(下游工序)在需要的时候到超市提取需要的产品 2)供应(上游工序)生产以补充从超市中提取的产品
A B C D
a、一种针对分段流动进行生产控制的方法 b、不需要给出生产排程单,就可以控制供应
Version I
2
Date 2008/02/15
大批量生产方式
计划排产
计划排产 计划排产
Version I
3
Date 2008/02/15
浪费
• 生产过程中不为产品增加价值的部分 • 浪费只增加成本和时间
关于浪费要记住的事:
• 浪费实际上是问题的表面,而不是根本原因 • 浪费表明系统内存在的问题(在工序和价值流层面都有) • 我们需要发现和解决浪费的根本原因
Version I
4
Date 2008/02/15
过量生产
=生产的比下一个工序需要的多 =生产的比下一个工序需要的早 =生产的比下一个工序需要的快
A
B
Version I
5
Date 2008/02/15
局部效率与系统效率
我们应该生产得多快?
Version I
6
Date 2008/02/15
节拍时间
Flipchart4-3
Version I
29
Date 2008/02/15
Whiteboard 4-4
节拍时间=460分钟/460件=60秒 单位提取时间=60秒*20件=20分钟
Version I
30
Date 2008/02/15
Flipchart4-4
187秒总工作量 60秒的节拍时间
3.1个操作员
A 峰值 需求
B
较低的 峰值
顾客
成品
Version I Date 2008/02/15
顾客
10
连续流加工
Version I
11
Date 2008/02/15
连续流加工
3分钟 12分钟
Version I
12
Date 2008/02/15
流动中的问题点
任何单件流不能继续的地方
计划排产
计划排产
计划排产
节拍时间
每班的有效工作时间
每班的顾客需求量
27600 秒
60 秒
460 件
Version I
7
Date 2008/02/15
Flipchart3-1
Version I
8
Date 2008/02/15
设立库存超市还是按直接发送来安排生产
Version I
9
Date 2008/02/15
Flipchart3-2
• 分类型进行批量加工 • 数量波动
a、一种针对分段流动进行生产控制的方法
b、不需要给出生产排成单,就可以控制供应
(上游工序)的生产
Version I
16
Date 2008/02/15
尝试只在一点控制生产பைடு நூலகம்程
定拍工序
Version I
17
Date 2008/02/15
在定拍工序进行混合生产
Version I