球墨铸铁件的缺陷和金相检验2012年
球墨铸铁件产生缺陷的原因有哪些?

球墨铸铁件产生缺陷的原因有哪些?球墨铸铁件产生缺陷的原因不单是球化处理问题,那么还有什么问题?在球墨铸铁件生产中,常见的铸件缺陷除有灰铸铁件的一般缺陷外,还有球化不良、球化衰退、夹渣、缩松、石墨漂浮、皮下气孔等。
通常,产生这些缺陷的原因不单是球化处理问题,有时还有造型制芯、熔炼浇注、配砂质量、落砂清理等许多生产工序的问题,因此必须具体分析。
以便采取相应的合理措施加以解决。
(1)球化不良特征:在铸件或试棒断面上分布有明显可见的小黑点,愈往中心愈密。
金相组织中.有聚集分布的厚片状石墨原因分析:1.原铁液硫含量过高2.铁液氧化3.残余球化剂量不足4反球化元素的干扰防止方法:1.尽量选用低硫的焦炭和新生铁。
若原铁液含硫量过高,应采用炉内、炉外脱硫或相应提高球化剂的加入量。
交界铁液一定要分离干净,灰铸铁的铁掖不应混入球墨铸铁中。
球化处理时,防止炉渣出到浇包中2.操作中严防铁液氧化3.熔制配比适当、成分稳定的中间合金,并采用合适的处理温度,注意球化处理操作。
防止铁液与合金作用过分激烈或“结死”在包底4镁球墨铸铁中。
加人少量的稀土,可中和反球化元素的干扰(2)球化衰退特征:球墨铸铁铁液,停留一定时间后,球化效果会消失原因分析: 铁液的残余镁量和残余稀土量随着时间的延长会逐渐减少,过了一定时间后。
球化剂残余量已减少到不足以保证铸件球化时,就造成球化衰退镁量和稀土量逐渐减少的原因是:1. 在铁液表面的MgS、CeS与空气中氧作用,发生下列反应:2MgS+O2=2MgO气↑+2S2CeS+ O2=2CeO气+2S烟状的MgO和CeO在空气中逸损,S返回铁液与Mg、Ce作用又生成MgS、CeS,这样循环,Mg、Ce不断损失2.镁在铁液中溶解度极小,大部分镁以微小的气泡悬浮在铁液中。
当有搅拌、回包、浇注、机械振动等情况时,镁气泡会集聚上浮,并穿出铁液表面。
遇空气燃浇而损失3.镁、稀土与氧有极大的亲和力。
铁液表面的镁和稀土要逐渐氧化、镁还有蒸发损失等防止方法:1.经球化处理的铁液应有足够的球化剂残余量2.降低原铁液硫含量,并防止铁液氧化3.球化处理后应扒净渣子4.缩短铁液经球化处理后的停留时间5.在铁液表面加覆盖熔剂,如石墨粉、木炭粉、冰晶石粉等(3)夹渣(黑渣)特征: 在铸件断面上呈现暗黑色,没有光泽,主要由琉化镁、硫化锰、氧化镁、二氧化硅、氧化铁、氢化镁等所组成,是一种非金属夹杂物,可用硫印、氧印等方法显示出来。
球墨铸铁常见缺陷的分析与对策
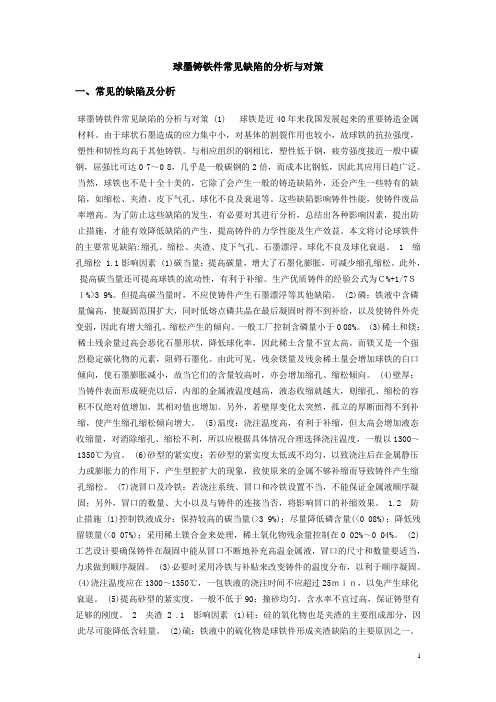
球墨铸铁件常见缺陷的分析与对策一、常见的缺陷及分析球墨铸铁件常见缺陷的分析与对策 (1) 球铁是近40年来我国发展起来的重要铸造金属材料。
由于球状石墨造成的应力集中小,对基体的割裂作用也较小,故球铁的抗拉强度,塑性和韧性均高于其他铸铁。
与相应组织的钢相比,塑性低于钢,疲劳强度接近一般中碳钢,屈强比可达0 7~0 8,几乎是一般碳钢的2倍,而成本比钢低,因此其应用日趋广泛。
当然,球铁也不是十全十美的,它除了会产生一般的铸造缺陷外,还会产生一些特有的缺陷,如缩松、夹渣、皮下气孔、球化不良及衰退等。
这些缺陷影响铸件性能,使铸件废品率增高。
为了防止这些缺陷的发生,有必要对其进行分析,总结出各种影响因素,提出防止措施,才能有效降低缺陷的产生,提高铸件的力学性能及生产效益。
本文将讨论球铁件的主要常见缺陷:缩孔、缩松、夹渣、皮下气孔、石墨漂浮、球化不良及球化衰退。
1 缩孔缩松 1.1影响因素 (1)碳当量:提高碳量,增大了石墨化膨胀,可减少缩孔缩松。
此外,提高碳当量还可提高球铁的流动性,有利于补缩。
生产优质铸件的经验公式为C%+1/7Si%>3 9%。
但提高碳当量时,不应使铸件产生石墨漂浮等其他缺陷。
(2)磷:铁液中含磷量偏高,使凝固范围扩大,同时低熔点磷共晶在最后凝固时得不到补给,以及使铸件外壳变弱,因此有增大缩孔、缩松产生的倾向。
一般工厂控制含磷量小于0 08%。
(3)稀土和镁:稀土残余量过高会恶化石墨形状,降低球化率,因此稀土含量不宜太高。
而镁又是一个强烈稳定碳化物的元素,阻碍石墨化。
由此可见,残余镁量及残余稀土量会增加球铁的白口倾向,使石墨膨胀减小,故当它们的含量较高时,亦会增加缩孔、缩松倾向。
(4)壁厚:当铸件表面形成硬壳以后,内部的金属液温度越高,液态收缩就越大,则缩孔、缩松的容积不仅绝对值增加,其相对值也增加。
另外,若壁厚变化太突然,孤立的厚断面得不到补缩,使产生缩孔缩松倾向增大。
球墨铸铁金相试样制备中的常见缺陷及其原因分析
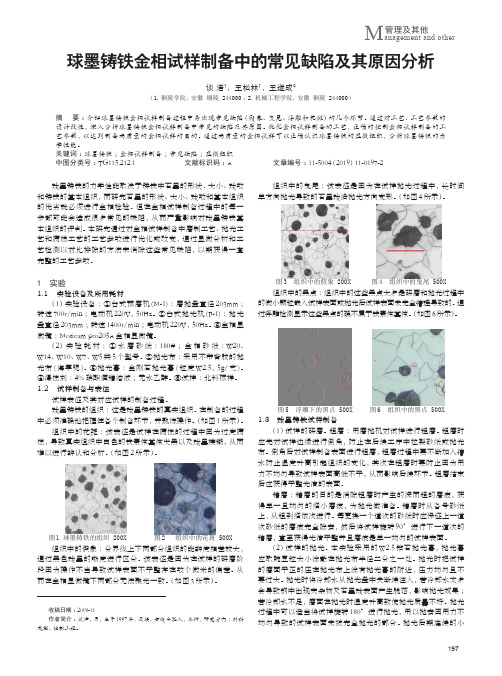
球墨铸铁金相试样制备中的常见缺陷及其原因分析
谈 浩¹,王松林¹,王继成²
(1. 铜陵学院,安徽 铜陵 244000 ;2. 机械工程学院,安徽 铜陵 244000)
摘 要 :介绍球墨铸铁金相试样制备过程中易出现常见缺陷(假象、曳尾、浮雕和花斑)的几个环节。通过对工艺、工艺参数的
收稿日期 :2019-11 作者简介 :谈浩,男,生于 19ห้องสมุดไป่ตู้7 年,汉族,安徽合肥人,本科,研究方向 :材料 成型、控制工程。
组织中的曳尾 :该表征是因为在试样抛光过程中,长时间 单方向抛光导致的石墨球沿抛光方向变形。(如图 4 所示)。
图 3 组织中的假象 200X 图 4 组织中的曳尾 500X 组织中的黑点 :组织中的这些黑点大多是研磨和抛光过程中 的微小颗粒嵌入试样表面或抛光后试样表面未完全清理导致的。通 过浮雕检测显示这些黑点的确不属于铁素体基体。(如图 6 所示)。
2 结果及讨论 2.1 球墨铸铁试样制备中常见的缺陷及应对措施
文献标识码 :A
文章编号 :11-5004(2019)11-0197-2
球墨铸铁的力学性能取决于铸铁中石墨的形状、大小、球数 和铸铁的基本组织,而研究石墨的形状、大小、球数和基本组织 的优劣就必须进行金相检验。但在金相试样制备过程中的每一 步都可能会造成很多常见的缺陷,从而严重影响对球墨铸铁基 本组织的评判。本研究通过对金相试样制备中磨制工艺、抛光工 艺和腐蚀工艺的工艺参数进行优化或改变,通过显微分析和工 艺检测以对比排除的方法来消除这些常见缺陷,以期获得一套 完整的工艺参数。
试样表征及其对应试样的制备过程。 球墨铸铁的组织 :这是球墨铸铁的真实组织。在制备的过程 中必须准确地把握住各个制备环节,并熟练操作。(如图 1 所示)。 组织中的花斑 :该表征是试样在腐蚀的过程中因为过度腐 蚀,导致真实组织中白色的铁素体基体发黑以及球墨模糊,从而 难以进行辨认和分析。(如图 2 所示)。
球墨铸铁件的缺陷和金相检验2012年

发挥。
共四十五页
球墨铸铁 的特性 (qiúmò-zhùtiě)
球墨铸铁可以像钢一样,通过热处理和 合金等措施来进一步提高其使用性能。比如, 处理过的球墨铸铁可以取得很好的韧性,延 伸率高达24%;抗拉强度可以高达1400MPa, 基本接近钢材(gāngcái),与钢材(gāngcái)相比,球墨 铸铁还有很多优点。比如铸造性能好,成本 相对较低。
60-70
球化分级
(f
6级
石墨呈聚集分布的蠕虫状、片状及球 状、团状、团絮状
小于60%
ē 共四十五页
石墨 大小 (shímò)
球墨铸铁石墨球的大小对力学性能的影 响很大,减小石墨球径,增加石墨球在单 位面积的个数可以明显地提高球墨铸铁的 强度、塑性和韧性。
石墨球径的减小,使单位面积上球墨铸铁数 量增多,可使抗疲劳强度提高,因此(yīncǐ),细 化石墨也是提高抗疲劳强度的一个要求。
因此,对球墨铸铁的金相研究,是我们了解球墨铸 铁,使用球墨铸铁的前提条件。
共四十五页
球状石墨 的形成 (shímò)
球状石墨的形成经历了形核与生长两个阶段。其 中的形核是石墨的首要过程,铁液在熔炼及随后的 球化、孕育处理中产生大量的非金属夹杂物,初生 的夹杂物非常小,在随后浇铸、充型、凝固过程相 互碰撞、聚合(jùhé)变大,上浮或下沉,成为石墨析 出的核心。
于焦炭含量较高等熔炼条件的限制,往往达不到这一标 准,应进一步改善熔炼条件,有条件可进行炉外脱硫, 一般要求小于0.06%。
共四十五页
典型缺陷(quēxiàn)——球化不良
球化不良和球化退化
特征:断口银灰色,分布(fēnbù)芝麻状黑 斑点。金相组织分布(fēnbù)大量厚片石墨。
关于球铁件的检验
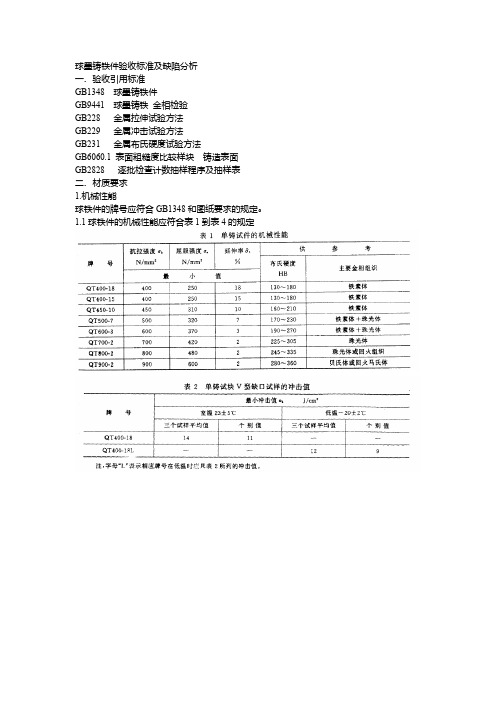
球墨铸铁件验收标准及缺陷分析一.验收引用标准GB1348 球墨铸铁件GB9441 球墨铸铁金相检验GB228 金属拉伸试验方法GB229 金属冲击试验方法GB231 金属布氏硬度试验方法GB6060.1 表面粗糙度比较样块铸造表面GB2828 逐批检查计数抽样程序及抽样表二.材质要求1.机械性能球铁件的牌号应符合GB1348和图纸要求的规定。
1.1球铁件的机械性能应符合表1到表4的规定1.2球铁件的机械性能以抗拉强度和延伸率两个指标为验收依据。
1.3须做屈服强度、冲击韧性和硬度试验时,应在图样上或在有关的技术文件中注明。
其数值应符合本标准的规定。
2. 金相组织2.1 金相组织标准按GB9441-88《球墨铸铁金相检验》2.2球化分级 (jia )铸件毛坯本体的球化率在70%以上,球化级别80%为1-3级,最差部位原则上不低于4级2.3.石墨等级原则上球径为5-7级。
2.4 基体组织(参考)3 .化学成分原则上化学成分不作为验收依据,客户明确要求的除外。
球铁体的化学成分、金相组织及热处理工艺应符合图样或技术文件中的注明。
三.几何形状与尺寸球铁件的几何形状与尺寸应符合图样中的规定要求。
1.尺寸公差1.1本标准规定的尺寸公差,是指球铁件在正常生产情况下应达到的公差。
1.2球铁件的尺寸公差数值应符合表5的规定;公差等级按表6的规定选取。
现我公司球铁件主要用户的公差等级一般为CT9级2.其他尺寸要求铸件应符合相应的毛坯图尺寸规定。
铸件错型≤1.0mm,砂芯歪斜量≤1.5mm。
四..表面质量1 .铸件毛坯表面应无粘砂、氧化皮等缺陷,铸件毛坯表面的浇冒口、出气孔、多肉、飞边、毛刺等清除干净。
加工面浇冒口残余不大于1mm。
其余原则上不大于2 mm2. 铸件毛坯不允许有裂纹、缩孔、疏松、冷隔等影响使用性能的铸造缺陷。
3铸造毛坯非加工表面粗糙度Ra≤100粗糙度评定按GB6060.1-85的规定进行。
4 铸造毛坯不允许有锈蚀。
球墨铸铁金相缺陷分析
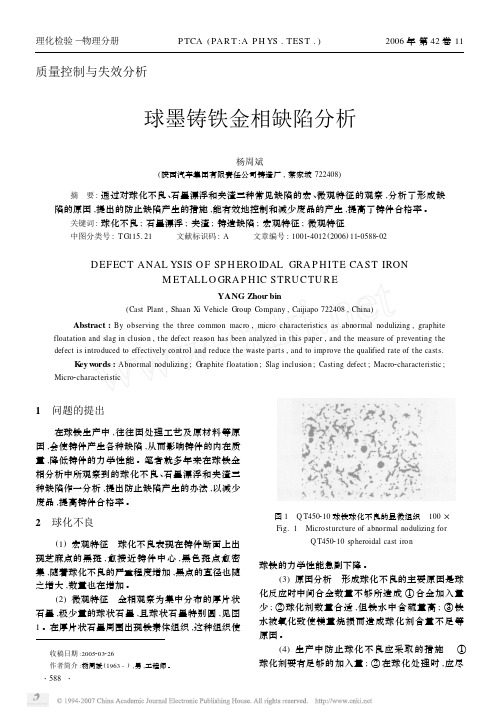
图 3 Q T450210 球铁中的夹渣 100 × Fig. 3 Included slage of Q T450210 sp heroidal cast iron
在球铁生产中 ,往往因处理工艺及原材料等原 因 ,会使铸件产生各种缺陷 ,从而影响铸件的内在质 量 ,降低铸件的力学性能 。笔者就多年来在球铁金 相分析中所观察到的球化不良 、石墨漂浮和夹渣三 种缺陷作一分析 ,提出防止缺陷产生的办法 ,以减少 废品 ,提高铸件合格率 。
2 球化不良
(1) 宏观特征 球化不良表现在铸件断面上出 现芝麻点的黑斑 ,愈接近铸件中心 ,黑色斑点愈密 集 ,随着球化不良的严重程度增加 ,黑点的直径也随 之增大 ,数量也在增加 。
Key words : Abnormal nodulizing ; Grap hite floatatio n ; Slag inclusion ; Casting defect ; Macro2characteristic ; Mic ro2c ha ract e ri st ic
1 问题的提出
(2) 微观特征 其石墨聚集 ,呈开花状和枝荔 状 ,有的完全爆裂 ,见图 2 。这种组织严重削弱了球 铁的力学性能 ,使材料的强韧性指标明显下降 。
4 夹渣
(1) 宏观特征 夹渣分布于铸件上表面及铸件 的死角处 ,夹渣在断面上呈断续的暗黑色区域或斑 点 ,无金属光泽 。
(2) 微观特征 有硫化物 ( MgS , FeS) 及氧化 物 (MgO ,SiO2 , FeO ,Al2 O3 ) ,在夹渣区除有球状石 墨外 ,还有类片状石墨 ,见图 3 。夹渣的出现大大的 降低了球铁的力学性能 ,特别是伸长率及冲击韧性 下降更明显 。
球墨铸铁缺陷
谈球墨铸铁缺陷研究姜海峰(哈尔滨理工大学材料科学与工程学院,黑龙江哈尔滨 150040)摘要:本文综合分析了球墨铸铁缺陷的研究现状,指出了缩孔缩松、石墨漂浮、皮下气孔、球化不良和球化衰退等球墨铸铁特有缺陷的形成原因及防止措施。
关键词:球墨铸铁;缺陷;现状‘球墨铸铁是本世纪4O年代末发明的,从1950年前后才真正用于生产中。
目前,球墨铸铁已广泛的用于制造一些受力复杂、强度、韧性、耐磨性要求高的零件,如柴油机、汽车及拖拉机的曲轴、凸轮轴、中压闸门,汽车及拖拉机的某齿轮以及农机、农具等零件。
球墨铸铁除具有一般铸造缺陷外,它还经常出现诸如缩孔缩松、夹渣、石墨漂浮、皮下气孔、球化衰退及球化不良等球墨铸铁特有的缺陷。
球铁缺陷的分析研究,多年来一直是铸造工作者和铸造厂家关心的热门话题。
一、缩孔缩松球墨铸铁件与灰铸铁件相比,具有较大的缩孔和缩松倾向,这一直是球墨铸铁件生产技术的关键问题之一,国内外的球铁专家、学者对此进行了大量的研究。
早期人们对球铁件缩孔的形成机理及冒口设计问题认识不清。
有人认为球铁具有与铸钢相同的收缩倾向,因此冒口也要和铸钢一样大。
与此相反,用小冒口甚至不用冒口也能生产出健全铸件。
近年来随着人们对球铁凝固特性认识的深入及电子显徽技术的发展,对球铁缩孔形成机理和冒口设计有了比较清楚的认识。
国内外研究者对球铁缩松作了大量的研究工作,提出了一些消除缩松的措施,但由于早期对缩松产生机理存在较大分歧,各自提出的影响因素和防止措施相差很大。
各家的观点主要集中在三个方面:(1)球墨铸铁糊状凝固特性;(2)石墨化膨胀量和膨胀力;(3)型腔扩大。
分歧较大是在石墨化膨胀的评价上,一者认为石墨析出引起膨胀和体积胀大,有利于消除缩松;一者认为球铁比灰铁大得多的石墨化膨胀力使共晶团之间的间隙扩大,数目增加,使缩松增加。
近年来,人们借助电子显微技术对球铁缩松进行微观观察及分析对缩松的产生和防止有了更进步的认识。
资料认为:石墨化膨胀是控制缩孔、减少缩松的因素,根据铸型刚性条件和铸件结构特点。
球墨铸铁缺陷的金相分析及防止措施
302020年第5期工艺试验与应用球墨铸铁缺陷的金相分析及防止措施球墨铸铁是近几十年才发展起来的高强度铸造金属材料。
与钢材相比,球墨铸铁还有很多优点。
比如铸造性能好,成本相对较低。
由于球墨铸铁产量的不断增加,性能不断开发, 现已成功地部分取代了锻钢和铸钢,成为前景广阔的金属结构材料。
力学性能与金属的金相组织密切相关,什么样的金相结构决定了什么样的力学性能。
球墨铸铁也不例外,因此,对球墨铸铁的金相研究,是我们了解球墨铸铁的先决条件[1]。
下面对我厂生产的材质为QT450-10A 铸件,在生产过程中出现的两种不同缺陷进行分析[2]。
1 显微缩松1.1 微观结构球墨铸铁的显微缩松在显微下观察类似呈片状、多角形,有时连续、有时断续,分布在共晶团边界,有时类似片状石墨(图1),往往我们会误认为该缺陷是由球化不良造成。
这样极大的影响判断问题的改进方向,同时有可能使问题更加突出[3]。
我们对同样试块的缺陷位置进行能谱分析,能谱图像显示该缺陷区域呈乳突状立体结构(图2)。
1.2 形成原因铸件凝固过程中,奥氏体支晶凝固后,残余的铁液则在支晶间最后凝固,因得不到补缩而形成显微缩松,这类显微缩松的形成原因有如下几种原因:(1)碳当量CE 值过低,使得石墨膨胀体积不足以补充凝固过程中的体积收缩;(2)合金成分如Cu、Mn、Cr、P 及残留Mg 过高,增大缩松倾向[4];(3)砂型强度偏低,在铸件凝固过程中铸件体积增大,在体积增大的部位得不到其他部位铁液的补充;(4)工艺设计不合理,热节处在凝固过程中周围没有足够的铁水补充收缩[5];(5)孕育不充分或孕育过量等。
毛洪宇,勾洋洋,张 森(沈阳远大压缩机有限公司,辽宁 沈阳 110020)摘要:摘要:通过显微镜和能谱分析,观察球铁渣气孔和显微缩松的微观特征,找出种差别并分析了形成缺陷的原因;提出的防止缺陷产生的措施,能有效地控制和减少废品的产生,提高了铸件合格率。
关键词:关键词:渣气孔;缩松;预防措施中图分类号:中图分类号:TG245 文献标识码:文献标识码:B 文章编号:文章编号:1673-3320(2020)05-0030-03收稿日期:2020-04-16定稿日期:2020-08-10作者简介:毛洪宇(1986-),男,毕业于辽宁工业大学材料成型及控制工程专业,工程师,主要从事铸造工艺及材料、模具设计制造。
球墨铸铁金相组织缺陷原因及防止方法概述
球墨铸铁金相组织缺陷原因及防止方法概述摘要:比较了球墨铸铁与灰铸铁、碳钢的优缺点,介绍了显微缩松,夹渣,石墨漂浮, 开花石墨球化,球化衰退,如球墨铸铁显微组织缺陷的特点,分析了化学成分、浇注温度、铸造工艺设计、砂型的紧性,组织基因的大小等因素,铸件壁厚对这些缺陷的形成有影响,并提出了相应的预防措施。
最后,指岀球墨铸铁的显微结构决定了铸件的属性,可以采取根据各种金相组织缺陷形成的原因从而采用相应的措施,以提高铸件的质量,提高企业的市场竞争力和经济效益。
关键词:球墨铸铁;金相组织;缺陷;防止措施[前言与灰铸铁不同的是,石墨铸铁中的石墨是球形的,在基质上分解效率较低,使其不耐拉伸、可塑性和灵活性,一切都高于灰色铸铁;与碳钢相比,它的可塑性较低,疲劳与普通中等碳钢相比,儿乎是普通碳钢的两倍,山于其生产成本低于钢。
此外,在球墨铸铁生产中,除了铸造缺陷外,还会出现一些独特的组织缺陷,如明显的微孔和夹渣、石墨浮花、石墨球化不良和球化衰退、口口和反白口、片状石墨和破碎石墨、磷共晶等。
这些组织缺陷各有特点,且相互关联,严重影响铸件的性能。
2显微缩松2.1特征球墨铸铁中的缩松是铸件硬化时岀现的缺陷,而山于无铁液的补充从而出现了缺陷。
除了肉眼可见的松树宏观缩松外,除了出现在金属显微镜下外,还存在明显的边界;一般情况下,间隙呈金刚石角状(严格地说,微孔不属于金相缺陷范畴)。
收缩降低了铸件的力学性能,影响了加工铸件的表面质量。
2.1.1浇注温度铸件浇注温度高,有利于补缩;但浇注温度过高会增加液态收缩量,不利于消除缩孔、缩松。
2.1.2砂型紧实度砂岩厚度太低或不均匀,在金属或石墨膨胀的静态圧力下,这种类型的型壁可能会变形使型腔扩大,不能很好地利用石墨化膨胀进行自补缩,容易导致铸件产生缩松。
2.1.3铸造工艺设计浇注系统、冒口、冷却器设计不当,不能保证液态金属的连续凝固;此外,冒口的数量和尺寸,以及与铸件的正确连接,都会影响冒口的进给效果,使铸件收缩疏松。
球墨铸铁 缺陷 判定依据
球墨铸铁缺陷判定依据【实用版】目录1.球墨铸铁概述2.球墨铸铁的缺陷分类3.球墨铸铁缺陷的判定依据4.球墨铸铁缺陷的防止措施正文一、球墨铸铁概述球墨铸铁是一种高强度、高韧性的铸铁材料,其综合性能接近于钢。
球墨铸铁是通过在铁水中添加球化剂,使铁水中的石墨球化,从而提高铸铁的性能。
在工业生产中,球墨铸铁广泛应用于各种大型零件的铸造,如汽车发动机缸体、轮毂等。
二、球墨铸铁的缺陷分类在球墨铸铁生产过程中,可能会出现多种缺陷,影响铸件的质量。
常见的缺陷有:球化不良、石墨漂浮、夹渣等。
1.球化不良:指铁水中的石墨没有完全球化,导致铸件的性能下降。
2.石墨漂浮:指石墨在铸件中分布不均匀,造成铸件的强度和韧性降低。
3.夹渣:指铸件中夹杂有砂粒、氧化皮等杂物,影响铸件的使用寿命。
三、球墨铸铁缺陷的判定依据判断球墨铸铁缺陷的依据主要包括宏观特征和微观特征。
1.宏观特征:通过肉眼观察铸件表面,检查是否有明显的缺陷,如裂纹、砂孔等。
2.微观特征:通过金相显微镜观察铸件的组织结构,分析缺陷的类型和程度。
例如,通过观察石墨的球化程度,判断球化不良的缺陷。
四、球墨铸铁缺陷的防止措施为了有效防止球墨铸铁缺陷的产生,可以从以下几个方面采取措施:1.选择合适的球化剂和添加剂:根据铸件的性能要求,选择合适的球化剂和添加剂,保证铁水的球化效果。
2.严格控制处理工艺:在生产过程中,严格控制铁水的温度、成分和处理时间,保证球化反应的充分进行。
3.选择优质的原材料:选用优质的铁水、砂子和涂料等原材料,降低缺陷的产生。
4.提高铸型的精度:采用精密的铸型,保证铸件的尺寸和形状精度,减少铸件的缺陷。
5.严格质量检测:对生产过程中的各个环节进行严格的质量检测,及时发现和消除缺陷。
- 1、下载文档前请自行甄别文档内容的完整性,平台不提供额外的编辑、内容补充、找答案等附加服务。
- 2、"仅部分预览"的文档,不可在线预览部分如存在完整性等问题,可反馈申请退款(可完整预览的文档不适用该条件!)。
- 3、如文档侵犯您的权益,请联系客服反馈,我们会尽快为您处理(人工客服工作时间:9:00-18:30)。
提高孕育效果的措施: a.选择强效孕育剂 b.必要的S的含量 c.改善处理方法 d.提高铸件冷却速度
球状石墨的生长条件 a、极低的硫、氧含量 b、限制反球化元素 c、保证必要的冷却速度 d、添加的球化元素 第一组:镁、钇、铈、钙、镧、镤、钐、 镝、镱、钬、铒 第二组:钡、锂、铯、铷、锶、钍、钾、钠 第三组:铝、锌、镉、锡
硅
球墨铸铁中锰的作用就主要表现在增加珠光体的稳定性,帮助形 成碳化锰、碳化铁。锰有严重的正偏析倾向,往往有可能富集于共晶 团界处,严重时会促使形成晶间碳化物,显著降低球墨铸铁的韧性。 锰也会提高铁素体球墨铸铁的韧脆性转变温度,锰含量每增加 0.1%,脆性转变温度提高10~12℃。球墨铸铁中,由于球化元素具有 很强的脱硫能力,不需要锰承担这种功能。 因此,球墨铸铁中锰含量一般是愈低愈好,即使珠光体球墨铸铁, 锰含量也不宜超过0.4~0.6%。一般都是遵循这一规律的。 铸态铁素体Mn:0.3-0.4% 珠光体球铁Mn:0.4-0.6%
碳、硅、锰、磷、硫
球铁 的化 学成 分
碳是球墨铸铁的基本元素,碳高有助于石墨化。由于 石墨呈球状后石墨对机械性能的影响已减小到最低程度, 球墨铸铁的含碳量一般较高,在3.5~3.9%之间,碳当量 在4.1~4.7%之间。铸件壁薄、球化元素残留量大或孕育
不充分时取上限;反之,取下限。将碳当量选择在共晶点
球墨 铸铁
球墨铸铁可以像钢一样,通过热处理和合金化等 措施来进一步提高其使用性能。比如,处理过的球墨 铸铁可以取得很好的韧性,延伸率高达24%;抗拉强 度可以高达1400MPa,基本接近钢材。
与钢材相比,球墨铸铁还有很多优点。比如铸造
性能好,成本相对较低。 由于球墨铸铁产量的不断增加,性能不断开发, 现已成功部分取代了锻钢和铸钢,成为前景广阔的金 属结构材料。
附近不仅可以改善铁液的流动性,对于球墨铸铁而言,碳 当量的提高还会由于提高了铸铁凝固时的石墨化膨胀提高 铁液的自补缩能力。但是,碳含量过高,会引起石墨漂浮。 当碳含量过低时,铸件易产生缩松和裂纹。
碳
根据各元素对共晶点实际碳量的影响,将这些元素的量折算成碳量的
增减。以CE%表示碳当量。为简化计算一般只考虑硅、磷的影响或只考虑
第二次收缩阶段。被树枝晶分割的溶池处成为真空,凝 固后的孔壁粗糙、排满树枝晶的疏松孔为缩松。 原因:碳当量低,磷含量高,增加缩孔缩松倾向。 措施:提高铸型刚度,如使用树脂砂,提高铁液碳
当量。
缩孔 和缩 松
石墨漂浮 特征:冷却过程中的过共晶铁液首先析出石墨球, 上浮聚集成石墨漂浮,分布于铸件最后部位的上部的
石墨 大小
随着珠光体的细化,球墨铸铁的强度和硬度有 所提高。若基体为粒状珠光体,则球墨铸铁在 保持一定强度的同时,具有更高的塑性。
珠光 体粗 细
珠光 体的 粗细
珠光 体数 量
珠光 体数 量
球墨铸铁金相检验评定铁素体数量。其百分 比,按大多数视场对照图片评定。一般不检查牛 眼铁素体数量,仅检查与其共存的珠光体数量。
磷
球墨铸铁中硫与球化元素的化合能力很强,生
成硫化物或硫氧化物,不仅消耗球化剂,造成球化
不稳定,衰退速度加快,而且还使夹杂物数量增多, 导致夹渣、气孔等铸造缺陷。 国外一般要求铁液含硫量低于0.02%,我国目 前由于焦炭含量较高等熔炼条件的限制,往往达不 到这一标准,应进一步改善熔炼条件,有条件可进 行炉外脱硫,一般要求小于0.06%。
渗碳 体数 量
渗碳 体数 量
球墨铸铁中的奥氏体、贝氏体、马氏体是由奥 氏体、上贝氏体或下贝氏体通过等温淬火,加入适 当元素获得。
马氏 体、 贝氏 体
选择适当的化学成分是保证球墨铸铁获得良
好的金相组织和高性能的基本条件,化学成分的
选择既要利于石墨的球化和获得满意的基体,以 期获得满意的性能,又要使球墨铸铁具有良好的 铸造性能。 球墨铸铁的成分一般是指五个元素:
球化 分级
球化级别
说明
球化率(%)
1级
2级
石墨呈球状,少量团絮,允许极少量 团絮状
石墨大部分呈球状,余为团状和极少 量团絮状
≥95
90-95
3级
4级 5级 6级
球化 分级
石墨大部分呈团状,余为团絮状,允 许有极少量蠕虫状
石墨呈大部分絮状或团状,余为球状、 少量蠕虫状 石墨呈分散分布的蠕虫状、片状及球 状、团状、团絮状 石墨呈聚集分布的蠕虫状、片状及球 状、团状、团絮状
硫
球墨铸铁的合金元素主要有钼、铜、
镍、铬、锑、钒、铋等金属。
这些元素的主要是起提高铸铁的强 度,稳定基体组织的作用。
合金 元素
1、球墨铸铁有较宽的共晶温度范围 2、球墨铸铁的糊状凝固特性
3、球墨铸铁具有较大的共晶膨胀
从铁-碳合金的平衡图看来,在共晶成分附近, 凝固的温度范围并不宽。实际上,铁液经球化处理和 孕育处理后,其凝固过程偏离平衡条件很远,在共晶 转变温度(1150℃)以上150℃左右,即开始析出石墨 球,共晶转变终了的温度又可能比平衡共晶转变温度 低50℃左右。
锰
磷是一种有害元素。它在铸铁中溶解度极低,当 其含量小于0.05%时,固溶于基体中,对力学性能几
乎没有影响。当含量大于0.05%时,磷在球墨铸铁中
有很强的偏析倾向,具有增大球铁的缩松倾向,极易
偏析于共晶团边界,形成二元、三元或复合磷共晶,
降低铸铁的韧性。当含磷量增加时,韧脆性转变温度 就会提高。 对于寒冷地区使用的铸件,易采用磷的下限含量。 磷的含量控制在0.04-0.06%以下。
铸铁,使用球墨铸铁的前提条件。
球 墨 铸 铁 的 金 相
球状石墨的形成经历了形核与生长两个阶段。其中
的形核是石墨的首要过程,铁液在熔炼及随后的球化、 孕育处理中产生大量的非金属夹杂物,初生的夹杂物非 常小,在随后浇铸、充型、凝固过程相互碰撞、聚合变 大,上浮或下沉,成为石墨析出的核心。
球状石墨核心形成以后,碳原子开始在核心基底上
铸铁进行孕育处理的目的是为消除球墨铸铁的白口化倾
向、消除过冷石墨、促进石墨化、细化共晶团及减少晶 间偏析等。
球墨 铸铁 孕育 的目 的
球化处理是球铁生产的基础,孕育处理是球铁生产的关键,孕育 效果决定了石墨球的直径、石墨球数和石墨球的圆整度。 为了保证孕育效果,孕育处理采用多级孕育处理。孕育处理越接 近浇注,孕育效果越好。 从孕育到浇注需要一定的时间,该时间越长,孕育衰退就越严重。 球化衰退防止:球化衰退的原因一方面和Mg、RE元素由铁液中逃 逸减少有关,另一方面也和孕育作用不断衰退有关,为了防止球化衰 退,采取以下措施: A、铁 液中应保持有足够的球化元素含量; C、降低原铁液的含硫量,并防止铁液氧化; C、缩短铁液经球化处理后的停留时间; D、铁液经球化处理并扒渣后,为防止 Mg、RE元素逃逸,可用覆盖剂 将铁液表面覆盖严,隔绝空气以减少元素的逃逸。
封面
球墨铸铁是指铁液在凝固过程中碳以球型石墨析
出的铸铁。与灰铸铁相比,其金相组织的最大不同是
石墨形状的改变,避免了灰铸铁中尖锐石墨的存在, 使得石墨对金属基体的切口作用大为减少,基本消除 了片状石墨引起的应力集中现象,使得金属基体的强 度利用率达到70-90%,从而使金属基体的性能得到
很大程度的发挥。
球墨铸铁 的特性
金相组织与力学性能的关系
力学性能与金属的金相组织密切相关,什么样的 金相结构决定了什么样的力学性能。球墨铸铁也不例 外,只有石墨球化,才能发挥金属基体的作用,使铸 铁的力学性能大幅度提高。也只有石墨球化,进一步 改变基体的性能才更有意义。 因此,对球墨铸铁的金相研究,是我们了解球墨
凝固
球化不良和球化退化
特征:断口银灰色,分布芝麻状黑斑点。 金相组织分布大量厚片石墨。 原因:原铁液含硫高,过量反球化元素。 建议选用低硫焦炭,脱硫处理,必要时增
加球化剂稀土量,控制冲天炉鼓风强度和料位。
缺陷 球化 不良
缩孔和缩松 特征:缩孔发生于第一次收缩阶段。表面凹陷及局
部热节凹陷,含气孔的暗缩孔,内壁粗糙。缩松发生于
提高 孕育 的措 施
石墨球螺旋生长模型 a)生长成的球体 b)角锥体单晶 c)锥顶角Φ 与θ 的关系
球 的 生 长 模 型
1、金相组织 球状石墨外貌接近球形, 内部呈放射状,有明显的 偏光效应。
石墨是由很多角锥体枝
晶组成的多晶体,各枝晶
的基面垂直于球径,C轴呈
辐射状指向球心。
球的 金相 形貌
球化 分级
硅的影响。 碳当量算式分别是CE%=C%+1/3(Si+P)%或CE%=C%+1/3Si%。碳是 铸铁生成石墨的来源,是石墨的自发晶核。硅在铸铁中含量较多,是强烈 促进石墨化的元素,能使铁碳合金的共晶、共析点向上向左移动,表明硅 降低了碳在液相和固相中的溶解度,增加了碳的活度,石墨就较容易析出 长大,促进了石墨化过程,因此增加部分硅就相当于增加部分碳。其关系 是当含硅1%时可使共晶点左移O.31%,即共晶点含碳量下降O.3%。将 CE%值和Fe—C稳定态相图上的共晶点C' 的碳量4.26%相比,即可判断某 一具体成分的铸铁偏离共晶点的程度,如CE%高于4.26%为过共晶成分; CE%低于4.26%为亚共晶成分;CE%=4.26%则为共晶成分。除衡量对凝
固过程可以作出判断外,还可以间接推断出铸铁铸造性能好坏及石墨化能
力的大小,是计算铸铁共晶度的基础。碳当量和共晶度都是较重要的参数。
碳当 量
在球墨铸铁中,硅是第二个有重要影响的元素, 它不仅可以有效地减小白口倾向,增加铁素体量,而 且具有细化共晶团,提高石墨球圆整度的作用。但是, 硅提高铸铁的韧脆性转变温度,降低冲击韧性,因此 硅含量不宜过高,尤其是当铸铁中锰和磷含量较高时, 更需要严格控制硅的含量。一般认为硅含量大于2.8% 时,可能降低韧性,使韧性-脆性转变温度升高。 因此,选择碳硅含量时,应按照高碳低硅的原则, 铸件在寒冷地区使用,则含硅量应适当降低。 铁素体C:3.6-4.0% Si:2.4-2.8% 珠光体C:3.4-3.8% Si:2.2-2.4%