球墨铸铁缺陷分析
(27)球墨铸铁件表面缺陷解读

球墨铸铁件表面缺陷清华大学于震宗引言球墨铸铁件的缺陷分为表面缺陷和内在缺陷两大类,后者即有关金属材质方面的缺陷,不属于本文范围内。
本文内容重点是砂型铸件的表面缺陷,包括用湿型砂、水玻璃砂、树脂砂等砂型和砂芯生产的铸件。
砂型球墨铸件的表面缺陷有多种,本文仅选择①粘砂,②砂孔和渣孔,③夹砂,④气孔,⑤胀砂、缩孔和缩松等缺陷进行讨论。
有的缺陷如灰班虽然发生在铸件表面上,而产生原因完全属于材质方面,则不包括在本文内:一. 球墨铸件气孔缺陷气孔是最难分析其形成原因和最难找出防治方法的铸件缺陷。
这是因为气孔的形成原因很多,从外观上又不易分清气孔是属于那种类型的。
虽然采用扫描电镜和能谱等微观分析方法有助于估计气孔的产生原因,但是这些先进的技术都还处于研究阶段,大多数铸造工厂尚难在生产中利用。
根据气孔发生机理,可分为裹入、侵入、析出和反应四类气孔。
其中裹入气孔是浇注时金属液中裹带着空气泡,随着液流进入型腔中而产生的气孔缺陷。
侵入气孔是铸件表面凝固成壳以前,砂型、砂芯等造型材料受热产生的气体侵入金属液中,形成气泡而产生的气孔球铁铸件最常遇到的气孔缺陷是反应气孔和析出气孔。
以下将分别讨论:1. 析出气孔金属液中溶解的原子态氢、氮气体元素,随金属温度下降而溶解度逐渐减小。
下降至结晶温度或凝固温度时,溶解度突然变小,氢、氮以分子态气相析出形成气泡,使铸件产生气孔,称为析出气孔。
生产铸铁的工厂中,最常见的析出气孔是使用树脂砂型和砂芯造成氨氮气孔,也有来自炉料和增碳剂的氮气孔。
①氨氮酚醛树脂覆膜砂的硬化剂为乌洛托平(六亚甲基四胺(CH2)6N4)。
铸铁件用热芯盒呋喃树脂含有尿素(CO(NH2)2)。
硬化剂用含有尿素和NH4Cl的水溶液。
冷芯盒和自硬砂用酚醛脲烷树脂的聚异氰酸酯组分中含有-RNCO基团。
上述树脂砂都含有多少不等的氨或胺,都是引起析出气孔的根源。
所含氮不同于空气中的氮,大气中78%是由氮组成,并不引起析出气孔缺陷。
球墨铸铁常见缺陷的分析与对策
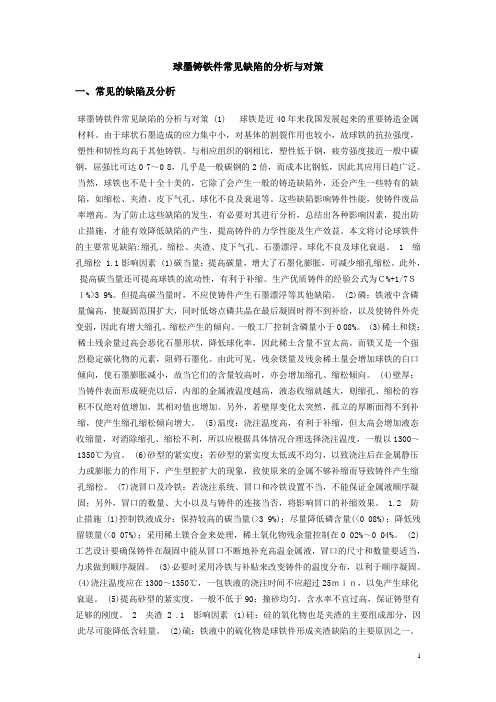
球墨铸铁件常见缺陷的分析与对策一、常见的缺陷及分析球墨铸铁件常见缺陷的分析与对策 (1) 球铁是近40年来我国发展起来的重要铸造金属材料。
由于球状石墨造成的应力集中小,对基体的割裂作用也较小,故球铁的抗拉强度,塑性和韧性均高于其他铸铁。
与相应组织的钢相比,塑性低于钢,疲劳强度接近一般中碳钢,屈强比可达0 7~0 8,几乎是一般碳钢的2倍,而成本比钢低,因此其应用日趋广泛。
当然,球铁也不是十全十美的,它除了会产生一般的铸造缺陷外,还会产生一些特有的缺陷,如缩松、夹渣、皮下气孔、球化不良及衰退等。
这些缺陷影响铸件性能,使铸件废品率增高。
为了防止这些缺陷的发生,有必要对其进行分析,总结出各种影响因素,提出防止措施,才能有效降低缺陷的产生,提高铸件的力学性能及生产效益。
本文将讨论球铁件的主要常见缺陷:缩孔、缩松、夹渣、皮下气孔、石墨漂浮、球化不良及球化衰退。
1 缩孔缩松 1.1影响因素 (1)碳当量:提高碳量,增大了石墨化膨胀,可减少缩孔缩松。
此外,提高碳当量还可提高球铁的流动性,有利于补缩。
生产优质铸件的经验公式为C%+1/7Si%>3 9%。
但提高碳当量时,不应使铸件产生石墨漂浮等其他缺陷。
(2)磷:铁液中含磷量偏高,使凝固范围扩大,同时低熔点磷共晶在最后凝固时得不到补给,以及使铸件外壳变弱,因此有增大缩孔、缩松产生的倾向。
一般工厂控制含磷量小于0 08%。
(3)稀土和镁:稀土残余量过高会恶化石墨形状,降低球化率,因此稀土含量不宜太高。
而镁又是一个强烈稳定碳化物的元素,阻碍石墨化。
由此可见,残余镁量及残余稀土量会增加球铁的白口倾向,使石墨膨胀减小,故当它们的含量较高时,亦会增加缩孔、缩松倾向。
(4)壁厚:当铸件表面形成硬壳以后,内部的金属液温度越高,液态收缩就越大,则缩孔、缩松的容积不仅绝对值增加,其相对值也增加。
另外,若壁厚变化太突然,孤立的厚断面得不到补缩,使产生缩孔缩松倾向增大。
球墨铸铁常见缺陷的分析与对策
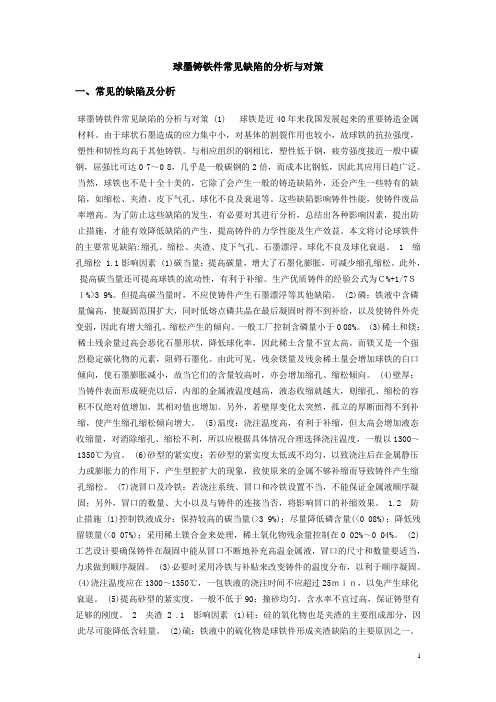
球墨铸铁件常见缺陷的分析与对策一、常见的缺陷及分析球墨铸铁件常见缺陷的分析与对策 (1) 球铁是近40年来我国发展起来的重要铸造金属材料。
由于球状石墨造成的应力集中小,对基体的割裂作用也较小,故球铁的抗拉强度,塑性和韧性均高于其他铸铁。
与相应组织的钢相比,塑性低于钢,疲劳强度接近一般中碳钢,屈强比可达0 7~0 8,几乎是一般碳钢的2倍,而成本比钢低,因此其应用日趋广泛。
当然,球铁也不是十全十美的,它除了会产生一般的铸造缺陷外,还会产生一些特有的缺陷,如缩松、夹渣、皮下气孔、球化不良及衰退等。
这些缺陷影响铸件性能,使铸件废品率增高。
为了防止这些缺陷的发生,有必要对其进行分析,总结出各种影响因素,提出防止措施,才能有效降低缺陷的产生,提高铸件的力学性能及生产效益。
本文将讨论球铁件的主要常见缺陷:缩孔、缩松、夹渣、皮下气孔、石墨漂浮、球化不良及球化衰退。
1 缩孔缩松 1.1影响因素 (1)碳当量:提高碳量,增大了石墨化膨胀,可减少缩孔缩松。
此外,提高碳当量还可提高球铁的流动性,有利于补缩。
生产优质铸件的经验公式为C%+1/7Si%>3 9%。
但提高碳当量时,不应使铸件产生石墨漂浮等其他缺陷。
(2)磷:铁液中含磷量偏高,使凝固范围扩大,同时低熔点磷共晶在最后凝固时得不到补给,以及使铸件外壳变弱,因此有增大缩孔、缩松产生的倾向。
一般工厂控制含磷量小于0 08%。
(3)稀土和镁:稀土残余量过高会恶化石墨形状,降低球化率,因此稀土含量不宜太高。
而镁又是一个强烈稳定碳化物的元素,阻碍石墨化。
由此可见,残余镁量及残余稀土量会增加球铁的白口倾向,使石墨膨胀减小,故当它们的含量较高时,亦会增加缩孔、缩松倾向。
(4)壁厚:当铸件表面形成硬壳以后,内部的金属液温度越高,液态收缩就越大,则缩孔、缩松的容积不仅绝对值增加,其相对值也增加。
另外,若壁厚变化太突然,孤立的厚断面得不到补缩,使产生缩孔缩松倾向增大。
球墨铸铁常见的铸造缺陷
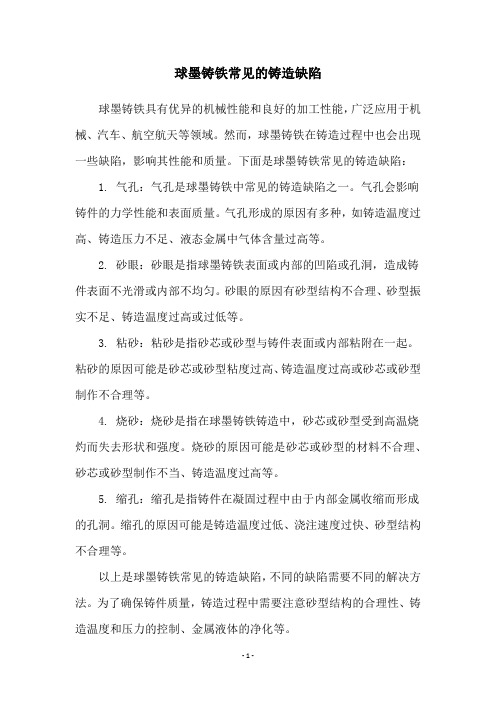
球墨铸铁常见的铸造缺陷
球墨铸铁具有优异的机械性能和良好的加工性能,广泛应用于机械、汽车、航空航天等领域。
然而,球墨铸铁在铸造过程中也会出现一些缺陷,影响其性能和质量。
下面是球墨铸铁常见的铸造缺陷:
1. 气孔:气孔是球墨铸铁中常见的铸造缺陷之一。
气孔会影响铸件的力学性能和表面质量。
气孔形成的原因有多种,如铸造温度过高、铸造压力不足、液态金属中气体含量过高等。
2. 砂眼:砂眼是指球墨铸铁表面或内部的凹陷或孔洞,造成铸件表面不光滑或内部不均匀。
砂眼的原因有砂型结构不合理、砂型振实不足、铸造温度过高或过低等。
3. 粘砂:粘砂是指砂芯或砂型与铸件表面或内部粘附在一起。
粘砂的原因可能是砂芯或砂型粘度过高、铸造温度过高或砂芯或砂型制作不合理等。
4. 烧砂:烧砂是指在球墨铸铁铸造中,砂芯或砂型受到高温烧灼而失去形状和强度。
烧砂的原因可能是砂芯或砂型的材料不合理、砂芯或砂型制作不当、铸造温度过高等。
5. 缩孔:缩孔是指铸件在凝固过程中由于内部金属收缩而形成的孔洞。
缩孔的原因可能是铸造温度过低、浇注速度过快、砂型结构不合理等。
以上是球墨铸铁常见的铸造缺陷,不同的缺陷需要不同的解决方法。
为了确保铸件质量,铸造过程中需要注意砂型结构的合理性、铸造温度和压力的控制、金属液体的净化等。
分析球墨铸铁气孔缺陷的成因及对策

分析球墨铸铁气孔缺陷的成因及对策球墨铸铁是一种重要的铸造材料,具有优异的力学性能和耐腐蚀性能。
然而,球墨铸铁在生产过程中常常会出现气孔缺陷,这给材料的性能和使用带来了一定的影响。
本文将分析球墨铸铁气孔缺陷的成因,并提出相应的对策。
一、球墨铸铁气孔缺陷的成因1. 原材料质量不过关球墨铸铁的原材料包括铸造合金、铁水和融化剂等。
如果原材料质量不过关,其中可能含有一些气体或杂质,这些气体和杂质在铸造过程中会引起气孔的形成。
2. 熔炼过程控制不当球墨铸铁的熔炼过程非常重要,包括预处理炉熔化、调温、组织调整等环节。
如果熔炼过程控制不当,如温度过高或过低、保温时间不足等,都会影响铸件的质量,导致气孔的生成。
3. 浇注工艺不合理浇注工艺是影响球墨铸铁气孔缺陷的另一个重要因素。
如果浇注过程中温度不适宜、过急或过慢,浇注口设计不合理等,都会导致铸件内部无法顺利排出气体,从而产生气孔。
4. 冷却过程不当冷却过程是球墨铸铁形成细小球状石墨的关键环节。
如果冷却速度过快或过慢,都会导致气孔的形成。
此外,冷却过程中如果没有进行充分的冷镦处理,也会使气孔得不到有效修复。
二、对策1. 加强原材料质量检验提高球墨铸铁的质量,关键在于对原材料进行严格的质量检验。
选用质量好、经过认证的原材料,并充分进行化验和试样,确保原材料中没有含有气体或杂质。
2. 控制熔炼过程在熔炼过程中,需严格控制炉温和保温时间,确保炉内温度适宜,熔铁中的合金溶解均匀。
同时,需要合理添加融化剂和调节剂,以提高铁水的流动性和抗气化能力,减少气孔的形成。
3. 优化浇注工艺浇注工艺的优化可以通过优化浇注温度和速度,改进浇注系统和浇注口的设计,避免过度的温度梯度和急剧的温度变化。
此外,还可以采取减少浇注冲击力和加强细化剂的添加等措施,提高铁水的流动性和浇注质量。
4. 控制冷却过程在冷却过程中,需要控制铸件的冷却速度。
这可以通过适当调整冷却水的供应量和加强冷却设备的管理来实现。
铸铁缺陷原因介绍

6、适当增加加工余量
缩松
铸件内部有许多分散小缩孔,其表面粗糙,水压试验渗水
一般认为由于球铁凝固特性所决定的,其影响因素有
1、碳、硅含量低;磷含量高
2、残留镁量偏高
3、浇注温度低,影பைடு நூலகம்冒口补缩效果
4、铸型紧实度低
1、适当提高铁液碳、硅含量,尽量降低磷含量。铁液球化处理后应充分孕育保证石墨充分析出,提高自身补缩能力
球墨铸铁件缺陷分析
在球墨铸铁件生产中,常见的铸件缺陷除有灰铸铁件的一般缺陷外,还有球化不良、球化衰退、夹渣、缩松、石墨漂浮、皮下气孔等。通常,产生这些缺陷的原因不单是球化处理问题,有时还有造型制芯、熔炼浇注、配砂质量、落砂清理等许多工序的问题,因此必须具体分析、以便采取相应的合理措施加以解决。
球铁特有的缺陷分析
6、在铸型表面喷涂锭子油碳质材料,使铁液与铸型界面造成还原性气氛、在铁液表面或铸型表面撒上少量冰晶石粉或氟硅酸钠等能减少或消除皮下气孔
碎块状石墨
显微组织为少量大块石墨球周围共晶团边界均匀分布碎块状石墨和铁素体,石墨球也生长成连接成分枝石墨,其宏观断面为界限分明的暗灰色斑点,主要产生在大断面铸件热节部位或冒口颈下
铁液碳当量超过共晶点,初生的球状石墨从高温液态中析出,由于密度的差别和镁蒸汽泡上浮使部分石墨上浮至铸件上表面聚集,随后在共晶转变时迅速变大,形成石墨漂浮。因此碳当量越高、铸件越厚、铁液残留镁含量越低,浇注温度越高,越容易产生
1、严格控制碳当量,当壁厚大于70mm的铸件,碳当量必须小于4.55%,当壁厚小于30mm,碳当量必须小于4.70%,其余按这个范围适当调整
4、在铁液表面加覆盖剂,如石墨粉、木炭粉、冰晶石粉等
夹渣
球墨铸铁常见的铸造缺陷
球墨铸铁常见的铸造缺陷球墨铸铁是一种用途广泛的合金材料,广泛应用于汽车、机械、农业机械、建筑设备等工业领域。
虽然球墨铸铁有很多优点,如高强度、高韧性、耐腐蚀和低温性能等,但它也有一些常见的铸造缺陷需要注意。
第一,浇口缺陷。
浇口是铸造过程中的关键部位,它是铸件的入口,直接关系到铸件的质量。
球墨铸铁的浇口缺陷主要包括翘口、裂纹和气孔等。
这些缺陷会导致铸件的强度降低,表面质量差,甚至无法使用。
第二,气孔缺陷。
气孔是铸铁材料中最常见的缺陷之一,也是球墨铸铁的重要缺陷类型。
气孔是由于铸造过程中未能完全去除空气或其他气体引起的。
气孔会导致铸件的强度下降,同时对铸件的密封和耐腐蚀性能也有影响。
第三,缩孔缺陷。
缩孔是铸件内部的气孔,是由于铸造过程中液态金属流动受阻引起的。
缩孔也会影响铸件的强度和维修性能,过多的缩孔会导致铸件完全失效。
第四,热裂缺陷。
球墨铸铁具有很好的耐热性能,但在铸造过程中可能会出现热裂缺陷。
热裂是由于铸件随着温度升高而产生的热应力引起的。
这种缺陷可能会导致铸件断裂,影响使用寿命。
为了避免这些缺陷的发生,需要在整个铸造过程中加强质量控制和监测。
对于浇口和气孔缺陷,可以在设计过程中优化铸件结构和浇注系统,加强铸造参数的控制和优化。
对于缩孔和热裂缺陷,需要加强熔炼和浇注过程的管理,避免过度的冷却和应力积累。
总之,球墨铸铁作为一种重要的铸造材料,在铸造过程中容易出现一些常见的缺陷。
加强质量控制和监测,优化铸造结构和参数控制,可以有效地减少这些缺陷的出现,提高球墨铸铁的质量和使用寿命。
浅析球墨铸铁件缺陷产生原因及防止措施
浅析球墨铸铁件缺陷产生原因及防止措施
1、坯料的缺陷:由于坯料的杂质含量过高,砂砾过大,沿铸缸边缘空隙较大等,都有可能导致炉内坯料缺陷大,从而产生球墨铸铁件缺陷。
2、成型工艺有问题:如砂芯型腔孔形不规则,型腔深度低,入型质量差,表面光洁度及粘结质量差等,都有可能产生球墨铸铁件缺陷。
3、浇注不合理:球墨铸铁件的浇注工艺过程中需要满足一定的条件,当不合理时,会导致溶质的不均匀分布,产生球墨铸铁件缺陷。
4、冷却不合理:冷却工艺是球墨铸铁件质量重要影响因素,冷却不合理,有可能使坯体结晶不良,从而产生球墨铸铁件缺陷。
二、防止球墨铸铁件缺陷的措施
1、提高坯料质量:在生产过程中,应加强原料检查,确保原料质量良好,并严格控制杂质含量,以减少成型过程中缺陷的发生。
2、改进成型工艺:应采用有利于消除和避免缺陷的成型工艺,如采用自动模具成型等技术,减少缺陷产生的可能性。
3、改善浇注工艺:采用有利于消除缺陷的浇注工艺,如采用连续浇铸或提高浇注压力,改善浇注品质,以减少球墨铸铁件缺陷。
4、优化冷却工艺:采用合理的冷却系统可以有效地控制坯体扩大速度,减少坯体内部残余应力,提高结晶度,以减少球墨铸铁件缺陷的产生。
三、结论
球墨铸铁件的缺陷的产生主要由坯料质量、成型工艺、浇注工艺以及冷却工艺不合理等原因引起。
因此,为防止球墨铸铁件缺陷的产生,应采取提高坯料质量、改进成型工艺、改善浇注工艺以及优化冷却工艺等措施。
只有这样,才能在生产过程中控制住缺陷,获得优良质量的球墨铸铁件。
浅析球墨铸铁件缺陷产生原因及防止措施
浅析球墨铸铁件缺陷产生原因及防止措施球墨铸铁件是金属材料的重要形式之一,铸件能有效地满足我们对各种结构形式的需求,而球墨铸铁件特别具有优良的物理机械性能,应用范围广泛,它们已成为轻量化、高强度、低成本的产品,可用来生产复杂的零部件和设备,因此球墨铸铁件成为工程用铸件中使用最多的一种类型。
但是,随着生产工艺的复杂性增加,球墨铸铁件在生产过程中也容易发生缺陷。
因此,本文的目的是研究球墨铸铁件的缺陷产生原因以及它们的防止措施。
一、球墨铸铁件缺陷产生原因1、生产工艺参数设置不当在球墨铸铁件生产过程中,不同工序的工艺参数设置不当,可能会造成缺陷产生。
如果没有适当调整球墨铸铁件的温度、合金比例、凝结时间、含气量等工艺参数,就会导致缺陷的产生,如缺棱、晶粒粗化、孔洞、收缩口等。
2、焊接工艺条件不当在球墨铸铁件的制造过程中,焊接工艺的条件设置不当,也会导致缺陷的产生,如熔池深度不够、焊接温度太高、电流大小不当、焊接电压太低等。
3、金属材料质量不佳金属材料质量不佳也是造成球墨铸铁件缺陷的一个重要原因,这是由于金属材料不合格,有氧化物、夹杂物等污染物。
这些杂质可以在球墨铸铁件内部形成孔洞或层,造成缺陷。
4、操作人员技术素养不足操作人员的技术素养也是产生缺陷的一个重要原因,如果操作人员缺乏技术素养,他们就不能熟练掌握工艺流程,也会导致生产过程中的缺陷。
二、防止球墨铸铁件缺陷的措施以上是球墨铸铁件缺陷的原因,那么如何防止缺陷产生呢?1、优化工艺参数设置在球墨铸铁件生产过程中,加强对工艺参数的监控,优化工艺参数设置,确保金属材料在加工上能满足一定的质量要求。
2、严格控制焊接工艺条件焊接是一项技术复杂的任务,因此我们应该在焊接工艺中严格控制各项工艺参数,确保球墨铸铁件能获得良好的焊接性能,从而防止缺陷的产生。
3、挑选优质金属材料在球墨铸铁件生产中,应该重视金属材料的质量,仅选用合格的金属材料,这样可以减少出现缺陷的概率。
4、提升操作人员技术素养提升操作人员的技术素养是防止球墨铸铁件缺陷的重要措施之一,建立科学的操作流程,以此来提高操作人员的技术水平,减少因技术不足而导致的缺陷。
球墨铸铁常见的铸造缺陷
球墨铸铁常见的铸造缺陷
球墨铸铁是一种常见的铸造材料,它具有高强度、耐磨性和耐腐蚀性等优良性能,被广泛应用于汽车、机械、建筑等领域。
然而,在球墨铸铁的生产过程中,常常会出现一些铸造缺陷,这些缺陷会影响产品的质量和使用寿命。
下面介绍几种球墨铸铁常见的铸造缺陷:
1. 气孔:气孔是由于熔体中的气体未能完全排除而形成的圆形
孔洞。
气孔的存在会降低球墨铸铁的强度和韧性,并且容易导致断裂。
2. 热裂纹:热裂纹是由于球墨铸铁在冷却过程中由于温差变化
引起的裂纹。
热裂纹的存在会影响球墨铸铁的机械性能和使用寿命。
3. 砂眼:砂眼是由于砂芯或模具中残留的砂粒等杂质导致的孔洞。
砂眼会使球墨铸铁表面粗糙,影响外观和表面质量。
4. 夹杂物:夹杂物是指在球墨铸铁中存在的非金属夹杂物,如
氧化物、硫化物和硅化物等。
夹杂物的存在会降低球墨铸铁的强度和韧性,并且容易导致断裂。
5. 缩孔:缩孔是由于球墨铸铁在凝固过程中由于体积收缩而形
成的孔洞。
缩孔的存在会降低球墨铸铁的强度和韧性,并且容易导致断裂。
以上是球墨铸铁常见的铸造缺陷。
生产者需要通过优化铸造工艺、提高工艺水平和加强质量控制等措施来减少这些缺陷的出现,从而保证球墨铸铁的品质和使用寿命。
- 1 -。
- 1、下载文档前请自行甄别文档内容的完整性,平台不提供额外的编辑、内容补充、找答案等附加服务。
- 2、"仅部分预览"的文档,不可在线预览部分如存在完整性等问题,可反馈申请退款(可完整预览的文档不适用该条件!)。
- 3、如文档侵犯您的权益,请联系客服反馈,我们会尽快为您处理(人工客服工作时间:9:00-18:30)。
大批量生产球墨铸铁金相缺陷分析及其对策
李明宽
摘 要:通过对石墨变异的各种特征的观察,分析形成缺陷的原因,提出防止缺陷产生的措施,有效地控制和减少
废品的产生,提高了铸件合格率。
关键词:蠕虫状石墨 爆炸性石墨 粗短型石墨 钉状石墨 石墨漂浮 表面片状石墨 列队石墨球 铸造缺陷
1. 问题的提出
在大批量球铁生产中,往往因过程及原材料等原因,会使铸件产生各种金相组织缺陷,从而影响铸件的内在质量,降低铸件的力学性能。
笔者就多年来在球铁金相分析中所观察到的蠕虫状石墨、爆炸性石墨、粗短型石墨、钉状石墨、石墨漂浮、表面片状石墨和列队石墨球七种缺陷并作相应的分析,提出防止缺陷产生的办法,以减少废品,提高铸件合格率。
2. 蠕虫状石墨
(1) 特征 短而粗、呈卷曲的厚片状端部较钝常与球状石墨联结在一起。
如图
1
图1 QT450-12球铁蠕虫状石墨显微组织 100×
(2) 原因分析 形成蠕虫状石墨的主要原因是球化反应时中间合金数量不够所造成A 合金加
入量少;B 球化剂数量合适,但铁水中含硫量高;C
铁水被氧化致使镁量烧损而造成球化剂含量不足,D 温度过高或停留时间过长,E 铁水中钛和铝过量等原因。
(3) 生产中防止蠕虫状石墨应采取的措施 A 球化剂要有足够的加入量;B 在球化处理时,应尽量防止镁的烧损,提高球化剂吸收率;C 严格控制原铁水含硫量,应选用低硫生铁;C 铁水温度应控制在工艺要求范围内(1510±10℃),铁水温度过高会产生球化剂烧损过多,缩短浇注时间,D 钛含量控制在≤0.05%,铝含量≤0.06%。
3. 爆炸性石墨
(1) 特征 爆炸性石墨由球状石墨爆裂而成,外形如花瓣,常出现在强过共晶球铁中,在厚大断面或石墨飘浮区内。
如图
图2 QT450-10球铁中爆炸性石墨 100×
(2) 原因分析 产生爆炸性石墨的主要原因为:A 碳硅当量过高(碳当量>4.6%,B 稀土量过多,尤其是中频炉熔炼。
(3) 防止爆炸性石墨应采取的措施 A 严格控制碳硅当量,碳不应超过3.8%,硅不应超过3%,厚大铸件的碳硅量应更低;B 加入少量强烈阻止石墨化的元素,如加入钼可防止爆炸性石墨;C 严格控制稀土元素残留量。
4. 粗短型石墨 (1) 特征 粗短型石墨呈现粗短的条状形常出现在厚大断面的中心或铸件的热节处.如图
3 图3 QT450-10球铁粗短型石墨 100×
(2) 原因分析 铁水中残存稀土量过多,特别是使用高纯炉料时较明呈地出现在碳当量较高的铸件中。
(3) 防止产生粗短型石墨的措施 A 严格控制碳硅当量,碳不应超过3.8%,硅不应超过3%,厚大铸件的碳硅量应更低;BC 严格控制稀土元素残留量≤0.02%。
5. 钉状石墨
(1) 特征 钉状石墨或为刺状石墨是由石墨蜕变为针刺的片状二次石墨,如图
4
图4 QT450-10球铁中钉状石墨 100×
(2) 原因分析 钉状石墨产生是铁水中微量的未被稀土中和的钛、锑、铅所致。
(3) 防止产生钉状石墨或为刺状石墨的措施 A 采用含钛、锑、铅少的原材料;B 适当增加稀土镁球化剂。
6. 石墨漂浮
(1) 特征 石墨粗大、密集断口呈暗黑色。
如图
5
图5 球铁中石墨漂浮 100×
(2) 原因分析 A 碳当量过高(碳当量>4.6%);B 浇铸温度偏高;C 截面的凝固速度过慢孕育不足。
(3) 防止产生石墨漂浮的措施 A 严格控制碳硅当量,碳不应超过3.8%,硅不应超过3%,
厚大铸件的碳硅量应更低;B 控制浇铸温度,小于1430℃厚大铸件应更低;C 厚大铸件应加强孕育。
7. 表面片状石墨
(1) 特征 表面片状石墨是球墨铸铁铸件的表面出现片状石墨。
如图
6
图6 球铁中石墨漂浮 100×
(2) 原因分析 砂型表面富积大量的硫,由于铁水中的镁与硫发生反应,使球状石墨恢复到片状石墨。
(3) 防止产生表面片状石墨的措施 采用优质煤粉减少砂型中含硫量。
8. 列队石墨球
(1) 特征 基体由珠光体和铁素体组成,部分铁素体呈现带状,石墨球在这种铁素体带内,沿直线排列。
如图
7
图7 球铁中列队石墨球 100×
(2) 原因分析 A 碳当量偏低;B 孕育不足;C 过高的浇铸温度。
(3) 防止产生列队石墨球的措施 A 严格控制碳当量大于4%;B 加强孕育;C 控制浇铸温度,小于1430℃厚大铸件应更低。
9 结论
通过以上铸造缺陷的分析以及在生产过程中采取的相应措施,稳定地大批量生产合格的球墨铸件。